
книги / Резание материалов
..pdf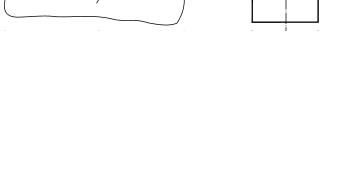
|
|
|
|
|
В |
|
|
|
|
|
|
|
С |
||||
|
|
|
|
|
|
|
|
|
|
|
|
|
|
|
|
|
|
|
|
О |
|
|||||
|
|
|
|
|
|
|
|
|
В |
|
|
|
|
|
|
||
С |
|
|||||||
О |
||||||||
|
|
|
|
|
|
|
аб
Рис. 38. Угол контакта при фрезеровании:
а – цилиндрической фрезой; б – торцовой фрезой
Кроме полного угла контакта различают также мгновенный угол контакта – центральный угол между радиусом, проведенным в начальную точку касания зуба фрезы с заготовкой, и радиусом, проведенным в точку мгновенного положения зуба.
Траекторией относительного рабочего движения точки режущей кромки фрезы является удлиненная циклоида. Поэтому стружка срезается в виде запятой (рис. 39), а толщина ее изменяется от нуля до amax на выходе зуба из контакта с заготовкой. При используемых отношениях скорости движения детали к скорости вращения фрезы дуга циклоиды мало отличается от дуги окружности. Для упрощения математического описания размеров срезаемого слоя при фрезеровании дугу циклоиды можно заменить дугой окружности с диаметром, равным диаметру фрезы. Ошибка не будет превышать 1 %. На рис. 39 точка А соответствует моменту выхода из зоны контакта с заготовкой первого зуба, точка В – второго. Приняв дли-
ну дуги ВС равной длине отрезка ВС, получим AC = amax = Sz sin . Для произвольногоугла контакта можно записать a = Sz sin .
При фрезеровании иногда рассматривают понятия о средней и срединной толщине среза. Средняя толщина среза а = (amax + + amin)/2 = amax/2. Срединная толщина среза, соответствующая уг-
61
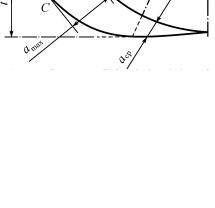
лу контакта /2 acp = Sz · sin( /2) = Sz(t/D)1/2. Для прямозубой фрезы b = В, для цилиндрической фрезы с винтовыми зубьями b является переменной величиной. Для торцовых фрез b = t / sin · cos , где t – глубина фрезерования, – угол в плане, – угол наклона режущей кромки.
В
А
С
Рис. 39. Расчетная схема для определения толщины срезаемого слоя при фрезеровании
Произведение глубины резания на подачу или ширины среза на его толщину дает номинальную, или расчетную, площадь среза (f, мм2), при резании одной режущей кромкой f = tS = ab.
При резании одновременно двумя и более режущими кромками действительная площадь среза отличается от номинальной на площадь гребешков, остающихся на обработанной поверхности из-за наличия углов в плане и закругления вершины лезвия. Отличия эти незначительны, и ими для практических расчетов можно пренебречь.
Площадь поперечного сечения среза, снимаемая одним зубом цилиндрической фрезы с прямыми зубьями, f = Ва. Она изменяется, как и толщина среза, от нуля до максимума:
fmax = Bamax = BSz · sin = 2BSz(t/D – t2/D2)1/2.
62
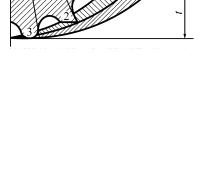
При фрезеровании в работе участвуют одновременно несколько зубьев (рис. 40). Поэтому вводится понятие о суммарной площади поперечного сечения среза. Для ее определения необхо-
димо знать, сколько зубьев одновременно находятся в работе и каков мгновенный угол контакта для каждого работающего зуба.
1
2
3
Рис. 40. К расчету суммарной площади срезаемого слоя несколькими зубьями цилиндрической фрезы
Количествозубьевфрезы, находящихсяодновременновработе,
m |
|
|
z |
, |
|
|
360 |
||||
|
|
|
где – полный угол контакта фрезы с заготовкой; – центральный угол между двумя соседними зубьями фрезы: = 360/z; z – число зубьев фрезы.
Значение m округляется до ближайшего большего целого числа. Если 1 < m < 2, то одновременно в работе находится два зуба, если 2 < m < 3 – три зуба, и т.д. Число одновременно работающих зубьев тем больше, чем больше t и z и меньше D. Мгновенные углы контакта для работающих зубьев 1, 2, 3 фрезы (см.
рис. 40): 1 = ; 2 = – ; 3 = – 2 и т.д.
Поскольку для каждого i-го зуба площадь поперечного сечения среза fi = BSz · sin , суммарная площадь поперечного сечения среза, снимаемого прямозубой фрезой,
63
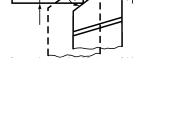
m
Аfi
i 1
m
BSz sin 1 sin 2 ... sin m BSz i .
i 1
Остаточное сечение среза при точении. Остаточное сече-
ние представляет собой треугольник (рис. 41), площадь которого определяется величиной подачи So (это основание треугольника) и углами в плане и 1 (т.е. углами при основании треугольника). Величина остаточного сечения среза влияет на величину шероховатости обработанной поверхности.
Рис. 41. Формирование остаточных гребешков на обработанной поверхности
1.4.3. Расчет основного времени резания
Время непосредственного срезания стружки называется ос-
новным временем выполнения технологической операции. Это время рабочего хода, т.е. движения инструмента относительно детали со скоростью подачи. Например, для продольного точения поверхности заготовки длиной l напроход (рис. 42) для каждого прохода машинное время рассчитывается по следующей формуле:
to = Lp.x /Sx = Lp.x /(nSo),
где Lp.x – длина рабочего хода, Lp.x = l + l1 + l2; l – длина поверхности детали, по которой осуществляется перемещение в направле-
нии подачи; l1 = lвр – длина врезания режущей кромки до набора полной глубины резания; l2 = lпер – перебег инструмента или детали в направлении подачи.
64

Рис. 42. Схема продольного точения заготовки для расчета основного времени резания поверхности l
Длина врезания зависит от геометрии инструмента и его конструктивных особенностей: при точении l1 = t · ctg + (0,5...2) мм; при сверлении l1 = (D/2 · tg ) + (0,5…2) мм; при фрезеровании цилиндрической фрезой l1 = [t(D – t)]1/2 + (0,5...2) мм; при симметричном фрезеровании торцовойфрезойl1 = 0,5[D – (D2 – B2)1/2] + (0,5...2) мм.
Значение 0,5...2 мм принимается для обеспечения свободного подхода инструмента к обрабатываемой поверхности.
Перебег при работе на проход составляет 1...5 мм в зависимости от размеров обработки.
При продольном точении в упор и при подрезке торца в упор перебег равен нулю (рис. 43), т.е. l2 = lпер = 0.
Рис. 43. Схема продольного точения заготовки (а) и подрезки торца (б) в упор для расчета основного времени резания поверхности l
Формулы для расчета to применительно к различным процессам обработки приводятся в справочной литературе.
65
Контрольные вопросы и задания
1.Дайте определение кинематическим элементам и характеристикам резания при точении.
2.Что называется поверхностью резания, обрабатываемой
иобработанной поверхностями?
3.Покажите на конкретном примере конструкцию и части токарного резца.
4.Дайте определение статической, инструментальной и кинематической системам координат.
5.Покажите схематично координатные плоскости в статической системе координат.
6.Как установка резца влияет на величины переднего, заднего углов и углов в основной плоскости?
7.Дайте определение элементам режима резания при точении, сверлении, фрезеровании: скорости резания, подаче, глубине резания, ширине фрезерования.
8.Дайте определение элементам и характеристикам срезаемого слоя при точении, сверлении, фрезеровании; сечению, его формам и размерам. Что такое остаточное сечение при указанных видах обработки?
9.Каковы особенности классификации резания по признакам: свободное и несвободное, прямоугольное и косоугольное, однолезвийное и многолезвийное, непрерывное и прерывистое?
66
Глава 2 ДИНАМИКА ПРОЦЕССА РЕЗАНИЯ
2.1.Деформация и напряжения в процессе резания
2.1.1.Некоторые сведения о пластической деформации металла
Врезультате экспериментальных и теоретических исследований установлено, что превращение срезаемого слоя в стружку при резании является одной из разновидностей процесса пластической деформации материала. Основным признаком пластической деформации является необратимое изменение формы тела под действием внешнихсилбез нарушения сплошности деформируемого тела.
Различают три основных вида деформированного состояния малого объема тела.
1. Растяжение (рис. 44, а), при котором вдоль одной из трех главных осей x, y, z деформации наблюдается удлинение, а вдоль двух остальных главных осей – укорочение. Если две отрицательные деформации укорочения равны между собой, то растяжение называют простым.
2. Сжатие – такая деформация, при которой вдоль одной оси происходит укорочение тела, а вдоль двух других осей – уширение и удлинение.
3. Сдвиг (рис. 44, б), при котором деформация вдоль одной из трех главных осей отсутствует, вдоль второй главной оси наблюдается укорочение, а вдоль третьей главной оси – равное ему удлинение.
Разновидностями сдвига являются чистый сдвиг и простой сдвиг. При чистом сдвиге (см. рис. 44, а) происходит равномерное укорочение вдоль одной оси и равномерное удлинение вдоль другой оси, перпендикулярной к первой. Квадрат ABCD превращается в
конгруэнтный ромб А1В1С1D1 при неизменном объеме тела. При простом сдвиге (см. рис. 44, б) деформация заключается в смещении
67
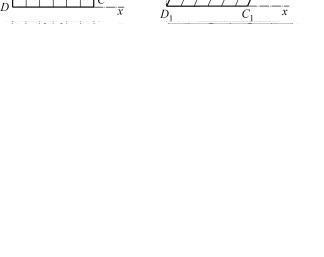
всех точек тела в направлении, параллельном только одной оси, на расстояние, пропорциональное расстоянию точки тела от этой оси в направлении второй оси. В результате простого сдвига квадрат ABCD превращается в равновеликий параллелограмм с теми же размерамиоснованияи высоты, что иу исходного квадрата.
|
|
|
|
|
В |
|
|
|
|
|
|
|
|
|
|
|
|
|
|
|
|
|
|
|
|
|
|
|
|
|
|
|
|
|
|
|
|
|
|
|
|
|
|
|
|
|
|
|
|
||
|
|
|
|
|
|
|
|
|
|
|
|
|
|
|
|
|
|
|
В1 |
||||||
|
|
|
|
|
|
|
|
С |
|
|
|
|
|
|
|
|
|||||||||
|
|
|
|
|
|
|
|
|
|
|
|
|
|
|
|
|
|
|
|
|
|
|
|
||
А |
|
|
|
|
|
|
|
|
|
|
|
|
|
|
|
|
|
||||||||
|
|
|
|
|
|
|
|
|
|
|
|
|
|
|
|
|
|
|
|
|
|
|
С1 |
||
|
|
|
|
|
|
|
|
|
|
|
|
|
|
|
|
||||||||||
|
|
|
|
|
|
|
|
|
|
А1 |
|
|
|
|
|||||||||||
|
|
|
|
|
|
|
|
|
|
|
|
|
|
||||||||||||
|
|
|
|
|
|
|
|
|
|
|
|
|
|
|
|
|
|
|
|
|
|
|
|
||
|
|
|
|
|
|
|
|
|
|
|
|
|
|
|
|
|
|
|
|
|
|
|
|
||
|
|
|
|
|
|
|
|
|
|
|
|
|
|
|
|
|
|
|
|
|
|
|
|
|
|
|
|
|
|
D |
|
|
|
|
|
|
|
D1 |
|||||||||||||
|
|
|
|
|
|
|
|
|
|
|
|
а |
|
|
|
|
|
|
|
|
|||||
|
|
|
|
|
|
|
|
|
|
|
|
|
|
|
|
|
|
|
|
|
|
|
|
|
|
|
|
|
|
|
|
|
|
|
|
|
|
|
|
|
|
|
|
|
|
В1 |
|||||
|
|
|
|
|
|
|
|
|
|
|
|
|
|
|
|
А1 |
|
|
|
|
|
|
|
||
|
А |
|
|
|
|
|
|
В |
|||||||||||||||||
|
|
|
|
|
|
|
|
|
|
|
|
|
|
|
|
|
|
|
|
|
|
||||
|
|
|
|
|
|
|
|
|
|
|
|
|
|
|
|
|
|
|
|
|
|
|
|
|
|
|
|
|
|
|
|
|
|
С |
|
|
|
|
|
|
|
|
|
|
|
|
|
|
|
||
|
D |
|
|
|
|
|
|
|
|
|
|
|
|
|
|
|
|
|
|
|
|
||||
|
|
|
|
|
|
|
|
|
|
|
|
|
|
|
|
|
|
|
|
|
|
|
|
||
|
|
|
|
|
|
|
|
|
|
|
D1 |
|
|
|
|
|
С1 |
|
|
|
|||||
|
|
|
|
|
|
|
|
|
|
|
|
|
|
|
|
|
|
|
б
Рис. 44. Схемы деформации чистого (а) и простого (б) сдвигов
Первые два вида (растяжение и сжатие) относятся к объемному деформированному состоянию, а третий (сдвиг) – к плоскому деформированному состоянию.
Частица срезаемого слоя, находящаяся далеко от режущего инструмента, свободна от напряжений и движется по направлению к инструменту с постоянной скоростью. По мере приближения к режущему инструменту напряжения в рассматриваемой частице возрастают, и, когда они превзойдут предел упругости обрабатываемого материала, частица получает пластическое смещение и изменяет направление своего движения. Эти изменения происходят за время пребывания частицы в некоторой переходной пластически деформированной зоне (рис. 45).
68
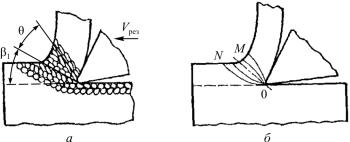
Рис. 45. Схема деформации частиц обрабатываемого материала в процессе резания (а) и образования поверхностей сдвига в переходной зоне стружкообразования (б) (β1 – угол сдвига; θ – угол текстуры стружки; Vрез – скорость резания; ON, OM – поверхности скалывания)
Поскольку в результате отделения слоя металла толщиной а и превращения его в стружку часть единого тела движется параллельно передней поверхности лезвия инструмента, а оставшаяся часть продолжает движение в прежнем направлении, то в точке, соответствующей сопряжению передней и задней поверхностей инструмента, под углом 1 к направлению движения, называемого углом сдвига, произойдет разделение тела на стружку и обрабатываемую деталь.
Представим переходную пластически деформируемую зону
ввиде параллелограмма ABCD (см. рис. 46, а), а линии скольжения
вней примем за прямые. Обозначим толщину этой зоны через х, а ее сдвиг через s. Значение s соответствует расстоянию (см. рис. 46, б), на которое сдвинулась верхняя сторона квадрата относительно нижней, и называется абсолютным сдвигом. В теории пластических деформаций для характеристики интенсивности сдвига пользуются величиной е, называемой относительным сдвигом. Он равен
отношению абсолютного сдвига s к толщине слоя AJC, претерпевшего этот сдвиг, т.е. е= s/ x. Геометрически еравен тангенсу угла наклонастороныквадратакосиz, т.е. е= tg (см. рис. 46, б).
Элемент срезаемого слоя ABCD под действием режущего клина инструмента деформируется и принимает форму параллелограмма EBCN. В треугольнике CDN (см. рис. 46, б)
69
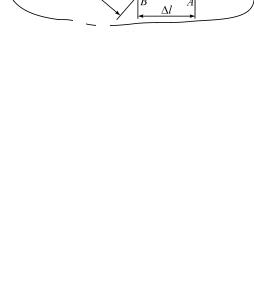
МС х; СМD 90 ; KNC ; NDC ;
|
ND s; |
FKC ; NCK ; |
|
|||
|
s |
ND |
= MD + MN |
ctg tg . |
(1) |
|
|
x |
MC |
|
MC MC |
|
|
NM
СD
Е
В А
а
N
M
K
C |
|
F |
|
D |
б
Рис. 46. Схема определения относительного сдвига в процессе резания
Анализ формулы показывает, что для определения относительного сдвига при определенном угле необходимо знать угол сдвига. Его можно определить по длине стружки. При перемещении инструмента на l длина стружки будет lc. Из АВЕ (см. рис. 46, а) следует:
lc |
|
l |
|
l |
и |
l |
|
cos |
. |
sin |
sin |
cos |
lc |
sin |
Отношение l/ lc = Kl получило название коэффициента усадки или укорочения стружки:
70