
книги / Технология композиционных материалов
..pdfРазностная схема (2.60) - (2.61) является частным случаем разностной схемы для уравнения теплопроводности общего вида. Для
рассматриваемой задачи можно применить более эффективный |
метод. |
|||
Положим, что |
на каждом из отрезков [Л. r +f ] |
функции |
Жг,#) |
|
и РСг,#*) |
постоянны и равны |
2(r}/) = Xj+i/v |
=■<%■+ t/2' |
|
Тогда уравнение (2.57) примет |
вид |
|
|
Проинтегрировав уравнение (2.62), получим |
|
|
|
||||||||
г £. , , |
|
|
+ “ 9 ~ |
- |
7 +<kу2 |
* Е г-С. = О, |
|
||||
J+11Чг dr*- |
|
”2 |
J |
|
' |
(2.63) |
|||||
|
|
|
|
|
|
|
|
|
|
|
|
Л е с 2 |
|
$ w ] |
|
</ = 0~ / |
|
|
|
||||
Введем обозначение для тешювого потока: |
|
|
|
||||||||
~ |
|
+ |
д^л |
= |
d-S(r-) |
|
|
(2.64) |
|||
|
<t+ /2 |
|
|
|
|
|
|
||||
Тогда из уравнения (2.63) имеем |
|
|
|
|
|
|
|
||||
|
5ГГ) |
= |
|
0 *. |
,, |
+ С. |
|
|
(2.65) |
||
Константу интегрирования |
|
С. |
определим из |
уравнения |
(2.65) |
||||||
при л = г. |
|
|
|
|
^ |
|
|
|
|
|
|
|
С.= |
S. |
|
2 |
|
e<j+ 1k |
|
|
|
||
|
J |
|
</ |
|
|
|
|
|
|||
Отсвда |
|
|
|
|
|
|
|
|
|
|
|
и в |
- |
5 |
- |
л г - л / |
(У |
|
|
(2.66) |
|||
-----;г— |
1k |
|
|||||||||
|
|
|
|
|
|
|
|
</ * |
|
|
|
Согласно первому из краевых условий |
(2.58) |
имеем S0 |
= 0, |
||||||||
следовательно, |
|
|
|
|
|
|
|
|
|
|
|
|
|
|
2 |
2 |
|
|
|
|
|
|
|
|
|
r-L.-n |
|
|
|
|
|
|
(2.67) |
||
|
|
|
|
|
|
|
|
|
|
|
Тогда второе краевое условие из (2.58) |
дает |
|||
* |
* |
( TN ~ в '>> |
||
откуда |
|
|
|
|
|
|
|
£* |
|
ТЫ = в |
+ |
~ |
SN |
|
Воспользовавшись формулой |
(2.66), |
проинтегрируем |
||
(2.64) и получим |
|
|
|
|
с 2 |
|
|
|
|
77л/ = 7. -
= 0. л/-/
/
Откуда имеем
Г = 7 |
+ = - |
</ |
d |
где |
|
(2.68)
уравнение
(2.69)
л ' |
- л 1 |
|
|
|
|
Л = |
4 |
|
|
|
|
J |
|
<f |
|
|
|
|
|
|
|
|
|
Если мы хотим обеспечить нужную температуру Т* |
в |
заданной |
|||
точке, то соответствующую величину |
можно вычислить |
следующим |
|||
образом. Пусть |
Т* = Тк |
тогда из |
соотношений (2.69) |
и |
(2.67) |
получим |
|
|
|
|
|
|
|
D - ( T |
cZ |
|
•л = . |
|
Ж+1/l |
<+Sk К +1> |
|
||
|
к+Z |
|
|
• l-< fr, *1.11,1
Отсвда находим
T* - в
Схема расчета распределения температуры по данной |
методике |
|||||
такова: |
|
|
|
|
S. |
|
- |
из рекуррентных соотношений |
(2.67) |
находим |
, |
||
- |
по формуле (2.70) |
определяем |
Тн ; |
|
^ |
|
- |
по формуле (2.68) |
определяем |
|
Т. |
t ; = ,У-/ |
|
- |
из рекуррентных соотношений |
v2.69) |
находим |
N - г .............о . *
При расчете предложенным методом этапы 3 и 4 основной расчетной схемы выполняются вместе.
Результаты расчетов. Расчеты выполнялись для заготовок |
со |
||||||||||||||
следующей геометрией: |
RQ = 9,2 см, |
R, = 10,65 |
см, |
^ = 25 |
см, |
||||||||||
R, = 25,4 см, |
И |
= 37 см. |
|
|
|
характеристики: изделия fa = |
|||||||||
Используемые теплофизические |
|
||||||||||||||
= 0,393 |
г/см3, |
fa = 1,80 |
г/см3 . |
|
%0 = 0,09 |
Вг/см-°С, |
|
||||||||
= 0,1 Вт/см«°С, |
<о0 = 2 , 3 |
см/Ом, |
|
3п= 138,9 |
см/Ом; |
нагревателя |
|||||||||
HQIP |
= 0,4 йг/см-°С, |
|
в |
HQ7.P |
- |
793,7 |
см/Ом; |
теплейзоляции |
|||||||
- |
|
|
|
|
^ |
|
= 0 см/0м; |
теплообмена |
на |
||||||
Я-иъол |
= 0,002 Вт/см.°с, |
|
0 -иГзол |
||||||||||||
внешней поверхности |
|
di = 0,8 |
йг/(ч-и.°и), |
9 = 50 °С. |
|
||||||||||
Технологические характеристики |
процесса: |
Т* = Ю0С |
|
||||||||||||
$(t) =■ RQ + (ft % |
if= 0,25 |
мм/ч. |
|
|
|
|
|
|
|
|
|||||
Обсудим результаты расчетов иг примере трех вариантов. |
|
||||||||||||||
В а р и а н т |
I . |
Полагаем, |
что |
величина |
|
постоянна и |
равна 26,4 см-1 - среднему значению полученной |
из геометрических |
||
соображений зависимости Syd(F) (2 . 68). |
Сила |
тока, проходящего |
|
через заготовку, определялась |
по формуле |
|
|
jii) = L ^ U ) |
- 6f(i)* М |
] W 5/i6 |
которая аппроксимирует экспериментальные данные для соотвегст.зую-
щего процесса. Вдоль координаты |
л |
брали равномерную разностную |
||||||
сетку |
с числом узлов |
N = 100, |
шаг |
по времени |
At = 3600 |
с. |
||
|
На рис.2.31 представлены результаты распределения температуры |
|||||||
вдоль |
координаты |
л |
в разные моменты времени от |
начала |
процесса. |
|||
|
Отметим, что температура в каждый момент времени |
монотонно убы |
||||||
вает. Кроме того, |
T ( f ) Ф Т* |
и их отличие в различные моменты вре |
||||||
мени составляет до 100 °С (т .е . |
величину порядка 10 % |
от |
значений |
|||||
Т# ). Это связано с |
некоторой нестыковкой модели по отношению к |
|||||||
экспериментальным значениям силы тока. |
|
|
|
|
|
|
|
|
Рис.2.31. Распределение тем |
||||||||||||
|
|
|
|
|
пературы в заготовке в раз |
||||||||||||
|
|
|
|
|
личные моменты времени |
от |
|||||||||||
|
|
|
|
|
начала |
пиролиза: / |
|
- |
$ |
= |
|||||||
|
|
|
|
|
= 10,65 |
см, |
начало |
пиролиза; |
|||||||||
|
|
|
|
|
|
2 |
- |
| |
|
= 15,45 |
см, |
через |
|||||
|
|
|
|
|
8 |
суток; |
5 - |
^ |
= 20,25 |
см, |
|||||||
|
|
|
|
|
через 16 |
|
суток; |
4 |
|
- f |
= |
||||||
|
|
|
|
|
= 22,65 см, через 20 суток |
||||||||||||
На рис. 2.32 |
представлены результаты распределения |
|
плотности |
||||||||||||||
материала заготовки вдоль координаты Л |
в разные моменты |
времени |
|||||||||||||||
от начала процесса. |
|
|
|
|
|
|
|
|
|
|
|
|
|
|
|
||
|
|
|
|
|
Рис.2.32. Зависимость плотно |
||||||||||||
|
|
|
|
|
сти материала |
заготовки |
|
от |
|||||||||
|
|
|
|
|
ее радиуса в процессе пироли |
||||||||||||
|
|
|
|
|
за: |
/ |
- |
£ |
= 13,65 |
см, |
через |
||||||
|
|
|
|
|
5 суток; |
2 |
|
f |
|
16,65 |
см, |
||||||
|
|
|
|
|
через |
Ю суток; |
3 |
- |
£ |
= |
|
||||||
|
|
|
|
|
= 19,65 |
см, |
через |
15 |
суток; |
||||||||
|
|
|
|
|
4 |
- |
f |
= 22,65 |
см, |
|
чэрез |
||||||
|
|
|
|
|
|
|
|
20 суток |
|
|
|
|
|
||||
Отметим, |
что наблюдается значительное |
отставание |
фронта |
пиро |
|||||||||||||
лиза от положения рабочей термопары..Оно составляет для |
моментов |
||||||||||||||||
времени /-4 |
соответственно 2,45; |
2,25; |
1,85 |
и 1,45 |
см. |
|
|
|
|
||||||||
В а р и а н т |
2. Зависимость Sy$ |
от |
плотности |
бралась |
в |
||||||||||||
соответствии с (2.68). |
В этом случае существенным моментом являет |
||||||||||||||||
ся то, что в начальной |
стадии /'зарастания" |
каркаса, |
|
при |
изменении |
||||||||||||
плотности от 0,393 до 0,763 г/см3 величина |
Sy# |
|
убывает |
|
от |
1000 |
|||||||||||
до 17,5 см”-1-. |
|
|
|
|
|
Т($) |
|
|
|
|
|
|
|
|
|
|
|
Для ликвидации дисбаланса величин |
и |
|
7* на каждом вре |
||||||||||||||
менном шаге использовалась следующая пересчетная процедура: |
|
|
|||||||||||||||
- определение |
Г- |
, j = Qtu |
при |
силе |
тока |
|
3 = 30 = 3('in) |
|
|||||||||
согласно формуле (2. 57); |
|
|
|
|
|
|
|
|
|
|
|
|
|
|
|||
- определение |
7. |
j, = 0tM |
при |
J = Jf = J0 + лj |
|
|
|
|
|
|
,(т'-т„ц»J , ♦ <-т,а)-тчз„
|
|
|
|
|
1 |
|
|
|
|
ъ ш |
|
- |
W |
|
) |
|
|
|
|
|
|
|
||
где |
Т0 (\) |
и |
7^ |
( $) |
- |
значения температуры в |
точке |
л = f |
при |
|||||||||||||||
|
|
|
|
|
|
|
|
|
|
7 |
= 30 |
и |
7 |
= 7^ ; |
|
|
|
|
|
|
||||
|
- |
определение |
7} |
|
%j |
|
= о,М |
при |
7 = J2 |
|
|
|
|
|
|
|||||||||
|
Поскольку |
величина |
|
j 2 |
входит |
в уравнение |
(2.6В) |
линейно, |
||||||||||||||||
то такая |
процедура |
практически |
полностью устраняет |
|
дисбаланс |
|||||||||||||||||||
Т($) и |
Т* |
Число узлов |
|
в разностной |
сетке по |
|
N |
и шаг по |
вре |
|||||||||||||||
мени |
|
|
брали |
как |
в |
варианте |
I. |
|
|
|
|
|
|
|
|
|
||||||||
|
Результаты расчетов представлены на рис.2.33 распределениями |
|||||||||||||||||||||||
плотности |
материала |
заготовки |
вдоль |
координаты |
л |
в |
оазличные мо |
|||||||||||||||||
менты времени от |
начала |
процесса. |
|
|
|
|
|
|
|
|
|
|||||||||||||
|
|
|
|
|
|
|
|
|
|
|
|
|
|
|
Г, |
|
|
|
|
|
|
|
|
|
|
|
|
|
|
|
|
|
|
|
|
|
|
|
г/см1 |
|
|
|
|
|
|
|
|
|
|
Рис.2.33. |
|
Изменение |
плотности |
|
i.- |
|
|
|
|
|
|
|
|
|
||||||||||
заготовки |
в процессе |
пиролиза: |
|
|
|
|
|
|
|
|
|
|
|
|||||||||||
О- |
начало |
пиролиза; |
/ |
|
- |
| |
|
= |
|
|
|
|
|
|
|
|
|
|
|
|||||
= 15,45 |
см, |
через |
8 |
суток; |
2 - |
|
|
|
|
|
|
|
|
|
|
|||||||||
£ |
= 17,85 |
ем, |
через |
12 |
суток; |
|
|
|
|
|
|
|
|
|
|
|||||||||
j - |
f |
= 20,25 |
см, |
через |
|
16 |
|
1,( |
|
|
|
|
|
|
|
|
|
|||||||
суток; |
4 |
|
| |
= 22,65 |
см, |
через |
|
|
|
|
|
|
|
|
|
|
||||||||
2С суток; |
|
5 |
| |
|
= 20,65 |
см, |
|
|
|
|
|
|
|
|
|
|
|
|||||||
через 24 |
суток; |
6 ,7 |
- / = 2 5 , 0 5 |
см |
|
|
|
|
|
|
|
|
|
|||||||||||
через |
26 |
и через |
38 |
суток |
|
|
|
|
|
|
|
|
|
|
|
|
||||||||
|
|
|
|
|
|
|
|
|
|
|
|
|
|
|
|
|
|
|
|
|
|
22 |
24 Г)Ом |
|
|
Отметим, что в этом варианте фронт пиролиза существенно "раз |
|||||||||||||||||||||||
мыт". Распределения плотности |
носят немонотонный характер, что свя |
|||||||||||||||||||||||
зано со спецификой поведения функции |
|
при 0,393 |
^ f ^ |
|||||||||||||||||||||
<0,763. Отставание фронта |
пиролиза |
от |
положения рабочей |
термопары |
||||||||||||||||||||
в моменты времени |
1-5 |
составляет |
соответственно |
4,8; |
4,65; |
4,85; |
||||||||||||||||||
4,65 и |
4,55 |
см. |
|
|
|
|
|
|
|
|
|
|
|
|
|
|
|
|
|
|
|
|||
|
В а р и а н т |
|
3. Расчет в течение 24 суток от начала пироли |
|||||||||||||||||||||
за проводился так же, |
как |
и |
в |
варианте |
2. После |
этого точка положе- |
кия рабочей термопары фиксировалась |
( | = 25,05 см) |
и темпера |
тура в ней изменялась по закону |
|
|
7Y f)= Т* + 0(1 |
- 24сут) |
|
где а - 1,5 град/ч. |
|
|
Полученные распределения плотности через 26 и 28 |
суток от |
|
начала пиролиза представлены на рис.2.33 кривыми 6 и |
7 . Отсюда |
видно, что применение формулы (2.59) позволяет эффективно запол нить периферийную часть изделия.
Глава 3. ТЕХНОЛОГИЯ ПРОИЗВОДСТВА ИЗДЕЛИЙ ИЗ КОМПОЗИЦИОННЫХ МАТЕРИАЛОВ НА ПОЛИМЕРНОЙ МАТРИЦЕ
3.1. Структура технологического процесса
3 .1 .I . Факторы, определяющие структуру технологического процесса, и исходные данные для проектирования
При изготовлении конструкций из волокнистых полимерных ком позитов материал и изделие формируется одновременно путем совме щения компонентов, при этом изделиям сразу придаются заданные геометрические размеры. Тип армирующего наполнителя, природа по лимерного связующего и конструкция детали определяют особенности технологического процесса переработки композиционного материала в изделие, при котором должна обеспечиваться необходимая ориента ция армирующего наполнителя, совмещение его со связующим, уплот нение материала и отверждение полимера.
Для проектирования технологического процесса производства из
делий из |
ПКМ исходными являются следующие данные: |
|
|
I) |
рабочий |
чертеж изделия (детали), в котором должны |
быть |
указаны размеры |
и соотношения, характеризующие геометрию |
и точ |
ность взаимного расположения всех видов основных и свободных по
верхностей, допуски и шероховатость поверхностей, материал |
и ос |
|
новные |
его структурные характеристики (схема армирования, |
число |
слоев и |
т .д .); |
|
2) технические требования на ПКМ и его характеристика - сос тавляющие компоненты, их относительное содержание, структурные параметры, характеристика исходных материалов, их технологические свойства;
3) технические требования на исс о; ные материалы;
4) технические требования на го: o iэе изделие и его испытание;
5)справочные сведения о технолсг. шских методах переработки ПКМ в изделие;
6)данные об оборудовании и технологической оснастке;
7)типовые технологические процессы;
8)производственное задание (программа выпуска).
3.1.2. Требования к технологическому процессу
Технологический процесс изготовл- н i изделий из ПКМ должен обеспечить:
-получение готового изделия с з дг ными физико-механически ми и специальными свойствами;
-точность и качество основных п зе юностей изделия и точ ность их относительного расположения;
-точность, качество и координации относительно друг друга
свободных поверхностей изделия;
-точность взаимного расположения системы основных и свобод ных поверхностей изделия;
-неизменяемость геометрии и размеров основных и свободных
поверхностей и их взаимной координации с течением времени;
-неизменяемость физико-механических и других свойств ПКМ в заданный период времени;
-производство с минимальными затратами и максимальной тех нико-экономической эффективностью.
При разработке технологических процессов решаются две техно логические задачи: формирование и получение ПКМ и формирование и получение изделия из ПКМ. Эти задачи могут быть решены методом технологической автономности (технологической независимости) либо методом технологического совмещения.
Первый метод применяют в основном в технологии металлических композиционных материалов. Например, вначале изготавливают полу фабрикат - лист, профиль, а затем из него изготавливают конкретную
деталь. В производстве конструкционных ПКМ, как правило, приме няют второй метод - метод технологического совмещения, когда процессы получения готового ПКМ и готового изделия технологичес ки совмещены и протекают одновременно. Это позволяет существенно сократить технологический цикл и резко удешевить производство.
3.1.3. Основные технологические операции
Технология изготовления деталей из волокнистых полимерных композитов включает следующие основные операции:
-входной контроль исходных материалов на соответствие ТУ
иГОСТам;
-подготовка армирующего наполнителя;
-приготовление связугацего;
-совмещение армирующего наполнителя со связующим;
-сборка и ориентация слоев армирующего наполнителя по фор
ме детали;
-уплотнение;
-отверждение и термообработка композита;
-механическая обработка;
-контроль качества изделий.
Входной к о н т р о л ь исходных компонентов играет особую роль, так как даже незначительные отклонения технических характеристик и свойств исходных компонентов отражаются на конечных результа тах технологического процесса и качестве изделия. Входной конт роль необходимо вывести из разряда случайных факторов, не поддаю
щихся прямому управлению и учету, в разряд систематических, |
поз |
воляющих производить отбраковку некондиционных материалов |
либо |
необходимую корректировку технологического процесса.
При входном контроле по действующим на предприятии методикам подвергаются проверке наполнители, все компоненты связующего, рас творители, антиадгезивы и другие материалы, предусмотренные техно логическим регламентом.
Цель входного контроля свойств исходных материалов - не толь ко отбраковка некондиционных материалов, но и установление конк ретных физико-механических свойств, позволяющее управлять процес сом создания изделий из ПКМ с заданными характеристиками.
В отличие от контрольно-сдаточных операций, где испытания на соответствие параметров готовых материалов выполняются ОТК, входной контроль параметров исходных материалов является не пе репроверкой, а операцией технологического процесса изготовления изделий из ПКМ. Поэтому он выполняется не контролерами ОТК, а производственными рабочими (лаборантами).
Подготовка армирующего наполнителя включает операции, на правленные на подготовку поверхности волокон к совмещению и по следующему взаимодействию с полимерными связующими. Эти операции в большинстве случаев проводятся на заводах, производящих арми рующие волокна и наполнители на их осйове. К таким операциям от носятся: расшлихтовка, аппретирование, вискеризация; активирова
ние поверхности, химическая |
очистка, сушка, подшлихтовка. |
|
Р а с ш л и х т о в к а |
- удаление излишнего |
количества за - |
масливателя с поверхности армирующих волокон путем |
прокаливания |
при температуре 473-723 К или пропускания через растворители. Для интенсификации процесса отмывки от замасливателя применяют ультра звук. Технологические замасливатели используют в производстве во локнистых наполнителей для предотвращения механических поврежде ний волокна при его переработке.
А п п р е т и р о в а н и е - нанесение на поверхность ми неральных и металлических волокон покрытий из растворов кремнийорганических и других соединений толщиной в несколько молекуляр
ных слоев, |
обеспечивающих гидрофобность волокон и химическое вза |
||||
имодействие |
с полимерной матрицей. Закрепление |
производится на |
|||
греванием до 353-473 К. |
|
|
|
|
|
В и с к е р и з а ц и я |
- выращивание на |
активных центрах |
|||
поверхности углеродных или карбидокремниевых волокон |
нитевидных |
||||
кристаллов |
С , StC , АСЫ и других путем газофазных реакций осаж |
||||
дения при температуре 1553-1673 К. |
|
|
|
||
А к т и в и р о в а н и е |
п о в е р х н о с т и |
- |
обработ |
||
ка углеродных волокон в жидкоили газофазных окислителях, |
приво |
||||
дящая к окислению и стравливанию поверхностного слоя |
волокна. |
||||
Травление проводят в азотной кислоте и в ее смеси с серной |
при |
||||
температуре |
353-393 К или в газовых средах (воздух, озон) |
при |
|||
температуре |
673-1073 К. |
|
|
|
|
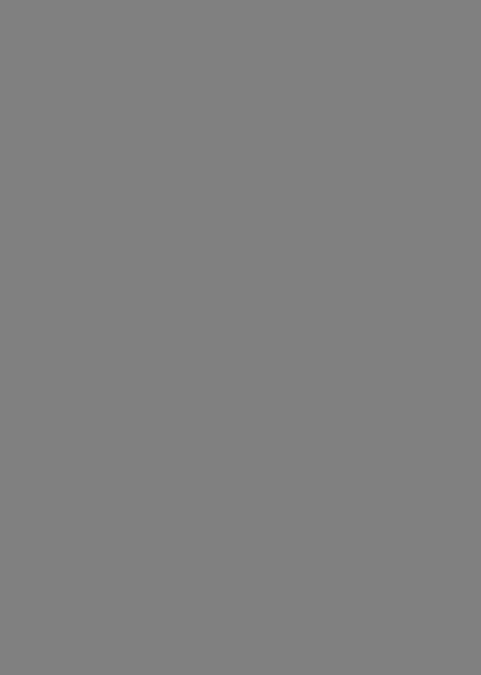