
книги / Нанодисперсные и гранулированные материалы, полученные в импульсной плазме
..pdfпри металлизации А120 3 содержание никеля с 20 уменьшалось до 17,8 % масс, за один цикл плазменной обработки идо 15,1 % масс, за четыре цикла металлизации. В связи с этим для получения композиции заданного состава в исходной шихте необходимо иметь некоторый избыток металлической составляющей.
В результате плазменной металлизации существенно изменяются свойства порошковой шихты: улучшается текучесть металлизированных порошков и увеличивается их насыпная плотность (табл. 4.2). Улучшение такого важного технологического показателя, как текучесть, делает полученные в импульсной плазме композиционные порошки весьма перспективными по сравнению с ме ханическими смесями того же состава при использовании в процессах, требую щих обеспечения непрерывной и равномерной подачи порошка. Изменение те кучести композиционного дисперсного материала связано, по-видимому, как с процессом металлизации, так и со сфероидизацией частиц в ходе плазменной обработки. Увеличение числа циклов плазменной обработки (проходов шихты через разрядный промежуток импульсного плазмотрона) помимо возрастания выхода магнитных частиц (степени металлизации) приводит к усреднению ме таллической фазы в обрабатываемых порошках. Об этом говорят гистограммы перераспределения магнитных свойств шихты, свидетельствующие о постоян но увеличивающемся с числом циклов плазменной обработки количестве час тиц с одинаковыми максимальными магнитными свойствами (рис. 4.19).
Таблица 4.2. Физико-технологические свойства металлизированных порошков
Материал |
Насыпная плотность, г/см3 |
Текучесть, с |
Механическая смесь WC—Со |
5,71 |
10 |
Металлизированный WC |
6,24 |
3 |
Механическая смесь НС—Ni |
1,70 |
— |
МеталлизированныйTiC |
1,95 |
68,5 |
3 |
3,74 |
- |
Механическая смесь Cr C2—Ni |
28,3 |
|
Металлизированный Сг3С2 |
4,15 |
|
Механическая смесьА1203—Ni |
1,25 |
— |
МеталлизированныйА1203 |
1,53 |
92 |
Максимальная степень металлизации проявляется при введении в импульс ную плазму оптимальных количеств обрабатываемой смеси порошков. При вы сокой степени загрузки импульсной дуги дисперсной фазой, по-видимому, снижаются эффективность на1рева компонентов исходной шихты и полнота перехода металлической компоненты в жидкую и паровую фазы, что сказыва ется на процессе металлизации и его показателе —выходе магнитных частиц (рис. 4.20). С увеличением энергии импульсной плазмы наблюдается сдвиг максимума зависимости выхода магнитных частиц от расхода порошка в сторо ну больших значений.
Z41
Массовая доля |
Число циклов |
магнитных частиц, % |
обработки |
100
50
100
50
100
50
100
50
Усиление магнитных свойств
Рис. 4.19. Пютограммы перераспределения магнитных свойств металлизированного никелем порошка оксида алюминия
Рис. 4.20. Зависимость выхода магнитных частиц после плазменной обработки от расхода шихты при разной энергии импульса плазмы: / - W=450 Дж; 2 ,3 - W= 600 Дж: 1,2 - TiC + Ni (20% масс.); 3 - СГ3 С2 + Ni (20% масс.)
Некоторый рост выхода магнитных частиц с увеличением расхода исходной смеси порошков может быть связан с возрастающей при этом вероятностью ге
терогенной конденсации паров металла на керамических частицах за счет уве личивающегося их количества в газодисперсном потоке и возрастанием степе ни использования образовавшегося при импульсном воздействии на исходную шихту металлического пара.
Таким образом, проведенные эксперименты по металлизации керамических порошков выявили зависимость результатов обработки от:
1)расхода керамического порошка и его дисперсности, определяющих веро ятность гетерогенной конденсации на частицах керамики металлизирующего компонента из паровой фазы и эффективность нагрева дисперсных компонен тов исходной шихты;
2)дисперсности и концентрации металла в газодисперсном потоке, опреде ляющих эффективность испарения металла под воздействием импульса плазмы
иего концентрацию в газовой фазе;
3)энергии разряда, определяющей полноту перехода металлической компо ненты в жидкую и паровую фазы;
4)числа циклов обработки, определяющего кратность плазменного воздействия на компоненты шихты. От его увеличения возрастает степень металлизации и рав номерность распределения металла по поверхности металлизированных частиц.
На основании этих данных могут быть построены диаграммы выбора опти мальных условий процесса металлизации керамических частиц (рис. 4.21).
Повышение эффективности модифицирующей обработки порошков в им пульсной плазме связано не только с подбором оптимальных условий ее прове дения, но и с аппаратурным оформлением процесса.
Для снижения числа циклов плазменной обработки, необходимого для по вышения степени металлизации керамического порошка и связанного с пере загрузкой шихты после каждого из них, была создана двухканальная импульс ная плазменная установка. Принцип работы ее основан на последовательном прохождении газодисперсным потоком обрабатываемого вещества двух неза висимых импульсных дуг [1.59, 1.81].
Установка представляет собой два независимых малоиндуктивных генера тора импульсных токов, разряжающихся на импульсные дуги в плазмохими ческом реакторе между высоковольтными электродами и заземленным корпу сом. Важной частью источников питания установки являются блоки питания БП-5000-3,6, обеспечивающие зарядку емкостных накопителей энергии (ЕНЭ) постоянным током, выбор и поддержание режима работы установки, управление разрядом ЕНЭ на нагрузку путем подачи управляющих импульсов на ГИИ.
Функциональная схема блока питания приведена на рис. 4.22. Напряжение се ти 380 В через цепь блокировок подается на выход источника тока ИТ-З-ЗФ и пре образуется в переменный ток неизменной величины, который затем преобразуется
Рис. 4.21. Зависимость выхода магнитных частиц (степени металлизации а) от расхода исходной шихты Gaи энергии импульса плазмы И'для шихты: а - TiC - 20 % масс. Ni; б - А12 0 3 - 20 % масс. Ni
Рис. 4.22. Схема блока питания двухканальной импульсной плазменной установки
в постоянный ток неизменной величины с помощью выпрямителя ВЗ-5000-ЗФ. Емкостный накопитель заряжается постоянным током в течение времени зарядки:
т3 |
(4.1) |
где С —емкость накопителя; Uc - напряжение на накопителе; /3 —ток зарядки на выходе блока питания.
Допустимая частота F циклов зарядки-разрядки определяется по формуле
т3 + т6 + 0,0Г
где т3 —время зарядки накопителя, с; т5—длительность блокировки зарядки нако пителя (0,012 с), которая устанавливается при регулировании системы управления.
На выходе выпрямителя установлен делитель обратной связи, сигнал с которо го, пропорциональный напряжению на накопителе, поступает в систему управле ния. Здесь он сравнивается с заданным напряжением. Когда напряжение на нако пителе достигает заданного уровня, система управления СУМ-10А начинает выра батывать сигналы, поступающие на зарядный коммутатор в источнике тока, про цесс зарядки прекращается. Через 4 мс после окончания зарядки система управле ния вырабатывает сигнал «поджиг», поступающий на блок разряда (БР). СУМ-10А задает один из режимов работы: а) заряд или разряд накопителя синхронизируется от внутреннего генератора тактовых импульсов прибора; б) заряд или разряд нако пителя синхронизируется от внешнего датчика. Блок разряда предназначен для преобразования выходного сигнала «поджиг» блока питания и подачи управляю щих импульсов на первичную обмотку импульсного трансформатора (ИТ).
Генератор импульсных токов собран на конденсаторах марки К75-15 (1 мкФ, 10 кВ) емкостью до 10 мкФ при запасаемой энергии на ЕНЭ 125 Дж на каждый канал. Ошиновка —плоская, с центральным расположением камеры реактора, что позволило снизить индуктивность разрядного контура до 0,6 мкГн и повы сить энерговклад в импульсную дугу реактора. Конструктивно разрядная схема на оба канала вместе с реактором и ГИИ выполнена в виде отдельного модуля размерами 700 х 700 х 600 мм.
Двухканальный реактор имеет цилиндрический корпус, внутри которого на изоляторах расположены два высоковольтных водоохлаждаемых трубчатых электрода. Во фторопластовых изоляторах предусмотрены отверстия для ввода газодисперсного потока сырья и вывода продуктов в сборник.
На установке проводились процессы плазменной обработки газодисперсно го сырья и получены дисперсные композиционные гранулированные материа лы А120 3—Ni, WC—Со. Равномерность обработки потока и постоянство пара метров разрядов обусловливают однородность продукта плазменной обработки по размерам, составу и свойствам. Использование двухканальной установки позволяет снизить число циклов плазменной обработки и тем самым повысить эффективность плазменной металлизации керамики.
4 .4 . Модифицирование углеродных материалов в импульсной плазме
В современном производстве композитов на основе углеродных волокон (УВ) определилась тенденция, в основе которой лежит подход, связанный с разработ кой методов модифицирования поверхности УВ, в том числе с использованием высококонцентрированных потоков энергии (ВПЭ) с целью улучшения их адге зионной прочности соединения с матрицей [4.36—4.38]. В ряде случаев предлага емые методы поверхностной обработки, улучшая прочность сцепления волокна и матрицы, приводят к некоторому снижению прочностных характеристик собственно волокна. Так, поданным [4.38], в Японии используются промышлен ные технологии модифицирования поверхности УВ, улучшающие свойства ком позита, изготавливаемого из обработанных волокон, но одновременно приводя щие к потере прочности волокон на разрыв примерно на 30 %. В таком подходе нет противоречия, поскольку прочность УВ составляет 1000 МПа и значительно превышает прочность углерод-углеродных композитов на его основе, для кото рых характерная сдвиговая прочность составляет десятки мегапаскалей.
Предложено большое количество методов модифицирования УВ с целью улучшения прочности сцепления их с матрицей и повышения уровня прочнос ти композитов [4.39-4.43]. В основе всех этих способов лежат два типа измене ний, привносимых в УВ в процессе обработки:
—изменение рельефа поверхности УВ;
—изменение химического состояния поверхности УВ, под которым подразу мевается как качественное и количественное изменение состава функциональ ных групп, привитых на волокно, так и изменение структуры поверхности собственно УВ в ходе модифицирующей обработки.
Изменение химического состояния поверхности (ХСП) оказывает влия ние на прочность композита, изменяя не только непосредственно химичес кое взаимодействие волокна с матрицей, но и поверхностную энергию во локна, повышение которой является предпосылкой хорошей адгезии в этой системе [4.44].
Был исследован процесс модифицирования УВ «Урал Н-24», изготавливае мых из вискозной нити, в импульсной плазме аргона и водорода1. Энергия еди ничного разряда продолжительностью 10~4...1(Г5 с составляла от 25 до 40 Дж. Нить протягивалась через зону разряда со скоростью, обеспечивающей пяти шести кратное воздействие импульсного разряда на единицу поверхности жгу та волокон [4.45 ,4.46].
Топографические изменения рельефа поверхности волокна в ходе модифици рующей обработки оценивались с использованием растровой и просвечивающей электронной микроскопии. Для количественной оценки изменения рельефа по верхности волокон измерялась площадь их удельной поверхности методом БЭТ.
Определение поверхностной энергии углеродных моноволокон проводилось гравиметрическим методом с использованием однокомпонентных полярных и неполярных (углеводородных) жидкостей марки ЧДА, характеристики которых приведены в табл. 4.3.
Таблица 4.3. Принятые в |
расчетах дисперсионные, |
полярные и полные силы |
поверхностного |
|||
натяжения реактивов, 1(Г Н/ои |
|
|
|
|||
Характеристика |
Гексан |
Октан |
Декан |
Вода |
Формамид |
|
используемых |
||||||
жидкостей |
|
|
|
|
|
|
Y Î |
18,4 |
21,3 |
23,4 |
21,8 |
39,5 |
|
YL |
0 |
0 |
0 |
51,0 |
18,7 |
|
18,4 |
21,3 |
23,4 |
72,8 |
58,2 |
||
УI |
В применяемой методике [4.47] использовали представление о том, что силы Ван-дер-Ваальса, определяющие закономерность смачивания в отсутствие хи мического взаимодействия жидкости с волокном, можно разделить на три ви да: дисперсионные; ориентационные, или полярные; индукционные, или наве денные.
1 Использовались газы техническойчистоты, осушенные пропусканием надКОН и Р2О5.
Обычно влиянием индукционных сил пренебрегают. Тогда работу адгезии можно представить в виде двух составляющих: W= /£ + I SL,P где I°sL —вклад дисперсионной составляющей и I fLS —вклад полярной составляющей.
Для предельных углеводородов вследствие практически одинаковой элекгроотрицательности водородных и углеродных атомов взаимодействие при сма чивании ими поверхностей твердых тел определяется только дисперсионными силами: yL= у£, где yL—поверхностная энергия жидких углеводородов; у°L — дисперсионная составляющая поверхностной энергии этих жидкостей.
Из теории Лондона, описывающей дисперсионное взаимодействие [4.44,
4.47], выражение для |
на границе раздела твердое—жидкость имеет вид |
|
(4.3) |
где Yi ,У° —дисперсионные составляющие поверхностной энергии смачиваю щей жидкости и твердого тела, соответственно.
Таким образом, измерив величину энергии межфазного взаимодействия твердого тела (волокна) с несколькими неполярными жидкостями, для которых известно y°L =yTL , можно определить у? • Для этого использовали известное соотношение для W
и строили график в координатах у£ (1+cos 0)- 2yjÿ* . Тангенс угла наклона полу
ченной линейной зависимости был равен 7Ÿ? • Определить краевой угол смачивания 0 углеродных волокон прямым мето
дом чрезвычайно трудно. Для этого использовался гравиметрический метод, в котором углеродное волокно подвешивается к кронштейну весов и приводится в соприкосновение с жидкостью.
При погружении и выходе волокна на поверхность жидкости по показани ям весов фиксируется сила F, связанная с массой жидкости1, поднимающейся над поверхностью раздела воздух—жидкость: F = Cy^cosB, где С —периметр волокна, а 0 —краевой угол смачивания жидкостью волокна в воздухе или в па ре жидкости [4.44]. Для определения периметра волокна проводятся гравимет рические измерения при погружении волокна в углеводородную жидкость, ко торая характеризуется абсолютной смачиваемостью углеродного волокна, т.е. cos 0 = 1.
1 Подъемной архимедовой силой, действующей волокно, погруженное в жидкость, пренебрега ем в силу малости этой величины.
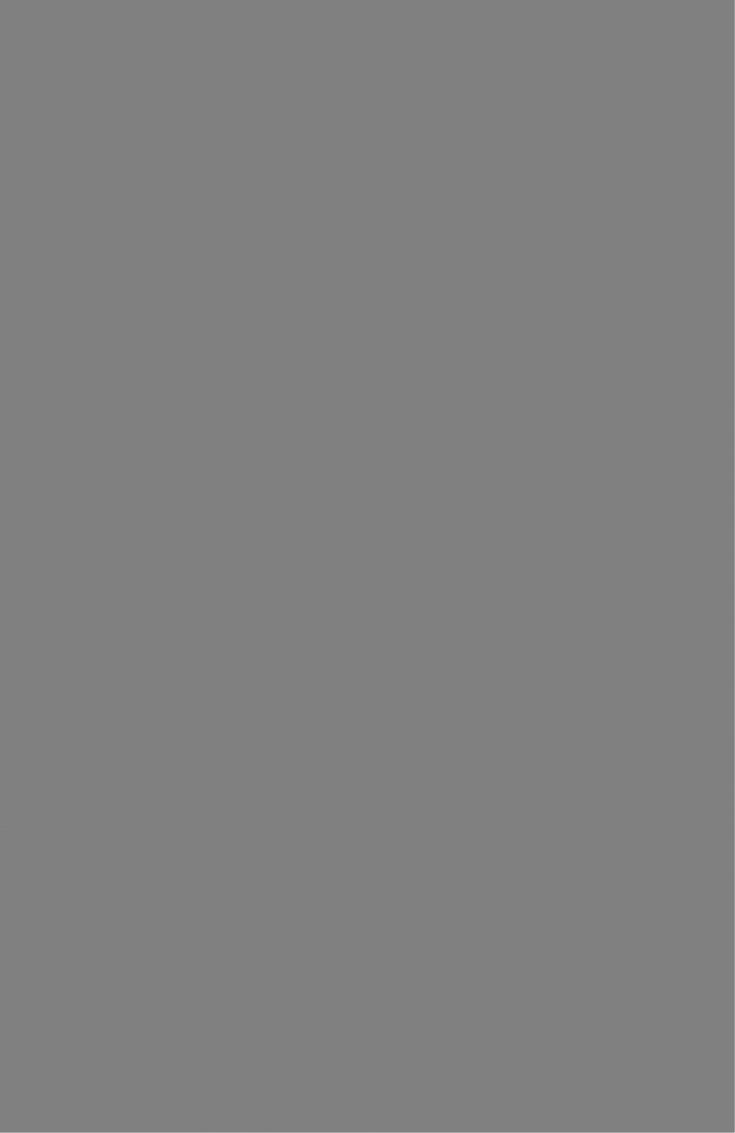
Результаты экспериментов по определению |
и yps для УВ «Урал» до и пос |
ле модифицирующей обработки в импульсной плазме представлены в
табл. 4.4.
2
Таблица 4.4. Поверхностная энергия УВ «Урал» до и после обработки в импульсной плазме, мДж/м
Характеристика |
|
|
т |
материала |
TÎ |
T Î |
УS |
До обработки |
21,1±3,1 |
15,8±2,5 |
36,9+6,0 |
После обработки в ИП: |
|
22+2,8 |
51±5,7 |
аргона |
29±2,9 |
||
водорода |
30,2±2,8 |
18,5+2,3 |
48,7±5,1 |
Данные по измерению поверхностной энергии УВ «Урал» свидетельствуют, что после модифицирующей обработки УВ увеличивается значение yf, что предполагает хемосорбцию на их поверхности полярных функциональных групп. Прививка функциональных групп на волокнах, обработанных в восста новительной и нейтральной средах, происходит, по-видимому, при контакте их с воздухом. Увеличение сорбционной способности УВ связано с нарушениями, привносимыми в структуру поверхности в процессе обработки УВ в импульс ном разряде.
Дисперсионная составляющая поверхностной энергии при обработке УВ из менилась незначительно. Аналогичные зависимости наблюдались и для высо копрочного волокна Т-300 в исследованиях Доннета [4.38] с соавторами. Уве личение значения у£ связывается со стравливанием с поверхности УВ слоев уг лерода, плохо сцепленных с УВ.
С помощью метода РФС, используя данные работ [4.36,4.49], нами была оп ределена природа хемосорбирующихся на поверхности УВ функциональных ipynn, ответственных за возрастание полярной составляющей поверхностной энергии при модифицирующей обработке УВ в импульсной плазме.
Для анализа состава функциональных групп использовалась методика диффе ренциального анализа рентгеновских фотоэлектронных спектров линии С Is УВ. Различие в спектрах УВ до и после обработки определялось вычитанием конт рольного спектра С Is исходного волокна и спектра модифицированного УВ. Этот метод базируется на представлениях о влиянии разных по природе функци ональных групп на энергию связи Is электронов углерода, которая фиксируется в эксперименте. В основе этой методики лежат представления о том, что:
- энергия связи Is электронов атома углерода, связанного только с углерод ными или водородными атомами, одинакова и равна 284,6 эВ;
- связь углеродного атома с атомами кислорода приводит к химическому сдвигу линии C ls в сторону больших энергий связи примерно на 1,5 эВ на каж дую связь.