
книги / Новые композиционные и керамические материалы
..pdf3.2. Конструкционная керамика на основе
карбида кремния
Карбид кремния нашел широкое применение в технике благодаря уникальному сочетанию физических свойств регулируемой электропроводности, высокой твердости и теплопроводности, малому температурному коэффициенту линейного расширения (ТКЛР), высокому сопротивлению окислению при температурах < 1500 оС. Эти свойства стимулируют разработку широкого класса материалов на основе SiC, включая материалы конструкционного назначения.
Преимущественно ковалентный тип химической связи в SiC не позволяет получать из него обычным спеканием изделия высокой плотности без введения добавок, активирующих процесс спекания.
В отсутствие активирующих добавок спекание порошков карбида кремния можно реализовать при температуре выше 2100 оС. При этом образуется поликристаллический материал с высокой пористостью 22–40 %, так называемый рекристаллизованный карбид кремния.
Достижение более высокой плотности рекристаллизованных материалов возможно путем введения активирующих добавок. Параметры получения и реализуемые свойства спеченного SiC (рис. 27) в значительной степени зависят от вида и количества активирующих добавок, которые можно разделить на кислородсодержащие и бескислородные. К первой группе отно-
сятся Al2O3, Y2O3, CeO2, BeO, их комбинации Al2O3–Y2O3, Al2O3–MgO. Ко второй группе относятся B, C, B4C, BN, BP, AlN и такие их комбинации, как В–С, Al–C, B–Al–C и др.
Плотная керамика на основе SiC имеет модуль упругости 380–480 ГПа; прочность при изгибе 700–1000 МПа; К1С = 3–4 МПа·м1/2; коэффициент теплопроводности 65–320 Вт/(м·К); ТКЛР=(3,5–4)10-6 К-1 в интервале 20–1000 оС. Значение К1С можно
81
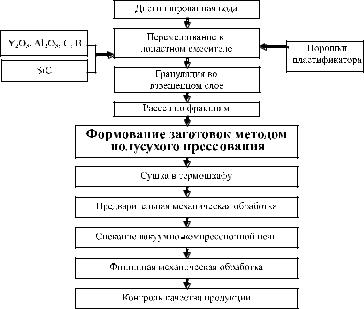
повысить до 7–8 МПа·м1/2 введением дисперсной фазы TiB2. При высоких температурах керамика сохраняет высокие прочностные свойства: при 1500 оС прочность при изгибе достигает 500 МПа.
Добавка оксида алюминия, как правило, позволяет уменьшить размер кристаллов до 1–2 мкм, что позволяет достичь прочности 750 МПа. В то же время образование алюмосиликатов по границам кристаллов SiC при нагревании приводит к тому, что горячая прочность при температурах выше 1000 оС у керамики с добавкой Al2O3 ниже, чем с добавкой бора и углерода.
В качестве исходного вещества для использования в технологии спеченного карбида кремния применяются микропорошки SiC с размером частиц 0,6–1,5 мкм и высокой степени чистоты, примеси металлов не должны превышать 0,1 %, содержание кислорода должно быть менее 1 %.
Рис. 27. Принципиальная схема получения спеченного карбида кремния
82
Вводимые добавки при спекании инициируют фазовый переход -SiC -SiC, что способствует процессу спекания карбида кремния. Например, добавка бора при температуре выше 2000 оС приводит практически к полному переходу -SiC -SiC с образованием крупных неизометричных пластинчатых кристаллов SiC политипа 6Н. При введении добавки алюминия и оксида бериллия происходит частичный переход -SiC -SiC с преимущественным образованием политипа 4Н и формированием структуры из изометричной формы кристаллов.
Использование оксидных активаторов позволяет получать плотные материалы из SiC при температурах до 2000 оС, боруглеродных – до 2200 оС. Наиболее предпочтительной для спекания является среда аргона.
Остаточная пористость материала влияет на основные фи- зико-механические характеристики. Так, твердость спеченного карбида кремния 26–28 ГПа при нулевой пористости падает до 20 ГПа при пористости 5–6 %. При горячем прессовании (ГП) порошков карбида кремния без добавок также получаются изделия с высокой пористостью. Так, при давлении 58,84 Мпа и температуре 2350 оС максимальная относительная плотность горячепрессованного SiC-материала не превышает 84 %.
При введении в прессуемые порошки карбида кремния добавки аморфного бора были получены изделия с пористостью до 4 % при удельном давлении прессования порядка 9,8 МПа. ГП получило широкое развитие при изготовлении мелкосерийных ответственных деталей простой формы, не требующих механической обработки. Технология ГП карбида кремния по сравнению с обычным спеканием позволяет снизить количество добавок, сохранить исходную мелкодисперсную структуру, использовать более грубодисперсные порошки, достичь практически беспористого состояния.
При использовании порошка -SiC (средний размер частиц 0,26 мкм) с добавками 6 % Al, 1 % B и 1 % C увеличение удельного давления прессования от 20 до 60 МПа при температуре
83
1650 оС приводит к увеличению плотности горячепрессованных образцов от 2,6 до 3,1 г/см3, а прочность при изгибе возрастает при этом от 340 до 550 МПа. Анализ микроструктуры горячепрессованного SiC-материала показал наличие областей, вытянутых перпендикулярно направлению прессования, что свидетельствует о жидкофазном механизме спекания в условиях горячего прессования SiC.
Для получения изделий сложной формы применяют метод изостатического горячего прессования (ГИП). При этом могут осуществляться два варианта применения технологии ГИП: 1) доуплотнение без капсулирования предварительно спеченного полуфабриката до относительной плотности 93–95% и 2) обработка порошкообразных полуфабрикатов, капсулированных в газонепроницаемую оболочку из молибдена, вольфрама или тантала. Температура процесса составляет 1950 оС при давлении 200 МПа, а выдержка 2–3 часа. Наибольшее уплотнение при горячем прессовании (2000 оС) порошков SiC достигается с использованием добавок бора и углерода.
Горячепрессованные SiC-материалы имеют более высокий уровень механических свойств по сравнению с рекристаллизованным карбидом кремния. Однако реализация метода горячего прессования в промышленных масштабах связана с чрезвычайно большими трудностями по причине низкой стойкости графита, используемого для пресс-форм и способного работать при температурах выше 2000 оС, а применение метода горячего изостатического прессования связано со значительными усложнениями технологии.
Приведенных выше недостатков, отмеченных для получения SiC-материалов методами рекристаллизационного спекания и горячего прессования, лишена технология получения поликристаллического SiC-материала методом реакционного спекания, при котором заготовка, прессованная из смеси порошков первичного карбида кремния и углеродистого материала, пропитывается расплавом или парами кремния. При использовании этого метода имеется широкий выбор способов формования за-
84
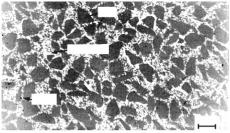
готовок изделий (полусухое, гидростатическое прессование, шликерное литье, экструзия, инжекция), а получаемые при этом после реакционного спекания материалы обладают свойствами, близкими к свойствам материалов, получаемых горячим прессованием.
Впервые SiC-изделия методом реакционного спекания были получены в 1950-х гг. При этом в качестве углеродистой добавки использовались графит, смесь древесного угля и пекового кокса, нефтяной кокс, сажа. Временной связкой в таких изделиях служили резольно-формальдегидная смола, параформальдегид, декстрин, пульвербакелит и жидкий бакелит. Пропитка заготовок кремнием проводилась в среде его расплава и паров при температуре 2050 оС
иатмосферном давлении либо при 1500–1600 оС в вакууме.
Вкомпозиционной системе SiC–Si и в системе SiC–Si–C при наличии углерода и избытка несвязанного кремния в процессе пропитки прессованной заготовки жидким кремнием наблюдается процесс перекристаллизации исходного карбида
кремния (SiCи) через жидкий кремний (путем растворения наиболее мелких зерен SiC в кремнии и осаждении их на более крупных) и формирование кристаллов SiC правильной огранки или близкой к ней (рис. 28).
SiC
Silicium
Pore
m
Рис. 28. Микроструктура реакционноспеченного SiC, полученного пропиткой заготовки из SiC расплавом кремния
Силицирующий обжиг заготовок, прессованных из порошков SiC и шихты состава SiC–C, сопровождается следующими физикохимическими процессами: 1) непосредственно химическим взаимо-
85
действием кремния с углеродом и образованием карбида кремния (Si + C → SiC); 2) растворением углерода в расплаве кремния и выделением из него карбида кремния; 3) растворением карбида кремния в жидком кремнии – перекристаллизацией. Все эти процессы могут протекать совместно, но интенсивность их протекания существенно зависит от температуры.
Так, при температурах 1600 и 1700 оС процесс силицирования углеродосодержащих заготовок идет достаточно неполно, остается до 4,5–6,0 % несвязанного углерода. При температуре 1800 оС процесс карбидообразования резко интенсифицируется, содержание углеродистого компонента снижается до 0,2–3,4 % в зависимости от выдержки. Образующийся при этом вторичный карбид кремния (SiCв), представляющий собой изначально мелкие кристаллы -SiC-модификации, при повышении температуры до 2000 оС начинает перекристаллизовываться в -SiC. В результате формируется структура реакционноспеченного SiCматериала, представляющая собой зерна карбида кремния, сросшиеся в единый карбидный каркас, в котором диспергированы в виде полигональных участков включения несвязанного кремния.
Структуру реакционноспеченного SiC-материала, получаемого при одном и том же режиме силицирования, можно регулировать изменением содержания углерода в шихте, плотности прессованных заготовок, а также крупностью частиц составляющих шихту компонентов. На рис. 29 представлена технологическая схема получения изделий из реакционноспеченного карбида кремния.
Достигнутый уровень свойств карбидкремниевой керамики, полученной по рассмотренным выше технологиям, приведен в табл. 6.
|
|
|
|
Т а б л и ц а 6 |
|
Сравнительный уровень свойств различных видов |
|||||
|
карбидкремниевой керамики |
|
|
||
|
|
|
Вид керамики |
|
|
Свойства |
|
|
|
|
|
|
реакционно- |
спеченный |
ГП |
ГИП |
|
|
|
спеченный |
|
|
|
Плотность, г/см3 |
|
2,9–3,1 |
2,7–3,15 |
3,05–3,2 |
3,15–3,2 |
ТКЛР 10-6 К-1 |
|
4,3–3,5 |
4,4–4,8 |
3,9–5,4 |
4,0–5,2 |
86
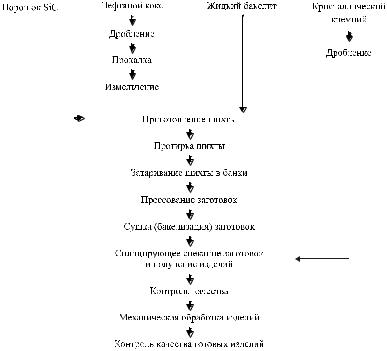
|
Теплопроводность при 300 |
45–81 |
40–85 |
80–110 |
90–150 |
||||||||||||
|
К, Вт/(м К) |
|
|
|
|
|
|
|
|
|
|
|
|
||||
|
Модуль Юнга, ГПа |
350–380 |
207–402 |
410–450 |
420–450 |
||||||||||||
|
|
|
|
|
|
|
|
|
|
|
|
|
|
|
|
|
|
|
К1С, МПа м1/2 |
4,0 |
|
|
2,5–6,5 |
3–4 |
5,5–7,0 |
||||||||||
|
Прочность при изгибе, МПа |
175–500 |
340–580 |
550–800 |
600–800 |
||||||||||||
|
|
|
|
|
|
|
|
|
|
|
|
|
|
|
|
|
|
|
Максимальная температура |
1200–1400 |
1500–1600 |
1400– |
1600 |
|
|
||||||||||
|
применения, оС |
|
|
|
|
|
1600 |
|
|
|
|
||||||
|
|
|
|
|
|
|
|
|
|
|
|
|
|
|
|
|
|
|
|
|
|
|
|
|
|
|
|
|
|
|
|
|
|
|
|
|
|
|
|
|
|
|
|
|
|
|
|
|
|
|
|
|
|
|
|
|
|
|
|
|
|
|
|
|
|
|
|
|
|
|
|
|
|
|
|
|
|
|
|
|
|
|
|
|
|
|
|
|
|
|
|
|
|
|
|
|
|
|
|
|
|
|
|
|
|
|
|
|
|
|
|
|
|
|
|
|
|
|
|
|
|
|
|
|
|
|
|
|
|
|
|
|
|
|
|
|
|
|
|
|
|
|
|
|
|
|
|
|
|
|
|
|
|
|
|
|
|
|
|
|
|
|
|
|
|
|
|
|
|
|
|
|
|
|
|
|
|
|
|
|
|
|
|
|
|
|
|
|
|
|
|
|
|
|
|
|
|
|
|
|
|
|
|
|
|
|
|
|
|
|
|
|
|
|
|
|
|
|
|
|
|
|
|
|
|
|
|
|
|
|
|
|
|
|
|
|
|
|
|
|
|
|
|
|
|
|
|
|
|
|
|
|
|
|
|
|
|
|
|
|
|
|
|
|
|
|
|
|
|
|
|
|
|
|
|
|
|
|
|
|
|
|
|
|
|
|
|
|
|
|
|
|
|
|
|
|
|
|
|
|
|
|
|
|
|
|
|
|
|
|
|
|
|
|
|
|
|
|
|
|
|
|
|
|
|
|
|
|
|
|
|
|
|
|
|
|
|
|
|
|
|
|
|
|
|
|
|
|
|
|
|
|
|
|
|
|
|
|
|
|
|
|
|
|
|
|
|
|
|
|
|
|
|
|
|
|
|
|
|
|
|
|
|
|
|
|
|
|
|
|
|
|
|
|
|
|
|
|
|
|
|
|
|
|
|
|
|
|
|
|
|
|
|
|
|
|
|
|
|
|
|
|
|
|
|
|
|
|
|
|
|
|
|
|
|
|
|
|
|
|
|
|
|
|
|
|
|
|
|
|
|
|
|
|
|
|
|
|
|
|
|
|
|
|
|
|
|
|
|
|
|
|
|
|
|
|
|
|
|
|
|
|
|
|
|
|
|
|
|
|
|
|
|
|
|
|
|
|
|
|
|
|
|
|
|
|
|
|
|
|
|
|
|
|
|
|
|
|
|
|
|
|
|
|
|
|
|
|
|
|
|
|
|
|
|
|
|
|
|
|
|
|
|
|
|
|
|
|
|
|
|
|
|
|
|
|
|
Рис. 29. Технологическая схема производства изделий из реакционного карбида кремния
87
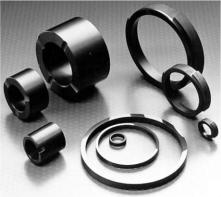
Рис. 30. Кольца скольжения и уплотнительные кольца из SiC
Керамические детали из плотного SiC используют для изготовления роторов газовых турбин, накладок на поршни, подшипников, фильер, высокотемпературных теплообменников, форсунок, горелок и т.д. (рис. 30). Керамические пресс-формы из SiC выдерживают до 500 тыс. циклов. Широкое применение спеченная керамика из SiC нашла в производстве бронеодежды,
вкомбинированной защите военной и банковской техники.
3.3.Керамические нагревательные элементы сопротивления
Внастоящее время известны следующие материалы, которые можно применять в качестве нагревательных элементов при высокой температуре: молибден, вольфрам, графит, диоксид
циркония, хромит лантана LaCrO3, дисульфит молибдена, карбид кремния и др. Mo, W, C и другие можно применять и при температуре > 2000 оС, но в этих случаях значительным лими-
тирующим фактором является окружающая рабочая среда. В качестве нагревательных элементов, которые можно применять при высокой температуре, несмотря на окисление и открытую окружающую рабочую среду, известны ZrO2, LaCrO3,
МoSi2, SiC и др.
88
Нагреватели из SiC – типичные неметаллические нагревательные элементы сопротивления, которые можно применять при высокой (~ 1400–1600 оС) температуре в печах с нормальной воздушной средой. Нагревательные элементы обычно изготавливают из карбида кремния зеленого цвета без примесей – α-SiC с гексагональной структурой. Нагревательные элементы являются изделиями из рекристаллизованного карбида кремния. Они не имеют других связующих веществ, кроме SiC. Свойства: плотность 3,2 г/см3, открытая пористость 19–30 %, предел прочности при изгибе 40–70 МПа, твердость 2,4–3,2 ГПа, коэффициент теплопроводности 18,6–25,6 Вт/(м·К). Сопротивление SiC минимально при 550–600 оС, от комнатной температуры до указанной уменьшается, при более высоких температурах увеличивается. Стойки к действию кислот и щелочей, очень стабильны при обычной температуре. Однако при очень высокой температуре они иногда проявляют реакционную способность под влиянием водяного пара, водорода, азота и т.д.
Нагревательные элементы из LaCrO3 представляют собой керамику, полученную в результате частичной замены в твердом растворе ионов La на ионы Са. Свойства: температура плавления 2490 оС, плотность 6,5 г/см3, пористость 21 %, предел прочности при изгибе 50 МПа, коэффициент теплопроводности 1,8 Вт/(м·К). Нагревательные элементы из LaCrO3 реагируют уже при сравнительно низкой температуре со щелочами, оксидами MgO, SiO2 и др., в результате чего ухудшается электропроводность нагревательного элемента. Поэтому в качестве футеровки применяют Al2O3, который сохраняет химическую стабильность для 1800 оС.
89
3.4. Керамические пористые материалы
Керамические изделия и материалы данного класса должны обладать повышенной пористостью (обычно более 30 %), которую создают преднамеренно. Она определяет решающим образом свойства, необходимые для их применения, такие как высокая тепло- и звукоизолирующая способность, проницаемость, удельная поверхность и некоторые другие.
Пористый – изобилующий порами. Poros (греч.) – отверстие, проход, скважина. Порами называют пустоты в материале, несплошности. Пористые материалы – материалы, часть которых занята порами.
К основным разновидностям классификации пористых материалов относятся разделение материалов по пористости и плотности, по строению, по химическому составу, по огнеупорности, по назначению:
–по пористости и плотности материалы подразделяют на низкоплотные с относительно невысокой пористостью 35–40 %; легковесы (пористость 45–75 %) и ультралегковесы (пористость свыше 75 %);
–по строению различают изделия с зернами наполнителя, ячеистые (включая пенные) и волоконные;
–по химическому составу выделяют силикатные, алюмосиликатные, оксидные, бескислородные и т.п.;
–по огнеупорности подразделяют на легкоплавкие (менее 1350 оС), тугоплавкие (1350–1580 оС), огнеупорные (1580– 1770 оС), высокоогнеупорные (1770–2000 оС), высшей огнеупорности (≥ 2000 оС);
–по назначению выделяют теплоизоляционные изделия (решающий показатель – коэффициент теплопроводности); теплозащитные; фильтрующие (один из основных показателей – коэффициент проницаемости).
Способы получения пористых керамических материалов очень многообразны, что предопределяет и различные подходы
90