
книги / Основы технологии машиностроения
..pdfХарактеристика технологических методов сборки |
241 |
На фиг. 139 показана схема ручной электрической машины для болтовых и винтовых соединений. На шпиндель машины могут быть установлены различные инструменты, меняющие ее назначение. Установкой торцового ключа получаем гайковерт, захвата для шпи лек — шпильковерт, отвертки — винтоверт.
При достижении момента затяжки винтового соединения торцо вые зубья муфты, снабженные скошенными гранями, раздвигают диски, преодолевая сопротивление пружины, сжатие которой регу лируется в соответствии с заданным моментом затяжки.
Применение быстроходных электродвигателей для этих машин (10 0 0 0 — 12 000 об/мин) снижает их вес на единицу мощности.
Фиг. 140. Вставка к ручной |
электриче |
Фиг. 141. Вставка |
к ручной электри |
ской машине с торцовым |
ключом. |
ческой машине |
для отвертки |
Питание электродвигателей переменным током повышенной частоты (180—200 пер/сек) требует применения специального умформера.
В целях безопасности корпуса электрических машин заземляются, для чего в подводке предусматривается дополнительный провод.
Шпиндели электрических машин снабжаются устройствами для смены вставок. Вставка для торцового ключа (с закрепленной сменной торцовой головкой) показана на фиг. 140, а вставка для отвертки — на фиг. 141. На фиг. 142 показана самораскрывающаяся головка для механизированного завинчивания шпилек. Шпилька захваты вается внутренней резьбой губок 1, которые удерживаются пальцем 2. Сначала губки свободно охватывают шпильку, но когда последняя упрется своим торцом в кнопку 3, губки войдут внутрь втулки 4, сцепятся с ней посредством шариков 5 и сожмутся конической частью втулки 4, закрепив при этом шпильку в патроне. Косые зубья муфты 6 войдут в зацепление с зубьями втулки 4, шпилька начнет вращаться и завинчиваться в резьбу базовой детали.
Высота выступающей части шпильки регулируется соответствую щей установкой чашки, при упоре которой в плоскость базовой детали втулка 4 продолжает вращаться и опускаться, пока зубья на ее торце не выйдут из зацепления с зубьями муфты 6. В этот момент губки 1 раскрываются и освобождают шпильку. В хвостовике 7 головка пружины 8 упирается в винт 9. На хвостовике 7 закреплена зубчатая полумуфта 11, сцепляющаяся с полумуфтой 12. Когда шпилька будет полностью завинчена, стакан 13 остановится, но хвостовик 7 будет продолжать вращаться со шпинделем. При этом зубья полумуфты 12 будут подниматься по скосам зубьев полумуфты 11 к поднимать ста-
16 Кован
242 Характеристика технологических методов производства
кан 13, что посредством плунжера 10 вызывает сжатие пружины 8 и затяжку ввинчиваемой шпильки. При дальнейшем смещении ста кана 13 вверх произойдет размыкание зубьев муфты 6 и прекращение передачи крутящего момента на шпильку [71] Не достатком головок с захватом шпилек за резьбу является вытягивание ниток резьбы под гайку. Поэтому при увеличенном на тяге посадочной части шпильки целесооб разно удерживать шпильку не .за резьбу,
аза поясок.
Впоследнее время получили широкое распространение гайковерты ударного дей ствия. Одна из конструкций подобного гайковерта приведена на фиг. 143.
Он состоит из сборного корпуса 1, в ко тором смонтирован пятилопастный пнев матический роторный двигатель 2, удар
|
|
|
ный роликовый механизм и шпиндель 3 |
|||||||||||
|
|
|
с фиксатором для сменных торцовых |
клю |
||||||||||
|
|
|
чей. Вращение от |
вала |
ппевмодвигателя |
|||||||||
|
|
|
передается на |
обойму |
4 роликов |
5. |
По |
|||||||
|
|
|
следние при вращении |
|
обоймы |
ударяют |
||||||||
|
|
|
о выступы а шпинделя и сообщают ему |
|||||||||||
|
|
|
ударные импульсы, обеспечивая необходи |
|||||||||||
|
|
|
мый момент затяжки |
винтового |
соедине |
|||||||||
|
|
|
ния. Реверсирование вращения |
осуществ |
||||||||||
|
|
|
ляется |
изменением |
направления |
|
подачи |
|||||||
|
|
|
сжатого воздуха при помощи золотника 6. |
|||||||||||
|
|
|
Пусковое |
устройство, |
приводимое |
в |
дей |
|||||||
|
|
|
ствие от курка 7, вмонтировано в рукоятку |
|||||||||||
|
|
|
гайковерта. |
|
указанного |
гайковерта |
||||||||
|
|
|
Достоинствами |
|||||||||||
|
|
|
являются |
малый |
вес, обусловленный от |
|||||||||
|
|
|
сутствием редуктора, |
и |
ликвидация реак |
|||||||||
|
|
|
тивного момента, |
воспринимаемого в дру |
||||||||||
|
|
|
гих конструкциях руками рабочего. |
|
||||||||||
|
|
|
Гайковерт |
предназначен для |
завинчи |
|||||||||
Фиг. |
142. Самораскрываю- |
вания |
резьбы |
до 6 |
мм; он работает при |
|||||||||
щаяся |
головка |
для механи |
давлении |
сжатого |
воздуха 5— 6 а/п; число |
|||||||||
зированного |
завинчивания |
ударов |
2500—3000 |
в минуту. |
Вес |
гайко |
||||||||
|
шпилек. |
верта |
около |
2 кг |
при |
габарите |
180 х |
|||||||
На фиг. |
|
X 219 х 65 мм. |
гайковерт, |
предназна |
||||||||||
144 представлен гидровинтовой |
||||||||||||||
ченный для завертывания |
гаек, |
винтов, болтов |
и шпилек размером |
М10—М12, а также для обработки отверстий (сверление, разверты вание).
Характеристика технологических методов сборки |
243 |
Фиг. 143. Пневматический реверсивный гайковерт ударного действия.
Фиг. 144. Гидровинтовой гайковерт для резьб М10—М12 (конструкция НИИТракторосельхозмаша, тип УГР-10:
1 — рукоятка, 2 — золотник, 8 — пусковая скоба: 4 и б—винты гидродвнгателя; 6 — ведомое зубчатое колесо Редуктора, 7—шпиндель; б—пружина золотника; 9 — сменная торцовая головка.
16*
244 Характеристика технологических методов производства
Масло под давлением подается от насоса по гибкому металличе скому рукаву через рукоятку 1 к золотнику 2 и при нажатии пуско вой скобы 3 поступает по каналам в корпусе к винтам 4 и 5 (всего винтов три). От вращающегося под давлением масла ведущего винта 5 через редуктор момент передается на шпиндель со сменной торцовой головкой 9. Масло, пройдя через винты гидродвигателя, теряет давле ние и идет на слив через редуктор, пустотелую рукоятку и дюритовый наружный шланг.
Величина крутящего момента регулируется изменением давления масла, подаваемого к гайковерту.
К преимуществам гидравлического гайковерта относится бесшум ность работы, высокий к. п. д., доходящий до 0,55—0,65 (вместо 0,07—0,11 и 0,4—0,5 соответственно у пневматических и электриче ских гайковертов), и малый их вес.
Гайковерт развивает на ключе крутящий момент до 5 кгм\ число оборотов — до 350 об/мин. Он работает при давлении масла в напор ном рукаве до 60 кг/см2, в сливном — до 6 кг!см2\ расход масла до 20 л/мин. Вес гайковерта — 2,4 кг.
На фиг. 145 изображен пневматический двухскоростной нормали зованный узел гайковерта, предназначенный для компоновки различ ного типа многошпиндельных устройств с минимальным расстоянием между осями завертываемого крепежа 60 мм. В зависимости от типа гайковерт позволяет завертывать гайки с диаметром резьбы до МЗО; при этом он конструктивно выполнен таким образом, что навертыва ние гаек осуществляется при малом крутящем моменте и высокой скорости и окончательная затяжка при меньшей скорости, но боль шем моменте. Величина момента регулируется давлением подаваемого к гайковерту сжатого воздуха.
Гайковерт состоит из сборного цилиндрического корпуса 1, в средней части которого имеется фланец 2 с отверстиями для крепеж ных болтов. В верхней части корпуса расположен пневматический лопастной двигатель, вращение от которого через редукторы первой ступени 3 и второй ступени 4 и муфту быстрого вращения 5 (при навер тывании крепежа) или редуктор 6 и муфту замедленного вращения 7 (при довертывании крепежа) передается на шпиндель 8 и через квад рат 9 для сменного инструмента на торцовый ключ. Свободное навер тывание гайки производится через муфту 5. К концу навертывания гайки, когда сопротивление возрастает, происходит автоматическое переключение на малую скорость, и винтовое соединение дотягивается с заданным моментом через редуктор 6 и муфту 7. Этот принцип работы обеспечивает повышение производительности и уменьшение расхода сжатого воздуха.
Двухскоростные пневматические гайковерты работают при давле
нии сжатого |
воздуха |
5— 6 am при |
расходе |
свободного |
воздуха |
0,736 м3/мин. |
Число |
оборотов при |
холостом |
ходе 356, |
530 или |
840 об/мин; крутящий момент на ключе 19,9; 13,3 и 8,3 кгм (в зависи мости от типа). Вес гайковерта 4,3 кг.
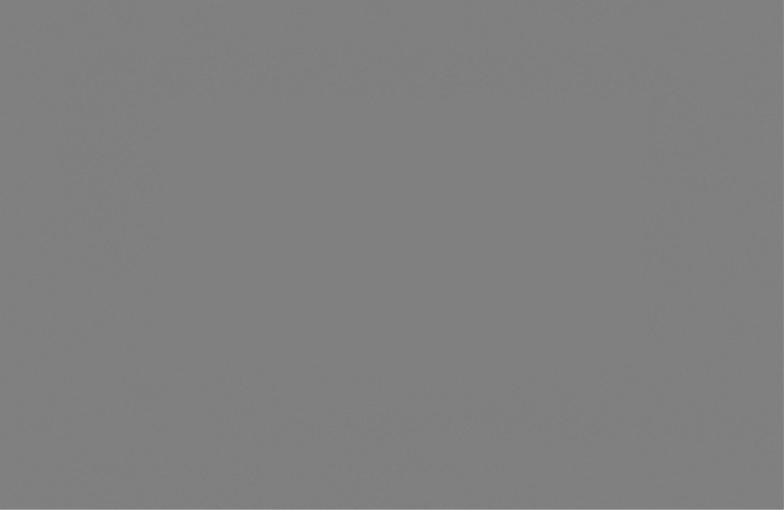
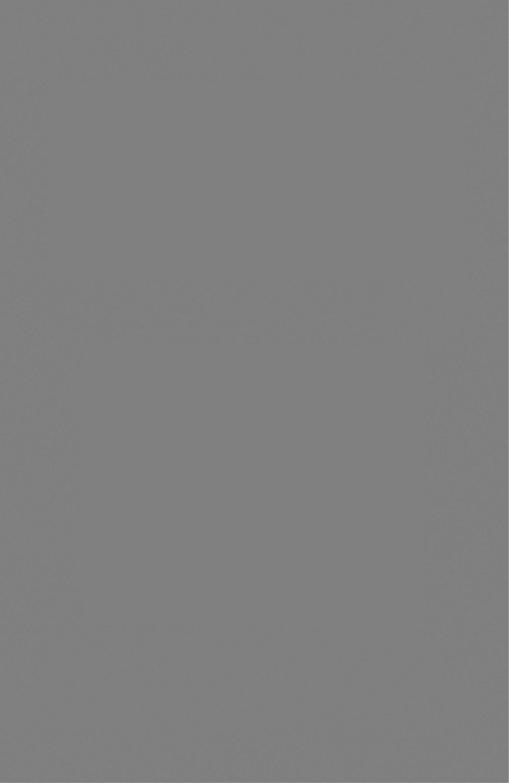
Характеристика |
технологических методов |
сборки |
247 |
(конструкция подобного |
нормализованного |
узла |
показана |
на фиг. 145).
Нормализованные узлы 1 в соответствии с расположением гаек на собираемом изделии размещаются и крепятся на основной плите 2
ипромежуточной плите 3. Через фланец 4 сжатый воздух подводится
кузлам по каналам в воздухораспределительной плите 5. Включение гайковерта производится нажатием рукоятки 6\ при этом поршень 7 пускового цилиндра открывает впускной клапан. Рукоятка 8 служит для включения цилиндра 9 съемника 10, обеспечивающего легкое снятие инструмента с гаек или головок завернутых винтов. Враще
ние торцовых ключей 11 передается шпинделями 12. Для удобства выполнения работы и уменьшения влияния веса механизированного инструмента на утомляемость рабочего, инструмент подвешивают на пружинных блоках. При поточной сборке на непрерывно дви жущемся конвейере пружинные блоки устанавливаются на тележках, перемещающихся по монорельсам. Для тяжелого инструмента поль зуются двумя спаренными блоками.
В тяжелом машиностроении применяются электрические машины тяжелого типа или радиально-сверлильные станки со специальными патронами — торцовыми гаечными ключами.
Применение механизированного инструмента сокращает время, затрачиваемое на выполнение болтовых и винтовых соединений, до 10 раз по сравнению с временем выполнения этих работ вручную.
Проверка затяжки болтов, шпилек и винтов, производимая обыч ным ручным инструментом, дает субъективную оценку, поэтому целе сообразно производить проверку затяжки тарированным инструмен
том или ключами с динамометром (фиг. 148). |
должно производиться |
Крепление гаек и винтов при сборке |
|
в определенном порядке, показанном на фиг. |
149 и 150. При прямо |
угольной форме соединяемых поверхностей затягивание винтов и гаек
248 |
Характеристика технологических |
методов |
производства |
следует |
начинать от середины, а не с |
краев, |
так как отклонение |
от плоскостности при значительной длине устанавливаемой крышки может вызвать ее искривление. Затяжка гаек и винтов в произволь ном порядке также может вызвать коробление или по меньшей мере перекос закрепляемой детали. При этом затяжка гаек должна произ водиться не только последовательно, но и постепенно, в два-три приема, до полной затяжки.
Применение многошпиндельных гайковертов не только повышает производительность труда, но и обеспечивает равномерность затяжки всех гаек.
Шпоночные соединения осуществляются клиновыми, призматиче скими и сегментными шпонками. При сборке соединения с клиновой
Фиг. 149. Схема затяжки гаек на прямо |
Фиг. 150. Последо |
||
угольной головке или крышке; цифры |
вательность |
за |
|
указывают последовательность затяжки. |
тяжки |
гаек |
на |
|
фланце |
или |
круг |
|
лой |
крышке. |
шпонкой ось охватывающей детали смещается относительно оси вала на величину посадочного зазора, что вызывает радиальное биение тем большее, чем больше посадочный зазор. Кроме того, несоот ветствие уклона дна паза охватывающей детали уклону шпонки ведет к перекосу сажаемой на вал детали.
При соединениях с призматическими или сегментными шпонками сборка шпонки с валом осуществляется с натягом, соответствующим по меньшей мере плотной посадке. Во избежание перекосов шпонки
врезультате врезания ее кромки в тело вала или кромки шпоночного паза вала в тело шпонки, необходимо особенно тщательно выполнять посадку шпонки в паз вала; целесообразнее всего вводить шпонку
впаз под прессом или при помощи струбцины и специальной пластины с мелким пазом, которым она накладывается на шпонку; в этом слу
чае давление передается по оси симметрии шпонки, равномерно распределяясь по всей ее длине. Практикуемая посадка шпонок молотком требует больших производственных навыков, так как нерав номерные по силе и внецентренные удары молотка ведут к перекосу шпонки в поперечном и в осевом направлениях.
При посадке на призматическую или сегментную шпонку между верхней плоскостью шпонки и дном паза охватывающей детали дол жен быть зазор; в этом случае будет обеспечено центрирование охва тывающей детали.
Характеристика технологических методов сборки |
249 |
Контроль посадки шпонки на перекос и высоту выступающей части, можно производить призмой, центрируемой боковыми гранями выступающей части шпонки, и набором предельных щупов.
Шлицевые соединения (неподвижные), в зависимости от применяв; мой посадки центрирующих элементов, разделяются на тугоразъем ные и легкоразъемные. При тугоразъемных соединениях рекомен дуется предварительный подогрев охватывающей детали до темпе ратуры 100—120°; в этом случае значительно уменьшается усилие, необходимое для осуществления соединения, что обеспечивает более правильную посадку. При легкоразъемных соединениях посадка охватывающей детали не требует больших усилий. Перед соедине-
Фиг. 151. Посадка на коническую шейку с креплением штифтом.
нием необходимо устранить случайно оставшиеся в соединяемой паре ваусенцы и забоины. Шлицевые соединения проверяются на радиаль ное и осевое биение с установкой вала в центры бабок контрольного приспособления и на качку, т. е. относительное угловое смещение, проверяемое обычно вручную.
Штифтовые соединения осуществляются посредством конических и цилиндрических штифтов.
Штифты применяют не только в качестве соединительного, но также и в виде установочного элемента, координирующего взаим ное положение деталей, в которые вставлен штифт.
При выполнении штифтовых соединений с посадкой на конус
(фиг. 151, а) сверление отверстия под |
штифт в конической |
шейке |
необходимо производить в сборе с охватывающей деталью. |
Из-за |
|
неточностей обработки по диаметру |
конической шейки |
вала |
и конического отверстия, раздельно обработанные в соединяемых деталях отверстия под штифт не совпадут при соединении, и штифт либо не войдет в отверстие (фиг. 151, б), либо охватывающая деталь не будет плотно сидеть на конической шейке (фиг. 151, в). При таких соединениях’ целесообразно производить сверление и развертывание отверстия под штифт при сборке; при этом отверстие под штифт в охватывающей детали можно выполнить предварительно в про цессе механической обработки.
250Характеристика технологических методов производства
Кнеподвижным неразъемным соединениям относятся соедине ния, выполненные с гарантированным натягом, стяжками, разваль цовкой, клепкой, сваркой, пайкой, склеиванием и методом холодной
•штамповки.
Соединения с гарантированным натягом осуществляются прессо выми посадками или путем теплового воздействия на сопрягаемые детали. Прессовое соединение осуществляется под давлением пресса, когда охватываемая деталь вводится (запрессовывается) в отверстие охватывающей детали или, наоборот, охватывающая деталь насажи вается (напрессовывается) своим отверстием на охватываемую деталь.
Наличие натяга |
при осуществлении соединения |
вызывает |
упругие |
|||||
и пластические |
деформации сопрягаемых деталей, в особенности |
|||||||
их поверхностных слоев; в результате |
этих деформаций |
на по |
||||||
верхности сопряжения |
возникают значительные |
нормальные дав |
||||||
ления. |
|
|
|
|
|
|
|
|
Сила Рп, которую необходимо приложить для осуществления |
||||||||
запрессовки, может быть определена по формуле |
|
|
||||||
|
|
Pn = fnPlcdl |
кг, |
|
|
|
|
(103) |
где /„ — коэффициент |
запрессовки, |
т. |
е. |
коэффициент |
трения |
|||
(сцепления) при запрессовке; |
|
|
|
|
|
|||
р — удельное давление на сопрягаемых поверхностях в кг/мм2\ |
||||||||
d — номинальный диаметр соединения в мм\ |
|
|
||||||
I — длина |
посадочных поверхностей |
в мм. |
|
от мате |
||||
Коэффициент |
запрессовки выбирается |
в |
зависимости |
риала сопрягаемых деталей, чистоты обработанных поверхностей, наличия смазки и удельного давления на сопрягаемых поверхно стях. Величина коэффициента запрессовки возрастает с улучшением чистоты посадочных поверхностей, достигая определенного оптимума, затем начинает снижаться, несмотря на дальнейшее улучшение чистоты; это снижение зависит от удельного давления и по мере роста удельного давления идет сначала резко, а затем замедленно; при этом резкое уменьшение величины коэффициента запрессовки по мере роста удельного давления наблюдается у сопряжений с более чистыми посадочными поверхностями [64].
При выборе коэффициента запрессовки f n (коэффициента трения) можно пользоваться следующими данными [6 8 ]: для случая, когда вал и втулка изготовлены из стали 30—50 (со смазкой машинным маслом) /„=0,06-4-0,22, из чугуна СЧ28-48 /„=0,06ч-0,14, из магние воалюминиевых сплавов /„ =0,02ч-0,08, из латуни /„ = 0,05-4-0,10, из пластмассы /л = 0,54.
Принимая:
D — наружный диаметр втулки (ступицы) в мм, d9 — диаметр отверстия пустотелого вала в мм, i — натяг посадки в мм,
Еа — модуль упругости материала втулки в кг!мм%,