
книги / Резание материалов
..pdfГлава 3 ТЕПЛОФИЗИКА ПРОЦЕССА РЕЗАНИЯ
3.1.Температура резания и тепловое поле
3.1.1.Источники образования тепла
и распределение тепла между стружкой, инструментом и деталью
Теплота – один из основных физических факторов, сопровождающих процесс резания. Температура на поверхности контакта в зоне главной режущей кромки достигает 800…1000 °C. Теплота имеет как положительное, так и отрицательное влияние на процесс обработки резанием.
Положительное воздействие на процесс резания: облегчает деформирование материала срезаемого слоя, способствует образованию пограничного слоя на контактных поверхностях стружки и заготовки с низким коэффициентом трения, вследствие чего уменьшается износ инструмента и повышается качество обработанной поверхности.
Отрицательное влияние теплоты заключается в том, что она приводит к снижению твердости режущего инструмента. Это способствует потере режущих способностей инструмента и ускоренному его изнашиванию. Изменяются также его радиальные размеры, что вызывает снижение точности обработки. Нагрев жестко закрепленной обрабатываемой заготовки ведет к изменению ее размеров и деформациям, что также влияет на точность обработки. Высокая температура в зоне резания при шлифовании вызывает дефекты поверхностного слоя деталей в виде шлифовочных трещин и прижогов.
В связи с этим знание закономерностей образования и распределения тепла при резании различных заготовок является важной задачей технологов машиностроительных предприятий.
Выделение теплоты объясняется преобразованием механической работы при срезании стружки в тепло. Установлено, что при
171
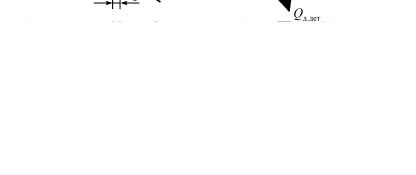
резании конструкционных материалов более 99,5 % работы резания переходит в тепло.
На основании этого общее количество тепла, образующегося при резании от деформации и трения по передней и задней поверхности инструмента, можно определить с помощью выражения
Q = Qд + Qт.п + Qт.з.
Расположение источников тепла представлено на рис. 112, а. Тепло деформации Qд образуется в зоне сдвигов на условной плоскости сдвига; тепло трения на передней поверхности Qт.п – в пределах площадки контакта между стружкой и инструментом шириной с; тепло трения на задней поверхности Qт.з – в пределах площадки контакта между поверхностью резания и инструментом. Образовавшееся тепло распространяется из очагов теплообразования к более холодным областям, распределяясь между стружкой, деталью и инструментом.
а |
б |
Рис. 112. Источники образования тепла в зоне резания (а) и распределения его в стружку, инструмент и деталь (б)
Между стружкой, деталью и инструментом устанавливаются тепловые потоки, изображенные на рис. 112, б. Часть тепла деформации Qд.с от условной плоскости сдвига переходит в струж-
172
ку. Из зоны трения на передней поверхности в стружку переходит часть тепла трения, равная Qт.п – Qп, где Qп – тепло, уходящее в инструмент.
Таким образом, тепло стружки Qс определяется суммарным тепловым потоком:
Qс = Qд.с + Qт.п – Qп.
Часть тепла деформации Qд.дет от условной плоскости сдвига переходит в деталь. Туда же из зоны трения на задней поверхности переходит часть тепла трения, равная Qт.з – Qз, где Qз – тепло, уходящее в инструмент. В результате этого интенсивность теплового потока в деталь
Qдет = Qд.дет + Qт.з – Qз.
Температурное поле режущего клина инструмента устанавливается в результате действия суммарного теплового потока Qи с передней и задней поверхностей:
Qи = Qп + Qз.
На основании этого можно составить выражение, описывающее расход образовавшегося при резании тепла:
Q = Qс + Qдет + Qи + Qср.
где Qср – количество тепла, уходящего в окружающую среду. Подставив вместо Q общее количество тепла, образующегося
при резании от деформации и трения по передней и задней поверхности инструмента в последнее выражение получим в совокупности уравнение теплового баланса при резании материалов.
Q = Qд + Qт.п + Qт.з.= Qс + Qдет + Qи + Qср.
Поскольку образовавшееся тепло пропорционально совершаемой работе, количество тепла зависит от рода и механических свойств материала обрабатываемой детали, геометрических параметров инструмента и режима резания. На процентное распределение тепла между стружкой, деталью и инструментом главное влияние оказывают механические и теплофизические свойства материала детали и скорость резания.
173
В 1915 году Я.Г. Усачев установил, что наибольшее количество тепла переходит в стружку, составляя при обработке стали от 60 до 85 % от общего количества тепла. С увеличением скорости резания доля тепла, уходящего в стружку, увеличивается, а ее средняя температура растет. Исследования последних лет показали, что процентное распределение тепла значительно зависит от рода обрабатываемого материала (табл. 5).
Таблица 5
Распределение теплоты между стружкой, инструментом и деталью при точении твердосплавными резцами
Обрабатываемый |
|
|
Количество |
|||
|
Режим резания |
теплоты, % |
|
|||
материал |
|
|
||||
|
|
Qс |
Qд |
|
Qн |
|
|
|
|
|
|||
Алюминий |
V = 100 |
м/мин, S = 0,12 мм/об, |
21 |
73 |
|
2,2 |
Чугун |
42 |
50 |
|
1,5 |
||
|
t = 1,5 мм |
|
||||
Сталь 40Х |
|
71 |
26 |
|
1,9 |
|
|
|
|
||||
Сталь 45 |
V = 30 |
м/мин, S = 0,3 мм/об, |
69,2 |
27,4 |
|
3,4 |
|
t = 4 мм |
|
||||
|
|
|
|
|
|
|
Титановый сплав |
V = 35 |
м/мин, S = 0,3 мм/об, |
73,4 |
16,8 |
|
9,8 |
|
t = 4 мм |
|
||||
|
|
|
|
|
|
|
Спеченная сталь |
V = 100 |
м/мин, S = 0,08 мм/об, |
55 |
28 |
|
17 |
|
t = 0,1 мм |
|
||||
|
|
|
|
|
|
При постоянной скорости резания средняя температура стружки и распределение тепла между стружкой, инструментом и деталью зависят главным образом от работы, расходуемой на резание, и теплопроводности обрабатываемого материала.
Средняя температура стружки при обработке стали значительно выше, чем при обработке чугуна и особенно алюминия, что вызвано как большей работой пластического деформирования, так и работой трения на передней поверхности.
Уменьшение количества тепла, уходящего в стружку, при обработке чугуна связано с элементным типом стружки при его резании. Вследствие более высокой теплопроводности алюминия по сравнению со сталью и чугуном тепло из зоны деформации интенсивно распространяется в деталь, тем самым резко уменьшая количество тепла, остающегося в стружке.
174
Количество тепла, уходящего в инструмент, очень мало и при резании любых материалов с любыми режимами обработки намного меньше количества тепла, уходящего в стружку и деталь. Основной причиной низкой интенсивности теплоотвода в инструмент является более низкая теплопроводность инструментального материала по сравнению с обрабатываемым. Уменьшение количества тепла, отводимого в инструмент, при обработке хрупких материалов связано также с элементным видом стружки, при образовании которой отсутствует постоянный контакт между стружкой и передней поверхностью. В результате экспериментальных исследований установлено, что при резании с небольшой скоростью резания (до 30…40 м/мин) относительное количество теплоты составляет: Qс = 60…70 %, Qи = 3 %, Qдет = 30…40 %,
Qср = 1…2 %.
Распределение тепла между стружкой, деталью и инструментом коренным образом изменяется при увеличении скорости резания: количество тепла, уходящего в стружку, возрастает, а уходящего в деталь и инструмент – уменьшается. Например, при точении стали 40Х со скоростью резания 20…50 м/мин в стружку уходит в среднем около 45 % тепла, а в деталь и инструмент – соответственно 47 и 4,5 %; при скорости резания 100…300 м/мин
встружку уходит 75 % тепла, а в деталь и инструмент – соответственно только 22 и 1,5 %. При скорости резания 400…500 м/мин
встружку уходит до 98 % тепла, в инструмент – 2…3 %.
Уменьшение доли тепла, переходящего в деталь при увеличении скорости резания, вызвано изменением соотношения между скоростью резания и скоростью распространения тепла из зоны деформации. Из очага теплообразования на условной плоскости сдвига (см. рис. 112, б) в деталь течет тепловой поток Qд.дет. Скорость распространения тепла зависит от градиента температур на условной плоскости сдвига и в детали и температуропроводности обрабатываемого материала. Если скорость резания, т.е. скорость, с которой режущий клин инструмента пересекает тепловой поток, мала, то тепло от условной плоскости сдвига беспрепятственно перейдет в деталь.
175
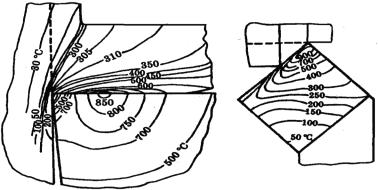
3.1.2.Понятие о тепловом поле
итемпературе резания
Температурное (тепловое) поле – это совокупность значений температур в различных точках тела в данный момент времени.
Зная величину и направление тепловых потоков, можно расчетным путем установить законы распределения температур на контактных площадках. На рис. 113 представлено изменение температуры θx для различных точек площадки контакта на передней поверхности инструмента при точении стали ШХ15. Несмотря на то, что доля тепла, уходящего в инструмент, очень мала, средняя температура θ на передней поверхности инструмента в несколько раз превосходит среднюю температуру стружки.
Рис. 113. Температурные поля в стружке, детали и резце при точении стали ШХ15 резцом из твердого сплава Т14К8 (V = 80 м/мин, S = 0,5 мм/об, t = 4,1 мм)
Температура контакта на передней поверхности приблизительно равна температуре контактной поверхности стружки; это свидетельствует о том, что температура различных слоев стружки по ее толщине неодинакова – убывает по мере приближения к свободной стороне стружки. Максимальная температура 850 °С соответствует точке, лежащей приблизительно на половине ширины площадки контакта. К лезвию икконцу площадки температураубывает.
176
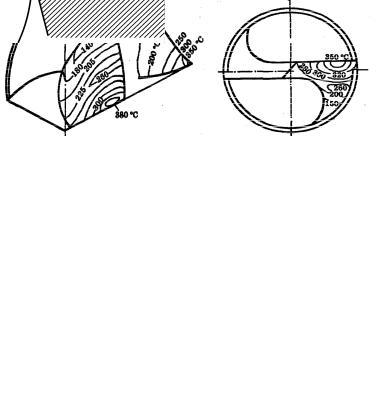
При сверлении также наблюдается неравномерный характер распределения температуры по передней и задней поверхностям сверла (рис. 114). Поэтому под температурой резания θ понимают среднюю температуру на поверхности контакта инструмента со стружкой и поверхностью резания.
Рис. 114. Тепловое поле и характер распределения температуры резания на передней и задней поверхностях сверла диаметром 30 мм при сверлении стали45 (V = 25 м/мин, S = 0,11 мм/об), измеренное160 термопарами
Аналогично изменяется температура при точении стали 40 (рис. 115). Максимальное значение температуры 870 °С находится в середине контакта на расстоянии 0,5 мм от режущей кромки в точке максимального давления стружки на переднюю поверхность.
Если через θп.ср и θз.ср обозначить средние температуры на
площадках контакта передней и задней поверхностей, то температура резания
θ = (θп.срс + θз.срс2)/(с + с2).
Рис. 115. Изменение температуры θх по ширине площадки контакта с при точении стали 40 (t = 1,5 мм; S = 0,21 мм/об; V = 115 м/мин)
Для незатупленного инструмента ширина сз площадки контакта задней поверхности с поверхностью резания исчезающе
177
мала, а поэтому температуру резания можно считать равной средней температуре на площадке контакта стружки с передней поверхностью, т.е. θ = θп.ср. Передняя поверхность инструмента нагревается за счет тепла деформации и трения. Поэтому температура резания равна сумме температуры деформации θд и средней температуры трения на передней поверхности θп.ср, т.е.
θ= θд + θп.ср.
3.1.3.Влияние условий резания на среднюю температуру резания. Второй закон резания
Температура резания зависит от мощности тепловых источников в зоне деформации и на передней поверхности инструмента и интенсивности стоков тепла в деталь и инструмент.
Значительное влияние на величину температуры в зоне резания оказывает обрабатываемый материал. Чем выше предел прочности и твердость металла заготовки, тем большую работу необходимо затратить на срезание стружки и тем больше выделится теплоты. Чем выше теплопроводность обрабатываемого материала, тем ниже (при прочих равных условиях) температура резания, и наоборот. Примером обрабатываемых материалов с высокой теплопроводностью могут служить алюминиевые сплавы, с низкой – титановые. При обработке аустенитных сталей и сплавов температура в 1,5…2 раза выше, чем при обработке конструкционных сталей.
При обработке жаропрочных сталей и сплавов температура еще выше, так как помимо высоких прочностных свойств эти материалы, как правило, обладают и низкой теплопроводностью.
Роль инструментальных материалов также весьма значительна. Чем ниже теплопроводность инструментального материала, тем выше температура резания. Например, минералокерамика имеет теплопроводность ниже, чем твердосплавные инструменты, а поэтому температура при работе с минералокерамикой будет выше.
Твердые сплавы группы ТК имеют температуру выше, чем резцы из ВК, так как титан имеет низкую теплопроводность.
178
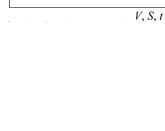
На теплосодержание стружки и ее среднюю температуру оказывает влияние режим резания: глубина резания, подача и скорость резания. По мере увеличения скорости резания клин инструмента все быстрее пересекает тепловой поток, и поэтому в деталь успевает перейти меньшее количество тепла и все большее количество тепла остается в стружке. Уменьшение доли тепла, уходящего в инструмент, при увеличении скорости резания связано с уменьшением ширины площадки контакта на передней поверхности, через которую тепло из стружки переходит в инструмент.
При увеличении глубины резания удельное количество тепла в стружке уменьшается, при увеличении подачи практически остается постоянным, а при увеличении скорости резания возрастает. Увеличение глубины резания и подачи сопровождается уменьшением средней температуры стружки. При увеличении же скорости резания средняя температура стружки вначале интенсивно возрастает, а затем, после достижения скоростью резания определенного значения, рост температуры почти прекращается, и она мало зависит от дальнейшего увеличения скорости.
При этом средняя температура стружки стремится к некоторому пределу, величина которого определяется типом и механическими свойствами обрабатываемого материала, геометрическими параметрами инструмента, глубиной резания и пода-
чей (рис. 116).
На рис. 116 видно, что прирост температуры отстает от увеличения скорости резания. Это объясняется тем, что с увеличением скорости резания несколько снижается величина составляющей силы резания Pz, в определенном диапазоне скоростей резания снижается коэффициент трения, большее количество
179
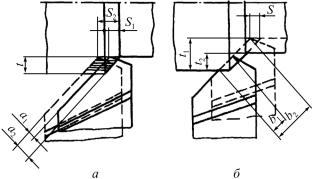
тепла отводится стружкой. В общем виде зависимость температуры резания от скорости резания можно выразить следующим выражением:
C1 V ZT ,
где ZT = 0,26…0,72.
Кроме того, видно, что в меньшей степени на прирост средней температуры влияет глубина резания t, чем подача S.
С увеличением подачи S возрастает толщина среза a и составляющая силы резания Pz, следовательно, количество выделяющейся теплоты увеличивается (рис. 117, а).
Рис. 117. Влияние подач S (а) и глубины резания t (б) на изменение площади сечения аb и интенсивность теплоотвода в зоне резания
Но составляющая силы резания Pz возрастает в меньшей степени, чем увеличивается подача, и поэтому прирост тепла отстает от роста подачи. При этом центр давления стружки на резец отдаляется от режущей кромки, и увеличивается площадь соприкосновения стружки с резцом. Поэтому улучшаются условия теплоотвода. Температура резания повышается значительно медленнее увеличения подачи. Эту зависимость можно выразить, как
C2 SYT ,
где при точении сталей YT = 0,20...0,45.
180