
книги / Ремонт подъемных кранов
..pdfвыдают наряд-допуск, в котором должны быть указаны меры по обеспечению безопасных условий выполнения ремонта (меры по предупреждению поражения ремонтного персонала электрическим током, падения рабочих с высоты, наезда ра ботающих кранов на ремонтируемый, выхода ремонтников на подкрановые пути действующих кранов). Если нужен выход ремонтников на подкрановые пути, то должен быть оформлен их допуск, который предусматривает соответству ющие меры безопасности. Порядок выполнения ремонта оп ределяется сложностью конструкции крана и принятым пла ном ремонта.
Кран, подлежащий ремонту, нужно остановить в зоне, определённой для выполнения ремонта, и отключить трол ли. Ремонтную зону в пролете цеха, в котором расположено более одного крана, необходимо оборудовать подъёмными устройствами, служащими для опускания с крана грузов и их подъёма, а также установить упоры на подкрановых пу тях, предупреждающие столкновение ремонтируемого и ра ботающих кранов. Кроме того, нужно секционировать цехо вые тролли — это позволяет отключать участок в зоне ре монта от остальной части троллей, находящихся под напря жением. Площадь цеха под краном, который подлежит ре монту, должна быть огорожена и обозначена табличками, запрещающими вход в зону ремонта крана [4].
4.2 Технология ремонта металлоконструкций
При выводе крана в ремонт особое внимание следует уде лять состоянию несущей металлоконструкции. Ее освобож дают от груза и определяют состояние сварных швов и час тей конструкций, которые расположены рядом с ней. В за висимости от конструкции моста крана необходимо предва рительно установить леса или подмостки для осмотра свар ных швов и ремонта металлоконструкций. Для ремонта ме таллоконструкций удобно использовать леса подвесного типа (рис. 4.1).
Рис. 4.1 Леса подвесного типа
Элементы конструкции, которые потеряли в результате коррозии более 5 % первоначального сечения с двумя и бо лее усталостными трещинами, значительными по длине и опасными по расположению, с повторными усталостными трещинами в том месте, в котором они уже были однажды заварены, или рядом, а также с резкими изгибами в месте деформации, необходимо удалить и заменить новыми. Заме нить нужно также элементы конструкции с трещинами в полках или надрывами, а также элементы, которые не дают возможности получить после ремонта требуемую несущую способность. Если узел имеет значительное количество де фектов, то его следует заменить новым.
Анализ металлоконструкций кранов показывает, что ус талостные трещины в них появляются уже через 5...7 лет нормальной эксплуатации, а иногда и быстрее. Чаще всего трещины появляются в концевых балках и близлежащих от них сечениях пролётных балок и ферм. Усталостным разру шениям подвергаются преимущественно элементы, нагружен ные переменными напряжениями растяжения, т.е. нижние пояса ферм, нижние горизонтальные листы, растянутые во локна вертикальных листов пролётных и концевых балок. Усталостные трещины в сжатых элементах практически от сутствуют. Это объясняется большим запасом прочности, вследствие необходимости обеспечения устойчивости, и боль-
шими пределами выносливости материалов при работе эле ментов на сжатие. Фактические сроки службы (месяцы) в зависимости от режимов работы деталей кранов приведены ниже (для справки):
|
с |
Т |
ВТ |
Канат |
6 |
3,5 |
2,5 |
Ходовое колесо ............................... ..... |
7 |
4,5 |
4 |
Зубчатая муфта механизмов движения: |
12 |
|
|
м оста......................................................... |
18 |
9 |
|
тележки.................................................... |
18 |
8 |
4 |
Зубчатое колесо механизмов: |
60 |
|
|
подъёма.............................................. ..... |
60 |
60 |
|
передвижения тележки. |
18 |
8 |
4 |
передвижения моста |
24 |
9 |
6 |
Тормозная накладка |
1,5 |
1,0 |
0,5 |
При эксплуатации кранов наиболее часто возникают де фекты:
1.Трещины в сварных швах в местах соединения главных
иконцевых балок — зона А (рис. 4.2). При ремонте повреж дённые участки швов вырубают и заваривают вновь.
Рис. 4.2 Трещины в швах в месте примыкания вертикальных листов главных балок к концевым балкам
2. Поперечные трещины сварных швов поясов главной фермы в Месте соединения с концевой балкой — зона В. Эти повре>КДеНия на верхнем поясе ликвидируют посредством разделки трещины по шву и её заварки. Сверху приварива
ют металлическую накладку толщи |
|
ной, равной толщине пояса. В ниж |
|
нем поясе, где заварку выполнить |
|
невозможно, можно наложить ме |
|
таллическую накладку сверху и при |
|
варить её (рис. 4.3). Такие исправ |
|
ления можно производить, если тре |
|
щина в сварном шве не вызвала зна |
|
чительных деформаций конструк |
|
ции и не привела к смещениям её |
|
отдельных частей. Если из-за трещи |
|
ны произошло смещение частей ме |
|
таллоконструкции более 10 мм, то |
|
мост необходимо демонтировать и за |
|
тем восстанавливать при снятой на |
Рис. 4.3 Установка |
грузке (вес тележки, собственный |
накладки на нижнем |
вес главной балки). |
поясе главной балки |
3.Трещина в сварном шве или в
основном металле вертикального листа главной балки в месте примыкания кронштейнов горизонтальных настилов (рис. 4.4). При ремонте повреждённые места старого шва или основного металла вырубают под заварку и накладывают новый шов.
Рис. 4.4 Трещины в вертикальном листе главной балки
4. Трещины в основном металле нижних поясов вспомога тельных ферм, в уголках и раскосах горизонтальных ферм (рис. 4.5). Эти трещины можно устранить посредством их за варки, а также приваркой к повреждённым местам дополни тельных деталей, листов, планок и уголков. Сварные швы и сечения дополнительных деталей необходимо рассчитывать на равнопрочность. Длину планок и уголков определяют, ис ходя из необходимой длины сварных швов: L = [F/(4SaK) + С, где L — длина одного шва с одной стороны от повреждённого участка, мм; F — площадь сечения восстанавливаемого эле мента моста, мм2; S — толщина сечения сварного шва, мм2, определяемая толщиной свариваемых элементов; а — коэф фициент ослабления шва, а = 0,8; К — коэффициент, харак теризующий соотношение допускаемых напряжений на раз рыв и срез в элементе моста и сечении шва, К = 0,8; С — дополнительная длина шва на непровар в начале шва, С = 20 мм.
Т
Рис. 4.5 Трещины в основном металле нижних поясов ферм
5.Изгиб уголков форменных мостов. Его устраняют при небольших прогибах или заменяют при больших прогибах.
6.Трещины в швах в местах крепления букс мостов и тележек (рис. 4.6). Их устраняют посредством вырубки швов
иосновного металла и новой заварки. При этом необходимо
Рис. 4.6 Трещины в местах установки букс
разгрузить повреждённые места. Для этого под концевую балку следует подвести клинья или приподнять угол моста домкратом.
7. Разрыв уголков нижнего пояса главной фермы вблизи сварного шва (рис. 4.7). Для восстановления уголка старую косынку (рис. 4.7, а) следует удалить и заменить ее удлинён ной косынкой и новым уголком (рис. 4.7, б).
Рис. 4.7 Разрыв уголка иижнего пояса фермы вблизи сварного шва
Трещины в листовых элементах металлоконструкций ре монтируют заваркой: кромки трещины 1 (рис. 4.8) дополни тельно по 20...30 мм за её границы в направлении возможно го развития трещины разделывают, по концам разделки свер лят отверстия 2 и зачищают до блеска. Глубина, вид раздел ки и диаметр отверстия определяются толщиной сваривае мого металла. Трещину заваривают электродом Э42А-Ф (кон струкции из углеродистых сталей) или Э50А-Ф (конструк-
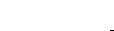
ции из низколегированных сталей), оставляя отверстия незаверенны ми. Ответственные элементы при этом усиливают накладками 3 (тол щиной 0,6...0,7 толщины элемен та). Приварку накладки следует выполнять фланговыми швами, из бегая наложения усиленных и по перечных швов.
При ремонте или реконструк
Рис. 4.8 Схема приварки усиливающей накладки ции кранов возникает необходи
мость усиления металлоконструкций. Схемы усиления нижних и верхних поясов и раскосов показаны на рисунке 4.9 (усиливающий элемент обозначен пунктиром).
а) ч г |
ч г |
|
|
|
В клёпаных элементах ме |
DC И Г |
т |
DIC |
таллоконструкций все слабые |
||
ч г |
ч г |
ят ж |
Ж |
расшатавшиеся заклёпки |
|
нужно заменить новыми уве |
|||||
Ч'Г |
Ч'Г |
ж т |
Ч|Г |
Ж |
личенного размера. Заклёпки |
|
|
|
|
|
диаметром до 12 мм разреша |
б) |
|
Ж А |
- ! .1 А |
ется клепать в холодном со |
|
... |
J'L |
стоянии, свыше 12 мм — с |
|||
J L |
|
|
|
|
|
в) . b j ! L _ , ; L D !C _ J!L jjL . |
1 DC |
нагревом до 1100... 1200 °С. В |
|||
один приём может быть уда |
|||||
|
I •I |
I |
|
|
лена только одна заклёпка, |
|
|
|
|
|
|
Рис. 4.9 Схема усиления |
заменять последующую зак |
||||
элементов металлоконструкций: |
лёпку можно только после ус |
||||
а — верхний поясов; |
тановки предыдущей. |
||||
|
б — нижних поясов; |
На все виды ремонтов ме |
|||
|
в — раскосов |
|
таллоконструкций кранов не |
обходимо разработать рабо чие чертежи в соответствии с действующими государствен ными стандартами. Чертежи разрабатывает отдел главного механика. Их следует утвердить в установленном на пред приятии порядке. При разработке рабочих чертежей нельзя
уменьшать сечения элементов, изменять сечения и длину сварных швов конструкций. На выполнение ремонта метал локонструкций предприятие, осуществляющее ремонт, дол жно получить разрешение Федеральную службу экологичес кого технологического и атомного надзора (Ростехнадзор).
При ремонте металлоконструкций кранов нужно исполь зовать тот же материал, из которого выполнена основная конструкция. При отсутствии необходимых данных о мате риалах следует произвести химический анализ для опреде ления марки стали. Для металлоконструкций, работающих на открытом воздухе при температуре от -25 до -40 °С, сле дует применять при ремонте мартеновскую сталь спокойной плавки. На все используемые материалы должны быть сер тификаты завода-изготовителя. Если они отсутствуют, то нужно выполнить полный химический анализ материала, а также механические испытания на временное сопротивле ние, предел текучести и относительное удлинение.
Перед сваркой металлоконструкций детали тщательно очи щают. Они не должны иметь кривизны и подрезов. В местах наложения сварных швов детали нужно очистить от ржав чины до металлического блеска на ширину не менее 20 мм. Узлы металлоконструкций следует собирать на плитах, стел лажах или стендах, которые гарантируют правильную уста новку деталей. Сборку нужно выполнять без приложения усилий, создающих в деталях изгибы или упругие деформа ции. При производстве ремонтных работ на месте установки крана действует правило свободной сборки.
Если в металлической конструкции имеются элементы с прогибами (изгибы стоек и раскосов ферм, полок уголков нижних или верхних'поясов ферм), то допускается их прав ка в холодном состоянии при условии, что прогиб не превы шает 3 % свободной длины элементов. Холодную правку осу ществляют с приложением статической нагрузки и только при положительной температуре воздуха.
Правку выполняют посредством струбцин (рис. 4.10, а), домкратов (рис. 4.10, б), скоб (рис. 4.10, в) и рычагов
Рис. 4.10 Приспособление для правки металлоконструкций
(рис. 4.10, г). Вмятины, которые не поддаются правке, ремон тируют приваркой рёбер жёсткости (рис. 4.11). При значи тельном изгибе элементов разрешается их правка с нагревом до 900... 1150 °С (от вишнёвого до оранжевого цвета каления). Правку с нагревом до 700... 1100 °С применяют для элементов
|
|
|
|
из углеродистых сталей, до |
|
|
|
|
|
900... 1150 °С — для элементов |
|
Ш П I LL |
|
................... |
|
из низколегированных сталей. |
|
ТТМ1 МГ |
|
|
|
Деформированные элементы ме |
|
|
|
|
|
||
|
|
|
|
таллоконструкций нагревают го |
|
JJJ |
" V |
i - U I I I I Ш |
|
релкой с выпуклой стороны в ме |
|
I H I I I I I |
TTTTTTT |
|
|||
|
|
|
|||
|
|
|
сте наибольшей деформации. |
||
|
|
|
|
||
|
|
|
|
Охлаждать элементы после прав |
|
|
|
|
|
ки можно только при положи |
|
m in 0,25h d > 0,25h |
|
|
тельной температуре воздуха. |
||
.... |
|
...... |
|
Правка деформированных эле |
|
|
— |
ментов наплавкой валиковых |
|||
|
|
|
|
|
|
^ т т |
|
1 ^ |
— |
швов ударами |
не допускает |
|
|
|
|||
Рис. 4.11 Схема приварки |
ся [5]. Правку |
нужно прекра |
|||
щать при температуре не ниже |
|||||
рёбер жёсткости |
|
70 °С (красный цвет каления). |
|||
|
|
|
|
Перед сваркой узлов следует обязательно проверить:
а) соответствие размеров деталей их чертежам, наличие сертификатов на металл, на деталях должна быть мар кировка, перенесенная с основного металла контролё ром ОТК;
б) правильность разделки металла под сварочные швы и соответствующие зазоры между деталями, подлежащи ми сварке. Размеры сварочных швов необходимо уста навливать по толщине металла свариваемых деталей или расчётом.
При выполнении сварочных работ под открытым небом при температуре ниже О °С, рабочее место сварщика должно быть защищено от ветра и попадания осадков. Наименьшая отри цательная температура, при которой разрешается производить сварочные работы на металлоконструкциях кранов (табл. 4.2), должна быть согласована с местным органом Ростехнадзор.
Таблица 4.2
Минимально допустимая начальная температура, °С, стали при ручной и полуавтоматической дуговой сварке без предварительного подогрева
Толщина стали, мм |
Углеродистая сталь |
Низколегированная сталь |
До 16 (включительно) |
-30/-30 |
-20/-20 |
Свыше 16 до 30 |
-30/-20 |
-10/-0 |
Свыше 30 до 40 |
-10/-10 |
0/+5 |
Свыше 40 |
0/0 |
+5/+10 |
Примечание. В числителе указана температура для решетчатых конструк ций, в знаменателе — для листовых конструкций.
Сварные швы не должны иметь неровности, пористость, непровары, раковины, незаплавленные кратеры, трещины в основном или наплавленном металле, а также не допускают ся подрезы основного металла и неправильная высота швов. Сварщик, выполнявший шов, должен поставить личное клей мо в начале и в конце сварочного шва. На сварочных швах, которые сосредоточены в одном месте, разрешено ставить одно клеймо сварщика.