
книги / Ремонт подъемных кранов
..pdf"V"' |
* |
ТТ'Т-Т 111 |
но-блестящих хромовых покры |
Щ Р1щ |
\^\\N\\N>NNN\N\NNN |
тий, а точечный — при анодном |
|
Ш111111 |
травлении серо-блестящих по |
||
|
|
|
крытий. Покрытия с канальча- |
т |
* |
|
тыми порами целесообразно при |
|
менять для деталей, работающих |
||
■ ■ |
1 |
б) |
с ограниченной смазкой, а покры |
тия с точечной поверхностью — |
|||
а) |
|
для деталей, к которым предъяв |
|
Рис. 3.33 Схема |
ляются требования хорошей при- |
||
формирования |
рабатываемости. |
||
канальчатого (а) и |
Пористым хромированием по |
||
точечного (б) пористого |
вышают износостойкость порш |
||
|
хрома |
невых колец, поверхность цилин |
дров двигателей и других деталей, работающих в условиях трения скольжения.
Хромирование в саморегулирующем электролите. Суще ственным недостатком сернокислых хромовых электролитов является постепенное обеднение их хромом, который осаж дается на деталях. Это приводит к нарушению соотношения между хромовым ангидридом и серной кислотой. Последнее обстоятельство нарушает нормальную работу ванны и сни жает производительность процесса из-за малых значений выхода по току. Чтобы поддержать нормальное протекание процесса, необходима частая корректировка состава элект ролита.
Для устранения этих недостатков применяют хромирова ние в саморегулирующихся электролитах. Электролиты име ют в своем составе хромовый ангидрид (250-300 г/л), а так же соли сульфатастронция SrS04 (5-6 г/л) и кремнефторис того калия K2SiF6 (18-20 г/л). При определённой температу ре электролит способен растворить такое количество сульфа та стронция и кремнефтористого калия, которое соответствует нормальному протеканию процесса хромирования. В состав электролита эти вещества вводят в избыточном количестве, поэтому часть их будет находиться на дне ванны в виде твёр
дой фазы. В процессе хромирования количество хромового ангидрида будет падать, однако при этом будет автоматичес ки уменьшаться и содержание в растворе SrS04 и K2SiFe.
При снижении содержания Сг03 ниже допустимого (200 г/л) в электролит следует ввести дополнительное коли чество хромового ангидрида, которое вызовет автоматичес кое регулирование состава электролита за счёт растворения SrS04 и K2SiFe, находящихся на дне ванны.
При использовании саморегулирующегося электролита при меняют плотность тока 50-100 А/дм2, температуру электроли та 50-70 °С, напряжение тока 12 В. Преимущества примене ния такого электролита: автоматическая корректировка его со става; повышенная скорость осаждения хрома (40-90 мкм/ч) в связи с более высоким выходом по току (18-20 %); относитель но высокая рассеивающая способность электролита (17-20 %); высокая твёрдость покрытия (9,5-10 ГПа). Основной недоста ток — повышенная агрессивность электролита.
Хромирование в тетрохроматном электролите. Состав этого электролита следующий (в г/л): хромовый ангидрид — 350-400, серная кислота — 22,5, едкий натр — 40-60, са хар — 13. При использовании электролита применяют повы шенную плотность тока (60-80 А/дм2) и низкую температу ру электролита (16-24 °С). Тетрахроматный электролит име ет высокий выход по току (28-30 %) и высокую рассеиваю щую способность. Покрытия отличаются хорошей прирабатываемостью. Электролит целесообразно применять при вос становлении деталей, имеющих невысокую поверхностную твёрдость (3,5-4 ГПа), а также в качестве защитно-декора тивного покрытия.
3.6.1 Осталивание
Процесс электролитического осаждения железа. Оста ливание намного производительнее и экономичнее хроми рования, так как скорость осаждения металла составляет 0,3-0,5 мм/ч, а выход по току достигает 85-90 % , т.е. в
5 -6 раз выше, чем при обычном хромировании. Сцепляемость железного покрытия с поверхностью стальной дета ли достаточно высокая (400-450 МПа). К недостаткам про цесса относится снижение усталостной прочности деталей, достигающее 30 % при покрытии стальных деталей. Это обусловлено наличием растягивающих внутренних напря жений в покрытии.
Осталивание применяют для наращивания поверхностей деталей под неподвижные посадки, для восстановления де талей с большим износом (до 23 мм), а также с целью полу чения подслоя в 13 мм для тонкого хромового покрытия (0,02-0,03 мм).
Процесс осталивания обычно протекает в хлористых элек тролитах, основным компонентом которых является хлорис тое железо FeCl2 •4HzO. Концентрация хлористого железа в электролитах может быть в пределах от 200 до 700 г/л. Наи более стабилен в работе электролит средней концентрации, содержащий (400 ± 20) г/л FeCl2 •4Н20, (2 ± 0,2) г/л НС1 и (10 ± 2) г/л МпС12 •4Н20. Наличие соляной кислоты необхо димо для устойчивой работы ванны; хлористый марганец способствует повышению сцепляемости покрытия с основ ным металлом.
При осталивании деталь является катодом. В качестве анода используют низкоуглеродистую сталь марки 08 или 10. В процессе электролиза анод постепенно растворяется. Кон центрация соляной кислоты при работе ванны снижает ся, поэтому необходимо периодически контролировать со став электролита с добавлением концентрированной соля ной кислоты.
Качество покрытия (твёрдость, износостойкость, вязкость) зависит от состава и температуры электролита, плотности тока. Мелкозернистые и вязкие покрытия получаются при малой плотности тока и высокой температуре; с увеличени ем плотности тока, снижении температуры электролита и уменьшении концентрации хлористого железа твёрдость по крытия возрастает.
Технологический процесс осталивания мало чем отлича ется от хромирования. При подготовке детали к осталиванию не всегда требуется предварительное её шлифование: при наращивании значительного слоя деталь обычно не шлифу ют. Другие подготовительные операции (обезжиривание, изо ляция мест, не подлежащих осталиванию, вторичное обез жиривание, анодная обработка) принципиально те же, что и при хромировании.
В процессе осталивания выделяется большое количество вредных газов, поэтому требуются мощные вентиляционные установки.
3.6.2 Электролитические покрытия на токе переменной полярности
С целью интенсификации процессов нанесения электро литических покрытий и повышения их качества применяют установки с использованием тока переменной полярности, т.е. с использованием переменного тока. Сущность процесса заключается в том, что в межэлектродное пространство ван ны в течение одного периода подаются два импульса тока — катодного и анодного, причём длительность катодного пери ода составляет 15 мин., а анодного — 15 с. Смена полярнос ти обеспечивается автоматами типа APT и др.
Покрытия, выполненные на токе переменной полярнос ти, отличаются меньшими внутренними напряжениями в связи с тем, что в период катодной обработки образующий ся тонкий слой не достигает предельных значений, прН ко торых появляются микротрещины. Кроме того, в период анодной обработки происходит частичное растворение ме талла покрытия, которое протекает интенсивнее с выступа ющих частей, и тем самым повышается равномерность по крытия по толщине.
Применение тока переменной полярности приводит к сни жению поляризации электродов, что позволяет повысить цлотность тока и, следовательно, производительность процесса.
3.6.3 Вневанное электролитическое осаждение металла
Восстановление хромированием или осталиванием круп ногабаритных деталей (корпуса коробок передач, блоки ци линдров) и деталей сложной конфигурации (коленчатые валы) связано с рядом технологических трудностей (необходимость иметь ванны больших размеров, сложность подвесных при способлений и изоляции мест, не подлежащих покрытию, и др.). Поэтому такие детали восстанавливают вневанным осаж дением, принцип которого заключается в том, что местная ванна создаётся только в зоне покрытия. Вневанный процесс выполняется тремя способами: струйным, проточным и на тиранием.
|
Схема струйного процесса пока |
|
зана на рисунке 3.34 на примере |
|
осаждения хрома на шейке колен- |
^ |
чатого вала. Электролит подаётся |
0 |
насосом на шейку вала через под |
|
водящую трубу 1 и отверстия спе |
|
циальной насадки 2, которая явля |
|
ется анодом. Катодом служит де |
|
таль 3. В нижней части шейки раз |
|
мещена ванночка 4, в которую сте |
Рис. 3.34 Схема струйного |
кает непрерывно поступающий |
электролит. |
|
процесса |
Из ванночки электролит стека |
|
ет в общую ванну 5, где он подогревается до необходимой температуры подогревателем 6 и подаётся насосом к детали. Для обеспечения равномерного покрытия деталь вращается с частотой 26 об/мин.
Проточный процесс заключается в том, что в зоне покры ваемой поверхности создаётся местная ванна, через которую циркулирует электролит. Этот способ особенно эффективен при покрытиях металлом внутренних цилиндрических по верхностей. На рисунке 3.35 показана принципиальная схе
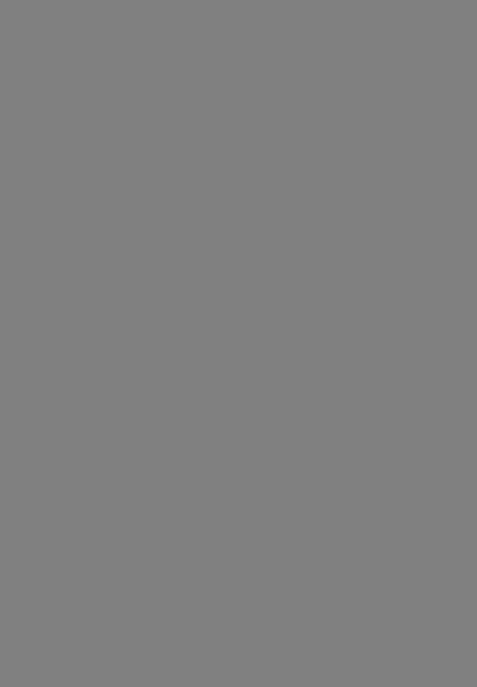
подшипники в корпусных деталях, на валах, в бронзовых втулках при износах до 0,1 мм. Используют железные, цин ковые и медные покрытия.
3.6.4 Автоматизация электролитических процессов восстановления деталей
Для обеспечения высокого качества покрытий необходи мо в процессе электролиза строго придерживаться опреде ленной температуры электролита, плотности тока и кислот ности электролита. Для этого современные электролитичес кие ванны оснащаются устройствами, автоматически регу лирующими процесс. Для поддержания температурного ре жима применяют различного вида терморегуляторы. Авто матическое регулирование плотности тока осуществляют при борами типа АПТ-10, АПТ-200. Универсальные автоматы АК-2 и АК-3 обеспечивают комплексное регулирование тем пературы электролита и плотности тока. Имеются установ ки, оснащенные системой комплексной автоматизации галь ванических процессов.
3.6.5 Химическое осаждение металлов
Этот процесс заключается и том, что при определённых условиях металл осаждается из раствора на поверхности де тали самопроизвольно без воздействия электрического тока. В практике ремонтных предприятий находит применение хи мическое никелирование стальных поверхностей и деталей, при котором никель восстанавливают из растворов сернокис лого или хлористого никеля с помощью соли-восстановителя (гипофосфит натрия, калия или кальция). Осаждение нике ля, возможное на сталь, цинк, алюминий, никель, серебро, протекает при температуре раствора 92-94 °С. Скорость от ложения осадка невысокая и составляет 10-20 мкм/ч, по этому процесс целесообразно применять для деталей, имею щих износы не более 0,05-0,1 мм. В процессе осаждения
никеля одновременно из раствора восстанавливается и осаж дается фосфор в количестве 5-10 % от массы осадка никеля. Фосфор повышает твёрдость осадка до 4,2-5,3 ГПа.
Подготовка поверхности и обработка наращенного слоя включает те же операции, что и при гальванических покры тиях. Термообработка покрытия (нагрев до температуры 400 °С с выдержкой в течение 1 ч) способствует повышению твёрдости осадка до 7,58 ГПа в связи с образованием соеди нения Ni3P и увеличению прочности сцепления осадка с ме таллом детали до 320 МПа.
Преимуществом химического никелирования являются простота процесса и возможность получения износостойкого и равномерного покрытия с хорошими антикоррозионными свойствами. При ремонте машин химическое никелирование применяют для восстановления точных деталей топливных насосов и гидравлических приводов.
3.6.6Определение режимных параметров электролитических покрытий
Время электролиза, ч
т ЮЛу
EjKn ’ |
(3.39) |
|
где h — толщина осаждаемого слоя, м; определяется в зави симости от величины износа поверхности детали; у — плот ность осаждающегося металла, г/см3; Е — электрохимичес кий эквивалент, г/А-ч (таблица 3.19); / — плотность тока на катоде, А/дм2 (таблица 3.19); h — коэффициент выхода ме талла, по току (КПД-ванны, таблица 3.19)
Количество ангидрида, г |
|
Q = F (Р + q), |
(3.40) |
где F — поверхность детали, подлежащая покрытию, м2; Р — расход ангидрида в граммах на 1 м2 поверхности При h = 1 мкм; при хромировании Р = 14 г/м2; q — потери осуждаемого ме талла, г; при хромировании q —300...320 г.
Таблица 3.19
Значения показателей для различных видов покрытия
Показатели
Е
п
h
___________ 1__________
Виды покрытий Хромирование Осталивание
0,323 |
1,042 |
||
0,12. |
..0,18 |
О 0° |
о чо |
20... |
50 |
20... |
50 |
6,9... |
7,1 |
7,8 |
3.7 Применение при ремонте полимерных материалов
Достоинства полимерных материалов — достаточная проч ность, хорошая химическая стойкость, высокие антифрик ционные свойства, износостойкость. Ремонт деталей с при менением полимерных материалов не требует сложного обо рудования и отличается незначительной трудоёмкостью. К недостаткам относятся низкая тепловая стойкость отдельных материалов, недостаточная усталостная прочность.
На ремонтных предприятиях полимерные материалы при меняют для заделки в деталях вмятин, трещин, пробоин, раковин, отколов, для восстановления размеров изношенной детали, для изготовления быстроизнашиваемых деталей или отдельных их частей. Различают термореактивные и термо пластические полимерные материалы.
Термореактивные материалы (реактопласты) характеризу ются тем, что при переходе под действием тепла в пластичес кое состояние подвергаются необратимым процессам, т.е. их нельзя после отверждения снова расплавить для вторичного использования.
Термопластические материалы (термопласты) характери зуются тем, что при повторном нагревании могут вновь под вергаться формованию.
Из термореактивных пластмасс получили распространение эпоксидные смолы ЭД-16 и ЭД-20 в различных композициях
путём добавок к смоле отвердителей, пластификаторов, напол нителей, красителей и других компонентов. Эпоксидная смо ла — это вязкая жидкость светло-коричневого цвета. Путём введения в смолу отвердителя смола переходит в твёрдое и нерастворимое состояние. В качестве отвердителя широко при меняют полиэтиленполиамин, представляющий собой вязкую маслянистую жидкость разных оттенков — от тёмно-бурого до светло-жёлтого. С целью придания полученной смеси эластич ности, вязкости и прочности вводят пластификаторы, из кото рых наиболее распространён дибутил-фталат, представляющий собой маслянистую желтоватую жидкость. Для улучшения физико-механических свойств отверждённой композиции до бавляют наполнители (железный порошок, графит, слюду, стек лоткань, тальк, асбест и др.). Термореактивные пластмассы применяют для заделки вмятин, трещин, пор и раковин в тон костенных деталях, а также для восстановления в корпусных деталях посадочных поверхностей под подшипники.
Из термопластов в ремонтном производстве используют полиамидные смолы. Они хорошо работают в условиях тре ния скольжения после нанесения их на поверхность детали слоем толщиной до 0,6-0,7 мм различными способами (газо пламенным, вихревым, вибрационным и др.)* Из полиами дов типа капролактам (капрон), АК-7 и П68 изготовляют методом литья под давлением подшипниковые втулки, втул ки рессор, оси и другие детали. Полиамиды выпускаются в виде гранул. Для повышения износостойкости, прочности и других свойств в полиамидные смолы вводят наполнители: графит, металлические порошки, тальк и др.
3.7.1 Технология нанесения на деталь полимерных покрытий
Основными способами нанесения на деталь полимерных покрытий являются газопламенный, вихревой и вибрацион ный. При всех способах нанесения покрытий требуется тща тельная подготовка поверхности путём очистки её от грязи,