
книги / Резание материалов
..pdfподобранные среды повышают стойкость этих инструментов в 5…10 раз. Не менее важное значение имеют СОТС для работы автоматических линий, где важно обеспечить высокую размерную стойкость инструмента.
Охлаждающие свойства СОТС способствуют увеличению оптимальной скорости резания на 25…30 %, за счет чего на 20…40 % увеличивается производительность обработки, при этом стойкость режущего инструмента не уменьшается.
СОТС уменьшает усадку стружки и ослабляет ее зависимость от подачи и переднего угла. Уменьшая усадку стружки, среда способствует тем самым уменьшению пластической деформации
иснижению усилий резания на 20…30 %. В результате уменьшения усилий резания снижаются деформации отдельных частей станка, инструмента и детали, повышается точность обработки
иуменьшается износ оборудования. Наконец, воздействуя на усилия резания, СОТС влияют тем самым на мощность, потребляемую станком. Можно считать, что СОТС снижают расход энергии, подводимой к станку, на 5…20 %, а это имеет большое практическое значение, поскольку парк станочного оборудования современных машиностроительных заводов огромен.
При механообработке, особенно в условиях развития гибких автоматизированных производств и безлюдной технологии, все более остро встает вопрос формирования стружки, удобной для отвода из зоны резания. Ученые, исследовавшие эту проблему, утверждают, что, облегчая пластическую деформацию обрабатываемого материала, СОТСспособствуют образованию сливной стружки.
Имеющаяся взаимосвязь между явлениями трения, износа
ихарактеристиками качества поверхности, формируемой при резании, позволяет сделать вывод, что применение СОТС, различных по составу и свойствам, оказывает существенное влияние на характеристики качества обработанной поверхности и, в первую очередь, на высоту микронеровностей, уменьшая их на 20…40 %, а также на параметры, характеризующие физическое состояние обработанного поверхностного слоя. Это проявляется в том, что при работе с СОТС уменьшаются глубина, степень упрочнения
имикротвердость поверхностного слоя на 30…40 %.
221
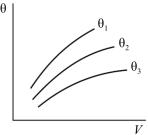
Обобщая вышеизложенное, можно сделать вывод, что СОТС являются одним из резервов машиностроительных предприятий в деле повышения производительности труда, улучшения качества обрабатываемых деталей, повышения долговечности оборудования, экономииинструментальных материаловиэлектрическойэнергии.
3.2.5. Методы подачи СОЖ
Основным методом подачи СОЖ является полив сверху. К другим методам относятся: подача под давлением; подача через тело инструмента; метод масляного тумана; подача со стороны
|
задней поверхности инструмента. |
|||||
|
Все эти методы имеют свои |
|||||
|
преимущества и недостатки. На |
|||||
|
рис. 132 видно, что эффективность |
|||||
|
охлаждения |
существенно |
зависит |
|||
|
от способа подачи СОТС. |
|
||||
|
Рассмотрим |
некоторые |
совре- |
|||
|
менные методы |
и |
эффективность |
|||
Рис. 132. Влияние СОТС на |
подачи СОТС при обработке реза- |
|||||
нием. |
|
|
|
|
||
температуру резания: Т1 – без |
Полив |
сверху, |
свободно па- |
|||
СОТС; Т2 – охлаждение |
||||||
дающей струей – наиболее простой |
||||||
туманом; Т3 – охлаждение |
||||||
поливом |
и дешевый |
способ |
подачи СОЖ |
(рис. 133), однако КПД мал, расход эмульсии 12…15 л/мин, масла 3…4 л/мин. Плохой отвод тепла из-за механических препятствий и паровой рубашки. Охлаждается стружка и деталь, а инструмент практически не охлаждается. Струя должна быть непрерывной и направленной в точку отрыва стружки от передней поверхности резца для лучшего отвода тепла.
Подача СОЖ под небольшим давлением (0,5…3 атм). Подача возможна сверху, снизу. Стойкость резцов выше в 1,5…2 раза, сбивается паровая рубашка, через тело резца – сверла, фрезы, резцы. Скорость резания можно увеличить на 25…40 %. Диаметр отверстия 2 мм.
222
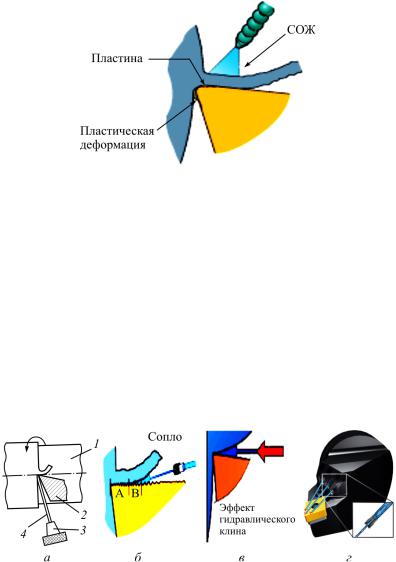
Рис. 133. Подача СОТС поливом сверху
Подача СОЖ под большим давлением (15…20 атм) со сто-
роны передней или задней поверхности снизу, а также через тело режущего инструмента (рис. 134). Для уменьшения рассеивания СОЖ нужно уменьшить расстояние до режущей кромки. В результате образуется гидравлический клин, обеспечивающий попадание СОТС глубоко под стружку и даже деформирующую стружку. Диаметр отверстия 0,5…0,7 мм. Стойкость повышается в 4…5 раз. Небольшой расход 0,5…1 л/мин, хорошее охлаждение, нет паровой рубашки. Однако при этом увеличивается шум, брызги, необходимы фильтры, спецнасосы, велики потери СОЖ.
Рис. 134. Подача СОТС под высоким давлением со стороны задней поверхности (а), со стороны передней поверхности (б), эффект гидроклина (в) и через тело резца (г) (1 – заготовка; 2 – резец; 3 – сопло; 4 – струя СОЖ)
223
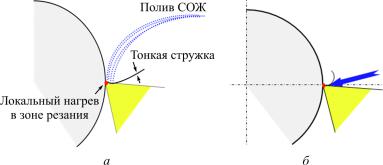
Сверхвысокое давление подачи СОТС. С целью повышения эффективности процесса резания сегодня разработаны системы подачи СОТС со сверхвысоким давлением. Принято считать, что низкое давление (наиболее распространено сегодня) до 20 бар, высокое давление 20–70 бар, а сверхвысокое давление 70–600 бар.
На рис. 135 приведены сравнительные схемы подачи СОТС по двум вариантам при точении титанового сплава типа ВТ6 и дана оценка эффективности нового метода подачи СОТС.
Рис. 135. Сравнительный анализ схемы подачи поливом (а)
ипод высоким давлением (б)
1.Полив сверху. Локальный нагрев в зоне резания. Низкая теплопроводность. Низкий модуль упругости. Скорость 40…60 м/мин. Стойкость ≈20 мин. Износ по передней поверхности. Длинная витая стружка.
2.Направленная подача СОЖ под высоким давлением. Дав-
ление деформирует и ломает стружку на мелкие, удобные для утилизации части. Струя направлена непосредственно в зону нагрева. Меньше нагрев пластины и ниже температура в зоне резания. Возможность увеличения скорости и стойкости. Скорость 90…150 м/мин (в 2 раза больше). Стойкость выше на 100 %. Элементная стружка.
Для реализации метода высоконапорной подачи СОТС необходимо провести модернизацию оборудования как нового, так
истарого (установка сверхвысокого давления увеличивает стоимость ≈20 %).
224
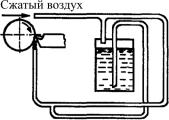
Модернизация станка включает в себя: герметизацию рабочей зоны станка, дополнительную вентиляцию, фильтрацию СОЖ, увеличенный расход СОЖ (+10 %).
Масляный |
туман – СОЖ |
|
|||
и воздух создают барботаж. В зо- |
|
||||
ну резания подается 1 л смеси на |
|
||||
8 м3 воздуха (рис. 136). Стойкость |
|
||||
инструмента |
увеличивается |
в |
|
||
6…7 раз. Осаждается на горячие |
|
||||
поверхности и испаряется. При- |
|
||||
меняется в автоматических лини- |
Рис. 136. Подача СОТС |
||||
ях. Самый большой эффект охла- |
|||||
в распыленном состоянии |
|||||
ждения, так как |
температура |
на |
|||
выходе из сопла |
снижается |
до |
под действием сжатого |
||
воздуха |
|||||
4…12 ºС, легко проникает в мик- |
|||||
|
ротрещины.
Расход СОТС незначительный – эмульсии на водной основе 200…400 г/ч, а масляной жидкости 1…5 г/ч.
Подача охлажденных или ионизированных газов (азот, угле-
кислота, сжатый воздух через трубчатое сопло) снижает температуру за счет испарения газов. Более экологична, применяется для скоростного резания. Стойкость повышается в 1,5…2 раза.
3.2.6. Рекомендации по применению СОТС
Правильный выбор СОТС может повысить период стойкости инструмента в 1,5…3 раза, снизить высоту микронеровностей до
1,5 раза (табл. 8).
Преобладающим видом изнашивания инструментов при обработке сталей и сплавов IV и V групп является адгезионно-уста- лостное (табл. 9). В этом случае необходимо применять СОТС с повышенной смазывающей способностью. При обработке сплавов VI группы преобладает абразивное изнашивание и, как следствие, часто применяются более дешевые и гигиенические водные СОТС.
225
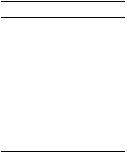
|
|
Таблица 8 |
|
Рекомендации по выбору СОТС при обработке |
|||
|
сталей II и III групп |
|
|
|
|
|
|
Тип оборудования |
Временное сопротивление сталей |
||
1000 МПа |
>1000 МПа |
||
|
|||
Токарные, расточные, |
Аквол-2, |
Аквол-11, |
|
фрезерные, сверлильные, |
Аквол-6 (8…12 %), МР-3, |
Укринол-1 (3…5 %) |
|
многооперационные |
МР-1у, МР-7 (100 %) |
|
|
станки; автоматические |
|
|
|
линии |
|
|
|
Токарные автоматы |
МР-1у, ОСМ-5 (100 %) |
|
|
Протяжные и зубообра- |
МР-3, МР-1у, |
|
|
батывающие станки |
ОСМ-5 (100 %) |
|
|
Резьбонарезные станки |
МР-6, ЛЗ-СОЖ (100 %) |
|
Таблица 9
Рекомендации по выбору СОТС при обработке сталей и сплавов IV–VI групп
Тип оборудования |
Группа материалов |
|
стали IV |
сплавы |
|
|
и сплавы V групп |
VI группы |
Токарные, расточные, |
Аквол-6, |
Аквол-11, Укринол-1, |
фрезерные, многоопе- |
Аквол-2 (8…12 %), |
Аквол-2, Аквол-6 |
рационные станки |
МР-1у, |
(3…5 %), МР-1у, |
|
МР-7 (100 %) |
МР-3 (100 %) |
Сверлильные станки |
Аквол-6, |
Аквол-11, Укринол-1, |
|
Аквол-2 (10…20 %), |
Аквол-2, Аквол-6 |
|
МР-1у, МР-7 (100 %) |
(3…5 %) |
Протяжные станки |
МР-1у, МР-3, ОСМ-5, |
МР-1у, МР-7, ОСМ-5 |
и токарные автоматы |
МР-6, МР-7 (100 %) |
(100 %), Аквол-6, |
|
|
Аквол-2 (5…100 %) |
Резьбонарезные |
МР-6, МР-99 (100 %) |
МР-7, МР-1у (100 %), |
станки |
|
Аквол-2, Аквол-6 |
|
|
(5…100 %) |
Характерной особенностью использования СОТС при обработке титановых сплавов является малая эффективность присадок, содержащих серу, азот, фосфор, поскольку эти элементы хорошо растворимы в титане. Гораздо более эффективны в качестве присадок галогены, и в первую очередь йод.
226
Контрольные вопросы и задания
1.Перечислите источники возникновения теплоты при точении. Что такое тепловой баланс?
2.Раскройте понятия температурного поля и температуры резания.
3.Перечислите основные методы измерения температуры
взоне резания.
4.Как температура резания зависит от условий обработки?
5.Сформулируйте второй закон резания.
6.Напишите эмпирическую формулу для подсчета температуры резания.
7.Каково назначение СОТС? Каковы требования к СОТС?
8.Приведите общую классификацию СОТС.
9.Каковы наиболее эффективные методы подачи СОТС?
10.Почему новая свежеприготовленная эмульсия на водной основе имеет белый цвет, а синтетическая СОТС – прозрачная?
227
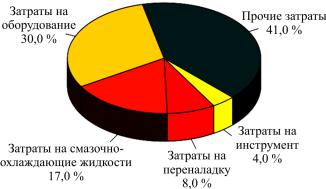
Глава 4 ИЗНОС И СТОЙКОСТЬ РЕЖУЩЕГО ИНСТРУМЕНТА
4.1. Краткие сведения об инструментальных материалах
Режущий инструмент является важной частью оснастки при проведении процесса резания. В то же время затраты на режущий инструмент в общем объеме затрат на резание относительно невелики и составляют 3…4 % (рис. 137). Однако режущий инструмент – это постоянно расходуемый материал, и отсутствие хотя бы одного инструмента приводит к остановке производства изделий, срыву программ и планов предприятий. Общие суммы затрат на режущий инструмент на многих крупных предприятиях России составляют до 1…3 млн руб. в год.
Рис. 137. Распределение затрат на основные элементы процесса резания и режущий инструмент
Затраты на режущий инструмент с каждым годом нарастают не только в связи с расширением производства, но и с разработкой и появлением новых более эффективных изделий машиностроения с применением более труднообрабатываемых материалов. В результате стойкость режущих инструментов существенно снижает-
228
ся, а расход и затраты на инструмент увеличиваются. Сегодня данную проблему решают путем разработки новых инструментальных материалов, применения различных износостойких и упрочняющих покрытий на различных режущих инструментах.
В связи с этим знание классификации, свойств и области применения новых материалов режущих инструментов позволяет быстро и эффективно решать проблемы технологической подготовки производства по повышению производительности и качества, снижению себестоимости обработки современных изделий машиностроения.
4.1.1.Требования, предъявляемые
кинструментальным материалам
Высокие эксплуатационные характеристики режущих инструментов в значительной степени зависят от качества материала, из которого эти инструменты изготовлены. Материалы, предназначенные для режущих инструментов, должны по ряду показателей значительно превосходить материалы, применяемые в машиностроении для изготовления различных деталей.
Основные требования к инструментальным материалам следующие:
1.Инструментальный материал должен иметь высокую твердость – в состоянии поставки или достигаемую в результате его термической обработки – не менее 63...66 HRC по Роквеллу (шкала С). Необходимо, чтобы при значительных температурах резания твердость поверхностей инструментов существенно не уменьшалась.
2.Высокая теплостойкость инструментального материала. Под теплостойкостью (красностойкостью) материала понимается его способность сохранять свои физико-механические свойства,
вчастности твердость, при высокой температуре.
3.Высокая теплопроводность инструментального материала. Чем ниже теплопроводность, тем меньше теплоотдача и выше температура инструмента в процессе резания. Теплопроводность
229
повышается с увеличением содержания в инструментальном материале компонентов с максимальной теплопроводностью.
4.Наряду с теплостойкостью инструментальный материал должен иметь высокую износостойкость при повышенной температуре, т.е. обладать хорошей сопротивляемостью истиранию обрабатываемым материалом.
5.Важным требованием является достаточно высокая прочность инструментального материала. Если высокая твердость материала рабочей части инструмента сопровождается значительной хрупкостью, это приводит к поломке инструмента и выкрашиванию режущих кромок.
6.Инструментальный материал должен обладать технологическими свойствами, обеспечивающими оптимальные условия изготовления из него инструментов. Для инструментальных ста-
лей это хорошая обрабатываемость резанием и давлением; бла-
гоприятные особенности термической обработки (малая чувствительность к перегреву и обезуглероживанию, хорошие закали-
ваемость и прокаливаемость, минимальные деформирование и образование трещин при закалке и т.д.); хорошая шлифуемость после термической обработки.
7.Инструментальный материал должен обладать достаточ-
ной теплопроводностью.
8.Инструментальный материал должен иметь возможность
обрабатываться в холодном и горячем состоянии.
9.Инструментальный материал долженбыть экономичным. Для твердых сплавов первые два требования менее сущест-
венны, но зато особое значение приобретает хорошая шлифуемость, а также отсутствие трещин и других дефектов, которые возникают в твердом сплаве после припайки пластин, при шлифовании и заточке инструмента.
4.1.2. Классификация инструментальных материалов, их маркировка и применение
К инструментальным материалам относятся восемь групп материалов, главное отличие которых в максимальной температуре теплостойкости (красностойкости):
230