
книги / Основы технологии машиностроения
..pdfУстановка заготовок для обработки на станках |
51 |
или |
|
еэ = В cos а, |
(9) |
где е, — погрешность закрепления вследствие поворота |
заготовки; |
В— размер опорной базирующей поверхности в направлении зажимной силы;
а— угол, образуемый опорной базирующей и боковой поверх ностями (пространственное отклонение поверхностей заго товки).
Для черных поверхностей можно принимать угол поворота Р |
= 1°, |
|||||
для |
предварительно |
обработанных |
поверхностей |
р = |
0°40', |
для |
чисто |
обработанных |
р = 0°20\ для |
шлифованных |
р = |
0°04' |
[25]. |
Во избежание поворота заготовок при установке в приспособле ниях с направлением зажимной силы параллельно опорной бази рующей поверхности зажимные приспособления тисочного типа конструируют так, чтобы зажимная сила прижимала опорную базирующую поверхность к установочным элементам приспособле ния х.
Осевые смещения заготовок, закрепляемых в зажимной гильзе (цанге), в патроне или на оправке, также зависят от шероховатости
и |
макронеровностей поверхности, состояния поверхностного слоя |
и |
жесткости зажимных устройств. |
Радиальные смещения заготовок, закрепляемых в цангах и патро нах, определяются смещением оси заготовки относительно оси вра щения и зависят главным образом от геометрических погрешностей формы закрепляемой поверхности и жесткости зажимных устройств. Эти погрешности установки, так же как и погрешность базирования, не увеличивают непосредственно отклонений по выдерживаемому диаметральному размеру, но вызывают пространственные отклоне ния во взаимном положении элементарных поверхностей заготовок и изготовленных деталей.
Работы в области определения деформаций поверхностных слоев и погрешностей закрепления заготовок нельзя считать закончен ными в такой степени, чтобы можно было рекомендовать опреде ленный метод расчета их величии. Поэтому мы принуждены пользо ваться практическими данными, представляющими собой некоторые средние значения погрешностей закрепления заготовок 1.2
Таким образом, погрешность закрепления возникает под воз действием зажимных сил в результате смещения заготовки относи тельно установочных элементов приспособления и определяется так же, как и погрешность базирования, разностью предельных расстояний измерительной базы относительно установленного на раз мер режущего инструмента.
1 Конструкции зажимных устройств рассматриваются в курсе «Основы кон струирования приспособлений»
2 См. приложение 1
4*
52 |
Точность в машиностроении |
|
||
П о г р е ш н о с т ь |
у с т а н о в к и |
заготовок для |
обработки |
|
на станках, которую обозначим через |
еу, определяется суммарным |
|||
значением погрешности базирования |
гб |
и погрешности |
закрепле |
ния еэ. При обработке плоскостных заготовок и торцовых поверх ностей тел вращения погрешность базирования и погрешность
закрепления являются коллинеарными векторами, |
лежащими |
на одной прямой, и суммируются арифметически: |
|
еу = еб + ев. |
(10) |
При обработке поверхностей вращения векторы погрешности базирования и погрешности закрепления могут иметь любое угловое
|
|
|
|
|
|
|
взаимное |
положение. В этих |
|||||
|
|
|
|
|
|
|
случаях |
погрешность |
уста |
||||
|
|
|
|
|
|
|
новки определяется геометри |
||||||
|
|
|
|
|
|
|
чески, |
как векторная сумма |
|||||
|
|
|
|
|
|
|
погрешности |
|
базирования |
||||
|
|
|
|
|
|
|
и погрешности |
закрепления; |
|||||
|
|
|
|
|
|
|
при этом наиболее вероятное |
||||||
|
|
|
|
|
|
|
значение |
погрешности |
уста |
||||
|
|
|
|
|
|
|
новки |
определяется сумми |
|||||
|
|
|
|
|
|
|
рованием |
по |
правилу |
квад |
|||
Фиг. 41. Установка с базированием по |
ратного |
корня: |
|
|
|
||||||||
|
ey = v |
|
|
|
|
||||||||
цилиндрическому отверстию на |
жесткую |
|
^ |
F |
R |
(н > |
|||||||
оправку |
при |
свободной посадке и закрепле |
Для |
примера |
на фиг. 41 |
||||||||
нием оправки |
в самоцентрирующем |
патроне. |
|||||||||||
ванием отверстием на |
жесткую |
|
показана установка с базиро |
||||||||||
оправку при |
свободной посадке; |
||||||||||||
в этом случае имеем погрешность базирования |
eg, а при закреплении |
||||||||||||
оправки |
в |
самоцентрирующем |
патроне — погрешность |
закрепле |
|||||||||
ния |
е3. |
Погрешность |
установки в |
данном |
случае |
определяется |
|||||||
по |
формуле (11). |
|
|
|
|
|
|
|
|
|
|
||
|
Указанные на чертежах расчетные размеры, вытекающие из кон |
структивных связей, в ряде случаев не соответствуют геометрическим связям, вытекающим из принятого построения технологического процесса, и неудобны для выполнения промеров на обрабатываемых заготовках. По технологическим соображениям приходится иногда изменять принятые конструктором измерительные базы. В этих случаях, а также при перемене установочных баз в процессе обра ботки необходимо производить пересчет размеров на базе геометри ческого анализа связей между конструктивными размерами и при нятыми 'базами.
Рассмотрим в виде примера чертеж распределительного валика (фиг. 42). Для условий эксплуатации важно, чтобы при изготовлении валика были выдержаны размеры lv /2 и L; при этом размер L задан с жестким допуском. Непосредственное измерение размера L в произ водственных условиях осуществить не представляется возможным.
Установка заготовок для обработки на станках |
53 |
Непосредственные измерения можно производить либо по размеру х', либо по размеру х" Определяя один из этих размеров, технолог должен задать на него допуск, обеспечивающий соблюдение задан ного конструктором допуска по размеру L.
Исходя из этого условия, задачу можно решить следующим образом.
1. Если технолог решил вместо размера L задать размер х', то
|
^1 |
^max |
^min» |
- ---- х ----- |
|
||||||
г |
_ ^т. |
|
-U у' |
J__ -Ш |
1 lt |
|
f-2 |
— |
|||
^'maxт а х |
|
2о |
|
~ |
max |
' |
2 |
-[- |
|
||
|
|
|
|
||||||||
|
|
lm)n |
1 |
|
|
/о_ |
• |
|
|
- |
|
^min |
X . |
|
1 ^tmn |
|
|
|
|||||
|
|
~T |
H-----^— ’ |
|
|
|
|||||
|
? |
= |
bh |
, |
* |
1 |
bh |
|
|
|
|
|
° L |
~2~ + |
*»' + |
— |
----- L-------- |
|
|||||
или |
|
|
|
|
|
|
|
|
|||
|
|
|
|
|
|
|
|
// |
|
|
|
|
a |
_ |
* |
. |
8/I + B/2 |
|
|
|
|
||
|
|
— |
°x' |
H------ g---- ’ |
|
|
|
|
|||
откуда |
имеем |
|
|
|
|
2E |
S |
f r |
|
2.Если вместо размера L
задать размер х', то
|
Lmax = X, |
^mln |
^2min . |
|||
|
2 |
|
2 |
* |
||
|
/ . |
— y" |
'max |
/, |
_ |
|
|
rmn |
Лгшп |
_-rnax, |
|||
|
2 |
2 |
|
’ |
||
6L = |
+ |
— + |
~2 ~ — Ь*пH------ 2---- • |
откуда получаем
5/, + 8/2
Ьх»— 8L
т. e. тот же результат, что и в первом случае.
Таким образом, в общем виде, исходя из основного уравнения размерных цепей, имеем
т—!
» i - 2 », /=|
54 |
|
Точность в машиностроении |
|
||||
или |
|
|
|
от—2 |
|
|
|
|
|
|
|
|
|
|
|
|
|
*1 = * ,+ s |
|
|
|
||
откуда |
|
|
|
/= I |
|
|
|
|
|
|
от—2 |
|
|
|
|
|
|
|
|
|
|
|
|
|
|
&* = « |
* |
- 2 |
....... |
<12> |
|
|
|
|
|
/=| |
|
|
|
где 8Х— допуск |
на |
искомый |
размер; |
|
|
|
|
8L— допуск |
на |
заменяемый |
размер; |
цепи; |
|||
8г — допуски |
на |
размеры |
остальных |
звеньев |
|||
пг — общее количество всех |
звеньев |
размерной |
цепи, включая |
||||
искомый и заменяемый размеры. |
|
При обработке способом индивидуального получения заданных размеров заготовку устанавливают с выверкой относительно рабочих элементов станка, а рабочий инструмент устанавливают на размер индивидуально для каждой заготовки путем пробных проходов и промеров.
Следует при этом заметить, что в ряде случаев установка произ водится без выверки. В частности, при установке зацентрованной заготовки в центрах токарного станка выверка не производится, так как она не может изменить положения заготовки; исключается выверка каждой заготовки по высоте при установке ее обработан ной поверхностью на стол фрезерного станка. Выверка положения заготовки производится либо непосредственно по обрабатываемой поверхности, либо по разметочным рискам.
На фиг. 43 показана схема выверки по черной поверхности рейс масом. Выверка по разметочным рискам корпусной детали (фиг. 44) производится от стола станка рейсмасом, при помощи которого обрабатываемая поверхность устанавливается параллельно поверх ности стола. Иногда для этого пользуются линейкой и уровнем, при помощи которых обрабатываемой поверхности придают гори зонтальное положение; для выверки очень крупных деталей при меняют оптические методы.
Заготовки, обрабатываемые способом индивидуального получе ния заданных размеров, обычно подвергают предварительной раз метке, т. е. на заготовке прочерчивают линии, указывающие границы поверхностей, до которых должна быть произведена обработка. Для прочерчивания на заготовке этих линий требуется предвари тельно нанести на нее оси симметрии, главные центровые оси, а также ряд вспомогательных и контрольных рисок. Большое значение имеет при разметке выбор исходных поверхностей, от которых выдер живается положение наносимых при разметке рисок. Для этого
могут быть использованы в |
той или |
иной |
степени соображения |
о базировании заготовок при |
обработке |
их |
на станках.1 |
1 П р ак ти ч еск и е |
приемы |
р азм етки д олж н ы бы ть хорош о усвоены |
студентом |
в проц ессе учебной |
п р ак ти ки |
(в учебны х м астерских) по к у р су техн ологи и |
м еталлов, |
поэтом у зд есь вопросы о азм етки не р азви ваю тся . |
|
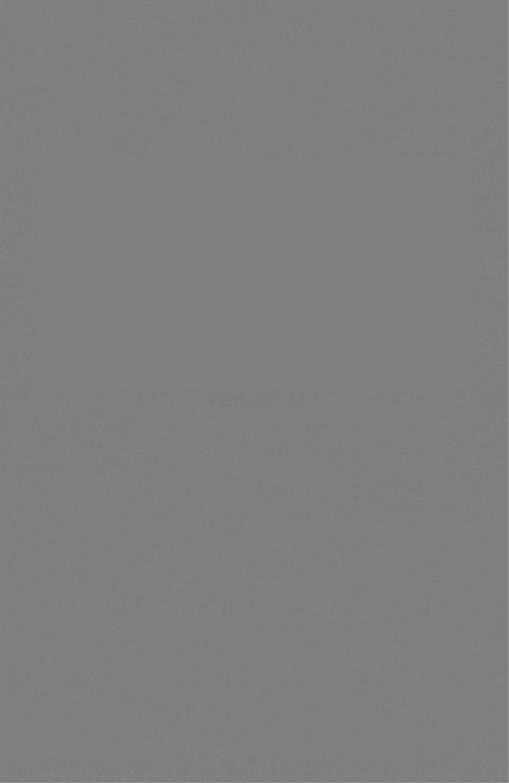
56 Точность в машиностроении
бующих выверки заготовок при их установке для обработки на стан ках.
Выверка заготовки по разметочным рискам производится обычно рейсмасом, игла которого при перемещении рейсмаса по столу станка или выверенной подкладке не должна отклоняться от раз меточной риски, проходя через середину ее керновых углублений (см. фиг. 44).
Выверка может быть также произведена по обработанным на пред шествующих операциях поверхностям; в этом случае рейсмас напра вляется либо по оставшимся после обработки половинам керновых углублений, либо его загнутой иглой непосредственно по обрабо
танной |
поверхности. |
Для |
повышения точности при выверке по обработанной поверх |
ности |
вместо рейсмаса применяют штангенрейсмас. |
Во всех случаях требующееся положение выверяемой заготовки достигается подкладками, простыми и сдвоенными клиньями или домкратиками и другими универсальными установочными приспо соблениями.
Выверку производят и после закрепления заготовки, так как под воздействием зажимных сил заготовка может изменять свое положение.
Выверка не может быть произведена с абсолютной точностью, поэтому приходится считаться с погрешностью выверки, влияющей на точность обработки при данной установке
Разметка и установка заготов(?к с выверкой являются операциями трудоемкими и требующими высокой квалификации исполнителей. Применение приспособлений при обработке способом автоматиче ского получения размеров на предварительно настроенных станках обеспечивает определенное положение заготовок без выверки, сокра щает во много раз время, затрачиваемое на установку, и не требует больших производственных навыков от исполнителей. В этом заклю чаются значительные преимущества установки заготовок в приспо соблениях. Однако применение специальных приспособлений эко номически оправдывается только при определенной, более или менее значительной производственной программе, а в условиях единичного производства вполне оправдывается с экономической точки зрения
разметка |
и |
установка заготовок |
с выверкой. |
|
|
|
|
||||
§ 3. РА С Ч Е Т |
Т Е Х Н О Л О Г И Ч Е С К И Х |
Д О П У С К О В |
П РИ |
О Б Р А Б О Т К Е |
СПОСОБОМ |
||||||
|
|
А В Т О М А Т И Ч Е С К О ГО П О Л У Ч Е Н И Я РА ЗМ Е РО В |
|
|
|||||||
П он яти е о |
ж есткости техн ологи ческой системы стан ок -заго то п ка-и н стр у м ен т. |
||||||||||
Р асчет ж есткости техн ологи ческой |
системы . Р асч ет |
п од атливости и |
отж ати й |
тех н о |
|||||||
логи ческой системы . О п ределение |
м акси м альн ого и |
м ин и м альн ого |
зн ач ен и я |
с о ста |
|||||||
вляю щ ей |
силы |
р езан и я |
по норм али |
к |
обрабаты ваем ой |
поверхности . |
К олебан ие |
||||
вы держ иваем ы х разм еров |
за го то во к |
к а к р е зу л ь т ат |
нестабильн ости силы р езан и я |
||||||||
и о тж ати й |
элем ентов техн ологи ческой |
системы . |
|
|
|
|
|
1 В еличины погреш ности у стан овки с вы веркой см. в п ри лож ен и и 2
|
|
|
|
Расчет технологических |
допусков |
|
|
|
57 |
|||||
|
К оп и рован и е и зак о н о м ер н о е ум ен ьш ен ие погреш ностей при о б р аб о тк е на м етал |
|||||||||||||
л о р еж у щ и х |
с та н к ах . |
П огреш н ости , |
остаю щ и еся |
постоянны м и |
в |
партии о б р а |
||||||||
ботан ны х |
за го то в о к . |
В л и я н и е гоом етрически х |
погреш ностей |
стан ка |
на |
точн ость |
||||||||
ф ормы о б работан н ой |
за го т о в к и . |
В л и я н и е |
погреш ности |
н астрой ки |
стан ка |
|||||||||
на |
вы держ и ваем ы й р а зм ер . П огреш н ости , |
зако н о м ер н о изм еняю щ ие |
свое |
зн ач ен и е |
||||||||||
в |
парти и |
|
обраб о тан н ы х |
за го то в о к . |
Р азм ер н ы й |
износ и н стр у м ен та . |
В л и я н и е |
|||||||
тем п ер ату р н ы х деф орм ац и й |
элем ен тов тех н о л о ги ч еско й системы на |
вы держ иваем ы й |
||||||||||||
разм ер . |
|
|
|
|
|
|
|
|
|
|
|
|
|
|
|
Р асч ет |
р езу л ьтати в н о й |
погреш ности |
о б р аб о тк и . |
|
|
|
|
||||||
|
С о о б р аж ен и я об |
о к р у гл е н и и |
расчетны х зн ач ен и й тех н о л о ги ч еск и х д о п у ск о в . |
|||||||||||
Д о п у ск и |
на |
разм еры |
черны х за го т о в о к . |
П ро стр ан ствен н ы е |
о тк л о н ен и я |
в заи м о |
||||||||
с вя зан н ы х |
элем ен тов |
за го т о в о к и |
д етал ей |
м аш ин . |
|
|
|
|
|
А. Расчеты жесткости, податливости и отжатий
технологической системы станок — заготовка — инструмент
При обработке на металлорежущих станках заготовок станок, установочное приспособление, обрабатываемая заготовка, режущий инструмент и несущие его элементы (державки, оправки, расточные скалки и т. п.) представляют собой упругую систему, которую для краткости будем называть упругой системой станок — заготовка — инструмент.
В процессе обработки сила резания изменяется под влиянием переменных условий обработки. В частности, к изменению силы резания приводят колебания размеров заготовок и, следовательно, неравномерность глубины резания; колебания механических свойств материала заготовок; притупление вследствие износа и изменение в связи с этим геометрических параметров режущего лезвия в про цессе обработки и другие технологические факторы.
Сила резания при обработке в условиях упругой системы станок— заготовка — инструмент вызывает упругие деформации, а также смещение элементов системы за счет зазоров в их сочленениях. Величина упругих деформаций и отжатий зависит как от силы резания, так и от жесткости упругой системы, т. е. ее способности противостоять действующей силе. Нестабильность силы резания вызывает неравномерность деформаций и отжатий элементов упру гой системы, в результате чего возникают погрешности формы обработанной поверхности и, следовательно, колебания ее размеров. Таким образом, точность обработки зависит от жесткости упругой системы станок — заготовка — инструмент.
Жесткость, как известно, определяется отношением действующей силы к величине деформации, вызываемой этой силой.
С точки зрения точности обработки наиболее существенное значение имеют колебания величины составляющей силы резания, направленной по нормали к обрабатываемой поверхности.
Под жесткостью упругой системы станок — заготовка — инстру мент понимают отношение этой составляющей силы резания к сме щению лезвия инструмента, установленного на размер в направле-
58 Точность в машиностроении
нии нормали к обрабатываемой поверхности. Таким образом, жест
кость системы (/) равна: |
' |
|
|
|
I = |
-у - кг/мм, |
(13) |
где Ру — составляющая |
силы резания, направленная |
по нормали |
|
к обрабатываемой |
поверхности, в кг\ |
|
|
Y — вызываемоё силой |
Ру отжатие элементов системы в мм. |
Жесткость может быть выражена также отношением приращения силы резания АРу к приращению отжатия AY:
дяу
! = ~К?~
Части станка не только деформируются, но одновременно изме няется их взаимное положение вследствие наличия зазоров и упру гости стыков, поэтому жесткость узлов не рассчитывается, а опре деляется экспериментально.
Как показали исследования, жесткость узлов станка изменяется при одновременном действии составляющих силы резания Ру и Рг сравнительно с жесткостью, измеренной под воздействием только радиальной составляющей силы резания Ру. В ряде случаев на жест кость узлов оказывает влияние также составляющая силы реза ния Рх. Поэтому более точные данные получаем при определении жесткости или податливости в процессе резания, когда на резуль таты измерения влияют все три составляющих силы резания.
Опыты проф. А. П. Соколовского [49] показали, что жесткость суппорта токарного станка при одновременном действии составляю щих силы резания Ру и Рг значительно выше, чем при действии только радиально составляющей силы резания Ру. Влияние соста вляющей силы резания Р2 на жесткость передней и задней бабок может быть иным. При нагружении бабок составляющая силы резания Р2 обычно уменьшает жесткость.
Отжатия узлов станков, кроме того, зависят от нагрузки; в част ности, отжатия системы зависят от передаваемого шпинделем кру тящего момента, производными которого являются прогиб шпин деля, смещение обрабатываемой заготовки на центре и перемещение центра в гнезде шпинделя вследствие одностороннего действия поводка.
Для определения жесткости узла станка производят ряд нагру жений, возрастающих от нуля до некоторой наибольшей величины, в зависимости от размеров станка; для каждой нагрузки измеряется отжатие испытуемого узла в. направлении нормали к обрабатываемой поверхности. Затем производят разгружение узла, фиксируя оста точные отжатия; при нагружении и разгружении строятся зависи мости
У-ПРуУ,

Расчет технологических допусков |
59 |
при этом нагрузочная и разгрузочная ветви характеристики жестко сти обычно не совпадают, т. е. в результате рассеивания энергии за один цикл нагружения и разгружения имеет место гистерезис (фиг. 45); на основе полученных данных определяется жесткость узла.
Жесткость станка определяется расчетом на основе эксперимен тально полученных величин жесткости его узлов. В частности, определение жесткости токарного станка при обработке вала в цен
трах производится |
на основе |
|
|
||||||
следующих соображений. |
|
|
|
||||||
Под воздействием состав |
|
|
|||||||
ляющей |
силы |
резания |
Ру, |
|
|
||||
приложенной в любой точке |
|
|
|||||||
пролета |
(фиг. 46), |
передняя |
|
|
|||||
бабка переместится |
из |
поло |
|
|
|||||
жения А в положение А' |
на |
|
|
||||||
величину отжатия Yn6, зад |
|
|
|||||||
няя бабка — из положения В |
|
|
|||||||
в положение В' |
на величину |
|
|
||||||
Y3 б, суппорт—из положе |
|
|
|||||||
ния С в положение С' на ве |
|
|
|||||||
личину |
Ycyn и ось вращения |
|
|
||||||
заготовки—из положения АВ |
|
|
|||||||
в положение А'В' |
|
В сечении |
|
|
|||||
х ось сместится на величину |
|
|
|||||||
Y %\ при |
этом |
|
|
|
|
|
|
|
|
Y x |
= Y n 6 + |
K |
|
|
|
|
|||
Упб = |
Ра . |
|
у |
|
Рв |
|
|
||
1пб |
|
Г |
эб = |
1зо |
|
|
|||
|
Ра = Рч I— X |
|
|
|
|
||||
|
|
Р — Р |
— |
|
|
|
|
||
|
|
г В — г у |
|
I » |
|
|
|
|
|
где РА и |
Рв — давления |
на переднюю |
и заднюю бабки, вызы |
||||||
Подставляя |
ваемые составляющей силы резания Рг |
||||||||
значения |
РА и Рв, получаем |
||||||||
|
|
|
|
|
|
Р и |
I — |
V/ |
Р иУ_ |
|
|
|
пб |
|
1пб |
I |
Y зб = |
1зб |
Значение К определяем из треугольника А'В'А":
К= _х_
Уэб -- Упб I
откуда
K = ( Y 36- Y a6) . *
60 |
Точность в машиностроении |
следовательно,
Yx = Y a6 + ( Y « - Y a6) . J L .
После соответствующих подстановок и преобразований получаем
Ф иг. 46. К расч ету о тж ати й у п ругой системы стан ок — за го то в к а .
Обозначив через Y cmсуммарное отжатие узлов станка при любом положении резца вдоль оси заготовки, имеем по фиг. 46
|
|
|
Y |
= Y |
4- Y |
|
|
|
|
||
где |
|
|
|
|
|
|
|
|
|
|
|
|
|
|
V |
|
— |
Л |
' |
|
|
|
|
|
|
|
1 суп |
|
. |
|
|
|
|
|
|
|
|
|
|
|
|
fct/n |
|
|
|
|
|
Подставляя значения |
Yсуп и Yx, получим |
|
|
|
|||||||
v |
_ |
гу |
|
|
|
|
|
|
|
|
|
1 cm |
|
Icyn |
|
1пб |
|
|
|
|
|
|
|
|
|
|
|
|
|
|
|
|
|||
ИЛИ |
|
|
|
|
|
|
|
|
|
|
|
Уш = |
Ру [•— |
+ |
Ino |
+ |
1 |
4 |
- |
• ( - у |
(14) |
||
|
|
L Icyn |
\ |
/ |
/эб |
\ |
1 |
|
|||
Жесткость станка |
jcm при этом определяется |
следующим |
выра |
||||||||
жением: |
|
|
|
|
|
|
|
|
|
|
|
1cm— |
У — |
|
|
|
|
|
1 |
|
|
(15) |
|
-Л- + — |
|
l — x y |
1 |
/ х V |
|||||||
|
|
|
|
|
|||||||
|
|
|
|
I |
/ |
Уаб |
' W |
|
|||
|
|
|
Icyn |
|
!пб |
|
|
Применение формулы (15) для расчета жесткости станка сопря жено с неудобствами вследствие сложности вычислений. Подтвердим это примером. Допустим, что jCyn = 2780 кг/мм, jn6 = 3850 кг/мм