
Аэрокосмическая техника высокие технологии и инновации – 2016
..pdfУДК 621.924.9
О ВОЗМОЖНОСТИ ИСПОЛЬЗОВАНИЯ ЛЬДА В КАЧЕСТВЕ АБРАЗИВНОГО МАТЕРИАЛА ПРИ ОЧИСТКЕ И БЕЗРАЗМЕРНОЙ ОБРАБОТКЕ ДЕТАЛЕЙ
ГАЗОТУРБИННОГО ДВИГАТЕЛЯ С.Е. Коретко, М.А. Ганзен
Рыбинский государственный авиационный технический университет имени П.А. Соловьева, Рыбинск, Россия
technology@rsatu.ru
Описываются возможности применения безразмерной механической обработки деталей газотурбинного двигателя частицами льда взамен пескоструйной обработки с целью повышения промышленной чистоты и снижения производственных затрат.
Ключевые слова: газотурбинный двигатель, деталь, очистка, безразмерная обработка, лед, ледоструйный аппарат.
Очистка поверхностей является важным этапом производства ряда ответственных деталей газотурбинного двигателя (ГТД). Как правило, эта технологическая операция применяется для придания (восстановления) требуемого внешнего вида поверхностей или их подготовки к покраске (удаления ржавчины, окалины, окислов и других загрязнений). От качества очистки во многом зависит итоговое качество поверхностей деталей, стойкость покрытий, а следовательно, долговечность двигателя и ряд других его характеристик, напрямую влияющих на конкурентоспособность. Это характерно и для прочих металлических изделий в сфере машиностроения, строительства и др.
Для очистки (зачистки) поверхностей часто применяется электрический или другой абразивный инструмент (шлифовальные машины). При этом работа (подача инструмента) выполняется вручную, что приводит к высокой трудоемкости операции и нестабильному качеству поверхностей, возможности их повреждения абразивным кругом.
Автоматизированная очистка поверхностей может быть выполнена при помощи пескоструйных аппаратов, очищающих поверхность за счет кинетической энергии абразивного материала
121
(песка), разгоняемого потоком сжатого воздуха [1]. Однако для этого способа очистки характерно образование пыли, заполняющей воздух рабочей зоны, что требует применения средств защиты органов дыхания или создания герметичных пескоструйных камер, возможности которых весьма ограничены из-за малой рабочей зоны.
В качестве альтернативы пескоструйным аппаратам используются установки для очистки поверхностей гранулами сухого льда (замороженной углекислоты) [2]. Мировым лидером в производстве таких аппаратов является фирма Kärcher (Германия). Гранулы сухого льда представляют собой абразивные тела, превращающиеся в углекислый газ при нагреве, сразу после контакта с очищаемой поверхностью. Это позволяет избежать запыления, однако приводит к росту загазованности рабочего пространства углекислым газом, а значит, требует применения мощной вентиляции при работе в помещении. Кроме того, сухой лед является сравнительно дорогим расходным материалом, требует особых условий производства, транспортировки и хранения, что связано с необходимостью применения криогенной техники.
На основе анализа преимуществ и недостатков существующих способов очистки предполагается разработка аппарата для очистки поверхностей изделий струей частиц обычного льда (замороженной воды).
Принцип действия предлагаемого устройства аналогичен существующим пескоструйным аппаратам и дробеметным установкам. Энергия сжатого воздуха в нем преобразуется в кинетическую энергию абразивных частиц, направляемых на очищаемую поверхность. Основное отличие заключается в том, что в качестве абразивного материала используется лед (замороженная вода). Схема устройства представлена на рисунке.
Работа устройства происходит следующим образом. В морозильный агрегат 3 заливается вода, которая охлаждается до отрицательной температуры и превращается в лед. С целью сокращения затрат времени на заморозку вода может быть предварительно охлаждена до температуры +2…+4 ºС. Морозильный агрегат представляет собой цилиндрическую емкость, охлаждаемую фреоном. Измельчитель 4 перемалывает лед в частицы нужного размера. Частицы льда под действием собственного веса
122
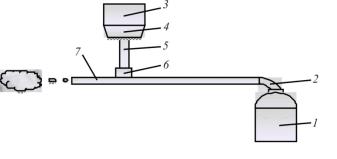
опускаются по трубопроводу 5 в эжектор 6. Воздух сжимается компрессором 1 и выпускается через трубопровод 2 в эжектор 6. Поток воздуха подхватывает частицы льда и выбрасывает их через распылитель 7 на очищаемую поверхность. Соударение частиц льда с поверхностью приводит к разрушению и удалению поверхностных загрязнений. После очистки поверхность обдувается сухим сжатым воздухом, идущим от компрессора (без льда), для исключения коррозии деталей.
Рис. Схема устройства для очистки частицами льда: 1 – компрессор; 2 – трубопровод подвода воздуха; 3 – морозильный агрегат;
4 – измельчитель; 5 – трубопровод подвода льда; 6 – эжектор; 7 – распылитель
Авторами статьи подготовлена заявка на полезную модель (патент) «Устройство для очистки поверхностей изделий частицами льда».
К преимуществам предлагаемого устройства можно отнести:
–экономичность (использование более дешевого расходного материала – воды – с меньшими расходами энергии на ее заморозку);
–экологичность (отсутствие пыли и углекислого газа в рабочей зоне, простота уборки производственного помещения);
–возможность мобильного исполнения устройства и его работы в неоснащенных местах (в условиях города, на строительных объектах, при наличии воды и электрической энергии);
–долговечность конструкции устройства (эксперименты показали, что твердость льда составляет порядка 150 HB, следовательно, частицы льда не будут изнашивать более твердые по
123
сравнению с ними детали аппарата, выполненные, к примеру, их конструкционной стали).
В настоящее время создается экспериментальный прототип устройства, с помощью которого планируется провести ряд научных исследований (определение оптимальной температуры и твердости льда для очистки деталей из различных конструкционных материалов, оптимального давления воздуха, расстояния и угла распыла частиц льда, размера этих частиц и других параметров устройства). Также планируется провести опытноконструкторские работы, направленные на создание высокоэффективного устройства для заморозки воды и перемалывания льда. На основе этого предполагается создать серийный образец ледоструйного аппарата, предназначенного для очистки и безразмерной обработки деталей ГТД, а также других металлических изделий в сфере машиностроения.
Список литературы
1.Устройство для пескоструйной обработки: пат. 115282
Рос. Федерация № 2011148988/02, МПК B24C 3/00 / Крашинников А.И., Кушнир А.П.; заявл. 02.12.2011, опубл. 27.04.2012. –
Бюл. № 12.
2.Устройство для очистки поверхности от загрязнений: пат. 68951 Рос. Федерация № 2007134067/22, МПК B24C 3/06 / Матвеев С.А., Йоффе Г.Б.; заявл. 12.09.2007, опубл. 10.12.2007. –
Бюл. № 34.
124
УДК 621.452.3.034
ИССЛЕДОВАНИЕ ДИНАМИЧЕСКОГО ПОВЕДЕНИЯ РОТОРА ПРИ КОНТАКТНОМ ВЗАИМОДЕЙСТВИИ СО СТАТОРОМ
А.Д. Куракин, М.Ш. Нихамкин, С.В. Семенов
Пермский национальный исследовательский политехнический университет, Пермь, Россия
dj-anton-pstu-2010@mail.ru, nikhamkin@mail.ru, sergey.semyonov@mail.ru
Приведены экспериментальное исследование и математическое моделирование поведения гибкого неуравновешенного ротора при его контакте со статором с учетом влияния величины дисбаланса, трения в контакте, упругой податливости статора. Математическая модель выполнена на основе модели ротора Джеффкотта и идентифицирована по экспериментальным данным.
Разработанная экспериментальная методика и полученные данные могут быть использованы при верификации и отработке расчетных методик. Разработанная методика математического моделирования может быть использована для выяснения и устранения причин задевания ротора о статор, а также как основа более сложных моделей, разрабатываемых с целью повышения вибрационной надежности роторных систем.
Ключевые слова: роторная динамика, роторная система, задевание ротора о статор, математическое моделирование, модель ротора Джеффкотта.
Работа агрегатов, в составе которых есть вращающиеся элементы, в определенных случаях сопряжена с возникновением процесса задевания вращающейся части (ротора) о невращающуюся часть (статор). Контактное взаимодействие происходит по различным причинам [1–3]. Оно сопровождается увеличением вибрации конструкции, повреждением или выходом из строя агрегата в целом. Наиболее остро проблема задевания встает в авиационном двигателестроении из-за тенденции планомерного уменьшения массогабаритных и увеличения мощностных характеристик. Закономерности поведения роторов при задевании о статор представляют интерес с точки зрения обеспечения вибра-
125
ционной безопасности турбомашин, авиационных двигателей, электрических машин, насосов и т.п. Снижение вибрации роторных машин – необходимое условие их надежной и безопасной эксплуатации [4].
Проблема динамики роторов в условиях контактного взаимодействия со статором неоднократно рассматривалась в работах отечественных и зарубежных ученых. В процессе задевания ротора
остатор возникают следующие явления: изменение собственных частот и форм колебаний, увеличение демпфирования, появление в спектре вибрации супер- и субгармоник, интенсивный износ контактирующих поверхностей, неравномерный нагрев ротора и обусловленный им эффект термического дисбаланса [5].
Данная работа посвящена экспериментальному и математическому исследованию вибрационных процессов, возникающих в результате задевания ротора о статор. Экспериментальное исследование проводилось на специальной роторной установке, позволяющей осуществлять задевание ротора о статор. Методика исследования подразумевала проведение двух серий экспериментов: с задеванием и без.
Наибольший практический интерес для представления результатов исследования имеет диаграмма Кэмпбелла, представляющая собой массив спектральных характеристик, построенных на разных частотах вращения. При анализе результатов эксперимента с отсутствием задевания ротора о статор (рис. 1) можно увидеть, что на диаграмме Кэмпбелла присутствуют супер- и субгармоники, но явной закономерности в возбуждении выявить невозможно. Хаотичное возбуждение супер- и субгармоник можно отнести к дефектам в подшипниках качения роторной системы. При анализе результатов исследования при задевании ротора
остатор (рис. 2) на диаграмме Кэмпбелла можно увидеть супер- и субгармоники на некоторых частотах в диапазоне частот от 0 до 800 Гц.
Области с данными гармониками обозначены 1 и 2 на рис. 2.
Характер возбуждения супер- и субгармоник в данном случае можно считать признаком задевания ротора о статор, так как он имеет явный упорядоченный характер и отличается от характера возбуждения, показанного на рис. 1.
126
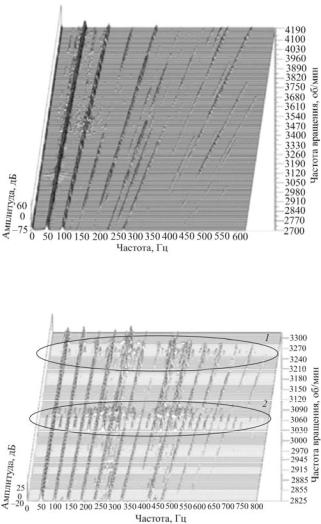
Рис. 1. Диаграмма Кэмпбелла для эксперимента без задевания о статор
Рис. 2. Диаграмма Кэмпбелла для эксперимента с задеванием ротора о статор
На этапе расчетного исследования на основе простейшей модели ротора Джеффкотта (Jeffcott rotor model) была разработана математическая модель, состоящая из системы двух дифференциальных уравнений:
127
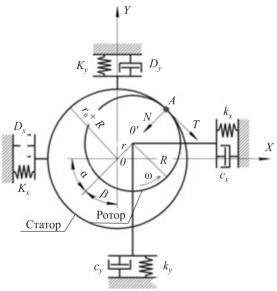
x |
y |
2 |
|
|
||||||||
mx cx x kx x Kx |
|
|
Kx |
|
|
Dx x em |
cos t, |
|||||
|
|
|
|
|||||||||
r |
r |
|
|
|
||||||||
|
|
y |
x |
|
|
|
||||||
|
2 |
sin t. |
||||||||||
my cy y ky y Ky |
|
|
|
|
Ky |
|
|
|
Dy y em |
|
||
|
|
|
|
|
|
|||||||
r |
r |
|
|
|
||||||||
|
|
|
Расчетная модель роторной системы показана на рис. 3.
Рис. 3. Расчетная схема
Для решения системы дифференциальных уравнений была разработана программа в среде Mathcad. Использовался метод Рунге–Кутты четвертого порядка с фиксированным шагом по времени, равным 0,001 с. Полученные результаты также были представлены в виде диаграммы Кэмпбелла, на ней можно увидеть возбуждение гармоник выше первой гармоники (1х) на тех частотах вращения, на которых происходило задевание. Также происходит возбуждение супер- и субгармоник.
Полученные результаты расчетного и экспериментального исследований согласуются и свидетельствуют о едином признаке задевания ротора о статор.
128

Рис. 4. Диаграмма Кэмпбелла, построенная по расчетным виброперемещениям
Разработанные расчетные и экспериментальные методики могут быть использованы для улучшения эксплуатационных характеристик роторных систем, а также послужить основой для последующихкомплексныхисследованийзадеванияротораостатор.
Список литературы
1.Костюк А.Г., Шатохин В.Ф., Волоховская О.А. Движение неуравновешенного ротора с задеванием о статор // Теплоэнерге-
тика. – 2012. – № 2. – С. 3–11.
2.Иноземцев А.А., Нихамкин М.Ш., Сандрацкий В.Л. Динамика и прочность авиационных двигателей и энергетических установок. – М.: Машиностроение, 2008. – Т. 4. – 192 с.
3.Белоусов А.И., Балякин В.Б., Новиков Д.К. Теория и проектирование гидродинамических демпферов опор роторов / под ред. А.И. Белоусова. – Самара: Изд-во Самарского НЦ РАН, 2002. – 335 с.
4.Кельзон А.С., Журавлев Ю.Н., Январев Н.В. Расчет и конструирование роторных машин. – Л.: Машиностроение, 1977. – 288 с.
5.Muszynska A. Rotordynamics / Taylor & Francis Group. NW. – USA, 2005. – 1054 p
129
УДК 621.7
МОДЕЛЬ ДЕФОРМАЦИОННОГО ИЗМЕНЕНИЯ ПОРИСТОСТИ ПОВЕРХНОСТНОГО СЛОЯ ДЕТАЛЕЙ ПОРОШКОВОЙ МЕТАЛЛУРГИИ ПРИ ВИБРАЦИОННОЙ ОБРАБОТКЕ
Ю.П. Анкудимов1, И.В. Садовая1, Ю.Г. Чернега2
1 Донской государственный технический университет, Ростов-на-Дону, Россия,
2 Таганрогский политехнический институт – филиал Донского государственного технического университета, Таганрог, Россия
i_sagulenko@mail.ru
Приводятся результаты моделирования пористости поверхностного слоя деталей из порошковых материалов при их обработке в вибрирующих гранулированных средах (вибрационная обработка). Представлена методика расчета пористости порошкового материала по глубине поверхностного слоя деталей.
Ключевые слова: детали порошковой металлургии, пористость, вибрационная обработка.
Учитывая роль поверхностного слоя при работе деталей в узлах авиационной техники, развитие технологии получения порошковых деталей перспективно осуществлять на основе формирования благоприятной поровой структуры материала поверхностности, например бипористости рабочего и предрабочего слоя [1].
Одним из методов модифицирования рабочих поверхностей порошковых спеченных деталей являются методы поверхностнопластического деформирования, в частности вибрационная обработка в твердой гранулированной среде [2].
Детали порошковой металлургии подвергаются таким же технологическим операциям вибрационной обработки, как и детали из компактных материалов: скруглению острых кромок, сглаживанию микронеровностей поверхности, упрочнению поверхностного слоя. При этом взаимодействие частиц обрабатывающей среды с поверхностью детали оказывает влияние и на такой важный показатель, как пористость поверхностного слоя. Для выявления взаимосвязи степени изменения пористости поверхности при единичном контакте ее с частицей рабочей среды, имею-
130