
книги / Технология композиционных материалов
..pdfСовмещение армирующего Заполнителя |
со с в я з у ю щ и м . |
Совмещение |
|
производится следующими способами: |
|
|
|
- нанесением раствора или расплава |
связующего |
на |
поверхность |
армирующих волокон при прохождении их через жидкое |
связующее или |
с помощью вращающегося ролика, погруженного в связующее;
-напылением жидкого связующего из пульверизатора;
-пропиткой под вакуумом или давлением, когда связующее про сасывается или продавливается через армирующий наполнитель, пред варительно выложенный по конфигурации изделия и заключенный в герметичную полость;
-напылением на поверхность ленты или ткани из армирующих во локон порошка связующего и последующей пропиткой расплавом при прокатке между горячими роликами;
-дублированием лент и тканей с пленочными связующими и по следующей пропиткой расплавом при прокатке горячими роликами или непосредственно при формовании. Для улучшения проникновения свя зующего в межволоконное пространство применяют принудительную пропитку, например, с помощью отжимных роликов или ультразвука.
Если используемые связующие обладают достаточной жизнеспо собностью, то после операции совмещения с армирующим наполните лем полученный материал (препрег) подвергают тепловой обработке для удаления растворителей, летучих продуктов и придания препрегу липкости, необходимой для дальнейших технологических операций.
Сборка и ориентация слоев наполнителя по Форме детали. Спо соб сборки и ориентирования слоев армирующего наполнителя опреде ляется геометрией детали и текстильной формой армирующего напол нителя.
При использовании тканей, широких лент при изготовлении дета лей сложной формы применяют ручную выкладку слоев наполнителя.
Для ориентирования армирующего наполнителя в плоских деталях жли деталях одинарной кривизны или препрегов в виде лент использу ют специальные выкладочные станки-автоматы с программным управле
нием.
Для изготовления деталей, имеющих форму тел вращения, из ком позита на основе лент, ровингов, жгутов и тканей применяют намот ку, которая зависит от ориентации волокон: геодезическую, хордо
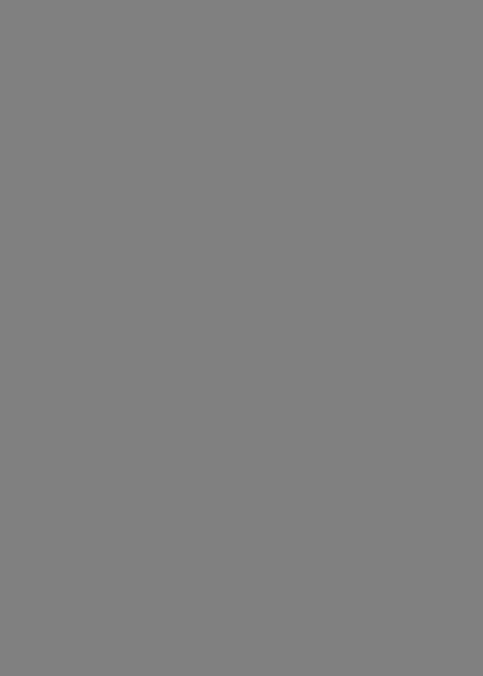
сокие сопротивления динамическим и знакопеременным нагрузкам» низкая стоимость изготовления.
К недостаткам клеевых соединений относятся малый диапазон эксплуатационных температур» незначительное сопротивление отсла иванию» длительное время отвержения клеевых швов» необходимость специальной подготовки поверхностей для склеивания» сложность соединения поверхностей сложной конфигурации, быстрое старение клея.
Для склеивания контактирующих поверхностей применяют клеи на основе полусинтетических или синтетических веществ, эпоксид ные клеи, флэксоны, фенольные клеи, полиуретановые, пластизольные и другие. Получило развитие производство высокопрочных пле ночных модифицированных клеев.
Для конструкций, работающих при температурах до 180-200 °С |
|
в условиях ударных нагрузок и высокой влажности, |
применяют кон |
струкционные высокотехнологичные клеи на основе |
эпоксидных |
олигомеров, модифицирование низкомолекулярными каучуками. Двух |
компонентные клеи могут отверждаться без нагревания и с нагрева нием. Особенность этих клеев - высокая скорость отверждения.
Флексоны представляют собой клеи на основе акриловых смол. Главной их особенностью является способность противостоять зна чительным кратковременным нагрузкам.
Однокомпонентные полиуретановые клеи 'отверждаются даже при отрицательных температурах. При их применении не требуется специ альной подготовки склеиваемых поверхностей. Интервал рабочих тем ператур 60-120 °С.
Клеи на основе полибензимидазолов, полиамидов обладают повы шенной теплостойкостью. Склеенные изделия пригодны к длительной эксплуатации при температуре до 250-320 °С, а при кратковременной эксплуатации - до 540 °С. Недостаток - высокая температура от верждения: 260-300 °С.
Преимущества циакрилатных и акриловых клеев перед другими кле ями - отверждение при комнатной температуре, высокая скорость от верждения, отсутствие операции перемешивания при изготовлении.
Методами, интенсифицирующими процесс склеивания, являются "сшивка" исходных молекул под действием теплоты; ультрафиолетовый, рентгеновский и гамма-излучений; метод воздействия потоками элект-
ронов и нейтронов. При тепловой "сшивке" для сокращения времени нагрева используют высокую частоту и ультразвук.
3.2. Производство препрегов
3.2.1. Препреги. Общее понггие
Может быть дано следующее определение препрега: препрег - это предварительно подготовленный, готовый к формованию матери ал в виде комбинации волокна и смолы в форме лент и листов. От загрязнения они с одной или с обеих сторон защищены легко уда ляемыми пленками. Для пропитки применяют эпоксидные, полиэфир ные, фенольные, кремнийорганические, полиамидные и термопластич ные (например, полисульфон) смолы. Композиции смол используют в виде жидкостей, горячих расплавов и разбавленных растворителем систем, а также в виде олигомерных смесей.
В качестве армирующих материалов применяют стекловолокно, борные, углеродные и высокомодульные арамидные волокна в виде тканей, лент или тесьмы.
3.2.2. Технологические характеристики препрегов
Примерно 80 % композшшонных материалов получают из препре гов. Предварительное формование изделий из препрегов позволяет:
-организовать массовое производство однонаправленных лент;
-получить заранее определенное соотношение между содержани ем смолы и волокон;
-заранее установить общий вес шпули;
-избежать смешивания смолы с отвердителем и катализатором;
-заранее подобрать липкость ленты и ее форму;
-увеличить время хранения при глубоком охлаждении (до -40°С) до многих месяцев и даже лет;_
-точно измерить вязкость смолы, что облегчит обработку,
уменьшит пористость слоев и обеспечит хорощую связь с сотовыми структурами;
- изменить режимы отверждения и получить различные механичес кие свойства композита;
- легко обработать некоторые неотвержденные препреги |
и в |
итоге уменьшить стоимость конечного продукта; |
|
уменьшить опасность токсичного воздействия при изготовле |
|
нии материала; |
|
- осуществить проверку характеристик смол и волокон |
еще до |
формования изделия. |
|
Препреги различаются по своим свойствам и не все обладают |
|
совокупностью перечисленных характеристик. |
|
Выбор наилучшей матрицы для препрега, предназначенного для |
|
изготовления конкретной детали, может быть сделан только |
после |
рассмотрения следующих вопросов: основные характеристики |
изделия, |
требования к механическим характеристикам, имеющееся производст
венное |
оборудование, стоимость. |
|
|
3.2.3. |
Выбор матрицы |
|
|
Все связующие (смолы), применяемые для изготовления препре- |
|||
гов, можно разделить на две группы: отверждаемые при |
170-180 °С |
||
и при 120-130 °С. Каждую из этих групп связующих можно |
еще под |
||
разделить на связующие с низкой и высокой текучестью. |
|
|
|
Смолы первой группы более теплостойки и устойчивы к дейст |
|||
вию внешней среды, а преимущество смол второй группы |
- |
низкие |
|
производственные издержки из-за относительно низких |
температур |
||
отверждения и лучшей адгезии к сотовым структурам. |
|
|
|
Типичным представителем матриц второй группы являются эпок |
сидные смолы, широко применяемые в производстве для углепласти ков. Эпоксидные смолы имеют хорошую адгезию к углеродным волок нам и незначительную усадку при отверждении, дают композиту вы сокие механические показатели.
Связующие первой группы используют в тех случаях, когда ком позиту требуется придать какие-либо определенные, служебные свой ства, например термостойкость, что достигается применением поли амидных и силиконовых связующих, позволяющих получать углепласти ки с рабочей температурой 350 °С.
3.2.4. Изготовление препрегов
Препреговая технология, или сухой метод формования, предус матривает пропитку волокон полимерной матрицей, отверждение ее
до состояния, при котором она достаточно стабильна, хранение во локон вместе с матрицей в течение определенного времени.
В препреговой технологии используется разделительная пленка, которая размещается между слоями препрега и должна перемещаться без разрушения волокон, приклеиваться к препрегу, но не к кром кам катушки, используемой при хранении. Поперечная прочность од нонаправленного препрега должна быть достаточной для того, чтобы с ним можно было работать на машине или вручную.
Рис.3.1. Схема технологического процесса получения препрега:
1 - катушка с волокнистым на
полнителем (лентой); |
2 |
- |
ван |
||
ночка со связующим; j |
- |
отжим |
|||
ные, ролики; 4 |
- |
шахта для |
суш |
||
ки: 5 - катушка |
с разделитель |
||||
ной пленкой; |
6 - катушка |
для |
|||
намотки препрега |
с регулируемой |
||||
скоростью |
|
|
|
S
Препреги изготовляют на пропиточных машинах, получая полу фабрикаты с требуемыми характеристиками (рис.3.1).
3.2.5. Контроль качества препрегов
При определении качества препрегов контролируют следующие параметры: содержание смолы в процентах, содержание летучих в процентах, липкость, текучесть, продолжительность желатинизации.
Содержание смолы или составляющих мономеров определяется экстракцией растворителя, пиролизом или методом химической иден тификации.
Содержание летучих определяется неполным пиролизом в стан дартных условиях испытания.
Липкости, т .е . вел:.ч/ну, характеризующую качество адгезии, определяют экспресс-методом по усилию отдира металлической плас тины от поверхности препрега. Уровень липкости определяется пока зателем, при котором препрег остается приклеенным к подложке вплоть до приложения заранее определенного усилия отслаивания (в кг/сы2 я в МПа).
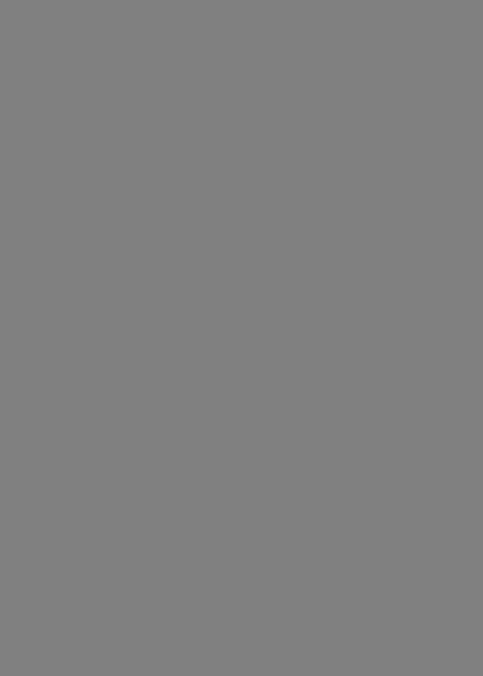
2) вакуумное формование, компоненты - препреги, реже сухое волокно и жидкая смола;
3)пресс-камерное формование, компоненты - препреги, много слойные конструкции, например с сотовым заполнителем;
4)выкладка (контактное формование), компоненты - ленты, ткани, маты и жидкая смола, препреги;
5)намотка мокрая; компоненты - сухое волокно и жидкая смо
ла; сухая - препреги;
6)прессование, компоненты - препреги;
7)термокомпрессионное прессование, компоненты - препреги;
8)центробежное формование, компоненты - сухое волокно, дис кретный наполнитель и смола в жидком состоянии;
9)инжекционное формование - сухой наполнитель, жидкая смола; 10) литье под давлением (литьевое формование); компоненты -
рубленое волокно, смола в гранулах; пресс-материал;
11)пултрузия, компоненты - сухое волокно и смола в жидком виде; препреги;
12)роллтрузия, компоненты - сухое волокно и жидкая смола;
препреги.
Технологические методы формования эластичными диафрагмами или вакуумными мешками включают автоклавное (гидроклавное), ва куумное и пресс-камерное формование изделий из ПКМ.
Втехнологический процесс формования изделий из ПКМ эластич ными диафрагмами входят следующие типовые технологические операции:
1. Подготовка поверхности формы путем нанесения противоадггзионного смазочного материала для предотвращения склеивания изде
лия с формой.
2.Укладка слоев заготовок из сухой ткани, пропитанной смолой. Число слоев должно обеспечивать нужную толщину изделия.
3.Укладка разделительной ткани для обеспечения отделения ва куумного мешка от фольги.
4.Укладка впитывающих, дренажных слоев.
5.Укладка эластичной оболочки и герметизирующего жгута, уста новка термопар, а также проверка мешка на герметичность.
6.Формование (отверадение основы) при заданных температуре, давлении и выдержке.
7« Управление процессом отверждения с заданными на ленте режи мами тормостатирования.
8. Демонтаж вакуумного мешка, снятие изделия с формы и пе редача на последующие технологические операции - обрезку, конт роль, испытания, зачистку, грунтовку, окраску и оформление тех нологического паспорта.
3 . 3 .I .I . Автоклавное (гидроклавное) формование изделий
При автоклавном (гидроклавном) формовании изделий давление прессования создается паром, горячей водой, глицерином или сжа тым воздухом, нагнетаемым в автоклав. Обогрев осуществляется па ром, горячей водой, жидкостью или обогревателями, расположенными в форме. Заготовка формуется при всестороннем равномерном давле нии. Параметры процесса - давление формования (0,5-7 МПа) и тем
пературный режим - определяются типом ПКМ.
5
Рис.3.2. Формование |
в |
автоклаве: |
1 - автоклав; 2 - |
жгут |
||||
для герметизации; |
3 |
- |
форма; |
4 |
- |
изделие |
формуемое; |
5 - |
мешок резиновый; |
6 |
- зажим; |
7 |
- |
кольцо |
прижимное; |
8 - |
тележка
При автоклавном формовании с помощью эластичного мешка созда ется избыточное внешнее давление в сочетании с внутренним разряже нием, что позволяет проводить процесс отверждения при повышенных температурах. Это способствует дополнительному улучшению пропитки эа счет снижения вязкости связующего. Современное автоклавное обо рудование позволяет регулировать закон изменения температуры и давления (рис.3 .2 ).
Преимущества автоклавного формования:
-возможность получения изделий равномерной толщины;
-возможность формования крупногабаритных изделий;
-высокое качество поверхности изделий.
3 .3 .1 .2 . Вакуумное формование
Сущность вакуумного формования заключается в использовании внешнего атмосферного давления величиной до I атм для получения из препрега монолитного материала. Достигается это использовани ем вакуумного насоса, который отсасывает воздух, содержащийся в объеме между формующей поверхностью, препрегом и непроницаемой пластиковой пленкой (вакуумным мешком), прилегающим к форме. Для отверждения в этом случае обычно используют печь, хотя мож но использовать и нагреваемую форму. Этот метод особенно эффективён из-за отсутствия дорогостоящих автоклавов и прессов (рис.
3.3).
Недостаток - пониженные свойства получаемого материала из-за недостаточного давления формования.
J
2
1
Рис.3.3. Формование в вакуум |
Рис.3.4. Формование в пресс-ка |
|||||||||
ном мешке: / - форма; |
2 |
- |
мере: / - |
форма; |
2 - |
изделие |
||||
кольцо прижимное; 3 - зажий; |
формуемое; |
з |
- |
жгут для |
гер |
|||||
4 - издеолие форму»емое; |
5 - |
метизации; |
4 |
- |
зажим; |
5 |
- |
|||
мешок |
вакуумный; о - |
жгут |
кольцо |
прижимное |
|
|
||||
для |
герметизации |
|
|
|
|
|
|
|
|
|