
580
.pdf
более удобный при монтаже и в процессе эксплуатации. Листы ОНДЕКСА не требуют дополнительных профилей для стыковки и закрытия листов от влаги. ОНДЕКС, как любой профилированный материал стыкуется внахлест. При проектировании светопрозрачного ограждения моста не следует забывать о его сохраняемости: и сотовый поликарбонат, и ОНДЕКС плавятся при горении, но испорченные листы ОНДЕКСА гораздо легче заменить. ОНДЕКС имеет и недостатки, это уже не плоская поверхность, а профилированная, т.е. необходимо учитывать сток воды при проектировании ограждения.
Обрешетка ограждения
Если на других мостах проект на дуги и стрингеры (направляющие) ограждения выполнялся сторонними организациями, то с применением нового материала на мостах в районе о.п. «Речпорт» и магазина «Лента» пришлось проектировать ограждение своими силами. В объеме был изображен мост со сходами и на объемной модели расставлены дуги и стрингеры ограждения. Трехмерная модель позволяет свести неточности к минимуму, и практически отпадает подгонка рам и дуг ограждения по месту, что положительно сказывается на виде решетки ограждения изнутри.
Плюсы и минусы конструкции мостов
Конструкции мостов имеют некоторые недостатки:
–в связи с тем, что ребра жесткости главных балок внутри пролетного строения расположены чаще, чем снаружи, при изготовлении балок на заводе произошло выпучивание стенки, таким образом ребра жесткости должны расставляться симметрично относительно оси балки;
–опорные части не совсем удобны при изготовлении и монтаже, ведется работа над проектированием новых опорных частей.
На наш взгляд, разработанные конструкции мостов, имеют следующие достоинства:
–балочное пролетное строение с пониженной строительной высотой выглядит привлекательней типовых пролетных строений и более удобно для пешеходов, оно смотрится изящнее балок с ходьбой поверху и ферм, которые предпочтительней возводить за пределами городской застройки;
–столбчатые немассивные опоры создают впечатление легкости, нет частокола опор;
–оптимизированные листовые шарниры крепления сходов к площадкам просты в исполнении и компактны;
–основные элементы моста (пролетное строение и косоуры сходов) изготавливаются на заводе, что сокращает объемы работ на стройплощадке;
–светопрозрачное ограждение мостов, металлический каркас ограждения и мост рассмотрены в комплексе;
–плиты пешеходной дорожки не требуют асфальтового покрытия, которое трудоемко в изготовлении и не всегда отличается эстетическим видом;
–проводятся эксперименты с окраской моста, применяются новые материалы, рассматриваются новые конструкции и учитываются недостатки конструкции при проектировании новых мостов.
Таким образом, при строительстве пешеходного моста в пределах городской застройки решается целый комплекс задач. В дальнейшем будут рассмотрены иные схемы мостов, отличающиеся архитектурной привлекательностью.
Научные руководители д-р техн. наук, проф. С.А. Бокарев, канд. техн. наук, доц. Б.В. Пыринов
М.В. Головин
(факультет «Мосты и тоннели»)
ВАЖНОСТЬ ПРОХОЖДЕНИЯ ПРОИЗВОДСТВЕННОЙ ПРАКТИКИ В ПРОЦЕССЕ ФОРМИРОВАНИЯ СПЕЦИАЛИСТА В ОБЛАСТИ СТРОИТЕЛЬСТВА ТОННЕЛЕЙ И МЕТРОПОЛИТЕНОВ
Для будущего специалиста по проектированию и строительству тоннелей и метрополитенов такой опыт невозможно переоценить. Студенты специальности «Тоннели и метрополитены» регулярно приглашаются на горностроительные предприятия для прохождения учебной, производственной и преддипломной практик. В рамках выступления хотелось бы осветить особенности строительства Большого Новороссийского тоннеля, т.е. знания и практические навыки, полученные в результате прохождения производственной практики.
Бамтоннельпроектом выполнен расчет обделки существующего тоннеля. В соответствии с результатами расчета, несущая способность обделки тоннеля не обеспечена как по основному сочетанию нагрузок, так при сейсмических воздействиях.
В соответствии с пунктом 5.25 СНиП 32-04–97 в статических расчетах обделки принята модель с заданной нагрузкой, основанная на положениях строительной механики. Статические расчеты выполнены с ис-
23
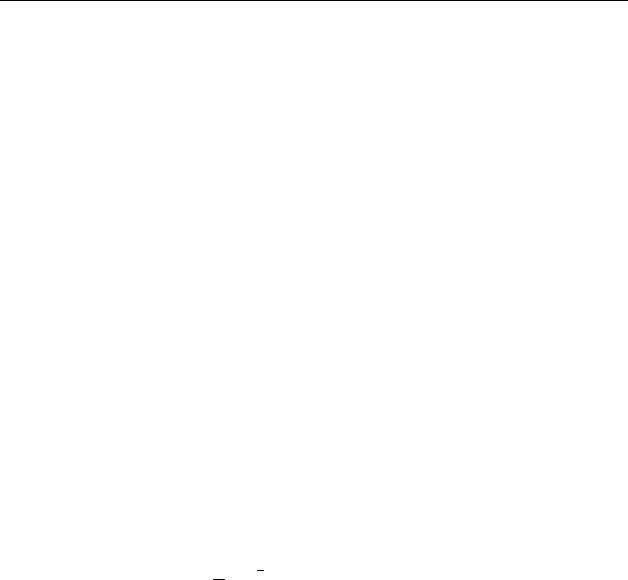
пользованием программы — «РК-6 — расчет подземных конструкций», разработанной институтом «Ленметрогипротранс».
Впрограмме реализован метод «Метрогипротранса» — расчет обделки тоннеля в упругой среде (Расчет тоннельных обделок / Под ред. проф. М.И. Дандурова. М.: Всесоюзное издательско-полиграфическое объединение МПС, 1960. Гл. III. С. 118).
Расчеты обделок тоннеля выполнены в соответствии с требованиями СНиП 32-04–97 на основное и особое сочетания нагрузок. В основном сочетании учитывались горное давление и собственный вес. В особом сочетании в соответствии с ВСН 193–81 была учтена расчетная сейсмичность 9 баллов.
Вданной работе освещены все основные вопросы, связанные со строительством Большого Новороссийского тоннеля, т.е. технологические этапы и механизмы, используемые при строительстве тоннеля, что имеет большое практическое значение для формирования практических навыков будущего специалиста.
Научный руководитель канд. техн. наук, доц. Г.Н. Полянкин
И.В. Касьянов
(факультет «Мосты и тоннели»)
ОЦЕНКА ДЕФОРМАЦИЙ ЗЕМНОЙ ПОВЕРХНОСТИ ПРИ ПРОХОДКЕ ПЕРЕГОННЫХ ТОННЕЛЕЙ МЕТРО
Исследование осадок приобретает большое значение, когда тоннельное сооружение имеет большой пролет, а над ним залегает относительно слабые и неустойчивые грунты.
Именно в таких условиях сооружены многие тоннели метрополитена, при которых наблюдались осадки земной поверхности до 150–200 мм и более, с образованием трещин в прилегавших к трассе зданиях, вызывавших необходимость выселения жильцов на период строительства тоннелей и последующего ремонта зданий.
На стадии проектирования прогнозирование осадок земной поверхности представляет собой сложную многофакторную задачу.
В работе рассматривались результаты расчета осадок земной поверхности для г. Новосибирска при проходке левого перегонного тоннеля в районе путепровода, находящегося на пересечении улиц Ипподромской
иГоголя, двух методик:
1.Осадки земной поверхности при сооружении тоннелей в кембрийских глинах (работа Ю.А. Лиманова).
Вданной работе грунт рассматривают как упруго-пластическую среду, для которой при напряженном состоянии, не превышающем предела прочности грунтов, применяется теория линейно деформируемых тел. Постоянство модуля деформации в этой теории ведет к некоторой неточности вычислений деформации.
Вцелях упрощения методики рассматривается плоская задача.
На основе этого, возможно применение математического метода теории упругости при установлении деформированного состояния грунта.
На основе принятой теории, введенных допущений для определения осадок необходимо правильно выбрать:
–расчетную схему;
–данные о характеристике грунтов;
–радиус тоннельной выработки.
По полученным данным была рассчитана зона действия мульды оседания по формуле
L = 2a + h tg(45 − ϕ) , |
(1) |
|
1 |
2 |
|
|
|
а также форма кривой оседания земной поверхности (кривая Авершина) и максимальная осадка по формуле
x
η = η0 (1− x )4 e4 L . (2)
L
Все параметры, входящие в формулы, были определены при помощи математического метода теории упругости.
2. Инструкция «по наблюдениям за сдвижениями земной поверхности и расположенными на ней объектами при строительстве в Москве подземных сооружений».
В данной работе грунт рассматривают как упруго-пластическую среду, для которой при напряженном состоянии, не превышающем предела прочности пород, применяется теория линейно деформируемых тел. Исходные данные соответственно те же.
Данная методика учитывает поперечные размеры тоннеля, деформацию колец обдели и слоистость грунтового массива, чего нет в первой методике.
Внешние границы мульды сдвижения на земной поверхности при подземном способе возведения сооружения следует определять по граничным углам, а внешние границы опасной ее части — по углам сдвиже-
24
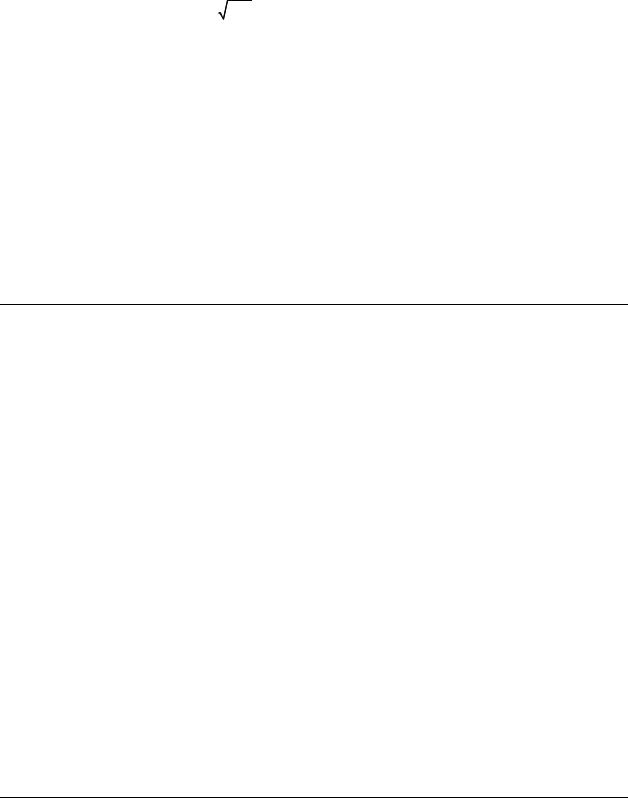
ния. Значения этих углов зависят от свойств горных, пород и определяются опытным путем. Углы разрывов принимаются на 10° круче углов сдвижения при f < 1,5 и на 5° круче при f > 1,5.
По полученным данным была рассчитана зона действия мульды оседания и максимальная осадка по формуле
|
|
|
|
ηm = qom n1n2 . |
(3) |
Были получены следующие теоретические данные:
–осадка земной поверхности над осью тоннеля 28 и 15 мм соответственно для 1 и 2 методики;
–зона мульды оседания соответственно 18,1 м и 14,38 м.
Расхождения значений осадок составляют 5 % во всех точках, кроме оси тоннеля — 35 %. Зона влияния мульды оседания также имеет достаточно большие расхождения.
Сравнивая результаты двух методик расчета осадки земной поверхности применительно к одним и тем же условиям, можно сделать выводы:
–обе методики имеют огромный ряд недостатков. Не учитываются конструктивно-технологические факторы;
–давление нагнетания тампонажного раствора за обделку тоннеля;
–степень заполнения тампонажным раствором строительного зазора (с учетом переборов грунта, подвижки его в строительный зазор, усадки раствора);
–скорость и характера прохождения щита (простои).
Проходка подземных выработок в городских условиях оказывает существенное влияние на осадки земной поверхности, что говорит о необходимости предварительного расчета, предостерегающего от дополнительных затрат на ремонт, перерасчет и восстановление зданий и сооружений, находящихся в зоне действия мульды оседания.
Научный руководитель канд. техн. наук, доц. Г.Н. Полянкин
Н.А. Козьмин
(факультет «Мосты и тоннели»)
РАЗРАБОТКА КОНСТРУКЦИЙ СТАЛЕЖЕЛЕЗОБЕТОННЫХ ПРОЛЕТНЫХ СТРОЕНИЙ НА ОСНОВЕ ПРОГОНОВ
ИЗ МЕТАЛЛИЧЕСКИХ ТРУБ
Темой работы является разработка конструкции, выполняемой на основе металлических труб из круглого проката, в качестве главных балок, и железобетонной плиты, включаемой с ними в совместную работу посредством металлических упоров. Расчетной нагрузкой были приняты автомобильная полосовая нагрузка А8 и нагрузка от гусеничного транспорта НГ-60. Конструкцию предполагается использовать на временных мостах, на мостах внутрихозяйственных дорог.
Исследование работы такой конструкции под действием нагрузок, предусмотренных СНиП 2.05.03–84* «Мосты и трубы», производилось в математической конечно-элементной модели, введенной в программный комплекс COSMOS/M. Расчет был выполнен для разрезного 18-метрового пролетного строения и неразрезного пролетного строения по схеме 2×18 м. Первой практически важной задачей явилось сравнение получаемых расчетных напряжений и перемещений с предельно допустимыми. На основе расчета (как автоматизированного, так и ручного) разрезного пролетного строения с габаритом проезжей части 6,0 м было рассчитано армирование плиты и выполнен его проект.
Дальнейшее направление исследования пошло по пути оптимизации геометрических параметров конструкции, таких как: шаг расстановки металлических прогонов поперек оси пролетного строения, толщина железобетонной плиты, высота упора. В частности, произведенное сравнение пролетных строений с разным шагом прогонов — 1,2 м и 1,4 м — показало преимущество последнего в плане более равномерного распределения нагрузки по прогонам и снижения напряжений в них.
Для нахождения коэффициента поперечной установки — важной характеристики пространственной работы мостовой многобалочной конструкции, а также для получения возможности производить ручной расчет, в математической модели были построены линии и поверхности влияния давления на прогоны в разрезном пролетном строении.
Научный руководитель канд. техн. наук доц. А.Н. Яшнов; канд. техн. наук, гл. спец. ООО «Опора» Б.В. Пыринов
25
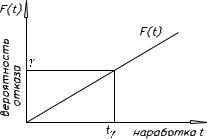
С.А. Надточий
(факультет «Мосты и тоннели»)
ОПРЕДЕЛЕНИЕ РЕСУРСА ПО ВЫНОСЛИВОСТИ ЭКСПЛУАТИРУЕМЫХ МЕТАЛИЧЕСКИХ ПРОЛЕТНЫХ СТРОЕНИЙ
Одним из важных условий обеспечения безопасности движения поездов по мостам является определение ресурса металлических пролетных строений по выносливости.
Была поставлена задача построения функции распределения усталостной долговечности элементов металлических пролетных строений F(t) как универсальной характеристики, позволяющей оценивать ресурс tγ для заданной вероятности разрушения γ. Преимущества такой постановки очевидны в условиях, когда вероятность отказов не нормирована и когда она может назначаться в зависимости от условий эксплуатации, конструкции элемента и пролетного строения и т.д.
Вероятностная постановка задачи предъявляет дополнительные требования к исходным данным и методам решения:
1.Необходимо располагать полновероятностными кривыми усталости или соответствующими многофакторными зависимостями.
2.Должны быть построены и сопоставлены с лабораторным экспериментом функции распределения долговечности по случаям отказов элементов мостов.
Кроме того, учитывая изменения в поездных нагрузках за время эксплуатации мостов, желательно иметь такой измеритель наработки, который бы заключал в себе эффект нестационарности процесса нагружения.
Рис. 1. Схема определения γ-процентного ресурса
Для описания кривой усталости в НИИЖТе предложено уравнение вида:
1 |
|
σ |
|
' |
C |
|
|||
|
|
b |
|
||||||
M (lg N) = AB1−ρ |
|
|
−1 |
, |
(1) |
||||
σmax |
|||||||||
|
|
|
|
|
|
где N — число циклов до разрушения; А, В, С — константы; ρ — коэффициент асимметрии цикла напряжения; σmax — максимальное напряжение в цикле; σ′b — условный предел прочности.
Это уравнение учитывает все основные факторы усталостного расчета, справедливо во всем диапазоне напряжений и обладает лучшей сходимостью с данными испытаний, чем обычная степенная зависимость.
Различия в схемах поездов и динамическом воздействии нагрузки было предложено учитывать в величине наработки.
ÊÍ = |
|
, |
(2) |
|
|||
Ý |
|
|
где и Э — накопленные повреждения для заданного и эталонного поезда; Кн — коэффициент наработки. Кн инвариантен ко многим условиям усталостного расчета. Это позволяет разделить свойство нагрузки и
усталости: все детали и конкретные особенности усталостного расчета отражаются на величине э, а расчеты Кн могут выполняться отдельно. Таким образом, наработка должна измеряться числом условных поездов, в котором и отражается эффект нестационарности процессов нагружения. В качестве эталонного был предложен поезд с локомотивом серии ВЛ-80 и четырехосными гружеными полувагонами.
Расчеты относительных накопленных усталостных повреждений производятся с использованием кривых
усталости по правилу линейного суммирования. |
(3) |
|||
= ∑δi |
=∑ 1 |
, |
||
k |
k |
|
|
|
i=1 |
i=1 Ni |
|
|
где k — число циклов под поездом; δi — повреждение от i-го цикла нагружения в долях от 1; Ni — число циклов до разрешения при работе не i-м уровне нагружения.
Разделение свойств нагрузки и усталости позволяет записать условие разрешения в виде:
∑∑ Ý (tj )nikHikgi =1, |
(4) |
j i |
|
26
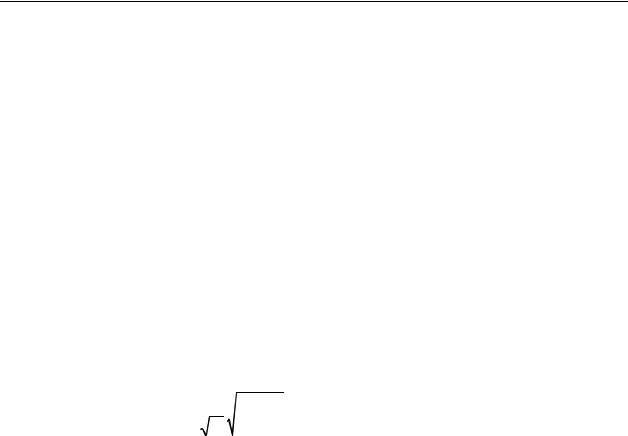
где j — индекс периода эксплуатации; i — индекс типа поездной нагрузки; ni — число поездов i-го типа; Δэ(tj) — относительное накопленное повреждение от статического воздействия эталонного поезда (для j-го периода эксплуатации эта величина может учитывать эффект нелинейности накопления повреждений, изменения в концентрации напряжений и другие факторы, вызывающие нестационарность в накоплении повереждений); Кнi — коэффициент наработки для i-го поезда; Kgi — поправочный коэффициент на динамическое воздействие нагрузки.
Это позволяет проводить исследования усталости по частям и объединять усилия исследователей на единой методической основе.
Научный руководитель ст. науч. сотр. НИДЦ СГУПС Ю.Н. Мурованный
Д.Н. Смердов
(факультет «Мосты и тоннели)
РАСЧЕТ УСИЛЕНИЯ ЖЕЛЕЗОБЕТОННЫХ КОНСТРУКЦИЙ КОМПОЗИТНЫМИ МАТЕРИАЛАМИ ПО ПЕРВОМУ ПРЕДЕЛЬНОМУ СОСТОЯНИЮ
Встроительстве преимущественно применяют три типа композитных материалов: стеклопластики, углепластики, арамидопластики. С физической точки зрения при усилении перспективно применять композиты на основе угольных волокон (углепластики). Так как они наряду с высоким пределом прочности при разрыве имеют модуль упругости не ниже, чем у стальной арматуры. Суть метода усиления заключается в приклеивании композитных лент на тщательно подготовленную поверхность усиливаемого элемента. Зарубежный опыт показывает, что усиление пролетных строений с использованием современных композитных материалов экономичнее по сравнению с традиционными методами усиления. Технология проста и не требует использования кранового оборудования и поддерживающих опор.
Вжелезобетонных конструкциях, усиленных композитными материалами, значительную роль имеет связь между бетоном и композитом из-за хрупкости механизма разрушения благодаря отклеиванию (потере сцепления). Такой механизм разрушения не должен произойти до разрушения усиленного элемента в результате изгиба или сдвига. Перед проектированием усиления требуется определить максимальную силу, которую возможно перераспределить от бетона на систему усиления, а также определить нормальные и поперечные напряжения на поверхности раздела бетон — система усиления. Максимальные напряжения в системе усиления должны быть меньше расчетного предела прочности ffdd,2:
f |
|
= |
1 |
|
|
2Ef |
ΓFk |
|
. |
(1) |
fdd,2 |
|
|
|
tk |
||||||
γ f ,d |
γc |
|
||||||||
|
|
|
|
|
|
|||||
|
|
|
|
|
|
|
где γ f ,d — коэффициент надежности, зависящий от характера разрушения системы усиления; γc — коэффициент надежности для бетона; Ef — модуль упругости композитного материала; ΓFk — удельная энергия разру-
шения поверхности раздела система усиления — бетон; tk — толщина холстов системы усиления. Соответствующее значение расчетной деформации εfdd в системе может быть вычислено по следующей
формуле: |
|
|
|
|
|
ε |
|
= |
f fdd,2 |
. |
(2) |
fdd |
|
||||
|
|
Ef |
|
||
|
|
|
|
Тогда несущую способность сечения балки в середине пролета можно определиться по формуле:
MRd = Rbb'f x(h0 − 0,5x) + R's A's (h0 − a's ) +
+Af ε fdd Ef a s , |
(3) |
где Rb — расчетное сопротивление бетона на сжатие; b'f |
— ширина полки балки; x — высота сжатой зоны |
бетона; h0 — рабочая высота сечения балки; R's — расчетное сопротивление сжатой арматуры; A's — площадь сжатой арматуры; a's — расстояние до центра тяжести сжатой арматуры; Af — площадь усиления; as — расстояние до центра тяжести растянутой арматуры.
27
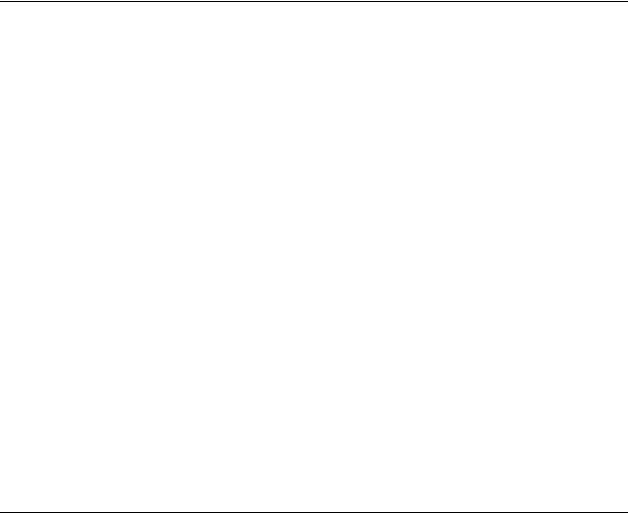
При проектировании усиления нужно определять фактическое состояние конструкции: искать наличие дефектов, неисправностей и повреждений, с учетом которых следует производить проверочные расчеты усиления.
Научный руководитель канд. тех. наук, доц. А.Н. Яшнов
А.А. Якимович
(факультет «Мосты и тоннели»)
СОВРЕМЕННЫЕ СПОСОБЫ ГИДРОИЗОЛЯЦИИ ТОННЕЛЬНЫХ ОБДЕЛОК
Гидроизоляция — неотъемлемая часть безопасной и долгосрочной эксплуатационной надежности тоннеля. Гидроизоляция является важным конструктивным элементом тоннельной обделки, защищая арматуру от коррозии и препятствуя проникновению грунтовых вод внутрь тоннеля.
Внастоящее время в Европе (например, в Испании) при строительстве и реконструкции транспортных тоннелей широко применяются пластиковые гидроизоляционные мембраны «Карфом». Пластиковые мембраны выполнены в форме сэндвича и состоят из трех слоев, где каждому отведена своя роль. Толщина мембраны рассчитывается в каждом отдельном случае и может составлять 4–20 мм.
К достоинствам системы можно отнести:
– адаптация к различным условиям окружающей среды (за счет варьирования толщинами слоев);
– система применима независимо от геометрии сооружений;
– низкий собственный вес;
– возможность использования в качестве гидроизоляции по внутренней стороне обделки;
– быстрый и дешевый ремонт (в случае, если гидроизоляция устроена с лицевой стороны тоннеля);
– долговечность.
ВРоссии, в частности на Юге, в настоящее время при строительстве тоннелей применяется другой материал гидроизоляции.
Пленка «Карбофол» представляет собой рулонный материал толщиной около 2,5 мм, состоящий из двух слоев: черный — непосредственно выполняет функцию гидроизоляции и белый — сигнальный, служит для выявления повреждений при монтаже.
Подготовка монтажной поверхности, прикрепление выравнивающего слоя и монтаж гидроизоляционной пленки производится с монтажной тележки на рельсовом ходу. Тележка оборудована выдвижными роликами, позволяющими в процессе монтажа уложить на них «Геотекстиль» либо «Карбофол» по контуру монтажной поверхности.
Научный руководитель канд. тех. наук, доц. Г.Н. Полянкин
К.Ю. Акинина
(факультет «Строительные и дорожные машины»)
ОЦЕНКА ЭФФЕКТИВНОСТИ ТЕХНОЛОГИЧЕСКОГО ПРОЦЕССА ТЕХНИЧЕСКОГО ОБСЛУЖИВАНИЯ
На работу автомобиля большое влияние оказывают узлы и агрегаты трансмиссии, ремонт агрегатов и узлов является трудоемким и дорогостоящим. Одним из основных показателей агрегатов и узлов является их долговечность, определяемая износом в эксплуатации до отказа или износа отдельных деталей или полностью агрегата. Стоимость агрегатов и узлов составляет около 20–25 % от общей стоимости автомобиля. Вопрос продления службы агрегатов и узлов весьма значителен. Немаловажным является качество технического обслуживания машин, так как от этого во многом зависит срок службы машины. Увеличение срока службы агрегатов и узлов способствует снижению капитальных затрат на автомобильном транспорте, экономии дефицитных и дорогостоящих материалов.
Поэтому анализ качества обслуживания машин имеет большое значение. Для выполнения такого анализа можно использовать одну из технологий управления качеством — FMEA-анализ (Failure Mode and Effects
Analysis).
FMEA-анализ проводится для разрабатываемых продуктов и процессов с целью снижения риска потребителя от потенциальных дефектов.
28
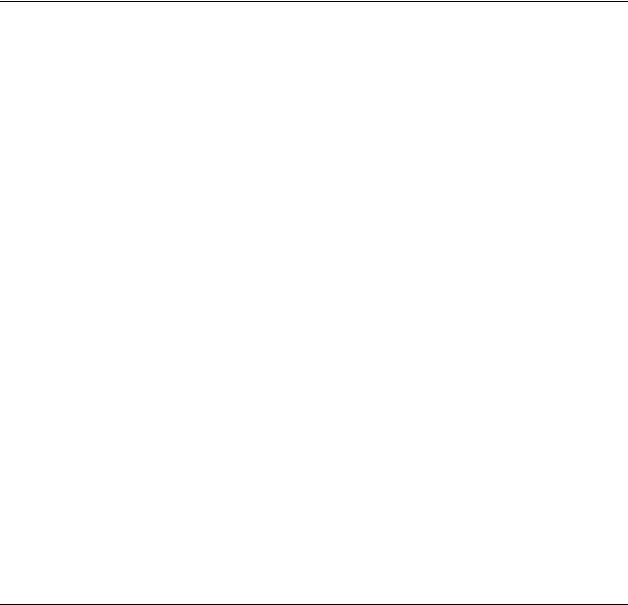
Метод FMEA начал активно применяться в промышленности с 60-х годов, прежде всего в США. Его использование позволило снизить себестоимость многих видов продукции без снижения ее качества и оптимизировать затраты на изготовление.
FMEA-анализ представляет собой технологию анализа возможности возникновения дефектов и их влияния на потребителя. Он проводится для разрабатываемых продуктов и процессов с целью снижения риска потребителя от потенциальных дефектов.
В отличие от функционально-стоимостного анализа FMEA напрямую не анализирует экономические показатели, в том числе затраты на недостаточно высокое качество, а позволяет выявить именно те дефекты, которые обуславливают наибольший риск потребителя, определить их потенциальные причины и выработать корректирующие действия по их устранению еще до того, как эти дефекты проявятся и, таким образом, предупредить затраты на их исправление.
Проведение FMEA-анализа процесса производства начинается на стадии технической подготовки производства и заканчивается своевременно до монтажа производственного оборудования. Целью FMEA-анализа процесса производства является обеспечение выполнения всех требований по качеству процесса производства и сборки путем внесения изменений в план процесса для технологических действий с повышенным риском.
Применение данного анализа для оценки эффективности технического обслуживания автомобилей позволило выявить операции с наибольшим значением коэффициента риска, причины возникновения несоответствий и определить факторы, в наибольшей степени, влияющие на качество выполнения работ, назначить мероприятия по улучшению процесса.
Научный руководитель канд. техн. наук, доц. Е.О. Юркова
А.Г. Бондаренко
(факультет «Строительные и дорожные машины)
ВИБРОУДАРНАЯ ТЕХНОЛОГИЯ ВОССТАНОВЛЕНИЯ ПАЛЬЦЕВ ТОРМОЗНЫХ СИСТЕМ НА ЖЕЛЕЗНОДОРОЖНОМ ТРАНСПОРТЕ
В настоящее время на железнодорожном транспорте все большее внимание уделяется безопасности движения. Одной из важных составляющих безопасности является исправность тормозного оборудования подвижного состава. Соответствие размеров деталей пневморычажной системы тормозов номинальным является определяющим для надежности работы тормозного механизма и времени срабатывания системы в целом.
Для шарнирного соединения тормозных тяг используются пальцы длиной от 63 до 120 мм и диаметром от 26 до 55 мм. Их износ приводит к увеличению зазоров в подвижных соединениях, следствием чего является увеличение времени срабатывания тормозов.
Основным дефектом деталей является изменение геометрических параметров выше предельно допустимых в результате износа по рабочей поверхности.
На сегодняшний день в большинстве депо и ремонтных механических мастерских при ремонте тормозного оборудования наряду с восстановлением рабочей поверхности производят замену изношенных пальцев новыми. Это обусловлено тем, что применение существующих технологий восстановления, в частности технологии наплавки, требует больших затрат, а потому экономически невыгодно. Наименее затратным является способ пластической деформации, которая не требует наличия дорогостоящего оборудования и инструмента. Этот способ может быть реализован в виброударном режиме с использованием малогабаритной машины ударного действия.
Восстановление изношенного объема металла может быть осуществлено за счет раздачи пальца при забивании в торец детали вращения стального стержня. В детали, подлежащей восстановлению до номинального диаметра, сверлится направляющее отверстие по всей ее длине. При этом соотношение диаметров стержня и отверстия на восстанавливаемом участке существенно влияет на уровень энергии единичного удара и величину раздачи детали, что является определяющим для качественного выполнения технологической операции.
Восстановленная таким образом деталь может рассматриваться как составная, а соответствующий подбор материала стержня может придать ей новые, улучшенные механические свойства. Кроме того, изготовленные из дорогостоящих износостойких сталей детали можно восстанавливать стержнями из более дешевой стали, не имеющей высокой стойкости к износу.
Предлагаемая технология раздачи цилиндрических деталей и оборудование для ее реализации позволит снизить стоимость восстановления пальцев с сохранением заданных показателей надежности и долговечности их работы в шарнирных соединениях рычажной системы привода тормозов подвижного состава.
Научный руководитель д-р техн. наук, проф. В.А. Каргин
29

М.С. Галай
(факультет «Строительные и дорожные машины»)
ОСНОВНЫЕ НАПРАВЛЕНИЯ СОВЕРШЕНСТВОВАНИЯ ЭЛЕКТРИЧЕСКОЙ НИЗКОЧАСТОТНОЙ МАШИНЫ УДАРНОГО ДЕЙСТВИЯ
Универсальная электрическая низкочастотная машина ударного действия предназначена для оконцевания многопроволочных жил проводов и кабелей в трубчатых наконечниках, опрессовки шлангов высокого давления, запасовки стальных канатов в алюминиевых и стальных гильзах, т.е. операций, требующих силового воздействия на предмет труда.
Машина представляет собой двухкатушечный электромагнитный двигатель, выполненный в виде корпуса с закрепленными в нем катушками прямого и обратного хода, внутри которых перемещается стальной сердечник — боек, передающий через индентор ударное воздействие на обрабатываемую деталь.
Усовершенствование данной машины необходимо осуществить на основе оптимизации времени движения бойка в течение рабочего цикла, равного одному полупериоду напряжения промышленной частоты.
Улучшение технических показателей электрической машины ударного действия является одним из способов повышения конкурентоспособности продукции. Но реалии современного рынка таковы, что продукция должна быть конкурентоспособна не только с технической точки, но также должна соответствовать всем требованиям, изложенным в нормативной документации, присущим этому классу машин. Подтверждение соответствия продукции установленным требованиям обеспечивается сертификацией. Для того, чтобы сертифицировать электрическую низкочастотную машину ударного действия необходимо разработать пакет документов, а также провести сертификационные испытания.
Проведение сертификации универсальной электрической машины ударного действия позволит достичь следующих преимуществ: обеспечить безопасность, надежность продукции (защиту от шума и вибрации); значительный приоритет над конкурирующими изделиями как на внешнем, так и на внутреннем рынках; повышение качества продукции; удовлетворенность требований потребителей (заказчиков).
Научный руководитель д-р техн. наук, проф. В.А. Каргин
А.С. Кочетков
(факультет «Строительные и дорожные машины»)
ЭКСПЕРИМЕНТАЛЬНОЕ ИССЛЕДОВАНИЕ СИЛ, ДЕЙСТВУЮЩИХ ОТ КОЛЕС ПОДВИЖНОГО СОСТАВА НА РЕЛЬСЫ, ДЛЯ ПРОВЕРКИ ТЕХНИЧЕСКОГО СОСТОЯНИЯ ХОДОВЫХ ЧАСТЕЙ ВАГОНА
Измерение силового воздействия колес подвижного состава на путь с использованием тензометрии дает информацию не только о весе вагона, но и о возможных неисправностях узлов и деталей.
Цель работы — экспериментальное исследование сил, действующих от колеса на рельс проходящего подвижного состава с использованием быстродействующей тензометрической системы.
Определение динамических характеристик воздействия проходящего поезда на рельсы типа Р65 проводили на прямом участке пути в реальных условиях эксплуатации. Вертикальные и боковые силы от колес, действующие на рельс, рассчитывались косвенным методом, через измерение деформации материала рельса. В процессе измерений использовалась сертифицированная быстродействующая тензометрическая система «Динамика-1» (сертификат № 32885-06), а также разработанные тензометрические усилители, плата ана- лого-цифрового преобразования типа L783 и переносная рабочая станция ACME II. В качестве первичных измерительных преобразователей использовались наклеиваемые тензодатчики типа КФ5П1-20-400-Н-12 с базой 20 мм, коэффициентом тензочувствительности К = 2,19 ± 0,01 и номинальным сопротивлением R = 398,4 ± 0,01 Ом.
Расчет вертикальных и боковых сил проводили по методу Шлумпфа. Для измерения вертикальных деформаций на шейку рельса симметрично с обеих сторон устанавливались два тензодатчика. По высоте рельса тензодатчики располагали в нижней части шейки на расстоянии (60±1) мм от основания подошвы. В момент прохождения колеса над местом установки тензодатчиков вычислялась сила действующая на рельс как:
FV =KV (U1(t0) + U2(t0)), |
(1) |
FB =KB (U2(t0) – U1(t0)), |
(2) |
где U1(t), U2(t) — сигналы с тензодатчиков, расположенных на внутренней и наружной сторонах рельса, мВ; KV, KB — коэффициенты пропорциональности для вертикальных и боковых сил, соответственно, кН/мВ; t0
— время прохождения колеса над тензодатчиками, с.
Коэффициенты в формулах (1) и (2) определялись экспериментально во время процедуры калибровки. Коэффициент для оценки вертикальной силы KV = 0,18 кН/мВ (5 %) измерялся при медленном прохождении
30
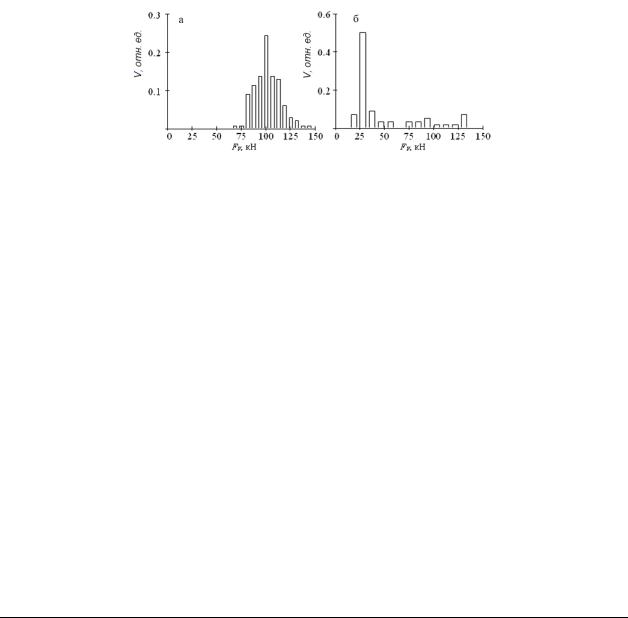
(скорость меньше 6 км/ч) локомотива ВЛ10у с известной осевой нагрузкой 250 кН. Коэффициент KB = 0,051 кН/мВ (3 %) определялся при распоре колеи домкратом с силой 10 кН, прикладываемой к боковым граням головки рельсов.
Максимальная осевая нагрузка для железных дорог РФ, установленная правилами эксплуатации, составляет 250 кН. Следовательно, допустимая вертикальная статическая сила, действующая от колеса на рельс, не должна превышать 125 кН.
Распределение вероятности вертикальной силы рассчитывались из экспериментальных гистограмм. Для груженых вагонов закон распределения вероятности вертикальной силы (рис. 1, а) определялся числом вагонов с грузами различного типа.
Рис. 1. Распределение частоты ν регистрации вертикальной нагрузки FV при прохождении груженого (а) и порожнего (б) состава
Из представленных на рис. 1, а экспериментальных данных находится максимальная вероятность появления вертикальной силы в диапазоне от 100 до 105 кН. Данное распределение является индивидуальным для каждого железнодорожного состава.
При этом 3,8 % всех колес воздействуют на рельс с силой, которая не более чем на 20 % превышает допустимую осевую нагрузку. Распределения вероятности для поезда, в составе которого подавляющее количество пустых вагонов, имеет характерный нижний порог вертикальной силы, равный весу тары четырехосного полувагона на одно колесо (28,1 кН).
Нормативы допускаемого бокового воздействия колес тележки на путь (FB) по условию предотвращения распора колеи для осевой нагрузки 250 кН определяются условием:
FB < 46 кН, |
(3) |
где FB — боковая нагрузка.
Устойчивость против вползания гребня колеса на рельс находится из требования:
K = |
FB |
< 0,86 , |
(4) |
|
|||
|
FV |
|
где FV — вертикальная нагрузка.
Анализ распределения вероятности боковой силы показывает, что она направлена наружу железнодорожной колеи и обеспечивает устойчивое движение экипажа. При этом 3 % обследованных колес создавали боковую силу, которая превышала критическое допустимое значение, определяемое из (3). Из проверенных 128 осей колесных пар ни одна не была забракована по критерию (4).
В работе на практике доказана возможность определения вертикальных и боковых сил методом Шлумпфа. Разработана схема установки и настройки тензодатчиков на рельсе. Проверено более 130 колесных пар на соответствие нормативов допустимого воздействия на путь. Для создания комплексной проверки технического состояния ходовых частей вагона в движении, вместе с известными нормативами по максимально допустимым боковым и рамным силам, необходимо применять критерий обнаружения дефектов поверхности катания колес, основанный на измерении вертикальной динамической силы.
Научный руководитель д-р техн. наук, проф. Л.Н. Степанова
Д.А. Митрошин
(факультет «Строительные и дорожные машины»)
СОВЕРШЕНСТВОВАНИЕ КОНСТРУКЦИИ ЗАПОРНОЙ АРМАТУРЫ НА ВЫСОКИЕ ПАРАМЕТРЫ
В различных отраслях промышленности применяется арматура для установок и трубопроводов, работающих на самых различных средах при давлении от сотен МПа до глубокого вакуума и при температурах от близких к абсолютному 0º до 1000º и более.
31
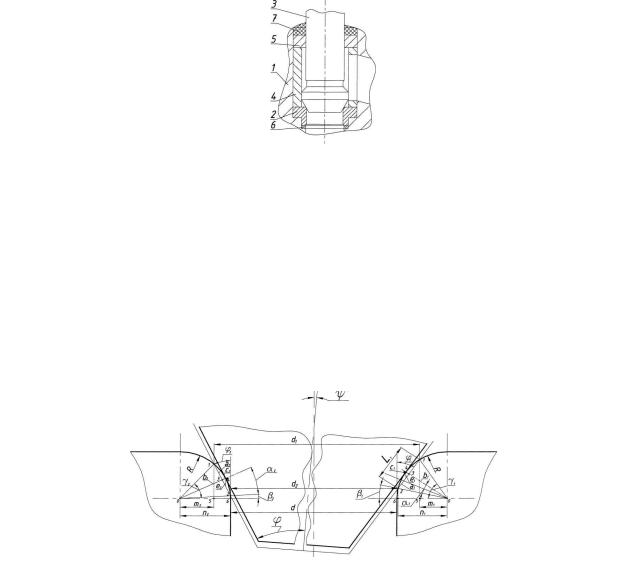
В данном докладе рассмотрена запорная арматура для высоких параметров с рабочей средой — вода, пар. В общем случае арматура содержит следующие основные элементы: корпус с присоединительными патрубками, крышку, рабочий орган и привод. Рабочий орган (РО) арматуры состоит из седла и затвора.
От надежности РО арматуры существенно зависит надежность всего изделия.
Широко распространенный вентиль конструкции Чеховского завода энергетического машиностроения (ЧЗЭМ) имеет в своей конструкции конусные уплотнительные поверхности шток-седло. При отклонении осей конических поверхностей уже на незначительный угол площадь уплотнения значительно уменьшается, что приводит к протечкам. Также затруднен ремонт, для восстановления уплотнительных поверхностей требуется произвести наплавку уплотнительной поверхности корпуса с последующей обработкой и произвести совместную притирку.
Нами предложено уплотнительные поверхности выполнять по конусной (шток) и торообразной (седло) поверхностям.
Такой вариант исполнения уплотнения шток-седло позволил существенно снизить трудоемкость изготовления вентилей, практически исключить брак при их производстве и, что особенно важно, увеличить надежность и срок службы в 1,8–2,5 раза.
На рис. 1 схематично изображена конструкция уплотнительного узла.
Рассмотрим клапанное уплотнение по конусной и торообразной поверхностям, при котором площадь уплотнения меняется незначительно, в зависимости от максимально возможного угла несоосности штока и седла.
Для начала был найден максимальный угол несоосности штока и седла.
Рис. 1. Конструкция уплотнительного узла:
1 — корпус; 2 — седло; 3 — шток; 4 — проставка; 5 — кольцо сальника; 6 — уплотнение; 7 — кольцо сальника
При некотором усилии формируется соосная уплотнительная поверхность, которая представляет собой усеченный конус с основанием в виде эллипса. Найдем диаметры эллипсов основания конуса (рис. 3):
d1 = d + 2R − m1 − m2 , d2 = d + 2R − n1 − n2 ,
где d1, d2 — большие диаметры верхнего и нижнего эллипса, мм; d — пропускной диаметр седла, мм; R — радиус скругления седла, мм; п1, п2 — расстояния от центра скругления (т. 0) до точки 6, мм; ml, m2 — расстояния от центра скругления (т. 0) до точки 5, мм.
Расстояния mi и ni определим из треугольников 015 и 026 (рис. 2). Используя схему (рис. 4) найдем mi и ni .
Зная t и f найдем малые диаметры (рис. 5):
d3 = d + 2R − 2n3.4 , d4 = d + 2R − 2m3.4.
Рис. 2. Схема расчета больших диаметров поверхности контакта шток-седло
32