
книги / Нанодисперсные и гранулированные материалы, полученные в импульсной плазме
..pdfния, процесс восстановления определяется в основном электрофизическими свойствами материала: шириной запрещенной зоны и температурой перехода от примесной к собственной проводимости. Так, установлено, что ширина за прещенной зоны зависит от природы химической связи, ее прочности и харак тера химической связи.
В полупроводниковых веществах с ростом доли ионной связи увеличивается степень асимметрии электронного облака, которое смещается в сторону анионообразователя, а это приводит к росту ширины запрещенной зоны. Но при нагревании связи в решетке настолько нарушаются, что создаются благоприят ные условия для процессов диффузии и отрыва отдельных частиц (возгонка, диссоциация). Температура, отвечающая этому состоянию, зависит главным образом от природы оксида, ширины запрещенной зоны, т.е. энергии его крис таллической решетки. Таким образом, реакционная способность оксида, или способность его начинать взаимодействовать с восстановителем, определяется его природой, физическим состоянием.
Рассмотренные механизмы взаимодействия импульса плазмы с оксидом на различных стадиях восстановления свидетельствуют о том, что в реакционном объеме существуют неодинаковые условия протекания восстановительных процессов из-за неодинакового термического воздействия, которому подверга ются частицы восстанавливаемого оксида при создании импульсов плазмы.
Гпа в8 4
ПОВЕРХНОСТНОЕ МОДИФИЦИРУЮ Щ ЕЕ ВОЗДЕЙСТВИЕ
ИМПУПЬСНОЙ ППЛЗМЫ НА ВЕЩЕСТВО
Одним из современных направлений материаловедения, химии и физики твердого тела является создание и исследование поверхностных микроструктур различных материалов, получаемых под воздействием высококонцентрирован ных потоков энергии.
Возникновение фазовой и структурной неоднородности на внешней поверх ности сопровождается активирующим действием поверхностных состояний на кинетику твердофазных превращений и процессов с участием газовой фазы, влияет на термомеханические и электрофизические свойства материалов.
Наряду с обработкой поверхности компактных материалов интерес проявля ется к проблеме модифицирования порошков, используемых в ряде процессов в дисперсном состоянии (катализаторы, порошки для напыления и др.) или служащих исходным сырьем для порошковой металлургии [4.1, 4.4, 4.28]. Так же как и у компактного материала, свойства порошков во многом зависят от свойств поверхностных слоев частиц.
Необходимость равномерного воздействия на всю поверхность каждой из обрабатываемых частиц всего ансамбля порошка при использовании энергии электронного луча и лазерного излучения для такой обработки приводит к зна чительным техническим трудностям аппаратурного оформления процесса. По этому в большой степени интерес проявлен к методам модифицирования, ос нованным на применении низкотемпературной плазмы.
4 ,1 Структуре- и ф азообразование в частицам иорошмов под воздейст вием плазм енны х пот оков
Исследованию поведения порошков карбидов в плазменных струях посвя щен ряд работ [4.2—4.71]. В работе [4.5] изучали процесс сфероидизации и свой ства продуктов обработки в аргоновой плазме порошков карбидов титана, вольфрама и хрома с размером частиц 40...80 мкм. Исходные порошки предс тавляли собой пористые частицы произвольной формы с развитой поверх ностью. После обработки частицы порошка имели округлую форму и сглажен ную поверхность. Мелкие частицы в результате плазменной обработки не толь-
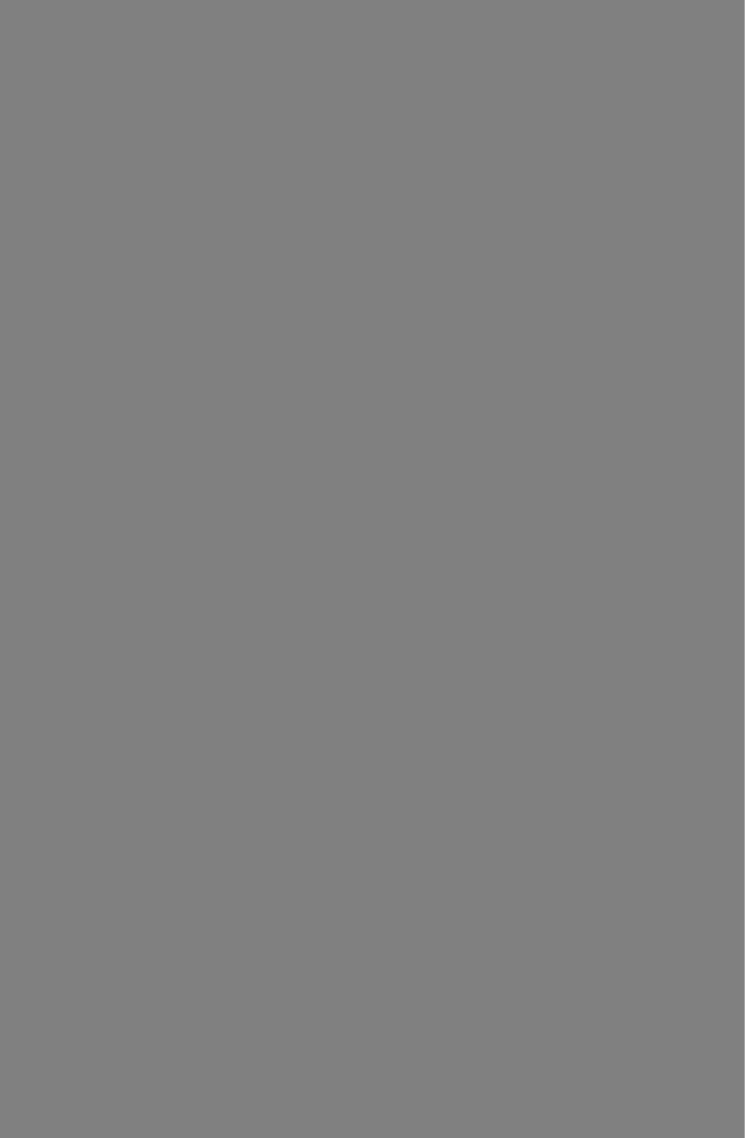
ются линии рентгеновской дифракции, соответствующие W2C и W, а в случае Сг3С2 —линии, соответствующие Сг7С3 и Сг. Такой характер изменения ста бильности карбидов переходных металлов IV—VI групп при плазменной обра ботке, по мнению авторов, связан с различием электронного строения карби дообразующих металлов и изменением их свойств, характеризующих проч ность кристаллический решетки.
Для фракционированных обработанных карбидов, имеющих область гомо генности, наблюдается увеличение степени обезуглероживания с уменьшением размера зерен продукта.
Наиболее высокие значения степени сфероидизации по фракциям (до 80 %) получены для WC и Сг3С2, по-видимому, из-за присутствия в продуктах обра ботки металлов, обладающих высокой теплопроводностью. По мнению авто ров, при плазменной обработке карбидов более значительное влияние на выход сферических частиц оказывает не теплопроводность, а степень обезуглерожи вания карбидов, связанная с прочностью их решеток.
Результаты исследований воздействия НТП дуговых и ВЧ разрядов на ок сидные дисперсные материалы представлены в работах [4.8—4.12]. В работе [4.8] проведен теоретический расчет температурных напряжений, возникаю щих в частицах дисперсных материалов при их взаимодействии с плазменной струей. Авторы делают попытку на основе этого расчета обосновать изменение гранулометрического состава порошков, полагая, что оно не может быть след ствием только процессов возгонки и испарения.
Как показали расчеты, значения тангенциальных и радиальных напряжений достигают сотен килограммов на квадратный миллиметр, что существенно пре вышает предел прочности материалов частиц. Эти напряжения должны приво дить к разрушению частиц или объемному их расширению с образованием по лых сфер.
Исследования порошков А120 3 и S i0 2 до и после их взаимодействия с A r-N 2 плазменной струей показали:
1)частицы порошка Si02 после обработки имели форму осколков лишь со слег ка оплавленными краями. Размер частиц уменьшился при этом почти в три раза;
2)у частиц порошка А120 3 в зависимости от мощности плазменной струи происходит изменение гранулометрического состава как в сторону увеличения, так и в сторону уменьшения размера. При уменьшении размера частиц они имеют вид сплошных матовых сфер, а при увеличении размеров частицы стано вятся пустотелыми (полыми) сферами. На взгляд авторов, рассмотренные вы ше превращения обусловлены сочетанием температурных напряжений с про цессами газовыделения при кристаллизации.
Вработе [4.8] рассмотрено изменение химического состава порошков А120 3
вВЧ плазме Аг, Аг—Н2, Аг—СО, Аг—СН4.
В плазме аргона конверсия А120 3 может достигнуть 30 % и обычно возраста ет с уменьшением массового расхода порошка, размеров частиц и с увеличени ем мощности плазмотрона. Авторы полагают, что образование полученного мелкодисперсного высокопирофорного порошка чистого алюминия происхо дит в результате конденсации его из газовой фазы. Это позволяет объяснить указанный характер полученных зависимостей увеличением количества испа ренного оксида.
Использование в качестве плазмообразующего газа смеси Аг—Н2 не привело к существенному увеличению разложения А120 3. В то же время использование добавок СО и СН4, подаваемых в хвостовую часть плазменного факела, т.е. в зо ну протекания реакций образования алюминия, приводило к увеличению кон версии в два и четыре раза соответственно. Это объясняется различной термо динамической прочностью Н20 и СО в температурном интервале возможного окисления алюминия.
По данным рентгеновского анализа в продуктах обработки оксида алюми ния в Аг, Аг—Н2, Аг—СО плазмах были обнаружены А1, а-А120 3 и у-А120 3. При использовании плазмы Аг—СН4 также был обнаружен А14С3.
С приведенными данными хорошо согласуются результаты, полученные в работах [4.10, 4.11] при обработке А120 3 в ВЧ аргоно-азотной плазме.
Продукты обработки собирались на охлаждаемых подложках и представляли собой образования в форме сталагмитов темно-серого цвета. Цвет образцов ме нялся на белый при нагревании в кислороде до 1570 К. Рентгеновский анализ по казал наличие а-А120 3 и небольших количеств у- и 5-А120 3.Линий рентгеновской дифракции, соответствующих металлическому А1, даже в образцах с недостатком кислорода до 8 % масс, обнаружено не было. Авторы объясняют данный факт присутствием алюминия в виде мельчайших агрегатов, не обнаруживаемых рент геновскими методами и сформированных конденсацией из паров в жидких ка пельках оксида алюминия, быстро затвердевших в процессе резкого охлаждения.
Максимальная степень восстановления А120 3, полученная в экспериментах, составляла 17 %. Зависимости степени восстановления от массового расхода порошка, мощности плазмотрона и исходного размера частиц качественно полностью совпадают с данными, приведенными в [4.7].
Авторы работы [4.12], изучив взаимодействие плазм состава Аг—Н2 и Аг—СН4 с порошком А120 3 и проведя термодинамический анализ данных систем, приш ли к выводам, аналогичным приведенным в [4.8]: в плазме состава Аг-СН4 вос становление А120 3 может идти достаточно успешно благодаря стабильности СО при высоких температурах. Водород же не обладает высокой способностью к восстановлению из-за нестабильности Н20 при высоких температурах.
Механизм процесса авторы представляют следующим образом. Частицы А120 3 нагреваются и плавятся. При этом оксид алюминия испаряется в виде как
алюминия, так и субоксидов А10, А120 , А102. Пары алюминия и субкосиды рез ко охлаждаются и во время охлаждения окисляются в А120 3. Частицы, которые не испаряются полностью, охлаждаются из жидкой фазы и затвердевают как сферические. В обработанном продукте большая часть частиц являлась сфери ческой. Средние размеры частиц продуктов были меньше средних размеров частиц исходного А120 3. Кроме того, в распределении по размерам продукта об работки А120 3 имелось два пика: один соответствует размеру частиц примерно 7 мкм, другой, как и у исходного порошка, 40 мкм.
Рентгеновским методом в продуктах обработки исходного а-А120 3 в плазмах состава Аг—Н2 и Аг—СН4 были идентифицированы а - и у-А120 3, металла обна ружено не было. В продуктах обработки в Аг—СН4 плазме присутствует много черных частиц, являющихся углеродом —продуктом разложения СН4. При об щем согласии между собой результатов работ [4.8—4.12] небольшие расхожде ния в них вызваны, по-видимому, некоторыми различиями в условиях экспери ментов.
Приведенные данные, как и при обработке компактных материалов высоко концентрированными потоками энергии (ВПЭ), указывают, что причиной из менений в дисперсных материалах, обработанных в плазме, является не только термическое воздействие, но и взаимодействие материала частиц с газовой фа зой. Такое взаимодействие может проходить как без изменения химического состава материала частиц, например в процессах поглощения-выделения газа, так и сопровождаться химическими реакциями с компонентами газовой фазы.
Как отмечалось в гл. 1 и 2, высокая интенсивность энергетического воздей ствия и его малая длительность, характерные для плазмы конденсаторного раз ряда, позволяющие локализовать структурные и фазовые превращения в тон ких поверхностных слоях веществ; высокая технологичность импульсной плаз мы, делающая возможным использование ее для обработки псевдоожиженных слоев порошков и газодисперсных потоков, дают основания считать импульс ную плазму конденсаторного разряда высокоэффективным способом поверх ностного модифицирования дисперсных материалов.
Модифицирующее воздействие импульсной плазмы изучено на оксидах (А120 3, Z r02), карбидах (TiC, WC, Сг3С2), графите, углеродном волокне (УВ), а также при металлизации порошков.
4 .2 . М одиф ицирую щ ее воздейст вие им пульсной ппезм ы е е морф ологию , структуру и сост ав дисперсны х оксидов и карбидов.
Сф ероидизация карбидов и оксидов в им пудьсной п л азм е
Схема установки для модифицирующей обработки порошков в состоянии газодисперсного потока показана на рис. 1.10. В этом случае вещество подвер
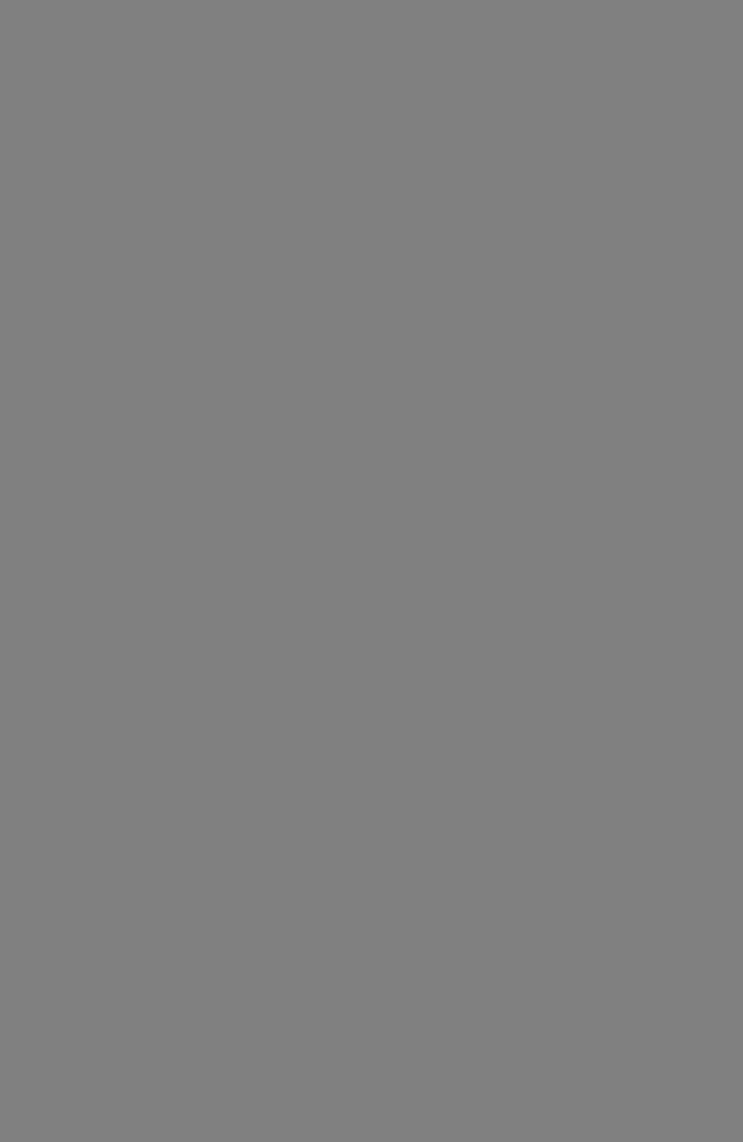
никающих в цикле нагрев—охлаждение частиц порошка импульсом плазмы. Причем характер функции распределения частиц после импульсной плазмен ной обработки зависит от состава плазмообразующего газа. Гранулометричес кий состав порошка после обработки в плазме водорода характеризуется боль шим содержанием мелких фракций, что свидетельствует о более интенсивном воздействии импульсной водородной плазмы на обрабатываемый порошок по сравнению с плазмой аргона.
Таблица 4.1. Технологические свойства порошков до и после обработки в импульсной плазме
Исходный |
Размер |
Условия |
Площадь |
Насыпная |
|
|
модифицирующей |
удельной |
плотность, |
Текучесть, с |
|||
порошок |
частиц, мкм |
|||||
|
|
обработки |
поверхности, м /г |
г/см3 |
|
|
а-А120 3 |
63...100 |
До обработки |
7,5 |
1,28 |
60,2 |
|
|
|
Импульсная |
3,7 |
1,48 |
51,7 |
|
|
|
плазма аргона |
|
|
|
|
|
|
Импульсная |
4,0 |
1,56 |
48,1 |
|
|
100 |
плазма водорода |
|
|
|
|
Z r02-Y20 3 |
До обработки |
8,3 |
2,95 |
57 |
||
(11,5 % масс. |
|
Импульсная |
6,1 |
3,61 |
44 |
|
У20 3) |
|
плазма аргона |
1,2 |
|
|
|
TiC |
40..Л00 |
До обработки |
1,85 |
48,3 |
||
|
|
Импульсная |
8,8 |
2,21 |
40,2 |
|
|
|
плазма аргона |
|
|
|
|
Сг3С2 |
30...63 |
До обработки |
15,3 |
2,81 |
6,3 |
|
|
|
Импульсная |
5,6 |
3,16 |
5,1 |
|
|
|
плазма аргона |
|
|
|
Некоторое расширение гранулометрического состава в сторону больших размеров связано с процессом агломерации и образованием частиц конгломе ратного строения. Это возможно из-за столкновения оплавленных с поверхнос ти частиц, по-разному ускоренных фронтом ударной волны из-за различия в их размерах. Об этих превращениях можно судить по характерным типам структур частиц после импульсного плазменного модифицирования (рис. 4.4).
Здесь представлены фрагменты структур частиц разного размера, свидетель ствующие об образовании проплавленного поверхностного поликристаллического слоя у частиц размером >100 мкм. Исследование сколов частиц размером < 50 мкм для А120 3, 40 мкм для Z r02 и 60...70 мкм для TiC и Сг3С2 показывает, что они проплавляются на всю глубину (рис. 4.4, е, и, л). Это согласуется с ре зультатами расчета (см. гл. 2). У ряда частиц (рис. 4.4, м) на гладкой поверхнос ти присутствуют каплевидные образования, появление которых связано с переконденсацией на них испарившегося под воздействием импульса плазмы мате-
Рис. 4.2. Гранулометрический состав порошка оксида алюминия (т— массовая доля частиц): 1 —исходный; 2 —обработанный в плазме аргона; 3 —в плазме водорода
т, %
Рис. 4.3. Гранулометрический состав порошка карбида титана: 1 —исходный; 2 —обработанный в плазме аргона
риала частиц. На пове рхности отдельных микросфер (рис. 4.4, в) наблюдаются фасетки в виде каскадов кубичес ких кристаллов, появ ление которых свиде тельствует о возможном их росте из расплава в условиях резкого пере охлаждения.
Степень сфероццизации р обработанного в плазме исходного по рошка является косвен ной характеристикой эффективности нагрева его импульсами плазмы. Степень сфероидизации может быть определена оптическим методом как отношение числа сферических частиц к общему их количеству в нескольких полях зре ния микроскопа. Общее число просчитанных частиц при этом состав ляло не менее 650 шт. На рис. 4.5 представлена за висимость степени сфе роидизации от числа циклов обработки по рошков А120 3 и TiC дис персностью 63... 100 мкм. С учетом более высоких теплофизических ха рактеристик плазмы водорода эффектив ность сфероидизации в
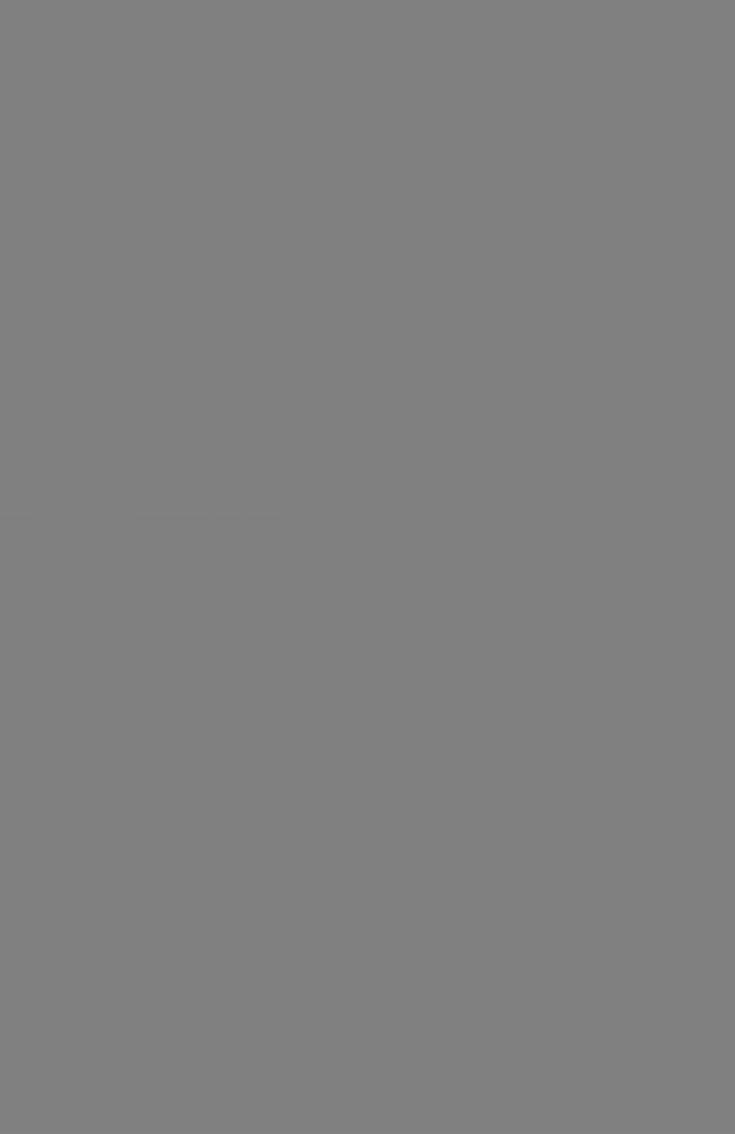