
книги / Резание материалов
..pdfния существенно облегчает практическое использование установленного закона.
Всесторонне обоснованное доказательство гипотезы о постоянстве оптимальной температуры резания превратило ее в закон, который составил основу нового направления в теории резания металлов – оптимизация процессов резания по физическим и технологическим параметрам.
Это направление проверено при проведении широкого комплекса научно-исследовательских работ на предприятии ОАО «Пермский моторный завод» совместно с ПНИПУ и внедрении процесса скоростного протягивания деталей газотурбинных двигателей на оптимальных скоростях резания твердосплавными протяжками. Скорости резания увеличились с 2 до 30 м/мин, т.е. в 15 раз, а стойкость протяжек повысилась более чем 10 раз. При этом значительно улучшилось качество и стабильность процесса, повысилась усталостная прочность деталей.
3.1.5. Основные методы изучения тепловых явлений
Температура резания может быть определена расчетными и экспериментальными методами.
Для аналитических расчетов тепловых потоков и темпе-
ратур применяются различные методы расчетов – метод источников теплоты, метод конечных разностей, метод конечных элементов.
Метод источников теплоты использует приближенное распределение теплоты по различным законам. Метод имеет много допущений с учетом мощности источников тепла и характеризуется большой сложностью расчетов. Метод конечных разностей основан на замене истинных значений производных, входящих в дифференциальные уравнения теплопроводности, приближенными значениями в определенных точках-узлах. Метод конечных элементов (МКЭ) сегодня наиболее распространен в связи с появлением различных компьютерных программ инженерных расчетов. Этот метод позволяет осуществлять раз-
191
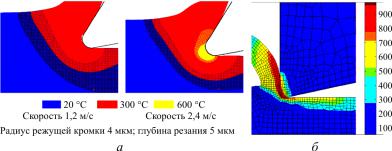
личную детализацию решения в различных областях изучаемого объекта. Разбиение на элементы здесь возможно с учетом геометрических параметров, физических свойств, соединением деталей из различных материалов. Примеры использования МКЭ при расчете температур резания и тепловых полей приведены на рис. 123.
Рис. 123. Результаты расчетов тепловых полей при сверлении (а) и при строгании (б) методом МКЭ
Расчетные (теоретические) методы весьма сложны, требуют применения компьютеров и не всегда точны. Это обусловлено тем, что реальные условия резания обычно схематизируют, в результате чего трехмерные источники и стоки теплоты заменяют на двух- и одномерные, упрощают начальные и граничные условия и т.д. Несмотря на значительные успехи, достигнутые в использовании аналитических методов для изучения тепловых явлений в зоне деформации и на контактных поверхностях инструмента, экспериментальные методы благодаря их надежности и простоте являются главным инструментом исследования.
Экспериментальные методы можно разбить на две группы:
косвенные и непосредственные.
Перечислим косвенные методы:
1. Метод цветов побежалости. Несмотря на свою простоту этот метод дает значительные погрешности, связанные с тем, что определяется только температура окисленной поверхности
192
стружки. К примеру, при резании с обильным охлаждением цвета побежалости исчезают, в то время как температура в месте контакта стружки с инструментом очень высока.
2.Метод термокрасок. Для выявления температуры пользуются свойством специальных красок менять цвет при определенных температурах. Например, при 155 °С цвет из пурпурного переходит в голубой, при 190 °С из белого – в зеленокоричневый, при 255 °С из зеленого – в темно-коричневый, при 305 °С из желтого – в красно-коричневый, при 440 °С из фиолетового – в белый. При использовании этого метода краска смешивается с алкоголем и наносится ровным слоем на грани исследуемых резцов. Некоторая погрешность в данном случае заключается в том, что оттенок переходящих красок меняется в зависимости от продолжительности действия тепла. Этот метод применяется для определения температуры на поверхностях инструмента. Специальную термочувствительную краску наносят тонким слоем на поверхность инструмента. Тепло на поверхностях инструмента изменяет цвет краски. Определенная шкала «цвет–температура» позволяет определить температуру поверхности инструмента. Недостаток метода: при продолжительной работе оттенки краски изменяются и не соответствуют шкале.
3.Метод микроструктурного анализа. Основан на изменениях, которые происходят в поверхностных слоях инструмента вследствие воздействия на них тепла, возникающего в процессе резания. Предложенный ранее способ измерения температуры
впроцессе резания путем анализа микроструктуры тончайшего слоя обработанной поверхности, претерпевающей заметные изменения при достаточно большом нагреве, пока не получил распространения, так как его можно использовать только при высоких режимах резания, когда поверхность резания или обработанная поверхность нагревается выше критических точек.
4.Калориметрический метод. Данным методом определяется распределение тепла между стружкой, инструментом и обрабатываемой деталью, а также средняя температура стружки и инструмента с использованием специального калориметра.
193
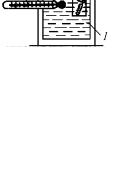
На рис. 124 изображена схема постановки опыта при определении количества тепла Q, переходящего при точении в стружку и резец, и их средних температур θ. Внизу, перед передней поверхностью резца установлен калориметр 1 с сеткой 2 для сбора стружки и ртутным термометром 3. Для обеспечения лучшего попадания струж-
Рис. 124. Применение калориметра ки в калориметр резание про- для определения количества тепла, изводят при левом вращении переходящего в стружку, и ее шпинделя. Среднюю темпера-
средней температуры туру стружки или резца можно определить по формуле
θ = θсм + Gв(θсм – θв)/сG,
где θсм – температура смеси (воды в калориметре после резания), град; Gв – масса воды в калориметре, г; θв – начальная температура воды в калориметре, град; G – масса стружки или резца, г; с – теплоемкость стружки или резца, кал.
Количество тепла, перешедшего в стружку и резец, определяют по формуле
Q = (cг – снθн)G,
где сг – теплоемкость горячей стружки или резца, кал; сн – теплоемкость ненагретой стружки или резца, кал; θн – начальная температура стружки или резца.
Непосредственные методы измерения температуры являются более точными, так как позволяют получить результаты, более близкие к действительным. К непосредственным методам относятся следующие:
1. Метод искусственной термопары Я.Г. Усачева (1914). Недостаток метода в том, что нельзя близко подойти к передней или
194
задней поверхности. А самый большой интерес представляет температура на контактных поверхностях.
2.Метод полуискусственной термопары Я.Г. Усачева (1914– 1916). Проволока термопары изолирована от резца и контактирует лишь в месте расклепки.
3.Метод естественной термопары. При этом необходимо:
иметь в виду, что снятие термоэлектродвижущей силы (ТЭДС) с вращающейся заготовки происходит с использованием токосъемника;
применять цельные резцы;
проводить тщательную тарировку.
4.Метод двух резцов. Разнородные материалы резцов образуют термопару (но этот метод неудобен).
5.Оптический метод. Используется при скоростной обработке с применением пирометров.
6.Радиационный метод. Основан на измерении теплоты лучеиспускания, но имеетряднедостаткови поэтому малоприменим.
7.Метод бегущей термопары (точен, но трудоемок). Этот метод позволяет одновременно измерять температуры на контактных площадках резец–стружка и резец–деталь. Резец перерезает защитную трубку, и проводники термопары образуют горячие спаи двух искусственных термопар. Контакты выводят на соответствующие приборы.
Наиболее распространен в настоящее время метод естественной термопары. Для определения температуры строится тарировочный график на основе тарировки резец–деталь.
Определить температуру резания можно и аналитически при помощи теоретических формул. Однако эти формулы являются, как правило, приблизительными из-за ряда допущений.
Основными объектами изучения являются: а) количество выделяемого при резании тепла и его распределение между стружкой, деталью и инструментом; б) температура, устанавливающаяся на контактных поверхностях инструмента; в) температурные поля в зоне деформации и режущем клине инструмента.
195
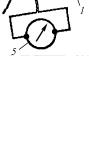
Метод термопар. Для измерения средней температуры на контактных поверхностях инструмента и в различных точках контактных площадок применяют разнообразные термопары. На рис. 125 изображен метод искусственной термопары, предло-
женный Я.Г. Усачевым. Резец, применяемый в опытах, представляет собой корпус, к которому прижата режущая пластинка 2 из
|
быстрорежущей |
стали |
или |
|
твердого сплава. В корпусе |
||
|
сделано отверстие, в которое |
||
|
вставлена изоляционная труб- |
||
|
ка 3. Стандартная термопара 4 |
||
|
(медь–константан, хромель– |
||
|
алюмель и др.) с гальваномет- |
||
|
ром 5, подключенным к ее |
||
|
концам, вставлена в изоляци- |
||
|
онную трубку так, что ее спай |
||
Рис. 125. Измерение температуры |
касается нижней |
плоскости |
|
передней поверхности |
пластинки 2. Спай термопары |
||
искусственной термопарой |
регистрирует |
температуру |
|
|
опорной плоскости пластинки. |
||
Большим достоинством метода является возможность |
ис- |
пользования стандартных термопар с известными термоэлектрическими характеристиками, а потому не нуждающихся в специальной тарировке. Располагая отверстия в различных точках передней и задней поверхностей, можно составить представление о температурном поле в режущем клине инструмента.
Однако методу присущи и серьезные недостатки, ограничивающие область его применения. Измеряемая термопарой температура ниже температуры на контактных поверхностях инструмента, и разность температур зависит от расстояния спая термопары от указанных поверхностей, увеличиваясь при увеличении толщины режущей пластинки.
Практически не удается достигнуть толщины пластинки менее 1,5…2,0 мм, а поэтому из-за большого градиента температур измеряемая температура на 50…80° ниже действительной. При
196
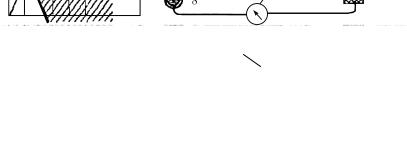
долговременном резании вследствие износа передней и задней поверхностей инструмента расстояние между спаем термопары и контактными поверхностями сокращается, что приводит к возрастанию температуры. Наконец, метод искусственной термопары трудно использовать при вращающемся инструменте.
Более простым и совершенным является метод естественной термопары, предложенный Е. Гербертом и К. Готвейном. Метод основан на том, что в процессе резания (рис. 126, а) в месте соприкосновения передней поверхности инструмента со стружкой и задней поверхности с поверхностью резания естественным путем создаются термопары, электродами которых являются материал обрабатываемой детали и материал режущей части инструмента. Величина электродвижущей силы и направление термотока зависят от вида инструментального и обрабатываемого материалов, образующих термопару.
а |
б |
Рис. 126. Естественная термопара (а) и схема измерения температуры резания естественной термопарой (б)
Если обрабатываемую деталь и инструмент включить в замкнутую электрическую цепь, то величина термоэлектродвижущей силы, возникающей в термоэлементе, будет пропорциональна температуре скользящего «спая» образовавшейся термопары. Методом естественной термопары измеряют не максимальную, а некоторую среднюю контактную температуру на передней и задней поверхностях инструмента. Например, при обработке углеродистой стали инструмент является положительным элек-
197
тродом, если он изготовлен из быстрорежущей стали, и отрицательным, если он из твердого сплава.
Схема измерения температуры при точении методом естественной термопары изображена на рис. 126, б. Обрабатываемая заготовка 1 изолирована от патрона 3 и центра задней бабки эбонитовыми прокладками и пробкой 5. Цельный резец 2 из быстрорежущей стали или твердого сплава изолирован от резцедержателя эбонитовыми прокладками. Резец делают цельным для того, чтобы
вместе приваривания или припаивания режущей пластинки к корпусу резца не образовались паразитные термопары. Заготовка медным проводником 10 соединена с гибким валом 6, закрепленным
вэбонитовой втулке, установленной на конце шпинделя станка 4. Контактный наконечник 7 гибкого вала опущен в ванночку со ртутью 8. Милливольтметр 9 одной клеммой соединен с торцом резца, а вторым – с ртутным токосъемником. Замкнутая электрическая цепь состоит из заготовки, проводника, гибкого вала, токосъемника, милливольтметра, резца, заготовки. Заготовку изолируют от станка для устранения влияния паразитных термопар, могущих возникнуть между отдельными деталями станка. Однако роль паразитных термопар при высокой температуре контактных поверхностей инструмента незначительна, и за счет некоторого снижения точности измерения установку можно упростить, отказавшись от изоляции заготовки, сохранив изоляцию только резца.
Достоинством метода естественной термопары является то, что его легко осуществить не только при точении, но и при сверлении, нарезании резьбы метчиком, строгании, фрезеровании, протягивании и других видах работ. Для перевода показаний миливольтметра в градусы Цельсия естественная термопара должна
быть предварительно подвергнута специальной тарировке. В электропечь помещают тигель с расплавленным металлом, имеющим низкую температуру плавления: свинцом, оловом, сурьмой, сплавом Вуда и т.п.; стержни из обрабатываемого и инструментального материалов опускают на одинаковую глубину в расплавленный металл, а к их концам присоединяют милливольтметр, применяемый в опытах по измерению температуры при резании. Между стержнями помещают контрольную термо-
198
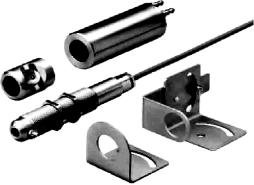
пару, гальванометр которой проградуирован в градусах. Нагревая и охлаждая расплавленный металл, сравнивают показания милливольтметра в милливольтах и гальванометра в градусах и строят тарировочный график мВ – °С.
Большим неудобством при применении метода естественной термопары является необходимость новой тарировки термопары при изменении материалов детали или инструмента.
Оптический и радиационный методы. Оптические пиромет-
ры для измерения температуры резания применяются при скоростной обработке металла, когда стружка и резец нагреваются весьма сильно вплоть до светлого каления. Однако опыт использования этого метода недостаточен, чтобы можно было делать определенные выводы.
Стационарный инфракрасный пирометр применяется для бесконтактного измерения температуры неметаллических или окрашенных (анодированных) металлических объектов или металлических объектов с покрытием в диапазоне от0 до 500 °С (рис. 127).
Рис. 127. Инфракрасный бесконтактный пирометр IN 3000
Данный пирометр имеет фиксированную установку коэффициента излучения 95 % и оптическое соотношение (соотношение расстояния до объекта контроля и диаметра области измерения) 5:1. Эти характеристики в сочетании с временем отклика 300 мс позволяют решать различные задачи измерения (рис. 128).
199
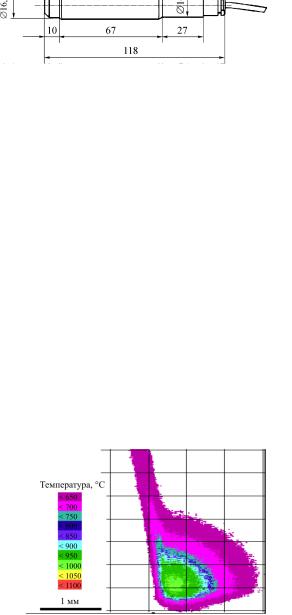
а
б
Рис. 128. Схема инфракрасного пирометра (а) и параметры измеряемого объекта (б)
Упрочненная конструкция пирометра гарантирует высокую безопасность даже в неблагоприятных промышленных условиях. Также имеется версия пирометра IN 3000 со встроенным блоком воздушной продувки. На рис. 129 представлен фрагмент результатов измерения температуры резца с помощью пирометра.
Рис. 129. Результаты измерения температуры токарного резца с помощью пирометра
200