
книги / Основы технологии машиностроения
..pdfХарактеристика технологических методов производства деталей машин 161
Пр о к а т
Вмашиностроении прокат применяется как исходный материал для поковок и для непосредственного изготовления из него деталей путем обработки снятием стружки на металлорежущих станках.
Для непосредственного изготовления деталей машин из проката применяют калиброванные прутки и горячекатаную сталь повышен ной и обычной точности.
По ГОСТу 7417-57 калиброванные прутки изготовляют диаметром от 3 до 30 мм по классу точности 2а, от 3 до 65 мм — по 3-му и За классам точности и от 3 до 100 мм — по 4 и 5-му классам точности. При креплении в цанговых зажимах применяются калиброванные прутки 5-го класса точности. Калиброванные прутки 4-го и высших классов точности обычно не подвергают обработке лезвийным инструментом, а непосредственно шлифуют.
По ГОСТу 2590-57 круглая горячекатаная сталь повышенной
точности изготовляется диаметром 5—150 мм\ диаметральные раз меры ее выдерживаются приблизительно по 8-му (до 56 мм), по 9-му (свыше 50 до 125 мм) и грубее 9-го (130—150 мм) классам точности; круглая горячекатаная сталь обычной точности изготовляется диа метральными размерами 5—250 мм, которые выдерживаются приб лизительно по 9-му классу точности (до 95 мм) и несколько грубее 9-го класса точности для размеров 100—250 мм. Предварительная обра ботка горячекатаной стали производится лезвийным инструментом либо из отрезанных заготовок, либо непосредственно из прутка.
В ряде случаев для изготовления деталей соответствующей кон фигурации применяют квадратную, шестигранную, полосовую, угло вую. швеллерную и других профилей стали, а также бесшовные
исварные трубы.
Вусловиях крупносерийного и массового производства (сель хозмашиностроение, вагоностроение, автомобилестроение) оправ
дывается применение проката специальных профилей (фиг. 100),. почти полностью исключающего или значительно сокращающего механическую обработку, на долю которой остается в основном отрезка, сверление отверстий и зачистка. В тех случаях, когда в силу технических условий все же требуется обработка некоторых поверх ностей проката специальных профилей, съем стружки значительно уменьшается и сокращается время, затрачиваемое на обработку.
При изготовлении деталей высоких классов точности из проката применяют в целях сокращения обработки снятием стружки х о л о д ное п р о ф и л ь н о е в о л о ч е н и е . Этим методом может быть получен профиль, соответствующий контуру готовой детали, причем размеры могут быть выдержаны с допусками, исключающими необходимость последующей обработки резанием.
На фиг. 101 показаны последовательные переходы при волочении v полосовой стали для получения прутка с профилем сегментной шпонки. На фиг. 102 показано волочение этих шпонок из круглого
11 Кован 572
162 Характеристика технологических методов производства
Фиг. 100. Прокат специальных про филей
Фиг 101. Волочение полосовой стали для сегментных шпонок
Фиг 102. Волочение круглой стали для сегментных шпонок
Характеристика технологических методов производства деталей машин 163
проката и на фиг. 103 — волочение фасонного профиля из круглого проката.
Метод холодного профильного волочения стали является деше вым и высокопроизводительным и обеспечивает значительную эко номию металла. Например, при волочении сегментных шпонок из прямоугольного профиля стали 45 с последующей рубкой на прес сах и шлифованием плоскостей расход металла на одну шпонку составляет 9,6 г, а при обработке снятием стружки на ту же шпонку расходуется 13,8 г; таким образом, экономия металла на 1 шт. составляет 4,2 г, или более 30%. Производительность при этом повы шается более чем в 3 раза. Вместе с тем холодное профильное воло чение повышает поверхностную твердость и износостойкость деталей.
Наиболее целесообразным является применение профильного волочения для деталей с одинаковым фасонным профилем по всей длине. Холодным волочением могут быть получены самые разно образные профили: храповые колеса, мелкие шестерни, угловые, корытообразные и другие сложные профили. При этом без затрудне ний выдерживается 4-й класс точности и 6-й класс чистоты поверх ности.
Механической обработке заготовок из проката предшествует правка прутков и резка проката на заготовки. Отрезанные заготовки также подвергаются в ряде случаев правке в процессе механической обработки.
П р а в к а п р о в о л о к и производится на правйльно-отрез- ных станках. Правка осуществляется роликами, отрезка произво дится ножом по упору (фиг. 104). Остающаяся после правки кривизна достигает 0,5—0,7 мм на 1 пог. м проволоки.
П р а в к а п р у т к о в осуществляется на правильно-калибро вочных станках. Правка производится правйльными, а калибровка— отдельными калибрующими роликами (фиг. 105). Остающаяся после правки кривизна черного прутка достигает 0,9—0,5 мм на 1 пог. м.
Правйльно-калибровочные станки применяются также для правки и калибровки длинных прутковых заготовок после обработки
их на бесцентрово-токарных станках. В этом случае остающаяся |
|
после правки |
кривизна достигает 0,2—0,1 мм на 1 ж длины вала |
и может быть |
уменьшена до 0,05 мм/м. |
Правка на правйльно-калибровочных станках является высоко производительным методам: 1,4—1,6 м/мин при правке и 0,6— 0,8 м/мин при калибровке прутков. Точность калибровки по диа метру достигает 30—50 мк.
Холодная правка нарезанных из проката заготовок, а также холодная правка поковок производится на прессах, а цилиндри ческие заготовки небольшой длины правятся на накатных станках с гладкими плашками.
Х о л о д н а я п р а в к а на п р е с с а х (фиг. 106) приме няется для зацентрованных заготовок. Место и величина прогиба определяются индикатором при провертывании заготовки в центрах,
П+
i64 |
Характеристика технологических методов производства |
/ — правильные ролики; 2 — тянущие |
ролики, 3 — отрезное кольцо; 4 — отрез |
ной нож; |
5 — упор. |
Фиг. 105. Схема правильно-калибровочного станка:
1 — вращающаяся рама; 2 — правйльные ролики; 3 — калиб рующие ролики; 4 — пруток, подвергающийся правке.
Характеристика технологических методов производства деталей машин 165
которые затем отводятся, а заготовка опускается на жесткие опор ные призмы. Прилагаемое усилие и величина хода ползуна регули руются в приводных прессах нажимом педали. Остающаяся после правки кривизна заготовки составляет в зависимости от ее диаметра 0,05—0,15 мк на 1 мм общей длины заготовки.
Разрез по АД
Фиг. |
106. Схема правки заготовок на |
прессе: |
1 — отводимые центры; |
2 — опорные призмы; 3 — индикатор; |
4 — заготовка; б — ползун. |
Разновидностью этого метода является правка заготовки, уста новленной в центрах, струбциной вручную. При той же точности правки производительность труда при правке струбциной значи-
тельно ниже, чем при правке на прессах. |
|
|
|
||||||
Х о л о д н а я |
п р а в к а |
на |
|
|
|
||||
н а к а т н ы х с т а н к а х с г л а д |
|
|
|
||||||
к и м и |
п л а ш к а м и (фиг. 107) при |
|
|
|
|||||
меняется для незацентрованных цилин |
|
|
|
||||||
дрических заготовок |
небольшой длины. |
|
|
|
|||||
Правка достигается |
прокатыванием за |
|
|
|
|||||
готовки |
между |
плоскими |
гладкими |
|
|
|
|||
плашками. Этот |
метод обеспечивает вы |
Фиг. |
107 Схема правки цилинд |
||||||
сокую |
производительность |
труда |
при |
рических заготовок на накатных |
|||||
точности правки 0,05—0,15 |
мк на 1 мм |
|
станках: |
|
|||||
/ — плоские гладкие |
плашки; |
||||||||
общей длины заготовки. |
|
|
|||||||
|
|
|
2 — заготовка. |
|
|||||
В результате холодной правки про |
напряжений в материале, |
||||||||
исходит |
перераспределение внутренних |
||||||||
вызывающее деформацию |
детали. |
Поэтому |
холодную |
правку |
|||||
не применяют |
при |
изготовлении |
особо ответственных |
деталей |
|||||
машин. |
|
|
|
для механической обработки |
проката |
||||
Р е з к а з а г о т о в о к |
|||||||||
производится на |
ножницах |
и прессах, |
распиливанием, отрезными |
резцами на станках токарного типа, анодно-механическим способом,
фрикционными |
дисками, газовой |
(кислородной) |
резкой и дуговой |
электрорезкой. |
н о ж н и ц а х |
и п р е с с а х |
является высоко |
Р е з к а на |
производительным методом резки заготовок из проката. Однако при этом методе резки получается вмятина; величина ее в направле нии, перпендикулярном к резу, определяется на основании опытны^
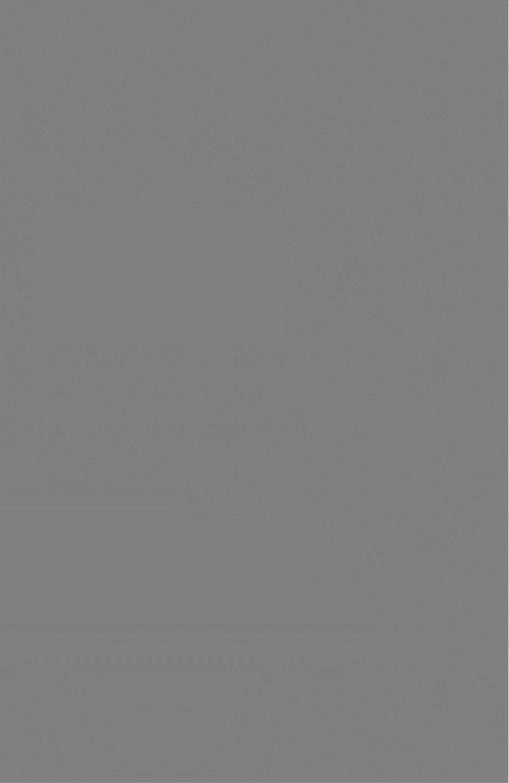
Характеристика технологических методов производства деталей машин 167
зубьев 30—60 или 18—30, в зависимости от конструктивного испол нения. Резка производится обычно при подачах 0,01—0,03 мм/зуб.
Р е з к а а б р а з и в н ы м и |
к р у г а м и |
применяется для |
разрезания закаленных стальных |
заготовок, |
а также прутков |
из инструментальных сталей и других твердых материалов. Круги для отрезки изготовляются на бакелитовой или вулканитовой связке и допускают окружную скорость круга: на бакелитовой связке 50 м/сек, на вулканитовой связке 30 м/сек.
Величина пропила при разрезании в 1,5—2 раза превышает
толщину инструмента — ножовочного полотна, |
ленточной пилы, |
дисковой пилы, отрезной фрезы или абразивного круга. |
|
Р е з к а о т р е з н ы м и р е з ц а м и на |
станках токарного |
типа применяется обычно для заготовок из прутка или трубы, а также для предварительной разрезки прутков и труб на мерные заготовки. Наибольший диаметр разрезаемого прутка зависит от модели станка. Имеются крупные станки для разрезания слитков; например слиткоразрезной станок, модель 1865, предназначен для разрезания слит ков диаметром до 600 мм и длиной до 3200 мм. В тяжелом машино строении успешно применяют резку отрезными резцами деталей значительно большего диаметра при вылете резцов, достигающем 650 мм. Резцы оснащены твердым сплавом Т5К10; ширина их 18— 22 мм. Резка производится с подачами 0,2—0,4 мм/об при скорости резания 35—200 м/мин в зависимости от обрабатываемого материала и наличия охлаждения.
Обычно отрезка производится не до конца, а оставляется шейка диаметром 0,07—0,2 диаметра отрезаемой заготовки, которая по окон чании резки отламывается. Однако опыт показывает, что как при отрезке без оставления шейки, так и при отрезке заготовок с цент ральным отверстием поломки инструмента наблюдаются редко.
Точность резки по длине заготовки не зависит от рассмотренных методов резки и длины заготовки, но зависит от ее поперечного раз мера, так как отклонение от перпендикулярности поверхности реза (торца) к оси заготовки возрастает пропорционально поперечному
ее размеру, а при отрезке резцами — радиусу |
прутка или разнице |
радиусов наружной и внутренней поверхностей для труб. |
|
А н о д н о - м е х а н и ч е с к а я р е з к а |
производится вра |
щающимся беззубым диском или беззубой лентой, аналогично диско вой или ленточной пилам. При этом разрезаемый пруток — анод соединен с положительным полюсом, а инструмент, т. е. диск или лента — катод — с отрицательным полюсом низковольтного генера тора. Инструмент скользит с небольшим давлением по плоскости реза, а струя рабочей жидкости подается соплом в зазор между прут ком и инструментом; на поверхности анода образуется плохо прово дящая ток пленка; разрушение металла происходит в результате электрохимического растворения пленки и механического удаления
ее диском или лентой. Твердость и прочность металла |
заготовки |
при анодно-механической резке не имеет существенного |
значения; |
168 |
Характеристика технологических |
методов |
производства |
|
этим методом можно резать |
любые металлы, |
включая и твердые |
||
сплавы. |
|
|
|
|
|
Электрические параметры режима анодно-механической резки |
|||
определяются следующими |
данными: |
рабочее напряжение тока |
2 0 —30 в\ сила рабочего тока 20—500 а\ плотность тока 7 0 —500 а/см2. Для анодно-механической резки обычно применяют постоянный ток. Переменный ток снижает интенсивность процесса и повышает износ инструмента.
Применяемые для резки металлов диски изготовляют преиму щественно из листовой стали. На выпускаемых нашей промышлен ностью станках для анодно-механической резки применяются диски диаметром 200 — 1050 мм и толщиной 0 ,5 — 2 мм. Износ дисков состав ляет 25 — 30% от веса удаленного металла и зависит от режима и условий проведения процесса. Ширина реза определяется толщи ной диска и зависит от его жесткости и осевого биения; обычно ширина реза в 1,5— 2 раза больше толщины диска.
В качестве рабочей жидкости применяют водный раствор жидкого стекла, соли фосфорной или кремниевой кислоты, сернистый натрий, взвеси глины в воде и другие жидкости, способные образовывать на аноде пленку, плохо проводящую ток. Подача жидкости состав ляет 5— 35 л/мин, в зависимости от диаметра разрезаемого прутка.
Окружная скорость диска 15— 20 м/сек\ подача 7 — 30 мм/мин; удельное давление диска 0 ,5 — 2 кг/см2, в зависимости от диаметра разрезаемого прутка.
В связи с незначительными давлениями, при которых протекает процесс, достигается высокая точность резки (300— 600 мк при диаметре отрезаемого прутка 18— 120 мм). Чистота поверхности при анодно-механической резке находится в пределах 2 —4-го класса чистоты по ГОСТу 2789-51. Твердость поверхности у стали несколько повышается лишь при жестких режимах за счет термических воздей ствий. Съем металла составляет 2000 — 6000 мм3/мин на дисковых
исвыше 6000 мм3/мин на ленточных станках.
Врезультате резки с высокими плотностями тока образуется «белый» поверхностный слой глубиной 10— 30 мк. При малых плот
ностях тока |
изменения структуры не наблюдается г. |
Р е з к а |
ф р и к ц и о н н ы м и д и с к а м и является высоко |
производительным методом мерной резки проката любых профилей и марок, включая высокопрочные труднообрабатываемые конструк ционные стали.
Процесс резки фрикционными дисками основан на использова
нии |
теплоты трения, |
возникающей в месте |
контакта разрезаемого |
|
1 |
Различные модели |
станков для анодно-механической |
резки применяются |
|
в зависимости от размеров отрезаемой заготовки; в частности, например: |
||||
|
Модель стан к а .........................АМО-32 |
4821 |
АМО-12 |
|
|
Наибольший диаметр прутка |
|
300 |
|
|
в „и,и |
100 |
150 |
Характеристика технологических методов производства деталей машин 169
металла с кромкой диска. Температура разрезаемого металла при этом повышается настолько (до 800—1100°), что он легко удаляется из пропила в виде пучка искр при весьма незначительном износе фрикционного диска. Иногда в связи с повышением температуры в зоне пропила происходит плавление частиц металла. Применяют диски с гладкой или насеченной кромкой (шаг насечки 3—4 мм, глубина насечки 1,5—2,0 мм)', окружная скорость диска 60— ПО м/сек. Диаметр диска выбирают в зависимости от размера разре заемого материала. В частности, например, для резки проката диа метром до 20 мм применяют диск 500 X 3,5 мм\ для проката диамет ром 100 мм — диск 700 X 5 лш; для резки тонкостенных труб диа метром 130 мм применяют диск 400 X 2,5 мм. Толщину диска В
принимают по соотношению В = 0,007D мм, где |
D — диаметр |
диска в мм. |
во избе |
Диск зажимается между шайбами, диаметр которых |
|
жание вибраций должен быть Ош > 0,5D. |
|
При резке прутков диаметром больше 10 мм рекомендуется при менять охлаждение диска. Производительность резки фрикцион ным диском выше производительности резки дисковой пилой при
близительно в |
2,5 раза |
и в 9 раз выше производительности резки |
приводной ножовкой. |
|
|
Г а з о в а я |
( к и с л о р о д н а я ) р е з к а применяется глав |
|
ным образом для резки |
листовой, полосовой и квадратной стали, |
но этот метод может быть применен также и для резки профильного проката. Правильно выполненная газовая резка не вызывает пере жога и оплавления кромки реза. В поверхностном слое реза на глу бину 2—5 мм получается нормализация стали, а при резке закали вающейся стали — закалка. Получившаяся высокая твердость устра няется местным или общим отжигом.
Чистый рез обеспечивается при содержании углерода до 0,3%; с повышением содержания углерода чистота реза ухудшается, а про
цесс резки замедляется; при |
содержании углерода свыше 0,8% |
не следует применять газовую |
резку. |
Некоторые легирующие элементы, в зависимости от содержания их в стали, затрудняют газовую резку (3% Сг; 0,25% Мо; 10% W; 2% А1) или препятствуют резке (5% Сг; 20% W; 10% А1). Содержа ние никеля свыше 20% несколько замедляет резку. Марганец, крем ний, медь, ванадий, титан, фосфор и сера в количествах, применяе мых в конструкционной стали, не препятствует резке.
Газовой резкой по шаблону (копирная резка) можно получать из толстолистовой, полосовой или квадратной стали заготовки весьма сложной конфигурации, почти не требующие благодаря точности и чистоте реза последующей механической обработки (звездочки, зубчатые колеса и т. п.). Обычная точность резки + 0,5 мм\ при резке на точных машинах + 0,2 мм.
Д у г о в а я э л е к т р о р е з к а применяется как для чер ных, так и для цветных металлов и сплавов.
170 |
Характеристика технологических методов производства |
При дуговой электрорезке металл разрезается в результате его расплавления в зоне реза. Этот метод не обеспечивает вследствие оплавления кромки точности и чистоты реза, которые получаются при кислородной резке, но при достаточной квалификации резчика дает в ряде случаев вполне удовлетворительные результаты.
П о к о в к и
Поковки могут быть получены свободной ковкой, ковкой в под кладных штампах и штамповкой в закрепленных штампах. Исход ными заготовками для поковок являются слитки и прокат. Слитки применяют для крупных поковок, получаемых свободной ковкой.
Слитки представляют собой усеченную пирамиду квадратного или многоугольного сечения, либо (при круглом сечении слитков) усеченный конус. Отношение длины слитка к среднему поперечному размеру принимается от двух до трех.
Слитки отливаются с прибылью, которую располагают у широ кого конца слитка. В процессе ковки как прибыль, в которой распо лагается усадочная раковина, так и донная часть слитка удаляются; при этом с удаляемой прибылью отходит 20—35%, с донной частью 5 —10% от веса слитка.
Сортовой прокат применяют для средних и мелких поковок, получаемых как свободной ковкой, так и штамповкой. Свобод ной ковкой можно выполнять поковки от самых мелких до самых крупных размеров, весом порядка 200 пг и более. Горячая штам повка применяется для поковок обычно весом от долей килограмма до 200 кг. В некоторых случаях горячей штамповкой изготовляют поковки и большего веса. Штамповка сравнительно со свободной ковкой обеспечивает более высокую точность и значительно большую :производительность.
Рассмотрим области применения различных методов изготовления поковок.
С в о б о д н а я к о в к а производится на ковочных молотах (паровоздушных, пневматических, рессорно-пружинных) и гидрав лических ковочных прессах.
Для мелких фасонных поковок весом до 40 кг, изготовляемых из сортового проката, применяют пневматические или рессорно пружинные, а иногда и паровоздушные молоты с весом падающих частей до 1 /7г.
Средние фасонные поковки весом до 300 кг, исходным материалом для которых служит крупный прокат или обжатая болванка, куют на паровоздушных молотах с весом падающих частей 1—3 пг, а более крупные поковки (фасонные весом до 700 кг и гладкие валы весом до 1500 кг) выполняют на паровоздушных молотах с весом падающих частей 5 ш и на гидравлических ковочных прессах силой пресса до 800 пг.
Применением ковочных прессов повышают производительность труда на 30—50% сравнительно с ковкой на паровоздушных моло