
книги / III. Internationales Kalisymposium 1965 Teil 2
.pdf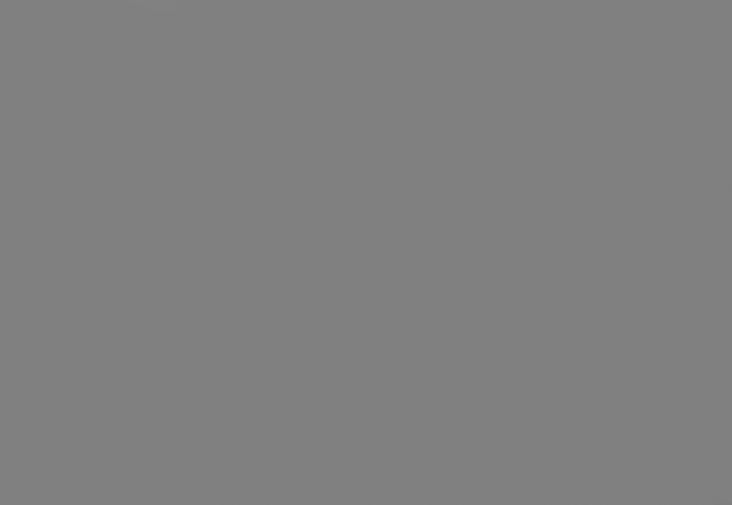
Bild 23. Einige ökonomische Daten zu provozierten Salz-Gas- Ausbrüchen
100 000 t eff. hochwertiges' Rohsalz ausgeworfen wurden, ge zeigt. Das hier praktizierte Abbauverfahren nennen wir Koh lensäure-Weitungsbau [45]].
In welchen Umfang die Grubenselbstkosten durch verschiedene provozierte Ausbrüche gesenkt werden konnten, läßt Bild 23 erkennen. Aus dem unteren Säulendiagramm läßt sich leicht die immense Bedeutung des K^O-Gehaltes für die Wirtschaft lichkeit eines provozierten Ausbruches schließen.
Die Forschungsarbeiten zur Bekämpfung der COg-Gefahren wur den im Rahmen der Tätigkeit der Forschungsgemeinschaft "Mineralgebundene Gase" durchgeführt. Weitere Arbeiten die ser Gemeinschaft zielen auf die gelenkte Einflußnahme hin sichtlich der Gestaltung der kausalen Zusammenhänge des Ausbruchsgeschehens hin £46 , 47 » 48].
Durchführung eines Totalabbauversuches
Der Kalibergmann hegt schon immer den Wunsch, mit möglichst geringen Substanzverlusten abbauen zu können. Die Ergebnisse der umfangreichen Forschungsarbeiten der letzten Jahre auf gebirgsmechanischem Gebiet [49 * 50 , 51 • 5 2 j ermutigten zu einem erneuten Totalabbauversuch, der im Rahmen eines Forschungsauftrages in der Grube Pöthen erfolgte [53[]• Nachdem auf Grund geophysikalischer Meßergebnisse eine Lau ge nge fahr verneint werden konnte, kam es darauf an, durch geeignete Maßnahmen eine geringe Hangendkrümmung und eine genügende Hangendunterstützung zu gewährleisten. Deshalb wurde festgelegti
1.eine Begrenzung der Abbauscheibe auf 3 m Höhe,
2.die Anlage vorläufiger quadratischer Stützpfeiler,
3.ein möglichst schneller Verhieb,
4.eine schnelle Hohlraumverfüllung durch Zubruchschießen der getrimmten Pfeiler und des Hangenden.
In dem 200 x 95 m umfassenden Versuchsfeld wurden 18 Abbaue auf die im Bild 24 skizzierte Weise angelegt. Folgende Hauptparameter wurden gewählt:
Abbaubreite 5 m,
Querhiebbreite 3,5 m,
Pfeilerfläche 3,5 x 3,5 m.
Das die einzelnen Abbauphasen kennzeichnende Zyklogramm ist aus Bild 24 ersichtlich. Nach dem Durchschlägigwerden mit der Wetterkopfe trecke dienen die Baue zunächst noch kurz zeitig der Wetterführung, um dann in die Pfeilertrimmphase einbezogen zu werden, der das Zubruchschießen folgt. Dabei wird jetzt der Bruch in jedem Abbau in drei Etappen geschos sen.
Die Pfeiler werden auf etwa 18 bis 20 % ihrer Ursprungs fläche getrimmt. Unter Berücksichtigung der Streckenpfeiler und Streuverluste liegen die Abbauverluste des Verfahrens bei etwa 20 %. Die Standzeit der Abbaue liegt im Mittel bei etwa 70 bis 80 Tagen. Das gebirgsmechanische Verhalten des Baufeldes, das hach einem festen Meßprogramm überwacht wird,

|
|
|
|
\T\Abbau auffahren |
|||
|
i |
i i i M i I L I I |
i J i i L j —i— i |
{7] Schießen der Durch hiebe |
|||
|
y j |
rimmen |
aer rrener |
||||
f. |
•w w |
|
|
ElTri |
d |
Pf il |
|
|
|
|
Bohren der Bruch kante |
||||
|
t 10m |
Schrapper- StegKetten- |
[71 |
|
|
||
|
\J] Abbau dient der Bewetterung |
||||||
|
|
haspel |
förderer |
\&\Schießen des |
Bruches |
||
|
|
|
|
Bild 24. Abbauschema und Arbeitsablauf zum Kammerpfeiler bruchbau im Südharz-Kalibergbau
entspricht im wesentlichen den theoretischen Erwartungen,
Die wirtschaftlichen Parameter des Verfahrens können noch nicht voll befriedigen. Die Ursache hierfür liegt vor allem in der Anwendung der für dieses Verfahren ungeeigneten Schrapperförderung begründet. Für weitere Totalabbaufelder ist die Verwendung gummibereifter Förderfahrzeuge vorgese hen.
Einführung des AN/DK-Schießverfahrens
Nach dem Bekanntwerden der günstigen wirtschaftlichen Ergeb nisse» die man anderwärts bei der Anwendung des AN/DKSchießverfahrens erreichen konnte» galt es diese Methode auch für unseren Kalibergbau nutzbar zu machen. Im einzelnen mußten ein Sprengstoffladegerät und ein einbiasfähiger Sprengstoff entwickelt sowie für uns geeignete Verfahrens-
Varianten geschaffen werden.
Das im Bild 25 (siehe Bildtafel I) gezeigte entwickelte Lade gerät arbeitet nach dem Prinzip des druckluftbeaufschlagten Behälters. Der Füllinhalt beträgt etwa 30 kg Sprengstoff.
Das Gerät ist wie der dazugehörige Kompressor fahrbar ge staltet. Es ist mit einer pneumatischen Fernbetätigung aus gerüstet. Die mittlere Verblasmenge liegt unter Berücksichti gung kurzer Pausen bei 6 bis 7 kg Sprengstoff/min. Zeitein sparungen gegenüber der Verwendung patronierter Sprengstoffs ergeben sich beim Sprengstoffeinblasen nach Überschreitung einer SprengStoffmenge von etwa 100 kg/Schicht.
Die anderwärts verwendeten AN-Prills standen uns in der DDR nicht zur Verfügung. Unser AN-Grundstoff wird durch Absie bung aus den bei der Herstellung feinkörnigen Ammoniumnitrats anfallenden Backfraktionen gewonnen. Er hat relativ ungün stige Festigkeitsund Porositätswerte aufzuweisen, so daß zugesetzter Dieselkraftstoff - wie Bild 26 (siehe Bildta fel I) erkennen läßt - nur in die Oberflächenbereiche der Körner eindringt. Der dadurch entstehenden Entmischungsge fahr muß durch häufiges Wenden der Sprengstoffbehälter be gegnet werden [54 , 55].
Dieser Nachteil wurde inzwischen durch die Ermittlung eines anderen geeigneten Köhlenstoffträgers mit höherer Viskosi tät, der obendrein noch billiger ist, beseitigt. Der neu ge schaffene Sprengstoff Dekamon 2 ist durch eine hinreichende Gleichmäßigkeit für längere Zeit ausgezeichnet.
Der Sprengerfolg ist bei Verwendung von Dekamon 2 infolge der besseren Bohrlochausnutzung und des innigeren Kontaktes zwischen Sprengstoff und Bohrloch recht gut, so daß je nach den örtlichen Verhältnissen Vorgabesteigerungen um 16 bis 70 % gegenüber den bisherigen Gewinnungsverfahren möglich sind. Die Unabhängigkeit des Bohrlochdurchmessers von einem Patronendurchmesser gestattet dessen jeweils lagerstätten bezogene Optimierung. Der Detonationsablauf wird obendrein mit zunehmendem Lochdurchmesser günstiger.
Dekamon 2 ist annähernd um 2/3 billiger als patronierter Sprengstoff. Weitere Kostensenkungen resultieren aus der Steigerung der Hauerleistung, so daß - wie sich aus Bild 27
Bild 27. Mögliche Beeinflussung der Gewinnungskosten b e i m Einsatz von Dekamon 1 (A) gegenüber Donarit 2 (B)
ergabt - eine Senkung der gesamten Gewinnungskosten |
i m A b |
|
bau auf etwa |
60 bis 75 % möglich ist. |
|
Vorerst wird |
in 6 Kaligruben mit Dekamon geschossen . Die |
|
weitestgehende Umstellung des gesamten Kalibe r g b a u e s |
au f |
|
Dekamonanwendung ist vorgesehen. |
|
Einführung des Großlochstroßverfahrens |
|
|
|
Die Einführung des AN/DK-Schießens ist noch |
nicht |
a u s r e i c h e n d , |
|
um den Produktiv!.tätsforderungen an die |
Gewinnung |
i n u n s e r e n |
|
Kaliund Steinsalzgruben Genüge zu tun. |
Im |
R a h m e n d e r B e |
|
mühungen um eine höhere Hauerleistung ist die E i n f ü h r u n g |
|||
des Großlochstroßverfahrens in mächtigeren |
L a g e r s t ä t t e n b e |
||
reichen besonders erwähnenswert. |
|
|
|
Es wurden hierzu umfassende Untersuchungen |
i n e i n e r S t e i n |
||
salzgrube durchgeführt, in der etwa 30 |
m mächtige |
S t e i n s a l z - |
schichten zu Strossen waren [56]« Bild 28 zeigt die zeich nerische Erfassung eines GroßlochabSchlages. Die wichtigsten technischen Daten sind in der Darstellung angegeben.
Bei der verallgemeinernden Auswertung der Versuche und durch theoretische Untersuchungen gelang es, eindeutige funk tionelle Zusammenhänge zwischen den wichtigsten Gewinnungs parametern zu ermitteln. Diese wurden in einem Schaubild, das im Bild 29 gezeigt wird und allen in Präge kommenden Be trieben als Grundlage für die Anwendung des Großlochstrossens dienen kann, dargestellt. Das eingezeichnete Beispiel bezieht sich auf folgende Verhältnisse:
Die Strossenhöhe liegt bei 5 m, und die Abbaubreite beträgt 14m . Daraus ergibt sich ein optimaler Bohrlochdurchmesser von 60 mm. Die Zahl der je Abschlag zu bohrenden Löcher be trägt 7. Der zu erwartende spezifische Sprengstoffverbrauch liegt bei ungefähr 220 g/t.
Zunächst wurde bei den Versuchen mit SFG-Säulendrehbohrma- schinen bei 640 mm SpindelVorschub min, 80 mm Lochdurchmesser und 5 bis 10 m Lochlänge gearbeitet. Schließlich wurde
Bild 28. Großlochabschlag vom 12.11.1964
Bild 29. Optimale Abstimmung der Gewinnungsparameter beim Großlochstrossenbau
eine Steinbruchbohrmaschine der SMG vom !fyp SG 750, die für Untertageverhältnisse umgebaut wurde, eingesetzt. Der Lochdurchmesser betrug jetzt 75 mm, und es wurden bis zu 39 m lange Löcher bei 50 bis 55° Neigung gebohrt.
Die Einsatzergebnisse waren recht positiv, jedoch werden durch die vorgesehene Verwendung wendiger Bohrwagen noch günstigere wirtschaftliche Ergebnisse erwartet. Im Vergleich zum bislang üblichen firstartigen Verhieb sanken die Gewin nungskosten um etwa 50 % ; dabei reduzierte sich der Zündmit telaufwand um 92 %.
Die bei verschiedenen AnwendungsVarianten des Großlochstrossens erreichbaren Hauerleistungen wurden bei den Versuchen ermittelt und sind im Bild 30 graphisch dargestellt.
Bild 30. Hauerleistungssteigerungen beim Großlochstrossen verfahren
Untersuchungen zur Einführung von Hochleistungsgeräten zum Laden und Fördern
Veranlaßt durch die bekannt gewordenen großen Erfolge in anderen Ländern bei der Benutzung nicht gleisgebundener För derfahrzeuge, wurden Untersuchungen zum Einsatz von Hochlei stungsgeräten zum Laden und Fördern in unseren Kaliund Steinsalzgruben durchgeführt» Zunächst wurde in einer Stein salzgrube die Kombination Bagger/Dumper getestet» Dabei er gab sich eine wirtschaftliche Überlegenheit gegenüber dem Schrappbetrieb ab 320 t Schichtfördermenge [57].
Nachdem schwedische Kiruna-Trucks zur Verfügung standen, er folgte eine Testung der Kombinationen Bagger/Kiruna-Truck und Doppelfrässcheibenlader/Kiruna-Truck. Fotos beider Kom binationen werden als Bilder 31 und 32 (siehe Bildtafel II) gezeigt.
Der Bagger UB 80 vom VEB Nobas wurde mit Löffeln verschiede nen Inhalts erprobt. Bei 1,35 TD? Löffelinhalt wurde eine
Ladeleistung bis zu 250 t/h erreicht. Ein Bagger und zwei
Trucks der Type KT 1.25 - letztere übernahmen die gesamte Abbauund Streckenförderung der Grube - erreichten bei
380 min reiner Arbeitszeit und 2000 m Förderlänge eine För derleistung von 940 t/Schicht, die bei störungsfreiem Be trieb auf 1000 t/Schicht gesteigert werden kann. Produktivi tätssteigerung und Kostensenkung sind erheblich.
Im Streckenvortrieb wurden beim Einsatz von Doppelfräs scheibenladern der SMG die 20-t-Trucks in 5 bis 6 min bela den. Die Vortriebsleistung stieg um 86 %,und die Kosten
sanken auf 70 %9 Weitere Verbesserungen sind möglich.
Die Forschungsarbeiten bezogen sich auf die Testung aller wichtigen Gerätedaten und Geräteeigenschaften, auf die um
fassende Organisationsproblematik in allen ihren Details und auf tiefgründige ökonomische Analysen. In letztere wur den - zunächst allerdings nur theoretisch - auch andere Ge
räte |
mit einbezogen. Es |
zeigte sich |
- wie Bild 33 erkennen |
läßt |
daß zum Beispiel |
l'ransloader |
und vor allem Scooptrams |
Förderentfernung in m |
|
------------Gerätekombination DFSL-1 K iru n a -T r.------------- |
Transbader |
----------- Geratekombination DFSLr2 Kiruna-Tr. ------------- |
Scoopmobil |
Bild 33. Ladeund Förderkostenvergleich der Geräte Doppel- frässcheibenlader/Kiruna-Truck, Transloader und Scoopmobil