
Аэрокосмическая техника высокие технологии и инновации – 2016
..pdfбы одновременно обладали сразу несколькими положительными признаками: универсальностью (безотносительностью к методу обработки), малой методической погрешностью, минимальным вмешательством в процесс обработки, отсутствием необходимости в изменении конструкции инструмента или заготовки. К числу методов, наиболее полно удовлетворяющих указанным критериям, можно отнести метод «естественной» термопары и различные варианты дистанционной термометрии, в том числе инфракрасной.
Как известно, метод «естественной» термопары позволяет определить среднюю температуру по площади контакта инструмента и заготовки. Суть метода заключается в том, что в качестве элементов термопары служат резец и обрабатываемая заготовка, материал которых разнороден. Спаем термопары здесь является место контакта резца со стружкой и заготовкой в процессе резания. Метод дает хорошие результаты в случае непрерывного контакта инструмента и заготовки (точение), однако попытки применить его для исследования процессов с прерывистым резанием (фрезерование) наталкиваются на целый ряд методических проблем, большая часть из которых связана с периодическим разрывом цепи «естественной» термопары и сложностью калибровки такой термопары.
В момент входа в контакт очередной режущей кромки фрезы и заготовки на фоне полезного измеряемого сигнала возникает импульсная помеха, обусловленная паразитными трибоэлектрическими и электрохимическими эффектами (трибоЭДС, контактная разность потенциалов, разность электродных потенциалов при обработке с СОЖ и пр.). Помимо этого, внутреннее сопротивление «естественной» термопары достаточно мало и составляет порядок единиц Ом, а входное сопротивление типичного измерительного преобразователя (АЦП, вольтметра, платы сбора данных) на много порядков выше и может достигать десятков МОм. При выходе из контакта режущей кромки фрезы цепь термопары разрывается, и в этот момент на вход измерительного преобразователя начинает действовать помеха нормального вида, амплитуда которой, как правило, приводит к перегрузке преобразователя, рассчитанного на величину полезного сигнала в диапазоне десятков мВ.
151
Для калибровки «естественной» термопары чаще всего используется метод тарирования в печи, для чего необходимо изготовить электроды из инструментального и обрабатываемого материалов [1]. Недостатком такого подхода является то, что для проведения тарирования необходимы электроды в виде длинных стержней малого диаметра, что считается весьма затруднительным, длительным и дорогостоящим процессом и практически не может быть осуществлено без участия предприятия – изготовителя инструментов. Возможным выходом из этой ситуации является применение экспресс-метода тарирования естественной термопары, основанного на том, что электроды не помещаются в нагретую печь, а контактируют с нагретым до известной температуры промежуточным телом, что дает возможность использовать электроды малых размеров и любой геометрической формы [2].
Экспериментальный теплофизический анализ процесса обработки можно проводить не только с помощью термопар, но и методами бесконтактной (радиационной) термометрии, например, с использованием тепловизоров. В этом случае основной технической проблемой является несоответствие скоростных характеристики промышленных приборов интервалу времени в течение которого зона контакта режущей кромки фрезы и заготовки появляется в поле зрения тепловизора. Например, при скорости вращения фрезы n = 5000 об/мин и числе зубьев z = 3 требуемое время отклика матрицы тепловизора должно иметь порядок нескольких миллисекунд, что недоступно подавляющему большинству серийно выпускаемых моделей.
В то же время требование к высокой производительности тепловизора можно существенно снизить, если последний имеет возможность сохранения радиометрического видеопотока в файл или анализа видеопотока в реальном времени с функцией поиска максимальной температуры в кадре. При этом дополнительными ограничениями на условия проведения эксперимента являются выбор частоты вращения фрезы некратной частоте захвата кадров тепловизором и достаточная длительность одного опыта.
На рисунке представлен фрагмент (кадр) видеозаписи процесса фрезерования экспериментальных образов, полученный тепловизором FLIR E60 с частотой 60 кадров/с (работа проведена аспирантом М.С. Елкиным).
152
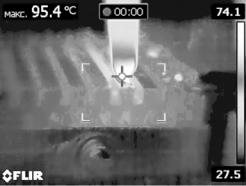
Рис. Кадр изображения тепловизора FLIR E60 с результатом измерения максимальной температуры в зоне резания
Анализ результатов показывает, что, несмотря на недостаточные скоростные характеристики тепловизора, в силу стробоскопического эффекта определенное число кадров видеопотока фиксирует момент выхода режущей кромки фрезы и область с максимальной контактной температурой резания.
Результаты получены в рамках выполнения базовой части государственного задания Минобрнауки России (НИР № 824 «Основы формирования допустимого уровня накопленной энергии в поверхностном слое деталей ответственных узлов машин, обеспечивающей требуемые эксплуатационные свойства»).
Список литературы
1.Макаров В.Н., Проскуряков С.Л., Макаров М.В. Точное измерение температуры резания методом «естественной» термопары // Вестник Верхневолжского отделения Академии наук Российской Федерации. – Рыбинск: РГАТА, 2001. – Вып. 4. – С. 126–131.
2.Безъязычный В.Ф., Тимофеев М.В., Фоменко Р.Н. Экс- пресс-метод тарирования термопар // Справочник. Инженерный журнал. – 2010. – № 7. – С. 38–42.
153

УДК 621.91.01
МАТЕМАТИЧЕСКОЕ МОДЕЛИРОВАНИЕ ОБЪЕМНЫХ ИСТОЧНИКОВ ТЕПЛА ПРИ ОБРАБОТКЕ МЕТАЛЛОВ РЕЗАНИЕМ
М.В. Тимофеев, М.С. Елкин
Рыбинский государственный авиационный технический университет имени П.А. Соловьева, Рыбинск, Россия
technology@rsatu.ru
Рассматривается математическая модель объемного источника тепла с поправкой на неравномерное распределением интенсивности по глубине его залегания. Показано существенное различие температурных полей в обрабатываемой заготовке с учетом поправки и без нее.
Ключевые слова: обработка резанием, объемный тепловой источник.
Хорошо известно, что при обработке материалов резанием часть затрачиваемой энергии переходит в тепловую энергию, что приводит к повышению температуры в зоне резания1. На сегодняшний день известен целый ряд способов схематизации и математического описания источников тепла в зоне резания. Среди них к наиболее точным относятся модели, учитывающие пространственное распределение источников тепла. Одна из возможных схем расположенияисточниковтеплапредставленанарис. 1.
Величины a1, h, h1, , 1, 2 определяют геометрические размеры источников тепла, q1, q2 и q3 – их интенсивности. Источники имеют переменную интенсивность по оси x, сонаправленной с вектором скорости резания, однако по оси y их интенсивность принимается постоянной. Введение последнего допущения позволяет несколько упростить аналитическую модель, но приводит к существенной погрешности, например, при расчете технологических остаточных напряжений ввиду искажения температурного поля.
Учет анизотропии интенсивности тепловых источников целесообразно связать с распределением интенсивности деформаций сдвига по глубине поверхностного слоя. Точное решение в
1 Безъязычный В.Ф. Метод подобия в технологии машиностроения. – М.: Машиностроение, 2012. – 320 с.
154
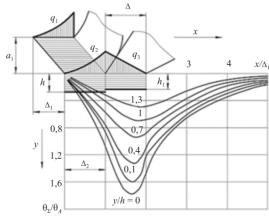
этом случае может быть получено на основе положений теории пластичности. В качестве первого приближения предлагается поправка к закону распределения интенсивности источника q3 в виде экспоненциальной функции с показателем m = 5.
Рис. 1. Схема действия объемных источников тепла в зоне резания [1]
Итоговое выражение для интенсивности q3 определяется из условия равенства мощности теплового источника Q работе сил трения Z в единицу времени на участке с координатами ∆2; ∆2+∆, затрачиваемой на преодоление сил трения по задней поверхности инструмента:
|
2 |
|
|
|
2 x |
|
|
|
|
|
|
|
|
|
|
|
|
|
|
|
|
|
||
|
|
|
|
|
|
|
|
|
|
|
|
|
|
|
|
|
|
|
|
|
||||
|
р 1 |
|
|
dx |
|
|
|
|
|
|
|
|
|
|
|
|
|
|
|
|||||
Z |
2 |
|
|
|
|
|
|
|
|
b v |
1 |
|
p |
v b |
; |
|||||||||
|
|
|
|
|
|
|
|
2 |
||||||||||||||||
|
|
|
|
|
|
|
|
|
|
|
1 |
|
|
|
|
|
1 |
|
||||||
|
|
|
|
2 h1 |
|
|
|
|
x |
|
m |
y |
|
|
|
|
|
|
|
|||||
|
|
|
|
b1 |
q3 |
|
|
h1 dydx |
|
|||||||||||||||
|
|
|
|
1 |
|
|
2 |
|
|
|
e |
|
|
|
||||||||||
|
Q |
|
2 |
0 |
|
|
|
|
|
|
|
|
|
|
|
|
|
|
|
|
||||
|
|
|
|
|
b1 h1 |
|
|
|
|
|
|
|
|
|
|
|||||||||
|
|
|
|
|
|
|
|
|
|
|
|
|
|
|
|
|
|
|||||||
|
|
|
b1 h1 q3 |
1 e m |
|
|
|
|
|
|
|
|
|
|
|
|||||||||
|
|
|
|
2m b1 h1; |
|
|
|
|||||||||||||||||
|
|
|
|
|
|
|
|
|
|
|
x |
m |
y |
|
|
|
|
|
||||||
|
|
|
|
|
|
|
|
|
|
|
|
|
|
|||||||||||
|
|
|
q x, y q3 1 |
|
|
2 |
|
e |
|
|
|
h1 , |
|
|
|
|||||||||
|
|
|
|
|
|
|
|
|
|
|
|
|
|
|
|
|
|
|
|
|
|
|||
|
|
|
|
|
|
155 |
|
|
|
|
|
|
|
|
|
|
|
|
|
|
|
|
|
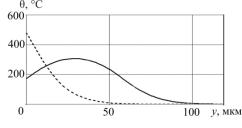
|
|
Z Q; |
|
|
|||
1 |
|
q3 |
1 e m |
|
|||
2 |
р v b1 |
|
2m b1 h1; |
||||
|
q3 |
m |
|
|
p |
v |
, |
|
1 e m |
|
h |
|
|||
|
|
|
1 |
|
где τр – сопротивление обрабатываемого материала пластическому сдвигу, Па; v – скорость резания, м/с; b1 – ширина сечения стружки, м.
Таким образом, в сравнении с тепловым источником, имеющим равномерное распределение интенсивности по глубине залегания рассматриваемого слоя, модель источника с экспоненциальным распределением дает в m/(1 – e–m) раз большую максимальную температуру в поверхностном слое за счет локализации тепловыделения ближе к обработанной поверхности. Аналогичную поправку можно использовать для первого и второго источников тепла в виде выражения exp(–m·y/a1) и exp(–m·y/h) соответственно.
Для количественной оценки влияния поправки были построены два графика распределения температуры в материале детали при концевом фрезеровании с учетом поправки и без нее (рис. 2). Материал детали – ХН77ТЮР, материал инструмента – В10ХОМ, глубина резания – 1 мм, ширина строки – 1 мм, подача – 0,1 мм/зуб, частота вращения шпинделя – 3000 мин–1, радиус фрезы – 8 мм, радиус округления режущей кромки – 10 мкм, передний угол – 20 , задний угол – 5 , угол наклона оси инструмен-
та – 10 .
Рис. 2. Распределение температуры в поверхностном слое детали: равномерный (––) и экспоненциальный (- - -) законы распределения интенсивности теплового источника
156
Анализируя формы полученных графиков, можно прийти к выводу, что при введении поправки на неравномерность интенсивности источников тепла по глубине поверхностного слоя детали температура локализуется ближе к обрабатываемой поверхности, причем ее максимальная величина выше, чем у в случае функции температуры, построенной без учета неравномерности интенсивности источника тепла. Кроме того, допущение постоянства интенсивностей источников по оси y приводит к возникновению фиктивного максимума на графике температуры и искажению результатов расчета параметров качества поверхностного слоя, формирование которых обусловлено тепловым фактором.
Результаты получены в рамках выполнения базовой части государственного задания Минобрнауки России (НИР № 824 «Основы формирования допустимого уровня накопленной энергии в поверхностном слое деталей ответственных узлов машин, обеспечивающей требуемые эксплуатационные свойства»).
УДК 621.438: 621.45.026
РАЗРАБОТКА ТЕХНОЛОГИИ ДОВОДКИ СОПЛОВОЙ ЛОПАТКИ ТУРБИНЫ НИЗКОГО ДАВЛЕНИЯ ГАЗОТУРБИННОГО ДВИГАТЕЛЯ
А.В. Викулин, В.А. Земляная
Московский авиационный институт (национальный исследовательский университет), Москва, Россия
chesnovava@mail.ru
Разработаны технологии теплового проектирования и доводки охлаждаемых лопаток высокотемпературных газовых турбин по тепловому состоянию и технологичности на стадии создания их первоначального проекта и последующей отработки базового варианта. Данные технологии применены при совершенствовании конструкции сопловой лопатки турбины низкого давления двигателя АЛ-31ФП. Разработаны перспективные схемы систем охлаждения для сопловых лопаток, которые позволяют повысить предельно допустимую температуру газа
157
перед турбиной, а следовательно, увеличить ресурс и надежность работы всего газотурбинного двигателя.
Ключевые слова: газовая турбина, сопловая лопатка, система охлаждения, модульная доводка, метод имплантации, поперечные перемычки, вихревая матрица, теплогидравлические характеристики.
Одной из главных тенденций развития авиационных газотурбинных двигателей является дальнейшее значительное повышение температуры газа перед турбиной до 2000–2200 °К. Такой уровень температур требует разработки не только систем охлаждения лопаток высокотемпературных турбин высокого давления, но и эффективно охлаждаемых лопаток турбин низкого давления. Повышение уровня теплообмена в сопловых и рабочих лопатках таких турбин связано со значительным усложнением конструкции их внутренней полости. Целью данной работы является разработка конструктивного исполнения внутреннего тракта сопловых лопаток турбины низкого давления (ТНД) и доводка их по тепловому состоянию.
Коллективом сотрудников кафедры технологии проектирования и производства двигателей летательных аппаратов была разработана поэтапная технология доводки по тепловому состоянию и технологичности охлаждаемых лопаток высокотемпературных газовых турбин [1].
Для создания базового первоначального проекта лопатки на ранней стадии ее проектирования, когда отсутствует выполненный в металле вариант, выбор типа интенсификаторов теплообмена, их расположения и геометрических параметров осуществляется исходя из анализа эмпирических и экспериментальных данных с учетом обобщения результатов теплогидравлических исследований перспективных систем турбулизаторов потока в каналах сложной конфигурации. Последующая доводка по тепловому состоянию первоначального проекта базовой лопатки осуществляется на упрощенных по геометрии и материалу вариантах, выполненных с применением универсального оборудования (модульная доводка).
С целью доводки лопатки по тепловому состоянию на более поздних этапах ее разработки, когда имеется литьевой вариант базовой лопатки, разработана технология с оперативным измене-
158
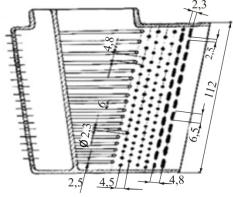
нием конструкции каналов охлаждения методом имплантации. Для окончательной доводки лопатки газовой турбины по тепловому состоянию и отработки ее по технологичности в процессе серийного производства используется технология доработки керамических стержней, формирующих тракт охлаждения модификаций лопатки.
Разработанные технологии были апробированы при совершенствовании конструкции сопловой лопатки ТНД двухконтурного турбореактивного двигателя АЛ-31ФП. В базовом исполнении во внутренней полости входной кромки лопатки установлен дефлектор и выполнены поперечные ребра. В канале выходной кромки размещены четырехрядная система штырьков, расположенных в шахматном порядке, а также двухрядная система поперечных перемычек (рис. 1).
Рис. 1. Базовый вариант сопловой лопатки турбины низкого давления
С целью совершенствования конструкции лопаток проведены тепловые и гидравлические испытания перспективных систем охлаждения, представляющих собой комбинированную разветвленную систему каналов, сформированную «широкой» вихревой матрицей и несколькими рядами прерывистых наклонных перемычек. Тепловые характеристики данных систем интенсификации теплообмена были получены по результатам калориметрических испытаний в жидкометаллическом термостате, а гидравлические – на основании изотермических продувок [2].
159
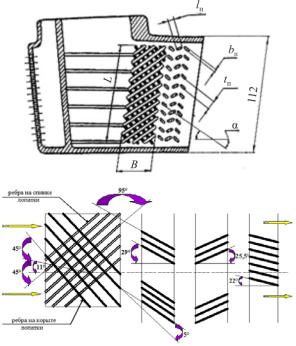
С учетом проведенных тепловых и гидравлических испытаний и полученных критериальных зависимостей установлено, что в области выходной кромки лопатки целесообразно разместить «широкую» вихревую матрицу и три ряда перемычек (рис. 2). Это позволило повысить уровень интенсификации теплообмена на 15–40% по сравнению с базовым вариантом лопатки. При этом наибольшее гидравлическое сопротивление наблюдается на первом ряду перемычек, расположенных за вихревой матрицей. Однако суммарное гидравлическое сопротивление комбинации «вихревой матрицы» и трех рядов наклонных перемычек соответствует гидравлическому сопротивлению базового варианта лопатки при том значении числа Рейнольдса [3].
Рис. 2. Конструкция системы охлаждения модификации базовой лопатки
Кроме того, предложена другая конструкция системы охлаждения сопловых лопаток ТНД, представляющая собой комбина-
160