
книги / Некоторые вопросы усталостной прочности стали
..pdfНеобходимо сказать также несколько слов о месте индукцион ной закалки в последовательности операций обработки изделия. С нашей точки зрения индукционная закалка должна произво диться после механической обработки, включая шлифовку, так как при механической обработке сталь подвергается как механи ческому, так и тепловому воздействию, которое может привести к нежелательному изменению структуры и свойств. Хотя некото рые исследователи [18] и пришли к выводам о том, что шлифовка после индукционной закалки не снижает предела усталости, однако эти выводы еще нуждаются в проверке. Работы, выпол ненные за последнее время [27], показали, что незначительное отклонение от правильного режима шлифовки приводит к прижогам, снижению твердости, а также возникновению растягиваю щих напряжений в поверхностных слоях. Необходимость после дующей шлифовки в значительной степени отпадает также и потому, что при индукционной закалке поводка и коробление изделия уменьшаются до весьма малых величин.
Рассмотрев влияние различных факторов на результаты индук ционной закалки, целесообразно подвергнуть анализу опубли кованные работы по индукционной закалке углеродистой стали.
Первой работой, в которой была поставлена задача исследова ния влияния индукционной закалки на усталостную прочность конструкционной углеродистой стали марки 40, явилась работа Шлейера и Одинга [24 ]. В этой работе был получен низкий пре дел усталости после индукционной закалки.
Неудачные результаты этих опытов, неоднократно упомина емые в литературе, объяснялись главным образом тем, что закалке подвергалась только цилиндрическая часть образца, в то время как галтель оставалась неупрочнеиной. Разрушение образцов
происходило |
по галтелям |
в местах окончания закаленного |
слоя. |
поздних опытах |
Кудрявцева и Новикова [7] был |
В более |
учтен опыт предыдущих исследований. Авторы подобрали такие режимы обработки, которые обеспечивали получение равномер ного слоя на рабочей части и галтели образца. Однако и в этой работе не было достигнуто эффективное повышение усталостной прочности при поверхностной закалке. Максимальное значение предела усталости образцов из стали 40 диаметром 10 мм после индукционной закалки составило 45,0 /сг/лш2, что превышает предел усталости этой стали, определенный на таких же образ
цах |
после обычной закалки и отпуска, всего лишь на 3,2 кг!ммй, |
т. е. |
на 7,5%. |
Для рассматриваемой работы Кудрявцева и Новикова харак терно также получение недостаточно высокой твердости при индукционной закалке. Максимальное значение твердости не превышало Я/?с = 54—56. Такое значение твердости, являющееся
высоким при обычной закалке, при индукционной закалке может быть повышено на несколько единиц.
5)
В этой работе контроль температуры отсутствовал. Приведенные данные показывают, что в рассматриваемой
работе авторам не удалось достигнуть таких режимов обработки, при которых были бы полностью использованы преимущества поверхностной индукционной закалки.
Отсутствие необходимых сведений не позволяет нам составить определенное мнение о причинах заниженных результатов; однако приведенные в работе данные позволяют высказать пред положение о том, что причиной являлась недостаточная мощность высокочастотной установки (для выбранного типа образцов) и, как следствие этого, малая скорость нагрева (ориентировочно оцениваемая нами в 200—300°/сек.).
Наиболее высокие результаты были получены в работе Коссого [4]. Коссой совершенно справедливо считает, что повышение усталостной прочности при индукционной закалке должно идти по пути предварительного улучшения структуры, подбора опти мальных параметров слоя и повышения скорости нагрева. Автор рассматриваемой работы правильно указывает на недостаточную мощность наиболее распространенных высокочастотных устано вок для обработки крупных изделий. С целью ускорения индук ционного нагрева применялся предварительный подогрев на раз личные температуры (200, 400 и 600°). За счет правильного исполь зования указанных выше факторов удалось получить более высокое значение твердости усталостных образцов, изготовлен ных из стали 45, доходящее до Нрс = 57—59, а также малую
ширину переходной зоны; однако от одновременного использо вания действия всех факторов, повышающих усталостную проч ность, автор отказался. В работе выяснялось лишь влияние каждого из факторов в отдельности. Это привело к тому, что хотя полученные значения и превысили данные других исследо вателей, однако, они еще не являются предельными. Максималь ное значение предела усталости 57,5 кг/мм2 было достигнуто на образцах диаметром 18 мм с нормализованной исходной струк турой при применении предварительного подогрева.
Анализируя выводы данной работы, нельзя не остановиться на одной принципиальной ошибке ее автора. Определение вели чины и характера распределения остаточных напряжений в зави симости от различных факторов производилось в работе на образ цах диаметром 60 мм при малых значениях отношения площади закаленного слоя к площади незакалениой сердцевины, в то время как исследование усталостной прочности производилось на образ цах диаметром 18 мм при тех же значениях глубины слоя и, следовательно, при значительно больших отношениях площади закаленного слоя к площади сердцевины. Как указывалось Еыше, возможны три варианта разрушения от усталости в зависимости от глубины слоя, причем в каждом случае наблюдается свое влияние факторов, приводящих к упрочнению или разупрочне нию. Отсюда следует, что применяя закономерности, установлен-
52
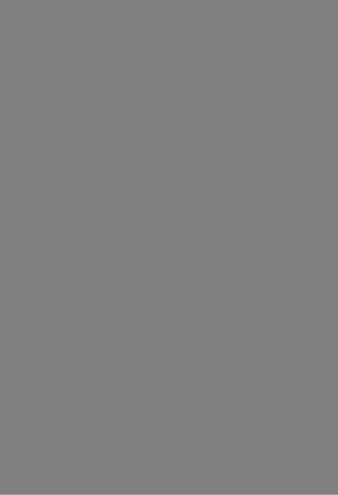
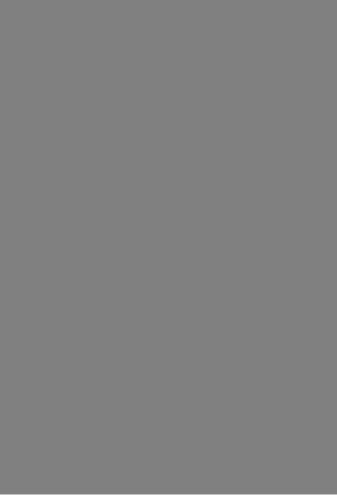
В качестве источника токов высокой частоты был использо ван высокочастотный генератор типа Л60А мощностью 60 кет, работающий на двух лампах типа Г431.
Настройка генератора осуществлялась за счет изменения количества групп емкостей, положения регулятора закалочного трансформатора и положения штурвала обратной связи. При обработке образцов всех серий регулятор закалочного транс форматора устанавливался в положение, соответствующее мак симальной мощности. Включались. все группы емкостей. Регу лировка осуществлялась только за счет изменения положения штурвала обратной связи. Такая регулировка была выбрана после ряда предварительных опытов, как обеспечивающая полу чение наивысшей твердости без значительного повышения тем пературы нагрева. При выбранной регулировке частота тока, определенная при помощи волномера, составляла 187 500 гц.
Для проверки правильности выбора частоты тока нами были использованы рекомендации Вологдина ' l l ] об оптимальной частоте тока, необходимой для получения заданной глубины закалки. Подсчет, произведенный на основании этих рекоменда ций (с учетом поправки на кривизну обрабатываемой поверх ности), показал, что данная частота является оптимальной для получения закалки глубиной 1,2-т-2,0 мм. В нашей работе пред полагалось производить закалку на глубину, равную или близ кую к этим значениям. Таким образом, полученная частота вполне нас устраивала.
Закалка образцов осуществлялась непрерывно последователь ным способом. При закалке образец вращался со скоростью 800—900 об/мин.
Нагрев образцов осуществлялся в индукторе из медной трубки с внутренним охлаждением. Эскиз индуктора представлен на фиг. 4. Подача воды для охлаждения при закалке производилась под давлением 2,5-s-3,0 am через спреер, изображенный на фиг. 5. Расстояние между индуктором и спреером составляло 10 мм. Более близкое взаимное расположение индуктора и спреера хотя и было желательно с целью получения закалки без возмож ного подстуживания, однако, оказалось невозможным, так как в этом случае вода заливала индуктор, что приводило к неравно мерному нагреву и охлаждению закаливаемой поверхности.
Температура при закалке замерялась посредством оптиче ского потенциометра, работающего по принципу исчезающей
нити.
Так как нагрев производился с весьма высокой скоростью (доходящей до 1200в/сек.), а на замер температуры отводился весьма непродолжительный отрезок времени (3—4 сек.), то с целью повышения точности замеров и предупреждения возмож ных ошибок был применен пирометр, работающий не по прямой, а по потенциометрической схеме, которая позволяет быстрее осу ществлять настройку на замеряемую неизвестную температуру.
55
Примененный прибор обладает весьма растянутой шкалой тем ператур (около 1° в мм).
Для выяснения влияния магнитных полей, создаваемых высокочастотным генератором, было произведено сравнение пока заний прибора при замере температур образца и соляной ванны. Сравнение накаленной нити при одном и том же показании при бора с поверхностью образца и с поверхностью ванны показало,
что расхождения в показаниях не превышают 10°, т. е. не выхо дят за пределы погрешности прибора.
Кроме указанной проверки, прибор проверялся при несколь ких температурах по поверхности соляной ванны и массивной плиты, температура которых замерялась контрольной термо парой. Расхождение в показаниях контрольной термопары и
примененного |
прибора составляло ± 5 °. |
Измерение |
температуры производилось на выходе образца |
из индуктора. |
При замере температуры внутри индуктора на |
различных режимах (замер производился снизу при более низком положении спреера, чем при закалке) было установлено, что внутри индуктора максимальная температура на поверхности образца, превосходит температуру, замеряемую на выходе из
56
Получение |
различной |
глубины |
слоя |
|
|
||
достигалось изменением |
скорости |
пере |
АА — первое |
пере |
|||
мещения |
образца |
и изменением |
подво |
ключение; Б Б — вто |
|||
димой мощности (за |
счет изменения силы |
рое переключение. |
|||||
тока на анодах ламп). |
|
|
|
|
|||
Подбор требуемой глубины слоя и необходимой твердости про |
|||||||
изводился |
на |
контрольных образцах. |
Для каждого |
режима |
индукционной закалки была произведена оценка средней ско
рости |
нагрева. Для этой цели был проделан следующий |
опыт. |
исследуемой стали было изготовлено несколько образцов, |
Из |
закаленных с нагревом в печи без последующего отпуска.Твер дость этих образцов составляла HRQ = 56—58. Затем выбран
ные образцы подвергались частичной закалке в рабочей части по тем же режимам, что и остальные. При этом твердость образ цов в месте окончания закаленного слоя изменялась от макси мально получаемой при индукционной закалке до исходной твердости. Время прохождения участка, на котором изменялась твердость, принималось за время нагрева. Средняя скорость
57
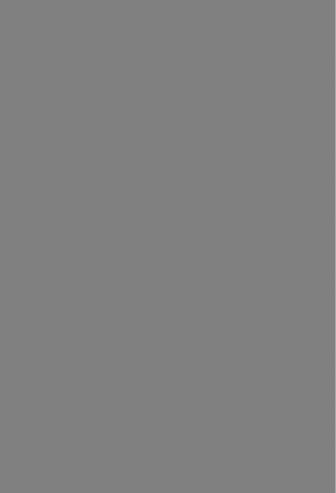
С нашей точки зрения соблюдение этих условий должно было обеспечить получение высокой усталостной прочности при опти
мальном |
режиме обработки. |
|
|
|
|
|
|||||||
Режимы обработки указаны в табл. 3. |
|
представлены |
|||||||||||
Фотографии |
разрезов |
контрольных |
образцов |
||||||||||
на фиг. |
7. |
|
|
|
|
|
|
|
|
Таблица 3 |
|||
|
|
|
|
|
|
|
|
|
|
|
|
||
Режимы обработки |
|
|
|
|
№ серин |
|
|
||||||
|
|
|
2 |
|
3 |
|
|
||||||
|
|
|
|
|
|
|
|
1 |
|
|
4 |
||
Ток |
анода |
в а . . . |
|
2.8 |
2.9 |
|
2,9 |
3,0 |
|||||
Ток |
сетки |
в а . . . |
|
0,32 |
0.33 |
|
0,33 |
0,34 |
|||||
Напряжение сети в в |
|
380 |
380 |
|
380 |
380 |
|||||||
Скорость перемеще |
|
25,4 |
20.0 |
|
18,5 |
16.0 |
|||||||
ния шейки в мм]сек . |
|
|
|||||||||||
Скорость перемеще |
|
|
|
|
|
|
|
||||||
ния галтели |
в мм/сек |
|
14,1 |
13,0 |
|
12,5 |
12,5 |
||||||
Температура в °С . . |
|
865 |
880 |
|
900 |
915 |
|||||||
Средняя скорость на |
|
|
|
|
|
815 |
|||||||
грева |
в |
°/сек................... |
|
1220 |
980 |
|
930 |
||||||
Глубина |
слоя |
в мм |
0,7 -0,8 |
1,1—1.3 |
1,8-2,0 |
Сквозная |
|||||||
|
|
|
|
|
|
|
|
|
|
|
|
закалка |
|
Твердость шейки Нрс |
6 0 -61 |
60-61 |
60 -61 |
5 9 -6 0 |
|||||||||
|
|
|
Исследование |
микроструктуры ц твердости |
|
||||||||
Исследование микроструктуры и твердости стали после индук |
|||||||||||||
ционной |
|
закалки |
производилось |
на образцах, подвергавшихся |
|||||||||
обработке по тем же режимам, |
что и образцы для усталост |
||||||||||||
ных испытаний. Фотографии микроструктур |
исследуемой стали |
||||||||||||
после |
индукционной |
закалки и |
низкого |
отпуска представ |
|||||||||
лены |
на |
фиг. |
8 |
и |
9. |
Структура |
закаленного |
слоя |
пред |
||||
ставляет |
|
собой |
мелкоигольчатый |
мартенсит |
при |
температуре |
|||||||
закалки |
900—915° |
и |
скрытнокристаллический мартенсит |
(гар- |
денит) при температуре закалки 865—880°. По мере возраста ния температуры закалки величина игл возрастает незначи
тельно. |
Д л я . сравнения приводится структура |
исследуемой |
стали, |
полученная при обычной закалке (фиг. 10). |
Как следует |
из сравнения приводимых структур, величина игл мартенсита при индукционной закалке с температуры 915° не превышает таковую у мартенсита обычной закалки.
Таким образом, превышение температуры обычной закалки на 85е в наших опытах не привело к получению крупноиголь чатого мартенсита., характеризующего перегрев.
59
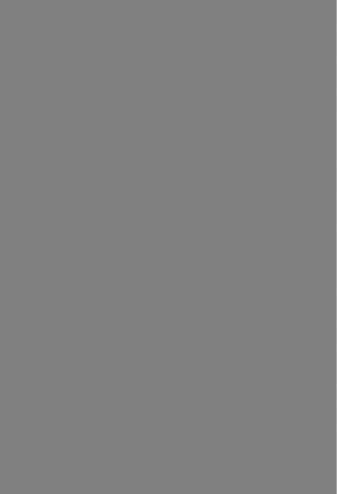