
книги / Технология композиционных материалов
..pdfТермопары для контроля и регулирования режима термостатирования в количестве не менее двух размещаются непосредственно на технологическом припуске. Концы термопар выводятся через швы ва куумного мешка перед их окончательной склейкой и закрепляются термостойкой липкой лентой.
В качестве разделительной ткани можно применять специально обработанную ткань на лавсановой основе.
Для разделения элементов и обеспечения легкого демонтажа на детали и узлы после полимеризации наносят тонкий слой антиадгезионного вещества - смесь кремнийорганического воска и поливинило вого спирта, а может быть применен только воск. Перед нанесением смазочного слоя поверхность оснастки обезжиривают.
3.5. Ооорудование для переработки полимерных композиционных материалов
По ряду выполняемых технологических операций оборудование для переработки ПКМ в изделия можно классифицировать следующим образом:
1.Оборудование для получения и подготовки материалов и по верхностей.
2.Оборудование для формообразования.
3.Оборудование для отверждения.
4.Оборудование для контроля качества.
5.Оборудование для утилизации.
Эта классификация не является строгой, так как зачастую в комп лексе оборудования тот или иной вид оборудования выполнен в виде модуля, осуществляющего операцию неразрывного технологического процесса.
3 .5 |
.1 . Оборудование для подготовки материалов |
|
К этом классу относится: |
|
- оборудование для предварительной обработки связующего пе |
ред |
совмещением с наполнителем; |
-оборудование для обработки наполнителя перед совмещением
сматрицей;
-пропиточное оборудование для получения препрега.
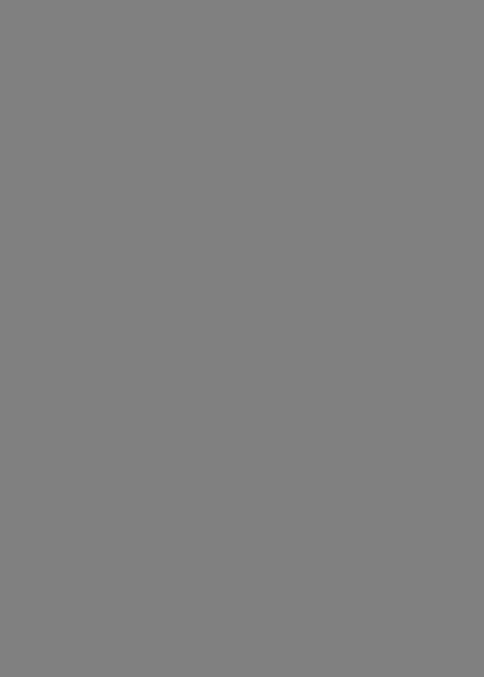
жащей изделие .с вакуумным мешком, и постоянный отсос летучих. Лучшие результаты достигаются при отверждении изделий в ав токлавах и гидроклавах. При этом изделие вместе с формой помеща ется в герметичный вакуумный мешок, из которого откачивается воз
дух, а также летучие, образующиеся в процессе отверждения. От верждение проводят под давлением 0,5-7 МПа. Температурный режим определяется типом ПКМ. Рабочая среда при автоклавном формова нии - азот, при гидроклавном - глицерин.
Для физических методов отверждения разработаны установки ра диационно-химической полимеризации в инфракрасных лучах. Но в настоящее время их применение в промышленности ограничено.
3 .5 .4 . Оборудование для разделительных операций
Ни один из распространенных в машиностроении способов раз мерной обработки изделий из композиционных материалов всех типов не обеспечивает высокого качества, так как при обработке готовых изделий вследствие механического воздействия инструментов на ма териал происходит межслойное разрушение и охрупчивание волокон в зоне обработки. При раскройных операциях углеродных тканей "раз лохмачиваются” и кромки реза. Разделительные операции традицион ными методами сопровождаются выделением большого количества пы ли, вредной для здоровья людей.
Решить эти проблемы позволяет использование для разделитель ных операций (раскрой, вырезка окон, размерная обработка) лазер ного луча, ультразвука, струи жидкости под давлением. Все эти про цессы легко автоматизируются.
3 .5 .5 . Оборудование для контроля качества
В производстве изделий из ПКМ важное значение имеют неразру шающие методы контроля качества и физико-механических свойств изделий.
Контроль сплошности и других скрытых дефектов осуществляют установками ультразвукового и рентгеновского контроля. Для непро водящих электрический ток изделий применяют также СБЧ-метод, ко торый позволяет проводить послойное зондирование.
Плотность материала определяют радиационными плотномерами, УЗК-плотномерами; модули упругости всех родов - акустическими ме тодами; прочность - голографическими методами •
Универсальным средством контроля являются вычислительные то мографы.
Для контроля геометрии сложных поверхностей наряду с кон тактными методами применяют более точные установки контроля с использованием лазерной техники, в частности автоматизированный комплекс неконтактного контроля с использованием лазерного опти ко-электронного дальномера. Эта установка позволяет измерять де тали диаметром до 5000 мм с точностью +0,05 от теоретической кри визны в любой точке контролируемой поверхности.
Глава 4. ТЕХНОЛОГИЯ ПРОИЗВОДСТВА КОМПОЗИЦИОННЫХ МАТЕРИАЛОВ НА МЕТАЛЛИЧЕСКОЙ МАТРИЦЕ
4.1.Общая характеристика процессов получения
иобработки композиционных материалов
Методы изготовления, используемые для получения композицион ных материалов на металлической матрице (МКМ) из различных комби наций волокон и матриц, непосредственно определяются свойствами этих волокон и матриц. Одни и те же методы могут быть использова ны для производства как готовых изделий, так и полуфабрикатов:
листов, полос, труб и т.д . 3 производстве рассматриваемых матери алов необходимо различать получаемые на предварительной стадии простые полуфабрикаты или препреги. К ним относятся волокна с покрытиями, предварительно пропитываемые жгуты волокон, сетки, по ристые ленты с одним слоем волокон и т.д .
Препреги используются в качестве элементов сборных много слойных заготовок - полуфабрикатов, получаемых компактированием.
Получаемые компактированием полуфабрикаты затем подвергаются процессам формообразования, раскроя, сварки, механической обработ ки для изготовления детали или узла. В ряде случаев процессы фор мообразования и компактирования могут быть совмещены, т .е . изго товление изделий может быть одностадийным (изделие формируется сразу) или двухстадийным. При двухстадийном изготовлении процессы
получения простого полуфабриката или препрега называют процесса ми первичного производства композиционных материалов.
При изготовлении композиционных материалов и изделий из них любым из существующих методов необходимо соблюдать следующие условия:
-сохранять прочность волокон на всех стадиях производствен ного процесса;
-предотвращать разрушение волокон;
-применять специальные меры по улучшению смачивания и сцеп ления между матрицей и волокнами;
-обеспечивать надлежащую упаковку, пространственное распре деление и ориентацию волокон в матрице.
4.2. Классификация методов производства композиционных материалов на металлической матрице
Методы получения и обработки МКМ удобно разделить |
на |
три ос |
новные категории: твердофазные, жидкофазные и осаждения. |
В |
от |
дельных технологических процессах могут применяться комбинирован ные методы.
Иногда указанную классификацию рассматривают как классифика цию процессов первичного производства композиционных материалов с металлической матрицей. В этом случае методы изготовления КМ на металлической матрице подразделяются на метод порошковой ме таллургии, технологии с использованием фольги и литье.
Для каждого из названных методов изготовления КМ характерны свои предварительные и заключительные операции. При изготовлении КМ методом порошковой металлургии предварительными являются опера ции укладки волокна в матрицу, затем иишкерное литье в каркас из волокон или скрепление волокон летучим связующим. Заключительными технологическими операциями являются спекание, горячее прессование (изостатическое или изотермическое).
При использовании метода фольги предварительными технологи ческими операциями являются скрепление волокон с фольгой летучими связующими или склеивающими веществами; прессование чередующихся слоев волокон и фольги; точечное либо непрерывное соединение фольги с волокнами (например, прокаткой). Окончательной операцией может быть диффузионная сварка по типу горячего прессования.
В случав применения метода литья предварительными технологи ческими операциями служат: литье готового изделия, или нанесение жидкого металла на поверхность отдельных волокон, или изготовле ние из непрерывных лент. При этом методе заключительные операции не нужны, либо применяют горячее прессование, или горячее изостатическое прессование.
4.2.1. Твердофазные методы получения композиционных материалов на металлической матрице
Твердофазные методы получения КМ с металлической матрицей предполагают механическое объединение (смешение) матрицы в виде порошка или фольги с волокнистым наполнителем. Твердофазные ме тоды широко используются при получении конструкционных компози тов. Этими методами получают многослойные ленты, листы, стержни, панели, лопатки турбин, силовые элементы в авиастроении.
Применяемые для производства композиционных материалов на металлической матрице твердофазные методы делят на три класса: импульсные, статические, динамические.
Импульсные твердофазные методы включают в себя три группы процессов: сварка взрывом, магнитно-импульсное компактирование, гидроимпульсное (электрогидроимпульсное) компактирование.
К статическим методам относятся диффузионная сварка, гидро статическое компактирование, спекание под давлением, изостатическое компактирование, термокомпрессионное компактирование, прес сование, статическая формовка.
Динамические методы - прокатка, волочение, динамическое го рячее прессование, роликовая формовка, вальцовочная прокатка.
4.2.1.1. Импульсные твердофазные методы
Импульсные, или высокоскоростные, методы компактирования наи более перспективны. Необходимая для компактирования или формиро вания энергия придается заготовке с огромной скоростью. В качест ве источников энергии используется энергия взрыва взрывчатых ве ществ (ВВ), электрический разряд в жидкой среде (обычно в воде) и импульсное электромагнитное поле. В зависимости от вида источника энергии эти новые способы получили название сварка взрывом, электрогидравлическое компактирование, электромагнитное компактирование.
Такие способы компактирования относятся к высокоэнергетичес
ким, так как совершают полезную работу за тысячные |
доли |
секунд |
||||
с колоссальной мощностью. |
|
|
|
|
|
|
При применении высокоскоростных способов компактирования от |
||||||
падает необходимость |
в прессовом оборудовании. В качестве |
техно |
||||
логической оснастки используется лишь один жесткий |
формующий |
|||||
элемент - пуансон или матрица. Роль ответной части оснастки |
иг |
|||||
рает передающая среда, через которую проходит энергия |
в |
виде |
||||
ударной волны от энергоносителя. |
|
|
|
|
|
|
Сварка в з р ы в о м . |
В качестве источника энергии при |
сварке |
взры |
|||
вом (компактирование энергией взрыва) используются бризантные |
|
|||||
взрывчатые вещества - тротил порошкообразный и литой; |
аммонит |
|||||
порошкообразный и прессованный; пластифицированные |
взрывчатые |
|||||
вещества, выпускаемые в виде ленты и листов. Последние более |
удоб |
|||||
ны в технологическом процессе, так как |
позволяют вырезать |
заряд, |
||||
соответствующий форме компактируемого |
изделия. |
|
|
|
|
|
Обычно сваркой взрывом получают изделия плоской |
|
формы |
или |
|||
в форме кольца. |
|
|
|
|
|
|
Метод компактирования энергией взрыва отличается чрезвычай ной простотой. На металлическое основание на прокладке из инерт ного материала укладываются чередующиеся слои матричной фольги и волокон. Над сборкой устанавливают массивную метаемую пластину, на которой располагают заряд БВ с детонатором. Массивная метаемая пластина служит энергоносителем, а параметры пластины (скорость
полета, масса пластины) являются основными параметрами сварки МКМ по этой схеме. Эта схема позволяет до некоторой степени сохранять параметры сварки МКМ постоянными для верхних и нижних пластин.
При взрывном компактировании часто используют схему сварки без метаемой пластины. В этом случае заряд ВВ располагается непо средственно на верхнем матричном слое, отделенном от матричной фольги инертной прокладкой.
Применяемые при сварке взрывом бризантные взрывчатые вещества отличаются большой удельной концентрацией энергии и большими ско ростями детонации - до 7000 м/с. Давление у поверхности заряда доходит до 250*I03 - 300* Ю8 кг/см2 (25*Ю3 - 30*I03 МПа).
Электрогшгоанлическое компактирование.При компактировании МКМ электрогидравлическим способом через жидкую среду пропускают мощ
ный кратковременный электрический разряд, который создает удар ную волну, воздействующую на компактируемый пакет либо через ме таемую пластину, либо через инертную диафрагму. Основным рабочим органом установки является разрядный контур, включающий конденса торную батарею и рабочий искровой зазор между электродами, нахо дящимися в резервуаре с водой. При достижении на конденсаторах определенного потенциала происходит пробой в воздушном разрядни ке и накопленная в конденсаторах энергия мгновенно преобразуется в искровой разряд в рабочем зазоре, в жидкости возникает газопа ровая область высокого давления. Возникает ударная волна, кото рая и осуществляет работу компактирования. При необходимости ав томатически может быть произведено несколько следующих друг за другом разрядов.
Разность потенциалов в применяемых установках достигает 4U кВ. При этом в рабочем промежутке разрядника возникают давления, рав ные нескольким тысячам атмосфер.
Этот способ позволяет изменять форму ударной волны в зависи мости от формы изделия применением так называемых инициирующих (взрывных) проволочек, которые соединяют электроды в рабочем зазо
ре разрядника. Можно применять не только |
взрывные проволочки, но |
|
и взрывные пластинки, ленты. Например, взрывная лента |
определенной |
|
ширины может создать более плоский фронт |
волны и тем |
самым обеспе |
чить равномерное усилие деформирования по всей поверхности компактируемого пакета.
Электромагнитное компактирование. Электросхема установок для электромагнитного компактирования аналогична электросхеме установок для электрогидравлического компилирования, однако принцип преобра зования накопленной в конденсат )рах электрической энергии в необхо димую для компактирования разли шн. Электромагнитное компактирова ние основано на преобразовании электрической энергии в механическую за счет импульсного разряда конденсатора через соленоид, вокруг ко торого при этом возникает мгновенное магнитное поле высокой мощнос ти, наводящее вихревые токи в трубчатой или плоской токопроводящей заготовке (матричного материала и армирующего волокна). Взаимодейст
вие вихревых токов с магнитным полем создает механические |
(пондер- |
|
моторные) силы, |
которые производят компактирование. |
|
В процессе |
деформирования заготовка под воздействием магнитно |
|
го поля получает ускорение в несколько сотен тысяч метров |
в секунду, |
развивая к моменту контакта всех слоев пакета с жестким основани ем скорость 200-300 м/с и испытывая давление до 4000-5000 кг/см2 (400-500 МПа) и более. Основной рабочей характеристикой магнитно импульсных установок является величина запасаемой энергии в кон денсаторной батарее, достигаемая 60-30 кДж.
При магнитно-импульсном пакетировании непосредственно магнит ным полем композита из материалов с низкой электропроводностью применяются технологические прокладки из медной или алюминиевой фольги, так называемые спутники, которые укладывают на компактируемый пакет. Процесс можно осуществить и без спутников. В этом случае для возбуждения пондермоторных сил в систему вводится спе циальный элемент - метательный диск из материала с низким омичес ким сопротивлением. При взаимодействии магнитных полей соленоида (индуктора) и диска последний с высокой скоростью устремляется к пакету и компактирует его.
4 .2 .1 .2 . Статические твердофазные методы
Статические процессы - диффузионная сварка, гидростатическое компактирование, спекание под давлением, изостатическое компактирование, термокомпрессионное компактирование, прессование, стати ческая формовка - применяются для компактирования конструкционных КМ, причем для композитов с хрупкими волокнами они являются основ ными, а для некоторых и единственно возможными.
Одним из основных видов полуфабрикатов и изделий, изготавли ваемых этими методами, являются трубы и другие полые профили.
Диффузионная сварка (спрессовывание по схеме диффузионной сварки). Полые издании большого диаметра и малой длины могут быть получены сваркой давлением сборных трубчатых заготовок с использо ванием наружной технологической оболочки и осевого вкладыша (тех нологического наполнителя).
Сущность процесса заключается в том, что при внедрении прессшайбы во вкладыш технологического наполнителя на стенки сборного пакета (заготовки трубчатого изделия) действует давление, вызван ное сопротивлением материала технологического наполнителя истече нию в полость цресо-^вИбы. и происходит сварка давлением. Силовые условия процесса з£висят от величины внутреннего диаметра прессшайбы, через которую истекает материал технологического наполни теля.
Температура прессования бороалюминиевых труб 560 °С, усилие
прессования до 80 кН. Полые изделия, полученные по |
этой |
схеме, |
при объемной доле волокон 50 % имеют сопротивление |
разрушению |
|
при растяжении 1200-1300 МПа. |
|
|
Другим вариантом изготовления армированных труб |
является |
|
компактирование за счет давления изнутри полой заготовки |
(в тех |
нологической оболочке) при прохождении через ее полость пуансона или нескольких последовательно уплотняющих пуансонов. Для труб из бороалюминия (волокна бора с покрытием карбидом кремния) сред ний коэффициент уменьшения сечения уплотняемой заготовки состав ляет 1,065. При этом сопротивление разрушению бороалюминиевых труб при растяжении равно 950-1150 МПа.
Прессование элементов плоских пакетов - заготовок по схеме диффузионной сварки - наиболее универсальный процесс.
Существует множество путей и схем реализации компактирования КМ на металлической матрице по схеме диффузионной сварки.
Сварка давлением пои горячем прессовании. При получении плос ких панелей и листов прессованием сборных заготовок в большинстве случаев, когда в композите используют хрупкие волокна, в качестве технологической оснастки применяют пресс-формы. В этих случаях прессование связано с изменением только одного размера заготовки - ее толщины. Панели на основе титановых сплавов с объемной долей волокон бора 21-27 % с покрытием карбидом крешшя после прессова
ния при температуре 760 ПС под давлением 84,4 МПа и |
с выдержкой |
|||
I час имеют временное сопротивление разрыву до 1400-1450 |
МПа. |
|
||
Гидростатическое компактирование. Изготовление спирально-ар |
||||
мированных труб с металлическими проволочными волокнами |
может |
|||
осуществляться методом гидростатического |
прессования |
пб |
схеме, |
|
при которой изделие выдавливается через |
канал матрицы вместе |
с |
||
оправкой под действием высокого давления жидкости. |
Заготовка |
|
||
должна быть предварительно герметизирована. При изготовлении |
ста- |
лездшиниевых труб процесс осуществляется с 50 /Р-ным обжатием за готовки по сечению при температуре 200 °С.
Ашютермическое компактирование. Этим способом изготавлива ют изделия: трубы, оболочки, профили, листы из легкоплавких МКМ, например из бороалюминиевого КМ. Наибольшее применение этот спо соб нашел при компактирования трубчатых изделий, его называют еще