
книги / Основы технологии машиностроения
..pdfХарактеристика технологических методов производства деталей машин 181
Л и т ь е в с т е р ж н е в у ю ф о р м у применяется для ответ ственных отливок сложной конфигурации (цилиндры двигателей, головки цилиндров, лопатки турбин и т. п.). Форма собирается из стержней по шаблонам и кондукторам и обеспечивает высокую
точность отливки (I—II классы). |
( к о к и л ь ) при |
Л и т ь е в п о с т о я н н у ю ф о р м у |
меняется для отливок как цветных, так и черных металлов. Стойкость форм при литье заготовок из легкоплавких сплавов
(цинк, алюминий, магний) достигает сотен тысяч отливок, при литье чугуна 1500—5000 отливок, при литье стали 600—700 мелких отли вок, 150—250 средних, 20—25 крупных [701.
Чтобы избежать образования твердой закаленной корки на поверх ности соприкосновения отливки с металлической формой, необходимо замедлить скорость остывания поверхностного слоя отливки; для этого внутренняя поверхность формы покрывается слоем облицовки толщиной 10—12 мм, на которую дополнительно наносится слой сажи; другим способом является предварительный подогрев формы до температуры 200—400° и покрытие рабочих поверхностей формы огнеупорной краской слоем около 0,1 мм.
Литье в постоянные формы дает значительные технико-экономи ческие преимущества по сравнению с отливкой в земляные формы: 1) повышается качество отливаемых заготовок (т. е. достигается более высокая точность отливок и чистота их поверхностей, улучшение структуры металла); 2) исключается процесс формовки, сокращается применение формовочных материалов и связанных с их переработкой и транспортированием агрегатов; 3) сокращаются производственные площади и 4) увеличивается производительность труда.
Заготовки, отливаемые в кокиль, должны допускать свободное удаление их из формы и не должны иметь резких переходов по тол щине стенок.
Для отливки в постоянные формы могут быть применены специаль ные машины. При этом упрощается работа и повышается производи тельность труда за счет механизации или автоматизации процессов открывания и закрывания формы, выемки стержней и удаления отливок. Машины могут быть одноместными и многоместными с кару
сельным столом, несущим до 12 |
форм. |
М е т о д н е п р е р ы в н о г о |
л и т ь я следует рассматривать |
как одну из разновидностей литья в металлическую форму. Сущ ность его заключается в том, что расплавленный металл непре рывно и равномерно поступает в охлаждаемую водой металлическую форму — кристаллизатор с одного конца и в виде затвердевшего слитка вытягивается с другого конца. Этим методом получают
слиток в виде трубы или |
прутка постоянного сечения любой длины |
с высокими механическими |
свойствами отливки и высоким качеством |
поверхности [72]. Таким образом, этот метод может быть применен для литых деталей, аналогичных деталям, изготовляемым из проката специальных профилей.
182 |
Характеристика технологических методов |
производства |
|||
|
Л и т ь е м е т о д о м |
в а к у у м н о г о |
в с а с ы в а н и я за |
||
ключается в том, |
что расплавленный металл засасывается из тигля |
||||
в |
металлическую |
форму |
путем |
создания в |
ней вакуума. Наряду |
с некоторыми технологическими |
преимуществами этого способа, он |
||||
обладает двумя существенными |
недостатками — низкой производи |
тельностью и ограниченной областью применения (отливка втулок и других заготовок несложной формы).
Ли . т ь е м е т о д о м в ы ж и м а н и я осуществляется следую щим образом: расплавленный металл заливается в нижнюю часть металлической формы и при опускании пуансона выжимается, заполняя пространство между нижней частью формы и пуансоном. Применяется этот метод для тонкостенных крупногабаритных дета
лей типа крышек, тонкостенных плит и т. |
п. [72]. |
Ц е н т р о б е ж н ы й м е т о д литья |
применяется в тех слу |
чаях, когда могут быть использованы центробежные силы для прида ния жидкому металлу формы изложницы. Центробежный метод при меняют чаще всего для тел вращения (втулки, трубы, гильзы) и для фасонных отливок, имеющих ось симметрии (фланцы, шкивы, колеса); ось вращения изложницы в этом случае совпадает с осью симметрии
отливок. Центробежным способом могут |
отливаться и заготовки, |
не имеющие оси симметрии (тормозные |
колодки, рычаги, вилки |
и т. п.); в этих случаях ось вращения центробежной машины лежит вне отливок и центробежная сила используется лишь для заполнения формы металлом, а образование наружных и внутренних контуров отливки осуществляется формой.
Допуски на размеры отливок, полученных центробежным спосо бом, соответствуют 7—8-му классу точности; в связи с этим значи тельно сокращается последующая механическая обработка. Заго товки, полученные центробежным литьем, характеризуются мелко зернистым строением. Шлаковые включения, скопляющиеся на внут ренней поверхности отливки, удаляются при последующей механи ческой обработке.
Для центробежного литья применяют металлические и футеро ванные изложницы. Изложницы, изготовленные из легированных сталей (хромоникелевой или хромомолибденовой), обладают стой костью 2000—3000 отливок.
Л и т ь е п о д д а в л е н и е м является высокопроизво дительным методом получения точных отливок, последующая меха ническая обработка которых либо совершенно исключается, либо сводится к отдельным операциям.
Литье под давлением осуществляется на специальных машинах с применением металлических форм, стойкость которых зависит от термических напряжений, возникающих в форме в процессе про изводства отливок; чем выше температура плавления отливаемого сплава, тем большие трудности возникают при отливке деталей этим сдособом. Поэтому литье под давлением применяется главным обра зом для цинковых, алюминиевых, магниевых и латунных сплавов
Характеристика технологических методов производства деталей машин 183
Производительность полуавтоматов для мелкого литья под давле нием (весом не более 300 г) достигает 300 циклов в час, автоматы для мелкого литья дают 500 и более циклов в час. Наиболее быстроход ные из современных машин этого типа достигают 1000 циклов в час; располагая по 6—8 деталей в форме, можно достигнуть производи тельности 6000—8000 отливок в час.
Для средних отливок (весом 0,3—3 кг) применяются обычно полуавтоматы, дающие 80—250 циклов в час. Машины для крупных отливок (весом 3—15 кг) дают 40—100 циклов в час.
Литьем под давлением возможно отливать армированные элементы машин путем установки в форму обработанных деталей из других сплавов (бронзы, чугуна, стали).
К заготовкам (деталям), отливаемым под давлением, предъяв
ляются технологические |
требования, аналогичные требованиям |
к заготовкам, отливаемым |
в кокиль. |
Средняя стойкость форм для литья под давлением зависит от вида заливаемого сплава и определяется ориентировочно следующими дан
ными: для цинковых |
сплавов |
150 000 отливок; для алюминиевых |
|||
и магниевых |
сплавов |
40 000; |
для медных сплавов 5000. |
приме |
|
Л и т ь е |
по |
в ы п л а в л я е м о й |
м о д е л и |
няется для получения весьма точных форм и размеров отливок, не тре бующих механической обработки или ограничивающих ее лишь отделочными операциями. Этим методом можно получить отливки из различных металлов, а также из твердых сплавов, не поддающихся последующей механической обработке.
Технология изготовления литейной формы при этом методе литья не требует формовочных уклонов у модели и разъема формы.
Л и т ь е в о б о л о ч к о в ы е ф о р м ы основано на свой стве термореактивной смоло-песчаной смеси принимать форму подо гретой металлической модели с образованием сравнительно тонкой и быстрозатвердевающей оболочки.
Литье этим методом обеспечивает высокую точность отливок, отклонения размеров которых находятся в пределах 4—5-го класса точности для элементов заготовки, полученных в одной полуформе, и 7-го класса точности для элементов, полученных в обеих полуформах. Чистота поверхности отливок соответствует 4-му классу по ГОСТу 2789-51. В связи с высокой точностью отливок значительно уменьшаются припуски на обработку; вместе с тем сокращается расход металла на литники. Значительно уменьшается также тру доемкость очистки литья и последующей механической обработки отливок. Этот метод применим для литья как черных, так и цветных металлов.
Литье в оболочковые формы открывает широкие возможности автоматизации производства путем применения многопозиционных автоматов карусельного типа для изготовления форм, кольцевых вращающихся печей для подогрева моделей, автоматизации сушки форм и других процессов изготовления форм и их заливки.
Н54 |
Характеристика технологических методов |
производства |
|
О б р у б к а и о ч и с т к а о т л и в о к |
производится с целью |
удаления литников, прибылей, заусенцев, пригара, окалины и т. п. Литники и прибыли у чугунных отливок отбиваются. Литники и прибыли у стального и цветного литья удаляются на ленточных
или дисковых пилах, эксцентриковых прессах-зубилах и газовой резкой. Заусенцы, пригар и другие неровности удаляются с поверх ностей отливок пневматическими зубилами и абразивными кругами. Для удаления литников и облоя у отливок, изготовленных литьем под давлением, применяют обсечиые штампы.
Очистка поверхностей отливок производится на дробеметных уста новках с механической подачей дроби. Голтовка в барабанах и песко струйная очистка не рекомендуются по изложенным выше сообра
жениям. |
|
|
М е х а н и ч е с к а я |
о б р а б о т к а |
з а г о т о в о к |
Получение заданных форм, размеров и качества поверхностей деталей машин достигается обычно соответствующей обработкой заготовок.
Доминирующее значение в современном машиностроении все еще имеет обработка резанием (снятием стружки). Применяется и окон чательная обработка без снятия стружки — пластическим деформи рованием, а также способом дробеструйного наклепа.
Обработка снятием стружки является наиболее широко приме няемым в настоящее время способом обработки заготовок для дета лей машин. Наряду с механической обработкой на металлорежущих станках, используется также и слесарная обработка. Удельное зна чение слесарной обработки в массовом и серийном производстве ничтожно, но в единичном и мелкосерийном производстве, а также при ремонтных работах слесарная обработка достаточно широко применяется для пригонки сопрягаемых деталей машин 1.
Обработка снятием стружки на металлорежущих станках произ водится лезвийными (резцы, фрезы, сверла, зенкеры, развертки, протяжки и др.) и абразивными (круги, бруски) режущими инстру ментами.
П р и о б р а б о т к е р е з ц а м и различают обдирочную обра ботку (обдирку), черновую, получистовую и чистовую обработку. В ряде случаев, в зависимости от точности выполнения черной заготовки, ограничиваются однократной обработкой лезвийными инструментами. Для получения точных размеров и высокой чистоты поверхности применяют тонкую обработку.
Обдирка применяется главным образом для заготовок, получен ной свободной ковкой, а иногда и для крупных отливок III класса точности. Обдирка производится с целью уменьшения пространст
1 О слесарно-пригоночны х работах и их механизации см. в § 2 этой главы «Ха рактеристика технологических методов сборки».
Характеристика технологических методов производства деталей машин 185
венных отклонений и погрешностей формы черной заготовки. При обдирке могут быть выдержаны размеры: для поковок по 10—11-му и для отливок — по 9—10-му классам точности по ГОСТу 2689-54.
После обдирки допускается местная чернота заготовки. Обдирку крупных (тяжелых) заготовок целесообразно производить на заводах и в цехах, поставляющих заготовки. В этом случае поверхностные дефекты заготовки выявляются на месте ее производства, умень шается вес заготовки перед ее транспортированием и удлиняется срок вылеживания ободранной заготовки (естественного старения).
Черновую обработку применяют для заготовок, подвергавшихся обдирке, для крупных штампованных поковок третьей и второй групп точности и для крупных отливок III и II классов точности; в первом случае черновая обработка обеспечивает S—7-й класс точности, а во втором и третьем случаях 7—5-й класс точности по системе ОСТ.
Достигаемая при черновой обработке чистота поверхности нахо дится в пределах 1—3-го класса по ГОСТу 2789-51.
Получистовая обработка применяется, когда при черновой обра ботке не может быть удален весь припуск, либо когда предъявляются повышенные требования к точности геометрических форм обрабаты ваемой заготовки и пространственным отклонениям ее элементов.
При получистовой обработке размеры заготовки выдерживаются с допусками по 5 и 4-му классам точности; чистота поверхности обес печивается в пределах 2—4-го класса по ГОСТу 2789-51.
Чистовая обработка применяется либо как окончательная, либо как промежуточная под последующую отделку (тонкая обработка, шлифование). Чистовая обработка в зависимости от процесса пред шествующей обработки обеспечивает 4-й и За классы точности и 4—6-й класс чистоты.
Однократная обработка применяется для заготовок, полученных методами, обеспечивающими высокую точность их выполнения (штам повка по первой группе точности, литье в кокиль, литье По выплав ляемой модели и т. п.). Она выполняется по черной поверхности, но с режимами, близкими к чистовой обработке.
В зависимости от точности выполнения заготовки, однократная обработка обеспечивает 4—7 классы точности и 3—5 классы чистоты.
Если требующаяся точность не позволяет ограничиться однократ ной обработкой, то ее используют, как предварительную операцию под тонкую обработку или шлифование.
Тонкая обработка резцами применяется как метод окончательной отделки, заменяющий шлифование, и осуществляется при высоких скоростях резания, малых глубинах резания (0,05—0,5 мм) и малых подачах (0,05—0,15 мм/об).
Тонкое точение обеспечивает 2а—3 классы точности 7—8 классы чистоты.
Высокая точность и чистота поверхности при тонкой обработке достигаются благодаря специфическим условиям ее выполнения. Станки для тонкой обработки отличаются весьма высокими геомет
166 Характеристика технологических методов производства
рической точностью и жесткостью, а режущие инструменты — высо кой износоустойчивостью.
Настройка инструмента и станка на размер выполняется при помощи микрометрических и индикаторных устройств с большой точностью.
Возникающие в процессе обработки с малыми глубиной резания и подачей силы резания незначительны и постоянны по величине, что в условиях жесткой системы станок — заготовка — инструмент сводит к минимуму величину колебания отжатий для партии заго товок.
Таким образом достигается уменьшение каждого из составляющих допуска на обработку.
Особо следует отметить тонкую обработку широкими резцами, к которой относится тонкое обтачивание широким резцом и тонкое строгание широким резцом. Глубину резания при тонкой обработке широкими резцами принимают не более 0,5 мм, а подачу назначают в зависимости от ширины резца; обычно подача на оборот или двой ной ход составляет не более 0,8 ширины резца.
Тонкая обработка широкими резцами обеспечивает 3—2а классы точности и 6—8-й класс чистоты, а при индивидуальном получении заданных размеров 2-й и даже 1-й класс точности и 7—9-й класс чистоты.
Обработка резцами токаря-новатора В. А. Колесова дает высо кую производительность труда, обеспечивая чистоту поверхности 4—5-го класса при глубине резания до 4 мм, подаче до 3 мм/об и ско
рости резания |
60—150 м/мин и до 7-го класса чистоты при глубине |
|
резания |
1 мм, |
подаче до 5 мм/об и скорости резания 90—200 м/мин. |
П р и |
о б р а б о т к е ф р е з а м и различают черновое, полу- |
чистовое и чистовое фрезерование, а при обработке торцовыми фре зами также и тонкое фрезерование; в некоторых случаях ограничи ваются однократным фрезерованием.
Черновое фрезерование применяют как метод предварительной обработки отливок и поковок, припуск на предварительную обра ботку которых превышает 3 мм. Черновое фрезерование плоскостей обеспечивает 2—4-й класс чистоты и отклонение от прямолинейности 0,15—0,3 мм на 1 м длины.
Получистовое фрезерование применяют в тех случаях, когда погрешности черной заготовки обусловливают большую глубину реза ния. Стружку в этом случае делят между черновым и получистовым фрезерованием. Применяют получистовое фрезерование также с целью уменьшения погрешностей геометрических форм и простран ственных отклонений, так как каждый проход инструмента значи тельно снижает эти погрешности. Получистовое фрезерование обеспе чивает 3—5-й класс чистоты и отклонение от плоскости 0,1—0,2 мм на 1 м длины.
Чистовое фрезерование применяют либо как метод окончательной обработки после чернового и получистового фрезерования, либо как
Характеристика технологических методов производства деталей машин 187
метод промежуточной обработки после чернового фрезерования перед последующей отделочной обработкой.
Чистовое фрезерование обеспечивает 4—6-й класс чистоты и откло нение от плоскостности 0,04—0,08 мм на 1 м длины.
Тонкое фрезерование применяют как метод окончательной обра ботки плоских поверхностей торцовыми фрезами. Припуск под тон кое фрезерование оставляют в пределах 0;2—1 мм. Тонкое фрезеро вание обеспечивает 6—8-й класс чистоты поверхности и отклонение от плоскостности 0,02—0,04 мм на 1 м длины.
Однократное фрезерование применяют в тех случаях, когда погрешности черной заготовки обусловливают незначительный при пуск на обработку (менее 2 мм). Однократное фрезерование обеспе чивает 4—5-й класс чистоты и отклонение от плоскостности 0,06— 0,1 мм на 1 м длины.
Применяя скоростные режимы при фрезеровании, получают: при черновом 3—5-й, при получистовом 4—6-й и при чистовом фрезе ровании 5—7-й классы чистоты поверхности.
С в е р л е н и е применяется для получения отверстий в сплошном металле. Сверление обеспечивает 5—4-й класс точности и 5— 3-й класс чистоты поверхности. Этот метод обработки отверстий нахо дит широкое применение в качестве предварительной обработки точных отверстий.
Обработка грубых отверстий ограничивается весьма часто одним
только сверлением. |
либо после сверления, |
либо для |
||
З е н к е р о в а н и е применяют |
||||
обработки |
отлитых |
или прошитых |
отверстий в черных заготовках. |
|
В первом |
случае |
зенкер, снимая |
значительную часть |
припуска, |
выправляет погрешности, имеющиеся у просверленного отверстия, а именно увод оси отверстия и смещение осей координированных отверстий. Это достигается при направлении зенкера кондукторной втулкой. Во втором случае зенкер сообщает отверстию правильную форму и выправляет ось отверстия. При зенкеровании литых и про шитых отверстий в черных заготовках получают 5-й класс точности и 3-й класс чистоты. При зенкеровании после сверления получают 4-й класс точности и 4-й класс чистоты поверхности. Однократное скоростное с охлаждением зенкерование литых отверстий в отлив
ках из серого |
чугуна |
обеспечивает 4-й класс |
точности |
и 4—5-й |
класс чистоты |
поверхности [55]. |
обычно |
как метод |
|
Р а з в е р т ы в а н и е |
отверстий применяется |
окончательной обработки либо как метод, предшествующий прити рочному шлифованию (хонингованию). Развертывание не исправляет увода и смещения оси отверстия и применяется для получения точного диаметрального размера.
В зависимости от предъявляемых к отверстию требований при меняют нормальное, точное и тонкое развертывание. Эти виды развер тывания различаются главным образом по допускам на диаметраль ные размеры разверток.
188 Характеристика технологических методов производства
Нормальное развертывание обеспечивает За—3-й класс точности и 6-й класс чистоты поверхности (развертки выполняются по 2а классу точности); точное развертывание дает 2а класс точности и 7-й класс чистоты (развертки выполняются по 2-му классу точности); тонкое развертывание — 2—1-й класс точности и 8-й класс чистоты (допуски на развертки принимают равными 0,6 от допусков 1-го класса точ ности).
Для окончательной обработки точных отверстий 2 и 1 классов точности диаметром 25—600 мм применяется развертывание плаваю щими пластинами. Пластина вставляется в паз оправки и имеет воз можность перемещаться в радиальном направлении.
Плавающие пластины не выправляют и не изменяют положения оси отверстия, которое должно быть точно определено предшествую щей обработкой, ими достигают лишь повышения точности диамет рального размера и качества поверхности отверстия.
П р о т я г и в а н и е применяют для обработки отверстий и пазов любого сечения, плоских и криволинейных поверхностей и наружных поверхностей вращения.
При протягивании имеется возможность упростить обработку, так как во многих случаях одна протяжка заменяет несколько инстру ментов (например, зенкер или расточный резец и развертку; черновую и чистовую фрезы и т. п.). Протягиванием обрабатывают предвари тельно обработанные либо черные поверхности.
Протягивание как метод обработки отверстий находит широкое применение благодаря высокой производительности.
Когда торец заготовки обработан, она этим торцом прижимается усилием резания к лобовой поверхности протяжного станка. Если торец заготовки не обработан, то она опирается на сферическую самоустанавливающуюся опору.
Протягивание плоских поверхностей осуществляют на верти кально-протяжных или горизонтально-протяжных станках с уста новкой обрабатываемой детали в приспособлении.
Обработка наружных поверхностей вращения производится на специальных протяжных станках с вращением заготовки, а криво линейных поверхностей — на протяжных станках с вращающимся столом. Применяется обработка протягиванием зубьев венцов зубчатых колес.
Протягивание является перспективным методом обработки, кото рый может осуществляться на станках различных типов, включая непрерывно действующие автоматизированные станки. Протягива нием обеспечивается За—2а класс точности и 5—7-й класс чистоты.
Прошивание1 отверстий применяют как метод окончательной обработки отверстий любой формы небольшой длины, обеспечиваю щий 2-й и выше класс точности и 7—8-й класс чистоты.
1 Реж ущ ей прошивкой называют короткую протяж ку, проталкиваемую через отверстие и работаю щ ую на сж атие.
Характеристика технологических методов производства деталей машин 189
Шл и ф о в а н и е применяют как метод окончательной обработки. Обдирочное шлифование как метод однократной окончательной обработки применяют при шлифовании плоских базовых поверх ностей для обеспечения необходимой плоскостности, обычно без выдерживания размера. Обдирочное шлифование производят на шлифо вально-обдирочных станках с верти кальным шпинделем, наборным из сег-
Фиг. |
ПО. |
Ш лифование |
Фиг. |
111. |
Ш лифование |
плоскости |
плоскости |
периферией |
периферией |
шлифовального |
круга на |
||
ш лифовального круга на |
станке |
с |
прямолинейно-возвратным |
|||
станке |
с |
вращающимся |
|
движением стола. |
|
|
|
столом. |
|
|
|
|
ментов кругом. Обычно применяют круги зернистостью 16—24, реже 24—36. Обдирочным шлифованием получают 5—6-й класс чистоты поверхности.
Фиг. 112. |
Ш лифование |
Фиг. 113. |
Ш лифование |
пло |
|
плоскости |
торцом чашеч |
скости |
торцом |
чашечного |
|
ного ш лифовального круга |
ш лифовального |
круга |
на |
||
на станке с |
вращающимся |
станке с прямолинейно-воз |
|||
столом. |
вратным |
движением стола. |
Предварительное шлифование плоских поверхностей после обра ботки лезвийным инструментом производится периферией (фиг. 110 и 111) или торцом чашечного круга (фиг. 112 и 113). В первом случае
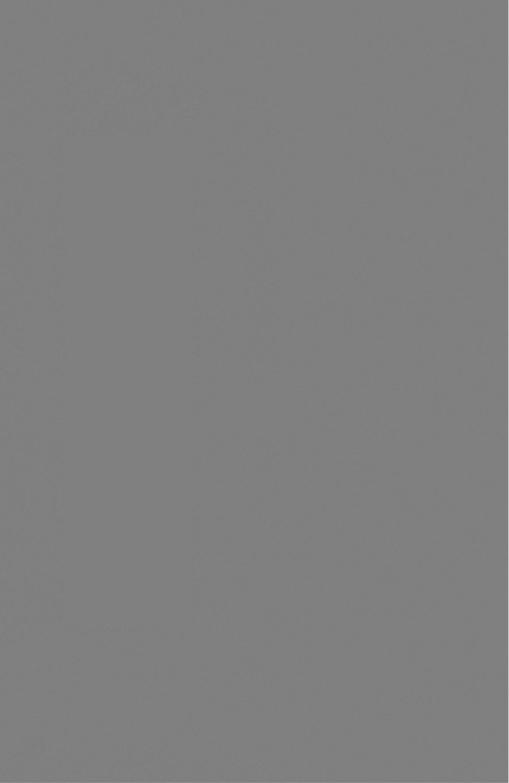