
книги / Некоторые вопросы усталостной прочности стали
..pdf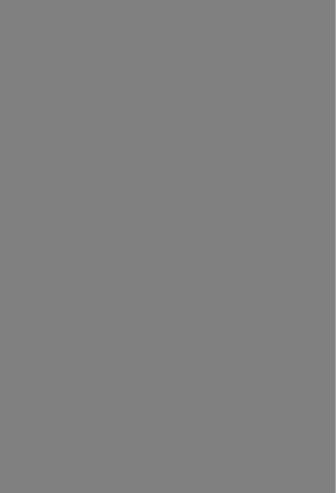
|
|
|
Таблица 1 |
|
|
|
П р е д ел в ы н о сл и |
У в е л и ч е н и е п р е |
|
Р еж и м ы о б р а б о т к и |
д ел а в ы н о с л и в о |
|||
в о с т и в 1сг[млА |
||||
|
|
|
сти в ° / 0 |
|
Б е з н а к л еп а |
...................................................... |
5 2 ,5 |
0 |
|
Н ак л еп п о п е р в о м у р е ж и м у . . . . |
5 4 ,7 |
4 .2 |
||
Н а к л еп п о в т о р о м у р е ж и м у . . |
5 7 ,4 |
9 ,3 |
||
Н а к л еп п о т р е т ь е м у р е ж и м у . . . . |
6 0 ,0 |
14,3 |
Удаление наклепанных слоев производилось травлением по разра ботанной нами методике.
Результаты исследования остаточных напряжений предста влены па фиг. 4. Наклеп по всем трем режимам дает принципиально одну и ту же картину
|
|
|
|
распределения |
остаточ |
|||
ы |
|
|
|
ных напряжений: в на |
||||
|
|
|
клепанном |
слое возни |
||||
|
|
|
|
кают сжимающие |
оста |
|||
|
|
|
|
точные |
напряжения |
|||
I 65- |
|
|
|
значительной величины, |
||||
|
|
|
в средней |
части — не |
||||
! » ■ |
|
|
|
значительные |
растяги |
|||
|
|
|
вающие и, наконец, на |
|||||
5 5 - |
|
|
|
противоположной |
сто |
|||
|
|
|
роне пластинки— опять |
|||||
----------- -------- ------------------ -— — |
||||||||
сжимающие, |
но |
уже |
||||||
10ч |
105 |
106 |
ю” |
небольшие. |
|
|
|
|
|
|
Число циклоб |
Как известно, подоб- |
|||||
Ф и г . 3. К р и в ы е в ы н о сл и в о ст и |
с т а л и _ 4 0 Х Н М А . |
пая картина характерна |
||||||
|
|
|
|
для пластин, |
изогну |
тых в результате наклепа, произведенного с одной стороны. Выпрямление пластины приложением внешнего момента приводит к перераспределению напряжений и к уничтожению сжимающих напряжений на стороне, противоположной наклепанной.
Несколько необычным является снижение величины сжимаю щих напряжений в поверхностной части наклепанного слоя. Для выяснения причины этого явления было предпринято специальное исследование, результаты которого изложены в отдельной статье.1 На основании этого исследования можно заключить, что фактически сжимающие остаточные напряжения в поверхностной части наклепанного дробью слоя имеют наиболь
1 П у л ь ц и н Н . |
М ., |
О б о с т а т о ч н ы х |
н а п р я ж е н и я х в п о в е р х н о с т н о й |
ч асти н а к л е п а н н о г о д |
р о б ь |
ю с л о я , « З а в о д |
с к а я л а б о р а т о р и я » , 1 9 5 1 , № 8. |
3 2
шее значение, а кажущееся снижение величины этих напряжений объясняется некоторой неотработанностыо методики. В процессе удаления поверхностного наклепанного слоя и последующего расчета величины напряжений не учитывается такой факт, как уменьшение в результате травле ния высоты гребешка шерохова тости обработанной дробью по-
Е Ж верхности.
0,6 |
0,8 |
1,0 |
1,8 |
8,0 |
2,2 |
2,4 |
|
|
< j s 5’‘sS' Расстояние отнаклепанной |
||||
|
|
|
поверхности 6 мм |
|
||
Ф и г. 4 . О статоч н ы е н а п р я ж е н и я в |
п л а с т и н а х ста л и 4 0 Х Н М А , |
|||||
в ы зв ан н ы е н а к л еп о м д р о б ь ю . |
|
|
|
Исследование напряжений в образцах с предварительно сня тыми неровностями подтверждает этот вывод. Кстати, в процессе
ной роликами поверхности 6 мм
Ф и г . 5 . |
О статоч н |
ы е н а п р я ж е н и я |
в п о |
Ф и г. 6 . О статоч н ы е |
н а п р я ж е н и я |
в е р х н о с т н о м с л о е |
о б р а б о т а н н ы х д р о б ь ю |
в п о в ер х н о ст н о м с л о е о б к а та н н ы х |
|||
|
о б р а зц о в -п л а с т и н . |
|
р о л и к а м и ц и л и н д р и ч е с к и х о б р а з |
||
|
|
|
|
ц ов . |
|
снятия |
неровностей стрела |
прогиба пластинки не |
изменяется, |
а следовательно, и напряжения по величине и распределению остаются прежними.
3 |
Сборник эак. 747 |
33 |
Исследование методом травления остаточных напряжений в образцах, наклепанных обкаткой роликами, а следовательно, сразу, без предварительной обработки, имеющих гладкую поверх ность, приводит к результатам, тоже подтверждающим сделанный ранее вывод. В обкатанных роликами образцах шероховатость поверхности в процессе первых травлений увеличивается, а сле довательно, и значения величин сжимающих остаточных напряже ний в поверхностной части слоя получаются большими, чем они должны быть.
На фиг. 5 и 6 представлены графики распределения напряже ний в наклепанных дробью и обкатанных роликами образцах.
Исследование влияния комбинированного упрочнения на остаточные напряжения и предел выносливости стали 12ХНЗА
Опыты проводились на стали состава: С = 0,13%, |
Сг = 0,74%, |
Ni = 3,05%, имеющей размер аустенитного зерна |
7. Предвари |
тельным исследованием была установлена оптимальная глубина
цементации. Для принятых |
в |
работе образцов |
с диаметром |
И ----------------------------------------------- |
— |
1 3 0 ------------------------------------------------- |
*■ |
? |
0 7,5 2 |
|
Ф и г . 7 . Ф ор м а о б р а з ц а ст а л и J 2 X H 3 A д л я и сп ы т а н и и на у с т а л о с т ь .
7,52 мм (фиг. 7) она оказалась равной 0,75 мм. Предел вынослив вости стали в исходном состоянии (без цементации) после терми ческой обработки (закалки и отпуска) составляет минимум 45 кг/мм2 и максимум 60 кг/мм2.
Исходя из условий технологии обработки цементованных изде лий, включающей производственную шлифовку, была выбрана следующая программа данного исследования:
1. Установление и сравнение между собою пределов выносли вости образцов в состояниях:
а) после цементации и тщательной шлифовки, б) после цементации и грубой шлифовки,
в) после цементации, тщательной шлифовки и обкатки роликами, г) после цементации, грубой шлифовки и обкатки роликами.
2.Исследование остаточных напряжений.
3.Установление взаимосвязи пределов выносливости и харак тера распределения остаточных напряжений.
Все образцы подвергались цементации на одну и ту же глубину 0,75 мм. При этом глубиной слоя считается расстояние от поверх
ности до слоя с содержанием углерода 0,4%.
Цементация проводилась в твердом карбюризаторе типа бондюжского, содержащем около 19% углекислого бария.
34
Режим цементации:
1)индивидуальная упаковка каждого образца в железных трубках;
2)прогрев до 750°;
3)прогрев до 970°;
4)выдержка при температуре 970° в течение 1 часа 45 мин.;
5)охлаждение с 970° вместе с печыо до температуры 100°.
Режим |
термической |
обработки |
||||
после |
цементации: |
в |
масле; |
|||
1) |
закалка |
с |
860° |
|||
■2) |
закалка |
с |
800° в |
масле; |
3)отпуск при 160° в течение 3 час.
сохлаждением в масле.
Нагрев |
под |
закалку |
проводился |
|
||
в ванне состава 46% NaCl и 54% КС1. |
|
|||||
Выдержка в ванне при температуре |
|
|||||
закалки |
15 мин. |
|
|
|
|
|
После второй закалки и отпуска |
|
|||||
проводилось измерение твердости. |
Фиг. 8. Схема обкаточного |
|||||
При |
обкатке |
роликами |
принята |
устройства. |
||
нагрузка |
250 кг. Схема |
устройства, |
представлена на фиг. 8. |
|||
на котором |
осуществлялась |
обкатка, |
Испытания на усталость проводились на машине консольного типа. Схема этой машины представлена на фиг. 9. База испытания— 5 млп. циклов.
Каждая серия включала от 6 до 8 образцов.
Результаты испытаний на усталость приведены в табл. 2. Усталостные кривые приведены на фиг. 10.
Полученные результаты показывают, что цементация даже при невыгодных условиях сравнения, когда предел выносливости в нецементированном состоянии принимается равным 60 кг/мм2, дает повышение усталостной прочности на 55%, а при тщательной шлифовке после цементации — более чем на 58%. Однако приме няемая в производственных условиях шлифовка не повышает, а, наоборот, снижает предел выносливости, портит деталь. Здесь то и приходит на помощь обработка шлифованной поверхности
* |
35 |
давлением. Обкатка роликами, оказывающаяся мало эффективной применительно к тщательно полированным образцам, значительно повышает предел выносливости грубо шлифованных образцов.
Так, если сразу после цементации и нормальной термической обработки нешлифованные образцы дают предел выносливости
93 кг!мм2, а тщательная шлифовка повышает его до 95 кг/мм2, то грубая шлифовка снижает предел выносливости до 80 кг/мм2.
Далее, если обкатка роликами образцов, тщательно шлифован ных после цементации, повышает их предел выносливости с 95 до 98 кг/мм2, то применение этой обработки к грубо шлифованным после цементации образцам оказывается значительно более эффективным, повышая их предел выносливости с 80 до 95 кг/мм2 и приближая, таким образом, эти образцы по усталостной проч ности к тщательно шлифованным.
В нашем исследовании была сделана попытка, определив остаточные напряжения, увязать их характер с изменением уста лостной прочности в результате комбинированного упрочнения. Исследование остаточных напряжений проводилось на сплошных
36
№
серии
/
2
3
4
5
6
|
|
|
|
|
|
|
|
|
|
Таблица 2 |
|
|
|
|
|
|
|
|
|
Изменение предела выноелн- |
|||
|
|
|
|
|
|
|
Предел |
пости по сравнению |
|
||
|
|
|
|
|
|
|
с пределом |
с пределом |
|||
|
|
Обработка |
|
Твердость |
выпоелноо- |
||||||
|
|
|
сти при |
выносливости |
выносливости |
||||||
|
|
|
|
|
|
* с 1!0 |
изгибе |
после закалки |
после закалки |
||
|
|
|
|
|
|
|
D кг/л.«* |
с высоким от |
с низким от |
||
|
|
|
|
|
|
|
|
пуском |
пуском |
||
|
|
|
|
|
|
|
|
кг/.и.н’ |
°/о |
кг/мм* |
°/о |
Без |
цементации, в |
|
|
|
|
|
|
||||
термически |
обрабо- |
|
|
|
|
|
|
||||
тайном |
состоянии . . |
34 |
45 |
0 |
0 |
— |
__ |
||||
|
|
|
|
|
|
42 |
60 |
— |
— |
0 |
0 |
Цементация на глу |
|
|
|
|
|
|
|||||
бину |
0,75 |
мм, |
без |
|
|
|
|
|
|
||
шлифовки ................. |
59 |
93 |
48 |
107 |
33 |
55 |
|||||
Цементация, |
тща |
|
|
|
|
|
|
||||
тельная |
шлифовка |
59 |
95 |
50 |
111 |
35 |
58,3 |
||||
Цементация, |
гру |
|
|
|
|
|
|
||||
бая |
шлифовка |
. . . |
58 |
80 |
35 |
78 |
20 |
33,3 |
|||
Цементация, |
тща |
|
|
|
|
|
|
||||
тельная |
шлифовка, |
|
|
|
|
|
|
||||
обкатка роликами . . |
60 |
98 |
53 |
118 |
38 |
63 |
|||||
Цементация, |
гру |
|
|
|
|
|
|
||||
бая |
шлифовка, |
об |
|
|
|
|
|
|
|||
катка роликами |
. . |
61 |
95 |
50 |
111 |
35 |
58,3 |
цилиндрических образцах длиной 100 мм и диаметром 7,52 мм. При этом определялись осевые напряжения первого рода. В про цессе опыта напряженный слой удалялся стравливанием в рас творе азотной кислоты с добавлением глицерина; периодически замерялись диаметр стержня и его длина. Точность замера при стравливании подиаметру равнялась0,01 мм, а по длине—0,001 мм.
По выявленной в результате опыта зависимости между изме нением длины стержня и толщиной стравленного слоя проводилось приближенное определение остаточных напряжений. Применя лась формула
|
л |
Е f n (ln - 0 - f n - i V n - i - 0 |
* |
|
Л“ " Т --------------- Д/п |
» |
|
где |
<з„ — остаточное |
напряжение в n-ом слое; |
|
|
Е — модуль упругости; |
|
|
|
I — начальная длина стержня; |
|
|
|
/„ — площадь поперечного сечения стержня после удаления |
||
|
слоя с напряжением о„; |
|
|
* |
В упрощающем |
предположении одноосного |
напряженного состоя |
ния. |
|
|
|
37
ln — длина стержня после удаления |
слоя с напряжением о„; |
/л- 1 — площадь поперечного сечения |
стержня до удаления |
слоя с напряжением о„; |
|
/„_] — длина стержня до удаления слоя с напряжением о„. Характер распределения остаточных напряжений в стержнях, прошедших различную обработку, представлен на фиг. 11. Из графиков видно, что цементация дает в поверхностном слое сжимаю щие остаточные напряжения; наклеп роликами приводит к уве
|
|
|
личению этих |
напряжений. |
||||||
|
|
|
Грубая |
шлифовка |
вызы |
|||||
|
|
|
вает |
появление |
в поверхно |
|||||
|
|
|
стном |
слое |
растягивающих |
|||||
|
|
|
остаточных |
|
|
напряжений. |
||||
|
|
|
В результате |
обкатки |
роли |
|||||
|
|
|
ками эти напряжения уничто |
|||||||
|
|
|
жаются и вместо них появля |
|||||||
|
|
|
ются |
сжимающие. |
|
|||||
|
|
|
Проведенное |
|
исследова |
|||||
|
|
|
ние, не претендуя на исчер |
|||||||
|
|
|
пывающую |
количественную |
||||||
|
|
|
характеристику, |
несомненно |
||||||
|
|
|
дает правильную |
качествен |
||||||
|
|
|
ную |
картину |
распределения |
|||||
|
|
|
остаточных напряжений при |
|||||||
|
|
|
различных |
видах |
поверхно |
|||||
|
|
|
стной |
обработки. |
|
|
||||
|
|
|
Совместное |
рассмотрение |
||||||
|
|
|
данных |
усталостных |
испы |
|||||
|
|
|
таний |
(табл. |
2) и исследова |
|||||
|
|
|
ния остаточных |
напряжений |
||||||
Фиг. 11. Остаточные напряжения в по |
(фиг. |
11) |
позволяет |
утвер |
||||||
верхности образцов-стержней |
стали ждать, |
что между величиной |
||||||||
|
12ХНЗА. |
|
предела |
выносливости |
и ве |
|||||
точных напряжений в различных |
личиной и характером |
оста |
||||||||
случаях |
поверхностной |
обра |
||||||||
ботки |
существует взаимная |
связь. |
|
|
|
в |
поверхностном |
|||
В |
самом деле, грубая |
шлифовка вызывает |
слое неблагоприятные растягивающие напряжения значительной величины. Предел выносливости при этом сильно падает. Этому не следует удивляться, так как хорошо известны случаи, когда вредное действие растягивающих напряжений при шлифовке приводит не только к понижению прочности, но и к прямому разрушению детали в результате возникновения шлифовочных трещин.
Поверхностный наклеп при обкатке роликами, уничтожая вредные растягивающие напряжения, заменяет их сжимающими напряжениями. Одновременно происходит повышение предела выносливости.
38
Тщательная тонкая шлифовка цементированных образцов позволяет получить высокий предел выносливости при малых сжимающих остаточных напряжениях и даже при их отсутствии. Однако при обкатке таких образцов, вызывающей значительные сжимающие напряжения на поверхности, все же удается несколько повысить предел выносливости.
Отсюда видно, что положительная роль сжимающих остаточ ных напряжений выявляется из данных эксперимента менее четко, чем вредное действие растягивающих остаточных напряжений.
Эффективным |
оказывается действие комбинированного упроч |
|||||||||||
нения на усталостную прочность надрезанных образцов. |
||||||||||||
Исследование влияния над |
|
|
|
|
||||||||
реза проведено на тех же образ |
|
|
|
|
||||||||
цах (фиг. |
7), |
но |
|
с диаметром |
|
|
|
|
||||
шейки 7,72 мм (вместо 7,52 мм). |
|
|
|
|
||||||||
На |
шейке |
такого |
образца |
|
|
|
|
|||||
после |
цементации |
и |
термиче |
|
|
|
|
|||||
ской обработки наносился над |
|
|
|
|
||||||||
рез (фиг. 12). Глубина надреза |
|
|
|
|
||||||||
0,1 мм, так что диаметр образ |
Фиг. |
12. Форма надреза на уста |
||||||||||
ца по дну надреза составлял |
||||||||||||
|
лостном |
образце. |
||||||||||
7,52 |
мм. |
|
на |
усталость |
показали, |
что цементованные и тер |
||||||
Испытания |
||||||||||||
мически обработанные |
образцы |
с надрезами |
снижают предел |
|||||||||
выносливости |
до величины |
меньше 50 кг/мм2, а |
наклеп обкаткой |
|||||||||
роликами |
таких |
образцов |
повышает |
предел |
выносливости до |
|||||||
82 кг/мм2. |
Таким |
образом, |
усталостная прочность цементован |
|||||||||
ного, надрезанного и обкатанного |
образца выше, |
чем образца, |
который после цементации подвергался грубой шлифовке.
Выводы
Цементация и поверхностный наклеп являются действенными средствами повышения усталостной прочности. Еще более эффек тивной оказывается комбинированная обработка, представляющая собой сочетание химикотермического упрочнения и поверхност ного наклепа.
При этом действие наклепа в случае надреза на цементованном изделии, а также в случае грубой производственной шлифовки после цементации оказывается особенно эффективным.
Одной из важнейших причин повышения предела выносливости при поверхностном упрочнении является создание благоприят ных сжимающих напряжений в поверхностных слоях детали.
с. и. кутковскик
УСТАЛОСТНАЯ ПРОЧНОСТЬ ПРИ ИНДУКЦИОННОЙ ЗАКАЛКЕ УГЛЕРОДИСТОЙ СТАЛИ
Проблеме повышения усталостной прочности при индукцион ной закалке стали токами высокой частоты в настоящее время уделяется все большее внимание. Ряд работ, выполненных за последние несколько лет, целиком или частично посвящен изуче нию различных факторов, обеспечивающих получение высокой усталостной прочности при индукционной закалке. Приведенные в табл. 1 данные показывают, однако, что исследователям большею частью удалось добиться высоких значений предела усталости (70—88 кг/мм*) лишь в случае применения легированных сталей, вто время как достигнутые максимальные значения предела уста лости углеродистой стали, как правило, остаются еще низкими. Лишь в одной из работ [4] было получено повышение предела усталости стали 45 до уровня 57,5 кг/мм2.
Анализ достигнутых результатов может поставить под сомне ние возможность получения высокой усталостной прочности при индукционной закалке углеродистой стали. Существует мнение, согласно которому углеродистая сталь рассматривается как материал, усталостная прочность которого не позволяет исполь зовать его в качестве высокопрочного материала для тяжело нагруженных деталей. Так, в инструкции МАП [22], выпущен ной в самое последнее время, указывается, .что «Сталь 45 пред назначается для малонагруженных деталей...».
Однако с таким мнением нельзя согласиться.
Автор настоящей работы поставил себе целью доказать возможность получения высокой усталостной прочности при индук ционной закалке углеродистой конструкционной стали1.
Теоретически такая возможность вполне может быть обосно вана.
Для подтверждения высказанного положенияследуетобратиться
канализу зависимости, представленной на фиг. 1, справедливость
1В последнее время, после выполнения настоящего исследования, в лите ратуре появились данные, подтверждающие наше положение [26].
40