
книги / Некоторые вопросы усталостной прочности стали
..pdfСтруктура переходной зоны состоит из мартенсита и мелких
включений феррита (фиг. 11). |
параметрах |
слоя, |
полученные на |
|
Данные о геометрических |
||||
основании микроанализа, представлены в табл. |
4. |
Таблица 4 |
||
|
|
|
|
|
|
|
№ серии |
|
|
|
1 |
2 |
3 |
4 |
Толщина мартенситной зоны в мм |
0,65 |
1,0 |
1.6 |
3,76 |
Толщина переходной зоны в мм |
0,15 |
0,25 |
0,30 |
— |
Отношение площади мартенсит |
|
|
|
|
ной зоны к площади закаленного |
|
|
|
|
слоя а ..................................................... |
0,823 |
0,814 |
0,860 |
- |
При определении параметров слоя за толщину мартенситной зоны принималось расстояние до появления первых участков феррита. Внутренней границей переходной зоны считалось место
окончания |
мартенситных |
уча |
|
|
|
||
стков. |
|
|
|
|
|
|
|
Из приведенных данных сле |
|
|
|
||||
дует, что с увеличением глу |
|
|
|
||||
бины |
закалки |
увеличивается |
|
|
|
||
и ширина |
переходной |
зоны; |
|
|
|
||
однако, на всех режимах вы |
|
|
|
||||
сокая скорость нагрева и пра |
|
|
|
||||
вильный подбор частоты |
тока |
|
|
|
|||
обеспечили |
получение доста |
|
|
|
|||
точно |
высоких |
значений |
пара |
|
|
|
|
метра |
ос. |
|
|
|
|
|
|
Исследование распределения |
|
|
|
||||
твердости по сечению произво |
|
|
|
||||
дилось при помощи микротвер |
|
|
|
||||
домера типа ПМТ-3 при на |
|
|
|
||||
грузке 200 г на поперечном |
|
|
|
||||
срезе образца. Замеры произво |
|
|
|
||||
дились через каждые 0,05 мм. |
Фиг. 12. |
Зависимость |
изменения |
||||
Специально проведенными опы |
твердости'от глубины образцов для |
||||||
тами |
было |
установлено, |
что |
различной |
толщины |
закаленного |
|
|
слоя. |
|
|||||
получающиеся |
при выбранной |
|
|
|
нагрузке значения твердости являются среднестатистическими значениями, соответствующими твердости по Викерсу. Этот вывод был подтвержден также и в данной работе при проведен ном сравнении результатов замера на приборе ПМТ-3 с резуль татами замеров на приборе Викерса.
61
Поверхностная твердость определялась на приборе Роквелла. Величина поверхностной твердости после индукционной закалки находилась в пределах Нрс = 59—61 для всех серий образцов.
Полученная при индукционной закалке твердость превышает твердость, получаемую при обычной закалке, на 3—4 еди ницы Нрс . Повышение температуры закалки до 915° не привело
к снижению твердости.
После отпуска поверхностная твердость понизилась до НРс = 56 -58 .
Кривые изменения твердости по глубине образцов предста влены на фиг. 12. Из приведенных графиков видно, что до некото рой глубины твердость закаленного слоя сохраняется постоян ной, затем наблюдается ее снижение до твердости сердцевины. Уменьшения твердости в переходной зоне в наших опытах не наблюдалось, что можно объяснить кратковременностью нагрева.
При сквозной закалке максимальная твердость сохраняется' в значительной части закаленного слоя.
Исследование остаточных напряжений
Исследованию подвергались осевые остаточные напряжения. Удалениеслоев производилось методом травления. Выбор данного метода определялся его простотой, а также желанием исключить влияние механического воздействия на удаляемый слой, неиз бежного при механическом методе определения напряжений.
Для исследования из рабочей части образца, имеющей диаметр 7,52 мм, вырезался цилиндр длиной около 80 мм, который под вергался стравливанию с поверхности. При этом замерялось изменение его длины. Вычисление величины остаточных напря жений производилось по упрощенной формуле1:
|
«*= [/И4- |
4) - /*-, (h -i |
- |
k )] ~ |
, |
|
||
где /0 — начальная |
высота |
цилиндра |
(т. е. длина |
образца); |
||||
fk — площадь сечения |
цилиндра после удаления |
k-то слоя; |
||||||
lk — высота цилиндра |
после удаления |
k-то слоя; |
|
|||||
Sk — площадь |
сечения |
k-ro слоя; |
|
|
|
|
||
Е |
— модуль нормальной |
упругости |
(принимался равным |
|||||
|
2, 1- 10® кг/см2). |
|
|
|
|
|
|
|
Графики распределения |
остаточных |
напряжений |
приведены |
|||||
на фиг. 13—16. |
|
|
|
|
|
|
|
|
Из |
приводимых |
графиков |
следует, |
что при |
поверхностной |
закалке значительные сжимающие напряжения (в нашем случае 40—50 кг/мм2) в поверхностных слоях сохраняются лишь в пре делах определенной глубины закалки; дальнейшее же увеличение
1 В предположении одноосного напряженного .состояния.
62
Фиг. 13. Остаточные напряжения |
Фиг. 14. Остаточные напряжения |
при глубине слоя 0,8 мм. |
при глубине слоя 1,2 мм. |
Фиг. 15. |
Остаточные |
напряжения |
Фиг. |
16. Остаточные напряже |
при |
глубине слоя |
1,8 мм. |
ния |
при сквозной закалке. |
глубины закаленного слоя приводит к возникновению растя гивающих напряжении в поверхностных слоях, которые при сквозной закалке достигают 20 кг/мм". Значительных растя гивающих напряжений в переходной зоне в нашем случае не наблюдалось.
Наибольшие растягивающие напряжения в пределах иссле дованных слоев (исследование производилось при стравлива нии на глубину 2 мм от поверхности) наблюдаются при малой глубине закалки (0,8 мм) на расстоянии 2 мм от поверхности и составляют 30—32 кг!мм"-.
Испытания на усталость
Испытания на усталость производились по методике, рекомен дованной ГОСТ 2860—45. Назначение нагрузок производилось по методу Бахарева [21J на основе свойств закаленного слоя. Для сравнения были произведены испытания также пятой серии образцов, изготовленных из исследуемой стали и подверг нутых обычной закалке и от пуску при 600° в течение 2 час.
(режим, соответствующий пред варительной термической обра ботке индукциоино закаленных образцов).
Фиг. 17. Кривые усталости иссле |
Фиг. |
18. |
Зависимость |
предела |
||
дованных |
образцов. |
усталости |
от глубины |
закалки. |
||
Результаты |
испытаний представлены |
в табл. 5 и |
на фиг. 17 |
|||
и 18. |
|
|
|
|
|
|
Как видно из приведенных |
в табл. |
5 данных, |
проведенные |
эксперименты |
полностью подтверждают высказанную нами точку |
|||
зрения о возможности значительного повышения |
усталостной |
|||
прочности^ при |
индукционной закалке стали |
45 по |
сравнению |
|
с обычной закалкой и высоким отпуском. |
Полученное |
нами |
||
максимальное |
значение предела усталости |
= |
78 |
кг!мм% |
64
|
|
|
|
|
|
|
|
|
Таблица 5 |
|
|
|
|
|
|
|
№ серии |
|
|
|
|
|
|
|
1 |
2 |
3 |
4 |
5 |
Глубина |
слоя |
в мм |
0.8 |
1,2 |
1.8 |
Сквозная |
|
||
Отношение |
площади |
|
|
|
закалка |
|
|||
|
|
|
|
|
|||||
слоя |
к площади сердце |
|
|
|
|
|
|||
вины |
р .............................. |
|
|
• |
0,62 |
1,15 |
2,65 |
|
|
Предел |
усталости |
|
|
|
|
|
|||
п к г/м м * .......................... |
|
|
|
04,0 |
78,0 |
70,0 |
68,0 |
44,0 |
|
Повышение |
предела |
|
|
|
|
|
|||
усталости но сравнению |
|
|
|
|
|
||||
с обычной |
закалкой |
и |
|
|
|
|
|
||
высоким отпуском В |
°/о |
146 |
178 |
173 |
155 |
100 |
существенно превосходит наибольшее из полученных в работах других исследователей, равное 57,5 /сг/лш2 [4]. Разница в полу ченных нами значениях по сравнению с упоминаемой работой может быть лишь частично отнесена за счет различного (18 мм против 7,52 мм) диаметра и соответствующего влияния масштаб ного эффекта.
Полученные в настоящей работе результаты с нашей точки зрения не являются предельными. Не исключена возможность получения и более высоких свойств за счет подбора режимов нагрева, а также за счет различной предварительной термиче ской обработки.
Выводы
1. В результате проделанной работы экспериментально под тверждено мнение о том, что относительно дешевый материал, каким является углеродистая сталь, простым, доступным и эко
номически выгодным способом может быть |
переведен |
в раз |
ряд высокопрочных материалов, причем |
повышение |
проч |
ности составляет десятки процентов. Этот вывод особенно важен для ответственного (авиационного и др.) машиностроения, для которого повышение показателей на несколько процентов уже имеет существенное значение.
2. Полученные результаты подтверждают приводимые в дру гих работах данные об оптимальных параметрах слоя, а также вывод о том, что изменение глубины слоя в широких пределах (в нашей работе при р = 1,15—2,65) не приводит к существен ному снижению усталостной прочности и, следовательно, дает возможность назначения более широких допусков на глубину закаленного слоя.
5 Сборник зак. 747 |
65 |
3. Результаты определения.остаточных напряжений, проведен ного в настоящей работе, подтверждают мнение о существенном влиянии остаточных напряжений на усталостную прочность стали при индукционной закалке. В тех случаях, когда поверх ностные слои находятся под воздействием сжимающих напря жений, усталостная прочность повышается.
ЛИТЕРАТУРА
1.В о л о г д и II В. П., Поверхностная индукционная закалка, Обо-
ронгнз, 1947.
2. |
Л о з и н с к и й |
М. Г., Поверхностная закалка н индукционный |
||||||||
нагрев |
стали, |
Машгнз, |
1949. |
|
|
|
|
|
||
3. |
К и л и |
и И. Н ., |
Термическая обработка стали при индукционном |
|||||||
нагреве, Металлургнздат, |
1950. |
|
|
|
прочность |
|||||
4. |
К о с с о й М, С., Остаточные напряжения и циклическая |
|||||||||
конструкционной |
стали |
|
при |
поверхностной |
закалке, |
ЦНИИТМАШ, |
||||
1950, |
кн. 39. |
|
|
|
|
|
|
|
|
и оста |
5. |
Н е й ш у л е р Е. А., Выносливость конструкционной стали |
|||||||||
точные напряжения |
при |
поверхностной индукционной закалке, |
1941. |
|||||||
6. |
К у д р я в ц е в |
И. |
В. |
и Н о в и к о в |
В. Н ., Исследование проч |
|||||
ности |
поверхностно |
закаленной |
стали, ЦНИИТМАШ, 1947, |
ки. |
10. |
|
||||
7. |
К у д р я в ц е в |
И. |
В. |
и Н о в и к о в |
В. Н ., Влияние |
поверх |
ностной закалки токами высокой частоты и цементации на усталостную
прочность стали, ЦНИИТМАШ, |
1947, кн. 10. |
8. М е щ а н и н о в а Г. П., |
Остаточные напряжения в связи с упроч |
няющей поверхностной обработкой, сборн. «Динамика и прочность авиадви
гателей», Оборонгиз, 1949, № 3. |
усталостной |
прочности |
конструк |
|||||
9. Г у р е в и ч |
Б. Г., |
Повышение |
||||||
ционной |
стали цементацией |
и азотированием, 1949. |
Влияние поверх |
|||||
10. |
К а р е л и н а А. Г. |
и М и р о л ю б о в И. Н., |
||||||
ностной |
закалки |
стали |
на |
предел |
усталости, |
Жури- |
техн. |
физики, |
1937, вып. 5.
11.С а д о в с к и й В. Д ., Влияние скорости нагрева при электро термообработке на структуру и свойства стали, ЛОНИТОМАШ, вып. 12. Машгиз, 1949.
12.М о р о з Л. С. и Ш у р а к о в С. С., Проблема прочности цемен тованной стали, Судпромгиз, 1947.
13. М а л ы ш е в К. А. и П а в л о в В. А., Особенности фазовых пре вращений при электронагреве, Труды Института физики металлов, УФАН,
1946, вып. 9. |
|
|
|
|
|
14. |
М а л ы ш е в К- А. |
и П а в л о в |
В. А ., Влияние |
электронагрева |
|
при закалке на структуру и |
механические |
свойства стали |
марок |
48Х и |
|
43XH3M, УФАН, 1946, вып. 9. |
|
|
|
||
15. |
К о н т о р о в и ч И. Е. и Л и в ш и ц Л. С., Остаточные |
напря |
|||
жения |
в стали, Оборонгиз, |
1943. |
|
|
|
16.В е й н ш т о к А. М ., Разработка оптимальных режимов поверх ностной закалки токами высокой частоты деталей авиамотора, НИАТ, 1948.
17.Г а р д и н А. И ., Поверхностная закалка током высокой частоты, Металлург, 1938, № 3.
18. В е й и ш т о к А. М., Исследование влияния поверхностной за калки токами высокой частоты на усталостную прочность стали, НИАТ, 1947.
19.В е й н ш т о к А. М ., Влияние мощности, частоты и глубины зака ленного слоя на усталостную прочность стали при обработке токами высокой частоты, НИАТ, 1947.
20.Г о л о в и и Г. Ф., Превращения в стали при больших скоростях нагрева токами высокой частоты, 1949.
66
21. Б а х а р е в В. М., |
Назначение нагрузок при испытании на уста |
лость сталей симметричным |
циклом, «Заводская лаборатория», 1941, № 4. |
22.Инструкция № 340-50 МАП, Выбор конструкционных сталей для изделий, подвергаемых термической обработке с индукционным нагревом, Оборонгиз, 1950.
23.О д и н г И. А., Остаточные напряжения и сопротивляемость уста лости стали, закаленной токами высокой частоты, «Вестник машиностроения». 1943, Ко 4—5.
24.Ш л е й е р Э. В. и О д и н г И. А., Влияние поверхностной за
калки токами высокой частоты на механическую прочность конструкцион ных сортов стали, «Вестник металлопромышленности», 1940, № 7.
25. С л а в и н Д . О. и Г р я з н о в а Т. С., Влияние структуры стали и скорости нагрева на температуру закалки токами высокой частоты, сборн. «Материалы в химическом машиностроении», НИИХИММАШ, вып. 6, 1950.
26. |
Н а з а р о в а |
Т. |
Н ., |
Свойства |
среднеуглеродистой стали, |
зака |
|
ленной |
с поверхности |
при |
нагреве |
тич, «Вестник |
машиностроения», |
||
1951, К» 9. |
Н. М., |
Влияние |
поверхностного |
упрочнения на |
пре |
||
27. |
П у л ь ц и н |
дел выносливости и остаточные напряжения в стали, сборн. «Некоторые во
просы усталостной прочности стали», Машгиз, 1953. |
|
and |
|||||
28. |
O s b o r n |
Н. В., |
Induction surface |
hardening, «Heat treating |
|||
forging», |
1941, |
№ |
12, |
V a n - N o t e |
W., Induction |
hardening |
and |
29. |
M a г t i n |
D. L., |
|||||
austenitizing caracteristics |
of several medium carbon steels, |
Transactions of |
|||||
ASM, vol, 36, |
1946. |
of the Failure of Metals under Repeated stresses». |
|||||
30. Сборн. «Prevention |
|||||||
1941. |
|
|
|
|
|
|
|
А. В. РЯБЧЕНКОВ и Е. Л. КАЗИМИРОВСКАЯ
ВЛИЯНИЕ АТМОСФЕРНОЙ КОРРОЗИИ НА УСТАЛОСТНУЮ ПРОЧНОСТЬ СТАЛИ
И МЕТОДЫ ПОВЕРХНОСТНОГО УПРОЧНЕНИЯ
Изменение усталостной прочности стали при атмосферной коррозии
Одним из самых распространенных видов коррозии металлов является атмосферная коррозия.
Около 80% всех металлических конструкций эксплуатируется в атмосферных условиях. Ежегодные потери и затраты металла на замену пришедших в негодность конструкций исчисляются миллионами тонн. Имеющиеся экспериментальные данные и результаты практических наблюдений говорят о том, что корро зия конструкционных и низколегированных сталей значительно усиливается в промышленных и приморских районах.
Ухудшение коррозионной стойкости металла связано с загряз нением атмосферы частичками солей и коррозионно-активными газами.
Особенно неблагоприятное влияние оказывает образующийся при сгорании низких сортов топлива сернистый газ.
С. Г. Веденкин [2], исследуя коррозионную стойкость низко легированных марок сталей в различных атмосферных условиях, получил, что средняя потеря углеродистой стали за год в сель
ской местности составила |
139 г/м 2, тогда как потеря за такое же |
время в паровозном депо |
составила 903 г/м 2. |
Атмосферная коррозия представляет собой случай электро химической коррозии, когда коррозионные процессы идут под пленкой влаги. Однако протекание электрохимического процесса в результате присутствия на поверхности металла весьма тонкого
слоя электролита |
будет |
несколько |
отличаться от протекания |
|
электрохимической |
коррозии при |
полном погружении |
металла |
|
в раствор электролита. |
Тонкая пленка влаги является |
слабым |
препятствием для диффузии кислорода воздуха к поверхности металла, а потому процессы атмосферной коррозии протекают преимущественно с кислородной деполяризацией даже в случае действия сравнительно кислой среды.
68
Кроме этого, тонкая пленка влаги создает большое сопроти вление коррозионному электрическому току, вследствие чего сила тока на поверхности металла будет мала. Присутствие в пленке влаги растворенных S02 или НС1 увеличивают скорость корро зионного процесса за счет повышения электропроводности пленки влаги, а также за счет ионов, разрушающих защитные пленки [11.
Отмечено, что значительное увеличение скорости коррозион ного процесса в присутствии S02 может происходить только при достижении вполне определенной (критической) влажности. Ниже этой влажности примеси S02 практически не оказывают влияния на скорость коррозии [1]. Таким образом, состав атмосферы и влажность воздуха являются важнейшими факторами при атмо сферной коррозии, и в зависимости от них коррозионнная стой кость металлов может существенно изменяться.
Необходимо отметить, что как в нашей, так и в зарубежной литературе имеются сведения о влиянии различных атмосферных условий на общую коррозионную стойкость металла и совер шенно отсутствуют данные о влиянии атмосферной коррозии на усталостную прочность металла. Изучение усталостной прочности при атмосферной коррозии имеет, кроме научно-теоретического интереса, большое практическое значение, поскольку значитель ное число металлических конструкций, деталей машин и средств транспорта работает в естественных атмосферных условиях,
одновременно подвергаясь |
переменным напряжениям. |
В связи с этим настоящая работа и имела своей основной |
|
целью создать методику |
коррозионно-усталостных испытаний |
при атмосферной коррозии |
и оценить влияние различных атмо |
сферных условий на усталостную прочность конструкционной стали 45.
Коррозионно-усталостные испытания проводились на изгото вленных в ЦНИИТМАШ машинах ЯК-8 конструкции С. И. Ядкевича [3]. Машина была специально приспособлена для проведе ния усталостных испытаний в условиях атмосферной коррозии и позволяла в этих условиях определять выносливость образца при симметричном изгибе с частотой 2800 циклов в минуту.
Внешний вид машины ЯК-8 представлен на фиг. 1, а ее прин ципиальная механическая схема приведена на фиг. 2. Испытуемый
образец 1, форма и размеры которого даны на фиг. 3, |
укреплен |
в захвате 2, неподвижно зажатом в раме станины. |
На цапфу |
образца напрессован радиальный подшипник 3. Обойму подшип ника охватывает трос 5, укрепленный концами в траверзе тяги 6. Трос 5 проходит по роликам 4 девиатора 7. Тяга 6 проходит через центральное отверстие вала мотора 8 и заканчивается грузовым стержнем, снабженным тарелкой 9 для удержания
грузов 10.
Работа машины состоит в том, что грузы, лежащие на тарелке грузового стержня, вызывают натяжение троса на головке деви атора и создают прогиб образца. Электродвигатель, вращая
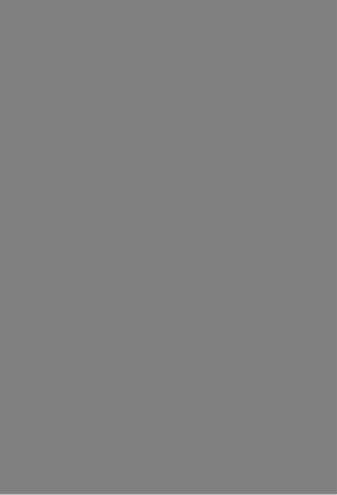