
книги / Электронно-лучевая сварка и смежные технологии
..pdfпроцессы технологические
1
Uуск’
55Х2Н2МФА, 28 18Х2Н4МА, 40Х2Н2МА
Инструмен тальная сталь X32CrMoV33 (0,32%С; 0,34%Si; 0,42%Мп; 2,82%Сг; 2 ,6%Мо)
3 |
4 |
5 |
|
6 |
|
|
,8-3,0 |
(0,8—20)-1 О4 Скрытоигольчатый |
|
8,8-11,8 ГПа, |
|
|
|
|
пакетный |
мартенсит, |
|
67-69 HRC3 (зона |
|
|
|
центральная зона с |
|
скрытоигольчатого |
|
||
|
нормально |
|
мартенсита). |
|
|
|
|
направленными |
|
Микротвердость сталей |
|
||
|
к поверхности |
|
возросла на 37-100%. |
|
||
|
дендритами |
|
|
|
|
|
|
и переходная зона. |
|
|
|
|
|
|
Ширина вторичных |
|
|
|
|
|
|
ветвей дендритов |
|
|
|
|
|
|
уменьшилась |
|
|
|
|
|
|
с 2,5-3,7 |
|
|
|
|
|
|
до 1,25-1,5 мкм |
|
|
|
|
|
|
Дендритная структура |
|
750 HV. Испытания на |
|
||
|
высокой дисперсности |
и |
изгиб обнаружили |
|
||
|
мартенсит. Остаточный |
повышенные вязкие |
|
|||
|
аустенит отсутствует. |
|
свойства. Выдержка при |
Продолжение |
||
|
Дендритная сетка |
|
520 °С в течение |
|||
|
ферритной |
структуры |
V, |
1 ч привела к падению |
|
|
|
насыщена карбидами |
твердости на |
|
|
||
|
Мо, Сг |
|
|
50-70 HV, |
|
|
|
|
|
|
а при 600 “ С — на |
.табл |
|
|
|
|
|
150-200 HV, что |
||
|
|
|
|
свидетельствует |
|
|
|
|
|
|
о повышенной |
стали. |
37 |
|
|
|
|
теплостойкости |
|
еСмежны
Таблица 38. Характеристики электронно-лучевого оплавления с получением аморфного и стеклообразного строения
Сплав, хи м и ч е с к и й |
|
Парам етры |
н а грев а |
|
|
со став |
|
|
|
|
|
U ?{|, и В |
1п, мА |
t, с |
Стали |
А 1S 1 1 0 4 5, |
60 |
10 -2 1 5 |
- |
415 0, |
1090 |
|
|
|
89 .5 |
а т .% С г , |
80 |
30 |
|
10.5 |
Та, |
|
|
|
( 7 8 , 2 - 8 1 % )С г ,
( 1 5 , 1 - 8 , 9 ) % Z г , (6 ,7 - 10,1) % G е
|
Глубина |
Тверд ост ь |
||
|
аморфного |
оп лав ле нной |
||
V , м м /с |
слоя, |
зоны |
||
ск орость |
|
|
||
|
охлаж ден ия |
|
|
|
260 |
3 0 |
м к м , |
67 -7 0 |
HRC, |
|
>107 |
* С/ с |
(1100 |
HR С,) |
1200 |
1200 |
|
|
О с о б е н ности м и к р о стр ук ту ры
-
В ис хо дн ом сос тоя нии э в т е к т и ч е с к и е фазы а -С г ,
P ' - C r j a , о - С т , Р' - С г *Т a ;
пл а стин ч ат ая
ми к р о с т р у к т у р а после оп л а в л е н и я ,
од н ород но е стр оен ие
A I 7 Q S i1 7 F e 1 3 |
25 |
1 0 0 - 5 0 0 |
Ф орм и р о в а н и е |
|
|
|
сф е р и ч е ск и х |
|
|
|
част иц |
|
|
|
0,5 мкм |
|
|
|
аморфной фазы |
Fe61Cr24B9ClNi3Mo2, |
130 |
( 8 - 4 0) 10 - 6 |
2 0 - 3 0 мкм |
F e 7 0 C r 1 0 P 1 3 C 7 , |
|
|
|
F e 8 1 S i4 B 1 3 C 2 ,
F e 4 0 N i4 0 S i1 0 B 1 0
Нежелательным представляется образование столбчатой струк туры в перекристаллизованной приповерхностной зоне образцов и деталей. Поскольку столбчатая структура формируется при боль ших значениях плотности вложенной энергии и значительном чис ле импульсов (ws=5 Д ж /см 2; л=40), то для модификации титановых сплавов можно рекомендовать более мягкие режимы обработки (ws= 2 ...3 Д ж /см 2) при сохранении большого числа импульсов. Фор мирование в поверхностном слое после облучения остаточных ра стягивающих напряжений должно приводить к понижению уровня служебных характеристик изделий (усталостной прочности, эрози онной стойкости, жаростойкости и др.). Следовательно, для повы шения значений этих рабочих характеристик необходима финиш ная термообработка (стабилизирующий вакуумный отжиг) облучен ных образцов и изделий. Такая термообработка может быть легко реализована при использовании стандартных вакуумных печей. В результате исследования влияния финишной термообработки на физико-химическое состояние поверхностных слоев мишеней было установлено:
■химический состав в приповерхностных областях при отжи ге практически не изменяется;
■в процессе термообработки в приповерхностной зоне тол щиной примерно 10 мкм происходит почти полный распад а "-ф а зы с образованием a-фазы и небольшого количества (3-фазы, а также аннигиляция дефектов кристаллической ре
шетки (резко снижается полуширина рентгеновских линий)
и релаксация остаточных растягивающих напряжений;
■значения микротвердости поверхностных слоев облученных образцов после отжига несколько превышают величины, ха рактерные для образцов в исходном состоянии.
Усталостные испытания образцов из сплава ВТ18У показали, что с помощью электронно-лучевого облучения удается повысить их циклическую долговечность как минимум на порядок.
Полученные результаты свидетельствуют о перспективности модификации поверхностных слоев деталей из жаропрочных титано вых сплавов импульсным электронным пучком с целью повышения их эксплуатационных свойств. Технологии импульсного электрон но-лучевого облучения могут быть использованы в авиационной, газодобывающей, судостроительной промышленности, а также медицинской технике.
Комбинированные технологии модифицирования поверх ности. В последние годы активно развивают технологии модифи-
технологические процессы |
223 |
цирования поверхности второго поколения [106]. На поверхность металла наносят одноили многослойные покрытия (толщиной 0,01-5 мм) дуговыми или плазменными методами напыления либо наплавкой, а затем покрытия модифицируют под воздействием электронного пучка. Электронно-лучевая обработка изменяет структуру и свойства покрытий: происходит рекристаллизация, уменьшается пористость и количество микронеоднородностей. В ре зультате возрастает твердость и износостойкость покрытий, также их адгезия с основным металлом. Например, износостойкость хро мовых покрытий на титановом сплаве ВТЗ-1 после электронно лучевой обработки увеличивается в 10 раз.
Эффект формообразования при электронно-лучевом оплав
лении. При оплавлении электронным пучком боковой поверхнос ти быстро вращающегося цилиндра экспериментально обнаруже но образование шестеренчатой формы [26].
Образцы из стали различных марок в форме цилиндра с радиу сом 1-3 см и длиной 5 -10 см закрепляли в горизонтальном поло жении в вакуумной камере и приводили во вращение с частотой 5000-10000 об/мин. Затем образцы нагревали электронным пуч ком, падающим на верхнюю образующую цилиндра и перемеща ющимся вдоль этой образующей со скоростью 5 мм/с. Парамет ры электронного пучка следующие: ускоряющее напряжение 40 кВ, сила тока пучка70-80 мА, эффективный радиус пучка г =0,1... 1 мм.
Поскольку теплоотвод с образца был ограничен, быстро проис ходил процесс теплонасыщения, после чего поверхность цилинд ра оплавлялась. Ввиду быс трого вращения образца ис точник теплоты распределя ется по кольцу эффективной ширины ДН=2гэф. Поэтому расплавленная область так ж е имела форму кольца, пе ремещающегося по поверх ности цилиндра вм есте с
пучком (рис. 100).
На переплавленной боко вой поверхности цилиндра было зафиксировано образо вание характерной структуры: на поверхности появлялось л зубьев (л= 15...35), высота
224 |
Смежные |
которых достигала 1/5 радиуса цилиндра, из-за чего образец прини мал вид шестерни (рис. 101).
Неровность внешнего края была намного меньше высоты зу бьев. Количество зубьев в образцах изменяли, но в пределах од ного эксперимента оно оставалось постоянным. В процессе сме щения кольцеобразной жидкой фазы нарастающие за ней зубья образовывали ребра, вытянутые вдоль образующей цилиндра (или слегка отклоняющиеся от нее по винтовой линии).
Были сделаны попытки управлять количеством зубьев с помо щью нанесения равноотстоящих рисок вдоль образующих цилин дра (риски в сечении имели форму квадрата 1 х1 мм). Количество зубьев совпало с количеством рисок, а сами зубья располагались строго посередине между рисок.
Описанные эксперименты открывают возможность целенаправ ленного изменения формы поверхности цилиндра путем ее локаль ного переплава.
Области и перспективы применения. Электронно-лучевое модифицирование поверхностей является перспективным техноло гическим процессом, освоение которого в промышленных масшта бах еще продолжается. Основа для более широкого его примене ния — глубокие лабораторные исследования, хорошие результаты опытно-промышленных испытаний, высвобождающееся на многих предприятиях оборудование для электронно-лучевой сварки. Кро ме того, электронно-лучевое модифицирование поверхностей для многих практических задач имеет решающие преимущества по сравнению с другими методами модифицирования (лазерное, ионное, ТВЧ и др.), такие как большая глубина модифицирова ния, вакуумная защита обрабатываемой поверхности, более высокая
технологические процессы |
225 |
производительность процесса, лучшие характеристики модифи цированного поверхностного слоя. В первую очередь электрон но-лучевое модифицирование поверхностей будет развиваться
вавтомобилестроении, производстве сельскохозяйственной тех ники и машин для переработки сельскохозяйственной продукции,
винструментальной и легкой промышленности, в турбостроении. Во многих случаях электронно-лучевое модифицирование зам е нит технологические процессы нанесения упрочняющих покры тий, несмотря на их сравнительную невысокую стоимость. М ож но также отметить успешное применение электронно-лучевого модифицирования при обработке оптических стекол.
Оборудование для электронно-лучевой обработки
Для реализации технологических процессов электронно-луче вой обработки поверхностей металлов используют как специали зированное оборудование [50, 63, 74], так и установки для элек тронно-лучевой сварки с небольшой модернизацией. Модерниза ция сварочных установок заключается в следующем:
■в электронной пушке либо на ее нижнем торце устанавли вают малоиндуктивную отклоняющую систему;
■систему управления отклонением электронного пучка заме няют на специализированную (быстродействующую, с про граммным управлением);
■манипулятор изделия или электронной пушки, а также его систему управления дорабатывают или заменяют для обес
печения высоких скоростей перемещения (до 40 мм/с). Для автоматического управления электронно-лучевыми технологи
ческими процессами локальной термообработки, поверхностной за калки и пайки изделий, программного управления параметрами элек тронно-лучевой сварочной аппаратуры предназначена система управ ления «ПУЛЬСАР» (ООО «Техномашприбор», Львов, Украина).
Система управления создана на базе персонального ком пью тера класса Pentium с минимальным объемом ОЗУ 32 Мб.
В состав системы управления кроме персонального ком пью тера входит: плата вывода аналоговых сигналов (L-1208); плата ввода-вывода дискретных и числоимпульсных сигналов (D IO -64); плата ввода аналоговых сигналов (L-154); датчики температуры (до 8 шт.); катушка динамической развертки электронного пучка; система быстродействующей развертки электронного пучка.
Система управления обеспечивает:
■развертку электронного пучка в двух координатах;
226 |
Смежные |
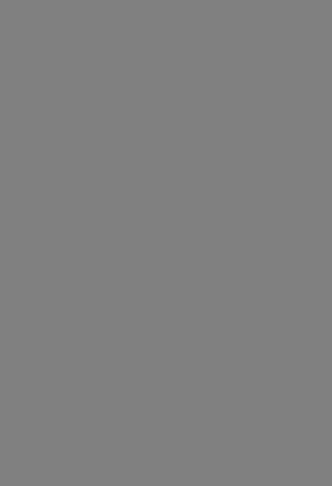
вод 3 выполнен из термостойкого неметаллического пресс-матери ала АГ-4В. Питание отклоняющей системы ОЛ138 осуществляет ге нератор развертки СУ225. Параметры отклоняющей системы при ведены ниже.
Техническаяхарактеристика отклоняющей системы ОЛ138:
Максимальный угол отклонения |
|
электронного пучка,...° ............................................ |
45 |
Максимальная частота колебаний |
|
тока треугольной формы, Г ц .................................... |
10000 |
Сопротивление постоянному |
|
току отклоняющей катушки, Ом |
|
по координате: |
|
X ................................................................................... |
12,75±1,10 |
Y ............................................................................... |
Не более 3,5 |
Индуктивность отклоняющей |
|
катушки по координате, м Г: |
|
X ................................................................................... |
Не более 20 |
Y ............................................................................... |
3,00±0,15 |
Удельная энергия отклонения |
|
для катушки по координате Y, м кД ж /к В .............. |
92-138 |
Чувствительность катушки |
|
по координате X, А, не м енее .................................. |
1,05 |
Минимальный диаметр |
|
лучепровода, м м ......................................................... |
28 |
Масса, к г ......................................................................... |
3,5 |
Для измерения параметров температурного поля можно также использовать пирометрические системы, позволяющие осуществ лять контроль бесконтактно, через иллюминатор вакуумной кам е ры (см., например, [69]).
Электронно-лучевая наплавка
Известные методы порошкового напыления и наплавки (дуго вая, электрошлаковая, плазменная) имеют множество недостатков: трудности контроля и регулирования режимов нанесения покры тий, поводка и коробление детали, недостаточная прочность сцеп ления покрытий и основы.
Большинство перечисленных недостатков лишен метод элект ронно-лучевой наплавки (ЭЛН) в вакууме. Он более экономичен,
228 |
Смежные |
так как не требует применения инертного газа, при расплавлении в вакууме происходит рафинирование основы и наплавляемого по рошка от газовых примесей. Размер жидкометаллической ванны может быть очень мал, быстрая ее кристаллизация и последую щее охлаждение дает мелкую однородную структуру с высокой твердостью и износостойкостью.
В табл. 39 [75] приведены свойства покрытий из самофлюсующихся порошков на основе никеля и порошка высокохромистого чугуна, наплавленных методом ЭЛН. Показатель наплавляемости порошков означает способность порошка усваиваться .ванной расплавленного металла без газовыделения и при минимальном проплавлении основы. Покрытия после ЭЛН имеют твердость при мерно на 5 единиц выше твердости, получаемой при газотерми ческом методе нанесения покрытий. Пористость ЭЛН-покрытий невелика и в 4 -7 раз меньше пористости, получаемой при напыле нии с последующим оплавлением. Граница покрытие-основа без дефектна и практически неразличима на нетравленых шлифах.
Композиционные порошки как присадочный материал для на плавки получают спеканием в вакууме механических смесей кар бида титана с порошками металлов и сплавов, дроблением спеков и россевом на фракции. В качестве компонентов для приго товления смесей можно использовать СВС-карбид титана марки КП Т -7 производства Закарпатского опытно-металлургического за-
Таблица 39. Свойства покрытий, наплавленных промышленными порошками
М арка порошка |
Наплавляемость |
Пористость, |
Твердость, HRCg |
|
|
|
% |
наплавление |
ЭЛН |
|
|
|
||
|
|
|
с |
|
|
|
|
оплавлением |
|
|
|
|
(ТУ |
|
|
|
|
поставщика) |
|
П Г -1 0Н -01 |
Отличная |
1,0 |
56 -6 3 |
63±1 |
П Г -1 2Н -01 |
« |
0,7 |
3 6 -4 5 |
45±1 |
П Г -1 2 Н -0 3 |
« |
1,4 |
55 -6 2 |
62±1 |
П Р -Н 80Х13С 2Р |
«< |
0,2 |
2 5 -4 5 |
40±1 |
ПР-Н73Х16СЗРЗ |
« |
0,4 |
4 5 -5 0 |
53±2 |
П Г -У С 25 |
« |
0,3 |
55 -5 6 |
59±1 |
технологические процессы |
229 |
Таблица 40. Свойства покрытий, полученных эл ектронно-лучевой
наплавкой композиционных порошнов
Шустовой состав |
Элементный состав Me-связки, масс. % |
Напла |
Порис |
Твер |
||||||||
|
|
|
|
|
|
|
|
|
вляв- |
|
тость, |
дость, |
|
с |
Fe |
Ni |
Сг |
Si |
В |
W |
Мо |
мость |
% |
HRC3 |
|
42%ПС+42% |
0,65 |
28 |
50 |
13 |
3 |
2,4 |
1,7 |
1,3 |
Удовлетво |
2,8 |
53±1 |
|
ПГ-Ю Н -01+16% |
|
|
|
|
|
|
|
|
рительная |
|
|
|
Р6М5 |
|
|
|
|
|
|
|
|
|
|
|
|
35% TiC+65% |
5 |
55 |
- |
40 |
- |
~ |
- |
- |
Отличная |
1,9 |
65±3 |
|
ПГ-УС25 |
|
|
|
|
|
|
|
|
|
|
|
|
42% TiC+29% |
2,6 |
28,4 |
40 |
29 |
|
|
|
|
Удовлетво |
1,4 |
53±1 |
|
ПХ20Н80+29% |
|
|
|
|
|
|
|
|
рительная |
|
|
|
ПГ-УС25 |
|
|
|
|
|
|
|
|
|
|
|
|
42% |
4,5 |
27,5 |
40 |
28 |
|
|
|
|
|
|
3,1 |
58±1 |
Ti С+29%ПХ20Н8СЧ- |
|
|
|
|
|
|
|
|
|
|
|
|
+27,8% ПГ-УС |
|
|
|
|
|
|
|
|
|
|
|
|
25+1,2% С |
|
|
|
|
|
|
|
|
|
|
|
|
50%*ПС+5% |
0,9 |
Ост. |
40 |
2 |
|
— |
5,4 |
4,4 |
« |
« |
3,4 |
53±1 |
ПХ20Н80+45% |
|
|
|
|
|
|
|
|
|
|
|
|
Р6М5 |
|
|
|
|
|
|
|
|
|
|
|
|
50% TiC+50% |
1,1 |
Ост. |
— |
- |
- |
- |
6,0 |
5,0 |
« |
« |
1,1 |
65±2 |
Р6М5 |
|
|
|
|
|
|
|
|
|
|
|
|
35% TiC+7,5% |
1,3 |
75 |
9 |
6,3 |
|
|
4,6 |
3,8 |
Хорошая |
1.1 |
62±1 |
|
ПХ20Н80+6,5% |
|
|
|
|
|
|
|
|
|
|
|
|
ПГ-УС25+50% |
|
|
|
|
|
|
|
|
|
|
|
|
Р6М5+1,0%С |
|
|
|
|
|
|
|
|
|
|
|
|
вода (Украина) по ТУ 48-056003-89, а также промышленные по рошки производства Торезского завода наплавочных твердых спла вов (Украина) и объединения «Тулачермет» (Российская Федера ция), а такж е промышленные порош ки сплавов П Г -1 0 Н -0 1 , ПХ20Н80, ПГ-УС25, Р6М5, Царамам-А. Суммарный химический состав порошковых смесей выбирают из условий высокой ж идкотекучести металлического расплава и хорошей смачивемости им карбида титана. В табл. 40 [75] приведены свойства ЭЛН -покры - тий, наплавленных композиционными порошками на основе титана. Как видно, при правильном подборе химического состава металли ческой матрицы удается получить покрытия с малой пористостью и высокой твердостью. Твердость покрытий можно регулировать, из меняя содержание карбида титана и химический состав металличес кой матрицы. Для некоторых составов возможно повышение твердо сти и прочности покрытия его термической обработкой.
230 |
Смежные |