
книги / Новые композиционные и керамические материалы
..pdfк их классификации. Практически все способы могут быть отнесены к двум основным группам:
–методы твердофазного спекания керамического порошка,
втом числе с применением различных порообразователей (выгорающих, газобразующих добавок, волокнистых заполнителей и т.д.) и пенообразователей;
–методы структурного выщелачивания или возгонки одного из компонентов системы.
При более детальной классификации выделяют 10 принципиально отличающихся друг от друга методов:
–подбор зернового состава исходной массы для формования;
–введение в исходную массу зерен природного или искусственного полученного заполнителя, имеющего собственную пористость;
–вспучивание в ходе термической обработки всей массы или отдельных ее компонентов;
–вовлечение воздуха в суспензии керамических материалов при их механической обработке за счет введения пенообразующих добавок или отдельно приготовленной пены;
–вдувание или образование газа в расплаве и удержание газовых пузырьков;
–закрепление в суспензии газовых пузырьков, образующихся в результате протекания химических реакций взаимодействия или разложения вводимых в массу газообразующих добавок;
–дублирование полимерной матрицы с последующим ее удалением в процессе термообработки;
–экструзия пластифицированных керамических масс;
–введение в массу керамических волокон;
–введение в исходную массу и последующее удаление (испарением, возгонкой и т.д.) добавок, оставляющих поры.
Реальные способы получения часто являются комбинацией 2–3 различных методов. Рассмотрим некоторые из них.
Одним из наиболее простых способов получения пористых керамических материалов является спекание порошков с введе-
91
нием в исходную шихту различных выгорающих добавок-
порообразователей. Для создания пористости в керамическую массу перед формованием вводят разлагающиеся или газообразующие компоненты. Такими компонентами являются органические вещества: кристаллическая мелкодисперсная целлюлоза, амины, спирты, высшие масла, кремнийорганические смолы, а также карбонаты, нитраты и другие неорганические соединения, которые разлагаются с образованием газообразных продуктов при нагревании. Газообразующие добавки и добавкипорообразователи помогают регулировать объем и размеры пор. Например, после выгорания мелкодисперсной целлюлозы, введенной в исходную керамическую шихту, остаются пустоты таких же малых размеров, как и кристаллы микроцеллюлозы. Поры остаются после удаления разлагающихся веществ, содержащихся в исходной шихте, при нагревании до температуры разложения.
Существует много других менее тонких методов создания пористости, например введение древесных опилок, крахмала, различных видов углей и продуктов коксования, полых полимерных гранул и т.д. В зависимости от состава шихты, вида добавки и проектируемой конфигурации изделий используют порошкообразные, пластичные и жидкотекучие массы.
Регулирование пористости и размера пор керамических пористых материалов при спекании осуществляется также за счет изменения гранулометрического состава порошков исходных материалов. Например, использование узкофракционных зерен заполнителя. Известно, что при кубической укладке равновеликих шаров пустотность составляет почти 50 %. Однако реализовать такую модель упаковки практически невозможно, так как керамические зерна не шаровидные и даже при узком фракционировании различаются по размерам. Поскольку крупные зерна практически не спекаются, обычно вводят часть тонких зерен, образующих керамическую связку в обжиге.
92
При использовании монофракционных зерен, содержании 10 % тонких фракций, давлении прессования 5–10 МПа удается получать керамику с пористостью 35–40 % и равномерным строением. Пористость может быть повышена до 50–65 %, если заменить плотные зерна заполнителя гранулами с собственной пористостью.
Использование в качестве выгорающих добавок узкофракционных полимерных дисперсных материалов позволяет управлять процессом порообразования. Для создания пористых керамических материалов с регулируемой сквозной пористостью необходимо получение в керамических массах бесконечных кластеров выгораемых частиц. Для этого надо выбрать условия, при которых полимерные частицы создают во всем объеме массы бесконечные кластерные структуры. После выгорания этих структур в керамических материалах формируются соответствующие им сквозные поры. Например, в исходный керамический порошок вводят непредельный углеводород, способный полимеризоваться при нагревании, эмульгатор и воду. Полимеризация непредельного углеводорода происходит при температуре менее 100 оС в течение 1–48 ч. После сушки органическое вещество удаляют прокалкой при температуре 1000 оС и изделие обжигают при 1400–1600 оС. Регулирование пористости осуществляется путем изменения количества воды. Увеличение количества воды приводит к увеличению пористости, а ее уменьшение снижает пористость и повышает прочность. Способ позволяет получить пористую керамику, имеющую равномерно распределенные поры размером 1–10 мкм.
В другой работе в качестве порообразователя использован узкофракционированный полиметилметакрилат (ПММА) с размером сферических частиц ~ 0,2 мкм. Содержание оксида алюминия в исходной шихте составляло 80 %. Исходные смеси с различным содержанием порообразователя прессовали, сушили, затем проводили многоступенчатую термообработку и спекали при температуре 1180 оС. В зависимости от содер-
93
жания ПММА диаметр пор в полученных образцах составлял
10–60 мкм.
3.4.1 Использование волокнистых материалов для получения пористых материалов
Процесс изготовления пористых волокнистых изделий сводится к получению собственно волокон, формованию из них различными методами изделий в виде пластин, труб и других и стабилизации полученной пористой структуры путем применения разнообразных связующих.
Для связывания волокон используют как органические (битумы, синтетические смолы), так и неорганические (глины, цемент, растворимое стекло и т.д.) связующие, выбор которых определяется условиями предстоящей службы изделий. Первые обеспечивают большую прочность и пористость, вторые – более высокую жаростойкость.
Связки распыляют на волокна, затем смесь уплотняют валками, избыток связующей жидкости удаляют. Полученные полуфабрикаты подвергают тепловой обработке.
3.4.2. Метод дублирования полимерной матрицы
Керамические материалы с пористостью 70–95%, имеющие высокую аэро- и гидропроницаемость, получают методом дублирования полимерной матрицы, являющимся разновидностью метода выгорающих добавок. В качестве полимерной матрицы, образующей сетчато-ячеистый каркас, который воспроизводят путем нанесения керамического порошка и выжигания основы, наиболее часто применяют органические вспененные полимеры. Первые данные о получении высокопористых материалов методом дублирования полимерной матрицы появились в США и Великобритании и относятся к концу 50-х – началу 60-х гг. XX в. В Научном центре порошкового материаловедения Пермского государственного технического университета разработка высокопористых керамических материалов методом дублирования поли-
94
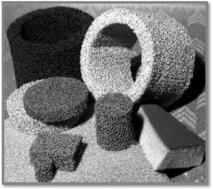
мерной матрицы ведется с 1976 года. К этому же времени относится и начало систематического изучения керамических материалов, полученных методом дублирования полимерной матрицы, в России и странах СНГ.
Рис. 31. ВПЯМ. Общий вид
Материалы были названы высокопористыми ячеистыми материалами (ВПЯМ) (рис. 31), встречается название «высокопористые проницаемые». Материалы, для которых характерно наличие очень высокой макропористости, называются высокопористыми в соответствии с зарубежной традицией (highly porous). В США и европейских странах принят также термин «пе-
нокерамика» (ceramic foam, das keramischen Schaumkörper).
Технологический процесс формования состоит из приготовления суспензии керамического порошка, нанесения ее на полимерную основу, удаления избытка суспензии, сушки пропитанной заготовки и спекания (рис. 32).
95
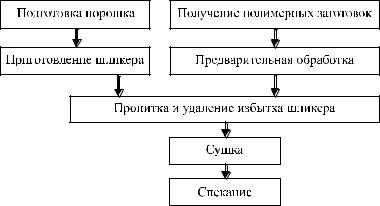
Рис. 32. Общая схема приготовления ВПЯМ
Подготовка порошка и приготовление шликера, хотя и имеют ряд особенностей, существенно не отличаются от традиционно применяемых в керамике (измельчение, синтез исходного порошка и т.д.). При получении ВПЯМ используют порошки диоксида циркония, муллита, оксида алюминия, талька, кордиерита, нитрида кремния и другие. Получение полимерных заготовок включает в себя выбор полимера с сетчато-ячеистым каркасом, операции по обеспечению его максимальной проницаемости за счет удаления перегородок между ячейками и нарезку пластин. Обычно применяют пенополиуретан, который выпускается во всем мире в количествах, превышающих выпуск всех остальных вместе взятых пенополимеров. Также важную роль играют высокая стойкость в агрессивных средах, отсутствие набухания и хорошие адгезионные свойства.
Одной из важнейших характеристик ВПЯМ является средний диаметр ячеек (d), отличающийся от диаметра ячеек в направлении, перпендикулярном к направлению вспенивания (d ) и диаметра ячеек в направлении вспенивания (dII) (рис. 33).
96
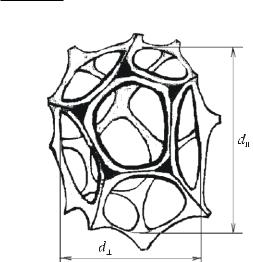
Связь между этими характеристиками находится из соотноше-
ния d 2d dII .
3
Рис. 33. Элементарная ячейка ВПЯМ
В состав шликера входят дисперсионная фаза (керамический порошок), дисперсионная среда и различные добавки, улучшающие реологические свойства шликера или адгезию к поверхности пенополиуретанов.
Для того чтобы шликер прочно удерживался на поверхности перемычек пенополиуретана вплоть до высыхания, в состав керамических шликеров вводят различные органические и неорганические клеящие вещества, способные образовывать пленку на поверхности органической пены, выгорающую без остатка вместе с материалом матрицы. Для этих целей применяют такие вещества, как декстрин, карбоксиметилцеллюлоза, поливиниловый спирт (ПВС). Для приготовления шликера чаще всего используют 3–5 %-й раствор ПВС в зависимости от вида ППУ и состава керамической композиции.
97
Соотношение дисперсной фазы и дисперсионной среды может изменяться в довольно широких пределах, на практике обычно применяют 2,0–2,3.
При шликерном литье, разновидностью которого является метод дублирования полимерной матрицы, шликеры должны обладать:
–низкой вязкостью, позволяющей пропитать куски пеноматериала с различным диаметром ячейки и толщиной;
–пределом текучести, способствующим фиксации шликера вплоть до полного высыхания на произвольно ориентированной стенке перемычки пористого полимерного материала без стекания с нее;
–высоким содержанием дисперсной фазы;
–равномерным распределением дисперсной фазы в дисперсионной среде (отсутствием расслаивания).
Наибольшее влияние на реологию шликера оказывает дисперсная фаза, в частности такие ее характеристики, как полярность, плотность, смачиваемость, дисперсность частиц и их распределение по размерам, форма частиц. В каждом отдельном случае, особенно при использовании порошков сложного состава, необходимо учитывать влияние тех или иных компонентов шихты на свойства шликера.
Пропитка осуществляется погружением в керамический шликер с применением вибрации или механического воздействия (циклы сжатие-растяжение). Наиболее сложной задачей является удаление избытка шликера при сохранении по возможности более однородного слоя керамического порошка на поверхности ППУ. Для жестких пенополиуретанов применяют метод центрифугирования, а для эластичных ППУ – метод отжимания.
3.4.3.Особенности спекания ВПЯМ
Входе спекания происходит деструкция пенополиуретана (ППУ), которая протекает в три этапа. В интервале 220…330 оС происходит потеря упругости ППУ. Степень деструкции на этом
98
этапе 0,2–0,3. При температуре 330–420 оС полимерный каркас быстро разрушается, степень деструкции 0,8, а при температуре выше 420 оС происходит окисление высокоуглеродистого остатка. Процесс сильно замедляется и к 660 оС прекращается практически полностью. Таким образом, до температуры 660 оС имеются еще какие-то остатки сетчато-ячеистого каркаса пенополиуретана, поддерживающего керамический порошок. При более высоких температурах и вплоть до спекания форма каркаса сохраняется только за счет адгезии керамических частиц. Не спеченный керамический каркас очень хрупок, что обычно является препятствием для каких-либо манипуляций с заготовкой на этой стадии. Тонкие перемычки имеют достаточную прочность только при спекании при температурах, близких к температуре плавления керамического материала, которая, например, для кордиеритового и цельзианового фарфоров составляет свы-
ше 1300 оС.
В большинстве случаев поверхность спеченного материала представляет собой практически беспористую копию поверхности выгоревшей органической матрицы. Перемычка керамического высокопористого материала не сплошная и имеет довольно сложное строение (рис. 34). Внутри, почти повторяя ее очертания, расположена полость, образовавшаяся после выгорания органической матрицы. Полость соединена с внешней поверхностью перемычки узкими каналами диаметром ~ 0,03 мм, по которым происходило удаление продуктов деструкции ППУ. Толщина стенок, образующих перемычку, 0,06–0,22 мм. Стенки перемычек и каналов гладкие. Форма закрытых пор, образовавшихся в процессе спекания из-за неплотной упаковки частиц, близка к правильной.
99

Рис.34. Перемычка ВПЯМ
На усадку материала и его прочность оказывает влияние анизотропия ячейки, так как ячейка ППУ приближена по форме к пентагондодекаэдру, вытянутому по одному из направлений (направлению вспенивания пенополиуретана) в 1,2–1,5 раза. В случае совпадения направления вспенивания ППУ с направлением силы тяжести анизотропия ячейки уменьшается, при несовпадении – увеличивается.
На усадку материала при спекании оказывает влияние также толщина слоя керамического порошка, нанесенного на полимерную основу. Спекание ВПЯМ, как и керамических материалов вообще, является очень сложным процессом, приводящим к объемным и фазовым изменениям исходных керамических материалов. При высоких температурах идут деструкция одних и синтез других соединений, изменение модификации, стеклообразование, зарождение и рост кристаллов и многие другие процессы, которые могут привести как к получению материала с высокими эксплуатационными характеристиками, так и к его разрушению.
100