
книги / Резание материалов
..pdf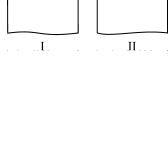
С увеличением глубины резания t (рис. 117, б) возрастает ширина среза b и общее количество теплоты, так как увеличивается составляющая силы резания Pz. Однако при этом увеличивается и длина активного участка режущей кромки b, отводящей теплоту в тело резца. Прирост температуры резания становится незначительным.
При резании определенного материала температура резания растет с увеличением скорости резания и размеров срезаемого слоя. Однако их влияние на температуру резания неодинаково. На основании измерений получена формула, связывающая температуру резания с толщиной, шириной срезаемого слоя и скоростью резания при работе различными инструментами:
θ = CθV manbq.
Коэффициент Cθ в формуле зависит от рода и механических свойств обрабатываемого материала, геометрических параметров инструмента и применяемой смазочно-охлаждающей жидкости. При любых видах обработки величины показателей т, п и q неодинаковы: m > n > q, т.е. на температуру резания наибольшее влияние оказывает скорость резания, затем толщина срезаемого слоя и наименьшее – ширина срезаемого слоя. Измерение температуры резания при увеличивающемся отношении b/a также свидетельствует об ее уменьшении. В чем причина неодинакового влияния величин b и a на температуру резания?
На рис. 118 изображены два одинаковых резца, срезающих слои материала с одинаковой площадью поперечного сечения F = 2аb. Резец I срезает слой шириной 2b и толщиной а, а резец II срезает слой шириной b и толщиной 2a. Таким образом, на передней поверхности резцов на площади контакта 2bа действуют тепловые источники, мощность которых можно считать приблизительно одинаковой.
181
Источники скользят по контактной поверхности стружки со скоростью, равной скорости стружки. При увеличении отношения длины движущегося полосового источника тепла к его ширине средняя температура трения в пределах площади контакта непрерывно уменьшается. К этому следует добавить, что и условия отвода тепла через тело инструмента для резца I более благоприятны, так как источник тепла относительно более удален от вершины резца, что также способствует снижению температуры резания. Таким образом, резец I должен работать с меньшей температурой резания, нежели резец II.
Неодинаковое влияние ширины и толщины срезаемого слоя на температуру резания позволяет сформулировать второй закон резания: для уменьшения температуры резания при заданной площади сечения срезаемого слоя необходимо работать с возможно большей глубиной резания t (шириной среза b) и меньшей подачей S (толщиной среза а), с возможно большим отношением b/a, т.е. с широкими и тонкими стружками.
Выражая физические размеры срезаемого слоя при точении в формуле через глубину резания, подачу и главный угол в плане, получим эмпирическую зависимость средней температуры резания от условий резания:
θ = CθV mS nt q(sin )n–q.
Коэффициент Cθ в формуле зависит от рода и механических свойств обрабатываемого материала, геометрических параметров инструмента и применяемой смазочно-охлаждающей жидкости. Из данного выражения следует, что при точении подача и глубина резания на температуру резания влияют с той же интенсивностью, что и толщина и ширина срезаемого слоя. Следовательно, для снижения температуры резания при заданной площади сечения срезаемого слоя необходимо работать с возможно большим отношением t/S. При заданных глубине резания и подаче температуру резания можно уменьшить, уменьшая главный угол в плане резца. Последнее связано с тем, что при уменьшении угла отношение b/a возрастает.
182
Интенсивность влияния скорости резания на температуру при различных скоростях неодинакова. Чем выше скорость резания, тем меньшее влияние оказывает ее увеличение на возрастание температуры резания. Поэтому и величина показателя степени при скорости резания уменьшается с ее увеличением. Например, при
V < 100 м/мин т = 0,5…0,4, а при V > 100 м/мин т = 0,4…0,25.
Уровень температуры резания зависит от рода и механических свойств обрабатываемого материала. Чем больше работа, затрачиваемая на резание, тем при прочих равных условиях выше и температура резания. Поскольку средняя температура стружки при резании чугуна ниже, чем при резании стали, температура резания при обработке чугуна также ниже на 40…50 %. С увеличением твердости и прочности обрабатываемого материала температура резания возрастает.
При постоянной мощности тепловых источников температуру резания можно понизить, интенсифицируя отвод тепла в деталь и инструмент. Этого можно достигнуть, охлаждая деталь, стружку, инструмент струей смазочно-охлаждающей жидкости. Поскольку в большинстве случаев скорость стружки превышает скорость распространения тепла в материале обрабатываемой детали, то, направляя струю жидкости на отделяющуюся от детали стружку, можно добиться понижения температуры только ее слоев, прилегающих к свободной поверхности. Температура резания при этом понижается незначительно.
Значительно больший эффект можно получить, если струя жидкости будет омывать инструмент и тем самым повышать теплообмен между инструментом и окружающей средой. Чем больше тепла перейдет в инструмент и окружающую среду, тем ниже будет температура резания. Поэтому насадок, через который сма- зочно-охлаждающая жидкость попадает в зону резания, должен быть расположен так, чтобы струя жидкости омывала не только деталь и стружку, но и инструмент.
Применение инструментальных материалов, обладающих высокой теплопроводностью, также способствует понижению температуры резания. С более низкой температурой резания работают инструменты, имеющиевнутреннееохлаждениережущей части.
183
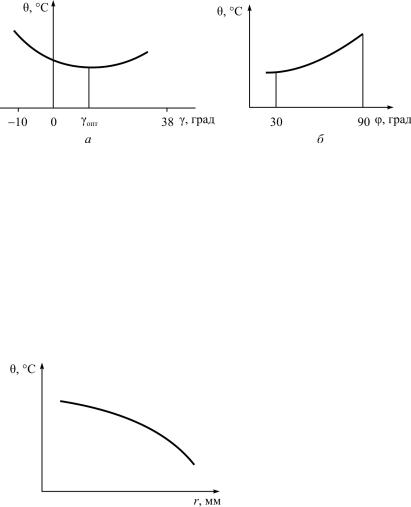
При увеличении переднего угла снижается коэффициент усадки стружки и, следовательно, касательная составляющая силы резания Pz. В результате этого уменьшается выделение тепла и снижается температура резания (рис. 119, а).
Рис. 119. Влияние изменения переднего угла γ (а) и главного угла в плане φ (б) на температуру резания θ
Однако увеличение переднего угла приводит к значительному уменьшению угла заострения , уменьшению массивности режущего клина и ухудшению условий теплоотвода, что, в свою очередь, приводит к повышению температуры резания.
При увеличении главного угла в плане увеличивается толщина сечения среза (a = S sin ). Это приводит к уменьшению коэффициента усадки стружки и составляющей силы резания Pz. Количество выделяемого тепла уменьшается (рис. 119, б).
|
Однако при увеличении |
|||
|
уменьшается массивность |
|||
|
режущего клина и активная |
|||
|
длина |
режущей |
кромки |
|
|
(ширина |
сечения |
среза) |
|
|
b = t/sin , от чего ухудша- |
|||
|
ются |
условия теплоотвода. |
||
|
Последний фактор является |
|||
|
преобладающим, |
поэтому |
||
Рис. 120. Влияние изменения |
при |
увеличении |
главного |
|
радиуса при вершине резца r |
угла |
в |
плане температура |
|
на температуру резания θ |
резания повышается. |
184
При увеличении радиуса вершины резца увеличивается коэффициент усадки, составляющая силы резания Py и количество выделяемого тепла. Однако при этом увеличивается массивность режущего клина резца и активная часть его режущей кромки, отчего улучшаются условия теплоотвода. Это приводит к преобладанию фактора снижения температуры резания (рис. 120).
3.1.4. Понятия об оптимальной температуре резания
В 30-х годах XX века профессором А.И. Соколовским и его учениками установлено, что зависимости интенсивности износа режущего инструмента V = ho.п или длины пути резания l = V·T от скорости резания V носят немонотонный характер с экстремальной точкой при так называемой оптимальной скорости резания. Знание оптимальных скоростей резания чрезвычайно важно для современного производства, особенно при изготовлении деталей из жаропрочных и других труднообрабатываемых материалов, обработка которых характеризуется весьма низкой размерной стойкостью инструмента и повышенным его расходом.
Значение указанного вопроса в степени возрастает при эксплуатации инструмента в условиях автоматизированного производства и на станках с ЧПУ. И не случайно вопрос об установлении оптимальных режимов резания, соответствующих наибольшей размерной стойкости, отнесен к числу важнейших экономических проблем современного машиностроения. Установление оптимальных скоростей резания является исключительно трудоемким и дорогостоящим делом, требующим к тому же больших затрат обрабатываемого материала и инструмента. Для сокращения этих затрат в 1961 году проф. А.Д. Макаровым предложено проводить исследование по ускоренной методике, т.е. по данным о характере кривой интенсивности износа hо.л = f(V) для одного сечения среза, путем использования кратковременных температурных исследований определять оптимальные скорости резания для любого другого сечения среза, без постановки трудоемких стойкостных испытаний. Такая возмож-
185
ность появляется в том случае, если точкам минимума кривых hо.л = f(V) или максимума кривых l = f(V) для разных сечений среза соответствует одна и та же средняя температура контакта или резания. Выбор температуры обусловлен следующими обстоятельствами:
температура резания является важнейшим физическим параметром, оказывающим влияние на изменение свойств контактирующих материалов (обрабатываемый материал – материал инструмента);
температура резания (ТЭДС) является наиболее легко и просто измеряемым параметром процесса резания.
Отдельными исследователями установлено что критические точки зависимостей усадки стружки, среднего коэффициента трения по передней поверхности, удельной работы стружкообразования и др. от скорости резания при работе с различными толщинами среза наблюдаются при различных скоростях резания, которым соответствует постоянная температура контакта.
Экспериментальные исследования показали, что оптимальным скоростям резания (для заданного материала режущей части инструмента) при различных комбинациях скорости резания, подачи и глубины резания соответствует постоянная температура в зоне резания (оптимальная температура резания). Причем ус-
тановлено, что эта температура не зависит от изменения геометрии режущих инструментов (рис. 121).
Постоянным же температурам в зоне резания (в том числе и оптимальным) при различных комбинациях V, S, t, как правило, не соответствуют равные периода стойкости. Известно, что каждой скорости резания соответствует определенная подача, при которой резец имеет максимальную размерную стойкость. Поскольку радиальный износ может быть измерен с наивысшей точностью и наиболее закономерно изменяется во времени, а минимальная интенсивность радиального износа при различных комбинациях t, S, V имеет место при постоянной (оптимальной) температуре резания, то создается возможность на основе ускорен-
186
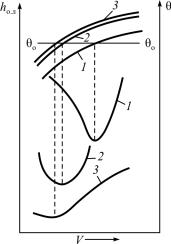
ных испытаний интенсивности радиального износа и температурных исследований очень быстро находить наивыгоднейшие сочетания элементов режима резания.
Эта возможность проверена экспериментально при обработке стали 30ХГСА, закаленной стали ЭХ12М и жаропрочного сплава ЭИ437А.
В результате экспериментальных исследований были сделаны следующие выводы:
1.Снижение скорости резания против оптимальной создает более благоприятные условия для развития явления адгезии.
2.Развитие явлений адгезии, повышение трения на по-
верхностях инструмента и по- |
Рис. 121. Влияние скорости реза- |
вышение объема пластических |
ния на температуру резания θ |
деформаций срезаемого слоя и |
и интенсивность износа резца hо.л |
обработанной поверхности, на- |
при различной геометрии резцов: |
блюдаемые при снижении ско- |
1 – 1, 1, 1, r1; 2 – 2, 2, 2, r2; |
рости резания против оптималь- |
3 – 3, 3, 3, r3 |
ного значения, обусловливают |
|
повышение интенсивности износа инструмента и повышение шероховатости обработанной поверхности.
3.Повышение скорости резания против оптимального значения приводит к уменьшению явлений адгезии, но резко усиливает диффузионные процессы между инструментальным и обрабатываемым материалами и усиливает защитную функцию окисных пленок, образующихся на поверхностях контакта, что оказывает непосредственное влияние на повышение интенсивности износа инструмента.
4.Закономерности изменения шероховатости и наклепа обработанной поверхности при изменении скорости резания анало-
187
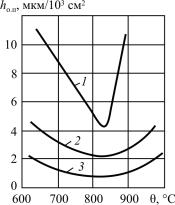
гичны закономерностям изменения интенсивности износа инструмента. При работе на скоростях резания, обеспечивающих минимум интенсивности износа инструмента, наблюдается минимум (или стабилизация) глубины и степени наклепа обработанной поверхности. Равенство скоростей резания, соответствующих точкам минимума или критическим точкам кривых
hо.п = f(V), Rz = f(V), H = f(V), hс = f(V), является вполне закономерным, так изменение отмеченных характеристик процесса резания
происходит в значительной мере под действием одних и тех же физических причин.
5. Поскольку при работе на оптимальных скоростях резания наблюдается минимальный наклеп и минимальная высота неровностей обработанной поверхности, то ведение процесса на оптимальных режимах имеет особо важное значение при выполнении окончательных операций изготовления ответственных деталей с повышенными требованиями к качеству поверхностного слоя.
Рис. 122. Зависимость относительного поверхностного износа hо.п от температуры при точении стали 40ХН2МА резцом из Т14К8 (t = 1 мм; S, мм/об:
1 – 0,43; 2 – 0,21; 3 – 0,11)
188
Оптимальная температура резания (контакта) – это температура, при которой наблюдается наименьшая интенсивность износа инструмента (рис. 122). Оптимальная температура зависит от свойств как обрабатываемого, так и инструментального материалов. Например, при обработке сталей 40ХНМА, ЭИ736 и ЭИ654 резцом Т14К8 значение оптимальной температуры резания θо составляет соответственно 820, 770 и 930 °С, а при обработке стали X18Н9Т резцами ВК8, ВK2
и Т14К8 – 785, 800 и 850 °С. При-
чем для различных подач оптимальная температура резания одна и та же – 820 °С (см. рис. 122).
В чем же состоит физическая сущность оптимальной температуры резания? Установлено, что большинство факторов, влияющих на интенсивность износа инструмента (отношение контактных твердостей, диффузия и адгезия, окислительные процессы, пластическое течение контактных слоев инструментального материала вследствие их размягчения и др.), является функцией температуры контактных поверхностей. Наиболее резкое изменение физических свойств обрабатываемых металлов и сплавов происходит при критических температурах структурно-фазовых превращений. При указанных температурах в приповерхностных контактных слоях обрабатываемого материала происходит скачкообразное изменение параметра кристаллической решетки, удельной теплоемкости, удельного электросопротивления, коэффициента линейного расширения, термоэлектродвижущей силы, модуля упругости и ряда других физических свойств. В связи с этим была выдвинута гипотеза о решающей роли структурно-фазовых превращений, происходящих в контактных слоях обрабатываемого материала, в создании условий, обеспечивающих наименьшую интенсивность износа инструмента. Основанием для выдвижения указанной гипотезы было то, что при температурах превращений происходит ослабление межатомных связей и потеря устойчивостиисходной фазы к смещению темпов при нагреве. В результате исследований установлено, что при чистовом точении (t = 0,25 мм; S = 0,10 мм/об) большой группы сталей резцом Т15К6 оптимальные температуры резания, измеренные методом естественной термопары, как температуры, соответствующие наименьшей интенсивности износа инструмента, достаточно хорошо согласуются (практически совпадают) с температурами точек АС3 структурно-фазовых превращений в указанных сталях (табл. 6).
Гипотеза о совпадении оптимальной температуры резания
стемпературой превращений нашла подтверждение и для жаропрочных сплавов, у которых провалы пластичности, как известно, являются результатом взаимодействия процессов деформации
спревращениями. Ранее было установлено равенство оптимальных температур резания и температур провала пластичности.
189
Таблица 6
Сопоставление оптимальных температур резания, полученных при точении некоторых сталей, с температурами их структурно-фазовых превращений
Марка |
Оптимальная |
Температура |
|
2 |
1 2 |
температура |
точки АС3 θ2, |
∆1 = θ2 – θ2, ºС |
|||
стали |
резания θ1, ºС |
ºС |
|
|
1 |
Сталь Э |
910 |
890 |
20 |
|
2,2 |
10 |
890 |
860 |
30 |
|
3,36 |
20 |
870 |
840 |
30 |
|
3,44 |
30 |
840 |
820 |
20 |
|
2,38 |
40 |
820 |
790 |
30 |
|
3,65 |
45 |
790 |
885 |
15 |
|
1,9 |
45 |
800 |
775 |
25 |
|
3,12 |
50 |
790 |
760 |
30 |
|
3,80 |
12Х2Н4А |
800 |
780 |
20 |
|
2,5 |
20XН |
850 |
835 |
15 |
|
1,76 |
20ХМ |
820 |
810 |
10 |
|
1,22 |
30ХГСА |
820 |
830 |
–10 |
|
1,22 |
30ХГСНА |
800 |
815 |
–15 |
|
1,87 |
50Х |
780 |
770 |
10 |
|
1,28 |
50ХНС |
800 |
770 |
30 |
|
1,75 |
После уточнения и углубления представлений о физической сущности оптимальной температуры резания разработаны ускоренные способы определения оптимальных скоростей резания. Способы основываются на научно установленных фактах совпадения оптимальных температур резания с критическими температурами различного рода превращений в обрабатываемых материалах (точки АС3 структурно-фазового превращения, точки Кюри, температура провала пластичности и др.) и скачкообразным изменением физических свойств металла при указанных температурах. По температурным зависимостям физических свойств металла и зависимостям, выражающим влияние скорости резания на среднюю температуру контакта, оптимальные скорости резания легко определяются графически.
Наличие ускоренных способов определения оптимальных скоростей резания по величине оптимальной температуры реза-
190