
Аэрокосмическая техника высокие технологии и инновации – 2016
..pdf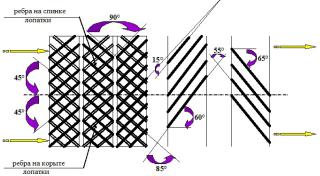
цию трехсекционной вихревой матрицы, в которой угол наклона ребер на спинке (корыте) изменяется на 270° при переходе от одной секции к другой, и двух рядов наклонных прерывистых перемычек (рис. 3).
Рис. 3. Перспективная система охлаждения сопловой лопатки
Предложенная схема охлаждения позволила еще более повысить уровень интенсификации теплообмена на участке матрицы (до 30 %). Уровень же интенсификации теплообмена на наклонных перемычках остался прежним и превышает аналогичные характеристики для базового варианта сопловых лопаток на 5–15 %.
Список литературы
1.Викулин А.В., Ярославцев Н.Л., Земляная В.А. Методология доводки теплонапряженных деталей газотурбинных двига-
телей // Труды МАИ. – 2016. – № 88. – С. 8–29.
2.Тепловые испытания и доводка охлаждаемых лопаток газовых турбин / А.В. Викулин, В.Г. Попов, Н.Л. Ярославцев
[и др.]. – Кострома: КПД, 2012. – 568 с.
3.Попов В.Г., Викулин А.В., Чеснова В.А. Совершенствование конструкции охлаждаемых лопаток высокотемпературных газовых турбин с целью повышения надежности и ресурса работы современных авиационных ГТД и энергетических ГТУ // Вестник Рыбинской государственной авиационной технологической академии им. П.А. Соловьева. – 2012. – № 2 (23). – С. 7–11.
161
УДК 620.17
ОЦЕНКА ВОЗМОЖНОСТИ ИСПРАВЛЕНИЯ ДЕФЕКТОВ ПРЕДНАПРЯЖЕННОГО СОСТОЯНИЯ ПУТЕМ МЕХАНИЧЕСКОЙ ОБРАБОТКИ С ЦЕЛЬЮ ПОЛУЧЕНИЯ ЗАДАННЫХ ОСТАТОЧНЫХ НАПРЯЖЕНИЙ В ДЕТАЛЯХ ИЗ ТИТАНОВЫХ СПЛАВОВ
Е.В. Колодочкина, К.Н. Поликарпова
Пермский национальный исследовательский политехнический университет, Пермь, Россия
Katekolodochkina@rambler.ru, mail_poli@mail.ru
Рассмотрен метод рентгеновской дифрактометрии для измерения остаточных напряжений с помощью роботизированного комплекса. Дано описание методики измерений остаточных напряжений. Результаты измерений на круглом образце в различных сечениях и под разными углами приведены в графической форме. Сделан вывод о характере остаточных напряжений.
Ключевые слова: остаточные напряжения, роботизированный комплекс, рентгеновская дифрактометрия.
Всовременной авиационной промышленности имеется большое количество изделий, характеризуемых высокой конструктивной сложностью, повышенными требованиями к точности изготовления, качеству поверхностей, а в итоге и к эксплуатационным свойствам продукции, ресурсу ее работы.
При существующих технологических процессах изготовления деталей встречаются серьезные затруднения в связи с появлением общего коробления, которое связано с перераспределением остаточных напряжений, возникающих в детали на всех этапах ее изготовления. Известно, что после любого вида обработки: механической, термической или термической комбинированной с химической и т.д. – в результате изменения структуры материала изделия приобретают новое свойство – состояние остаточной напряженности.
Внастоящее время существует много методов, позволяю-
щих как оценивать, так и прогнозировать остаточные деформации деталей, но все они носят частный характер и, как правило, не позволяют проектировать технологические процессы боль-
162

шинства подобных деталей, устраняющих коробление. Поэтому вопрос устранения остаточных напряжений остается попрежнему открытым.
Применяемые технологические процессы для изготовления деталей чаще всего не учитывают возможное наличие остаточных напряжений, приобретаемых в ходе процесса обработки. Особенно данное утверждение актуально применительно к такому типу деформаций, как преднапряженное состояние. Такие деформации приводят к многочисленным дефектам деталей, влияют на эксплуатационные свойства изделия.
В статье В.В. Карманова и соавт.1 рассматриваются остаточные напряжения, их влияние на детали, в особенности при производстве ответственных изделий. Предлагается выбрать метод для измерения напряжений. Авторы формулируют требования, предъявляемые к методу и оборудованию для контроля остаточных напряжений в лабораторных условиях и условиях производства. В результате приведено обоснование выбора метода рентгеновской дифрактометрии. Для реализации этого метода была создана лаборатория, оснащенная роботизированным комплексом. Были проведены измерения плоских и круглых образцов, деталей сложной формы.
Результаты, приведенные в статье, показывают широкие возможности применения роботизированного измерительного комплекса для исследования влияния различных технологических операций на величину и знак остаточных макронапряжений. Применение роботизированного комплекса обеспечивает повторяемость результатов и унификацию технологии измерений деталей различных видов и типоразмеров. Результаты исследований могут использоваться при создании баз данных и математических моделей для проектирования вновь разрабатываемых технологических процессов, а также для оптимизации существующих технологических процессов.
1 Опыт применения роботизированного комплекса Xstress для измерения технологических остаточных напряжений / В.В. Карманов, В.Н. Трофимов, А.С. Нуртдинов, С.Н. Звонов // Вестник Магнитогорского государственного технического университета им. Г.И. Носова. – 2015. – № 1 (49). – С. 55–59.
163
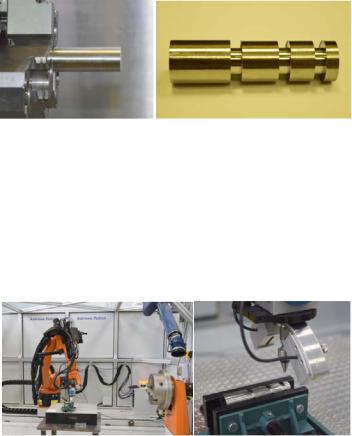
В настоящей работе была поставлена цель разработать унифицированную методику разработки технологического процесса с гарантированным получением остаточных напряжений в поверхностном слое.
Для достижения поставленной цели была взята заготовка в виде прутка (рис. 1). В ходе работы пруток был проточен на то-
карном станок Amada Machine Tools A-12 с ЧПУ Fanuc 18i-TB,
в результате чего был получен образец в виде вала (рис. 2), на котором проводили измерения остаточных напряжений в поверхностном слое.
Рис. 1. Заготовка |
Рис. 2. Образец |
Использовался роботизированный комплекс измерения остаточных напряжений Xstress Robot (рис. 3). Принцип его работы основан на методе рентгеновской дифрактометрии. С помощью гониометра (рис. 4), который может работать на роботе в любом положении, посылаются лучи в точку измерения на деталь. Отраженные лучи улавливает линейный датчик изображения. На гониометре установлен сменный коллиматор, который позволяет обеспечивать размер пятен от 1 до 5 мм.
Рис. 3. Xstress Robot |
Рис. 4. Образец |
164
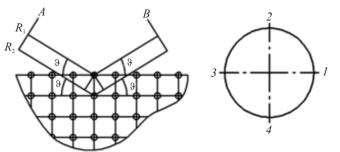
Суть метода рентгеновской дифрактометрии (рис. 5) заключается в том, что плоскопараллельный монохроматический пучок рентгеновских лучей падает под углом ϑ на кристаллическую решетку. Попадая на атомы вещества, рентгеновские лучи рассеиваются, причем наибольшей интенсивностью будут обладать лучи, отраженные под углом ϑ. Но эти лучи, попадающие на различные атомы решетки, также взаимодействуют между собой.
Условие усиления соблюдается, если колебания находятся в одной фазе и разность длины лучей (от плоскости А до плоскости В) равна целому числу волн. Если d – расстояние между кристаллографическими плоскостями, то 2d sin n , где λ – длина волны рентгеновского луча; n – целое число (n = 1, 2, 3, …) – порядок отражения.
Рис. 5. Метод рентгеновской |
Рис. 6. Сечение образца |
дифрактометрии |
|
Данный образец был разбит в сечении на четыре сектора (рис. 6) с интервалом в 90°. Далее последовательно на каждом проточенном диаметре в каждом секторе было взято по одной точке Р3, Р4, Р5, после чего в каждой точке проводились измерения под углом 0°, –45° и –90°. Полученные данные обработали статистически и математически в программе Microsoft Excel. Результаты представлены ниже в виде графиков (рис. 7).
Предполагалось, что в состоянии поставки в заготовке были заложены большие остаточные напряжения, при этом они достаточно непредсказуемые как по знаку, так и по значению.
При обработке результатов измерения выявили, что в трех секторах из четырех по всей длине, т.е. в трех измеренных точ-
165
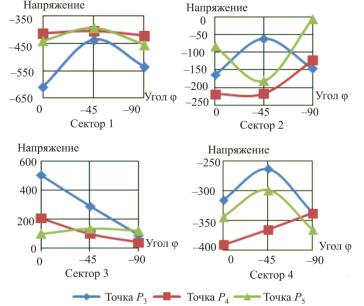
ках, присутствуют сжимающие напряжения, а в одном секторе по всей длине наблюдаются растягивающие напряжения. При этом присутствует большой разброс значений напряжений, соответственно, можно предположить, что до обработки присутствовало преднапряженное состояние.
Рис. 7. Значения напряжений в точках сечения профиля
На основе полученных данных можно сделать вывод, что необходимо вводить отпуск и исключать преднапряженное состояние, чтобы остаточные напряжения нормализовались по всей длине для гарантии качества получаемых изделий. На базе этого следует разработать технологию с гарантированным получением постоянных по знаку и по значению остаточных напряжений.
Данный вопрос требует подробного изучения в целях управления и оптимизации технологических параметров обработки для обеспечения требуемых показателей качества и повышения надежности ответственных деталей авиационнокосмической техники.
166
УДК 621-941
ПРОБЛЕМЫ ОПТИМИЗАЦИИ ТРАЕКТОРИИ ДВИЖЕНИЯ РЕЖУЩЕГО ИНСТРУМЕНТА ПРИ ТОКАРНОЙ ОБРАБОТКЕ ДЕТАЛЕЙ ГАЗОТУРБИННОГО ДВИГАТЕЛЯ
А.А. Северцов
Рыбинский государственный авиационный технический университет имени П.А. Соловьева, Рыбинск, Россия
technology@rsatu.ru
Рассматриваются проблемы оптимизации траектории движения режущего инструмента при токарной обработке для уменьшения затраченного времени при обработке деталей газотурбинной техники. Анализируются возможные путиих решения.
Ключевые слова: газотурбинный двигатель, деталь, токарная обработка, траектория, оптимизация, время.
Современная техника при повышении качества и снижении времени на обработку изделий расширила состав и количество деталей машин сложной геометрической формы, изготовление которых осуществляется на дорогостоящих многоцелевых станках и на станках с ЧПУ. В современном машиностроении, особенно в авиационной и космической отраслях, большинство продукции выпускается по индивидуальным требованиям заказчика, для чего используется гибкоструктурное производство на базе быстропереналаживаемого автоматизированного оборудования (станков с ЧПУ, в том числе с прямым управлением от ЭВМ).
Проблемами оптимизации траектории движения при токарной обработке, сложной геометрии детали с выбранным инструментом, позволяющими разработать программно-технологи- ческие методы повышения эффективности и точности обработки сложнопрофильных деталей при наименьших затратах времени на станках с ЧПУ, в большинстве случаев являются [1–4]:
–закономерности формирования отклонений контура при резких изменениях вектора силы резания, возникающих в результате изменения припуска и кривизны обтачиваемой поверхности;
–раскрытие технологических связей процесса точения, что позволило бы разработать технологические рекомендации по вы-
167
бору последовательности выполнения переходов, по программированию траектории и направления обхода контура, по выбору расстояния между смежными поверхностями и величины перекрытия с учетом параметров применяемых пластин;
–программируемые гибкие технологические циклы доработки углов сопряжения смежных поверхностей контура, позволяющие в автоматическом режиме пластиной меньшего радиуса
ишириной выбрать в углах и карманах остающийся материал;
–выявление технологических связей, позволяющих предложить методы управления точностью контурного точения на этапе разработки управляющих программ; они предусматривают выбор режимов обработки и геометрии пластины, при которых сила резания оказывает на отклонения контура минимальное влияние, а также коррекцию управляющей программы по результатам измерения первой изготовленной детали.
Изготовление на станках с ЧПУ многоэлементных деталей сложной геометрии – корпусов топливных и гидравлических систем аэрокосмической техники, полостей штампов и пресс-форм, шаблонов, кулачков, лопаток турбин и т.д. – представляет сложную технологическую задачу.
Входные параметры заготовки (припуск, твердость, жесткость) и инструмента (износ, затупление) изменяются как от детали к детали, так и в пределах одной детали. Эти параметры в большинстве случаев являются случайными, между тем как учесть при программировании только систематические составляющие этих факторов непросто. Все эти вопросы особенно усугубляются при обработке.
При токарной обработке программирование траектории затруднено из-за сложности учета углов и неровностей поверхности и снимаемого припуска при имеющихся режимах, изменения глубины, скорости точения и угла контакта пластины с обрабатываемой поверхностью – все это может повлиять на скол или повреждение детали.
Достижение требуемой точности обработки путем уменьшения влияния упругих деформаций при выполнении нескольких чистовых проходов существенно снижает производительность станка за счет увеличения времени. Если на универсальном станке рабочий может в процессе обработки учесть изменения припуска,
168
степень затупления инструмента и угол его контакта с заготовкой, то на станке с ЧПУ оператор такой возможности не имеет.
Список литературы
1. Солкин А.Ю. Компьютерные технологии управления в мехатронике. Оптимизация режимов резания при высокоскоростной обработке на металлорежущем оборудовании с ЧПУ // Вестник Волжского университета имени В.Н. Татищева. – 2011. –
№2. – С. 66–68.
2.Серебреницкий П.П., Схиртладзе А.Г. Технология, оборудование и автоматизация машиностроительных производств // Программирование для автоматизированного оборудования. –
М.: Высшая школа, 2003. – С. 62–65.
3.Солкин А.Ю. Методы оптимизации работы металлорежущего оборудования с ЧПУ в условиях высокоскоростной обработки // Вестник Волжского университета имени В.Н. Татище-
ва. – 2011. – № 2. – С. 138–139.
4.Кузнецов П.К., Солкин А.Ю. Проблема оптимизации NC-программ для механообрабатывающих станков с ЧПУ // Вестник Волжского университета имени В.Н. Татищева. – 2011. –
№2. – С. 28–30.
УДК 621.9.06:513
ИССЛЕДОВАНИЕ СЛОЖНЫХ КОНСТРУКЦИЙ В САПР SOLIDWORKS И СРЕДЕ ДИНАМИЧЕСКОГО МОДЕЛИРОВАНИЯ MATLAB
Д.Р. Мухатматханов, Ю.В. Идрисова
Уфимский государственный авиационный технический университет, Уфа, Россия
thedangl@inbox.ru
Представлен метод трансляции 3D-моделей механизмов САПР SolidWorks в среду динамического моделирования Matlab при проектировании сложных конструкций. Визуально показан процесс трансляции, оптимизации и анализа на примере поворотного стола, включающего статор, ротор, планшайбу. Рассмотрены возможные варианты анализа динамики механизма поворотного стола вращения в среде Matlab.
169
Ключевые слова: SolidWorks, SimMechanics, Matlab, пово-
ротный стол, трансляция.
В настоящее время современные информационные технологии открывают новые возможности при проектировании перспективных технических систем. В работе рассматриваются возможности использования трансляции 3D-модели механизмов САПР SolidWorks в среду динамического моделирования Matlab (SimMechanics) механизмов. SimMechanics – это библиотека
Simulink для физического моделирования механических систем, которая позволяет создавать модели механических объектов при проектировании сложных конструкций и совместно с другими пакетами MathWorks разрабатывать реальные прототипы систем управления.
Процесс создания математической модели системы управления в Simulink из 3D-модели элементов в SolidWorks состоит из нескольких этапов: экспорт 3D-модели SolidWorks в xml-файл, импорт xml-файла в среду Simulink, анализ динамики системы управления, выбор закона управления и исполнительного элемента в среде Simulink.
Проведено исследование функционирования поворотного стола, включающего статор, ротор, планшайбу. Проведена трансляция 3D-модели механизма САПР SolidWorks в среду динамического моделирования Matlab [1]. Осуществлены доработки динамической модели в среде Matlab (рисунок), обеспечивающие дискретное изменение вращающего момента на планшайбе.
При трансляции телам модели Simulink передаются соответствующие массоинерционные характеристики компонентов сборки SolidWorks. Для обеспечения визуализации модели Simulink геометрия элементов сборки SolidWorks передается с помощью транслируемых stl-файлов.
Моделирование поведения объекта в среде Matlab позволяет проводить анализ динамических характеристик: переходного процесса и частотных характеристик.
Результаты моделирования при структурном и кинематическом синтезе механизмов могут быть использованы с целью повышения точности позиционирования. Можно также оценить погрешность позиционирования планшайбы в зависимости от
170