
книги / Некоторые вопросы усталостной прочности стали
..pdf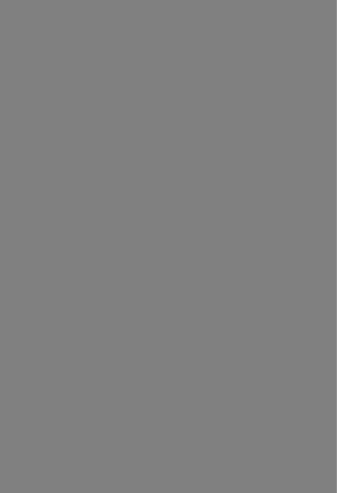
в случае дробеструйной обработки и обкатки роликами опасная точка располагалась на поверхности.
В соответствии со сказанным (стр. 169), можно заключить, что при данных видах обработки остаточные напряжения играли, безусловно, положительную роль, и всякое уменьшение их вредно отражалось на выносливости образцов.
При испытании же поверхностно закаленных образцов опас ная точка располагалась под упрочненным слоем (об этом гово рят изломы). Уменьшение эффективности остаточных напряжений, по крайней мере некоторое (стр. 169), являлось полезным.
Отметим, кстати, что не только при поверхностной закалке, но и при цементации, если опасная точка тоже располагается под слоем, упрочнение может оказаться при кручении более значи тельным, чем при изгибе. В опытах [36] с хромоникелевой сталью цементация гладких образцов на глубину 0,2 лш вызвала повы
шение предела выносливости при |
кручении на 26%, тогда как |
|
при изгибе предел выносливости |
увеличился только |
на 13%. |
Очевидно, остаточные напряжения |
представляли собой |
отрица |
тельный фактор, по крайней мере постольку, поскольку их интен сивность была больше, чем это необходимо для перевода опасной точки с поверхности под слой.
При циклическом кручении эффективность поверхностной обработки в случае образцов с кольцевой канавкой оказалась выше, чем в случае гладких образцов, хотя повышение это не столь резко, как наблюдаемое обычно при изгибе.
Возрастание эффективности поверхностной обработки при наличии кольцевой канавки связано с усилением полезной роли остаточных напряжений, объясняющимся в-первую очередь кон центрацией этих напряжений по дну канавки.
Значение усиления полезной роли остаточных напряжений при кручении много меньше, чем при изгибе, поскольку сама роль их при кручении меньше. В опытах 135) с высверливанием образцов указанная роль остаточных напряжений вообще оста лась невыявленной. В этих опытах кольцевая канавка наноси лась на цилиндрические усталостные образцы двумя способами — резцом и накаткой. Затем часть образцов из каждой группы высверливалась по оси с целью уменьшения остаточных напря жений. Возрастание' предела выносливости, связанное с накат кой, оказалось при кручении примерно одинаковым для сплош ных и полых образцов. В то же время при изгибе высверливание образцов снижало эффективность накатки в несколько раз.
Теоретический анализ, проведенный И. В. Кудрявцевым [15], показывает тем не менее, что при чистом сдвиге, какой имеет, в частности, место в точках поверхности дна канавки скручива емого образца, остаточные напряжения должны играть известную роль. И это подтверждается в наших экспериментах фактом за метного повышения предела выносливости образцов, обработан ных дробью, когда толщина упрочненного слоя практически не
182
отличалась от глубины канавки, и полученный эффект можно» следовательно, в большой мере приписывать действию остаточных напряжений.
Соображения, касающиеся образцов с кольцевой канавкой, переносимы па принципиально близкий случай образцов с гал телью малого радиуса.
Обращает на себя внимание то обстоятельство, что обкатка галтели малого радиуса самоустаиавливающимся роликом дала значительный эффект даже при таком сравнительно мягком мате риале, какой был использован для экспериментов. Повышение предела выносливости составило при кручении 20%, при изгибе — 35%.
Дробеструйная обработка образцов, не затрагивавшая поверх ности самой галтели, принесла все же при кручении заметную пользу, что опять-таки говорит об эффективности остаточных напряжений в условиях чистого циклического сдвига.
Нужно иметь в виду, что при нагружении образцов рассмат* риваемых типов опасная точка всегда располагалась на поверх ности галтели или дна канавки.
Упрочняющая поверхностная обработка оказалась при кру чении особенно эффективной для образцов с канавкой, нанесен ной под углом в 45° к образующей. Опасная точка здесь также неизменно располагалась на поверхности, дна канавки. Но если
вслучае кольцевой канавки напряженное состояние (от нагрузки)
вточках, расположенных на ее дне, не отличается от напряжен?
ного состояния |
точек тела гладкого скручиваемого образца, то |
в случае косой |
канавки дело обстоит иначе. В точках ее дна два |
отличные от нуля главные напряжения резко неодинаковы по величине. В этих условиях усиление полезной роли остаточных напряжений, связанное с наличием концентратора, приобретает большое значение, поскольку само влияние остаточных напря жений оказывается увеличенным благодаря изменению напря женного состояния в направлении приближения к линейному.
Косая канавка наносилась под углом 45° к оси образца, т.е, перпендикулярно одному и параллельно другому главным напря жениям. При этом было безразлично, к какому из главных напря жений она оказывалась перпендикулярной, поскольку циклы указанных напряжений при симметричном кручении совершенно одинаковы.
Заметим, однако, что если бы образцы испытывались в усло виях асимметричного кручения, то средние напряжения циклов главных напряжений имели бы различный знак. Тогда канавка, перпендикулярная главному напряжению с растягивающим сред ним напряжением цикла, была бы, очевидно, опаснее, чем канавка, ему параллельная. В то же время при наличии первой канавки поверхностная обработка, несомненно, дала бы больший эффект.
Сравнение результатов дробеструйного наклепа и обкатки роликами для образцов гладких и с косой канавкой указывает
лишний раз на то, что повышение эффективности поверхностной обработки в присутствии концентраторов напряжений связано именно с усилением полезной роли остаточных напряжений. В случае дробеструйной обработки толщина упрочненного слоя почти не превышала глубины канавки, тем не менее эффектив ность обработки в присутствии канавки оказалась в 7 раз больше, чем в ее отсутствии. В случае же обкатки частное от деления соответствующих показателей составляет только 2,2, хотя канавка прорезала упрочненный слой всего примерно на одну треть.
Для образцов с поперечным сверлением упрочняющая обра ботка внешней поверхности принесла меньшую пользу, чем для гладких. В данном случае при нагружении упрочненных образ цов опасная точка всегда располагалась внутри поперечного канала, около границы упрочненного слоя, в зоне действия растя гивающих остаточных напряжений.
При таких обстоятельствах степень упрочнения зависит пре имущественно от относительной толщины упрочненного слоя вблизи сверления.и от величины подслойного пика растягиваю щих остаточных напряжений. Чем толще слой и чем меньше пик напряжений, тем выше эффективность обработки.
Степень упрочнения оказалась значительной в случае закалки, при которой относительная толщина упрочненного слоя дости
гала весьма |
внушительных значений |
(до половины |
радиуса |
|
образца), |
но |
была совсем небольшой |
в случаях дробеструйной |
|
•обработки |
и |
обкатки. |
|
|
При малой относительной толщине упрочненного слоя и зна чительном подслойном пике растягивающих остаточных напря жений поверхностная обработка может оказать даже отрицатель ное влияние на выносливость изделий с поперечным сверлением. Так, в опытах [36] с хромоникелевой сталью цементация внеш
ней поверхности образцов с поперечным |
каналом на |
глубину |
0,2 мм снизила предел выносливости на |
17%. |
следует |
Для получения высоких положительных результатов |
упрочнять не только внешнюю поверхность изделия, но и поверх ность канала. В цитированных опытах цементация образцов с выполнением указанного требования (толщина слоя на пери ферии образца 0,2 мм, в канале 0,33 мм) увеличила предел выиог сливости на 150%. Подобным образом действует и азотирование. На образцах из стали ЭИ-275 С. В. Серенсеном и И. Е. Конторовичем [28] установлено, например, повышение предела выносли вости в результате применения этой обработки на 110%.
Что касается эффективности отдельных видов упрочняющей поверхностной обработки, то в рассматриваемых опытах, про веденных на нормализованной стали, поверхностная закалка дала весьма большой эффект (упрочнение гладких образцов составило при кручении 92%). Результаты применения механических мето дов упрочнения оказались значительно скромнее, особенно резуль таты применения дробеструйного наклепа.
184
Не представляет, однако, сомнений, что при применении предварительной термообработки в виде закалки с отпуском, в особенности с низким отпуском, эффективность механических методов упрочнения будет серьезно возрастать. На это указывают, например, эксперименты М. М. Саверина 126], которыми уста новлено (при циклическом изгибе) значительное изменение эффек тивности дробеструйной обработки в зависимости от предше ствовавшей термической обработки для образцов из стали 45Х (табл. 4).
|
|
Таблица 4 |
Термическая обработка |
Твердость Н £ |
Увеличение предела |
выносливости при изгибе |
||
|
|
в «/о |
О т ж и г ............................................................ |
179 |
9 |
Нормализация ..................... |
207 |
10 |
Закалка 4- высокий о т п у с к ................. |
302 |
18 |
Закалка без отпуска .............................. |
522 |
48 |
Для поверхностной закалки, наоборот, следует ожидать сни жения эффективности при применении предварительной термо обработки, значительно увеличивающей прочность материала,
на что |
опять-таки |
указывают данные, полученные при цикли |
||
ческом |
изгибе. В |
опытах И. В. Кудрявцева и В. Н» Нови |
||
кова [16], |
например, увеличение |
предела выносливости норма |
||
лизованных |
гладких |
образцов из |
стали 40 в результате закалки |
и отпуска при 350° составило 42%, увеличение же предела выносли вости улучшенных образцов после идентичной обработки не пре высило 8%. При тонких слоях закалка может дать даже отрица тельный эффект в случае исходной термической обработки мате риала на высокую прочность. Это связано с отпуском сердцевины вблизи границы слоя и образованием в данном месте пика растя
гивающих остаточных |
напряжений. |
|
|
|
|
|
|
|
|||||
|
|
|
|
|
ЛИТЕРАТУРА |
|
|
|
|
|
|||
1. |
Б о ч в а р |
А. А. и Ж а д а е в а |
О. С., Известия АН |
СССР, |
отдел, |
||||||||
техн. наук, 1947, № 3. |
|
|
|
|
|
|
|
|
|
|
|||
2. |
Г л и к м а н Л. А. , С а н ф и р о в а Т. П. и С т е п а н о в В. А., |
||||||||||||
Журн. техн. физики, 1949, т. 19, стр. 327. |
В. А., |
Журнал техн. физики. |
|||||||||||
3. |
Г л и к м а н |
А. Л. |
и |
С т е п а н о в |
|||||||||
1946, т. 16, стр. 661. |
|
|
|
|
|
|
|
|
|
|
|
||
4. |
Г у л я е в |
А. П ., |
Металловедение, |
Оборонгиз, |
1949. |
|
УССР, |
||||||
5. |
Д а в и д е и |
к о в |
Н. Н ., |
Усталость |
металлов, |
изд-во АН |
|||||||
1949. |
|
|
|
|
|
|
|
|
|
|
|
|
|
6. |
Д а в и д е и |
к о в |
Н. |
Н ., |
Журн. |
техн. |
физики, |
1944, |
т. |
14, |
|||
стр. 507. |
|
|
|
|
|
|
|
|
|
|
|
|
|
7. |
З а й ц е в |
Н. Н ., |
«Авиационная |
промышленность», |
1941, |
№ |
19. |
||||||
8. |
К а р п е и к о Г. |
В., |
«Заводская |
лаборатория, |
1950, |
№ 8. |
|
|
185
9. |
К и д и н И. |
Н ., Термическая обработка стали при индукционном |
нагреве, |
Металлургиздат, |
1950. |
10. |
К и ш к и н С. Т., |
Известия АН СССР, отдел, техн. наук, 1946,. |
№12.
11.К и ш к и н С. Т. и П е т р у с е в и ч Р. Л., Известия АН СССР,
отдел, |
техн. наук, 1948, № 1. |
|
ЦНИИТМАШ, |
кн. |
40, |
Машгиз, |
1951. |
|||||||||||||||||
|
12. |
|
К о б р и н М. М., |
Труды |
||||||||||||||||||||
|
13. |
|
К о н т о р о в и ч И. Е. |
и |
Л и в ш и ц |
Л, С., |
Остаточные |
напря |
||||||||||||||||
жения |
в стали, Оборопгиз, 1943. |
|
|
|
|
|
кн. |
|
39, |
Машгиз, |
1950. |
|||||||||||||
|
14. |
|
К о с с о |
й М. С., |
Труды |
ЦНИИТМАШ, |
|
|
||||||||||||||||
|
15. |
|
К у д р я в ц е в |
И. В., |
Внутренние |
напряжения |
как резерв |
проч |
||||||||||||||||
ности в |
машиностроении, |
Машгиз, |
1951. |
|
|
|
|
Труды ЦНИИТМАШ, |
||||||||||||||||
кн. |
16. |
|
К у д р я в ц е в |
И. В. и Н о в и к о в В. Н ., |
||||||||||||||||||||
Ю, |
Машгиз, |
1947. |
|
|
|
и |
Н о в и к о в |
В. Н. «Вестник |
машино |
|||||||||||||||
|
17. |
|
К у Д р я в ц е в И. В. |
|||||||||||||||||||||
строения», |
1947, |
№ |
7. |
|
И. |
В., |
Са |
в е р и м |
М. |
М. |
|
и Р я б ч е н - |
||||||||||||
|
18. |
|
К у д р я в ц е в |
|
|
|||||||||||||||||||
к о в А. В., Методы поверхностного упрочнения детален |
машин, |
Машгиз, |
||||||||||||||||||||||
1949. |
|
К у л и к о в |
|
О. О., |
Труды |
ЦНИИТМАШ, |
кн. 40, |
Машгиз, |
1951. |
|||||||||||||||
|
19. |
|
|
|||||||||||||||||||||
|
20. |
|
К у л и к о в |
|
О. О., |
Труды ЦНИИТМА'Ш, |
кн. |
49, |
Машгиз, |
1952. |
||||||||||||||
|
21. |
|
О д и н г И. |
А. |
и Е ф р е м о в |
А. И ., |
«Вестник металлопромыш |
|||||||||||||||||
ленности», |
1931, |
№ |
|
10. |
|
Прочность и |
пластичность |
металлов, |
Оборопгиз, |
|||||||||||||||
|
22. |
|
Р а т н е р С. И., |
|||||||||||||||||||||
1949. |
|
|
|
|
|
|
|
|
|
|
|
|
|
|
|
|
|
|
|
|
|
|
|
|
|
23. |
Р е |
б и н д е р |
П. А., Юбилейный |
сборник |
АН |
СССР, |
1, |
1947. |
|||||||||||||||
стр. |
24. |
Р о в и н с к и й |
Б. |
М., |
Журн. |
техн. |
физики, |
1950, |
|
т. 20, |
||||||||||||||
1497. |
|
|
|
|
|
|
|
|
|
|
|
|
|
|
|
|
|
|
|
|
|
|||
|
25. |
|
Р я б ч е н к о в А. В., Труды |
ЦНИИТМАШ, |
|
кн. |
31, |
Машгиз, |
||||||||||||||||
1950. |
|
|
|
|
|
|
|
|
|
|
|
|
|
|
|
|
|
|
|
|
|
|
|
|
|
26. |
|
С а в ер |
и н М. М., |
Упрочнение машиностроительных деталей дро |
|||||||||||||||||||
беструйным наклепом, изд. ИТЭИН, 1948. |
|
|
|
|
|
|
1951, № |
2. |
||||||||||||||||
|
27. |
|
С а в е р и н |
М. М., «Вестник машиностроения», |
||||||||||||||||||||
|
28. |
С е р е н с е н С. В. и |
К о н т о р о в и ч |
И. Е ., Влияние |
азоти |
|||||||||||||||||||
рования на усталость конструкционной стали, Оборонгиз, 1947. |
|
Оборон |
||||||||||||||||||||||
гиз, |
29. |
Ф р и д м а н |
|
Я. Б ., Механические |
свойства |
|
металллов, |
|||||||||||||||||
1952. |
|
|
С. Г., |
Труды |
ЦНИИТМАШ, |
кн. |
43, |
Машгиз, |
1951. |
|||||||||||||||
|
30. |
|
Х е й ф е ц |
|||||||||||||||||||||
|
31. |
|
Ш л е й е р Э. В. и О д и и г И. А., |
«Вестник металлопромышлен |
||||||||||||||||||||
ности», |
|
1940, № |
7. |
|
|
|
|
Труды |
ЦНИИТМАШ, |
кн. |
24, |
Машгиз, |
1949. |
|||||||||||
|
32. |
Я Ц к е в и ч С. И ., |
||||||||||||||||||||||
|
33. |
A l m e n |
J. О ., |
Product |
Engineering, |
1950, |
№ |
11. |
|
of |
Metals, |
|||||||||||||
|
34. |
G o u g h |
and |
S o p |
w i t h , |
The Journal |
of the |
Institute |
||||||||||||||||
V. LVI, 1935, № 1. |
|
|
|
|
|
|
|
|
|
|
|
|
|
|
|
|
|
|
|
|||||
|
35. |
T h u m |
A. und |
В a u t z W., Forschung. a. d. Gebiete d. |
Ineenieur- |
|||||||||||||||||||
wesens, |
Bd 6, № 3, 1935, S. 121. |
|
|
|
|
|
|
|
|
|
|
|
* |
|
||||||||||
|
36. |
W i e g a n d |
|
H. |
und |
S c h e i n o s t |
R., |
Arch’iw |
fur |
das |
Eisenhiit- |
|||||||||||||
tenwesen, |
1939, |
Heft |
|
9. |
|
|
|
|
|
|
|
|
|
|
|
|
|
|
|
|
|
Б. ГГУРЕВИЧ, С. И. СИНДЛЕР u Е. В. ТРУНИНА
Д Р О Б Е С Т Р У Й Н Ы Й Н А К Л Е П Ц Е М Е Н Т О В А Н Н Ы Х Ш Е С Т Е РЕ Н 1
При работе нагруженных зубчатых передач наиболее часто встречаются два основных вида разрушения зубьев:
а) поломка зубьев, являющаяся наиболее опасным видом разру
шения, приводящим |
к выходу из строя всей зубчатой передачи; |
б) поверхностное |
выкрашивание, заключающееся в образова |
нии различной формы углублений — «ямок» на рабочих поверх ностях зубьев.
Поломка зубьев нередко вызывается усталостью металла и происходит из-за недостаточной прочности зубьев при перемен ных изгибающих напряжениях. Поломка зубьев может проис ходить также в тех случаях, когда зубья, подвергаясь воздей ствию больших ударных нагрузок, имеют недостаточную удар ную прочность.
Основные пути устранения поломки зубьев шестерен сводятся к применению различных конструктивных и технологических методов, повышающих как их статическую прочность, так и проч ность при переменных напряжениях (увеличение модуля зацеп
ления, |
применение |
легированных |
сталей, |
введение |
поверхност |
|||||||||
ного |
упрочнения |
зубьев, |
включая |
поверхности |
выкружек |
|||||||||
у корней, |
и |
т. п.). |
|
|
|
|
|
|
|
|
|
|
||
Распространенным дефектом в работе отдельных наиболее нагру |
||||||||||||||
женных зубчатых передач двигателей |
является поверхностное вы |
|||||||||||||
крашивание, сосредоточенное у ножки зуба. |
|
|
|
|||||||||||
Явления поверхностного выкрашивания на рабочей поверхности |
||||||||||||||
зубьев после сравнительно непродолжительной работы новой зуб |
||||||||||||||
чатой |
передачи |
довольно |
подробно |
исследованы Трубиным |
[1 ], |
|||||||||
Грозиным |
[2] |
и другими |
исследователями. |
|
|
|
|
|||||||
Различают два вида выкрашивания: |
|
выкрашивание, |
которое |
|||||||||||
1. |
|
Ограниченное, |
или |
начальное |
||||||||||
происходит |
в первые |
часы |
работы зубчатой передачи |
(момент |
||||||||||
приработки) |
и |
затем |
прекращается. |
Образовавшиеся |
в |
этом |
1 Работа проводилась заводом Министерства транспортного и тяжелого машиностроения совместно с ВНИИ этого же министерства. Режимы дро беструйного наклепа образцов и деталей разработаны и осуществлялись институтом.
187
случае углубления в дальнейшем либо не изменяются, либо постепенно заглаживаются.
2. Прогрессирующее выкрашивание, развивающееся по мере работы зубчатой передачи и приводящее к окончательной порче. поверхности зубьев за довольно короткий срок работы. Прогрес сирующее поверхностное разрушение зубьев вызывает искаже ние* профиля последних, что обусловливает появление дополни тельных ударных усилий в процессе работы передачи, в свою очередь способствующих большему разрушению поверхности зубьев. Выкрошившиеся частицы металла, попадая в смазку, ускоряют процесс износа трущихся поверхностей.
Работами ряда исследователей установлено, что выкрашива ние металла начинается в местах наибольших контактных напря жений и является следствием усталости поверхностного слоя металла.
Опыт работы ряда заводов показал, что даже при отсутствии прогрессирующего выкрашивания цементованные шестерни, на которых после первых часов приработки обнаруживается явле ние начального выкрашивания, как правило, заменяются новыми.
Попытки ликвидировать явление как начального, так и про грессирующего выкрашивания путем повышения твердости це ментованной поверхности зубьев до 60—62 единиц Роквелла за счет дополнительной обработки шестерен при отрицательных температурах (—100-г— 120°), а также внедрением гидрополирования, обеспечивающего получение более гладкой поверх ности зубьев по сравнению с пескоструйной поверхностью, положительных результатов не дали. Следует отметить, что кони ческие шестерни большей частью после цементации и термиче ской обработки подвергаются пескоструйной очистке и устана вливаются на передачи без дополнительной шлифовки зуба.
Исследованиями ряда авторов [1, 2, 3] установлено, что процесс поверхностного выкрашивания в значительной степени зависит от усталостной прочности и напряженности рабочей поверхности зубьев шестерен.
Цементация шестерен, широко применяемая в машиностро ении, значительно повышает их поверхностную твердость и сопротивление усталостным разрушениям. Однако, как показали исследования Гуревич и Юрьева [4], Мороза и Шуракова [5], в цементованном слое хромоникельвольфрамовой стали марки 18ХНВА, в силу его структурной неоднородности, могут воз никать внутренние растягивающие напряжения, которые сни жают эффективность поверхностного упрочнения.
Настоящая работа имела в виду выяснить возможность даль нейшего повышения усталостной прочности и сопротивления контактной усталости цементованных шестерен, изготовляемых из хромоникелевой и хромоникельвольфрамовой сталей марок 12ХНЗА и 18ХНВА, путем дополнительной обработки поверх ности зубьев дробеструйным наклепом.
188
Под действием дробеструйного наклепа в цементованном слое может произойти частичный распад имеющегося в нем остаточ ного аустенита, который сопровождается повышением твердости на некоторой глубине от поверхности и возникновением допол нительных сжимающих напряжений.
Появление более высоких напряжений сжатия в поверхностном слое цементованного зуба, по нашему мнению, помимо повыше ния общей усталостной прочности, должно было уменьшить вредное. действие растягивающих напряжений, ответственных за возникновение поверхностного выкрашивания, и тем самым ликвидировать это явление.
Вопросы применения комбинированного метода упрочнения поверхности деталей цементацией и дробеструйной обработкой мало исследованы и в технической литературе нашли недоста точное освещение.
В работе изучалось влияние дробеструйного наклепа на пре дел усталости цементованной стали марок 12ХНЗА и 18ХНВА; на чувствительность к надрезу цементованной стали марок 12ХНЗА и 18ХНВА и на характер явления ограниченного выкра шивания рабочей поверхности цементованных зубьев шестерен, изготовленных из стали 18ХНВА.
Методика и материал исследования
Изучение влияния комбинированного упрочнения цемента цией и дробеструйным наклепом на предел усталости стали марок 12ХНЗА и 18ХНВА производилось испытанием на усталость образцов диаметром 5,97 и 7,52 мм. Образцы готовились из прутков диаметром 20 мм, химический состав которых приведен в табл. 1.
Таблица I
Марка стали |
Углерод, |
Мар |
Крем |
Фос- |
|
Хром, |
Ни |
Воль |
Молиб |
°/о |
ганец, |
ний, |
«г |
|
°/о |
кель, |
фрам, |
ден, |
|
|
°/о |
°/о |
|
®|о |
®/о |
% |
|||
|
|
|
|
||||||
18ХНВА |
0,17 |
0,34 |
0,22 |
0,021 |
0,010 |
1,51 |
4,25 |
0,37 |
0,26 |
12ХНЗА |
0,14 |
0,41 |
0,21 |
0,019 |
0,022 |
0,72 |
3,06 |
- |
- |
Цементация усталостных образцов производилась в твердом карбюризаторе, содержащем от 10 до 12% углекислого бария. Температура цементации была принята равной 910—920°, а дли тельность выдержки при этой температуре определялась из рас чета получения цементованного слоя глубиною 0,5—0,6 мм. После цементации и медленного охлаждения в ящиках образцы
189
подвергались отпуску при температуре 630° в течение 3 часов и последующей окончательной термической обработке. Оконча
тельная |
термическая обработка |
состояла |
из |
закалки с темпера |
|||||||||
|
|
|
|
|
|
туры |
780—800° |
в |
масло |
||||
|
|
|
|
|
|
и |
отпуска |
при |
темпера |
||||
|
|
|
|
|
|
туре |
180—200° |
в |
течение |
||||
|
|
|
|
|
|
3 часов. |
образцов |
испы |
|||||
|
|
|
|
|
|
|
Часть |
||||||
|
|
|
|
|
|
тывалась |
на |
усталость |
|||||
|
|
|
|
|
|
после |
окончательной тер |
||||||
|
|
|
|
|
т |
мической |
обработки |
(за |
|||||
|
|
п . |
f Д |
■ 1 |
калки и низкого |
отпуска), |
|||||||
|
|
а |
остальные |
образцы ис |
|||||||||
|
|
|
|||||||||||
- |
*0 |
|
|
пытывались |
после |
допол- |
|||||||
|
|
--------- 150--------------- ------------11------------* |
нительного дробестру йиого |
||||||||||
Фиг. |
1. |
Образцы |
для испытания на |
уста |
наклепа. |
|
|
|
|
|
|||
|
|
|
лость: |
|
|
|
Усталостные испытания |
||||||
|
|
|
|
|
|
осуществлялись |
|
на |
ма |
||||
|
|
|
|
|
|
шине, |
воспроизводящей |
изгиб вращающегося образца при симметричном цикле напря жений. Эскиз усталостного образца приведен на фиг. 1.
Фиг. 2. Изменение твердости по |
Фиг. 3. Изменение твердости по |
глубине цементованного слоя стали |
глубине цементованного слоя стали |
18ХНВА. |
12ХНЗА. |
Твердость цементованного слоя по глубине, замеренная на специальных образцах (косых шлифах), проходивших цемента цию и последующую термическую обработку вместе с усталост ными образцами, приведена на фиг. 2 и 3. Микроструктура цементованного слоя приведена на фиг. 4.
190