
книги / Теория механизмов и машин курсовое проектирование
..pdf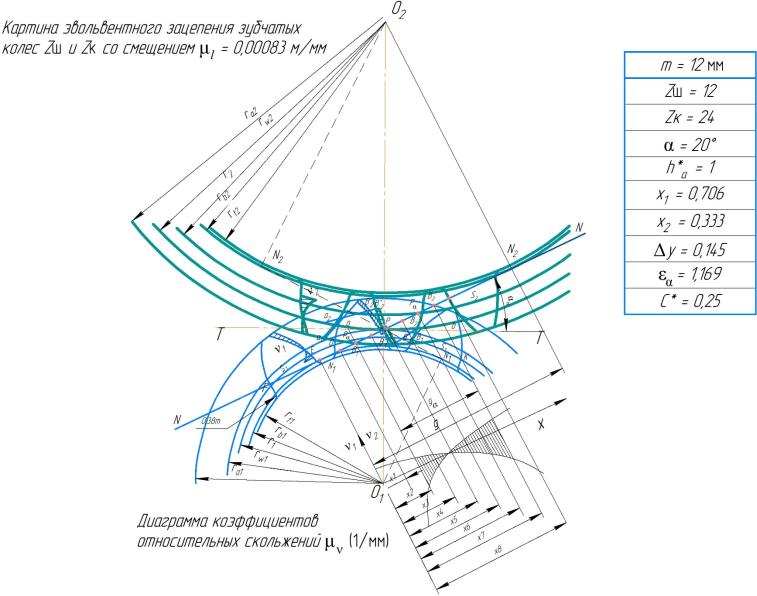
70
Рис. 3.6. Картина эвольвентного зацепления корригированных зубчатых колес и диаграмма коэффициентов относительных скольжений
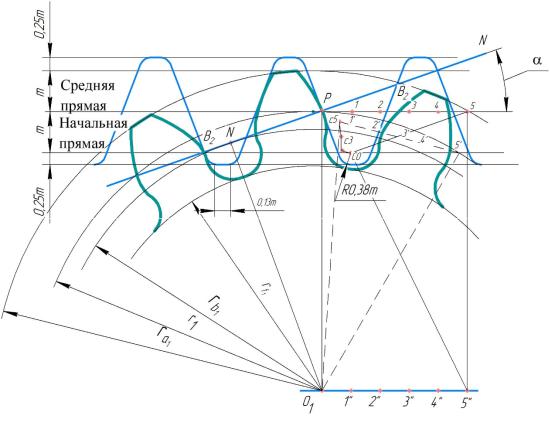
3.5. Построение картины инструментального зацепления
Для построения картины инструментального зацепления выбирают исходный контур зубчатой рейки, например по ГОСТу 16530-70, и определяютвсеразмерызубчатогоколесабезсмещения(рис.3.7) исосмещением (рис. 3.8) по соответствующим формулам, приведенным в табл. 3.2.
Внастоящеевремяширокоиспользуютметодобкатки,применяястандартный инструмент и сдвигая его на определенную величину от центра или к центру заготовки зубчатого колеса.
Рис. 3.7. Инструментальное зацепление шестерни с рейкой без сдвига
При нарезании зубчатого колесабез смещения режущего инструмента (см. рис.3.7) рейка располагается так, что ее модульная средняя линия совпадает с делительной прямой и касается делительной окружности радиуса r = m·z2 нарезаемого колеса. При таком положении рейки толщина зуба и
ширина впадины равны на модульной прямой.
При нарезаниирейкойколеса со смещением (см. рис.3.8) по окружности радиуса r = m·z2 будет уже катиться не средняя модульная прямая, а де-
лительная прямая, отстоящая от модульной прямой на величину смещения xm.
71
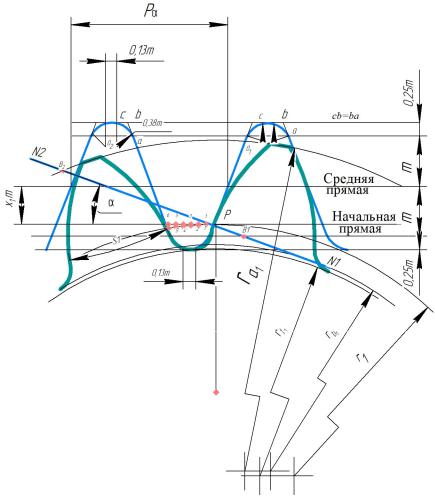
Построение инструментального зацепления начинается с вычерчивания профиля инструментальной рейки. Для этого проводят среднюю линиюрейки.Отнееоткладываютвверхивнизрасстояния,равныеm и1,25m. На этих расстояниях вычерчивают прямые, параллельные средней линии. Далее среднюю линию рейки разбивают на ряд отрезков, равных половине шага, т.е. получают точки, через которые проводят боковые грани зубьев рейки под углом 20° к вертикали (см. рис. 3.8).
Рис. 3.8. Картина инструментального зацепления со смещением
Для нахождения центра C0 дуги закругления головки инструмента необходимо выполнить обычные сопряжения пересекающихся прямых радиусом ρ = 0,38m. Таким образом, получают 3–4 зуба инструментальной рейки. В случае нарезания нормального колеса касательная P 5 к делительной окружности должна совпадать со средней линией рейки (см. рис. 3.7). Если нарезается колесо со смещением, то делительная окружность его должна касаться делительной прямой рейки, отстоящей от средней рейки на величину смещения x1m (см. рис. 3.8).
72
В соответствии с вышеизложенным проводят делительную прямую, отстоящую от средней линии рейки на величину смещения x1m в направлении, соответствующем положительному или отрицательному смещению инструмента. Через точку пересечения делительной прямой с профилем зуба рейки P проводят вертикаль, на которой от точки P откладывают отрезок, равный радиусу делительной окружности нарезанного колеса, т.е. получают его центр и из него затем проводят все окружности. Построение эвольвенты производят изложенным ранее способом.
Переходная кривая, сопрягающая эвольвентную часть профиля зуба с окружностью впадин, образуется на станке автоматически как результат движенияподачискругленнойчастиголовкизубаинструментальнойрейки относительно заготовки колеса.
Для построения относительных траекторий точек, лежащих на профиле рейки, сообщают заготовке и рейке движение с угловой скоростью колеса ( ω). Тогда колесо остановится, а делительная прямая рейки будет перекатываться без скольжения по делительной окружности колеса. Точки 1, 2, 3, 4 на делительной прямой рейки (см. рис. 3.8) будут совпадать с точками 1 , 2 , 3 , 4 , 5 на делительной окружности колеса. Указанные точки предварительно были полученыпутем откладыванияравныхотрезковдлиной 5–10 мм на делительной окружности и делительной прямой рейки.
ЦентрC0 дуги закругления головки инструмента при таком перекатывании опишет удлиненную эвольвенту (см. рис. 3.7). Для построения этой эвольвенты соединяют точку C0 прямыми линиями с точками 1, 2, 3, 4, 5 и 1 , 2 , 3 , 4 , 5 и затем названные точки между собой. В результате получают ряд треугольников (см. рис. 3.7).
Для определения, например, положения точки C5 необходимо из центра 5 провести дугу радиусом C05, а из центра вращения колеса, засечь эту дугу радиусом C05 . Точно так же определяются положения точек C1, C2, ..., C5,... Соединив точки C0, C1, C2, ..., C5, получают траекторию точки C0. Если из найденных точек C0, C1, C2, ..., C5 построенной кривой провести дуги радиусом ρ = 0,38m, то огибающая этого семейства дуг и будет профилем ножки зуба.
Построение профиля ножки зуба при станочном зацеплении можно провести и другими методами, в частности упрощенным. Из точки 1 определяют радиус окружности касательной к головке рейки, а затем из точки 1 проводят дугу того же радиуса. Построения повторяют соответственно для точек 2 и 2 , 3 и 3 и т.д.(см. рис.3.7,3.8). Огибающая всех положений построенных дуг будет профилем ножки зуба.
73
3.6. Пример выполнения задания
Исходные данные: m = 12 мм, z1 = 15, z2 = 18.
Построение картины инструментального зацепления без сдвига
Таблица 3.10 Параметры инструментального зацепления шестерни
Параметр |
Обозна- |
Формула |
Значение, |
l, |
Значение |
|||
|
чение |
|
|
|
мм |
м/мм |
вмасштабе,мм |
|
Шаг зацепления |
p |
|
m |
37,699 |
|
75,3982 |
||
|
|
|
|
|
|
|
||
Радиус делитель- |
r1 |
|
m·z1 |
|
90 |
|
180 |
|
ной окружности |
2 |
|
|
|||||
|
|
|
|
|
||||
|
|
|
|
|
|
|
|
|
Радиус основной |
rb1 |
r1∙cosα |
84,572 |
|
169,1447 |
|||
окружности |
|
|||||||
|
|
|
|
|
|
|
||
|
|
|
|
|
|
|
|
|
Толщина зуба |
|
|
p/2 |
18,849 |
|
37,6991 |
||
по делительной |
S1 |
|
|
|||||
окружности |
|
|
|
|
|
0,0005 |
|
|
|
|
|
|
|
|
|
||
Радиус окружно- |
rf1 |
r1 – m(ha* + c*) |
75 |
150 |
||||
сти впадин |
||||||||
|
|
|
|
|
|
|
||
|
|
|
|
|
|
|
|
|
Радиус началь- |
rw1 |
rw1 = r |
90 |
|
180 |
|||
ной окружности |
|
|||||||
|
1 |
|
|
|
||||
Глубина захода |
hd |
(2ha*)m |
24 |
|
48 |
|||
зубьев |
|
|||||||
|
|
|
|
|
|
|||
Высота зуба |
h |
hd + c*m |
27 |
|
27 |
|||
Радиус окружно- |
ra1 |
rf1 + h |
102 |
|
204 |
|||
сти вершин |
|
|||||||
|
|
|
|
|
|
|
||
|
|
|
|
|
|
|
|
Зубчатая рейка располагается так, чтобы ее модульная средняя линия совпадаласделительнойпрямойикасаласьрадиусаделительнойокружности нарезаемого колеса. Через точку P пересечения делительной прямой с профилем зуба рейки проводится вертикаль. По ней от точки Р откладывается отрезок, равный r1, получается центр колеса О1.
ПостроениеэвольвентызубаначинаетсяотточкиP.Послепостроения одной ветви эвольвенты откладывается толщина зуба по делительной окружности. Из полученной точки строится вторая ветвь эвольвента зуба.
74
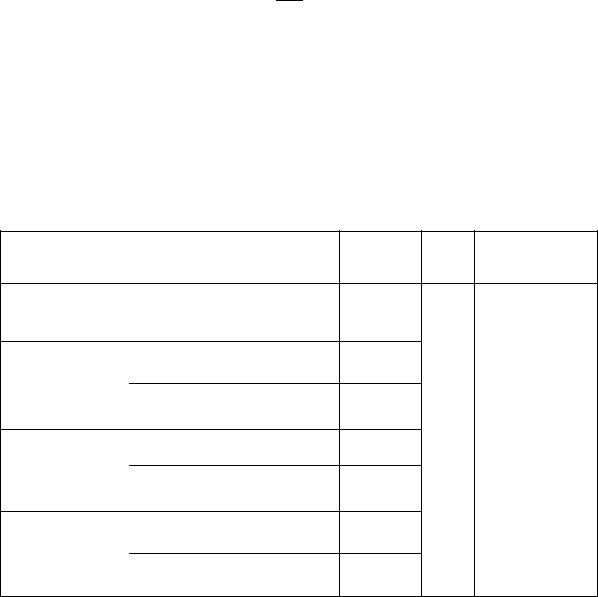
Таким образом строится несколько зубьев колеса (рис. 3.9). Полученное колесо будет с подрезом зуба. Такое колесо исправляется, и строится картина корригированного зацепления z1 и z2 (рис. 3.9).
Построение картины неравносмещенного эвольвентного зацепления зубчатых колес
Передаточное число зацепления u = z2 / z1 = 18 / 15 = 1,2 (1 < u <2). Всекоэффициентыдляопределенияпараметровзацепленияопределя-
ются табличным методом по В.Н. Кудрявцеву.
Коэффициент сдвига первого колеса x1 = 0,677, второго колеса x2 = 0,508, y = 0,19, y = 0,995.
Угол зацепления определяется табличным методом, используя инволютную функцию:
invαw = 2x∑ tgα + invα.
z∑
Согласно табл. 3.9 invα = 0,014904.
invαw = 2(0,677 + 0,508) tg20° + 0,014904 = 0,0410436.
15 + 18
Исходя из полученного значения угол зацепления αw = 27°35'. Масштабный коэффициент построения μl = 0,0005 м/мм. Результаты
расчета в табл. 3.11.
Таблица 3.11 Параметры эвольвентного неравносмещенного зацепления
Параметр |
Обозна- |
|
|
Формула |
|||
|
чение |
|
|
|
|
|
|
Шаг зацепления |
p |
|
|
|
π∙m |
||
Радиус |
r1 |
|
|
|
m∙z1 |
|
|
|
|
2 |
|
||||
делительной |
|
|
|
|
|
||
r2 |
|
|
|
m∙z2 |
|
||
окружности |
|
|
|
||||
|
|
2 |
|
||||
|
|
|
|
|
|
||
Радиус |
rb1 |
|
|
r1∙cosα |
|||
основной |
rb2 |
|
|
r2∙cosα |
|||
окружности |
|
|
|||||
Толщина зуба |
S |
1 |
|
p |
+ 2x ∙m∙tgα |
||
|
|
||||||
по делительной |
|
2 |
1 |
|
|||
S |
|
|
p |
+ 2x ∙m∙tgα |
|||
окружности |
2 |
|
|||||
|
|
||||||
|
|
2 |
2 |
|
|||
|
|
|
|
|
|
Значение, μ , |
Значение |
ммм/мм в масштабе, мм
37,6991 |
|
75,3982 |
|
|
|
|
|
90 |
|
180 |
|
|
|
|
|
108 |
0,0005 |
216 |
|
|
|
|
|
84,5723 |
169,1447 |
|
|
|
|
||
|
|
|
|
101,4868 |
|
202,9736 |
|
|
|
|
|
24,7633 |
|
49,5267 |
|
|
|
|
|
23,2871 |
|
46,5742 |
|
75
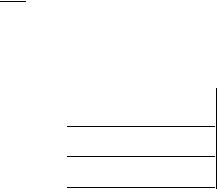
Окончание табл. 3.11
Параметр |
Обозна- |
|
Формула |
Значение, |
мμ/мм, |
Значение |
||||||
чение |
|
мм |
в масштабе, мм |
|||||||||
Радиус |
rf1 |
r |
– m(h* |
+ c* – x ) |
83,124 |
|
166,248 |
|||||
|
1 |
|
a |
|
|
|
1 |
|
|
|
||
окружности |
|
|
|
|
|
|
|
|
|
|
|
|
|
|
|
|
|
|
|
|
|
|
|
|
|
впадин |
rf2 |
r |
– m(h* |
+ c* – x ) |
99,096 |
|
198,192 |
|||||
|
|
2 |
|
a |
|
|
|
2 |
|
|
|
|
|
|
|
|
|
|
|
|
|
|
|
|
|
Межосевое |
aw |
|
m( |
zΣ |
+ y) |
209,94 |
|
419,88 |
||||
расстояние |
|
2 |
|
|
||||||||
|
|
|
|
|
|
|
|
|
|
|
||
|
|
|
|
|
|
|
|
|
|
|||
Радиус |
r |
|
r (1 + |
|
2y |
) |
95,4273 |
|
190,8545 |
|||
|
|
|
|
|||||||||
w1 |
|
1 |
|
|
|
zΣ |
|
|
0,0005 |
|
||
начальной |
|
|
|
|
|
|
2y |
|
|
|
||
|
|
|
|
|
|
|
|
|
|
|
|
|
окружности |
rw2 |
|
r2(1 + |
|
|
|
) |
114,5127 |
|
229,0255 |
||
|
|
|
zΣ |
|
||||||||
|
|
|
|
|
|
|
|
|
|
|
||
Глубина |
hd |
|
(2ha* – ∆y)m |
21,72 |
|
43,44 |
||||||
захода зубьев |
|
|
||||||||||
|
|
|
|
|
|
|
||||||
Высота зуба |
h |
|
hd + c*m |
24,72 |
|
49,44 |
||||||
Радиус |
ra1 |
|
rf1 + h |
|
107,844 |
|
215,688 |
|||||
окружности |
|
|
|
|
|
|
|
|
|
|
|
|
r |
|
rf2 + h |
|
123,816 |
|
247,632 |
||||||
вершин |
|
|
|
|||||||||
a2 |
|
|
|
|
|
|
|
|
|
|
|
На вертикальной линии межцентрового расстояния проводятся дуги начальных окружностей. Через точку их касания P проводится прямая под углом αw к горизонтали. Построения эвольвент первого и второго колеса начинаются из точки P. Проводятся окружностивершин и впадин. Получается практический участок линии зацепления. Находятся рабочие участки профилей зубьев. Строятся диаграммы коэффициентов относительных скольжений (см. рис. 3.9):
ν1 = 1 – g x– x u2-1; ν2 = 1 – g x– x.
Таблица 3.12
Значения коэффициентов удельных скольжений
Координата |
Значение, мм |
ν1 |
ν2 |
0 |
0 |
– ∞ |
1 |
|
|
|
0,83143 |
x1 |
23,948 |
– 4,932 |
76
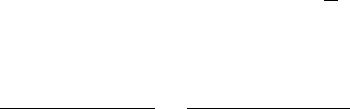
|
|
|
Окончание табл. 3.12 |
|||
|
|
|
|
|
|
|
Координата |
Значение, мм |
ν1 |
|
|
ν2 |
|
x2 |
52,593 |
|
– |
|
1,247 |
|
x3 |
88,373 |
0 |
|
|
0 |
|
x4 |
133,81 |
|
|
0,6226 |
|
– |
x5 |
164,53 |
|
|
0,8486 |
|
– |
x6 |
194,42 |
1 |
|
|
– ∞ |
|
Выбирается масштаб для диаграмм μν= 201 = 0,05 Коэффициент перекрытия (аналитически):
|
|
|
|
+ |
|
|
– aw∙sin(αw) |
|
|
εα = |
|
ra12 |
– rb12 |
ra22 – rb2 |
2 |
= |
|||
|
|
|
π∙m∙cos(α) |
|
|
|
|||
|
|
|
|
|
|
|
|
107,8442 – 84,57232 + 123,8162 – 101,48682 – 209,94∙sin(27°35')
|
|
|
|
|
= 1,147. |
|
|
π∙12∙cos(20°) |
|
||||
Коэффициент перекрытия (графически): |
|
|
||||
εα = |
B1B2 |
= |
40,609454 |
|
= 1,146, |
|
π∙m∙cos(α) |
|
|
||||
|
π∙12∙cos(20) |
|
|
где B1B2 – активная линия зацепления, мм (с чертежа).
Отклонение теоретического значения коэффициента перекрытия от практического составляет ∆εε ∙100 = 1,1471,147– 1,146 ∙100 = 0,087 %.
77
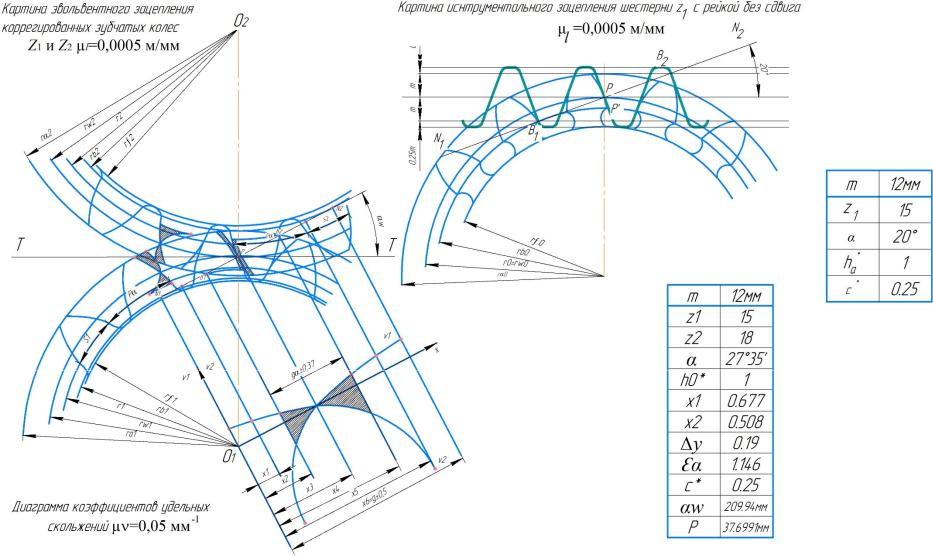
78
Рис. 3.9. Пример оформления третьего листа

4. ПРОЕКТИРОВАНИЕ КУЛАЧКОВЫХ МЕХАНИЗМОВ
При проектировании кулачковых механизмов решаются две основные задачи [4, 6].
Первая задача определение начального радиуса R0 кулачка и смещения e для механизмастолкателемили начального радиусаи межцентрового расстояния для механизмов с коромыслом. Критерий угол давления должен быть меньше или равен δmax, аугол передачи движения больше или
равен γmin.
Вторая задача профилирование кулачка по заданному закону движения выходного звена.
Исходные данные:
а) схема механизма и вид выходного звена; б) закон движения кулачка (обычно равномерный); в) закон движения выходного звена;
г) фазы движения и соответствующие им фазовые углы;
д) допускаемый максимальный угол давления δmax или допускаемый минимальный угол передачи γmin.
4.1.Определение основных размеров кулачкового механизма
споступательно движущимся роликовым толкателем
Алгоритм решения задачи.
1. Строятся диаграммы движения выходного звена.
2. Строится совмещенный график S = f |
dS |
при равенстве масштаб- |
|
dφ |
|
ных коэффициентов μS = μdS (рис. 4.1). |
|
|
|
|
|
|
|||
|
|
dφ |
|
|
|
|
|
|
|
При графическом дифференцировании диаграммы перемещения S |
|||||||||
|
1 |
|
|
μS |
|
μS μφ |
|
||
полюсное расстояние H = |
|
|
. Тогда μdφ |
= |
|
|
= |
μφ |
= μS (рис. 4.1). |
μφ |
μφH |
||||||||
|
|
|
dS |
|
|
|
|
|
|
При вращении кулачка по часовой стрелке отрезки аналога скорости для фазы удаления откладываются вправо от вертикальной оси, а для фазы сближения– влево,т.е.втусторону,кудабудетнаправлен векторскорости толкателя при повороте его на 90º в сторону вращения кулачка (см.
рис. 4.1). При вращении кулачка против часовой стрелки ddSφ на фазе удаления откладывается влево, а на фазе сближения вправо по оси абсцисс.
79