
книги / Моделирование контактных явлений при абразивном глобоидном зубохонинговании
..pdf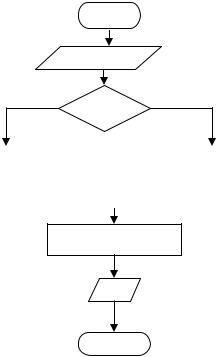
Начало
dn, l, E1, T2
dn > 0
Sigma = E1 * (dn / l) |
|
Sigma = 0 |
||
Delta = dn * (E1 / E2) |
|
Delta = 0 |
||
|
|
|
|
|
|
|
|
|
|
P = Sigma * Delta ^ 2
P
Конец
Рис. 104. Алгоритм программы расчета силы резания
После расчета значений силы резания в каждой из 30 точек при определенных условиях обработки найдем ее среднее значение, благодаря которому определим источник теплоты.
Предположим, что вся работа сил трения переходит в тепло. Тогда определим силу трения, Н:
F = Py f , |
(45) |
где f – коэффициент трения, f = 0,1.
Количество теплоты, Дж, равное работе, можно определить по
формуле |
|
Q = Fδy . |
(46) |
|
111 |
Эта формула действительна для данного случая, так как величина δy – перемещение, равное деформации по оси ОY, мала по сравнению с размерами инструмента и детали и может считаться отрезком. Исходя из этого, можем считать, что работа совершается по прямой, а не по окружности.
Величина δу является переменной и различна для каждой из точек профиля, также она зависит от параметров установки глобоидного хона и материала инструмента и детали. Значение этой величины осредняем.
После нахождения количества теплоты определить источник теплоты, Вт/м2, можно по формуле
q = |
Q |
, |
(47) |
|
Sτ |
||||
|
|
|
где S – площадь контакта; τ – время контакта;
S = lh, м2,
где l – длина контакта, l = 46,67·10–3 м; h – ширина контакта. Является величиной переменной, различна для каждой точки профиля, равна величине деформаций по оси Х. Для расчетов принимаем ее среднее значение.
Определим время контакта.
Средняя длина окружности инструмента, мм, c = πDx = π 122,89 =385,87.
Скорость вращения инструмента Vx = 0,4 м/с. Тогда время одного оборота инструмента, с,
|
c |
|
385,87 |
10−3 |
|
tx = |
|
= |
0,4 |
= 0,965 с. |
|
Vx |
|||||
|
|
|
Таким образом, время контакта, с,
τ = thc .
112
5.3. Расчет источника теплоты Пример расчета источника теплоты
Выполним расчет источника теплоты для операции хонингования поверхности ротора винтового забойного двигателя.
Материал детали – сталь 45.
Материал абразивного слоя хона – синтетический алмаз, каучу-
ковая связка, р = 38 %, φд = –0,262, dA = –0,5, dZ = 0, dG = 0.
Исходные данные, имеющие постоянные значения:
Dx – средний диаметр глобоидного хона, Dx = 122,89 мм; dд – средний диаметр ротора, dд = 49,28 мм;
ωх – угловая скорость вращения инструмента, ωх = 7,423 рад/с; ωд – угловая скорость вращения детали, ωд = 0,824 рад/с;
V′прод – продольная скорость движения детали, V′прод = = 6,3·10–5 м/с .
Данные, имеющие переменное значение:
Е2 – модуль упругости заготовки, Е2 = 200 000 000 000 Па; µ2 – коэффициент Пуассона заготовки, µ2 = 0,25.
Остальные данные для расчета источника теплоты являются переменными и изменяются в соответствии с характеристикой и геометрией профиля рабочей поверхности хона (табл. 6).
Определим силу трения, Н, по формуле (45):
F =54,386 0,1 =5,4.
Количество теплоты, Дж, равное работе, можно определить по формуле (46):
Q = Fδy .
График изменения величины δу для каждой из 30 точек для рассматриваемого случая изображен на рис. 105.
Среднее значение величины δу ср = 0,0786 мм.
Q = 5, 4 0,0786 10−3 = 0, 424 10−3 Дж.
113
|
|
|
Таблица 6 |
Данные для расчета источника теплоты |
|||
|
|
|
|
№ п/п |
Р, H |
δy, мм |
h, мм |
1 |
54,5389 |
0,100 762 |
0,191 447 |
2 |
51,494 |
0,100 494 |
0,190 938 |
3 |
46,446 |
0,099 875 |
0,189 762 |
4 |
38,268 |
0,098 385 |
0,186 932 |
5 |
30,627 |
0,096 353 |
0,183 071 |
6 |
23,749 |
0,093 824 |
0,178 266 |
7 |
10,402 |
0,085 397 |
0,162 254 |
8 |
3,966 |
0,076 669 |
0,145 672 |
9 |
1,117 |
0,068 615 |
0,130 369 |
10 |
2,911 |
0,076 21 |
0,144 799 |
11 |
8,953 |
0,085815 |
0,163 048 |
12 |
33,175 |
0,098 141 |
0,186 468 |
13 |
52,885 |
0,101 003 |
0,191 906 |
14 |
69,969 |
0,100 539 |
0,191 023 |
15 |
84,908 |
0,097 277 |
0,184 826 |
16 |
84,908 |
0,097 277 |
0,184 826 |
17 |
93,738 |
0,091 2 |
0,173 28 |
18 |
95,044 |
0,083 075 |
0,157 843 |
19 |
87,191 |
0,071 116 |
0,135 12 |
20 |
58,291 |
0,045 956 |
0,087 316 |
21 |
40,828 |
0,031 6 |
0,060 04 |
22 |
29,797 |
0,022 965 |
0,043 634 |
23 |
41,571 |
0,035 032 |
0,066 561 |
24 |
57,443 |
0,048 313 |
0,091 795 |
25 |
79,184 |
0,063 618 |
0,120 874 |
26 |
82,511 |
0,069 246 |
0,131 568 |
27 |
87,844 |
0,074 583 |
0,141 708 |
28 |
91,893 |
0,079 557 |
0,151 158 |
29 |
93,612 |
0,082 34 |
0,156 447 |
30 |
94,364 |
0,083 932 |
0,159 471 |
Ср. значение |
54,387 596 67 |
0,078 639 |
0,149 414 |
114
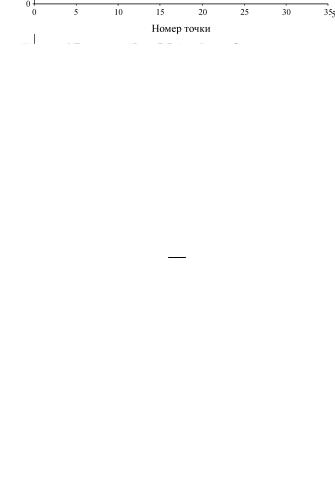
Рис 105. График изменения деформации по OY
Определить источник теплоты, Вт/м2, можно по формуле (47):
q = SQτ.
График изменения величины h для каждой из 30 точек для рассматриваемого случая изображен на рис. 106.
Рис. 106. График изменения ширины контакта
Среднее значение величины h = 0,149 мм. Определим время контакта.
Средняя длина окружности инструмента, мм, c = πDx = π 122,89 =385,87.
115
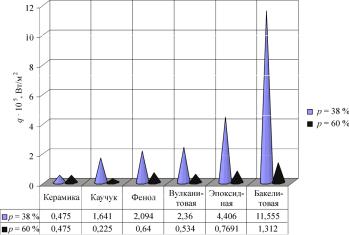
Скорость вращения инструмента Vx = 0,4 м/с. Тогда время одного оборота инструмента, с,
|
|
|
tx = |
c |
= |
385,87 10−3 |
= 0,965. |
|
|
|
|
|
|
Vx |
0,4 |
|
|
|
|||
|
|
|
|
|
|
|
|
|
||
Таким образом, время контакта |
|
|
|
|
||||||
|
|
|
th |
0,965 0,149 10−3 |
|
|
−4 |
|
||
|
|
τ = c = |
|
385,87 10−3 |
= 3,75 10 |
|
. |
|||
Источник теплоты, Вт/м2, |
|
|
|
|
||||||
|
Q |
|
|
|
|
0,424 10−3 |
|
|
|
5 |
q = |
|
= |
|
|
= |
1,6 10 . |
||||
Sτ |
46,67 10−3 0,149 10−3 3,75 10−4 |
|
Изменение источника теплоты при изменении характеристик абразивного слоя
Выполним расчет источника, изменяя вид связки инструмента, вид абразивных включений, их концентрацию.
Покажем изменение значений источника теплоты в зависимости от характеристик абразивного слоя (рис. 107–109).
Рис. 107. Изменение источника теплоты при различных видах связки
(алмаз, dA = –0,5, dZ = 0, dG = 0)
116
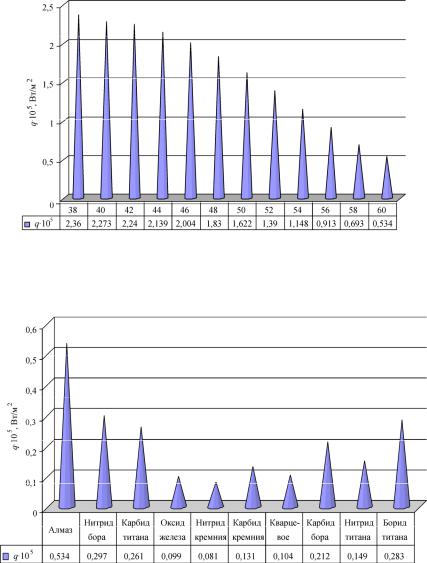
Рис. 108. Изменение источника теплоты при изменении концентрации алмазов в вулканитовой связке (dA = –0,5, dZ = 0, dG = 0)
Рис. 109. Изменение источника теплоты при изменении вида абразива при р = 60 % в вулканитовой связке (dA = –0,5, dZ = 0, dG = 0)
117
5.4. Теплофизические характеристики материалов
Немалое влияние на температуру оказывают теплофизические свойства материала, причем как материала инструмента, так и материала детали.
Теплофизические свойства материала ротора указаны в табл. 7.
|
|
|
|
Таблица 7 |
|
Теплофизические свойства материала ротора |
|||
|
|
|
|
|
Марка |
Теплопровод- |
Плотность |
Теплоемкость |
Температуро- |
стали |
ность λ, Вт/м·К |
ρ, кг/м3 |
с, Дж/кг·К |
проводность а, м2/с |
Сталь 45 |
32 |
7744 |
561 |
0,074·10–4 |
Поскольку материал глобоидного хона является неоднородным и состоит из связки, абразивных включений, воздушных пор, при определении теплофизических свойств материала инструмента в целом необходимо учитывать свойства каждого элемента, входящего
всостав материала.
Втабл. 8 указаны теплофизические свойства компонентов, входящих в состав материала глобоидного хона.
Общие формулы для расчета теплофизических характеристик инструмента, Вт/м·К, следующие:
λ = λ1m1 +λ2m2 +... +λnmn , |
(48) |
где λ1…λn – коэффициенты теплопроводности всех n компонентов круга; m1…mn – массовые доли компонентов.
Аналогичным образом можно определить среднюю плотность круга, кг/м3, и удельную теплоемкость, Дж/кг·К:
ρ =ρ1m1 +ρ2m2 +... |
+ρnmn ; |
(49) |
c = c1m1 +c2m2 +... |
+cnmn . |
(50) |
Коэффициент температуропроводности, м2/с, характеризует связь между всеми свойствами:
a = |
λ |
. |
(51) |
|
|||
|
ρc |
|
118

Таблица 8 Теплофизические свойства компонентов материала глобоидного хона
Материал |
Тепло- |
Плот- |
Теплоем- |
Температуро- |
про- |
ность |
кость |
проводность |
|
|
водность |
|||
Вулканитовая связка |
0,085 |
2470 |
1200 |
2,86775E–08 |
Бакелитовая связка |
0,23 |
1250 |
1590 |
1,15723E–07 |
Каучук |
0,21 |
1200 |
1350 |
1,2963E–07 |
Фенолформальдегид- |
|
|
|
|
ная связка |
0,22 |
1200 |
1340 |
1,36816E-07 |
Эпоксидная связка |
0,55 |
1180 |
960 |
4,85523E-07 |
Керамическая связка |
0,2 |
900 |
790 |
2,81294E–07 |
Алмаз |
174 |
1700 |
670 |
0,000152766 |
Оксид железа |
80,4 |
7874 |
460 |
2,21974E–05 |
Карбид кремния |
490 |
3100 |
678 |
0,000233134 |
Кварцевое стекло |
1,38 |
2202 |
728 |
8,60856E–07 |
Нитрид кремния |
62,8 |
3440 |
800 |
2,28198E–05 |
Карбид бора |
121 |
2520 |
961 |
4,99645E–05 |
Нитрид бора |
41,84 |
2180 |
794 |
2,41721E–05 |
Карбид титана |
68 |
4920 |
649 |
2,12961E–05 |
Нитрид титана |
340 |
5440 |
598 |
0,000104515 |
Борид титана |
64,5 |
4380 |
636 |
2,31541E–05 |
Физический смысл коэффициента температуропроводности заключается в следующем:
dt |
|
∂2t |
|
∂2t |
|
∂2t |
|
– изменение температуры во времени. |
|||
|
= a |
|
|
+ |
|
|
+ |
|
|
|
|
|
|
2 |
|
2 |
|
2 |
|||||
dτ |
|
∂x |
|
∂y |
|
∂z |
|
|
|||
|
|
|
|
|
|
|
|
Эта формула показывает, что до наступления стационарного режима теплообмена температура зависит от коэффициента температуропроводности, от всех трех теплофизических свойств материала. Но, когда наступает стационарный режим, температура тела зависит
119
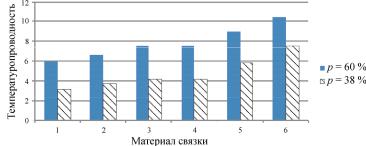
только от коэффициента теплопроводности. Поскольку стационарный режим теплообмена устанавливается только через несколько секунд после начала обработки, используем коэффициент температуропроводности.
На диаграмме покажем, как коэффициент температуропроводности зависит от изменения вида связки (рис. 110).
Рис. 110. Диаграмма изменения коэффициента температуропроводности: 1 – вулканитовая связка; 2 – бакелитовая связка; 3 – каучуковая связка; 4 – фенолформальдегидная связка; 5 – эпоксидная связка; 6 – керамическая связка
Из диаграммы видно, что с увеличением плотности связки он увеличивается.
Выполним расчет коэффициента температуропроводности, изменяя концентрацию алмаза с 38 % (структура № 12) до 60 % (структура № 1) в различных видах связки. Обрабатываемый материал – сталь 45, ϕд = –0,262, dA = –0,5, dZ = 0, dG = 0 (рис. 111).
Из рис. 111 видно, что с увеличением концентрации алмазов коэффициент температуропроводности увеличивается.
Выполним расчет коэффициента температуропроводности, изменяя концентрацию кварцевого стекла с 38 % (структура № 12) до 60 % (структура № 1) в различных видах связки. Обрабатывае-
мый материал – сталь 45, ϕд = –0,262, dA = –0,5, dZ = 0, dG = 0 (рис. 112).
120