
книги / Ремонт подъемных кранов
..pdf3.5.6 Технологический процесс металлизации
При всех способах ремонта деталей металлизацией техно логический процесс состоит из подготовки детали к металли зации, нанесения покрытия и обработки детали после метал лизации.
Подготовка детали к металлизации включает операции очистки, обезжиривания и механической обработки детали для придания напыляемой поверхности правильной геомет рической формы и создания на поверхности детали шерохо ватой поверхности с целью улучшения сцепления покрытия с основным металлом. Наиболее распространено образование шероховатой поверхности путём дробеструйной обработки детали чугунной дробью при давлении воздуха 0,4-0,6 МПа в течение 3-5 мин. Детали с твёрдостью свыше 350 НВ под вергают электроискровой или анодно-механической обработ ке, получая необходимую шероховатость.
Нанесение металла. При металлизации тел вращения деталь закрепляют в центрах токарного станка, а металлизатор устанавливают на суппорте. При металлизации плос ких поверхностей напыление осуществляют при помощи металлизатора вручную. Качество покрытия зависит от ряда факторов: давления воздуха в процессе напыления, расстоя ния от сопла пистолета до детали, скорости подачи проволо ки и скорости движения детали относительно потока распы ляемого металла, принятого режима металлизации, обеспе чивающего минимальную окисляемость напыляемых частиц. При дуговой металлизации применяют проволоку диамет ром 1-1,5 мМ; силу тОка 90-150 А; Скорость подачи прово локи 0,6-1,5 м/мин. При меньшей скорости дуга горит с перебоями й покрытие получ&ется неравномерным. Превы шение скорости не обеспечивает полного расплавления про волоки. Скорость металлизации принимают 5-15 м/мин., про дольную подачу металлизатора 1,5-5 мм/об.
Механическая обработка напыленных покрытий имеет ряд особенностей, связанных с их повышенной хрупкостью
и твёрдостью. В зависимости от припуска на обработку, твёр дости и требований качества поверхности напыленного слоя выполняют токарную обработку или шлифование. При точе нии напылённых покрытий применяют резцы из сплава Т15К6 с пониженными режимами резания: глубина резания 0,1-0,3 мм, подача 0,1-0,15 мм/об. Шлифование износос тойких покрытий, имеющих высокую твёрдость, следует выполнять алмазными кругами на вулканитовой основе.
3.5.7 Эксплуатационные свойства металлизационных покрытий
Прочность сцепления покрытия с основным металлом не достаточна. Так, например, прочность сцепления при элект рометаллизации составляет 10-25 МПа, при газовой метал лизации — 12-28 МПа, при плазменной — до 40 МПа. Проч ность сцепления возрастает с ростом силы тока, расхода газа, от применения предварительного подогрева детали до темпе ратуры 200-300 °С, подслоев из легкоплавких сплавов или молибдена, а также оплавления поверхности после её напы ления.
Износостойкость металлизационных покрытий достаточно высокая, что предопределяется значительной их пористос тью (до 10-20 % объёма), которая способствует удержива нию в напылённом слое смазочного масла. При плазменном напылении порошковой проволокой получают покрытие с пористостью в пределах 2-5 % .
Значительное повышение износостойкости можно получить при плазменной наплавке путём применения тугоплавких ма териалов.
Усталостная прочность деталей весьма низкая, что объяс няется слабой прочностью сцепления металлизационного покрытия с металлом детали и необходимостью создания весь ма шероховатой поверхности при подготовке детали к метал лизации. Поэтому металлизированные детали, особенно по лученные способами дуговой и газопламенной металлизации,
не рекомендуется использовать в условиях работы со знако переменными и повторными нагрузками.
3.5.8 Определение технологических параметров процесса металлизации
При разработке технологического процесса восстановле ния детали металлизацией определяют толщину покрытия, частоту вращения детали, величину тока, время на металли зацию. Эти параметры могут быть рассчитаны или подобра ны по литературным источникам.
Толщина покрытия цилиндрических поверхностей
D - d |
„• |
- |
h = — — |
+ 8 +6 |
(3.34) |
где D — номинальный размер детали, мм; d — наружный диаметр подготовленной поверхности, мм; 5' — припуск на механическую обработку; 8 "— дополнительная толщина по крытия, перекрывающая углубления, которые возникают при подготовке поверхности детали («рваная» резьба и др.); 8 ” = 1/2 глубины «рваной» резьбы.
Толщина слоя, наносимого за один проход металлизатора,
мм
• 10^ QK,
(3.35)
6 VJSy’
где Q — производительность металлизатора, г/ч; Км — коэф фициент использования металла; VH — окружная скорость детали, см/мин.; S — подача металлизатора, см/об.; у — плот ность напыленного металла, г/см3.
Величина силы тока
1 = |
(3.36) |
где dn — диаметр проволоки, мм; Vn — скорость подачи про волоки, см/мин. (принимают из паспорта металлизатора);
h.C — опытные коэффициенты, для стали: h = 3,5; С = 0,1; для латуни h = 1,5; С = 0,48.
Время на металлизацию, ч
0,006nDlhy
(3.37)
QKM
где D — номинальный диаметр детали, мм; I — длина вос станавливаемой поверхности, см.
3.6 Электролитические и химические покрытия
При ремонте строительных и дорожных машин процесс электролитического осаждения применяют для восстановле ния деталей, имеющих сравнительно малые износы, для за щиты деталей от коррозии, а также для декоративного по крытия. В ремонтном производстве наиболее распростране ны хромирование и осталивание, в меньшей степени медне ние, никелирование, цинкование. При гальванических про цессах не изменяются структура и свойства основного мате риала детали, так как нагрев детали не превышает 70-90 °С. Твёрдость может быть получена от 50-70 НВ — для цинко вых, до 1200 НВ для хромовых покрытий.
Электролитическое (гальвани |
|
|
ческое) покрытие — это процесс |
|
|
нанесения металла на поверхность |
|
|
детали путём кристаллизации его |
|
|
из раствора соответствующей соли |
|
|
(электролита) в результате про |
|
|
хождения через соль электричес |
|
|
кого тока. На рисунок 3.30 пока |
|
|
зана простейшая схема электро |
|
|
литического осаждения металла. |
|
|
Ванну 1 заполняют электроли |
Рис. 3.30 Схема |
|
том 4. При пропускании через |
||
электролитического |
||
него постоянного тока молекулы |
||
осаждения металла |
||
раствора расщепляются на поло |
||
|
жительно заряженные частицы — катионы, которые пере мещаются к отрицательному электроду 3 (катоду), где осаж даются, превращаясь в нейтральные атомы, и отрицательно заряженные частицы — анионы, перемещающиеся к поло жительному электроду 2 (аноду), где также теряют свой за ряд и превращаются в нейтральные атомы. При многих про цессах катодом служит обрабатываемая деталь, анодом — либо металл, соль которого находится в растворе, либо ме талл, который нерастворим в электролите.
Качество покрытий зависит от рассеивающей способности электролита. Под этим понимают свойство электролита обес печивать равномерные по толщине покрытия на катодах слож ной формы, элементарные поверхности которых размещены па разных расстояниях от анода. Рассеивающая способность электролита Р (в %) определяется по формуле
Р = ^ 1 Г ^ '100, |
(3,38) |
где К — отношение расстояний катодов от анодов; Кх — ко эффициент распределения масс металла, т.е. отношение мас сы металла, отложившегося на ближнем катоде, к массе ме талла, отложившегося на дальнем катоде.
При гальванических покрытиях деталей, имеющих вы ступы или острые кромки, невозможно получить равно мерные по толщине покрытия вследствие неодинаковой плотности тока: на выступающих частях плотность тока будет выше, чем в углублениях, т.е. рассеивающая способ ность электролита на различных участках детали будет раз личной. Для снижения рассеивающей способности элект ролита используют ряд приёмов. В частности, сФрёмятся расположить катоды на одинаковых расстояниях от анода (рис. 3.31, а) или применяют дополнительные (защитные) катоды, называемые экранами, которые принимают на себя часть тока и тем самым устраняют образование на высту пающей части детали повышенной толщины слоя покры тия (рис. 3.31, б).
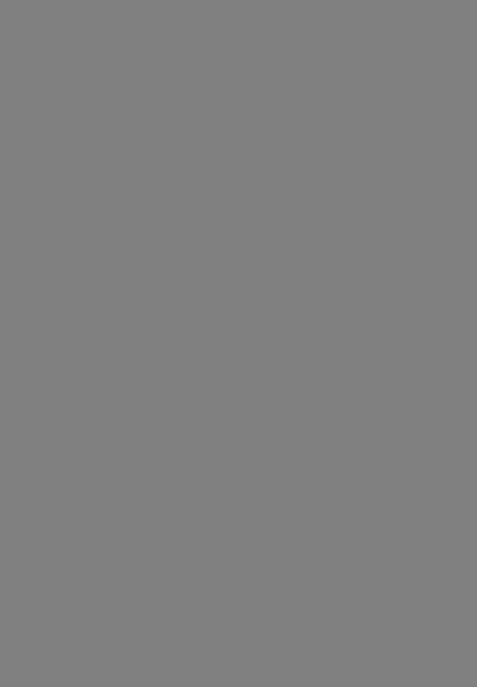
4)изоляция мест, не подлежащих хромированию, покры тием этих мест цапон-лаком в смеси с нитроэмалью в соотношении 1:2, либо нанесением плёнки из перхлорвинилового пластика толщиной 0,3-0,5 мм, либо при менением клея БФ и др.;
5)окончательное обезжиривание детали (эта операция дол жна выполняться весьма тщательно, так как тончайшая жировая плёнка изолирует поверхность детали от элект ролита. Наилучшие результаты обеспечивает электрохи мическое обезжиривание с подвеской детали на катоде. В качестве электролита используют щелочной раствор следующего состава (в г/л): едкий натр — 10, кальцини рованная сода — 2,5, тринатрийфосфат — 2,5, эмульга тор ОП-7 — 2-5. Обезжиривание протекает при темпера
туре раствора 70-80 °С, плотности тока 5-10 А/дм2, дли тельности процесса 1-2 мин.);
6)анодная обработка (декапирование), выполняемая с це лью удаления с поверхности детали тончайших плёнок окислов (эта операция осуществляется путём погруже ния детали вместе с подвеской в ванну для хромирова ния, но при включении обратного тока, т.е. анодом слу жит деталь. Процесс сводится к электролитическому растворению металла и одновременно к механическому отрыву окислов выделяющимся кислородом. После за вешивания детали в ванну её предварительно прогрева ют без тока 1-2 мин., а затем ведут анодную обработку
втечение 30-45 с при плотности тока 30-35 А/дм2). После анодной обработки деталь, не вынимая из ванны,
переключают на катод и наносят покрытие.
Хромирование. При хромировании в качестве электроли та используют водный раствор хромового ангидрида (Сг03). Процесс хромирования удовлетворительно протекает в при сутствии ионов S04 с применением нерастворимых (свинцо во-сурьмянистых) анодов (95 % свинца и 5 % сурьмы). Сер ная кислота в электролите играет роль катализатора, способ ствуя осаждению хрома. Соотношение между концентраци
ей хромового ангидрида и серной кислотой (Cr03/H 2S04) дол жно находиться в пределах от 90 до 120. В этом случае обес печивается наибольший выход по току хрома.
В зависимости от назначения покрытия применяют элект ролиты различных составов, приведённые в таблице 3.18.
Таблица 3.18 Состав электролитов для хромирования
Наименование показате- |
№ 1 |
Электролиты |
|
|
|
|||
лей и компонентов |
№ 2 |
№3 |
|
|||||
Хромовый ангидрид, г/л |
120 |
— |
150 |
200 |
— 250 |
300 |
— |
350 |
Серная кислота, г/л |
1,2 |
— |
1,5 |
2,0 |
— 2,5 |
|
3,5 |
|
Плотность тока, А/дм2 |
40— 100 |
20-60 |
10 — |
30 |
||||
Температура, °С |
50 — 65 |
45 — 55 |
40 |
— |
50 |
Электролит № 1, называемый разведенным, обеспечивает наиболее высокую износостойкость покрытия, отличается относительно высоким выходом хрома по току (16-18 % ) и лучшей рассеивающей способностью. Электролит N° 3, назы ваемый концентрированным, используют для защитно-деко ративных целей. При хромировании на этом электролите выход по току относительно мал (10-12 %). Этот электролит отличается низкой рассеивающей способностью. Электролит N° 2, называемый универсальным, по своим показателям за нимает промежуточное положение и применяется для полу чения износостойких покрытий с хорошими защитно-деко ративными свойствами.
В зависимости от плотности тока и температуры электро лита при неизменном его составе можно получить покрытия трёх видов: серые (матовые), блестящие и молочные. На ри сунке 3.32 показана схема расположения зон хромовых осад ков для ванны с содержанием хромового ангидрида Сг03 250 г/дм3. Серые осадки отличаются высокой твёрдостью, по вышенной хрупкостью и пониженной износостойкостью. Се рые осадки при восстановлении деталей не применяют. Бле стящие осадки обладают большой твёрдостью, но меньшей
|
хрупкостью. Эти осадки отлича |
|
|
ются хорошей износостойкостью |
|
|
при умеренных нагрузках. Мо |
|
|
лочные осадки отличаются дос |
|
|
таточной пластичностью, но ме |
|
|
нее тверды. Такие осадки нано |
|
|
сят на детали, работающие при |
|
|
знакопеременных и ударных на |
|
|
грузках. |
|
35404550556065 70 7580 |
В процессе электролита на ка |
|
Т ем перат ура, С |
тоде одновременно с металлом |
|
Рис. 3.32 Схема |
||
осаждается водород, который мо |
||
расположения зон |
жет образовывать либо химичес |
|
хромовых осадков |
||
кие соединения с металлом по |
||
|
крытия, либо механически проникать в катодный осадок с образованием пустот, значительным искажением кристалли ческой решётки, что в свою очередь приводит к повышению внутренних напряжений в осадке (водородная хрупкость). Внутренние напряжения имеют отрицательные значения (ра стягивающие напряжения). Если эти напряжения превыша ют предел прочности покрытия на растяжение, то в хромо вом покрытии возникают трещины. Для ориентировочного подсчета времени хромирования можно принять, что при ис пользовании электролита № 2 скорость осаждения хрома со ставляет в среднем 20 мкм/ч.
Заключительные операции после хромирования следую щие. Промывка детали вместе с подвеской в ванне с дистил лированной водой с целью сбора дорогостоящего хромового ангидрида. Промывка в холодной проточной воде и затем погружение на 0,5-1 мин. в ванну с 3-5%-ным раствором кальцинированной соды для нейтрализации остатков элект ролита и в заключение — промывка в тёплой проточной воде. Демонтаж деталей с приспособления, удаление изоляции и сушка в сушильном шкафу при температуре 120-130 °С. С целью снятия в хромированном слое внутренних напряже ний, возникающих в результате растворения в хромовом по
крытии водорода, в отдельных случаях проводят тепловую обработку деталей путём их нагрева в масляной ванне до тем пературы 150-120 °С с выдержкой в течение 1,5-2 ч. Завер шающей операцией является шлифование хромированных поверхностей электрокорундовыми кругами с зернистостью 60-120 и твёрдостью M l-М 3. Припуск на шлифование ос тавляют 0,08-0,1 мм. Хромовые покрытия, нанесённые с де коративной целью, подвергаются полированию с применени ем паст ГОИ.
Ванны для хромирования. Хромирование осуществляют в ваннах, имеющих мощный бортовой отсос, так как при хро мировании выделяются вредные пары. Внутреннюю сторону ванны облицовывают кислотоупорным материалом (винип ластом, эпоксидной смолой и др.). В ванну встраивают подо греватель. Для поддержания определённой температуры элек тролита используют терморегулятор. Наружный кожух ван ны изготовляют с теплоизоляцией. Источником тока служат низковольтные (6-12 В) генераторы, рассчитанные на ток от 250 до 1500 А, либо выпрямители.
Пористое хромирование. Рассмотренный выше процесс хромирования обеспечивает получение так называемого глад кого хрома, который характеризуется слабой смачивающей способностью по отношению к маслу и плохой прирабатываемостью. С целью устранения этих недостатков применяют пористое хромирование, т.е. образование на поверхности по крытия пор. Наиболее просто получить пористость электро литическим способом путём анодного травления покрытия в электролите. Анодное травление деталей проводят в той же хромовой ванне, в которой их хромировали, путём переклю чения полярности тока (деталь становится анодом). Продол жительность травления 5-10 мин. В это время происходят растворение хрома, протекающее более активно по границам первичных микротрещин, и образование пор канальчатого или точечного типа. На рисунке 3.33 показана схема форми рования канальчатого (а) и точечного (б) пористого хрома. Канальчатый хром получают при анодном травлении модоч-