
11059
.pdf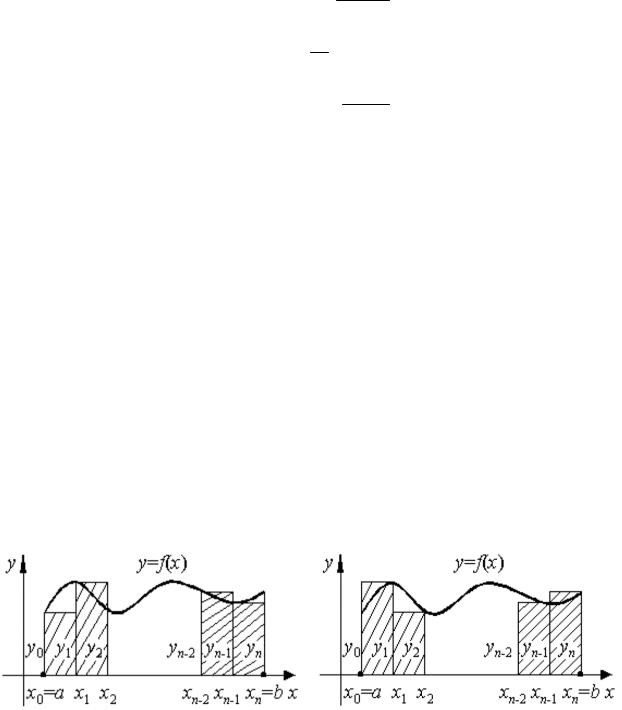
диаграмм деформирования материалов при разных типах нагружения экспериментальных образцов [1, 7-10]. Принцип действия РСГ заключается в определении напряжений и деформаций образца, размещаемого в месте разделения стержня, по данным, регистрируемым на некотором расстоянии от него. Формулы для определения механических характеристик испытываемого материала: напряжения σs(t), деформации εs(t), скорости деформации έs(t) и поглощаемой энергии Es(εs) по импульсам деформации мерных стержней (нагружающий εI(t), отраженный εR(t), прошедший εT(t)), которые регистрируются в эксперименте с помощью осциллографа, имеют следующий вид:
σs (t)= EAεT (t)
As
t
ε s (t )= − 2c и ε R (t )dt Ls 0
ε&s (t)= − 2cε R (t)
Ls
εи
E s (ε s ) = σ s (ε s )dε s
0
, |
(1) |
, |
(2) |
, |
(3) |
, |
(4) |
где Е, А и с – соответственно модуль Юнга, площадь поперечного сечения и скорость звука в мерных стержнях, As и Ls – соответственно площадь сечения и длина образца, tи – длительность испытания, в процессе которого была достигнута деформация εи.
Таким образом, одним из этапов обработки экспериментальных данных является интегрирование функций, заданных таблично. Эта задача усложняется тем, что указанные функции (прошедший импульс от времени или напряжение от деформации) могут иметь не постоянный шаг по оси абсцисс. Для решения задачи могут быть использованы имеющиеся методы численного интегрирования, большая часть которых основана на замене подынтегральной функции известной функцией, интеграл от которой легко вычисляется аналитически. Замену подынтегральной функции осуществляют полиномом нулевой, первой и второй степени, получая при этом методы прямоугольников, трапеций и парабол (Симпсона) соответственно (рис. 1) [11].
а |
б |
140
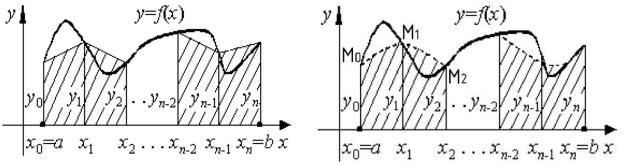
в г Рис. 1. Геометрическая иллюстрация методов численного интегрирования: левых
прямоугольников (а), правых прямоугольников (б), трапеций (в), парабол (г)
Метод прямоугольников заключается в замене подынтегральной функции на каждом элементарном отрезке значений аргумента константой и вычислении площади на основании суммирования площадей определенного числа прямоугольников, одна сторона которых будет определяться расстоянием между соответствующими соседними узлами интегрирования на оси абсцисс, а высота – значением подынтегральной функции в этих узлах. В случае выбора в качестве высоты прямоугольника значения функции в левом конце элементарного отрезка метод называют методом левых прямоугольников (рис. 1а, формула 5), а в случае выбора значения функции в правом конце – методом правых прямоугольников (рис. 1б, формула 6).
xn |
n −1 |
|
(xi +1 |
- xi ) |
|
y(x)dx = yi |
(5) |
||||
x0 |
i =0 |
|
|
, |
|
|
|
|
|
||
xn |
n −1 |
(xi +1 |
- xi ) |
|
|
y (x )dx = yi +1 |
(6) |
||||
x0 |
i =0 |
|
|
, |
|
|
|
|
|
где n – количество таблично заданных (зарегистрированных) значений интегрируемой функции.
Метод трапеций (рис. 1в) заключается в замене подынтегральной функции на каждом элементарном отрезке горизонтальной оси линейной функцией, а искомая площадь представляет собой сумму площадей прямоугольных трапеций, которые вычисляются как произведение полусуммы значений функции в крайних точках отрезка (полусумма оснований трапеции) на длину отрезка интегрирования (высота трапеции):
xn |
n −1 |
|
y |
i +1 |
+ y |
|
|
|
|
|
|
|
i |
|
|
|
|
||||||
y(x )dx = |
|
|
|
× (xi +1 |
- xi |
) |
|
|
|||
|
|
2 |
|
|
|
||||||
x0 |
i =0 |
|
|
|
|
|
|
|
. |
(7) |
|
|
|
|
|
|
|
|
|
|
|
||
Суть метода Симпсона (рис. 1г) состоит в приближении графика |
|||||||||||
функции на определенном |
интервале |
значений |
аргумента параболой |
y=ax2+bx+c. В этом случае при нахождении искомой площади на каждом шаге интегрирования нужно использовать два элементарных отрезка, причем их общее количество должно быть четным, а также три соседние точки графика, координаты которых известны (экспериментальные данные): М0(х0; у0), М1(х1; у1) и М2(х2; у2). Для реализации метода при переменной величине интервала между значениями аргумента на оси абсцисс необходимо на
141
каждом шаге интегрирования решить систему трех уравнений, линейных относительно неизвестных коэффициентов a, b, с, подставив известные значения x и y в выше указанных трех точках:
ax2 |
+ bx |
+ c = y |
|
, |
|
|
|
0 |
0 |
|
0 |
|
|
|
ax2 |
+ bx + c = y , |
|
|||
1 |
1 |
1 |
|
|
||
ax2 |
+ bx |
+ c = y |
|
. |
(8) |
|
|
2 |
2 |
|
2 |
|
Искомая площадь будет равна сумме площадей элементарных параболических трапеций, которые можно вычислить с использованием формулы Ньютона-Лейбница:
xn |
|
n −1 |
ai |
|
|
|
|
|
|
|
|
|
|
|
|
||
|
2 |
|
3 |
3 |
|
bi |
2 |
2 |
|
|
|
|
|
||||
|
|
|
|
|
|
|
|
||||||||||
y(x)dx = |
|
|
(x2i +2 − x2i |
)+ |
|
(x2i +2 |
− x2i |
)+ ci (x2i +2 |
− x2i |
) |
|
|
|||||
|
|
|
|
||||||||||||||
x0 |
|
i =0 |
3 |
|
|
|
2 |
|
|
|
|
|
|
, |
(9) |
||
|
|
|
|
|
|
|
|
|
|
|
|
|
|
|
|
||
где n – |
выбранное |
нечетное |
количество |
таблично |
заданных |
(зарегистрированных) значений интегрируемой функции.
Для оценки влияния выбора метода численного интегрирования на диаграмму энергопоглощения мелкозернистого фибробетона была вычислена площадь фигуры под диаграммой его динамического деформирования (рис. 2). Реализация вышеописанных численных методов была проведена в среде графического программирования LabVIEW [12]. Суммирование площадей элементарных фигур (прямоугольников, прямоугольных или параболических трапеций) производилось при использовании цикла с фиксированным числом итераций (For Loop), в структуре которого для передачи данных из одной итерации цикла в следующую были установлены сдвиговые регистры (Shift Register). При реализации метода Симпсона для решения системы из трех линейных относительно коэффициентов a, b, с уравнений использовалась функция Solve Linear Equations. Результат работы программного модуля представлен на рис. 3. На нем сплошными линиями показаны графики удельного энергопоглощения (значения откладывались на левой вертикальной оси), которые построены до момента начала разрушения с использованием рассмотренных методов интегрирования. Разница ∆ между максимальными и минимальными значениями удельной энергии в процессе нагружения показана штриховой линией (значения откладывались на правой вертикальной оси). При разрушении материала (в вершине диаграммы деформирования) эта разница составила ∆=13,6 %.
142
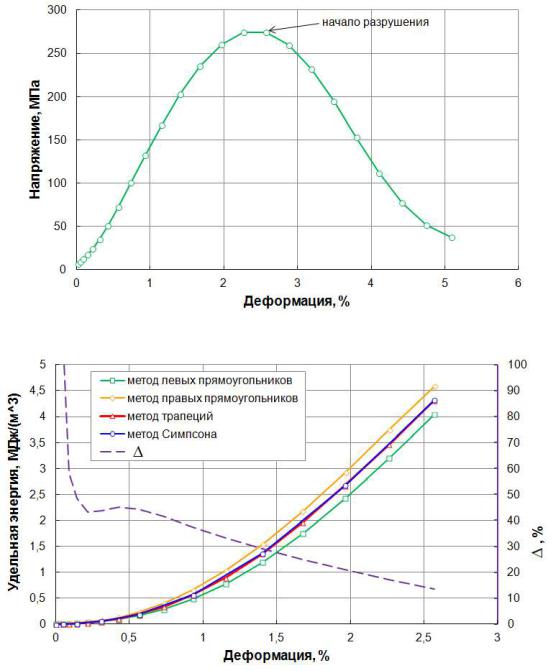
Рис. 2. Диаграмма динамического деформирования фибробетона
Рис. 3. Диаграммы удельного энергопоглощения фибробетона, полученные с использованием разных методов численного интегрирования
Литература
1.Chen W.W., Song B. Split Hopkinson (Kolsky) bar. Design, testing and applications. Springer, Boston, MA. 2011.
2.Li X., Chen Q., Chen J., Liao J., Lu Y. Dynamic increase factor (DIF) for concrete in compression and tension in FE modelling with a local concrete model. International Journal of Impact Engineering 163 (2022) 104079
3.Брагов А.М., Гонов М.Е., Ламзин Д.А., Ломунов А.К. Экспериментальное исследование динамического поведения мелкозернистых фибробетонов // «Механика композиционных материалов и конструкций, сложных и гетерогенных сред». Сборник трудов 11-й Всероссийской научной
143
конференции с международным участием им. И.Ф. Образцова и Ю.Г. Яновского. Москва, 2021. С. 23-28.
4.Bragov A.M., Lamzin D.A., Lomunov A.K. Experimental study of the processes of dynamic energy absorption of sand-lime brick. Procedia Structural Integrity. Vol. 32. 2021. P. 340-344.
5.Lamzin D.A., Bragov A.M., Lomunov A.K., Konstantinov A.Yu., Dell'Isola F. Analysis of the dynamic behavior of sand-lime and ceramic bricks. Materials Physics and Mechanics. 2019. Vol. 42. № 6. P. 691-698.
6.Bragov A.M., Igumnov L.A., Karihaloo B.L., Konstantinov A.Y., Lamzin D.A., Lomunov A.K., Petrov Y.V., Smirnov I.V. The investigations of the dynamics of fracture of brittle media on the basis of experimental data and theoretical analysis. Procedia Structural Integrity 6 (2017) 161-167.
7.Ламзин Д.А., Брагов А.М., Ломунов А.К., Константинов А.Ю., Новиков В.В., Гонов М.Е. Методические аспекты динамических испытаний хрупких материалов на сжатие // Приволжский научный журнал. 2019. № 4 (52). С. 65-78.
8.Bragov A., Igumnov L., Lomunov A., Konstantinov A., Lamzin D., Kruszka L. Use of the Kolsky method for dynamic tests of brittle media. MATEC Web of Conferences 174, 02022 (2018).
9.Xia K., Yao W. Dynamic rock tests using split Hopkinson (Kolsky) bar system – A review. Journal of Rock Mechanics and Geotechnical Engineering 7 (2015) 27-59.
10.Zhang Q.B., Zhao J. A review of dynamic experimental techniques and mechanical behaviour of rock materials. Rock Mechanics and Rock Engineering 47 (2014) 1411–1478.
11.Анкилов А.В. Высшая математика: учебное пособие. В 2 ч. Ч. 1 / А.В. Анкилов, П.А. Вельмисов, Ю.А. Решетников; под общей редакцией П.А. Вельмисова. – 2-е изд. – Ульяновск: УлГТУ, 2011. – 250 с.
12.Тревис Дж. LabVIEW для всех / Джеффри Тревис: Пер. с англ. Клушин Н.А. – М.: ДМК Пресс; ПриборКомплект, 2005. – 544 с.
В.В. Мыльников, М.В. Мыльникова, Д.И. Шетулов
ФГБОУ ВО «Нижегородский государственный архитектурно-строительный университет», г. Нижний Новгород, Россия
СТРУКТУРНЫЕ ИССЛЕДОВАНИЯ МАТЕРИАЛОВ С ИСПОЛЬЗОВАНИЕМ СОВРЕМЕННОЙ МИКРОСКОПИИ
Бурный скачок в развитии цифровизации в современных условиях сопровождается внедрением и разработкой различного программного обеспечения во всех сферах деятельности, в том числе металлографического оборудования [1–2]. Современные микроскопы оснащаются внушительными интерфейсами с огромным количеством всевозможных функций. Поэтому
144
возникла задача - выделить из всего этого многофункционального разнообразия наиболее важные функции и объединить их в необходимую последовательность в виде алгоритма проведения исследований при фрактографическом анализе разрушенных материалов – именно такая цель стояла в представленной работе. Для оценки применимости разработанных алгоритмов были исследованы дисперсные композиты с алюминиевой матрицей с различными размерами частиц и объемными долями [3–4].
Образцы были разрушены при одноосном растяжении прямым способом нагружения и постоянном контроле деформации на универсальной испытательной машине AG-Xplus-0.5 фирмы Shimadzu.
Поверхность разрушения была исследована с использованием методов фрактографического анализа с применением современной микроскопии [5– 8]. Одним из таких микроскопов является цифровой материаловедческий микроскоп Keyence VHX-1000.
Анализ функций, входящих в программное обеспечение микроскопа Keyence VHX-1000 позволил выявить наиболее важные и объединить их в необходимую последовательность в виде алгоритма проведения исследований при фрактографическом анализе разрушенных материалов:
Методика изучения поверхности разрушения материалов в 3-D изображении с использованием режима «e-Preview Optimal Image»
Поверхности разрушения после любого вида нагружения, будь это статическое, динамическое или циклическое, исследуем с использованием оптического микроскопа Keyence VHX-1000 с расширенными возможностями за счет усовершенствованной длиннофокусной оптической системы и цифровой обработки изображения в режиме «Optimal Image» c использованием функций автоматического распознавания объектива и приближения «DOUBLE’R». Разработанная методика проведения исследований, анализа и оценки 3D-структуры, дает возможность определения наиболее уязвимых мест в зонах локализации деформации и поверхностях разрушения, в основу её положено предположение о том, что выявление резких перепадов и значительных величин экстремумов в профиле обычно свидетельствуют о нестабильности прохождения процесса высокоэнергетического распространения магистральной трещины часто связанного с изменением механизма разрушения материала.
Методику изучения 3D-структуры рассмотрим на примере исследования экспериментального дисперсно-упрочненного композиционного материала, полученного нами [7] методом внутреннего окисления. На рис. 1 показаны поверхности разрушения прямоугольных образцов в 3D-изображении микроскопа Keyence VHX-1000, подвергнутого одноосному растяжению. Последовательность исследования заключается в выполнении следующих пунктов:
1.1 - выявляем направление наибольшего морфологически нестабильного изменения поверхности разрушения с максимальной шероховатостью по выделенному сечению, для этого:
145
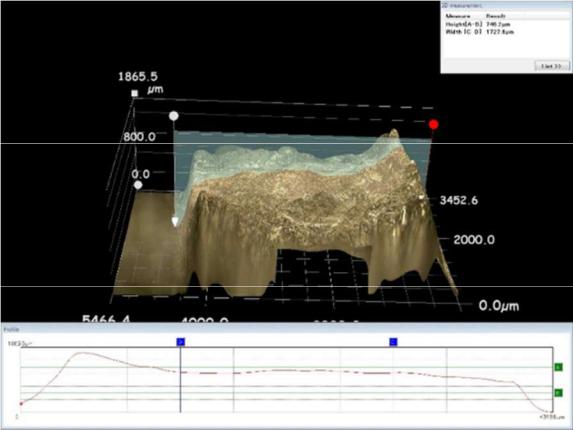
1.1.1- белый маркер позиционирования измерительной точки на микроструктуре закрепляется неподвижно в любом месте поверхности, причем измерения можно осуществлять при различных увеличениях оптики (в нашем случае – до 1000×раз);
1.1.2- красный маркер позиционирования измерительной точки на микроструктуре является подвижным, перемещая его, можно в режиме реального времени отследить направление максимального изменения шероховатости (скачки и перепады рельефа поверхности разрушения) по изменению профилограммы в нижней части экрана микроскопа;
1.2 - зафиксировать и сохранить выделенное сечение;
1.3 - проводим анализ профиля выделенного сечения поверхности разрушения материала, для чего используем следующие функции и средства измерения структурных элементов, заложенные в интерфейс микроскопа в виде квадратиков различного цвета (зеленые – горизонтальные секущие, синие – вертикальные секущие), обозначающие начало вертикальных и горизонтальных линий на отдельно вынесенной профилограмме в нижнюю часть изображения, которые дают возможность точного определения геометрических размеров на любом отрезке отображаемого профиля.
1.4 - Определив и зафиксировав наиболее морфологически разнородные места профиля поверхности, осуществляем выход из 3D- изображения в 2D-изображение и производим макроструктурный и микроструктурный фрактографический анализ по разработанным и стандартным методикам для более детального изучения.
146
Рис. 1. Изображения поверхностей разрушения образца из дисперсно-упрочненного композиционного материала
Необходимо отметить, что исследуемый фрагмент разрушенного образца или детали закрепляется на рабочем столе микроскопа неподвижно до исследования и в процессе исследования перемещения производит стол и объективы микроскопа для привязки систем отсчета и измерения к исследуемому элементу структуры. Многие важные функции, например, автоматического распознавания объектива и приближения «DOUBLE’R», определение края изучаемого объекта и точки измерения корректируется автоматически, что гарантирует достоверный результат измерения, нивелируя человеческий фактор. Такой подход значительно сокращает временные затраты.
Исследование выполнено за счет гранта Российского научного фонда № 22-13-20009, https://rscf.ru/project/22-13-20009/
Литература
1.Рeter Horňak, Margita Longauerová and Miloš Matvija. Metallography and Fractography XVII / Fractography and Materials Science (Metallography XVII). Nový Smokovec, High Tatra Mountains. Slovak Republic. 2020. рр. 470.
2.Quinn G.D. A History of the Fractography of Brittle Materials / Key Engineering Materials. 2009. Рр. 409. 1-16.
3.Чернышов Е.А., Романов А.Д., Романова Е.А., Мыльников В.В. Разработка технологии получения алюмоматричного литого композиционного материала с помощью синтеза упрочняющей фазы оксида алюминия в расплаве алюминия // Изв. вузов. Порошк. металлургия и функц.
покрытия. 2017. No. 4. С. 29–36.
4.Chernyshov E.A., Romanova E.A., Romanov A.D., Romanov I.D., Mylnikov V.V. Elaboration Of Aluminium Based Metalmatrix Composite Manufacturing // В сборнике: IOP Conference Series: Materials Science and Engineering. 2019. С. 012046.
5.Mike M.R. Fracture analysis of silicon die and ceramic package using fractography / International Journal of Microcircuits and Electronic Packaging. 1993. Рр. 350-362.
6.Мыльников В.В., Шетулов Д.И., Пронин А.И. Исследование изменений показателей сопротивления усталости стали 30ХГСН2А в процессе циклического деформационного упрочнения / Металловедение и термическая обработка металлов. 2020. № 10 (784). С. 52-60.
7.Naimark O., Oborin V., Bannikov M., Ledon D. Critical Dynamics Of Defects and Mechanisms Of Damage-Failure Transitions In Fatigue / Materials. 2021. Т. 14. № 10. DOI: 10.3390/ma14102554
8.Barathet V., Auradi V. Fractographic characterization of Al2O3 pparticulates reinforced Al2014 alloy composites subjected to tensile loading /
147
Frattura ed Integrità Strutturale. 2021. 57. Рр. 14-23. DOI: 10.3221/IGFESIS.57.02
148
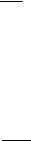
Д.А. Ламзин
ФГАОУ ВО «Национальный исследовательский Нижегородский государственный университет им. Н.И. Лобачевского»,
г. Нижний Новгород, Россия
ПРИМЕНЕНИЕ АППРОКСИМАЦИИ ПРИ ОБРАБОТКЕ ДАННЫХ ДИНАМИЧЕСКИХ ИСПЫТАНИЙ ХРУПКИХ МАТЕРИАЛОВ В
LABVIEW
Прочность хрупких материалов на сжатие в диапазоне динамических скоростей деформации определяется в основном с помощью классического метода Кольского [1-5]. Для определения прочности на растяжение часто применяется модификация этого метода – испытание на раскалывание, при котором цилиндрический образец разламывается на две половинки по диаметральной плоскости [6-10]. В обоих случаях образец размещается в системе разрезного стержня Гопкинсона (РСГ), а его нагружение осуществляется импульсом сжатия, который формируется после столкновения с нагружающим стержнем ударника, разогнанного газовой пушкой. Этот падающий (нагружающий) импульс сжатия распространяется по нагружающему стержню и после взаимодействия с образцов разделяется на отраженный от него импульс растяжения и прошедший через него импульс сжатия. При идеальных условиях проведения испытания должно соблюдаться равенство усилий, действующих на образец со стороны мерных стержней, то есть происходить равновесное нагружение. В процессе эксперимента производится запись осциллограмм, на которых отображаются импульсы деформации мерных стержней, зарегистрированные в их срединных сечениях с помощью электрической тензометрии. Далее производится выделение импульсов из осциллограмм и их взаимная синхронизация по времени, в результате которой анализируется выполнение предпосылки о равновесном нагружении образца. Кроме того, синхронизированные импульсы деформации или напряжения, а также вычисленные на их основе усилия используются для определения коэффициентов k1 (рис. 1) и k2 (рис. 2), которые требуются для вычисления скорости роста напряжений, достигаемой в процессе эксперимента [11]. Формула для ее нахождения в случае сжатия имеет вид [11]:
σc = |
k1A |
|
& |
|
|
|
A0 , |
(1) |
где А и А0 – соответственно площадь поперечного сечения мерных стержней и цилиндрического образца.
В случае растяжения вид формулы для определения скорости роста напряжений следующий [11]:
& |
2k2 |
|
=πLD, |
|
|
σt |
(2) |
149