
книги / Резание материалов
..pdf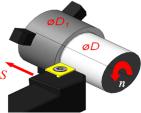
Движение резания – такое движение, которое необходимо для осуществления процесса превращения срезаемого слоя в стружку в данном сечении, точке или поверхности заготовки. При точении – это вращение заготовки. Движение подачи – такое движение, при котором стружкасрезается по всей длине заготовки.
При точении – это поступатель- |
|
||
ное перемещение |
токарного |
|
|
резца (рис. 4). Для снятия всего |
|
||
припуска |
часто необходимо, |
|
|
чтобы указанный процесс со- |
|
||
вершался непрерывно или по- |
|
||
вторялся периодически. Отли- |
|
||
чительным признаком главного |
Рис. 4. Общий вид главного |
||
движения резания является так- |
движения резания при продоль- |
||
же и то, что скорость этого |
ном точении (вращение заготов- |
||
движения во много раз превы- |
ки n, об/мин) и движения подачи |
||
шает скорость движения пода- |
(поступательное движение резца |
||
чи. Скорость движения резания |
S, мм/об; D, D1 – диаметры |
||
называют |
скоростью |
резания, |
обработанной и обрабатываемой |
скорость |
движения |
подачи – |
поверхности) |
|
просто подачей.
На станке предусмотрены и вспомогательные движения, которые не участвуют в процессе срезания стружки, – вращение ходового вала, ходового винта, подвод резца к заготовке, зажим и разжим заготовки, переключение скоростей и т.д.
Если движение подачи остановить, то обработка детали закончится при одном обороте детали.
Сущность того или иного метода обработки определяется только соотношением скоростей, осуществляемых при движении, и не зависит от того, сообщается ли движение резания и подачи инструменту или детали.
При фрезеровании главное движение резания осуществляется вращением фрезы, а движение подачи – перемещением заготовки или фрезы относительно друг друга.
21
При сверлении на сверлильном станке вращательное движение резания совершает сверло, а на револьверном станке – деталь. Соответственно движение подачи может совершать как инструмент, так и деталь. При некоторых методах обработки имеет место третье движение, являющееся вспомогательным движением формообразования и служащее для придания детали необходимой конфигурации. Таким третьим движением при нарезании резьбы резцом является его перемещение вдоль оси детали на расстояние, равное шагу резьбы за время одного оборота детали, а при фрезеровании венцов зубчатых колес червячно-модульными фрезами – поворот детали на один зуб за время одного оборота фрезы.
Взависимости от того, совершаются движения резания и подачи одновременно или в разное время, все инструменты делят на две группы: инструменты с простым и сложным рабочим движением.
Если движение подачи отсутствует в то время, когда совершается движение резания, то инструмент имеет простое рабочее движение. Если же движение резания и движение подачи совершаются одновременно, то инструмент имеет сложное рабочее движение. Большинство режущих инструментов (токарные резцы, сверла, зенкеры, развертки, фрезы и др.) имеют сложное рабочее движение. Инструментов с простым рабочим движением значительно меньше. К ним можно отнести строгальные и долбежные резцы, протяжки и некоторые другие инструменты.
1.1.2.Поверхности заготовки в процессе резания
Впроцессе срезания припуска на заготовке различают характерные поверхности: обрабатываемую, обработанную и по-
верхность резания (рис. 5). Обрабатываемой поверхностью 1
называют такую поверхность заготовки детали, с которой срезают стружку. Она исчезает в результате снятия припуска. Обработанной поверхностью 2 называют поверхность, образовавшуюся на детали после снятия стружки. Поверхностью резания 3 называют поверхность, непосредственно образуемую лезвиями инструмента в процессе резания. Эта поверхность яв-
22
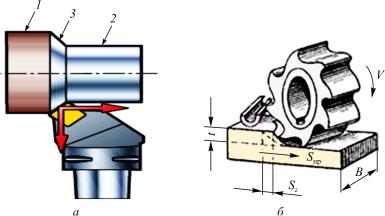
ляется переходной между обрабатываемой и обработанной поверхностями, она существует только во время резания и исчезает после окончания обработки.
Рис. 5. Поверхности заготовки в процессе резания при точении (а) и при фрезеровании (б): 1 – обрабатываемая; 2 – обработанная и 3 – поверхность резания (Sпр – продольная подача; V – скорость резания; t – глубина
резания; Sz – подача на зуб; B – ширина фрезерования)
Поверхность резания с геометрической точки зрения образована совокупностью траекторий относительного рабочего движения инструмента. Поэтому ее форма определяется формой лезвий инструмента и сочетанием движений детали и инструмента в процессе резания. При строгании поверхность резания является плоскостью, а при продольном точении – конволютнойвинтовой поверхностью.
Реальная форма обработанной поверхности всегда отличается от той идеальной формы, которая задается чертежом детали.
Если формообразование детали рассматривать только с геометрической точки зрения, то форма обработанной поверхности будет зависеть от формы поверхности резания, так как обработанная поверхность детали образована несрезанными участками поверхности резания. Для рассматриваемого токарного метода обработки обработанная поверхность представляет собой совокупность гребешков, очерченных двумя винтовыми поверхностями.
23
1.1.3. Кинематические схемы резания
Как показал проф. МВТУ им. Н.Э. Баумана Г.И. Грановский, несмотря на большое число методов обработки и их разнообразие, все они могут быть определены принципиальными кинематическими схемами, которые выражают абсолютные движения, сообщаемые в процессе резания инструменту и обрабатываемой детали механизмами станка. Кинематика рабочих органов металлорежущих станков намного упрощается при использовании принципиальных кинематических схем, основанных на сочетании равномерных движений: прямолинейных и вращательных. В зависимости от числа и характера сочетаемых движений принципиальные кинематические схемы могут быть разделены на восемь групп: I – одно прямолинейное движение (строгание, протягивание); II – два прямолинейных движения (отрезка ленточными пилами); III – одно вращательное движение (круговая протяжка); IV – одно вращательное и одно прямолинейное движение (точение, фрезерование, сверление); V – два вращательных движения (шевингование); VI – два прямолинейных и одно вращательное движение (зубодолбление); VII – два вращательных и одно прямолинейное движение (профильное круглое врезное шлифование); VIII – три вращательных движения (зубофрезерование спирально-конических колес). Наибольшее распространение получили принципиальные кинематические схемы: с одним прямолинейным движением и с одним прямолинейным
иодним вращательным движением.
Взависимости от соотношения угловых и линейных скоростей движений, сообщаемых инструменту и детали, возникают различные методы обработки.
1.2.Геометрия режущей части инструмента
1.2.1. Конструкция, части и поверхности токарного резца
Токарный резец представляет собой наиболее простой режущий инструмент в ряду других инструментов. Поэтому изучение конструкций режущих инструментов начинают с изучения его конструкции.
24
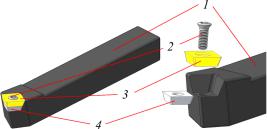
Токарный резец обычно имеет стержневую форму и состоит из двух частей: головки и тела резца (рис. 6). Головка резца является рабочей режущей частью резца. Она образуется в результате заточки на заточных станках и служит для срезания стружки с заготовки при точении. Тело резца (обычно прямоугольной формы в поперечном сечении) служит для установки и закрепления в резцедержателе токарного станка. Характерными размерами тела резца являются стандартизованные высота и ширина поперечного сечения.
Рис. 6. Составные части сборного токарного резца: 1 – державка резца; 2 – элемент крепления (винт);
3 – режущая сменная пластина; 4 – подкладная пластина
Для того чтобы режущий инструмент мог осуществлять процесс резания, его режущая часть должна быть очерчена определенными поверхностями. Рассмотрим эти поверхности резца (рис. 7). Передняя поверхность (1) – это такая поверхность инструмента, по которой в процессе резания сходит стружка. Главная задняя поверхность (2) – это поверхность инструмента, которая обращена к заготовке в сторону подачи резца и примыкает к поверхности резания.
Вспомогательная задняя поверхность (3) – это такая поверх-
ность инструмента, которая обращена к обработанной поверхности в противоположную от подачи резца сторону. Передняя и задняя поверхности инструмента могут быть вогнутыми, выпуклыми поверхностями, плоскостями или их комбинациями. Пересечение передней и главной задней поверхностей образует
25
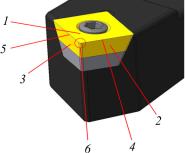
главную режущую кромку 4, а пересечение передней и вспомогательной задней поверхностей – вспомогательную режущую кромку 5.
Рис. 7. Основные элементы рабочей части резца: 1 – передняя поверхность; 2 – главная задняя поверхность; 3 – вспомогательная задняя поверхность; 4 – главная режущая кромка; 5 – вспомогательная режущая кромка; 6 – вершина инструмента
Между главной и вспомогательной режущими кромками располагается переходная кромка 6, которая образована пересечением передней поверхности с переходной задней поверхностью. Для простоты изготовления инструмента переходную кромку, называемую вершиной инструмента 6, очерчивают дугой окружности различного радиуса от 0,2 до 2 мм.
На переходной кромке вершиной инструмента называют ту точку лезвия, которой инструмент при его установке на станке коснется обрабатываемой поверхности. В зависимости от типа инструмента вспомогательных задних поверхностей на нем может быть больше чем одна (например, отрезной резец), а может и не быть совсем (например, осевая цилиндрическая фреза).
1.2.2.Системы координат и геометрические параметры резца (углы заточки)
При эксплуатации на металлорежущих станках и используемых в технологии изготовления резцов приемах заточки и контроля поверхности и кромок режущей части резца целесообразно
26
ориентировать резец относительно прямоугольного трехгранника, образованного тремя взаимно перпендикулярными плоскостями. В теории резания рассматривают три системы координат: статическую, инструментальную и кинематическую.
Статическая система координат (ССК) – прямоугольная система координат с началом в рассматриваемой точке режущей кромки, ориентированная относительно направления главного движения резания V. ССК применяется для приближенных расчетов углов резания в процессе резания и для учета изменения этих углов после установки на станок. Она является переходной от инструментальной системы координат к кинематической.
Инструментальная система координат (ИСК) – прямо-
угольная система координат с началом в вершине лезвия, ориентированная относительно геометрических элементов режущего инструмента, принятых за базу. Предназначена для установки
иконтроля геометрических параметров режущих инструментов в процессе их изготовления. ИСК применяется для изготовления
иконтроля инструмента.
Кинематическая система координат (КСК) – прямоугольная система координат с началом в рассматриваемой точке режущей кромки, ориентированная относительно направления скорости результирующего движения резания Vе. Кинематическая система координат предусматривает изменение углов инструмента в момент резания с учетом всех движений формообразования.
Для изучения основных геометрических параметров резца рассмотрим координатные плоскости в статической системе координат (рис. 8). Здесь резец получает определенную ориентацию относительно трехгранника.
Согласно ГОСТ 25762–83 основная плоскость (ОП) – коор-
динатная плоскость, проведенная через рассматриваемую точку режущей кромки перпендикулярно направлению вектора скорости главного движения. Все остальные координатные плоскости перпендикулярны основной плоскости.
Плоскость резания (ПР) – координатная плоскость, касательная к режущей кромке и перпендикулярная основной плоскости ОП в данной точке.
27
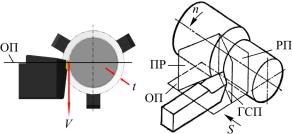
Плоскость (РП), рабочая плоскость, перпендикулярная основной плоскости, параллельная продольной подаче резца и касательная к обработанной поверхности.
Рис. 8. Схема расположения координатных плоскостей в статической системе координат
Для изображения положения передней и задней поверхностей и углов резца после заточки на заданную величину резец рассекают главной секущей плоскостью (ГСП) (см. рис. 8). ГСП перпендикулярна главной режущей кромке и основной плоскости. Углы на вспомогательной задней поверхности рассматривают во вспомогательной секущей плоскости (ВСП).
Углы резца в главной и вспомогательной секущих плоскостях изображены на рис. 9. Положение передней поверхности резца в сечении ГСП определяют передним углом . Передним углом резца называют угол между передней поверхностью или плоскостью, к ней касательной, и основной плоскостью. Передний угол характеризуют абсолютной величиной и знаком. Если передний угол располагается вне тела инструмента, то условились считать его положительным, а если в теле инструмента – отрицательным.
Положение задней поверхности в сечении ГСП определяют главным задним углом. Главным задним углом резца называют угол между главной задней поверхностью или плоскостью, к ней касательной, и плоскостью резания ПР, проходящей через главное лезвие перпендикулярно основной плоскости по касательной к поверхности резания. Задний угол по знаку должен быть только
28
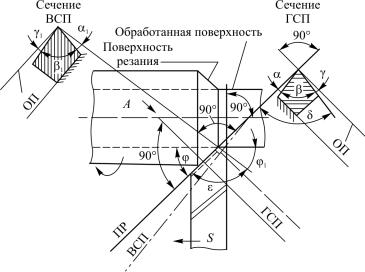
положительным. В противном случае лезвие резца при работе не коснется поверхности резания.
В сечении ГСП принято обозначать еще два угла – угол резания и угол заострения, или угол клина. Углом резания называется угол между передней поверхностью и плоскостью резания. Углом заострения называется угол между передней и задней поверхностями. Эти углы в ГСП связаны следующими соотношениями: + + = 90 , так как + = , то + = 90 .
Рис. 9. Геометрические параметры резца в ГСП и ВСП
Для изображения положения вспомогательной задней поверхности резец рассекают вспомогательной секущей плоскостью, перпендикулярной к вспомогательной режущей кромке и основной плоскости. Положение вспомогательной задней поверхности определяют вспомогательным задним углом. Вспо-
могательным задним углом 1 резца называют угол между вспо-
могательной задней поверхностью или плоскостью, к ней касательной, и плоскостью, проходящей через вспомогательное лезвие перпендикулярно основной плоскости. Положение главной
29

режущей кромки относительно основной плоскости определяют углом, расположенным в плоскости резания, проходящей через главное лезвие перпендикулярно ОП. Этот угол называют углом наклона главной режущей кромки (рис. 10 и 11). Угол есть угол между главной режущей кромкой или касательной к ней и основной плоскостью ОП, проходящей через вершину резца. Так же как и передний угол, угол должен характеризоваться не только абсолютной величиной, но и знаком.
Рис. 10. Схема определения положения угла наклона главной режущей кромки относительно основной плоскости в статической системе координат
Если вершина резца является наинизшей точкой главного лезвия, то угол условились считать положительным, а если наивысшей – отрицательным (см. рис. 11). Изменение угла наклона влияет на направление схода стружки при точении заготовок.
При положительном значении угла стружка сходит в сторону обработанной поверхности (рис. 11, а), ухудшая ее шероховатость. При отрицательном значении угла стружка сходит в сторону обрабатываемой поверхности (рис. 11, б), что используется при чистовой обработке заготовок. При нулевом значении угла стружка сходит вдоль резца в радиальном направлении
(рис. 11, в).
30