
Допуски изделий и средства измерений
..pdfталь, вырывания с поверхности частиц материала и других фак торов. Величина неровностей зависит от метода, условий и режи мов обработки, свойств материала детали и инструментов, гео метрии инструментов.
Шероховатость поверхностей оказывает влияние на трение и износ деталей, изменяет эффективные зазоры и натяги в соеди нениях, уменьшает прочность деталей при переменных нагруз ках, ухудшает стойкость деталей при коррозии, влияет на плот ность, герметичность и другие показатели.
Для количественного описания шероховатости используют не сколько параметров по ГОСТ 2789-73 (распространяется на все поверхности, кроме ворсистых), которые характеризуют отдель ные свойства шероховатых поверхностей.
Параметры оцениваются по неровностям профиля (сечения в плос кости, нормальной к поверхности), который может быть получен на приборе — профилографе с увеличением в несколько тысяч раз (рис. 55). Отклонения (параметры) профиля отсчитываются от средней линии тп—т профиля (проведенной так, чтобы сумма квадратов расстояний от каждой точки профиля до средней ли нии была минимальна) в пределах базовой длины (выбирается так, чтобы при определении параметров не учитывались неровно сти с большим шагом, например, волнистость).
Параметры шероховатости разделяются на высотные (харак теризуют неровности по высоте): Ra, Rz, Rmax и шаговые (харак теризуют неровности по длине): SM, S, tp. Последний параметр характеризует также форму неровностей.
Среднее арифметическое отклонение профиля Raесть среднее арифметическое абсолютных (без учета направления) значений отклонений профиля до средней линии по нормали в ней.
Высота неровностей по десяти точкам Rz есть среднее рас стояние между пятью наивысшими точками выступов и пятью наинизшими точками впадин; Rz характеризует среднюю высоту неровностей.
Параметры Ra и Rz применяются на чертежах наиболее часто. Причем параметр Ra, учитывающий положение каждой точки
профиля (интегральный показатель), более полно определяет шеро ховатость, нежели Rz, и поэтому рекомендуется к применению.
Наибольшая высота неровности профиля Rmax (см. рис. 55) — расстояние (в пределах базовой длины) между линией выступов, проведенной параллельно (эквидистантно) средней линии через наивысшую точку профиля, и линией впадин, проведенной через наинизшую точку профиля. При этом Rmax = Rp + Rv> где Rp — высота наибольшего выступа (т. е. расстояние от средней линии до высшей точки профиля), а й у — высота наибольшей впадины (т. е. расстояние от средней линии до низшей точки профиля).
Средний шаг неровностей профиля Sm (см. рис. 55) есть сред нее арифметическое значение шага неровностей по средней ли нии профиля (в пределах базовой длины).
Средний шаг неровностей профиля по вершинам S (см. рис. 55) — среднее арифметическое значение (в пределах базовой длины) шага неровностей по вершинам.
Относительная опорная длина профиля tp (см. рис. 55) — отноше ние опорной длины профиля к базовой длине I при уровне сечения р (р в % от Rmax). Опорная длина профиля складывается из отрезков Ьр отсекаемых линией сечения, параллельной (эквидистантной) средней линией профиля в материале детали и расположенной на заданном расстоянии Р (уровень сеченияр = iV^max *ЮО %) от линии выступов. Для каждой поверхности в зависимости от ее формы (закругленные или острые неровности) будет своя кривая изменения tp в зависимо сти от р. Всегда £0= 0> так как -линия сечения совпадает с линией выступов = 0 и *юо= ЮО» так как линия сечения совпадает с ли нией впадин (Zbi = 1).
С целью качественного сравнения шероховатости поверхнос тей в зависимости от значений Ra или Rz установлены классы шероховатости (с 1-го по 14-й). 1-й класс — для самых шерохова тых (грубых) поверхностей, 14-й — для самых чистых (гладких). На чертежах классы шероховатости не обозначаются, а указыва ются только значения параметров — (i?a, Rz, Дтах (мкм); Sm> S (мм); tp (%).
Для обозначения шероховатости на поверхностях деталей ис пользуют один из трех знаков (рис. 56): знак на рис. 56, а при меняют, если метод поверхности не установлен, знак на рис. 56, б — если поверхность должна быть получена с удалением слоя мате риала (точение, фрезерование, шлифование, травление и др.), знак на рис. 56, в — если поверхность должна быть получена без уда ления поверхностного слоя материала (литье, штамповка, обкат ка шариком или роликом и др.)
Над знаком указывают стандартные значения параметра или параметров, справа от него (при необходимости) — направление неровностей, базовую длину и на полке знака — способ обработ ки (если он является единственно возможным) или другие допол нительные сведения по обработке (рис. 56, г).
• ) |
с |
Параметр |
Способ обработки и Вр. |
l ) |
|
|
базоВая длина |
|
.Обозначение направ |
77/ |
ления нероВностей |
|
|
Рис. 56 |
|
Все параметры шероховатости, кроме Ra (используемого чаще других), записывают со своими буквенными обозначениями. Па раметры могут указываться в виде предельного числового значе ния (рис. 57, а), соответствующего наиболее грубой допускаемой шероховатости; двух предельных значений (рис. 57, б), определя ющих диапазон изменений параметра; номинального значения параметра с предельными отклонениями в процентах (из ряда 10, 20, 40 %) от этого значения (рис. 57, в). При необходимости в обозначении шероховатости приводятся несколько параметров (сверху — высотные, затем шаговые и далее tp рис. 57, г).
Если направление неровностей на поверхностях оказывает вли яние на работу соединений, то его обозначают одним из шести знаков (рис. 57, д), показывающих направление (волн) шерохова тости по отношению к линии поверхности.
Базовую длину указывают на чертеже (рис. 57, е), если она отличается от значений, соответствующих заданным величи нам Ra и Rz. Пример обозначения способа обработки приведен на рис. 57, ж.
Полиробать
Рис. 57
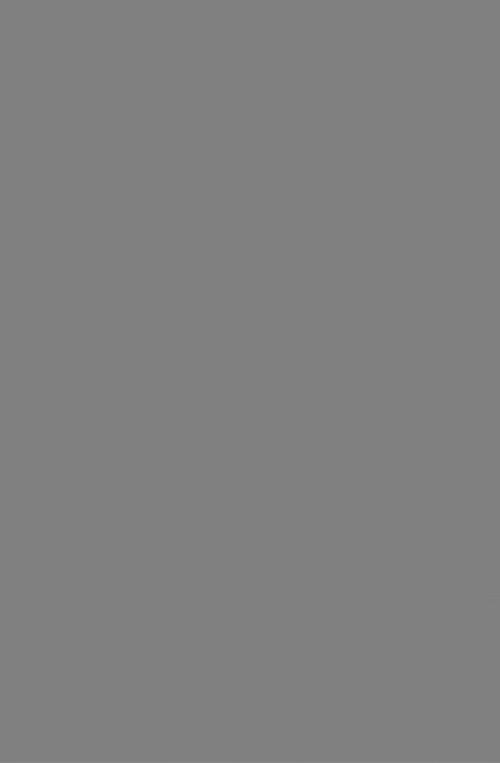
Пример обозначения требований к шероховатости поверхнос тей, а также допусков размеров, формы и расположения поверх ностей показан на рис. 59.
СП РАВОЧНАЯ ТАБ Л И Ц А 1 .8 .1
1.8.1. Значения параметров шероховатости (по ГОСТ 2789—73)
Высотные параметры Ra, R z, R ^ ^ y базовые длины, классы шероховатостей
Пред
почти
тельные
Да, мкм
значе ния Ra, мкм
50 80; 63; 40;
25 40; 32; 20
12,5 |
20; |
16; |
|
10; |
||
6,3 |
10; |
8; |
5 |
|||
3,2 |
5; |
4; |
2,5; |
|||
1,6 |
2,5; |
2; |
1,25 |
|||
|
1,25; |
1; 0,63; |
||||
0,8 |
0,63; |
0,5; |
||||
0,4 |
|
0,32; |
|
|||
0,2 |
0,32; |
0,25; |
||||
|
|
0,16 |
|
|||
|
0,16; |
0,125; |
||||
0,1 |
|
0,08 |
|
|
||
0,05 |
0,08; |
0,063; |
||||
|
|
0,04 |
|
|
||
|
0,04; |
0,032; |
||||
0,025 |
|
0,02 |
|
|
||
0,012 |
0,02; 0,016; |
|||||
0,006 |
|
0,01 |
|
|
||
|
0,01; 0,008 |
|
|
|
|
|
|
|
|
|
Базовая |
|
R f |
|
Лпих' “ К" |
длина, |
|||||||
|
|
|
|
|
|
|
|
|
мм |
|
320; |
|
250; |
|
200; |
8 |
|||||
|
|
|
160 |
|
|
|
||||
|
|
|
|
|
|
8 |
||||
160; |
125; |
100; 80 |
||||||||
|
||||||||||
80; 63; |
|
50; 40 |
8 |
|||||||
40; |
32; |
|
25; |
20 |
2,5 |
|||||
20; |
16; |
12,5; |
10 |
2,5 |
||||||
10; |
8; |
6,3 |
|
0,8 |
||||||
6,3; |
5; |
4; |
|
3,2 |
0,8 |
|||||
3,2; |
2,5; |
2; |
1,6 |
0,8 |
||||||
1,6; |
1,25; |
1; 0,8 |
0,25 |
Класс |
Возможные методы |
шеро |
|
хова |
обработки |
тости |
|
Грубое обтачивание, чер
1новоефрезерование, свер
1ление крупных отвер стий
Получистовое обтачива
3
ние, черновое фрезеро
4
вание торцовой фрезой, сверление, черновое зенкерование
Чистовое точение, раз
5
вертывание, чистовое и
6
тонкое фрезерование шли фование, чистовое про тягивание
Тонкое (алмазное) точе ние, тонкое развертыва
7
ние, чистовое и тонкое
8
шлифование, калиброва
9
ние после расточки, до водка, хонингование, су перфиниширование плос костей
0,8; 0,63; 0,5; |
|
|
Тонкое полирование, тон |
||
|
0,4 |
|
0,25 |
10 |
кая доводка, хонинго |
0,4; 0,32; 0,25; |
0,25 |
11 |
вание, суперфиниширо |
||
|
0,2 |
|
|
|
вание |
0,2; |
0,16; |
0,125; |
0,25 |
12 |
|
|
0,1 |
|
|
||
0,1; 0,08; 0,063; |
0,08 |
13 |
Зеркальная доводка |
||
|
0,05 |
|
0,08 |
14 |
|
0,05; 0,04; |
0,032 |
|
|
|
.
Шаговые параметры Sm, S ; отностительная опорная длина профиля tp
|
|
|
|
|
|
|
|
|
|
|
|
Уро |
|
|
|
|
|
|
|
|
|
|
|
|
вень |
|
|
|
|
SM, S , мм |
|
|
|
|
|
сече |
||
|
|
|
|
|
|
|
|
|
ния |
|||
|
|
|
|
т |
’ |
|
|
|
|
|
|
р , % |
|
|
|
|
|
|
|
|
|
|
|
|
от |
|
|
|
|
|
|
|
|
|
|
|
|
^тах |
|
|
|
|
|
|
|
|
|
|
|
90, |
90, |
|
|
|
|
|
|
|
|
|
|
|
80, |
|
|
|
|
|
|
|
|
|
|
|
|
80, |
70, |
|
|
|
|
|
|
|
|
|
|
|
70, |
60, |
12,5 10 |
8 |
6,3 |
5 |
4 |
|
3,2 |
2,5 |
2 |
1,6 |
1,25 |
60, |
50, |
|
50, |
|||||||||||
1 |
0,8 |
0,63 |
0,5 |
0,4 |
|
0,32 |
0,25 |
0,2 |
0,16 |
0,125 |
40, |
40, |
0,1 |
0,08 |
0,063 |
0,05 |
0,04 |
|
0,032 |
0,025 |
0,02 |
0,016 |
0,0125 |
30, |
30, |
0,01 |
0,008 |
0,006 |
0,005 |
0,004 |
0,003 |
0,002 |
|
|
|
25, |
25, |
|
|
|
|
|
|
|
|
|
|
|
|
20, |
|
|
|
|
|
|
|
|
|
|
|
|
20, |
15, |
|
|
|
|
|
|
|
|
|
|
|
15, |
|
|
|
|
|
|
|
|
|
|
|
|
ю, |
|
|
|
|
|
|
|
|
|
|
|
|
10 |
5 |
|
|
|
|
|
|
|
|
|
|
|
|
|
П ри м ер пол ьзован и я т аблицей. На чертеже обозначен параметр Ra - |
1,6 мкм. По таблице |
шероховатость поверхности соответствует 6-му классу шероховатости, базовая длина 0,8 мм; в зависимости от вида поверхности деталь может быть получена чистовым точением, чис товым развертыванием, тонким фрезерованием, шлифованием, чистовым протягиванием.
1.9. РАЗМЕРНЫЕ ЦЕПИ
ОБЩИЕ СВЕДЕНИЯ
Размерной цепью называется совокупность размеров, образую щих замкнутый контур и определяющих положение осей или по верхностей детали или положение деталей в сборочной единице.
Различают детальные и сборочные размерные цепи. В деталь ной размерной цепи все размеры принадлежат одной детали. Де тальные размерные цепи приходится решать при разработке про цессов обработки деталей. В сборочной размерной цепи размеры принадлежат различным деталям; сборочные размерные цепи обычно рассчитывают при конструировании и проектировании любой машины или агрегата.
Для упрощения анализа и решения размерных цепей все раз меры, зазоры, натяги, перебеги и т. д., входящие в цепь, условно представляют в виде замкнутой последовательности векторов с на правлением по часовой стрелке или против часовой стрелки, т. е. в виде схемы размерной цепи (рис. 60, а). Размеры, составляю щие размерную цепь, называются звеньями.
По расположению звеньев размерные цепи разделяют на ли нейные или параллельнозвенные (все звенья параллельны), плос костные (звенья расположены в одной плоскости) и пространствен-
ные (звенья расположены произвольно в пространстве). Выделя ют также угловые цепи, в которых звенья цепи — угловые пара метры, выраженные в угловой мере или в виде отношений.
Пространственные цепи решают, проектируя звенья на две или три плоскости, а плоскостные — проектируя на направления так называемого замыкающего звена.
Замыкающим звеном размерной цепи называется размер, ко торый получается только при сборке (например, расстояние меж ду деталями) или последним при изготовлении (например, раз мер детали, который на чертеже не указан, так как получается за счет выполнения других размеров). Остальные звенья (кроме за мыкающего) называются составляющими. Значение замыкающего звена зависит от размеров составляющих звеньев. Замыкающими звеньями сборочных размерных цепей обычно являются зазоры, натяги, смещения и другие параметры, погрешности которых оп ределяют качество работы всего сборочного узла. Замыкающие звенья на рис. 60 обозначены индексом суммы (Е), так как они сум мируют погрешности всех звеньев.
Составляющие звенья могут быть увеличивающими и умень шающими. Увеличивающими называют звенья, с увеличением ко торых замыкающее звено увеличивается (на схеме размерной цепи эти звенья имеют направления, противоположные направлению замыкающего звена: А 2, D , В2, С3, С4, С5 на рис. 60, а, б). Умень шающими называют звенья, с увеличением которых замыкаю щее звено уменьшается (на схеме размерной цепи такие звенья однонаправлены с замыкающим звеном: A v d, Bv Cv C2, C6 на рис. 60, a, 6).
Решение размерной цепи заключается в определении предель ных размеров или предельных отклонений звеньев в зависимости от конструктивных и технологических требований с целью обес печения нормальной работы сборочной единицы и достижения требуемой точности замыкающего звена.
Расчет размерной цепи предполагает решение прямой и обрат ной задачи. Прямая задача есть определение допусков и отклоне ний составляющих звеньев по заданному допуску (и отклонени ям) замыкающего звена. Обратная задача — определение допуска
иотклонений замыкающего звена по известным допускам и от клонениям составляющих звеньев. Полученное значение замы кающего звена сравнивают с заданными значениями и, в случае расхождения, решают прямую задачу.
Известны пять различных методов достижения требуемой точ ности замыкающего звена (и обеспечения тем качественной рабо ты изделия): 1) метод максимума — минимума (или полной вза имозаменяемости), при котором учитывают предельные размеры
иих сочетания при сборке изделия; 2) вероятностный метод, ког да учитывают вероятности соединений деталей с различными раз
мерами; и три метода, при которых изделия оказываются огра-
|
|
S = A , |
2 ? |
„ i d . % |
> ■d |
V , |
i |
Л ______ . |
|
ниченно взаимозаменяемыми: 3) подбор деталей (селективная сбор ка); 4) пригонка; 5) использование компенсаторов (метод регули рования). Наиболее распространен последний метод, при котором составляющие размеры выполняют с большими допусками (квалитеты от 12 до 17-го), а требуемый размер замыкающего звена достигается установкой регулировочных шайб, прокладок, вту лок и использованием специальных устройств. Например, требу емый зазор С2 (см. рис. 60, б) можно обеспечить установкой регу-
лировочных шайб между втулкой и стенкой корпуса (плато). Ре гулировочные шайбы и прокладки широко используются при сбор ке редукторов, коробок скоростей, различных приводов; специ альные гидравлические устройства применяют для регулировки за зоров в подшипниках скольжения, в клапанных механизмах и др.
Исходя из условия замкнутости, основное уравнение линейных и некоторых плоских цепей можно записать в следующем виде:
2 ^ 4 = 0 , |
(59) |
1 |
|
где — коэффициенты, характеризующие степень и направле ние влияния i -го звена на замыкающее звено, или передаточные отношения; А* — величина звена.
Для линейных (параллельнозвенных) размерных цепей
§1 = ± 1 . |
(60 ) |
где знак «плюс» применяется для увеличивающих звеньев, а «ми нус» — для уменьшающих.
В общем случае уравнение размерной цепи связывает замыка ющее звено Ах и составляющие звенья A t:
/(A z,Ai) = 0 , i = l,..., п. |
(61) |
Если А- не размер, а иной параметр (электрический, оптичес кий, механический и пр.), влияющий на эксплуатационный по казатель А^ изделия (мощность, расход энергии, скорость и пр.), то уравнение (61) называют уравнением функциональной цепи. Подробнее об этом см. [3].
РЕШЕНИЕ РАЗМЕРНОЙ ЦЕПИ МЕТОДОМ МАКСИМУМА — МИНИМУМА (ПОЛНОЙ ВЗАИМОЗАМЕНЯЕМОСТИ)
Метод предполагает, что заданная точность замыкающего зве на будет обеспечена без пригонки, подбора или дополнительной регулировки даже при самых неблагоприятных сочетаниях мак симальных и минимальных размеров деталей при сборке.
Пользуясь правилом «обхода по контуру» для размерной цепи (схемы размерной цепи) по рис. 60, б (направление обхода — по ча совой стрелке), напишем
+ С3 + С4 + С§ —CQ —С2 - CJ —С2 = 0.
Решив уравнение относительно замыкающего звена С2, получим
cz= (С3 + с4 + с5) - (Сб + с г + с2). |
(62) |
2817
Звенья, заключенные в первую скобку, есть увеличивающие зве нья, а во вторую — уменьшающие.
Следовательно, в простейшем случае уравнение размерной цепи можно записать в виде
= |
т |
пт
где Az — замыкающее звено; п — число увеличивающих звеньев АУВ; т — число уменьшающих звеньев A jM.
После составления уравнения в виде формулы (63) и определе ния номинального значения замыкающего звена поэтому уравне нию предельные значения замыкающего звена рассчитывают по уравнениям:
max |
= V АУВ |
- У А*™ • |
||
LJ |
(i max |
LJ |
j min’ |
|
|
п |
|
т |
|
max’
(64)
(65)
где AZmax, А ?^ах, AJJJ^ — наибольшие предельные размеры соответственно замыкающего звена, Uго увеличивающего звена, у-
го уменьшающего звена; Az min» Aimin’ ^Jmin — наименьшие пре дельные размеры соответственно замыкающего звена, i-vo увели чивающего звена, у-го уменьшающего звена.
Почленно вычитая из (65) выражение (64), получим:
^ ™ * - Л 1т1п |
- ^ т > - |
п |
т |
Разность предельных размеров есть допуск этого размера:
|
iImax - АImin = Гх; |
|
||||
дув |
_ дув |
_ 7^ув. |
7- _ i |
Щ |
||
/i шах |
*4 min ~ 1 i |
9 |
1 ~ |
|||
|
||||||
дум |
_ дум |
= грум. |
|
|
||
ушах |
у min |
у |
9 У = 1, •••> т, |
<««>
(67)
(68)
где Гх, 2]ув, ТУм — допуски соответственно замыкающего, i-ro увеличивающего и у-го уменьшающего звеньев.
По выражению (66) с учетом (67) и (68) определяем, что до пуск замыкающего звена равен сумме допусков всех (увеличива ющих и уменьшающих) звеньев:
т+п
Т г = £ T i> * = 1> |
т + п . |
(69) |
1