
Аэрокосмическая техника высокие технологии и инновации – 2016
..pdfУДК 665.612.2
ВОЗМОЖНОСТЬ ИСПОЛЬЗОВАНИЯ ОТХОДОВ ГАЗОВЫХ КОНДЕНСАТОВ В КАЧЕСТВЕ ТОПЛИВА
Е.В. Бояршинова, Н.Л. Бачев, Г.А. Арзамасова
Пермский национальный исследовательский политехнический университет, Пермь, Россия
katerinka_bev@mail.ru
Рассматриваются вопросы организации горения отходов газового конденсата (ОГК) непосредственно в пунктах приема газокомпрессорных станций. С этой целью определены стехиометрические соотношения и концентрационные пределы горения топливной смеси ОГК + воздух. Проведены термодинамические расчеты при разных коэффициентах избытка воздуха для определения параметров горения и состава продуктов сгорания.
Для верификации полученных результатов была разработана и изготовлена экспериментальная установка, состоящая из горелки и магистралей подвода компонентов. В процессе экспериментальных исследований регистрировались давления, температуры и расходы по линиям подачи, температура пламени в горелке. Экспериментально были измерены концентрации углекислого газа СО2, оксидов азота NOx и серы SOx, оксидов углерода СО, водяных паров Н2О и несгоревших углеводородов СН.
Ключевые слова: отходы газового конденсата, стехиометрическое соотношение, концентрационные пределы горения, горелка, состав продуктов сгорания.
Природный газ, транспортируемый по магистральным газопроводам, может содержать различные твердые и жидкие частицы, которые являются источниками преждевременного износа трубопроводов, запорной арматуры и технологических узлов компрессорной станции, что снижает эффективность и безопасность реализации основных процессов на линейных участках трубопровода и на компрессорных станциях. Поэтому очистка природного газа на линейных компрессорных станциях от механических примесей является неотъемлемым технологическим процессом его транспортировки, обеспечивающим безопасность
141
и надежность оборудования, а также качество природного газа как товарного продукта.
В результате процесса очистки образуются нефтесодержащие отходы, которые в соответствии с нормативно-технической документацией ОАО «Газпром» носят название «отходы газового конденсата в процессе очистки природного газа от механических примесей».
Отходы газового конденсата (ОГК) обладают высоким материальным и энергетическим ресурсом и при концентрации нефтепродуктов более 70 % могут использоваться в качестве самостоятельного топлива или органической добавки к основному топливу [1].
По компонентным составам ОГК и воздуха были определены их условные химические формулы и массовые элементарные составы.
Массовое стехиометрическое соотношение между ОГК и воздухом определялось по массовым долям элементов в составе горючего и окислителя по формуле
|
|
8 |
гор |
|
гор |
гор |
гор |
|
|
|
3 |
gC |
8gH |
gS |
gO |
|
|
Кмо |
|
|
|
|
|
|
|
|
|
|
gOок |
8 gСок 8gHок |
gSок |
|
|||
|
|
|
|
|||||
|
|
|
|
|
3 |
|
|
|
и составило Кмо = 13,7.
Нижний и верхний концентрационные пределы горения ОГК с воздухом определены с использованием правила Ле Шате-
лье [2, 3]
н |
|
|
r1 r2 ... rn |
|
|
, |
|||||||||
|
r1 |
|
|
|
|
r2 |
... |
rn |
|
||||||
|
|
|
|
|
|
|
|||||||||
|
|
|
|
|
|
|
|
|
|
||||||
|
|
|
|
|
|
|
2н |
|
|
|
nн |
|
|
||
|
|
1н |
|
|
|
|
|
|
|
|
|
|
|||
в |
|
r1 r2 ... rn |
|
, |
|||||||||||
r1 |
|
|
|
|
r2 |
|
... |
|
rn |
||||||
|
|
|
|
|
|
|
|
|
|||||||
|
|
|
|
|
|
|
|
|
|
||||||
|
|
|
|
|
|
|
2в |
|
|
|
nв |
|
|
||
|
|
1в |
|
|
|
|
|
|
|
|
|
|
где [r] – объемные доли j-го компонента, об. %; нj , вj – нижний и верхний пределы воспламенения пара j-го компонента.
142
Коэффициенты избытка воздуха α на нижнем и верхнем пределах горения рассчитывались с использованием параметров смешения по следующей методике [4, 5]:
|
1 |
|
|
1 |
|
|
|
н |
|
|
1 |
, |
|||
Км0 |
н |
||||||
|
|
|
|
|
|||
|
1 |
|
|
1 |
|
|
|
в |
|
|
1 . |
||||
Км0 |
|
в |
|||||
|
|
|
|
|
Результаты расчетов нижнего и верхнего пределов горения жидкофазных отходов приведены в табл. 1.
Таблица 1 Концентрационные пределы горения ОГК
Параметр |
Величина |
н , об. % |
0,460 |
в , об. % |
3,955 |
н |
15,8 |
в |
0,4 |
В результате проведенных исследований можно сделать вывод о том, что ОГК можно сжигать в утилизационных камерах сгорания непосредственно на пунктах приема газокомпрессорных станций с подачей воздуха от компрессора.
Для выбора оптимальных параметров горения ОГК в утилизационной камере сгорания требуется информация о параметрах и составе продуктов сгорания. Они получены в результате термодинамического расчета с использованием программного комплекса Астра-4.
На рисунке представлена зависимость температуры горения ОГК от коэффициента избытка воздуха.
В табл. 2 приведена массовая концентрация коррозионноактивных и вредных веществ в составе продуктов сгорания при сжигании ОГК.
Экспериментальные исследования по организации горения ОГК проводились с использованием ОГК как добавки к дизельному топливу и как самостоятельного горючего.
143
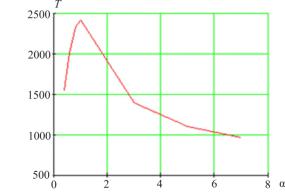
Рис. Зависимость температуры горения ОГК от коэффициента избытка воздуха
Таблица 2
Концентрация коррозионно-активных и вредных веществ, мас. %
|
NOх |
СО |
Серосодержащие |
Н2О |
0,4 |
0,04 |
27,5 |
0,094 |
3,1 |
0,6 |
0,77 |
17,3 |
0,096 |
5,9 |
0,8 |
1,7 |
11,88 |
0,03 |
5,56 |
1,0 |
2,34 |
8,6 |
0,0199 |
4,89 |
3,0 |
3,6 |
1,59 |
0,0023 |
1,95 |
5,0 |
3,6 |
0,7 |
0,001 |
1,18 |
7,0 |
3,56 |
0,4 |
0,0001 |
0,8 |
Экспериментально показана устойчивость горения в диапазоне α от 0,58 до 1,38 и определена концентрация загрязняющих и коррозионно-активных веществ в составе продуктов сгорания.
Таким образом, исследования показали, что ОГК могут использоваться как самостоятельное углеводородное топливо, так и в качестветопливнойдобавкикосновнымуглеводороднымтопливам.
Список литературы
1. Арзамасова Г.С., Карманов В.В. Извлечение ценных углеводородов как способ повышения экологической безопасности обращения с нефтесодержащими отходами газотранспортных
144
предприятий // Вестник Пермского национального исследовательского политехнического университета. Урбанистика. – 2013. – № 4. – С. 124–133.
2.Блинов Е.А. Теория горения и взрыва. – СПб.: Изд-во Сев.-Зап. техн. ун-та, 2007. – 119 с.
3.Воеводин Р.А., Бачев Н.Л., Арзамасова Г.С. Концентрационные пределы горения отходов газового конденсата // Вестник Пермского национального исследовательского политехнического университета. Аэрокосмическая техника. – 2015. – № 42. –
С. 104–113.
4.Зуева О.А., Бачев Н.Л., Бульбович Р.В. Пределы устойчивого горения нефтяных газов // Нефтяное хозяйство. – 2014. –
№6. – С. 64–66.
5.Зуева О.А. Концентрационные пределы горения попутных нефтяных газов // Вестник Пермского национального исследовательского политехнического университета. Аэрокосмическая техника. – 2014. – № 37. – С. 140–153.
УДК 621.9.06
ОЦЕНКА ТЕХНИЧЕСКОГО СОСТОЯНИЯ МЕТАЛЛООБРАБАТЫВАЮЩЕГО ОБОРУДОВАНИЯ С ЧПУ БЕЗ ЕГО РАЗБОРКИ
В.Г. Гусев, М.В. Тимофеев
Рыбинский государственный авиационный технический университет имени П.А. Соловьева, Рыбинск, Россия
technology@rsatu.ru
Проведен анализ существующих методов и объектов оценки технического состояния оборудования без его разборки, позволяющих сократить затраты на ремонт, а также уменьшить время простоя оборудования.
Ключевые слова: оборудование, диагностика, неразрушающий контроль, техническое состояние.
В современном мире с нарастающими требованиями к производительности станков с ЧПУ и качеству изготавливаемой продукции существенно повышается роль технического обслу-
145
живания и ремонта по фактическому состоянию с применением современных методов и средств диагностики технического состояния всех систем и узлов станка. Такая система успешно применяется на передовых отечественных и большинстве зарубежных предприятиях и основана на оценке технического состояния без разборки оборудования. От своевременного выявления той или иной неисправности во многом зависит, будет станок выпускать продукцию или будет простаивать в ожидании запасных частей для ремонта, поэтому техническое обслуживание и ремонт производится целенаправленно, устраняя конкретный дефект [1–3].
Основной целью диагностики технического состояния металлообрабатывающих станков с ЧПУ является предотвращение внезапных отказов и снижение простоев. С помощью диагностики технического состояния решаются следующие задачи:
–своевременное выявление дефектов узлов и деталей оборудования;
–поддержание эксплуатационных показателей оборудования в установленных пределах;
–прогнозирование технического состояния узлов и оборудования в целом;
–планирование технического обслуживания и ремонта оборудования по фактическому состоянию.
Современный металлообрабатывающий станок с ЧПУ имеет сложную структуру, включающую в себя механическую, гидравлическую, пневматическую, электрическую и электронную системы, а также системы смазки, подачи СОЖ, охлаждения шпинделя и пр. Некоторые системы станка, например гидравлическая, пневматическая, электронная, обладают встроенными средствами диагностики – индикаторами. Механическая система станка представляет практический интерес с точки зрения диагностики технического состояния как замкнутая технологическая система, влияющая на все показатели работоспособности оборудования в целом, и как система, объединяющая структурно и функционально другие подсистемы станка. В связи с этим ее диагностические показатели являются наиболее информативными, поэтому ниже речь пойдет непосредственно о диагностике технического состояния механической системы станка.
Поскольку механическая система станка состоит из множества элементов – узлов и деталей, являющихся объектами диаг-
146
ностики, ее техническое состояние характеризуется множеством состояний отдельных объектов диагностики [4]
∑Т = (Т1, Т2, Т3, …, Тm),
где Tm – объект диагностики; m – количество объектов диагностики.
Техническое состояние характеризуется нахождением в допустимых пределах диагностических признаков (прямых или косвенных), присущих каждому объекту диагностики:
Tm Dm1 , Dm 2 , Dm3 , , Dmk ,
где Dm – диагностический признак; k – количество признаков.
В качестве объектов диагностики технического состояния металлообрабатывающего станка выступают его механические узлы и детали, такие как подшипники, шпиндель, валы редукторов и коробки скоростей, муфты, зубчатые передачи, ременные передачи, электродвигатели, шариковые винтовые передачи, направляющие [4]. В свою очередь, каждый диагностический признак должен обладать набором допустимых значений, характеризующих следующие состояния: нормальное состояние (Dmk < П1mk), состояние предупреждения, при котором механизм может работать ограниченное время до ближайшего возможного ремонта (П1mk ≤ Dmk < П2mk), аварийное состояние (Dmk ≥ П2mk).
Всвязи с тем что, наряду с функциональной надежностью, станочное оборудование должно обеспечивать параметрическую надежность, в объекты диагностики следует внести точностные характеристики его формообразующих узлов: точность вращения шпинделя, прямолинейность перемещения вдоль осей, взаимную перпендикулярность осей, точность линейного позиционирования осей, точность углового позиционирования поворотных осей
ит.д. [4].
Взависимости от объекта, диагностику которого необходимо провести, применяется тот или иной метод или комплекс методов. Для получения информации о техническом состоянии современного металлообрабатывающего станка с ЧПУ используют: виброакустическую диагностику элементов привода главного движения и других механизмов, совершающих вращательное движение; диагностику по параметрам точности круговой траек-
147
тории; диагностику привода подач; контроль геометрических параметров и точности позиционирования; диагностику параметров точности перемещения формообразующих узлов.
Для получения полной картины технического состояния металлорежущих станков с ЧПУ вышеуказанные методы диагностики необходимо дополнять рядом следующих проверок: измерение температуры узлов, шумовых характеристик, силы зажима инструментальных оправок в шпинделях фрезерных станков и обрабатывающих центров.
Большинство диагностических задач решается методом виброакустической диагностики. Этот метод обладает широкими возможностями, что позволяет использовать его на всех этапах жизненного цикла станка в целом и отдельных его механизмов в частности, определять наличие и вид, а также степень развития дефекта. Круг объектов виброакустической диагностики включает в себя все механизмы, совершающие вращательные движения [4]. Кроме того, при определенной наработке метод виброакустической диагностики можно использовать и для диагностики механизмов станка, совершающих поступательные движения, например, направляющие скольжения.
Диагностика по параметрам точности и постоянства отработки круговой траектории позволяет производить комплексную оценку приводов подач станка с ЧПУ при круговой интерполяции с возможностью количественного определения следующих отклонений: рассогласование приводов, люфты в шариковинтовой паре, люфты в направляющих, отклонение от перпендикулярности, отклонение от прямолинейности [4]. Контроль геометрических параметров с использованием современных средств измерения позволяет производить оперативную оценку точности перемещения формообразующих узлов и диагностировать параметрические отказы оборудования. Различные методы измерения геометрических параметров применительно к станочному оборудованию регламентируются ISO 230-1 (ГОСТ Р ИСО
230-1-2012).
Измерение параметров температуры позволяет оценить техническое состояние таких элементов станка, как подшипники, электродвигатели главного движения, подач и вспомогательных перемещений, насосов гидростанции, станции смазки, охлажде-
148
ния, подачи СОЖ, электрооборудования. При оснащении узлов станка стационарными датчиками открывается возможность контроля температуры в реальном времени и сигнализации о превышении допустимого уровня на панели оператора УЧПУ.
Необходимость измерения шумовых характеристик в первую очередь связана с проявлением вредного воздействия шума на организм человека. Кроме того, измерение уровня шума позволяет оперативно выявить источник локализации неисправности оборудования. Определение уровня шума производится по методике в соответствии с ISO 230-5 (ГОСТ ИСО 230-5-2002). Допустимый уровень шума приводится в паспорте станка или определяется по ГОСТ 12.2.107-85 в зависимости от мощности приводных электродвигателей. В качестве средства измерения для определения шумовых характеристик используется шумомер.
В целом внедрение безразборной диагностики технического состояния на предприятиях позволит повысить качество выпускаемой продукции, производительность работ по техническому обслуживанию и ремонту, предотвратить внезапные отказы оборудования и, как следствие, снизить процент брака, увеличить межремонтный ресурс, сократить объем ремонтных работ, значительно сократить стоимость технического обслуживания и ремонта.
Список литературы
1. Биргер И.А. Техническая диагностика. – М.: Машино-
строение, 1978. – 240 с.
2. Диагностика автоматизированного производства / С.Н. Григорьев, В.Д. Гурин, М.П. Козочкин [и др.]. – М.: Машиностроение, 2011. – 600 с.
3.Козочкин М.П., Сабиров Ф.С. Сертификация и испытания металлорежущих станков. – М.: ИТО, 2012. – 250 с.
4.Производственно-технический журнал ТОиР. – 2015. –
№4. – 80 с.
149
УДК 621.91.01
ИССЛЕДОВАНИЕ ТЕПЛОВЫХ ПРОЦЕССОВ ПРИ ФРЕЗЕРОВАНИИ С ПОМОЩЬЮ СКОРОСТНОЙ ИНФРАКРАСНОЙ ТЕРМОМЕТРИИ
Е.В. Тимофеева, М.А. Ганзен
Рыбинский государственный авиационный технический университет имени П.А. Соловьева, Рыбинск, Россия
technology@rsatu.ru
Рассматриваются два способа реализации теплового анализа процессов концевого фрезерования деталей: с помощью естественной термопары и посредством статистической обработки радиометрического потокового видео, полученного скоростным тепловизором.
Ключевые слова: обработка резанием, фрезерование, термометрия.
Исследование тепловых процессов при механической обработке материалов было и остается одной из ключевых задач технологии машиностроения. Повышение прочностных характеристик конструкционных материалов, интенсификация режимных параметров обработки приводят к тому, что температура процесса становится одним из факторов, которые ограничивают производительность процесса и оказывают существенное влияние на показатели качества изделия.
Традиционный процесс обработки металлов резанием изучается уже на протяжении многих десятилетий, в том числе и в аспекте тепловых явлений и их влияния на получаемый результат. Современные инструментальные методы радиометрии и анализа тепловых полей позволяют взглянуть с другой стороны на ранее полученные факты. Глубокое изучение влияния теплового фактора на процесс лезвийной обработки материалов дает более детальную картину физических процессов, протекающих в момент обработки, что, в свою очередь, позволяет точнее контролировать показатели качества получаемых поверхностей.
Вместе с тем, несмотря на многообразие методов и средств измерения температуры резания, способов исследования тепловых полей, существует ограниченное число подходов, которые
150