
книги / Технология композиционных материалов
..pdf3 .3 .1 .3 . Пресс-камерное формование
При формовании этим методом заготовка, обычно препрег или многослойная с сотовым наполнителем, располагается в замкнутой полости между жесткой (матрица) и эластичной (оболочка, чехол) частями пресс-формы. Эластичный резиновый чехол, заполненный при формовании сжатым воздухом, паром или горячей водой, созда ющими давление, является пуансоном. Обогрев осуществляется либо в термошкафу, куда загружают всю установку, либо паром или горя
чей, водой, которые используют для создания давления |
прессова |
||||
ния (рис. 3 .4 ). |
|
|
|
|
|
Применяется при изготовлении изделий с плотной структурой |
|||||
и высокими физико-механическими характеристиками, а |
также для |
||||
изготовления многослойных |
изделий, включающих в себя |
сотовую или |
|||
пенопластовую прослойку и |
оболочки из армированных пластиков. Не |
||||
требует |
сложного |
автоклавного |
оборудования. |
|
|
3 .3 .1 .4 . |
Выкладка |
(контактное |
формование) |
|
Выкладка заключается в послойной укладке заготовок из во локнистого наполнителя в форму. Этим методом можно изготовлять изделия простой формы практически любых размеров. Однако выклад ка не получила широкого применения, так как очень сложно полу чить материал с постоянным содержанием матрицы и с высоким объемным содержанием волокон. Материал имеет низкие физико-меха нические показатели, так как невозможно дать высокое давление при формовании. Способ требует больших затрат ручного труда.
3.3.1.5. Формование методом намотки
Намотка представляет собой метод формования изделий из ком позиционных волокнистых материалов путем наматывания нити, жгу та, ленты или ткани на вращающуюся или неподвижную формообразую щую оправу с последующим отверждением изделия на оправке. Намотка может проводиться как предварительно пропитанным связующим (преи мущественно термореактивным) волокнистым материалом, так и непропитанным. Поэтому методы намотки делятся на так называемые "мок рые” и ”сухие”. Наибольшее распространение получил "мокрый" метод.
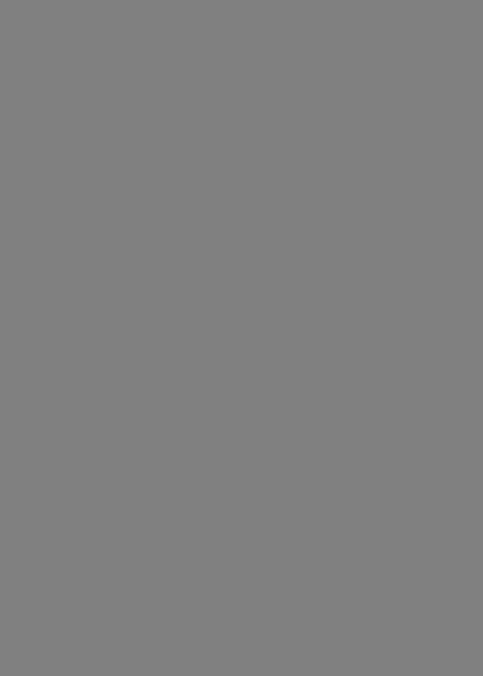
Методы намотки позволяют:
-выбрать оптимальную структуру материала в зависимости от требуемых свойств конечного изделия;
-максимально реализовать высокую прочность наполнителя и получить материал с хорошими характеристиками;
-автоматизировать процесс формования и получить изделия со стабильными свойствами.
Кнедостаткам метода можно отнести следующие:
1)зависимость скорости процесса от температуры и скорости отверждения, она обычно невалика для низкотеплостойких полиэфир ных смол;
2)трудность обеспечения постоянного сечения изделий по дли не, за исключением сравнительно простых форм - круглой, квадрат ной и некоторых других;
3)необходимость использования для получения изделий только жгутов и нитей.
В качестве полимерных матриц используются композиции на ос тове поливиниловых эфиров и эпоксидных смол. В настоящее время разрабатывается технология формования профильных изделий з приме нением полисульфона, полиэфирсульфона, пластифицированного поли амида.vАктуальными являются поиск и применение связующего со скры тым отвердителем, полимеризующимся при действии ультрафиолетового излучения за доли секунды.
Разработаны меюды получения изделий, сочетающие наг.члл/ спи рального или продольно-поперечного слоев и протяжку. В лаборатор ных условиях получена лопасти ветряных двигателей, имеющих слож ный профиль поперечного сечения из материала со сложной схемой ар мирования, полуфабрикаты для листовых автомобильных рессор, имею щих криволинейную поверхность и переменное поперечное сечение.
3 .3 .1 .6 . Прессование
Прессование зак лючается в пластической дефор тации материала при одновременном воздействии на него тепла и даыения и последую щей фиксации формы изделия. Проводится, как правию, в пресс-фор мах, конфигурация полости которых соответствует конфигурации из делия.
Рис.3.6. Схема получения прессматериала: / - катушка с волок нистым наполнителем; 2 - ванна пропиточная; J - шахта сушиль ная; 4 - валки тонущие; 5 - устройство для рубки; 6 - тара
приемная
6
Необходимое давление формования обеспечивается прессами, на которые устанавливаются пресс-формы. Помещенный в пресс-форму хо лодный или подогретый пресс-материал разогревается до рабочей температуры в подогреваемой пресс-форме (рис.3 .6).
3 .3 .1 .7 . |
Термокомпрессионное формование |
|
|
|||
|
Термокомпрессионный метод формования называют также формовани |
|||||
ем в |
эластичной оснастке, |
формованием с термическим |
расширением и |
|||
т .п ., |
но общепринятого названия он еще не имеет. Свое |
название |
ме |
|||
тод получил благодаря тому, |
что в качестве материала матрицы |
ис |
||||
пользуют |
силиконовый каучук |
и другие расширяющиеся при нагрева |
||||
нии эластомеры, вследствие |
|
температурной деформации которых созда |
||||
ется давление формования. |
Применяемые при этом методе |
формования |
силиконовые, кремнийорганические каучуки имеют коэффициент теплово го расширения (13-18)*1СГ5 К”1.
При этом методе пакет препрега вместе с эластичным элементом помещается в металлическую оформляющую полость. При повышении тем
пературы в соответствии |
с законом С^= tQ ( 1 + dl) t где d |
|
= |
|
= I/град, рабочее тело |
расширяется в |
большей степени, чем ограни |
||
чивающая его металлическая оснастка, |
что вызывает давление на |
от |
||
верждаемый материал. Благодаря этому |
отпадает необходимость |
в |
при |
ложении внешнего давления, как это делается при автоклавном формо вании. Применяется метод для формования изделий сложной формы, на-
пример At = 24*10“® К-1 ; сталь 12,2*10"® К"1.
3 .3 .1 .8. Центробежное формование
Сущность метода в том, что полимерная композиция, находящая |
||
ся в вязкожидком состоянии, подвергается действию |
центробежных |
|
сил, в результате чего заполняет форму и, отверждаясь, приобрета |
||
ет конфигурацию и размеры изделия. Центробежное формование |
поз |
|
воляет получать изделия, не содержащие пузырьков воздуха |
и не |
|
имеющие пор, без применения вакуумирования. В поле |
центробежных |
сил, в зависимости от вязкости системы, происходит перераспреде ление наполнителя и его миграция к поверхности формы, в резуль тате чего повышается твердость поверхности изделия. Наличие рав номерного поля центробежных сил позволяет в наиболее мягких усло
виях распределять волокна в системах детали, механически |
их |
не |
||||||
травмируя, что особенно важно для углеродных волокон. |
За |
|
счет |
|||||
регулируемой подачи волокна имеется возможность |
перераспределять |
|||||||
его как по толщине стенки, так |
и по длине изделия. |
Этим методом |
||||||
можно получать трубы, обечайки, |
шестерни и другие |
изделия |
форм |
|||||
вращения. |
|
|
|
|
|
|
|
|
3 .3 .1 .9 . Инжекционное формование |
|
|
|
|
|
|
|
|
При формовании инжекционным методом предварительно помещают |
||||||||
в форму армирующий материал и затем вводят связующее |
(рис. |
|
3.7) |
|||||
методом впрыска под давлением (иннекционнкй впрыск) |
|
либо |
созда |
|||||
нием в рабочей полости формы вакуума |
(инжекционный |
вакуумный). |
||||||
Наилучшие результаты дает сочетание |
этих методов. В качестве |
свя |
зующих используют композиции на основе ненасыщенных полиэфиров, но могут применяться и эпоксидные смолы, отверждающиеся при ком натной температуре.
Достоинства метода - сравнительно низкая стоимость прессформ, инжекционных устройств; возможность автоматизации процесса; экологическая чистота, обусловленная тем, что связующее на всех этапах процесса находится в закрытом от окружающей среды объеме; возможность получения крупногабаритных изделий, например мало мерных судов, кузовов легковых автомобилей и т .д .
Рис.3.7. Инжекционное формование: I - метод впрыска; Л - вакуум ный метод; / - формуемое изделие; 2 - нижняя форма; 3 - зажим; Li - смотровое окно; 5 - верхняя форма; 6 - патрубок впрыска свя
зующего; 7 - патрубок подачи связующего из резервуара
3.3Л . 10. Литье под давлением
Литьевое формование применяют при изготовлении деталей слож ной конфигурации. В этих технологиях используется исключительно рубленое волокно, как правило, предварительно пропитанное связую щим, так называемый пресс-материал (рис.3 .8 ). По прочности прессматериалы занимают промежуточное положение между изделиями из
Рис.3.8. Схема установки для литьевого формования: / - деталь; 2 - пресс-форма; 3 - нагреваемый кор
пус; k - литьевая композиция; 5 - шнек; 6 - прессматериал; 7 - бункер; 8 - привод
пресспорошков и слоистых материалов с ориентированным расположе нием волокон. Микронеоднородность структуры волокон вызывает не однородность прочностных характеристик изделий. Коэффициент вари ации по прочности достигает 20-30 %.
Для получения небольших по размеру, но сложных по форме де талей из композита, в которых невысокая степень армирования и произвольная ориентация волокон не препятствуют получению требу емых механических характеристик, часто применяют термопласты.
При получении изделий методом литья под давлением необходи мо учитывать, что выбор прессматериала зависит от назначения из делия; степень наполнения отражается на величине усадки и физико механических характеристик; сочетание рубленого волокна с диспер сными наполнителями приводит к ухудшению свойств композиционно го материала.
3 .3 .1 .I I . Пултрузия
Пултрузия - процесс, в котором волокна и пластичный материал матрицы одновременно истекают из фильеры, причем упрочняющие во локна при этом вытягиваются, а пластичный материал матрицы выдав ливается. В резулъгате получаются однонаправленные волокна в плас тической матрице. Этот процесс может быть непрерывным, а попереч ное сечение истекающего материала зависит от используемой фильеры (рис.З.Э).
Рис. 3.9. Основные элементы технологической линии для получения од нонаправленных профильных изделий: / - нитетракт; 2 - ванночка пропиточная; J - связующее; if - нагреваемая фильера; 5 - термока мера; 6 - протягивающее устройство; 7 - профильное изделие
Основные с'ГЭДИИ этого процесса:
- пропитка связующим пучка волокон;
•отжим избыточного связущего;
-придание материалу заданного сечения путем протягивания
его через фильеру; |
|
|
- отверждение; |
|
|
- разрезка на элементы заданной длины. |
1 |
|
Нагрев обычно индукционный. Фильер может быть несколько - |
||
предварительного формования я калибровочные. Поскольку |
при этом |
|
процессе исключается выдержка материала под давлением, |
то ис |
|
пользуют расплавы смол, не содержащие растворители |
(эпоксидные, |
полиэфирные).
Этот процесс прост, полностью автоматизирован и перспекти вен для промышленного производства профильных изделий из арми рованных пластиков.
3.3.1.12. Роллтрузия
Роллтрузия - метод, при котором пропитанное волокно протя гивают через систему прижимных и тянущих валков. При этом уплот нение волокна, отверждение связущего и придание материалу необ ходимой конфигурации осуществляются непрерывно в одну стадию.
Преимущества метода - малая стоимость оборудования, возможность получения крупногабаритных изделий, простота перестройки на дру гое изделие, высокая производительность (до I м/мин). При ролл трузия применяют связущее с низкой вязкостью (425-900 СП) и скоростью отверждения до 1-1,5 мин, это преимущественно эпоксид ные смолы, отверждаемые гетероциклическими аминами.
3.3.1.13. Формование с помощью вспененного слоя
Этот метод называется также формованием с отжимом связущ е го. Процесс проводят следующим образом (рис.ЗЛО):
1. С двух сторон пенопласта, пропитанного полимером, уклады вают армирующие материалы в виде ткани, мата и т .п .
2. Пакет помещают в пресс-форА^у и под давлением выжимают связущее из пенопласта, которое проникает в находящиеся с двух сторон от него слои армирующих материалов.
Рис.3.10. Формование с помощью
вспененного |
слоя: |
1 - |
слой |
пропитанного |
связующим |
вспе |
|
ненного материала; |
2 - |
форма; |
3 - трехслоиный пластик пос ле пропитки и отверждения;
Ц - армирующий материал; 5 - форма
3. Повышая температуру, отверждают пакет и получают изделие, содержащее в центре слой пенопласта.
При формовании с помощью вспененного слоя применяют сухой армирующий наполнитель в виде ленты, ткани, матов; смолы в жид ком состоянии, в качестве среды - преимущественно пористый ма териал.
Этот процесс характеризуется простотой технологии, позволя ет получать трехслойные легкие и жесткие конструкции. Применяет ся для формования изделий сравнительно простой формы.
3.4. Технологические материалы, используемые при формовании ПКМ
В зависимости от особенностей и назначения технологические материалы можно разделить на следующие группы:
1.Пленки для изготовления вакуумных мешков.
2.Герметизирующие материалы, из которых изготовляются жгу ты, ленты с двусторонним нанесением липкого слоя для создания контакта между пленкой вакуумного мешка и основанием приспособ ления для получения равномерного давления в зонах радиусных пе реходов.
3.Различные пористые материалы, служащие для создания рав номерного давления при вакуумировании мешка и обеспечения благо приятных условий работы пленок вакуумных мешков.
4.Разделительные пленки и смазочные материалы, обладающие противоадгезионными свойствами.
