
книги / Некоторые вопросы усталостной прочности стали
..pdf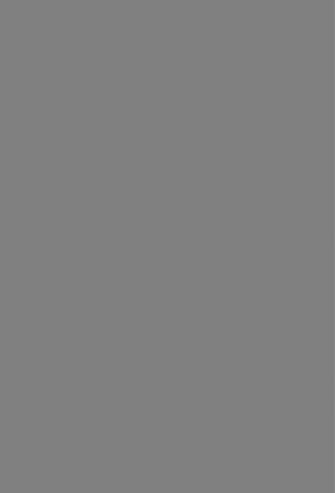
• Дробеструйный наклеп усталостных образцов производился на установке механического типа, , общий вид которой приведен на фиг. 5. Поверхность образцов обдувалась чугунной дробью
диаметром |
0,6—0,8 мм |
при скорости вращения ротора 65— |
70 м/сек. |
Длительность |
обдувки дробью составляла 4 минуты |
при расходе дроби 20—25 кг/мин.
Образцы, подлежащие дробеструйному наклепу, закрепля лись в специальных центрах и в течение всего времени обдувки вращались со скоростью 15 об/мин. Головки усталостных образ цов защищались от наклепа дробью специальными колпачками.
Испытания на усталость гладких образцов
Результаты испытания на усталость гладких цементованных образцов из исследованных сталей с дробеструйным наклепом и без него приведены на фиг. 6 и 7. Приведенные кривые показы-
110
!
106 |
|
|
100 |
|
|
|
|
|
|
|
|
юг к |
|
|
|
|
|
|
|
|
|
||
01,= %кг/1гм* |
| * |
|
г |
|
|
|
|
|
|
||
|
\ |
|
|
|
|
|
|
|
|||
| 98 |
|
X |
|
о., = 91%5кг(ммг |
|||||||
|
|
|
|
|
|||||||
S>90 |
|
|
§ 88 |
0 |
|
|
|
-8 с |
|||
$86 |
|
|
П |
|
|
|
|
|
|
|
|
1П |
|
|
( * |
|
|
|
|
|
|
|
|
|*2 |
|
|
|
|
|
|
|
|
|
||
П |
|
01,= 78кг/шг |
|
к |
|
|
|
|
|
|
|
*7* L . |
|
|
|
|
|
|
а ., = 7Ь кг/мд |
|
|||
70 |
|
|
|
|
ю6 |
г.юе н о 6 |
<ио6 |
5 ю6 |
|||
|
|
|
|
|
|||||||
|
Числа перемен нагрузки |
|
|
Число перемен нагрузки |
|
||||||
Фиг. |
6. |
Влияние дробеструйного |
Фиг. |
7. |
Влияние |
дробеструйного |
|||||
наклепа |
на предел усталости |
наклепа |
на |
предел |
усталости глад |
||||||
гладких |
цементованных образцов |
ких |
цементованных |
образцов |
из |
||||||
из стали |
18ХНВА (глубина це |
стали |
12ХНЗА |
(глубина |
цементо |
||||||
ментованного слоя 0,5 мм)‘. |
|
ванного |
слоя |
0,6 |
мм)\ |
|
|||||
|
|
|
I — с дробеструйным наклепом; |
I I |
—без |
||||||
|
|
|
|
|
|
наклепа. |
|
|
|
вают, что дробеструйный наклеп значительно повышает абсолют
ные значения предела |
усталости обеих сталей (с 75—78 до |
95—96 кг/мм2) и наряду |
с. этим снижает чувствительность цемен |
тованной стали к циклическим перегрузкам, о чем свидетель ствует резкое изменение левой части усталостной кривой.
Рассмотрение |
изломов цементованных |
усталостных |
образцов |
с поверхностным |
наклепом и без него |
указывает на |
то, что |
192
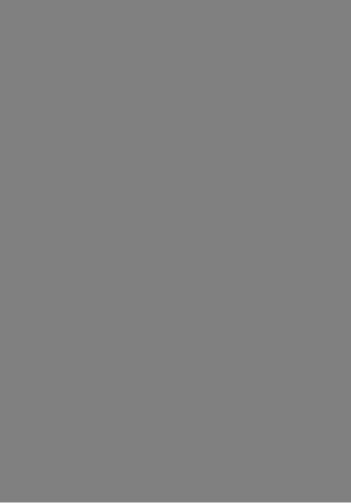
растягивающих напряжений находится в самом цементованном слое. Поэтому разрушение гладких цементованных образцов начи нается вблизи поверхности в цемен
|
96 |
|
|
’95кг/мм2 |
тованном слое, чем и объясняется высо |
|||||||||||
|
|
|
t l |
кая чувствительность |
к |
циклическим |
||||||||||
|
92 |
|
|
перегрузкам, |
характеризуемая |
резким |
||||||||||
|
88 |
|
|
|
перегибом |
усталостной кривой. |
|
|||||||||
|
8* |
|
|
|
|
Дробеструйный |
наклеп |
цементован |
||||||||
|
|
|
|
ной поверхности |
смещает зону |
макси |
||||||||||
s. 80 |
|
|
|
|||||||||||||
|
M M |
мальных |
растягивающих |
напряжений |
||||||||||||
|
|
|
78 / |
|||||||||||||
1 |
76 |
|
|
|
в |
подслойную |
область |
(сердцевину), |
||||||||
^a П |
|
|
|
которая, |
|
обладая |
значительно |
боль |
||||||||
|
|
|
шими |
пластическими |
свойствами, обу |
|||||||||||
s a |
|
|
|
словливает |
меньшую |
чувствительность |
||||||||||
s |
|
■62,5кг/им |
||||||||||||||
g & |
|
|
|
к циклическим |
перегрузкам. |
Меньшая |
||||||||||
|
|
|
|
|
чувствительность |
к циклическим пере |
||||||||||
|
|
Ей |
|
грузкам проявляется в виде более |
||||||||||||
|
|
|
пологой |
усталостной |
кривой. |
|
|
|||||||||
|
|
|
|
На фиг. |
10 в виде диаграммы приве |
|||||||||||
|
|
|
дена |
зависимость |
предела |
усталости |
||||||||||
Фиг. 10. |
Изменение пре |
гладких |
образцов |
из |
стали |
18ХНВА |
||||||||||
дела усталости гладких об |
от характера поверхностного |
упрочне |
||||||||||||||
разцов из |
стали 18ХНВА |
ния. Из этой диаграммы следует, что |
||||||||||||||
в зависимости от вида по |
наибольшее |
значение |
предела |
устало |
||||||||||||
верхностного |
упрочнения: |
сти обнаруживают |
образцы, подвергну |
|||||||||||||
1 — термическая |
обработка; |
|||||||||||||||
2 — термическая |
обработка н |
тые |
комбинированному |
поверхност |
||||||||||||
наклеп дробью; 3 — цементация |
ному |
упрочнению |
цементацией |
и дро |
||||||||||||
и |
термическая |
обработка; |
||||||||||||||
4 — цементация, |
термическая |
беструйному |
наклепу. |
|
|
|
|
|||||||||
обработка |
и наклеп дробью. |
|
|
|
|
|||||||||||
|
|
Испытания на усталость надрезанных образцов |
|
|||||||||||||
|
Влияние |
дробеструйного |
наклепа |
цементованной |
поверхности |
на чувствительность к надрезу определялось испытанием круглых образцов с кольцевыми надрезами двух типов. Одна серия образ цов имела кольцевой надрез глубиной 0,6 мм с радиусом у дна надреза 0,8 мм, при диаметре образца в месте надреза 5,97 мм. Этот надрез характеризовался теоретическим коэффициентом кон центрации а к = 1,54. Другая серия образцов имела более острый кольцевой надрез глубиной 0,8 мм с радиусом у дна надреза 0,3 мм и диаметром в надрезе 7,52 мм. Параметры этого надреза обусловливали концентрацию напряжений, характеризуемую тео ретическим коэффициентом а к = 2,65. Кольцевые надрезы нано сились на образцы до цементации. Эскизы образцов с надрезами приведены на фиг. 1. Цементация, последующая термическая обработка и дробеструйный наклеп производились одновременно
С гладкими |
образцами. |
условиях, что |
Образцы |
с надрезом испытывались в тех же |
|
и гладкие |
цементованные образцы. Результаты |
усталостных |
194
|
88 |
I е |
ч ~ г |
~ |
|
|
84 |
||||
|
80 |
|
б.,= 79кг/ммг |
||
|
|
|
|
|
|
\ |
76 |
|
|
|
|
I |
72 |
|
|
|
|
| |
68 |
|
|
|
|
|б 4 |
|
|
|
|
|
§- |
|
|
|
|
|
gfffl |
|
|
|
|
|
|
56 |
|
а-,= |
51,5к |
/ ш ‘ |
|
52 |
к |
|
! |
|
|
|
|
к |
||
|
|
|
|
|
48
НО6 3.10е 4.10е 5.10е N Числоперемен нагрузки
Фиг. 11. Влияние дробеструйного наклепа на предел усталости образцов из стали 18ХНВА с «мягким» надрезом (ак = 1.54):
|
- без |
I , |
<7_,==58,5л2 /Ш 2 |
|
?5 8
«о
8? 52
р
I"
^40 ' л
ач =36нг/U 2
36 Ч
321 ■
О10е 2.10е 3.10е 4.10е 5.10е N
Число перемен нагрузки
Фиг. 13. Влияние дробеструйного наклепа на предел усталости образцов из стали 18ХНВА с «острым» надрезом (ак = 2,65):
/ — с дробеструйным наклепом; / / — без наклепа.
I
| |
82 |
|
g->= 12,6л 'JmK |
^7* |
|
|
|
178 |
|
|
|
| |
66 |
|
|
| |
« |
|
|
|
58 |
и |
52J5i г/т г |
|
54 |
|
|
|
50 |
111- |
6.1U~ 0.10" ЧИЦ" оли~ N |
|
ti |
Число перемен нагрузки
Фиг. 12. Влияние дробеструй- ' ного наклепа на предел уста лости образцов из стали 12ХНЗА с «мягким» надрезом («к = 1.54):
/— с дробеструйным II — без наклс
62
а_ =57т/1шг
~ 58 ^5 4
I»
§%
$42
<а
itr.}=: 4кг/ш 2
■
30
"О Юе 2.10е 3.10е 4.10е 5.10е О Число перемен нагрузки
Фиг. 14. Влияние дробеструйного наклепа на предел усталости образцов из стали 12ХНЗА с «острым» надрезом («к = 2,65):
195
испытаний надрезанных цементованных образцов из обеих иссле дованных марок стали с дробеструйным наклепом и без пего приведены на фиг. 11—14. Из приведенных кривых следует, что обдувка дробью цементованной поверхности образцов из стали
18ХНВА и 12ХНЗА, имеющих более мягкий надрез, |
характери |
||||
зуемый коэффициентом |
а к = |
1,54, практически полностью устра |
|||
няет вредное действие |
надреза. Абсолютное значение предела |
||||
60 |
П, = 58,5щ*ш2 |
усталости |
цементованных образ |
||
|
|
цов с таким |
надрезом, |
подвергну |
|
55 |
|
|
тых дробеструйному наклепу, ока |
||
50 |
|
|
зывается равным (сталь 18ХНВА) |
||
- « |
|
|
или даже |
несколько |
большим |
|
|
(сталь 12ХНЗА), чем предел уста |
ч.1*38нгАш‘- лости гладких цементованных
£35 о_,-ЗЗнг/шл/и и г^ -Ч.— образцов без дробеструйного наI 40
'l 30 |
|
|
|
|
|
|
клепа. |
|
|
дробью |
цементован |
|||||
I 25 =Ь±Г |
|
|
|
Обдувка |
||||||||||||
|
|
|
ных образцов |
с более |
глубоким |
|||||||||||
|
|
|
|
|
|
|
надрезом, |
характеризуемым |
тео |
|||||||
^ 1 5 \— |
|
|
|
|
|
ретическим |
коэффициентом |
кон |
||||||||
10 |
|
|
|
|
|
|
центрации |
а к |
= 2,65, |
хотя |
и не |
|||||
|
|
|
|
|
|
|
снимает полностью вредного |
дей |
||||||||
|
|
|
|
|
|
|
ствия |
надреза, |
но |
тем |
не |
|
менее |
|||
|
|
|
|
|
|
|
резко |
снижает |
чувствительность |
|||||||
Фиг. |
15. |
Изменение |
из |
предела |
к такой |
концентрации |
напряже |
|||||||||
усталости |
образцов |
стали |
ний, повышая |
абсолютное |
значе |
|||||||||||
18ХНВА |
с «острым» |
надрезом |
ние предела |
усталости |
по |
|
срав |
|||||||||
(ак= 2 ,6 5 ) |
в зависимости |
от вида |
нению |
с |
цементованными |
образ |
||||||||||
поверхностного упрочнения: |
цами, имеющими такой же надрез, |
|||||||||||||||
1 — термическая |
обработка; |
2 — тер |
||||||||||||||
на 60%. |
Дробеструйный |
наклеп |
||||||||||||||
мическая обработка |
и наклеп дробью: |
|||||||||||||||
3 — цементация |
и |
термическая обра |
цементованной поверхности с над |
|||||||||||||
ботка; |
4 — цементация, |
термическая |
||||||||||||||
обработка и наклеп дробью. |
резом |
этого |
типа заметно |
умень |
||||||||||||
грузкам, |
на |
что указывает |
шает чувствительность к пере- |
|||||||||||||
изменеиие |
характера |
усталостной |
кривой и резкое увеличение области ограниченной выносливости.
На фиг. 15 в виде диаграммы приведеноизменение предела усталости образцов из стали 18ХНВА с глубоким надрезом в зави симости от вида поверхностного упрочнения. Из этой диаграммы видно, что комбинированное упрочнение поверхности надрезан ных образцов цементацией и дробеструйным наклепом обусло
вливает наименьшую чувствительность к концентрации |
напряже |
|||||
ний, создаваемой надрезами принятых параметров. |
|
|
|
|||
Эффективный |
коэффициент |
концентрации |
( kf = —1-1 |
) |
||
цементованных и |
наклепанных |
|
\ |
' |
снадр |
/ |
дробью образцов |
с |
надрезом |
||||
(а к = 1,54), будучи отнесен к пределу усталости |
гладких цемен |
|||||
тованных образцов |
без наклепа, |
оказывается меньшим |
единицы, |
1 9 $
а коэффициент чувствительности к надрезу TJ = 100^1—
при этом получает отрицательный знак.
Это обстоятельство указывает на то, что дробеструйный наклеп
цементованной |
поверхности |
при |
надрезе, |
характеризуемом |
||
а к = 1,54, полностью |
снимает его |
вредное действие. При |
более |
|||
глубоком надрезе (а к |
= 2,65) дробеструйный |
наклеп уменьшает |
||||
эффективный |
коэффициент |
концентрации и |
коэффициент |
чув |
ствительности к надрезу почти в два раза.
Испытания шестерен с комбинированным упрочнением зубьев
Для проверки эффективности дополнительного дробеструй ного наклепа цементованной поверхности зубьев нагруженных шестерен как в отношении предотвращения образования поверх
ностного выкрашивания, |
так |
и в отноше |
|
|
||||||
нии повышения их общей прочности, пар |
|
|
||||||||
тия ведущих конических шестерен трех |
|
|
||||||||
■наименований из трех разных передач |
|
|
||||||||
была |
подвергнута дробеструйному |
на |
|
|
||||||
клепу и установлена на двигатель для |
|
|
||||||||
прохождения |
длительных |
стендовых ис |
|
|
||||||
пытаний. |
Выбранные |
шестерни |
были |
|
|
|||||
наиболее |
подвержены |
явлению поверхно |
|
|
||||||
стного |
выкрашивания. |
|
|
|
|
|
|
|
||
Дробеструйному наклепу подвергались |
|
|
||||||||
окончательно |
изготовленные |
шестерни. |
|
|
||||||
Наклеп |
осуществлялся |
на |
дробеметной |
Фиг. 16. Схема располо |
||||||
установке ВНИИ транспортного машино |
жения шестерен |
в дро |
||||||||
строения |
чугунной |
дробью |
диаметром |
бемете: |
|
|||||
0,8—1,0 мм при скорости вращения ротора |
1 — дробемет; 2 —шестерня; |
|||||||||
3 — границы потока |
дроби; |
|||||||||
65—70 м/сек. Расход дроби при обра |
4 — промежуточное |
кольцо. |
||||||||
ботке |
шестерен составлял 40—45 кг/мин. |
|
|
Шестерни закреплялись на специальном валике и в процессе наклепа вращались со скоростью 15 об/мин. Расстояние от образующей ротора до упрочняемой поверхности зубьев соста вляло 300 мм. Схема расположения шестерен в дробемете приведена на фиг. 16. Посадочные поверхности шестерен (шлицы, втулки и др.) изолировались от дробеструйного наклепа путем применения специальных приспособлений и резиновых прокла док. После дробеструйного наклепа шестерни проверялись по ■всем параметрам, предусмотренным чертежом (биение зубьев по окружности начального конуса, прилегание по краске зубьев в зацеплении с сопряженной эталонной шестерней, толщина зуба по зубомеру и др.).
Результаты обмера партии шестерен в количестве 50 шт. показали, что дробеструйный наклеп практически не вызывает изменения этих параметров. Поверхность зубьев после наклепа
197
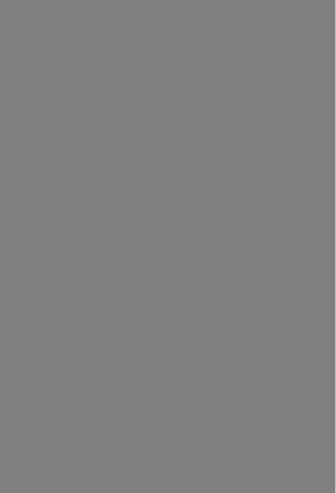
резу. Так, предел усталости, определенный испытанием образцов с надрезом (а к = 1,54), упрочненных комбинированным методом (цементацией и Дробеструйным наклепом), оказывается равным или даже более высоким, чем предел усталости гладких цементо ванных образцов без дополнительного наклепа дробью.
4. Дробеструйный наклеп цементованной поверхности зубьев шестерен из стали 18ХНВА наряду с повышением общей проч ности резко уменьшает явление начального выкрашивания рабо чей поверхности, наблюдаемое в процессе приработки зубчатой передачи.
|
|
|
ЛИТЕРАТУРА |
|
|
|
|
1. |
Т р у б и н |
Г. К., |
Контактная |
усталость |
зубьев |
прямозубых |
ше |
стерен, |
ЦНИИ'ГМАШ, кн. 37, Машгиз, 1950. |
и пластические деформа |
|||||
2. |
Г р о з н а |
Б. Д . Образование |
питтинга |
||||
ции метастабнльных структур стали, |
сборн. сТрение и |
износ в машинах», |
|||||
АН СССР, 1947. |
|
П. И., Исследование |
образования питтинга |
на |
|||
3. С о к о л о в с к и й |
|||||||
тяговых зубчатых передачах, М. МЭИТ, 1947. |
|
|
|
||||
4. |
Г у р е в и ч |
Б. Г. и Ю р ь е в |
С. Ф., О рели остаточных напряже |
ний в повышении предела выносливости стали при химико-термической обра ботке, сборн. «Повышение прочности деталей машин поверхностной обработ
кой», Машгиз, |
1952. |
|
5. |
М о р о з |
Л. С. и Ш у р а к о в С. С., Проблема прочности цементо |
ванной |
стали, |
Судпромгиз, 1947. |
Б. Ф. БАЛАШОВ
ПОВЫШЕНИЕ ПРОЧНОСТИ ДЕТАЛЕЙ ПУТЕМ АЗОТИРОВАНИЯ В СВЯЗИ С НАПРЯЖЕННЫМ СОСТОЯНИЕМ
И СВОЙСТВАМИ СЛОЯ
Введение
Изучению влияния азотирования на усталость различных сталей посвящен ряд работ советских и иностранных авторов. Во всех работах ставились задачи определения эффективности повышения прочности применительно к машиностроительным
сортам сталей при наличии концентрации |
напряжений, |
а также |
в зависимости от параметров слоя: его |
твердости и |
глубины. |
В большинстве случаев предлагавшиеся различные рекомендации по этим вопросам носят качественный характер.
Влияние параметров слоя на прочность исследовалось на глад ких лабораторных образцах диаметром до 10 мм. Почти всеми исследователями отмечено, что повышение предела усталости находится в прямой зависимости от глубины насыщения и проч ности сердцевины и мало зависит от твердости азотированного слоя.
Изучение конструктивной прочности на лабораторных образ цах является недостаточным, так как на этих образцах трудно выдержать соотношения размеров, встречающиеся в конструк циях; во-вторых, большая кривизна сопрягаемых поверхностей обусловливает повышенные градиенты напряжений и создает отличные от реальных деталей условия формирования слоя. Эти причины приводят к тому, что эффективность повышения проч ности от азотирования на лабораторных образцах, имеющих кон центрацию напряжений, оказывается сильно завышенной, дости гающей сотен процентов. Поэтому изучение конструктивной прочности применительно к деталям следует проводить на круп ных моделях или самих деталях.
Часто исследователи для характеристики прочности деталей, подвергающихся поверхностным обработкам, пользуются мел кими надрезами глубиной от 0,1 до 0,4 мм. Такие надрезы даже на крупных моделях не могут характеризовать чувствительности к концентрации напряжений по причинам, отмеченным выше.
200