
Аэрокосмическая техника высокие технологии и инновации – 2016
..pdf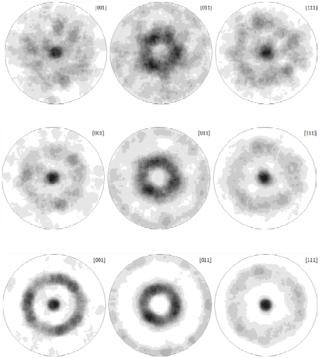
зерен состояло из шести элементов, во втором количество могло достигать 18, в третьем – 26. На рис. 2 представлены прямые полюсные фигуры, полученные в результате экспериментов.
а
б
в
Рис. 2. Полюсные фигуры после одноосного растяжения поликристалла с учетом 6 (а), 18 (б) и 26 (в) граничащих зерен
Во всех экспериментах можно говорить о формировании кристаллографической текстуры аксиального типа, однако степень остроты текстуры напрямую зависит от количества учитываемых «соседей». Из этого можно сделать два вывода: вопервых, учет большего количества окружающих элементов зерна не нарушает адекватность модели, так как не меняет тип текстуры, во-вторых, параметры выбранной модели ротаций стоит подбирать исходя из количества учитываемых «соседей». Кроме того, подробный учет фрагментно-зеренной структуры материала
241
позволит более точно описывать такие важные процессы, как фрагментация и дробление зерен. Таким образом, учет большего числа окружающих элементов можно рекомендовать к использованию в моделях подобного рода.
Список литературы
1.Трусов П.В., Волегов П.С., Кондратьев Н.С. Физические теории пластичности: учебное пособие. – Пермь: Изд-во Перм. нац. исслед. политехн. ун-та, 2013. – 244 с.
2.Тельканов М.А., Волегов П.С. Описание ротаций кристаллических решеток и фрагментации зерен при интенсивных неупругих деформациях поликристаллов // Вестник Тамбовского университета. Сер.: Естественные и технические науки. – 2016. –
Т. 21, № 3. – С. 1338–1341.
3.Хирт Д., Лоте И. Теория дислокаций. – М.: Атомиздат, 1972. – 600 с.
4.Попович В., Кондир А., Плешаков Е. Технология конструкционных материалов и материаловедение. – Львов: Папуга, 2004. – 422 с.
УДК 621.9
ТЕХНОЛОГИЧЕСКОЕ ОБЕСПЕЧЕНИЕ КОРРОЗИОННОЙ СТОЙКОСТИ ДЕТАЛЕЙ И УЗЛОВ МАШИН
В.В. Устименко
Рыбинский государственный авиационный технический университет имени П.А. Соловьева, Рыбинск, Россия
ustimenko-veronika-valerevna@yandex.ru
Рассматривается влияние коррозионной стойкости на параметры качества поверхностного слоя.
Ключевые слова: коррозионная стойкость, поверхностный слой, наклеп, шероховатость, энергетический коэффициент, подача, скорость резания.
В процессе эксплуатации рабочие поверхности деталей машин испытывают постоянное или циклическое воздействие агрессивной среды при одновременном внешнем механическом
242
нагружении, что приводит к разрушению поверхности металла с постоянным изменением размеров формы детали. Разнообразие условий эксплуатации обусловливает различные виды изнашивания рабочих поверхностей деталей машин и аппаратов.
Наиболее распространенный вид разрушения – коррозион- но-механическое изнашивание, происходящее в результате механических воздействий, сопровождающихся химическим или электрохимическим взаимодействием металла со средой. В результате совместного воздействия механического и коррозионного факторов в поверхностных слоях металла происходят взаимосвязанные явления, способствующие активации процессов упругопластического деформирования, химических и электрохимических реакций и т.д. Поэтому в реальных условиях интенсивность изнашивания при коррозионно-механических воздействиях определяется величиной и характером механических нагрузок, активностью коррозионной среды и физико-химическими свойствами конструкционных материалов. Поэтому исследование в области обеспечения коррозионной стойкости является актуальным [1].
Качество поверхности влияет на коррозионную стойкость. Бесспорным является то, что с уменьшением шероховатости поверхности коррозионная стойкость повышается. Это объясняется тем, что коррозирующие вещества собираются на дне впадины гребешков, образуя очаги коррозии. Чем меньше глубина впадин, тем меньше условий для образования очагов коррозии. Поэтому с уменьшением шероховатости разрушение поверхности уменьшается.
Поверхностный наклеп уменьшает коррозионную стойкость и, наоборот, увеличивает коррозионно-усталостную прочность. Как известно, при поверхностном наклепе имеет место неоднородная пластическая деформация, приводящая к возникновению разности потенциалов между неодинаково деформированными зернами металла. Так, ферритные зерна наклепываются значительно сильнее, чем перлитные. При этом ферритные зерна становятся анодами, а перлитные – катодами. Это значительно увеличивает количество коррозионных микроэлементов и ведет к общему усилению процесса коррозии. Повышение коррозионноусталостной прочности при наклепе объясняется уплотнением поверхностного слоя и закрытием путей для проникновения активных сред внутрь металла через дефекты поверхности, а также
243
возникновением при наклепе благоприятно действующих остаточных напряжений сжатия. Если при механической обработке в поверхностных слоях появляются растягивающие остаточные напряжения, то при соприкосновении с активной средой возникает коррозионное растрескивание деталей. [1]
Для того чтобы произошел процесс коррозионного растрескивания, необходимо наличие поверхностных или внутренних растягивающих напряжений.
При увеличении величины приложенных напряжений уменьшается время до полного разрушения металла. Для коррозионного растрескивания обычно необходимы высокие напряжения, приближающиеся к пределу текучести, однако часто разрушение может наступить и при напряжениях, значительно меньших предела текучести.
Наиболее эффективный метод повышения устойчивости металлов против коррозионного растрескивания состоит в использовании соответствующих конструктивных мероприятий и способов обработки, сокращающих до минимума величину остаточных напряжений. Если остаточные напряжения неизбежны, успешно может быть применена термообработка, которая их снимает. Если позволяют условия, может быть использована, например, дробеструйная обработка, вызывающая сжимающие поверхностные напряжения, которые впоследствии дают возможность нагружать материал, не вызывая напряженного состояния поверхности. Одним из методов, который получает все большее признание и который связан с электрохимическим фактором процесса растрескивания, является применение катодной защиты. Среди методов исследования взаимодействия напряжений и химических факторов можно особо отметить изучение зависимости величины катодного тока, необходимого для защиты, от величины механических напряжений.
Сравним теперь скорости коррозии обработанного и необработанного материалов при одинаковых условиях [2]:
Vк |
|
G |
, |
(1) |
|
V |
G |
||||
|
|
|
|||
к0 |
|
0 |
|
|
где Vк – скорость коррозии материала детали после механической обработки; Vк0 – скорость коррозии металла детали сравнения;
G – изменение внутренней энергии материала детали после ме-
244
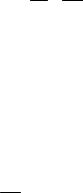
ханической обработки; G0 – изменение внутренней энергии материала детали сравнения.
Рассматривая процесс коррозии одиночного образца в замкнутом объеме электролита, можно прийти к выводу, что материал поверхностного слоя образца неоднороден и состоит из участков с разным количеством внутренней энергии, на поверхности образца будут образовываться микрогальваноэлементы, разница энергий которых Gi будет определяться выражением [2]
Gi = Gi – Gri, |
(2) |
гдеGi – полнаяэнергияматериала; Gri – энергияГиббсаматерила. Просуммировав величины Gi по всей площади образца,
получим выражение для определения энергий G и G0 [2]:
G = G – Gr = Gм, |
(3) |
G0 = G0 – Gr = Gм0 . |
(4) |
Подставляявыражения(3) и(4) ввыражение(1), получим[2]
Vк Gм ,
Vк0 Gм0
где Gм и Gм0 – механическая внутренняя энергия детали и образ-
ца сравнения.
Отношение внутренних энергий материала поверхностного слоя детали и образца сравнения можно представить энергетическим коэффициентом Кэ.
Управление коррозионной стойкостью заключается в использовании энергетического коэффициента Кэ, характеризующего термодинамическую активность материала поверхностного
слоя изделия [2]: Кэ Gм .
Gм0
Таким образом, данное исследование позволяет определить зависимость энергетического коэффициента от подачи, скорости резания для возможного прогнозирования коррозионной стойкости деталей машин, что является актуальным на современном этапе развития технологии машиностроения.
245
Список литературы
1.Безъязычный В.Ф. Метод подобия в технологии машиностроения. – М.: Машиностроение, 2012. – 320 с.
2.Федонин О.Н. Технологическое обеспечение коррозионной стойкости деталей из конструкционных сталей в условиях электрохимической коррозии: автореф. … д-ра техн. наук. –
Брянск, 2004. – 36 с.
УДК 621.924.1
ИССЛЕДОВАНИЕ ТЕХНОЛОГИЧЕСКОЙ СИСТЕМЫ ШЛИФОВАНИЯ
В.П. Ларшин1, Н.В. Лищенко2
1 Одесский национальный политехнический университет,
2 Одесская национальная академия пищевых технологий, Одесса, Украина
VPLarshin@rambler.ru
Выполнено исследование технологической системы шлифования, представленной в виде модели системы управления с соответствующими параметрами: входными, состояния и выходными. Показано, что процесс шлифования определяется совокупностью входных параметров, действующими возмущениями и взаимно влияющими друг на друга системными механизмами шлифования поверхности и износа шлифовального круга. Эти механизмы формируют выходные параметры процесса, относящиеся к обрабатываемой заготовке и шлифовальному кругу.
Ключевые слова: система, параметры, вход, состояние, выход, мониторинг, технологическая диагностика.
Теория технических систем охватывает системы-конструк- ции и системы-процессы. При этом системы-конструкции предназначены для реализации систем-процессов. В этом смысле технологическая система механической обработки, например, шлифования, является системой-конструкцией, которую собирает технолог для реализации системы-процесса, например, процесса профильного зубошлифования. В соответствии с теорией техни-
246
ческих систем одним из важных начальных этапов разработки систем является их адекватное описание (description) и моделирование (simulation), которые могут быть представлены в соответствующих форматах: словесное описание (текст) на обычных языках, специальные знаковые системы (языки программирования), блок-схемы, графы, математическая модель, временная диаграмма, комбинированный способ и т.п. Выбор соответствующего способа описания и моделирования зависит от цели исследования. Если такой целью является создание условий, обеспечивающих требуемое протекание процесса, т.е. выполнение необходимого алгоритма функционирования, то говорят об управлении процессом [1] и соответствующем алгоритме управления. В этом случае разрабатываемую техническую систему представляют в виде модели системы управления, имеющей вход, состояние и выход. При таком моделировании система – это математическая абстракция, принимаемая в качестве модели динамического явления [2], которая представляет это динамическое явление в терминах математических отношений. Модель системы управления характеризуют ее входом, выходом и состоянием. Вход представляет собой внешние силы в виде множества временных функций, действующих на динамическое явление (процесс). Выход представляет собой меры непосредственно наблюдаемого поведения этого явления (процесса). Зависимость между входом и выходом может быть сильной или слабой. Базовой характеристикой любого динамического явления является поведение системы, на котором в любой момент времени отражаются не только текущие приложенные силы (входные параметры), но и те из них, которые были приложены в прошлом по отношению к данному моменту времени. В этом смысле динамическое явление обладает памятью, в которой сохраняется влияние прошлых приложенных сил (параметров). При разработке модели указанное состояние системы представляет собой векторную функцию времени. Знание состояния системы в любой момент времени и знание указанных последовательно прилагаемых сил достаточно, чтобы определить выход и состояние системы в любой момент времени t > t0, т.е. начиная с момента t0. Обобщенные отношения между входом, состоянием и выходом абстрактной технической системы можно показать в виде схемы [2] на рисунке.
247
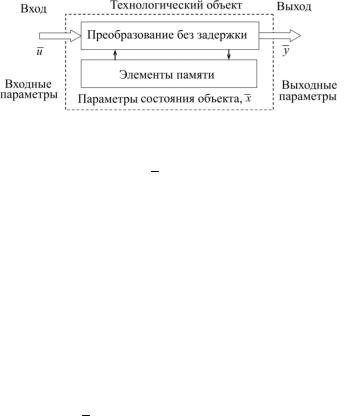
Рис. Концептуальное представление технической системы на основе модели «вход – состояние – выход» (возмущения не показаны)
В общем случае вход u , состояние x и выход y системы
являются векторными функциями времени, имеющими соответствующую размерность. Зависимость указанных функций от времени предполагает потенциальную возможность использования частотного подхода к исследованию системы.
Для всех указанных явлений (физических и иных) справедливы следующие принципы теории систем: 1) физической реализуемости, 2) детерминированности (определенности), 3) стохас-
тичности [2]. Первый принцип (non-anticipation principle) означа-
ет, что состояние и выход системы в любой момент времени t0 может быть функцией только тех входных величин, которые имели место при t < t0. Второй принцип характеризует детерминированную систему (deterministic system), у которой состояние и выход могут быть определены с уверенностью на основе полного знания ее состояния в момент времени t0 (необходимое условие) и знания входа u (t) на интервале времени t ≥ t0 (достаточное ус-
ловие). Третий принцип определяет стохастическую систему (stochastic or nondeterministic system), для которой указанное знание о состоянии и входе является достаточным, только чтобы обеспечить статистическое описание (statistical description) состояния и выхода системы в момент времени t. Указанная особенность автоматизированных технологических систем предполагает использование теоретико-вероятностного подхода для их исследования.
Современные исследования автоматизированной технологической системы шлифования на станках с ЧПУ выполняют по различным направлениям, принимая за основу соответствующий предмет исследования в объекте исследования. Когда объектом исследования является процесс в технологической системе, то
248
предметом исследования могут быть разные его свойства, начиная от методов формообразования (например, профильное зубошлифование или зубошлифование червячным кругом), выбора элементов технологической системы и заканчивая разработкой мониторинга процесса [3], технологической диагностикой и адаптивными системами.
Процесс шлифования представляют в качестве звена системы управления: разомкнутой (без обратной связи) или замкнутой (с обратной связью). Выходные параметры технологической системы (результат ее функционирования) вытекают из принципа целеполагания, который, в свою очередь, вытекает из функционального назначения изготовляемой детали, что нашло отражение в современной функционально-ориентированной технологии. Обычно выходными являются численные значения параметров точности обработки и качества обработанной поверхности. Например, применительно к процессу профильного зубошлифования к числу точностных параметров относятся: полная погрешность профиля, погрешность формы профиля, погрешность угла профиля, полная погрешность линии зуба, погрешность формы линии зуба, погрешность угла наклона зуба, погрешность шага, накопленная погрешность шага, радиальное биение. Эти параметры при зубошлифовании оценивают с помощью встроенной измерительной системы тактильного (tactile) типа, например, измерительной системы Renishaw.
Современный уровень развития автоматизированной технологической системы шлифования на станках с ЧПУ предполагает мониторинг параметров состояния этой системы и ее технологическую диагностику для поддержания стабильности функционирования. Например, к числу таких параметров при профильном зубошлифовании относятся следующие: Q'w, V'w, Т, F, АЭ. Здесь
Q'w (specific material removal rate) и V'w (specific material removal) –
удельные параметры съема припуска; Т, F – температурный (temperature) и силовой (force) параметры процесса; АЭ – параметр акустической эмиссии (acoustic emission).
Список литературы
1.Цыпкин Я.З. Основы теории автоматических систем. –
М.: Наука, 1977. – 560 с.
2.Herbert F. Discrete-time systems: an introduction to the theory. – New York: J. Wiley, 1965. – 241 p.
249
3. Klocke F. Manufacturing processes 2: grinding, honing, lapping. – Berlin: Springer, 2009. – 433 c.
УДК 621.9(075)
АНАЛИЗ ВЗАИМОСВЯЗИ ТРУДОЕМКОСТИ ИЗГОТОВЛЕНИЯ ДЕТАЛЕЙ ГАЗОТУРБИННОГО ДВИГАТЕЛЯ
И ПРОГРАММЫ ИХ ВЫПУСКА В.Ф. Безъязычный, Д.Н. Сыщиков
Рыбинский государственный авиационный технический университет имени П.А. Соловьева, Рыбинск, Россия
technology@rsatu.ru.
Излагается метод определения снижения трудоемкости изготовления детали в зависимости от количества изготовленных с учетом опыта рабочего, а также совершенствования технологических процессов. Установлена закономерность уменьшения трудоемкости изготовления детали в зависимости от количества выпущенных. Рассмотрен пример расчета применительно к изготовлению лопаток турбины газотурбинного двигателя.
Ключевые слова: лопатка, турбина, газотурбинный двигатель, трудоемкость изготовления, программа выпуска.
Время, затраченное работниками на изготовление одного изделия, сокращается с увеличением количества изготовленных изделий. Когда работник впервые изготавливает деталь, он затрачивает больше времени, чем когда он обрабатывает вторую. На третью он затрачивает еще меньше времени и т. д. Многократное повторение и накопленный опыт способствуют постепенному снижению затрат. Этот эффект был исследован и назван кривой обучения, которая определяется как функция, показывающая, как с увеличением выпуска изделия уменьшается количество времени, требующееся для производства единицы продукции.
Уменьшение технологического времени основано на следующем принципе: при эффекте обучения время изготовления деталей T уменьшается в соответствии с количеством деталей, изготовленных для достижения заданного целевого времени. При
250