
Допуски изделий и средства измерений
..pdfУравнения (63)-(65), (69) используют, решая обратную задачу размерной цепи.
При решении прямой задачи известен заданный допуск замы кающего звена [Т^]. Требуется так назначить допуски составляю щих звеньев, чтобы допуск замыкающего звена, рассчитанный по формуле (69), был не больше заданного [Т у , т. е.
r i < [ T z ]. |
(7 0 ) |
При этом предельные значения замыкающего звена не долж ны выходить за установленные пределы.
Допуски составляющих звеньев можно определить (распреде лить) несколькими способами: попыток, равных допусков и од ного квалитета.
При способе попыток на составляющие звенья назначают эко номически целесообразные допуски, добиваясь выполнения нера венства (70).
При способе равных допусков допуски всех звеньев называют одинаковыми, тогда из формулы (69) получим выражение для расчета этого одинакового (среднего) допуска Тс:
Tc = [Tz]/(77l + 7l). |
(71) |
При способе одного квалитета допуски составляющих звеньев принимают соответствующими одному квалитету (т. е. коэффици енты точности а для всех размеров одинаковы, см. п. 1.3). Учи тывая, что допуски размеров рассчитывают по уравнению (39), и ис пользуя формулу (69), получим выражение для расчета коэффи циента точности а (одинакового для всех размеров):
пг+п |
|
« = [Г2] / 5 > |
(72) |
1 |
|
где i — единица допуска (мкм) (см. табл. 1.3.2).
Далее, зная коэффициент точности по табл. 1.3.3, определяют квалитет и подбирают поля допусков указанного квалитета, обес печивая выполнение неравенства (70).
Пример 13. Рассчитать значение замыкающего звена (обратная
задача) для размерной цепи по рис. 60, |
б, если С\ = 150Ы2 (-о,4)> |
С2 = 15Ы 2 (_о,18 0)> С3 = 10,5hl2 (_o,i8 0 )> |
С4 = 160Ы2 (-о,4)» ^5 = |
= 10,5Ь12 (_о,180)* С6= 15М2 (-0,180)* По условиям работы замыка ющее звено (зазор С2) должно быть выдержано в пределах 0,28- 1,08 мм (соответствует посадке Н12/Ы2), т. е. [Т у = 1,08-0,28 =
=0,8 мм.
Ре ш е н и е . Номинальное значение замыкающего звена рас
считаем по формулам (62), (63):
С£ = (С3 + С4 + С5 ) - (С6 + С* + С2 ) -
= (10,5 + 160 + 10,5)- (15 + 150 + 15) = 1 мм.
Наибольший предельный размер замыкающего звена по фор муле (64) равен
А х шах = (С 3 шах + ^4 шах + ^5 max) ” ^ 2 min + ^ 1 min + ^ 6 min) =
= (10,5 + 160 + 10,5) - (14,82 + 149,6 + 14,82) = 1,76 мм.
Наименьший предельный зазор (замыкающее звено) по фор муле (65) равен
Ах min = (Сз min + ^4 min + ^5 min) ~ (^2 max + ^1 max + ^6 max) =
= (10,32 + 159,6 + 10,32) - (15 + 150 + 15) = 0,24 мм.
Допуск замыкающего звена по формуле (69) равен
6
Ti= Y<Ti = (0,4 + 1,18 + 0,18 + 0,4 + 0,18+0,18) = 1,52 мм
1
(^ m ax -^ m in = 1,76-0,24).
Результаты расчетов показали, что предельные значения замы кающего звена вышли за установленные пределы (А£тах = 1,76 мм > > \Ахmaxi = 1,08 мм, Ах. min= 0,24 мм < [A£min] = 0,28 мм) и допуск замыкающего звена (Т£= 1,52 мм) больше установленного допус ка1 [7У = 0,8 мм. Следовательно, необходимо изменить допуски составляющих звеньев и решить прямую задачу.
Пример 14. Используя исходные данные и результаты расчетов
впримере 13, решить прямую задачу способом одного квалитета.
Ре ш е н и е. По формуле (72) рассчитаем коэффициент точно сти всех составляющих размеров:
а = Ь ] ф ,
1
где [Тх] — заданный допуск замыкающего звена [Т£] = 800 мкм; i — единица допуска для заданного номинального размера: для раз
меров С2= 15 мм, Сз = 10,5 мм, С&= 10,5 мм, С6= 15 мм |
i = 1,08 мкм |
(см. табл. 1.3.2), для размеров С\= 150 мм, С4 = 160 мм |
i = 2,52 мкм |
(см. табл. 1.3.2). Тогда |
|
800 мкм |
= 95. |
a = --------------------------------------------------------------- |
(2,52 + 1,08 + 1,08 + 2,52 + 1,08 +1,08) мкм
В 10-м квалитете а = 64 (см. табл. 1.3.3); следовательно, до пуски составляющих звеньев должны быть взяты для части раз-
меров по 10-му квалитету, для остальных размеров — по 11-му квалитету.
Выбираем такие поля допусков указанных квалитетов, при кото рых предельные значения замыкающего звена не будут выходить за установленные пределы 0,28-1,08 мм. Принимаем: Сг = 150Ы1 (Ч) 25),
С2= 15Ы 0 (_0 0 7 )> Cg = 10js10 (±0 ,0 2 9)’ ^ 4 = 1 6 0 jsll (±0 Д2 5 )’ ^ 5 = = 10,5jsl0 (±0^0з5), Сб = 15Ы0 (_о,о70)* Выполним проверку приня тых полей допусков.
По формуле (64) наибольший предельный размер замыкающего звена составит
Ах шах — (Сз шах + с4шах + С 5 шах) - (С 2min + C j min + с 6 min) “
= (10,029 + 160,125 + 10,535) - (14,93 + 149,75 + 14,93) = 1,079 мм, что меньше допустимого значения, равного 1,08 мм.
По формуле (65) наименьший предельный размер замыкаю щего звена составит:
Ах min = (С8 min + С4 min + С5 min) “ (@2 max + Ci max + ^6max ) =
= (9,971 + 159,875 + 10,465) - (15 + 150 + 15) = 0,311 мм, что боль ше допустимого значения, равного 0,28 мм.
По формуле (69) допуск замыкающего звена составит
6
Тг = Х Tt = (0,25 + 0,07 + 0,58 + 0,25 + 0,07 + 0,07) = 0,768 мм, 1
что меньше заданного значения [Тs] = 0,8 Мм.
Итак, проверка показала, что указанные ранее поля допусков 10-го и 11-го квалитетов выбраны правильно. Следует заметить, что размеры деталей по длине (их свободные размеры) обычно принимают по 12-17-му квалитетам (см. п. 1.4), а более точные квалитеты (как в нашем случае) используют относительно редко.
РЕШЕНИЕ РАЗМЕРНОЙ ЦЕПИ ВЕРОЯТНОСТНЫМ МЕТОДОМ
Детали, изготовленные по одному чертежу, имеют размеры, которые несколько (в пределах допуска) отличаются друг от дру га. В партии изделий больше всего деталей с размерами, близки ми к середине поля допуска (со средними размерами), деталей же с размерами, близкими к предельным (наибольшим и наименьшим), обычно очень мало. Учитывая обычную технологию сборки, при ко торой сборщик наугад выбирает детали (условие полной взаимо заменяемости), практически невозможно ожидать, что в сбороч ном узле будут одновременно находиться детали с наибольшими увеличивающими размерами (например, С3тах, С4тах, С5 тах, см. рис. 60, б) и наименьшими уменьшающими размерами (на пример, С2 min? Cl min, С6 min, см. рис. 60, б). Следовательно, при сборке не будет изделий, в которых замыкающее звено имеет раз мер А2тах [по формуле (64)]. Аналогично — для размера A2min [по формуле (65)].
Для расчета наибольших, наименьших размеров и допуска за* мыкающего звена с учетом возможности соединения деталей с раз' личными размерами необходимо использовать зависимости теории вероятностей, которые мы здесь рассматривать не будем [3].
Среднее значение замыкающего звена можно приближенно оп ределить по формуле (63), используя средние значения составля ющих звеньев, если средние размеры деталей в партии соответ ствуют серединам полей допусков.
Допуск (вероятностный) замыкающего звена рассчитывают по формуле:
(73)
где Xj, Хг— коэффициенты (относительного рассеяния) замыкаю щего звена и i-ro составляющего звена, которые зависят от эмпи рических законов распределений размеров деталей при изготов лении и изменяются от 0,33 до 0,58. Часто в расчетах использу ют так называемый нормальный закон (Гаусса), при котором
и Xt равны 0,33; Т; — допуск составляющего звена.
Пример 15. Используя данные примера 13 (см. рис. 60, б), оп ределить допуск и предельные значения замыкающего звена ве роятностным методом, приняв Xt = X^= 0,33 (по нормальному за кону).
Р е ш е н и е . Средний размер замыкающего звена определим по уравнению размерной цепи (62)-(63), используя средние раз меры составляющих звеньев:
Az- (Сзс+ с4с + С§с) - (С2с+ С4с+ С6с),
гДе A L — средний размер замыкающего звена; С$с — средний размер, равный С3с = (С3тах + С3 2 = (10,5 + 10,32):2 = 10,41 мм; аналогично, С4с= 159,8 мм, С5с = 10,41 мм, С2с = 14,91 мм, Cic = = 149,8 мм, Сдс = 14,91 мм.
Ас1 = (10,41 + 159,8 + 10,41) - (14,91 + 149,8 + 14,91) = 1 мм. Допуск замыкающего звена по формуле (73) оказывается рав
ным (при |
= 0,33): |
При расчете допуска замыкающего звена по методу максиму ма — минимума [формула (69)] Тъ = 1,52 мм.
Наибольший предельный размер замыкающего звена равен
^Imax = ^ d + Г£/ 2 = 1+0,67/2 = 1,335 мм.
Наименьший предельный размер замыкающего звена равен
^Xmin=A ;I“ |
2 = 1 - 0,67 / 2 = 0,665 ММ. |
Как показывают результаты расчетов в примере 15, допуск за мыкающего звена оказывается меньше по сравнению со значением, полученным по методу максимума — минимума, а допуски со ставляющих звеньев (при решении прямой задачи) — большими (более дешевыми при изготовлении), что является преимуществом этого метода. Следует учитывать также, что на сборке возможно получение некоторого (очень малого) количества изделий, у ко торых значения замыкающего звена не соответствуют установ ленным пределам (брак).
РЕШЕНИЕ РАЗМЕРНЫХ ЦЕПЕЙ МЕТОДАМИ СЕЛЕКТИВНОЙ СБОРКИ, ПРИГОНКИ И РЕГУЛИРОВАНИЯ
Метод селективной сборки заключается в том, что заданная точность замыкающего звена достигается при сборке подбором де талей по их размерам. Детали предварительно рассортировывают на несколько групп; размеры деталей каждой группы очень близ ки. При сборке подбирают детали из одноименных групп. Число
(п) групп сортировки рассчитывают по уравнению
т+п
(74)
1
где Ti — допуск /-го составляющего звена (их количество состав ляет т + п); [Т%\ — заданный допуск замыкающего звена.
Этот метод обычно используют в точных размерных цепях с ма лым числом звеньев (3-4), например, в соединениях поршень — цилиндр, в подшипниках скольжения и др.
При методе пригонки заданная точность замыкающего звена (например, требуемая величина зазора) обеспечивается пригон кой (подрезкой, пришлифовкой, шабрением и др.) одной из дета лей. Например, требуемый зазор в размерной цепи на рис. 60, б может быть получен подрезкой торца втулки.
Размеры пригоняемой детали рассчитывают с учетом припуска на обработку так, чтобы пригонка была возможна при расчетных допусках и отклонениях составляющих звеньев. Способ пригонки (черновая или чистовая подрезка, пришлифовка и др.) должен обес печивать необходимую точность размера, т. е. допуск на пригонку Тприг должен быть не больше заданного допуска замыкающего звена:
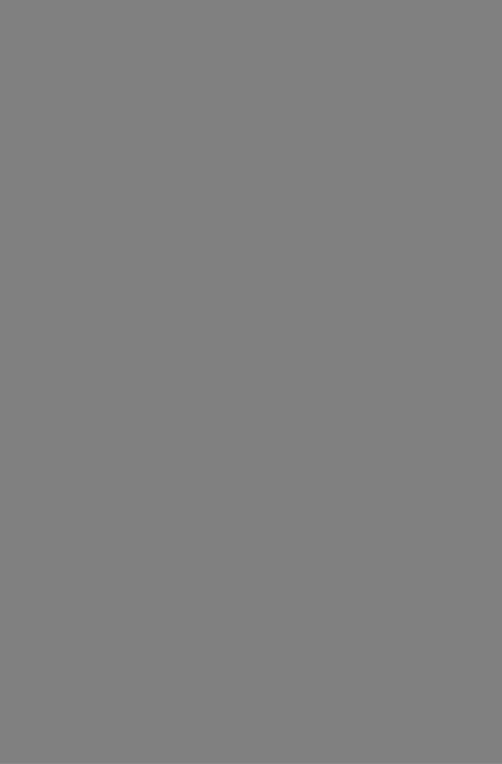
По формуле (77) определяем величину компенсации:
Тк = (T l + Т 2 + Т 3 + Т4 + Г 5 + Г 6) -
- [T5J = (0,4 + 0,18 + 0,18 + 0,4 +0,18) - 0,8 = 0,72 мм.
По формуле (78) рассчитываем число шайб (округляя в боль шую сторону до целого числа):
г = 0,72 / 0,5 = 2 шт.
При заданных предельных отклонениях составляющих звеньев предельные размеры замыкающего звена оказались равными (см. при мер 13)
min-0 ,2 4 мм; А^щах - 1*76 мм.
Установка регулировочных шайб в указанное место (см. рис. 60, б) приводит только к увеличению зазора (замыкающего звена) и боль шие зазоры установкой шайб не уменьшить. Следовательно, наи больший зазор при сборке должен быть не более допустимого значе ния 1,08 мм (см. пример 13).
Увеличиваем размер звена Cg (и тем уменьшаем зазор) на ве
личину |
|
|
А % max - |
1,08 = 1,76 - |
1,08 = 0,68 мм. |
Размер звена С6 оказывается равным |
||
С6 |
1 г0+0,68 |
_1 к+0,68 |
1 -0,18+ 0,68 “ 1О +0,50 |
(увеличиваем каждое из предельных отклонений на рассчитанную величину).
При сборке деталей с измененным размером Cg = 15+0>5’0 пре дельные размеры замыкающего звена изменились [расчет по фор мулам (64) и (65)] и стали равными (учитывая изменение размера на 0 ,6 8 ):
А х min = 0,24 —0,68 = —0,44 мм; Ах max = 1,76 - 0 ,6 8 = 1,08 мм.
Таким образом, если при сборке размер замыкающего звена (зазор), замеренный щупом или иным способом, окажется в преде лах от - 0,44 (это зазор между торцом втулки и наружной сторо ной стенки корпуса) до + 0,08 мм, необходимо устанавливать две шайбы по 0,5 мм (-0,44 + 1 = 0,56 и + 0,08 +1 = 1,08, что соответ ствует заданным значениям). Если зазор окажется в пределах 0,08-0,28 мм, достаточно установить одну шайбу (0,08 + 0,5 = 0,58, 0,28 + 0,5 = 0,78). Если же зазор будет в пределах 0,28-1,08 мм, установка шайбы не требуется.
1.10.ДОПУСКИ И ПОСАДКИ СОЕДИНЕНИЙ
СПОДШИПНИКАМИ КАЧЕНИЯ
Подшипники качения (шариковые, роликовые, игольчатые) являются точными изделиями, поэтому детали, контактирующие с ними (валы и корпуса) должны быть изготовлены не грубее 6-го (валы) или 7-го (корпуса) квалитетов.
В зависимости от точности изготовления и сборки (использу ется селективная сборка) подшипники качения выпускают сле дующих классов точности: 0, 6, 5, 4, 2, дополнительно 6Х и Т. Точность увеличивается от 0-го ко 2-му классу.
Классы точности (кроме 0-го класса) и, при необходимости, другие характеристики указывают на наружном кольце подшип ника перед его номером. Например, А125-205: здесь 205 — но мер подшипника, А — категория подшипника (также есть кате гории В и С, последняя не указывается), 1 — ряд момента тре ния, 2 — группа радиального зазора, 5 — класс точности. Если на кольце подшипника указан только его номер, например, 205, это означает, что данный подшипник относится к 0-му классу точ ности и категории С.
Классы точности 0 и 6 применяют наиболее часто, классы 5 и 4 — при больших числах оборотов и для обеспечения высокой точно сти вращения, класс 2 — для особо точных изделий.
Тела качения (шарики, ролики, иголки) и кольца подбирают при сборке селективным методом (число групп сортировки 10-15), поэтому внутренняя взаимозаменяемость подшипников качения ограниченная. Внешняя взаимозаменяемость у них полная, т. е. отказавший подшипник можно заменить аналогичным (того же номера и класса точности) экземпляром, при этом качество рабо ты изделия будет сохранено.
Присоединительные размеры подшипника, т. е. диаметр от верстия внутреннего кольца и наружный диаметр наружного коль ца, выполняют с постоянными (для данного интервала размеров и данного класса точности) отклонениями независимо от выбран ной посадки подшипника на вал и в корпусе. При этом измене ние характера соединения (посадки) внутреннего кольца на вал достигается путем изменения предельных размеров вала, т. е. по садки внутреннего кольца берут в системе отверстия. В свою оче редь, изменение посадки наружного кольца в корпус обеспечива ется изменением предельных размеров отверстия в корпусе, т. е. посадки наружного кольца подшипника в корпусе принимают по системе вала.
Посадки подшипников качения устанавливает ГОСТ 3325-85. Для получения посадок по внутреннему кольцу подшипника О- и 6-го классов точности валы могут быть изготовлены с поля ми допусков (рис. 61): гб, пб, т б , ic6, js6, h6, g6, f6 (для под шипников 5- и 4-го классов точности используют поля допусков 5-
и 4-го квалитетов, для 2-го класса точности — 4- и 3-го квалитетов). Для посадки наружного кольца подшипника в корпус ис пользуют поля допусков отверстий корпуса (см. рис. 61): Р7, N7, М7, К7, JS7, Н7, G7 (для подшипников 5- и 4-го классов точнос ти — поля допусков 6- и 5-го квалитетов, для 2-го класса точно сти — 5- и 4-го квалитетов). На рис. 61 поля допусков наружного кольца подшипника обозначены 10, 16, 15, 14, 12, внутреннего — LO, L6, L5, L4, L2 (цифра означает класс точности).
«Перевернутое» расположение полей допусков отверстий внут реннего кольца L0—L2 (по сравнению с расположением поля до пуска основного отверстия от нуля в «плюс») было принято для того, чтобы не вводить специальных посадок с небольшими натя гами для соединений валов с внутренними кольцами подшипни ков (стандартных посадок подобного типа недостаточно). Таким образом, посадки по внутреннему кольцу подшипника по сравне нию со стандартными изменяют свой характер в сторону умень шения зазоров (даже до перехода в натяг) и увеличения натяга: поля допусков с основными отклонениями п, ш, к с полем допуска внутреннего кольца образуют посадки с натягом (а не переход ные!), с основными отклонениями js, g, h — посадки переходные, с основным отклонением f — тип «скользящих» посадок (см. рис. 61).
Посадки на сборочных чертежах можно указывать в виде дро би (например, 0 30 L0/k6 и 0 62 JS7/10 на рис. 62) или в ви де поля допуска вала и отверстия (например, 0 30 кб и 0 62 JS7 на рис. 62).
Посадки подшипников качения выбирают в зависимости от ви да нагружения кольца, величины и характера действующих на грузок, условий эксплуатации, размеров и конструкции подшип ника и др.
Различают три вида нагружения: 1) местное (рабочая нагруз ка воспринимается одним и тем же местом дорожки качения; это обычно неподвижное кольцо, см. рис. 62); 2) циркуляционное (на грузка перемещается по кольцу или кольцо — относительно на грузки; это обычно вращающееся кольцо, см. рис. 62); 3) колеба тельное (кольцо воспринимает сумму постоянной большей и вра щающейся меньшей нагрузок).
При местной нагрузке кольцо монтируют с небольшим зазором или по легкой переходной посадке: h6, g6, f6 (внутреннее кольцо), JS7, Н7, G7 (наружное кольцо). Зазоры необходимы для предот вращения заклинивания тел качения под действием посадочного натяга на другом кольце, а также для обеспечения постепенного проворота кольца по посадочной поверхности под действием слу чайных толчков и вибрации. В этом случае износ беговой дорож ки, по которой перемещаются шарики или ролики, происходит более равномерно, что увеличивает срок работы подшипника.
При циркуляционной нагрузке кольцо устанавливают с натя гом, используя поля допусков: гб, рб, пб, m6, кб, js6 (внутреннее
Классы точности подшипников:
Рис. 61