
книги / Основы технологии машиностроения
..pdf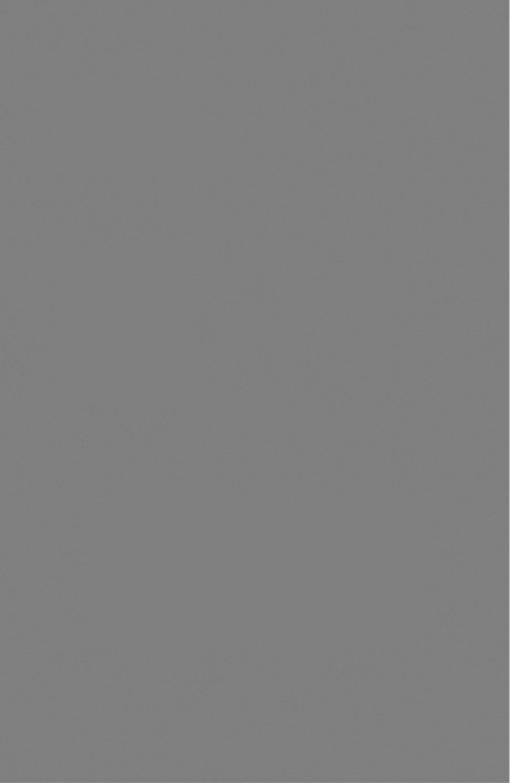
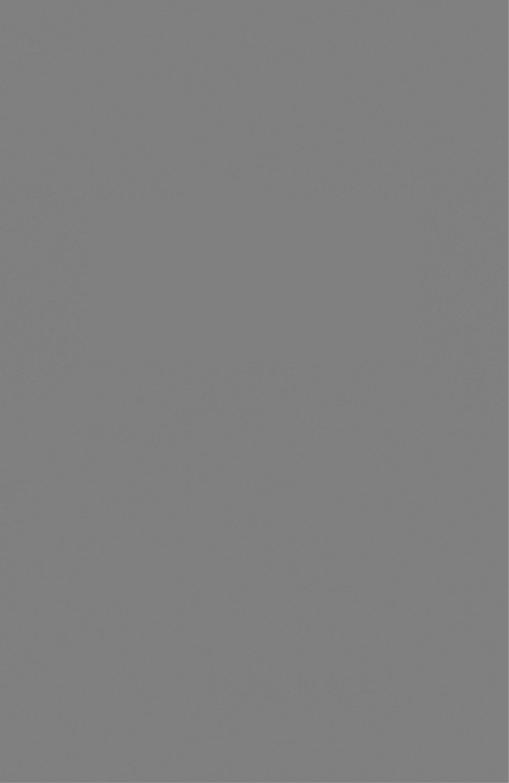
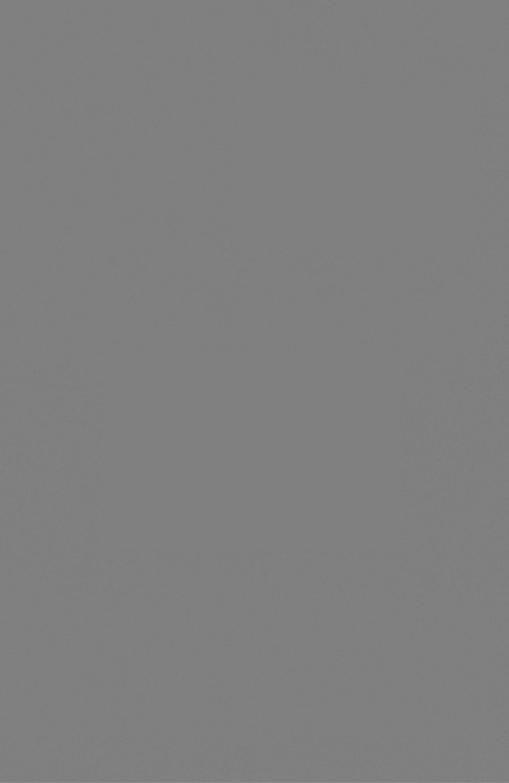
144 |
Точность в машиностроении |
бор е, позволяю щ ем |
наблюдать и фотографировать участки контакта плоскости |
кварцевой призмы с исследуемой поверхностью . Накладывая прибор на образец чистоты поверхности, а затем на контролируемую деталь, мож но производить оценку
чистоты обработанной поверхности |
методом сравнения. |
|
|
М е т о д |
и с с л е д о в а н и я |
е с т е с т в е н н ы х |
п р о ф и л о г р а м м |
применяется |
исключительно для научны х исследований, |
так как в этом случае |
для получения профилограммы исследуем ая деталь или образец подвергается р аз руш ению .
Д л я |
получения |
естественной |
профилограммы |
поверхность |
детали |
(образца) |
||||||||||||||
разрезаю т |
в интересующ ем |
исследователя направлении; |
поверхность разреза |
поли |
||||||||||||||||
|
|
|
|
|
|
рую т |
обычным способом |
для получения |
ми |
|||||||||||
|
|
|
|
|
|
крошлифа. |
Чтобы |
|
избеж ать |
завалов |
и |
по |
||||||||
|
|
|
|
|
|
вреж дений при разрезании, |
|
исследуемую по |
||||||||||||
|
|
|
|
|
|
верхность покрывают слоем хрома или меди. |
||||||||||||||
|
|
|
|
|
|
Полученный |
профиль |
поверхности |
увеличи |
|||||||||||
|
|
|
|
|
|
вают |
при |
помощи |
проектора |
либо |
фотогра |
|||||||||
|
|
|
|
|
|
фируют при больш ом |
увеличении или |
иссле |
||||||||||||
|
|
|
|
|
|
дую т на металломикроскопе. |
|
|
|
|
|
|||||||||
|
|
|
|
|
|
При |
прямом |
разрезе |
(перпендикулярно |
|||||||||||
|
|
|
|
|
|
исследуемой |
|
поверхности) |
|
профилограмма |
||||||||||
|
|
|
|
|
|
получается |
в одинаковом |
масштабе |
по |
осям |
||||||||||
|
|
|
|
|
|
абсцисс и ординат. |
|
При больш ом увеличении |
||||||||||||
|
|
|
|
|
|
профилограммы, она чрезмерно растягивается |
||||||||||||||
|
|
|
|
|
|
в длину и неудобна для |
изучения. |
Д л я |
по |
|||||||||||
Фиг. 85. |
Схема |
получения |
косого |
лучения |
естественных профилограмм целесо |
|||||||||||||||
образно |
применять |
метод |
|
косых |
ср езо в Г |
|||||||||||||||
|
среза. |
|
|
|
|
|||||||||||||||
|
|
|
|
У становка образца для получения |
косого |
|||||||||||||||
|
|
|
|
|
|
|||||||||||||||
части образца АВС образовавш иеся |
среза |
показана на |
фиг. |
85. П осле |
удаления |
|||||||||||||||
грани |
АС притирают |
пастой |
ГОИ |
с керосином |
||||||||||||||||
и протравливают. Ребро С ф отографируют при увеличении |
в 30 |
раз |
и |
получают |
||||||||||||||||
таким путем естественную |
профилограмму |
с различным |
увеличением |
по вертикали |
||||||||||||||||
и горизонтали. У гол |
а выбирают примерно от 0,5 до |
2°, |
что |
создает |
дополнитель |
|||||||||||||||
ное увеличение |
профиля |
по вертикали в 30 — 120 |
раз, так |
как |
масштаб |
|
|
|
М = |
1 |
tg« |
|
Таким образом , общ ее увеличение |
профиля по вертикали мож но получить |
в 900 — 3600, а по горизонтали в 30 раз (за счет увеличения при фотографировании).
1 М етод косых срезов предлож ен д-ром техн . наук проф. П . Е . Д ьяченко в 1939 г.
|
Качество поверхностей заготовок и деталей машин |
145 |
Д л я |
получения подобной профилограммы без разруш ения детали |
применяют |
м е т о д |
с л е п к о в . Этот метод заключается в том, что с исследуемой поверх |
ности снимается слепок, который в дальнейш ем подвергается профилографированию тем или иным способом . П омимо лабораторны х исследований, метод слепцов может быть с успехом применен для профилографирований очень крупны х деталей в сл у чаях, когда по тем или иным причинам не представляется возможным определить чистоту поверхности приборами непосредственно на детали, а такж е для определения
микропрофиля з |
труднодоступны х местах детали (например, |
отверстия». |
||||
М атериалом |
для |
получения слепков служ ит |
целлулоид. К усочек целлулоида |
|||
размером 10 X 40 X 2 мм опускаю т на 2 мин. |
в |
химически |
чистый ацетон, а затем |
|||
прикладывают к |
исследуемой поверхности, налож ив кусочек |
бумаги черного цвета |
||||
и придавив пальцем (черная бумага облегчает |
условия ф отограф ирования). П ол у |
|||||
ченный слепок |
после |
просуш ивания мож но |
фотографировать |
при определенном |
увеличении или оценивать высоту микронеровностей одним из рассмотренных выше методов; м огут быть применены профили графы, но с малым давлением иглы, во избе ж ание образования царапин на слепке. Н еобходим о иметь в виду, что слепок предстарляет собой обратный профиль поверхности, т. е. выступы профилограммы соот ветствуют впадинам поверхности, и наоборот.
Для характеристики качества поверхностей существенное зна
чение имеет состояние |
п о в е р х н о с т н о г о |
с л о я заготовок |
|
и деталей машины. |
п о в е р х н о с т н ы х |
с л о е в поль |
|
При |
исследованиях |
||
зуются |
следующими методами. |
|
Для определения глубины и общей характеристики поверхно стного слоя черных заготовок и при грубых методах механической обработки можно пользоваться обычным методом исследования мик рошлифов. На фиг. 86 показан микрошлиф поверхностного слоя стальной отливки, полученной по выплавляемой модели. Поверх ностный слой обезуглерожен почти до чистого феррита на глубину 0,15 мм. На этом же шлифе видны поверхностные микронеровности порядка 20—25 мк. На фиг. 87 показан микрошлиф поверхностного слоя стальной горячештампованном зэготоеки; на нем достаточно отчетливо виден обезуглероженный слой глубиной до 200 JW/си поверх ностные неровности высотой до 80 мк. На фиг. 88 показан микро шлиф поверхностного слоя холоднотянутой калиброванной стали, на котором виден частично обезуглероженный слой глубиной до 70 мк и поверхностные микронеровности порядка 40—50 мк.
На фиг. 89 показан микрошлиф поверхностного слоя горяче штампованной заготовки из стали марки 20X3. Поверхностный слой значительно обезуглерожен — на глубину до 225.м/с. Для отчет ливого представления о характере обезуглероженности на фиг. 90 дан микрошлиф сердцевины этой заготовки.
При исследовании микрошлифов можно наблюдать и поверх
ностные слои, деформированные после обработки снятием стружки. На фиг. 91 показан микрошиф поверхностного слоя той же заго
товки |
из стали маоки 20X3 после |
обтачивания; поверхностный |
слой |
значительно деформирован и |
имеет завихренное строение |
структурных составляющих; глубина деформированного слоя дости гает 80—90 мк. Другой пример приведен на фиг. 92, на которой показан микрошлиф поверхностного слоя заготовки из стали марки
Ю К о в а н S72
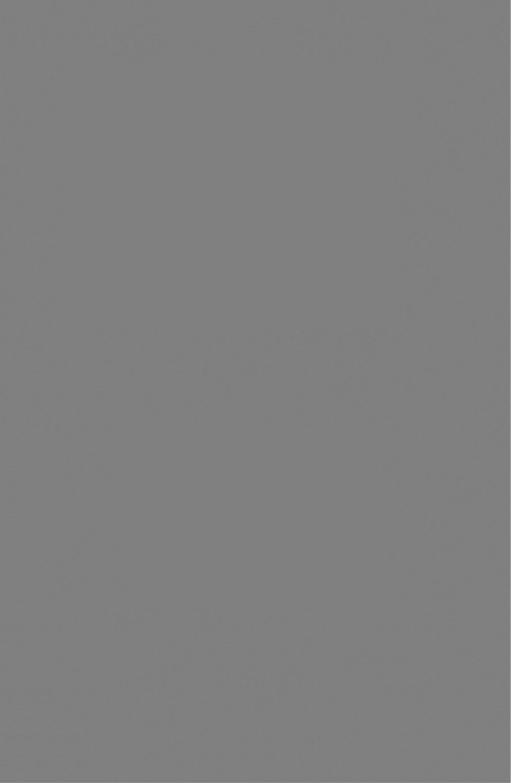
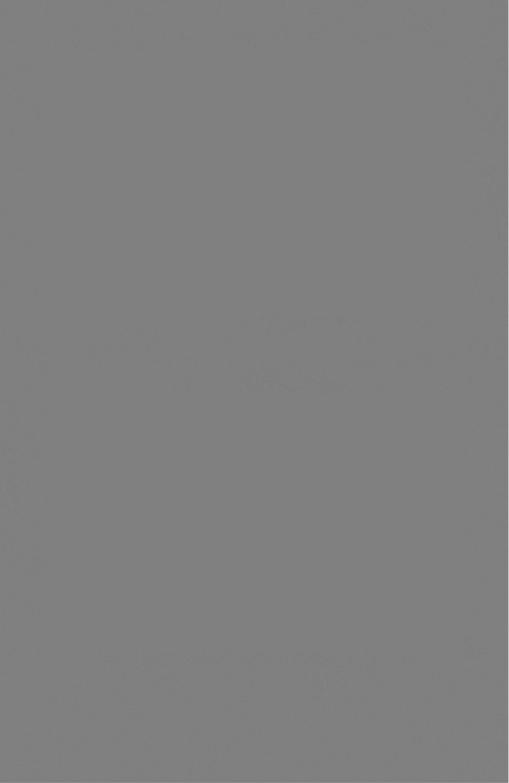
148 |
|
Точность в машиностроении |
|
45 после обтачивания; |
поверхностный слой значительно деформиро |
||
ван, на глубину до 100 мк. |
прямой |
||
При |
исследовании |
микрошлифов можно применять |
|
}и косой |
срез. Микрошлиф косого среза делается по схеме, |
приве |
денной на фиг. 85. Применением косого среза получают, как изве стно, картину поверхностного слоя в увеличенном масштабе, по этому прямой срез (перпендикулярно поверхности) применяют преи мущественно при большой глубине наклепанного слоя.
Для исследования поверхностного слоя применяют также при боры для испытания металлов на микротвердость методом вдавли
вания алмазной |
пирамиды. |
Находят применение приборы |
проф. |
|
М. М. Хрущова |
и Е. С. Берковича ПМТ-2 и |
ПМТ-3. В этих |
при |
|
борах применяется давление |
на пирамиду от |
1 до 500 г. Для |
стали |
|
рекомендуется применять давление 100 г |
|
|
Пользуясь этими приборами, можно определять глубину и сте пень наклепа путем измерения микротвердости на срезах. При изго товлении микрошлифов прямых и косых срезов нельзя покрывать исследуемую поверхность хромом, так как хром диффундирует в верхний слой металла, повышает его твердость и искажает дей ствительную микротвердость. При косом срезе нельзя сошлифовывать удаляемую часть образца, так как высокая температура, воз никающая при шлифовании, изменяет свойства металла. Эта опера ция производится полированием в специальном приспособлении, обеспечивающем срез под заданным углом. Полирование производят пастой ГОИ, сначала грубой, а затем средней и тонкой, последо вательно на трех притирочных плитах: чугунной и двух стеклянных. Путем измерения микротвердости на скошенной части образца от поверхности до исходного металла определяют глубину и степень наклепа; при этом наклеп кончается там, где показания микротвер дости получаются одинаковыми.
Для исследования поверхностного слоя применяют также р е н т г е н о с т р у к т у р н ы й а н а л и з . В этом случае для опреде ления внутренних напряжений в поверхностном слое металла страв ливают с поверхности образца слои толщиной 5—10 мк и после каж
.дого стравливания снимают рентгенограмму.
Этот метод требует сложной аппаратуры и большой затраты времени, так как на снятие и обработку каждой рентгенограммы требуется около 10 часов
Изменения в слоях металла толщиной менее 3—10 мк не улавли ваются рентгеноанализом. В этих случаях исследование поверх ностного слоя может быть произведено методом с т р у к т у р н о й э л е к т р о н о г р а ф и и , основанном на диффракнии электро нов *, позволяющей исследовать строение тончайшего поверхностного слоя различных материалов.
1 Диффракция электронов — явление рассеяния потока электронов атомами, молекулами, аморфными'или кристаллическими телами с образованием при некото рых условиях нескольких резко отграниченных пучков.
Качество поверхностей заготовок и деталей машин |
149 |
На фиг. 93 показаны поверхностные слои, исследованные мето^ дом структурной электронографии после обработки топким шлифо ванием, притиркой и отделочным шлифованием. Поверхностные слои, как показало исследование, состоят из трех зон [54].
Первая зона, толщиной от 2 до 3 А*, состоит из адсорбированной сгущенной пленки газа, которую можно удалить лишь нагревом поверхности в вакууме. Однако при соприкосновении поверхности с воздухом эта пленка незамед лительно образуется снова.
Вторая зона получается раз личной в зависимости от ме тода обработки. После тонкого
шлифования она достигает 80 А и состоит из сравнительно слабо соединенных между собой ча стиц окислов нитридов, и ме талла, обезуглероженного дей ствием высоких температур, раз вивающихся при шлифовании. После притирки вторая зона
достигает примерно 30 А |
и со |
|
|
|
|
|
|
|
||||
стоит из частиц абразива, окис |
|
|
|
|
|
|
|
|||||
лов |
и пыли, |
а |
после отделоч |
Фиг. |
93. |
Структурное |
состояние поверх |
|||||
ного |
шлифования — 15А и |
со |
ностных |
слоев |
стали |
после обработки: |
||||||
стоит из частиц окислов и пыли. |
а — тонким шлифованием, 6 |
- притиркой |
||||||||||
Третья зона |
после тонкого |
|
и в — отделочным |
шлифованием |
|
|||||||
шлифования |
распространяется |
|
|
|
|
|
|
|
||||
на глубину примерно 50 000 А и состоит |
из зерен металла, дефор |
|||||||||||
мированных |
давлением |
шлифовального |
круга, и из карбидов, |
вы |
||||||||
делившихся под действием высоких температур. |
Карбиды, |
рас |
||||||||||
полагающиеся по границам |
зерен, |
делают |
этот |
слой |
хрупким. |
|||||||
После притирки |
и отделочного шлифования третья |
зона |
достигает |
15 000 А и состоит из деформированных зерен металла. Далее третья зона постепенно переходит, образуя переходную зону влияния деформации, в нетронутый обработкой кристаллический металл.
Для исследования поверхностного слоя металла применяются также в лабораторных условиях метод стравливания слоев с опре делением микротвердости после каждого стравливания и метод опре
деления наклепанного слоя по скорости стравливания |
металла и др. |
||
Основание |
поверхностного слоя |
обработанных |
поверхностей |
у заготовок и |
деталей, как показали |
исследования, |
располагается |
* А — ангстрем (метрическая мера длины); 1 ангстрем равен одной десятимил лионной миллиметра
150 Точность в машиностроении
адэкватно макрогеометрическим погрешностям формы поверхности, ее волнистости и микронеровностям.
Качество поверхностей заготовок, как черных, так и в процессе их механической обработки, имеет технологическое значение; оно оказывает влияние на величину припусков на обработку, на режимы резания при обработке заготовок, на погрешность установки заго товки для обработки. Это влияние частично рассмотрено при опре делении погрешности установки и будет развито в дальнейшем изло жении. Здесь ограничимся общей характеристикой качества поверх ностей заготовок, в первую очередь черных, а затем обработанных различными методами.
На поверхности проката остаются следы погрешностей поверх ности прокатных валков, по мере износа которых поверхность про ката ухудшается; по исследованиям автора высота поверхностных микронеровностей проката обычно не превышает 150 мк. Поверх ностный слой проката обезуглерожен на глубину до 150 мк.
Ухолоднотянутой стали поверхностные микронеровности умень шаются до 40—50 мк; обезуглероженный слой растягивается при волочении, и в силу этого его глубина обычно не превышает 50 мк.
Упоковок высота поверхностных неровностей зависит от мето
дов ковки. Наиболее грубая поверхность, со значительными неров ностями, порядка 1,5—4 мм, получается при свободной ковке. На поверхностях горячештапованных поковок остаются следы ока лины и воспроизводятся поверхностные погрешности штампов; при этом высота поверхностных микронеровностей в зависимости от веса поковок и состояния штампов находятся в пределах 150—500 мк. Поверхностный слой поковок состоит из зоны обезуглероживания и переходной зоны, в которой наблюдается частичное обезуглеро живание. У горячештампованных заготовок глубина обезуглероженного слоя в зависимости от веса поковок находится в пределах 150—300 мк; при свободной ковке, также в зависимости от веса
поковки, может |
получиться более глубокий обезуглероженный |
слой — порядка |
500—1000 мк. |
Поверхности отливок копируют в той или иной степени поверх ности литейных форм. Наиболее грубая поверхность получается у отливок, залитых в земляную форму ручной формовки. Поверх ностные неровности достигают в этом случае для мелких отливок 500 мк, а для крупных отливок 1500 мк и зависят от величины зерен формовочной смеси, плотности набивки формы, тщательности ее отделки и других факторов. При литье в земляные формы машин ной формовки высота поверхностных неровностей достигает вели чины порядка 300 мк, при кокильном и центробежном литье 200 мк, при литье под давлением 5—10 мк.
Специфика технологических условий изготовления форм для литья по выплавляемой модели обусловливает высоту поверхностных микронеровностей для отливок, получаемых этим методом, в преде лах 8—40 мк.