
книги / Обработка резанием с вибрациями книга
..pdfизвестных смазочных сред в большей степени такому условию удовлетворяют суспензии на основе дисульфи да молибдена.
Результаты стойкостных исследований обычного и вибрационного сверления стали ЭИ654 на разную глу бину приведены в виде диаграмм на рис, 59. По оси ординат отложено количество просверленных отверстий, по оси абсцисс — номер смазочно-охлаждающей среды (табл. 20). Номер 6 соответствует работе всухую.
№
среды
J
2
3
4
5
Таблица 20
Составы смазочно-охлаждающих жидкостей, опробованные
при Стойкостных испытаниях
Состав среды |
|
Содержание |
|
|
компонентов в % |
||
Олеиновая кислота (техническая) .................... |
|
100 |
|
Сульфофрезол , ................................................ |
100 |
||
Сульфофрезол................................ |
... . |
, . . |
60 |
Керосин.............................................. |
« |
|
25 |
Олеиновая кислота |
|
15 |
|
Триэтаноламин........................................... |
|
* * |
0.2 |
Нитрит натрия................................................... |
|
|
0,15 |
Тринатрийфосфат............................................... |
|
|
0,3 |
Сода...................................................................... |
|
|
0,3 |
Бура...................................................................... |
|
|
0,5 |
Смачиватель ОП-7 |
|
|
0,1 |
В о д а ................................................................... |
|
|
98,45 |
Олеиновая кислота........................ |
* . . |
. - |
60 |
Керосин * ........................................... |
... |
|
30 |
Дисульфид молибдена....................................... |
|
10 |
Сверление производилось спиральными сверлами диаметром 1,5 мм из стали PIS. Предварительными ис
следованиями сверления стали ЭИ654 с олеиновой кислотой была установлена оптимальная геометрия за точки и режимы резания: 2<р—130°, ф=45°. Длина спи ральной части 15 мм; п = 1500 обjмин; SMuH=15 мм(мин; }—125 гц, Ля=0,01 мм. Вылет сверла во всех опытах при нят равным 20 мм. Из рис. 59 видно, что эффективность
действия сред № 1 — 4 приблизительно одинакова. Наи более эффективной при вибрационном сверлении ока
залась мОлибденйтойая суспензия (среда № 5), при этом ее эффективность значительно возрастает при пе реходе от обычного сверления к вибрационному, а так же с увеличением глубины сверления. Так, при глубине сверления 4—5 диаметров стойкость сверл при работе
с молибденитовой суспензией возросла в 10 раз по сравнению с вибросверлением в среде № 2 (сульфофрезол) и в 20 раз по сравнению с вибросверлением
Рис. 60. Кривые износа сверл при обычном и вибрационном свер лении:
/ — беа вибрации* с олеиновой |
кислотой: |
? — с вибрацией* |
с олеиновой ки |
|
слотой; 3 — без вибрации* |
с |
молибденовой суспензией; |
4 — с вибрацией, |
|
с |
молибденовой |
суспензией |
|
всухую, Дри увеличении глубины вибрационниго свер-, леиия со средами № 1—4 стойкость сверл (суммарная глубина сверления), как и при вибросверлении всухую, понижается. Иные результаты получены при работе с молибденитовой суспензией. При увеличении глубины вибросверления с 3 до 6 мм в случае ее применения
стойкость сверл даже несколько увеличилась. При глу бине 7,5 мм стойкость сверл уменьшилась незначитель
но. Это может быть объяснено различием в прочности на истирание смазочных пленок, возникающих от дей ствия молибденитовой суспензии и остальных сред.
На рис. 60 даны кривые износа сверл (а) и эффек тивность действия молибденитовой суспензии при уве личении глубины обычного и вибрационного сверления
(б) (с{в — сверление с вибрацией, б/в — без вибрации). Под эффективностью действия Э понимается отношение
количества просверленных отверстий с молибденитовой
суспензией Nм к количеству отверстий, |
просверленных |
с олеиновой кислотой Nu, выраженное |
в процентах, |
Э= ~ 100%. Как видно из графика, |
эффективность |
No |
|
действия молибденитовой суспензии увеличивается пря мо пропорционально глубине сверления, причем при сверлении с вибрацией эффективность выше приблизи тельно в 2 раза.
Анализируя полученные данные, можно сделать вы вод, что правильный выбор смазочно-охлаждающей среды позволяет значительно увеличить эффективность обычного сверления жаропрочных материалов. Задание вибраций в осевом направлении значительно повышает эффективность действия СОЖ, поэтому вибрационное резание в специальных средах является новым высоко производительным средством механической обработки деталей из труднообрабатываемых сталей и сплавов.
ВЛИЯНИЕ ОБРАБОТКИ РЕЗАНИЕМ С ВИБРАЦИЯМИ ИА КАЧЕСТВО ПОВЕРХНОСТИ И ЭКСПЛУАТАЦИОННЫЕ ХАРАКТЕРИСТИКИ ДЕТАЛЕЙ
Обработка резанием существенно изменяет эксплуа тационные свойства деталей, прежде всего за счет фор мирования определенного качества поверхностного слоя — его шероховатости и наклепа. Поэтому обработ ка резанием должна рассматриваться не только как способ получения деталей определенной формы и раз меров, но и как эффективный способ управления экс плуатационными качествами деталей. Освоение методов резания с вибрациями показало, что если вопросы ус тойчивого стружкодробления и точности размеров ре шаются практически достаточно легко и надежно, то обеспечение высокого качества поверхности требует тщательного внимания. Как показывают исследования, наличие вибраций может приводить как к катастрофи ческому ухудшению макро- и микрогеометрии поверх ности, так и сохранять ее почти неизменной или даже улучшать ее. Например, задание осевых низкочастот ных вибраций при сверленйи приводит к повышению чистоты поверхности, что позволяет исключить опера цию развертывания. Радиальные ультразвуковые коле бания [23] при точении с малыми подачами улучшают чистоту поверхности на один класс по ГОСТу 2789—59.
Выясним картину образования шероховатостей, пред ставляющих совокупность неровностей с относительно малым шагом. На черновых операциях шероховатость
поверхности в первом приближении образуется как гео метрический след рабочего движения резца относительно заготовки. При обычном резании шероховатость опре деляется подачей S0 и радиусом округленна режущей кромки г. При резании с вибрациями, кроме этих фак
торов, большое значение имеет кинематика движения, так как сложная траектория движения вершины инст румента развертывается на обработанной поверхности в виде шероховатостей различной высоты и направле ния. Наряду с этим, особенно при выполнении чистовых операций, высоту неровностей определяют также харак тер пластических деформаций в зоне резания, связан ный с неравномерным течением материала и наростом, явления упругого последействия материала поверхност ного слоя после прохода инструмента и высокочастот ные вибрации. Влияние скорости резания на чистоту поверхности связано с величиной образующегося на роста; в зоне максимального наростообразования полу чается наихудшан чистота поверхности. При обычном резании жаропрочных материалов максимальное наростообразование имеет место при крайне низких скоро стях резания (Ир«1 м[мин), поэтому для них повыше
ние скоростей резания во всех случаях ведет к повыше нию чистоты поверхности. На основании этого можно сделать вывод, что прирост скоростей и неравномер ность движения резания при обработке с вибрациями ведут к изменению условий формирования микронеров ностей.
Геометрическая картина образования шероховато стей приведена на рис. 61; для наглядности анализа принято <p=q>i; r=Û; фактическое синусоидальное дви жение резца заменено ломаным. Если частота вибра ций равна или кратна числу оборотов (см. рис. 61), то при движении резца с вибрациями в направлении по дачи его вершина перемещается по линии Oabcd, при
этом ширина основания |
1,2 остается постоянной и рав |
ной S 0. Следовательно, |
в этом случае изменяется |
внешний вид поверхности, однако высота неровностей остается постоянной и равной как при обычном точе нии. Если частота вибраций не равна и не кратна числу оборотов детали, то высота образующихся неровностей
становится переменной; максимальное значение ее пре вышает высоту неровностей при обычном точении. Это
ясно из рис. 61, когда за один оборот детали не укла дывается '/« длины волны К. Так как геометрический
закон изменения микронеровностей совпадает с зако-
ФернироОание шероховатостей |
Колебания Вершины |
V V V\A^лvvAv/ /\J \J \J \J \J \> J S^
Рис. 61. Кинематическая схема образования шероховатостей поверх ности при резании с вибрациями; типовые профилоТраммы поверх ностей
ном изменения снимаемой на каждом проходе толщи ны среза, средняя высота шероховатостей при резании с вибрациями остается равной, как при обычном резании. Но так как измерение производится на ограниченной
§ |
Н. Лодураер |
225 |
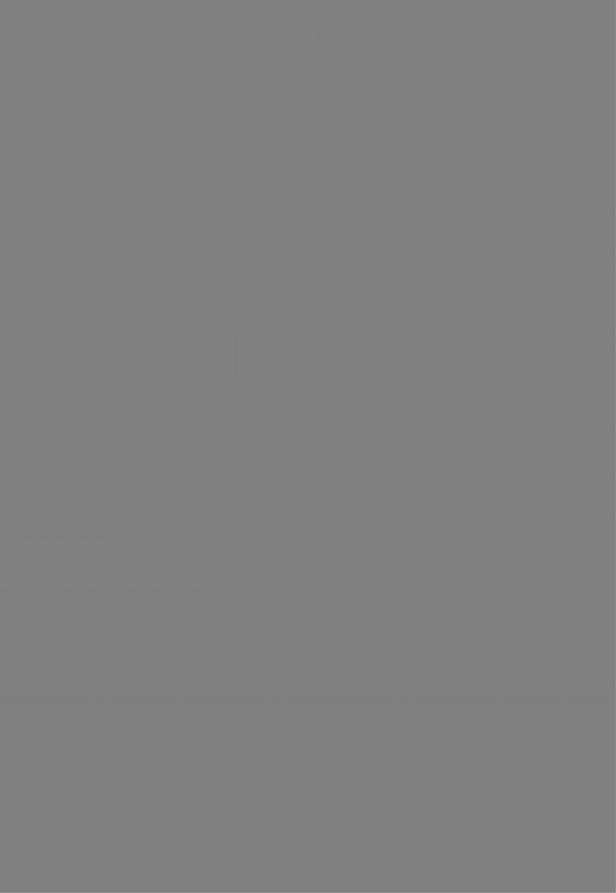
длине и на участке с наихудшей чистотой, обработка резанием с вибрациями показывает ухудшение чистоты поверхности. Участки наихудшей и наилучшей чисто ты на обработанной поверхности располагаются по винтовой линии (рис. 62); угол наклона определяется по формуле
X = arctg |
(4.17) |
2K/IS0
Из геометрической картины формирования микроне ровностей при резании с вибрациями высота образую щихся микронеровностей пропорциональна толщине сре заемого слоя, т. е.
*£ = Ч | So + 12А х sin -У- IJ - 2Ах s in - ^ |. (4.18)
Следовательно, высота микронеровностей поверх ности, обработанной с вибрациями, зависит от подачи на оборот, амплитуды колебаний и сдвига фаз коле баний. Так, при ф = 0 при резании с вибрациями полу чается чистота, одинаковая с обычным резанием, при тр=я — наихудшая чистота. Правильность изложенного подтверждают данные экспериментов по вибрационному точению валов при п —1500 об[мин, S u= 0,3 мм/об
(рис. 63). Чистота поверхности при экспериментах оп ределялась с помощью профилографа ИЗГМ7; на нем снимались профилограммы поверхности, которые далее подвергались обработке. Кроме того, для характери стики получающейся поверхности производилось фото-' графирование участков поверхности при значительном увеличении. Сравнение расчетных высот профилей с фактически записанными профилограммами указывает (см. рис. 61) на относительно меньшие величины нере гулярности. Это объясняется воздействием на процесс образования неровностей явлений пластического де-. формирования и упругого восстановления поверхности после прохода инструмента, они снижают нерегуляр ность микропрофиля, обусловленную только геометри ческой схемой формирования.
На основании приведенного рассмотрения можно рекомендовать для получения возможно высокой чисто ты поверхности задавать частоты вибраций, близкие к
числу оборотов детали |
п или кратные ему — . Для |
обеспечения дробления |
К |
стружки значения / должны |
Ю
Ю
СО
Размерная характеристика чистотыобработки
* 2
220
г о о
180
160
140
т
100
в о
60
40
20
о
|
|
п -640 об/мин |
|
||||
О—-с^2AX ~0t3nM |
|
Для всех |
|||||
| |
сj |
2Ajc=0,4ffH |
|
||||
|
£ |
|
|
|
|
у трех |
|
|
i. 2Ах=0Дмм |
|
случаев |
||||
|
)2Ах=0г6мн |
|
|||||
безвибраций |
|
г |
г |
||||
|
|
|
|
|
|
|
|
|
__^J H |
|
|
|
Л/ |
||
__iffIWI \ ^ |
I |
|
|||||
|
к |
|
\ |
|
|
||
|
|
Ш 1 |
|||||
i |
i £ 3 |
||||||
Et |
|
s v |
Ж Й |
\ |
|||
-VfrT"Hti |
|
||||||
è i |
|
C If |
1 |
|
|
Р
—Z 2 _ J
5 10) 15 20\/г
ц,= о
|
- - |
1 |
|
ч1- |
|
- |
|
|
|
|
Д |
|
|
Ï1 |
|
|
|
|
|
|
|||
|
л '1000об/мин |
|
|
|
|
||||||
|
Г- -Г\ |
|
|
|
|
|
|
|
|
/г |
|
|
/ |
\ |
|
|
|
|
|
|
/ |
|
|
|
/ |
\ |
|
|
|
|
|
|
|
i |
|
|
|
\ |
|
- | |
|
|
|
|
|
|
|
• |
к |
■ м |
\ |
|
|
/ |
|
|
|
/ |
|
Ji Л й |
V |
' |
\ |
А |
|
|
|
|
|||
|
|
|
|
? |
|||||||
/ |
К |
ч |
|
|
|
к |
|
|
/ |
||
|
|
\ъ |
Г |
/ |
/ |
|
|||||
И |
|
к |
|
у |
\ |
|
|
|
|||
М |
|
\ |
гр |
|
г | |
|
|
|
|||
|
|
Л |
|
|
|
Ï |
|
|
|
||
|
|
|
|
|
|
|
|
|
|
$ 10 1б\ 20/ гц
Частота осевых колебаний
л =1/40об/мин |
|
||
1 |
|
к |
j |
/г |
itми |
||
1i |
/ |
|
|
I£..N |
\ |
||
|
// |
||
|
_д_ |
||
~7 \\ |
|
||
1 |
\/1 |
1-*Г |
|
1 |
5/ |
||
пт |
|
i |
|
1 |
У\ |
|
4 н
15 20 / г ц
Рис.. 63 Зависимость чистоты поверхности от режимов резании и вибраций при использовании резцов с ра диусом (пунктирные линии) и с фаской (сплошные линии)
отличаться от — на 'небольшую |
величину — порядка |
|
К |
|
на |
5%. Амплитуда вибраций существенного влияния |
||
чистоту поверхности не оказывает. |
Учитывая это, |
во |
всех случаях для снижения динамического воздействия на станок значения f п Ах следует выбирать наимень
шими, обеспечивающими надежное дробление стружки. Рассмотрение экспериментальных данных по исполь зованию резцов с заточкой вершины по радиусу пока зывает, что чистота поверхности в зависимости от ре жимов резания и вибраций колеблется в пределах 2—4-го классов. Установление самых различных слу чайных режимов вибраций приводит к резкому ухудше нию чистоты поверхности, однако использование опти мальных режимов вибраций на основе изложенных рекомендаций ведет к сохранению чистоты поверх ности, получаемой при обычном точении, или незначи тельному ее понижению. Например, в производственных
условиях для |
режима резания я = 1250 о61мин, S 0 — |
=0,3 мм/об, |
при вибрациях с частотой* /= 2 0 гц, 2АХ~ |
=Q,325 мм получена чистота поверхности |
/?г= 39,8 мк, |
т. е. 4-го класса; в тех же условиях, но |
без вибрации |
получена Rz = 36 мк, т. е. того же класса. Аналогичные
результаты достигнуты и на других режимах резания. Для освоения точения с вибрациями применительно к получистовым операциям, т. е. для получения чистоты 5 и 6-го классов, были использованы резцы с заточкой вершины резца не по радиусу, а с фаской, т. е. резцы типа В. А. Колесова.
Картина получения наклепанного слоя при резании с вибрациями аналогична формированию шероховато стей. По мере резания образуется переменная глубина наклепа, пропорциональная толщине срезаемого слоя. Однако при последующих проходах, так как распрост ранение наклепанной зоны в глубь обрабатываемого материала значительно и имеется сдвиг фаз, зоны бо лее глубокого распространения наклепа перекрывают одна другую. Поэтому значительной неравномерности распределения наклепа по длине и глубине обработан ной поверхности ожидать не следует; при этом за счет некоторого циклического воздействия следует ожидать некоторого увеличения глубины. Правильность этого подтверждают данные экспериментов {14].
Вибрационное движение высокой частоты изменяет напряженное состояние в зоне резания. Знак остаточ ных напряжений, образующихся в поверхностном слое обработанной резанием детали, определяется знаком напряженного состояния этой поверхности в процессе резания *. Ранее было показано, что процесс пластиче ской деформации срезаемого слоя определяется дефор мациями сдвига и сжатия; вследствие этого при реза нии инструментами с положительными передними уг лами происходит интенсивное растяжение материала, формирующего поверхностный слой, образование зоны растягивающих напряжений.
На этот процесс накладывается явление «накатки»— уплотнение материала самого верхнего слоя, которое происходит при обычном резании только под действием определенного радиуса скругления режущей кромки р и контакта задней поверхности инструмента. Оно вызы вает образование зоны сжимающих напряжений. Соот ношение между размерами этих зон и действующими в них остаточными внутренними напряжениями опре деляется схемой обработки, режимами ее выполнения. Например, при обычном резании интенсивность явле^я накатки мала. Циклический характер взаимодействия обработанной поверхности с задней поверхностью ин струмента при резании с вибрациями значительно по вышает интенсивность этого явления прямо пропорцио нально частоте и амплитуде вибраций. Кроме того, при этом может иметь место качественный скачок, когда на части периода колебаний происходит резание с от рицательными задними углами.
Такие условия обработки создаются прежде всего при точении с радиальными ультразвуковыми колеба ниями. В этом случае циклический характер приложе ния сил при весьма интенсивном взаимодействии обработанной поверхности с задней поверхностью ин струмента обеспечивает существенное изменение напря женного состояния в формируемом процессом резания поверхностном слое в сторону образования поля сжи мающих напряжений; рост амплитуд колебаний интен сифицирует этот процесс. Поэтому при точении с уль-
1 Исключение из этого правила составляют только условия, об работки. например при шлифовании, приводящие к нагреву этого слоя выше точки Аса обрабатываемого материала.