
книги / Теория литейных процессов
..pdf7.5.2. Поверхностное расширение и ужимины
После заливки происходит интенсивная передача тепла металла в форму. Возникающий градиент температуры на поверхности формы вызывает неравномерное расширение отдельных слоев смеси.
Кварцевый песок является основным компонентом формовочной смеси и при повышении температуры расширяется, причем наиболее опасное расширение происходит до температуры 573 °С, при которой изменяется аллотропическая модификация песка.
Неравномерное расширение слоев смеси под поверхностью формы вызывает в ней напряжение, которое является опасным и может привести к повреждению формы. В зоне, где наблюдается наибольшее расширение песка (рис. 7.10), т. е. на поверхности формы, расширяющийся формовочный материал тормозиться соседними, слабоподвергшими действию тепла, слоями. В зоне возникает напряжение сжатия, которое при соответствующей конфигурации отливки переходит в напряжение, перпендикулярное к поверхности формы. Если это напряжение превысит жесткость напряженного слоя, то при определенных условиях (низкая прочность формовочного материала, влажность и газы) формовочный материал может вспучиваться и отслоиться. Этот механизм повреждения формы в литературе описывается как образование ужимин. Протекает этот процесс сложно, так как формовочная смесь представляет собой неоднородный материал, в котором при нагревании вначале происходит микрорасширение, вызывающее взаимное смещение зерен и частичное заполнение свободных пространств между ними, а лишь потом макрорасширение.
Рис. 7.10. Факторы, влияющие на образование ужимин: 1 - давление газов; 2 - сжимающее напряжение, обусловленное расширением зерен песка; 3 - растягивающее напряжение смеси; 4 - конденсационная зона; 5 - результирующая сила, вызывающая отслоение поверхностной корки смеси; б - направление перемещения поверхности расплава
Образованию ужимин способствуют слишком обширные горизонтальные стенки отливки при неправильно выбранном положении формы при заливке, а также неудачный выбор формовочной смеси, имеющей большое тепловое
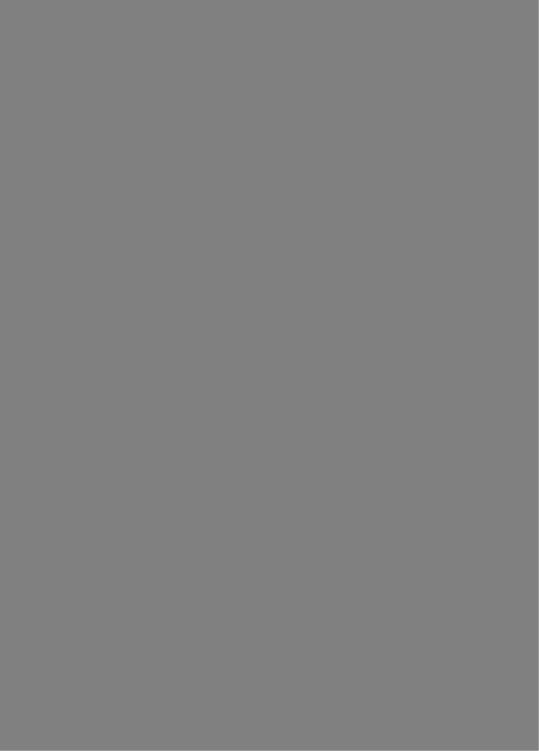
2N -» N2 (ситовидная пористость);
Водородная теория была применена для сплавов Mg, Al, Си, Fe, а азотная
-только для сплавов Fe.
2.Образование СО (только в сплавах железа). В расплаве присутствует кислород в форме оксидов. Содержание кислорода возрастает при контакте металла с формой, поскольку на поверхности отливки образуются оксиды FeO. При определенном содержании кислорода в металле происходит восстановление оксидов углеродом расплава по реакции
МеО + С (в металле) —>Me + СО (ситовидная пористость). Образовавшиеся пузырьки СО могут увеличиваться за счет диффузии
водорода, иногда других газов, которые в них ассоциируются в молекулы. СО как причина ситовидной пористости указывается для отливок из стали, высокопрочного и серого чугуна. В работах Гаака приводится теория возникновения ситовидной пористости в сером чугуне при наличии корольков внутри газовых пор вследствие протекания следующих реакций:
Fe203+3C (в металле) —►2Fe+3CO (ситовидная пористость)
или
2Fe20 3+3C (в металле) —>4Fe+3C02 (ситовидная пористость). Присутствующие СО или С02 образуют в пузырьках пленку графита.
3. Образование водяного пара. Эта гипотеза была предложена, в частности, для отливок Си, но была применена и для сплавов железа (для отливок из стали). Водяной пар образуется при повышенной температуре в сырой форме по уравнению
МеО + 2Н —►Me + Н20 (ситовидная пористость).
4. Образование сероводорода. Эта теория применяется специально для высокопрочного чугуна. При обработке чугуна магнием образуется MgS, который частисно остается в расплаве. При заливке в сырые формы происходит реакция
MgS + Н20 —>MgO + H2S (ситовидная пористость).
Таким образом, пористость в отливках из сплавов железа появляется главным образом при их изготовлении в сырой форме. Для стали наиболее важной причиной ситовидной пористости считают СО, в то время как в сером чугуне и, в особенности в высокопрочном, - водород. Однако механизм образования ситовидной пористости не является простым, на его возникновение оказывают влияние одновременно и другие газы: азот, водяной пар, углекислый газ и т. п.
Для предупреждения ситовидной пористости отливок производится тщательное раскисление металла и обеспечивается полная защита стали от воздействия влаги и водяного пара. Для этого необходимо хорошо просушивать футеровку печи и приспособления, которые входят в контакт с жидким металлом.
1.Природа газовой фазы при плавке металлов и сплавов.
2.В каком состоянии находятся газы в металлических сплавах?
3.Стадии взаимодействия газов с жидким металлом.
4.Закон абсорбции и Гснри-Далатсна и Сивергса.
5.Взаимодействие жидких металлов:
с водородом; кислородом; азотом.
6. Взаимодействие жидких металлов со сложными газами: оксидом углерода (СО); диоксидом углерода (С 02);
сернистым газом (S 02); метаном (СН4).
7. Какие материалы применяют для тиглей в печах?
8. Какие характеристики определяют огнеупорность материалов? Составы огнеупорных оксидных материалов?
9.Взаимодействие металлических расплавов с оксидными огнеупорными материалами и методы их устранения.
10.Явление смачивания и его влияние на взаимодействие расплавов с оксидной футеровкой.
11.Физико-химические и механические взаимодействия расплавов с формой (пригар, механическое воздействие давления расплава, химическое и физико-химическое воздействие, поверхностное расширение и ужимины, ситовидная пористость и причины ее возникновения).
Библиографический список
1.Гуляев Б. Б. Литейные процессы / Б. Б. Гуляев. - М. : Машиностроение, 1966.
2.Курдюмов А. В. Производство отливок из сплавов цветных металлов. Изд-е 2-е, доп. и перераб. / А. В. Курдюмов, М. В. Пикунов, В. М. Гурсин, Е. Л. Бибиков. - М. МИМиС, 1996.
Пикунов М. В. Теория литейных процессов: курс лекций / М. В. Пикунов. - М. МИСиС, 1991.
ГЛАВА 8. ФИЗИКО-ХИМИЧЕСКИЕ ОСНОВЫ РАСКИСЛЕНИЯ
ИРАФИНИРОВАНИЯ МЕТАЛЛИЧЕСКИХ РАСПЛАВОВ
8.1.Содержание газов в стали перед раскислением
Впроцессах выплавки стали в конвекторах, мартеновских и электродуговых печах до начала раскисления происходит непрерывное поступление газов в металл из печной атмосферы, шлака или непосредственно из газовой струи, вдуваемой в металлическую ванну.
Кислород. Особенности межфазового перехода кислорода в системах газовая фаза - оксидный расплав - металлический расплав связаны с различными формами его существования в фазах, наличием предела
растворимости в металлической фазе и возможностью выделения самостоятельной оксидной фазы основного металла.
При этом газовая фаза содержит кислород в виде молекул, а при очень высоких температурах - в виде атомов и ионов. Оксидный расплав содержит кислород в виде ионов О'2, переходящий в металл совместно с ионами основного металла Fe+2 или Си+2 для систем Fe-0 и Си-0 соответственно. Ионы других элементов в шлаке не участвуют в переходе в металл совместно с кислородом и влияют на равновесные характеристики через изменение активности распределяющих между шлаком и металлом кислорода или оксида основного металла.
Предельная растворимость кислорода в жидком металле в зависимости от температуры и состава шлака для систем Fe-0 и Си-0 может быть определена по их диаграммам состояния или по уравнениям
lg [О] = - 6320 / Т+ 2,734 или lg [0]£ *= - 6400 /Г + 0,756;
lg [о] ";с = - 6500 / Г+ 4,4688 (1356-1506 К); lg [О] "Г = - 3640 / Г+ 2,555 (1506 - 1700 К).
С понижением температуры жидкого металла растворимость в нем кислорода уменьшается. При 1650 °С растворимость кислорода составляет 0,276 %, при температуре кристаллизации - 0,17 %. При переходе железа в твердое состояние растворимость кислорода уменьшается скачкообразно. Растворимость кислорода в 5-Fe при температуре плавления (1538 °С) составляет 0,034 %, а далее при охлаждении она уменьшается в соответствии с
уравнением |
|
lg [0] = - 12630/Г + 5,51. |
(8.2) |
В y-Fe растворимость кислорода еще значительно ниже и составляет |
|
всего 0,003-0,004 %, в a-Fe - всего 0,002 %, причем |
она уменьшается с |
понижением температуры.
Все эти скачкообразные при аллотропических превращениях и постепенные в температурном интервале существования каждой из модификаций железа изменения растворимости кислорода приводят к
235
выделению из металла кислорода в виде дисперсной оксидной фазы. Чем меньше содержание кислорода, тем позднее начинается ее выделение. При относительно низких концентрациях кислорода его обособление в особую фазу происходит уже во время службы железного изделия. Протекает оно очень медленно, несколько быстрее при повышенных температурах металла.
Выделение кислорода в виде отдельной фазы при температурах прокатки или ковки может быть причиной плохой деформируемости стали в горячем состоянии и ее пониженной пластичности (особенно низкой ударной вязкости). Чтобы избежать всех этих неприятных явлений, необходимо уменьшить содержание растворенного в стали кислорода ниже предела его растворимости даже в охлажденном до минусовых температур (-30—40 °С) ct-Fe.
Для устранения всех отрицательных последствий присутствия кислорода сталь раскисляют с целью связывания растворенного в металле кислорода в прочные окислы, в большей части удаляющиеся из металла.
Азот и водород. Процесс растворения газов в металле является эндотермическим, поэтому с повышением температуры растворимость возрастает. Эндотермичность процесса объясняется тем, что расходуется энергия на разрыв связи между атомами в молекуле газов в жидком железе. Температурная зависимость константы растворения газов в жидком железе описывается выражениями
lg к Хз =(-770 /Т) -0,95; |
|
lg к„. = (-1900 / Т) + 2,47. |
(8-3) |
Согласно этим зависимостям, при 1600 °С |
к Хщ=0,044 % и |
КИщ=28,5см7100 г. Следовательно, |
|
[N] = 0,044 Тр Г ; [Н] = 28,5 |
(8.4) |
Фактическое содержание газов в стали во время плавки, как правило, ниже, а при вакуумировании выше значений, вычисленных по этим выражениям, так как равновесие между газовой фазой и металлом по распределению N2 и Н2 обычно не достигается ни во время плавки, ни при вакуумировании или обработке нейтральными газами. Кроме того, фактическое содержание газов может отличаться от данных [N] и [Н], определенных по формулам (8.4) вследствие влияния на растворимость газов (величины ЛГЛ. и
КИщ) содержания различных примесей.
Согласно известным исследованиям по этому признаку примеси можно делить на три группы: 1 - повышающие, II - снижающие, III - не изменяющие величины КХщ и K,h .
|
I |
II |
III |
*v. |
V, Nb, Cr, Та |
C, Si |
Mn, Mo, W, Cu, Ni, Со |
K„: |
РЗМ, Ti, V, Nb, Cr |
C, B, Si, Al |
Mn, Mo |
|
|
Растворимость водорода и азота в железе изменяется скачкообразно при переходе из жидкого состояния в твердое и при аллотропических превращениях в твердом состоянии. Причем высокотемпературная модификация <5-Fe растворяет меньше газов, чем низкотемпературная y-Fe (рис. 7.1 и 7.3).
Наиболее нежелательным является малая растворимость их в a-Fe, особенно в области низких температур. Фактическое содержание газов в стали обычно не превышает их растворимости в 5-Fe, но всегда выше их растворимости в a-Fe в области нормальных температур, поэтому возникает опасность выделения газов из твердой стали.
Для полного устранения этой опасности необходимо иметь в стали содержание азота не более 0,001-0,0015 % и водорода не более 1,0- 1,5см3/ 100 г. Такие низкие содержания газов можно обеспечить, если металл при плавке находится в равновесии с газовой фазой, в которой парциальное давление каждого газа не более 133,3 Па. Эти условия обычно не выполняются, поэтому необходимо нейтрализовать вредное влияние газов.
Газы могут находиться в следующих соединениях:
-на поверхности (за счет адгезии);
-в растворе в атомарной форме (истинная растворимость газов);
-в виде включений (оксидов, нитридов, гидридов);
-как реакционные газы.
Уменьшение давления газа в атмосфере, механические сотрясения (например, вибрация), усиленное механическое перемешивание ванны (индукционная и высокочастотная печь, ультразвуковая обработка) приводят к значительному уменьшению содержания газа в металле. Разливка при пониженном давлении (в вакууме) или при сильном механическом перемешивании (центробежное литье) сопровождается удалением газов и обеспечивает улучшение качества отливок.
8.2.Влияние газов на свойства стали
Содержание азота (%) в готовой стали в большой степени зависит от типа процесса:
томасовский |
0,015 - 0,020; |
|
бессемеровский |
0,01 - 0,015; |
|
электродуговой |
0,005 - |
0,01; |
мартеновский |
0,002-0,005; |
|
кислородно-конверторный |
0,002 - |
0,005. |
Это различие объясняется неодинаковыми условиями поглощения и выделения азота во время плавки.
В конверторных процессах с воздушным дутьем металл во время плавки непосредственно взаимодействует с газовой фазой, имеющей высокое парциальное давление азота (Рх%= 0,065-0,085 МПа), и интенсивно поглощает
его.
В мартеновском процессе условия для поглощения азота менее благоприятные, так как металл отделен от газовой фазы слоем шлака (по крайней мере, в период доводки), который является почти непроницаемым для азота (шлак растворяет азот в незначительных количествах). Кроме того, в результате кипения ванны пузыри СО уносят азот из металла в газовую фазу, поэтому в мартеновской стали наблюдается низкое содержание азота при высоком парциальном давлении его в газовой фазе.
Вдуговой электропечи условия близки к мартеновским, электрическая дуга оказывает активизирующее действие на азот, что приводит к повышению его концентрации в металле.
Вкислородных конверторах содержание азота зависит от концентрации его в дутье, причем при высокой температуре в зоне взаимодействия дутья и металла (> 2000 °С) по распределению азота между металлом и газовой фазой достигается равновесие.
Сравнение данных о содержании азота в стали, полученной различными способами, с растворимостью этого газа в железе показывает, что остаточное
содержание N, как правило, меньше его растворимости не только в y-Fe, но даже в 5-Fe, поэтому при затвердевании металла азот может оставаться в растворе, но при превращении y-Fe в a-Fe и дальнейшем охлаждении a-Fe растворимость азота становится значительно меньше фактического содержания его в металле. Следовательно, создаются условия для выделения азота из твердого раствора. Однако эти термодинамические возможности не реализуются, и азот остается в твердом растворе, образуя пересыщенный раствор. Такой раствор сохраняется в течение многих лет.
Однако выпадение азота из твердого раствора возможно при штамповке с большой скоростью и при работе готовых изделий при повышенных температурах. Выпадение азота из раствора снижает пластичность, прочность стали, и этот процесс называется старением. Оно является одним из серьезных пороков, вызываемых повышенным содержанием азота.
Для устранения этого влияния в сталь вводят элементы Si, Al, V, Ti, Zr и др., резко снижающие растворимость азота в жидком железе. При этом основное количество азота выпадет из раствора в виде первичных и вторичных нитритов, а остаточное содержание его в растворе не превышает растворимости в твердом железе при обычной температуре и не может вызывать старения.
Выделяющиеся из раствора нитриды (Si3N4, AIN, VN, TiN, ZnN) в большей части фиксируются в объеме затвердевшего металла в виде неметаллических включений, которые в меньшей степени снижают качество стали.
С повышением содержания азота понижается пластичность стали, но возрастают ее прочностные и другие характеристики, поэтому азот в некоторых случаях является полезной примесью стали. Азот вводят (0,015 - 0,03 % и выше) в сталь в виде азотированных ферросплавов (FeCr, FeV и др.).
Содержание водорода в стали в конце плавки мало зависит от типа процесса и обычно составляет 3-6 см3 / 100 г металла. Это значительно выше растворимости его в a-Fe.
Все гидриды металлов не устойчивы, поэтому разлагаются. Водород выделяется из металла в виде газа, как правило, в области температур 800-950 °С (после окончания прокатки или плавки).
Выделение Нз может вызывать образование внутренних трещин, называемых флокенами. Значительной склонностью к образованию флокенов обладают обычно легированные стали.
Д. Я. Полоцкий и А. Н. Морозов установили, что образование флокенов исключается при содержании водорода в стали не более 1,5- 2,0 см3 / 100 г.
Получение такого низкого содержания водорода открытыми процессами плавки стали невозможно, поэтому для уменьшения возможности образования флокенов в стали необходима дегазация металла путем вакуумирования или медленного охлаждения заготовок (слитков) в специальных камерах (обычно в течение трех суток). В последнем случае выделение водорода протекает с такой малой скоростью, при которой образование флокенов исключается.
При повышенном содержании водорода в легированных сталях также наблюдается развитие легированный металл в изложнице «растет» подобно кипящему или полуспокойному.
Высокопроцентный ферросилиций всегда имеет повышенное содержание водорода, так как может поглощать его из атмосферы, образуя гидриды SiH4.
Наиболее эффективными способами снижения отрицательного влияния водорода на качество стали является вакуумирование или обработка нейтральным газом. При этом достигается удаление водорода до 60-80 % и более, тогда как азот удаляется на 10-20 %. Такая высокая степень удаления водорода объясняется малыми размерами его частиц в жидком металле и высоким значением коэффициента диффузии Д[Н] = 2,5*10'2 см2/с, тогда как Д[1Ч] = 6*10'4см2/с.
Высокая эффективность удаления водорода при продувке металла нейтральным газом наблюдается в том случае, если над металлом нет печного шлака, который имеет высокое содержание водорода и снижает эффективность продувки.
Степень удаления водорода из металла при открытой плавке (Я=0,1 МПа) во время продувки газом зависит от начальной концентрации его и расхода газа. Эта зависимость может быть описана формулой шиферного (каменисто слоистого) излома и некоторых других видов порока. Например, при введении в металл большого количества предварительно не прокаленного богатого ферросилиция, содержание водорода в жидкой стали повышается до значений выше растворимости в 8-Fe. В этом случае наблюдается выделение водорода
уже в процессе кристаллизации слитка: |
|
Киг*5,5(1/[Н]к)-(1/[Н ]и), |
(8.5) |
где Vur - расход газа, м7т; [Н]„ и [Н]к - начальное и конечное содержание Н2 в металле, мл/ 100 г.
При продувке под вакуумом расход газа существенно уменьшается, так как он прямо пропорционален внешнему давлению:
(8.6)
где К™ - расход газа при продувке в условиях вакуума, м3/т; Vlir - расход газа при продувке в открытом ковше СР=0,1 МПа); Р - остаточное давление в вакуумной камере, кг/см2
При Р=0,4-0,5 кг/см2 расход газа уменьшается в 2 раза. Следовательно, эффективность дегазации металла может быть повышена при комбинированном применении продувки аргоном и вакуумирования.
8.3.Влияние газов на свойства чугунов
Водород. Растворимость водорода в железных сплавах увеличивается при движении слева направо в следующем ряду:
A g - P t - C u - F e - N i - P d - V - T a - T i - Z r - C e .
Начиная с 700 °С, поток водорода вызывает заметное обезуглероживание поверхности железоуглеродистых сплавов, особенно при повышенных давлениях. В результате образуется метан:
Fe3C + 2Н2 = 3Fe + СН4 |
- |
белый чугун. |
С + 2Н2 = СН4 |
- |
серый чугун, ковкий чугун. |
Серый чугун обезуглероживается более интенсивно, чем белый, так как больше их диффузионная подвижность в этих чугунах.
Скорость обезуглероживания значительно увеличивается при добавлении около 2 % (объемного) водяного пара. В чистом водороде скорость обезуглероживания определяется только скоростью химической реакции между С и Н, а в окислительной атмосфере, напротив, лимитируется в основном скоростью диффузии углерода в железе.
Скорость обезуглероживания железа во всех газах или смесях газов определяется процессом диффузии, если скорость химической реакции газов с углеродом выше скорости диффузии самого углерода.
Процессы обезуглероживания серого чугуна нашли практическое применение (английский патент, фирма General Motors Согр.), согласно которому предусматривается отливка тонких деталей из СЧ (2,5-4,3 % С, - 1 % Si и Мп, 0,35-0,55 % V), дальнейшее обезуглероживание во влажном водороде при 870-1100 °С для получения желаемой вязкости.
Проникновение водорода в серый чугун приводит к восстановлению оксидных включений, которые оказывают активное зародышевое влияние, и уменьшают степень переохлаждения при эвтектической кристаллизации.
Содержание Н2 в сером чугуне - 15-65 см7на 100 г.