
книги / Резание материалов
..pdf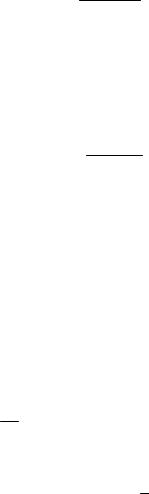
Kl cos .
Данную формулу называют формулой И.А. Тиме. С ее помощью можно выразить угол сдвига через коэффициент Kl:
Kl cos cos sin sin ctg sin , sin
отсюда
cos
tg = Kl sin .
Несмотря на принятые допущения о замене зоны первичной деформации единственной плоскостью сдвига и идеализации процесса превращения срезаемого слоя в стружку, формула И.А. Тиме совершенно точно выражает связь между Kl и углом сдвига , таккакотражаетусловиесплошностиматериала стружки.
Таким образом, относительный сдвиг при резании зависит от угла сдвига и переднего угла . Угол можно определить, зная а и ас, а всегда известен. Практически = 2...5. Определим, при каком относительный сдвиг будет минимальным. Для этого возьмем первую производную уравнения (1), приравняем ее к нулю и решим уравнение относительно :
d cosec2 sec2 0. d
Это условие справедливо при = 90° – ( – ). Тогда
min = 45° + 2 .
Зная относительный сдвиг, можно определить скорость деформации (с–1), которая представляет собой отношение максимальной главной деформации max к ее продолжительности деф
вединицу времени, т.е. Vдеф = max/ деф.
Вслучае неравномерной деформации сдвига ее скорость, или
скорость относительного сдвига, определяется как относитель-
71
ный сдвиг в единицу времени Vдеф = d /d . От Vдеф зависит температура, сопровождающая процесс деформации: чем выше ско-
рость деформации, тем меньше требуется энергии и меньше тепловыделение.
Пластические деформации материала срезаемого слоя при резании ограничиваются зоной стружкообразования. Наиболее интенсивно пластическая деформация протекает в очень узкой зоне, ширину которой для упрощения расчетов примем за прямоугольник толщиной х. Время деформации обрабатываемого
металла на этом участке составит деф = х/Vc = ( хKl)/V, т.е.
Vдеф = V/ хKl.
Скорость деформации при резании очень высока, и даже самые низкие скорости резания значительно превосходят скорости, достигаемые при испытаниях металлических образцов на удар. По экспериментальным данным, при обработке конструкционных материалов обычного качества х = 0,02...0,005 см; = 2...5; Kl = 2…4. При скорости резания 60 м/мин = 100 см/с, скорость деформации Vдеф ≈ 4000 с–1.
Высокие скорости деформации не позволяют установить четкую границу между хрупкими и пластичными материалами, поскольку один и тот же материал в зависимости от характера напряженного состояния при резании и скорости деформации может вести себя и как хрупкий, и как пластичный. Так, например, при точении чугуна стружка может быть сливной, при обработке вязких сталей – элементной.
2.1.2. Методы изучения и оценки пластической деформации
Существует несколько методов исследования деформации
всрезаемом слое.
1.Визуальное наблюдение отполированной боковой поверхности обрабатываемого образца: изучение микрошлифов зоны резания (корни стружки); по светлым пятнам и границам потускнения части металла можно судить о характере пластической деформации при резании. Например, с увеличением скорости резания при
72
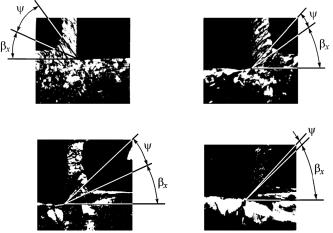
протягивании сплава ЭИ437БУ-ВД размер зоны деформации протянутых образцов уменьшается, а угол сдвига х увеличивается, что свидетельствует о снижении деформации (рис. 47).
а |
в |
бг
Рис. 47. Микрошлифы корней стружек сплава ЭИ437БУ-ВД:
а – 2 м/мин; б – 0,13 м/с; в – 0,43 м/с; г – 0,67 м/с (Sz = 0,1 мм/зуб; шлифы не травлены)
2.Метод измерения микротвердости и расчет напряжений
взоне резания. На полированной поверхности зоны резания
истружки наносят уколы алмазной иглой с помощью прибора микротвердомера ПМТ-3 с определенной нагрузкой. По глубине
иширине следа алмазной призмы вычисляют микротвердость в каждой точке. Затем переносят картину на бумагу, соединяют точки с одинаковой микротвердостью и рисуют схему пластической деформации в зоне резания. Например, на рис. 48 представлены результаты измерения микротвердости в зоне резания образцов из сплава ЭИ787-ВД, протянутых на различных скоростях резания с подачей на зубьях протяжки 0,06 мм/зуб. Установлено, что с увеличением скорости резания и снижением подачи пластическая деформация уменьшается.
73
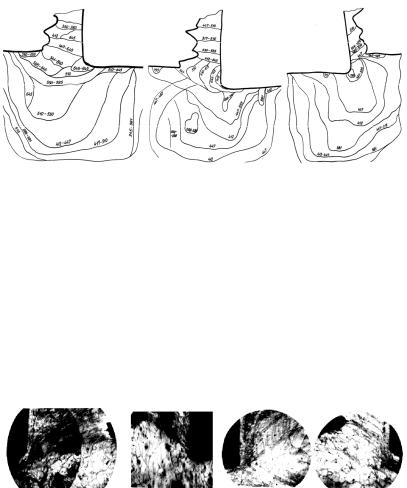
V = 8 м/мин |
V = 26 м/мин |
V = 40 м/мин |
Рис. 48. Распределение микротвердости в поверхностном слое образцов и корнях стружек из сплава ХН35ВТЮ-ВД, НВ 388…412 после протягивания на различных скоростях резания с подачей 0,06 мм/зуб протяжками
из твердого сплава ВК8
3. Электронно-микроскопическое исследование стружки и зоны резания: с помощью электронных и обычных микроскопов изучаются процессы изменения микроструктуры обработанной поверхности стружки. Например, на рис. 49 показана микроструктура поверхности металла после обработки на различных скоростях резания. При этом зона резания увеличилась более чем в 300 раз.
а |
б |
в |
г |
Рис. 49. Микрошлифы корней стружки при протягивании сплава ХН77ТЮР-ВД со скоростями резания, м/мин: а – 2; б – 8;
в – 26; г – 40 (Sz = 0,1 мм/зуб, шлифы протравлены, 300)
Наглядно видно изменение зерен металла перед зоной резания, в самой зоне резания и в обработанной поверхности вследствие мощной пластической деформации. Установлено, что с уве-
74
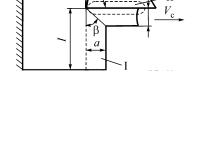
личением скорости резания величина пластической деформации существенно снижается.
4.Киносъемка (скоростная и замедленная) процесса резания.
5.Поляризационно-оптическое изучение напряжений зоны резания.
6.Рентгеноструктурный анализ зоны резания.
7.Метод координатной сетки.
2.1.3.Моделирование выхода режущего инструмента
из заготовки в процессе протягивания
Исходные данные (рис. 50): V – скорость резания; Vc – скорость перемещения стружки; a – толщина срезаемого слоя; a1 – толщина стружки; b – ширина срезаемого слоя (толщина образца); – угол сдвига; I – расстояние до выходного торца.
Условия резания при протягивании. Свойства об-
рабатываемых материалов:
b = 500…1200 МПа; модуль упругости Е = 210 000 МПа; коэффициент трения = 0,3.
Режимырезания: V = 0,5… 40 м/мин; Sz = 0,005… 0,3 мм/зуб.
Геометрия режущего клина инструмента: = –10°; 0°; +10°; = 3…8°; = 0…20°;
радиус округления = 0…0,02 мм.
Объекты исследования:
I – краевая зона обрабатываемой детали;
II – зона контакта стружки с инструментом; III – режущий клин инструмента.
Математическое моделирование деформации краевой зо-
ны детали. Приведем пример математического моделирования деформации краевой зоны детали при выходе инструмента из заготовки (рис. 51, 52). Обозначим: а – толщина срезаемого слоя;– угол сдвига; U – перемещение инструмента.
75
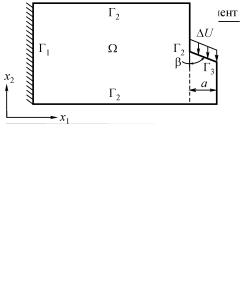
Рис. 51. Схема краевой зоны при выходе инструмента из заготовки
Рис. 52. Расчетная схема деформирования краевой зоны
Математические зависимости. Характеристики напряжен-
но-деформированного состояния (НДС):
U(r) – поля векторов перемещения точек тела; r – точка тела, заданная своим радиус-вектором;(r) – компоненты тензора деформации;
(r) – компоненты тензора напряжений; S(r) – степень деформации материала.
В образце реализуется плосконапряженное состояние:
33 = 13 = 23 = 13 = 23 = 0.
Придеформированиидолжнывыполнятьсяследующиеусловия:
– уравнение равновесия d ij r 0, r ;
– физические соотношения d ij r |
Сijmn r d mn r , |
r |
|
; |
|||||
|
|||||||||
– геометрические |
соотношения |
d ij r |
1 |
dUi, j r |
|||||
dU j, i r ; r |
|
|
|
|
2 |
|
|
|
|
|
; |
|
|
|
|
|
|
|
|
|
|
|
|
|
|
|
|
||
76 |
|
|
|
|
|
|
|
|
|
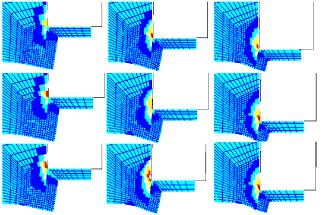
– граничные условия:
для точек левой стороны области
dU1 dU2 0, r 1;
для точек свободной поверхности dF1 dF2 0, r 2 ;
для точек, контактирующих с инструментом, dU2 U, dF1 0, r 3.
Результаты расчета изменения пластической деформации при выходе инструмента представлены на рис. 53.
I = 4 мм |
I = 3 мм |
I = 2 мм |
b = 50 + 300S
b = 50 + 200S
b = 50 + 100S
Рис. 53. Влияние модуля упрочнения материала на степень деформации краевой зоны детали
В результате проведенных расчетов при моделировании установлены закономерности и параметры деформации зоны сдвига с образованием заусенцев и разрушением режущих кромок инструмента. Предложены мероприятия по снижению неблагоприятного воздействия этого краевого эффекта. Решены проблемы повышения стойкости твердосплавных протяжек.
77
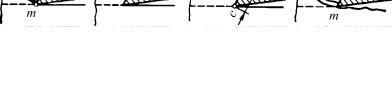
2.2.Процесс стружкообразования
2.2.1.Типы стружек при резании пластичных
ихрупких материалов
В1870 году И.А. Тиме была предложена классификация типов стружек, образующихся при резании различных материалов. Классификация оказалась настолько удачной, что, несмотря на то, что со времен И.А. Тиме появились совершенно новые конструкционные материалы, обрабатывающиеся с иными режимами резания, ею
пользуются и в настоящее время. Согласно классификации И.А. Тиме, при резании конструкционных материалов в любых условиях образуются четыре вида стружек: элементная, суставчатая, сливная и стружка надлома. Элементную, суставчатую и сливную стружку называют стружками сдвига, так как их образование связано с напряжениями сдвига при резании пластичных материалов. Стружку надлома иногда называют стружкой отрыва, так как ее образование связано с растягивающими напряжениями. Внешний вид всех перечисленных типов стружкиизображеннарис. 54.
a |
б |
в |
г |
Рис. 54. Типы стружек, образующихся при резании пластичных
ихрупких материалов: а – элементная; б – суставчатая;
в– сливная; г – стружка надлома
Элементная стружка (см. рис. 54, а) образуется при резании сталей высокой твердости с большой толщиной среза, низкой скоростью резания и малым передним углом и состоит из отдельных элементов 1 приблизительно одинаковой формы, несвязанных или слабо связанных друг с другом. Границу тп, отделяющую образовавшийся элемент стружки от срезаемого слоя, назы-
78
вают поверхностью скалывания. Физически она представляет собой поверхность, по которой в процессе резания периодически происходит разрушение срезаемого слоя.
У суставчатой стружки (см. рис. 54, б), которая образуется при резании сталей средней твердости, со средней толщиной среза, низкой скоростью резания и малым передним углом, разделения на отдельные части не происходит. Поверхность скалывания только наметилась, но она не пронизывает стружку по всей толщине. Поэтому стружка состоит как бы из отдельных суставов 1 без нарушения связи между ними.
Основным признаком сливной стружки (см. рис. 54, в), которая образуется при резании сталей невысокой твердости с повышенной скоростью резания и с большим передним углом, является ее сплошность (непрерывность). Если на пути движения сливной стружки нет никаких препятствий, то она сходит непрерывной лентой, завиваясь в плоскую или винтовую спираль, пока часть стружки не отламывается под действием собственного веса. Поверхность 1 стружки, прилегающую к передней поверхности инструмента, называют контактной стороной (поверхностью). Она сравнительно гладкая, а при высоких скоростях резания отполирована в результате трения о переднюю поверхность инструмента. Ее противоположную поверхность 2 называют свободной стороной (поверхностью) стружки. Она покрыта мелкими зазубринками-насечками и при высоких скоростях резания имеет бархатистый вид. Стружка соприкасается с передней поверхностью инструмента в пределах площадки контакта, ширина которой обозначена буквой с, а длина равна рабочей длине главного лезвия. В зависимости от рода и свойств обрабатываемого материала и скорости резания ширина площадки контакта в1,5…6 раз большетолщины срезаемого слоя.
Стружка надлома (см. рис. 54, г), которая образуется при резании хрупких материалов (например, чугуна, бронзы) при больших толщинах среза и малых скоростях резания, состоит из отдельных, не связанных друг с другом кусочков различной формы и размеров. Образование стружки надлома происходит путем вырывания частиц откалываниякрупных частиц неправильной формыили образования
79
мелкой металлической пыли. Поверхность разрушения тп может располагаться ниже поверхности резания, в результате чего последняя покрытаследамиот выломанных из нее кусочков стружки.
Тип стружки во многом зависит от рода и механических свойств обрабатываемого материала. При резании пластичных материалов возможно образование первых трех типов стружки: элементной, суставчатой и сливной. По мере увеличения твердости и прочности обрабатываемого материала сливная стружка переходит в суставчатую, а затем в элементную. При обработке хрупких материалов образуется или элементная стружка (чаще), или стружка надлома (реже). С повышением твердости материала, например чугуна, элементная стружка переходит в стружку надлома.
Из геометрических параметров инструмента наиболее сильно на тип стружки влияют передний угол и угол наклона главного лезвия. При обработке пластичных материалов влияние углов и принципиально одинаково: по мере их увеличения элементная стружка переходит в суставчатую, а затем в сливную. При резании хрупких материалов при больших передних углах может образовываться стружка надлома, которая по мере уменьшения переднего угла переходит в элементную. При увеличении угла наклона главного лезвия стружка постепенно превращаетсяв элементную.
На тип стружки оказывают влияние подача (толщина срезаемого слоя) и скорость резания. Глубина резания (ширина срезаемого слоя) на тип стружки практически не влияет. Увеличение подачи (толщины срезаемого слоя) приводит при резании пластичных материалов к последовательному переходу от сливной стружки к суставчатой и элементной. При резании хрупких материалов с увеличениемподачиэлементная стружкапереходитв стружку надлома.
Наиболее сложно на тип стружки влияет скорость резания. При резании большинства углеродистых и легированных конструкционных сталей, если исключить зону скоростей резания, при которых образуется нарост (о чем речь пойдет ниже), по мере увеличения скорости резания стружка из элементной становится суставчатой, а затем сливной. Однако при обработке некоторых жаропрочных сталей и сплавов, а также титановых сплавов повыше-
80