
книги / Нанодисперсные и гранулированные материалы, полученные в импульсной плазме
..pdf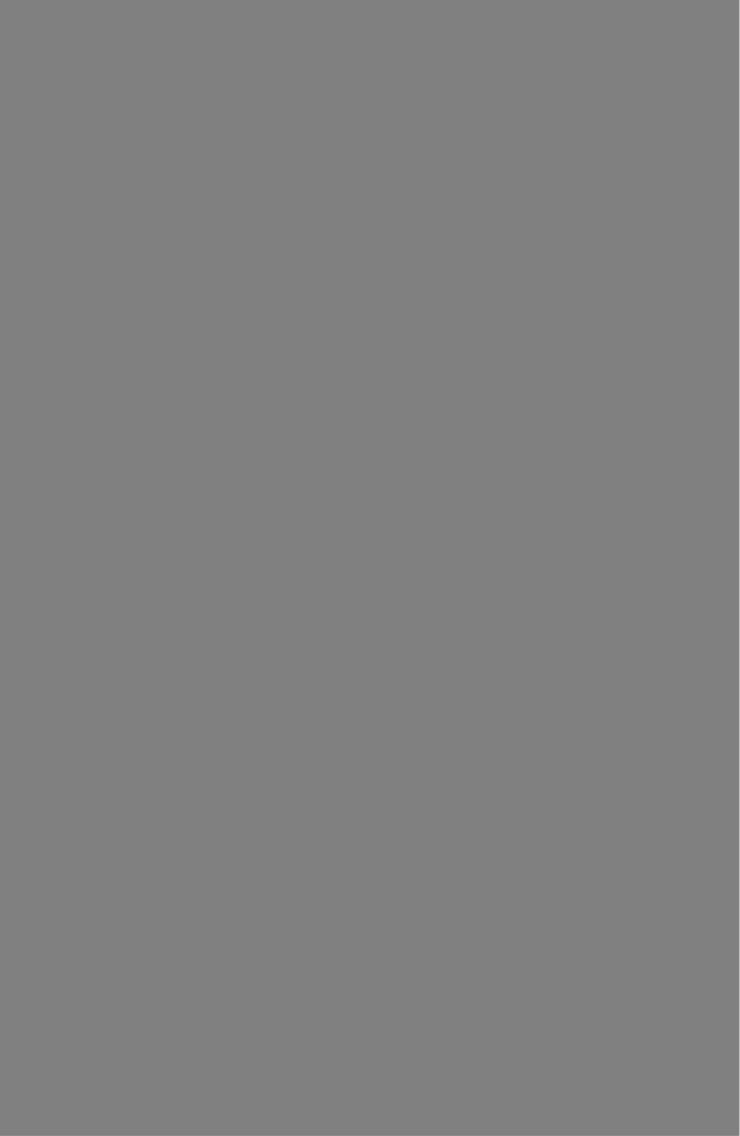
дов свидетельствуют о более значительном их обезуглероживании при металли зации, чем при плазменной обработке с целью сфероидизации.
Например, степень обезуглероживания для порошка карбида титана может достигать 20 % масс. Снизить ее при металлизации можно исключением опера ции предварительной сфероидизации и увеличением концентрации никеля в обрабатываемой шихте. В случае обработки карбида вольфрама, содержащего в исходном состоянии фазу монокарбида и следы полукарбида W2C, в металлизи рованном порошке содержание последнего увеличивается, т.е. происходит обеднение порошка углеродом. Для карбида хрома, содержащего в исходном состоянии преимущественно фазу Сг3С2 с примесью Сг7С3, в металлизирован ном порошке количество фазы Сг7С3 становится сравнимым с Сг3С2; кроме то го, здесь появляется Сг20 3. Это обусловлено увеличением содержания в порош ке после металлизации легкоокисляющейся фазы Сг7С3.
С этой же проблемой столкнулись и авторы работ по металлизации дисперс ных карбидов с использованием импульсной плазмы высоковольтного конден саторного разряда, воздействующей на фонтанирующий слой из частиц карби да (WC, TÎC) и металла (Ni, Со) [1.65].
Кратковременность импульса разрядного тока, генерируемого разрядным контуром установки, обеспечивает высокое значение импульсной мощности, достаточной для поверхностного расплавления керамических частиц (TiC, WC) дисперсностью 30...60 мкм и частичной сублимации, либо полного расплавле ния металлических частиц дисперсностью <10 мкм. В промежутках между им пульсами за счет межфазного взаимодействия расплавленного металла с кера микой осуществляется плакирование керамической фазы. Формирование пла кирующего металлического слоя происходит и за счет конденсации на керами ческих частицах испарившегося в импульсной плазме металла. Степень метал лизации керамики в этом способе составляет 80 % и зависит от продолжитель ности процесса и мощности импульсной дуги.
При металлизации карбида вольфрама в продукте плазменной обработки появляется полукарбид W2C, содержание которого увеличивается с увеличени ем энергии импульсного разряда и продолжительности металлизации карбида. Обезуглероживание карбидной керамики в этом способе связано с возможным многократным воздействием импульса плазмы на обрабатываемый порошок, находящийся в состоянии псевдоожижения. Содержание полукарбида вольф рама здесь может достигать ~ 30 % масс, (длительность плазменной обработки 30 мин; плазмообразующий газ —аргон; энергия разряда ~ 100 Дж). Введение в состав плазмообразующих газов метана снижает содержание W2C до ~ 20 % масс.
Кроме того, при таком способе металлизации существуют ограничения раз меров частиц исходной шихты условиями существования устойчивого фонта нирующего слоя. Для большинства керамических порошков (WC, TiC, А120 3,
Zr02) этот размер составляет около 25...30 мкм и более. Оптимальный же раз мер частиц напыляемого газотермическими методами порошка должен состав лять, мкм: А120 3 20...30; Zr02 10...15; WC 10...20; TiC 10...15 [4.33].
Таким образом, приведенные выше результаты исследований металлизации дисперсных материалов с использованием ВПЭ показали, что с учетом необхо димости равномерного воздействия на поверхность каждой из всей совокуп ности обрабатываемых частиц наиболее технологичной и эффективной являет ся поверхностная обработка порошков в низкотемпературной плазме. Измене ния, происходящие в порошке в результате такой обработки, в первую очередь обусловлены термическим воздействием плазмы. При обработке порошков в плазме дугового и ВЧ-разрядов такое воздействие может распространиться на значительные объемы материала ввиду относительно длительного пребывания частиц в высокотемпературной зоне плазменного реактора. Это приводит в ря де случаев к нежелательным изменениям химического состава металлизируе мых керамических частиц.
В связи с этим интересные результаты можно ожидать в случае применения для модифицирующей обработки импульсной плазмы конденсаторного разря да, сочетающей высокую интенсивность теплового воздействия с его малой длительностью. Это позволит локализовать взаимодействие с плазмой в тонких поверхностных слоях частиц наряду с возможностью регулирования его (взаи модействия) масштабов.
Однако применение способа обработки кипящих слоев керамических час тиц для металлизации в импульсной плазме не всегда эффективно. Более пер спективным, по-видимому, следует считать способ, основанный на обработке газодисперсных потоков. В работах [1.65,1.82] описаны результаты исследова ний по модифицированию частиц керамики (TiC, WC, А120 3) и алмаза при об работке газодисперсных потоков, содержащих частицы этих веществ, подавае мые в разрядный промежуток импульсного плазменного генератора по схеме, описанной выше (гл. 1). Дополнительным компонентом, вводимым в поток, были пары соответствующих элементосодержащих веществ. Их разложение под воздействием импульса плазмы и последующая конденсация элементов на по верхности частиц обеспечивали поверхностное легирование порошков. В каче стве элементосодержащих веществ, которые вводились в газодисперсный по ток на входе его в плазменный импульсный реактор, использовались СоС12, ацетилацетонат никеля и ВВг3. Содержание Со, Ni и В на поверхности обрабо танных частиц при такой схеме процесса не превышало нескольких процентов. Для достижения этого результата требовалось неоднократное пропускание ис ходной шихты через импульсный разряд.
Поэтому более эффективным является разработанный с участием авторов способ металлизации дисперсных части, расширяющий гранулометрический
состав металлизируемых порошков в область размеров < 30 мкм и дающий воз можность предотвратить заметное изменение фазового состава обрабатывае мых в плазме порошков. Сущность способа состоит в следующем.
Газодисперсный поток, представляющий собой струю плазмообразующего га за —аргона с распределенными в ней частицами керамики и металлизирующим компонентом, подается в импульсный плазмохимический реактор (см. рис. 1.10) через полый электрод непосредственно в зону формирования разряда.
При выделении в канале импульсного разряда энергии образуется импульс ная плазма, воздействующая на компоненты газодисперсного потока. Под тер мическим воздействием ее происходят нагрев, расплавление и испарение дис персной фазы [4.17, 4.34, 4.35].
Режимы обработки исходных смесей порошков: (А120 3, Z r02) — Ni; (НС, Сг3С2, В4С) —Ni; WC—Со могут быть определены с помощью математического моделирования термического воздействия импульсной плазмы на дисперсные материалы (гл. 2). Так, при энергии единичного импульса ~ 400 Дж во время разряда происходит полное расплавление и испарение частиц металла размером 10... 15 мкм и оплавление поверхности частиц керамики размером 30...60 мкм.
В указанных работах использовался карбонильный никель, гранулометри ческий состав которого соответствовал нормам ГОСТ 9722—79 (размер частиц < КГ5 м) и порошок металлического кобальта марки ПК-1, соответствующий ГОСТ 9797—79. Классификация металлических порошков для выделения фрак ции < ДО-5 м проводилась на зигзагообразном воздушном классификаторе мар ки MZR 100 (Германия) с пределом разделения порошков от 10-6 до 10~4 м. Классификация керамических порошков производилась на виброгрохоте фир мы Frich (Германия), дающем возможность разделить порошки размером от 2-10“5 м с шагом 5Ю _6 м.
Металлизация дисперсной керамики с использованием импульсной плазмы связана с межфазным взаимодействием в многофазной системе, которая фор мируется за время воздействия импульса плазмы (~ 10-4 с) на газодисперсный поток. Она состоит из нагретых и имеющих жидкий поверхностный слой частиц керамики, полностью расплавленных частиц металла и металлического пара.
Металлизация керамических частиц происходит в промежутке между им пульсами по двум каналам: 1) за счет межфазного взаимодействия расплавлен ных частиц металла с керамикой при их столкновении; 2) за счет конденсации на поверхности керамических частиц той части металлической составляющей шихты, которая перешла в паровую фазу под воздействием импульса плазмы. При этом керамические частицы, находящиеся в газодисперсном потоке, под вергаемом плазменному воздействию, являются готовыми центрами гетероген ной конденсации, что делает менее вероятным гомогенную конденсацию с вы делением металла в объеме.
т
Оценку эффективности металлизации частиц можно провести с использова нием метода магнитной сепарации на сепараторе УСМ-1Т по количеству при тягиваемых к магниту частиц из общей массы порошка. Изменение величины поверхностного магнитного поля в сепараторе обеспечивает притяжение час тиц, имеющих в своем составе разное количество металлической компоненты. Это дает возможность с использованием гистограмм выхода магнитных частиц судить о равномерности распределения металлической компоненты в обрабо танных частицах.
Проведенные для оценки правильности представленного механизма процес са исследования по металлизации узких фракций порошков при разных конце нтрациях никеля в исходной шихте подтвердили предположения о влиянии числа центров конденсации и концентрации никеля в паровой фазе на эффек тивность металлизации. Выход магнитных частиц с увеличением дисперсности обрабатываемого порошка возрастает. Аналогичное влияние оказывает повы шение концентрации металла в исходной шихте (рис. 4.13).
Рис. 4.13. Зависимость выхода магнитных частиц от содержания никеля в исходной шихте при разной дисперсности оксида алюминия; диаметр частиц АДОз, мкм: 1—100; 2 - 70; 3 —40
Металлографическое исследование порошка показало, что основная масса мелких фракций А120 3 приобрела сферическую форму, в то время как значитель ное количество частиц крупных фракций сохранили первоначальную форму. Исследование гранулометрического состава порошков до и после металлизации в импульсной плазме показывает существенное отличие его от гранулометри ческого состава порошков, подвергнутых модифицирующей обработке без ме таллизации (рис. 4.14). Видно, что плазменная обработка А120 3 при отсутствии никеля в составе исходной шихты вызывает большее измельчение материала. Измельчение может быть вызвано как разрушением частиц А120 3 из-за возник ших при нагреве высоких термических напряжений, так и переходом частиц ма териала в паровую фазу с последующей конденсацией в виде ультрадисперсного порошка. Присутствие никеля в плазменной струе, по-видимому, может привес ти: 1) к изменению условий формирования импульсной дуги по сравнению с га зодисперсным потоком, состоящим только из непроводящих частиц; 2) к сни жению температуры струи за счет значительного расхода ее тепловой энергии на нагрев и испарение металла. Все это наряду с присутствием никеля на частицах оксида алюминия, по-видимому, влияет на оба возможных механизма процесса
т , %
Рис. 4.14. Гранулометрический состав порошка оксида алюминия: 1 —исходный оксид; 2 —сферо- идизированный в плазме аргона; 3 —металлизированный в плазме аргона (т —массовая доля частиц)
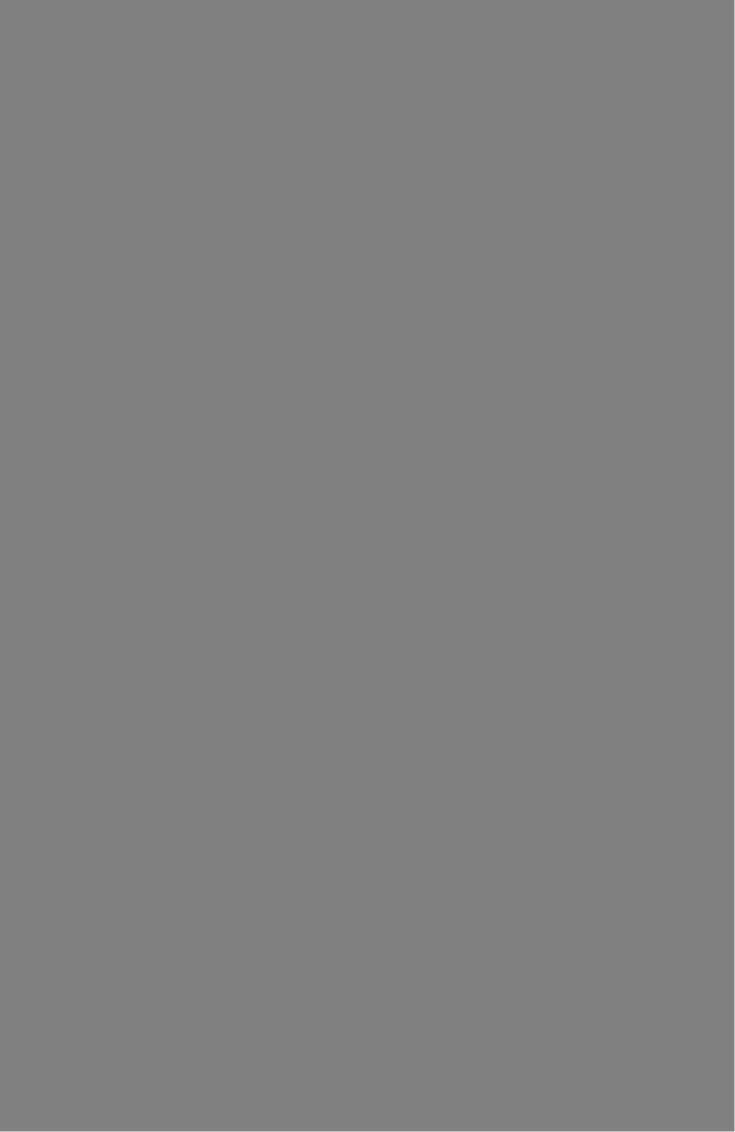
Рис. 4.16. Зависимость выхода магнитных частиц в продукте плазменной металлизации от числа цик лов импульсной плазменной обработки: 1 —В4 С + Ni; 2 —СГ3С2 + Ni; 3 ,4 —TiC + Ni; 5 —A12 0 3 + Ni; 6—Z r0 2 + Ni; 1—3 ,5 ,6 —размер частиц никеля < 10 мкм; 4 —10...20 мкм
Оценка толщины этого слоя, проведенная методом Оже-спектроскопии, с послойным стравливанием материала показала, что на поверхности металлизи рованных частиц в спектрах Оже-элекгронов (рис. 4.18) интенсивность линий, относящихся к алюминию оксида, чрезвычайно мала или они отсутствуют.
По мере травления поверхности частицы интенсивность линий Оже-элект- ронов алюминия возрастает и уменьшается интенсивность линий Оже-элект- ронов никеля. При стравливании слоя толщиной 4...6 нм линии никеля в спект рах Оже-электронов отсутствуют полностью. Формирование этого слоя метал ла на частицах происходит, по-видимому, за счет конденсации металлической составляющей исходной шихты, перешедшей в пар. Степень металлизации в этих системах за один цикл плазменной обработки снижается примерно до 70 % (см. рис. 4.16).
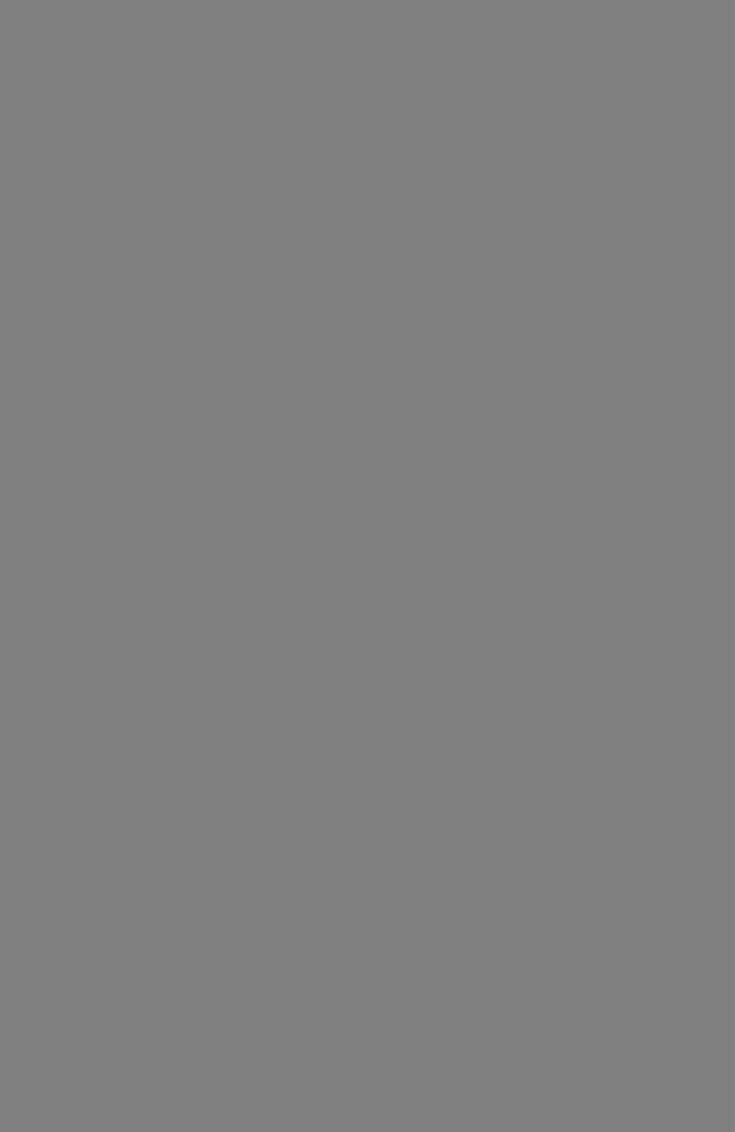
Рис. 4.18. Оже-спектры участка поверхности металлизированной частицы оксида алюминия: а — до ионного травления; б —после ионного травления
Рентгеновский и химический анализ не показал существенных изменений фазового и химического состава керамической компоненты получаемых ком позиций керамика—металл в ходе импульсной плазменной обработки. Так, со держание связанного углерода в карбиде титана изменялось мало (с 19,03 до 18,99 % масс.). В металлизированном карбиде вольфрама содержание W2C не превышало 1...2 % масс. У карбида хрома содержание связанного углерода из менялось с 12,49 до 12,4 % масс. Эти изменения существенно ниже, чем при об работке карбидов с целью металлизации в дуговых плазмотронах [4.30]. Карбид никеля и интерметаллиды в металлизированном продукте не обнаружены.
Химический анализ металлизированных порошков свидетельствует о некото ром обеднении при металлизации получаемого дисперсного кермета по металли ческой компоненте по сравнению с ее содержанием в исходной шихте. Например,
т