
книги / Ремонт подъемных кранов
..pdfмасел, оксидов. Поверхности, не подлежащие покрытию по лимерным материалом, изолируют фольгой или асбестом.
Газопламенное напыление заключается в том, что порош кообразный полимер подаётся в газовое пламя горелки и струёй воздуха в расплавленном состоянии наносится на поверхность предварительно нагретой детали. Для газопламенного напы ления наибольшее применение получили установки типа УПН.
Эти установки работают следующим образом. При подаче воздуха по каналу 2 (рисунке 3.37) инжектор 1 создаёт раз режение, которое по каналу 9 передаётся в питающий ба чок 5 с порошкообразным полимером и одновременно в ди афрагменный пневматический клапан 10. Под действием раз режения диафрагма оттягивает иглу 11 клапана. В результа те этого открывается отверстие для прохода сжатого воздуха и он поступает к вибратору 8. От воздействия вибрации и создавшегося в бачке разрежения порошок поступает по ка налу 9 к горелке. Туда же через штуцер 7 и смесительную камеру 6 поступает атмосферный воздух. Позиция 3 на ри сунке обозначает кран, 4 — регулятор воздуха.
При напылении покрывают за один проход поверхность шириной 20-70 мм. Толщина покрытия может составлять
Сж атый возд у х
Рис. 3.37 Установка для газопламенного напыления
141
до 10 мм. После покрытия напыленный слой дополнительно прогревают пламенем горелки. Для газопламенного напыле ния используют специальные порошки марок ТПФ-37, ПФН-12, а также полиэтилен, капрон, полистирол и различ ные составы из этих материалов с наполнителями.
После очистки деталь перед напылением покрывают теп лоизоляционным грунтом и нагревают распылительной го релкой до температуры, несколько превышающей темпера туру плавления полимерного порошка. Необходимость грун товки поверхности связана с предохранением покрытия от растрескивания после охлаждения.
При ремонте машин газопламенное напыление применя ют для заделки вмятин, забоин и следов сварки в деталях из тонколистового материала (на кабинах и оперении), для на несения покрытия на подшипники, а также в качестве анти коррозионного, электроизоляционного, теплоизоляционного и декоративного покрытий.
Вихревое напыление основано на погружении предвари тельно нагретой детали в камеру, в которой находится взвих ренный (псевдоожиженный) потоком воздуха или инертного газа полимерный порошок; частицы порошка, сталкиваясь с нагретой деталью, оплавляются и образуют на её поверхнос ти покрытие.
Аппарат для вихревого напыления имеет камеру 2 (рис. 3.38), разделенную сетчатой перегородкой 6 и тканью 5, предохраняющей от засорения отверстия пе регородки. На ткань насы пают порошкообразный по лимер (капролактам, поли этилен и др.) с размером частиц 0,1-0,15 мм. Толщи
на слоя порошка должна быть не менее 100 мм. Восстанавли ваемую деталь 4, нагретую до температуры несколько выше
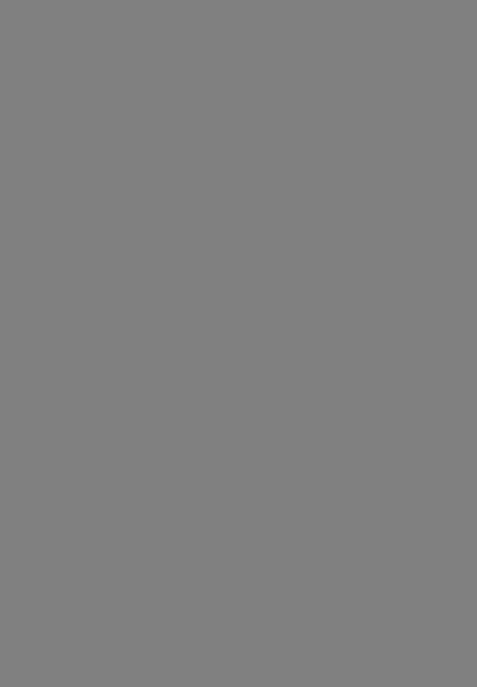
тате вибраций сосуда с частотой 50-100 Гц порошок полиме ра переходит в псевдоожиженное состояние и, контактируя с нагретой деталью, образует неравномерность покрытия. Пос ле нанесения покрытия деталь помещают в горячую камеру для оплавления слоя. Вибрационный способ нанесения покры тий весьма перспективен: не требуется ацетилена, сжатого воз духа, деталь не охлаждается потоком газа. К недостаткам это го способа относятся высокие требования к дисперсности по рошка и равномерное и хорошее покрытие толщиной до 1,5 мм.
Вибровихревое напыление. При этом способе напыления на слой псевдоожиженного газом полимерного порошка на кладываются с помощью специального устройства колеба ния с частотой 50-100 Гц и с амплитудой до 10 мм. Установ лено, что при вибровихревом способе напыления повышает ся качество покрытия и возможность нанесения слоя боль шей толщины, чем при вихревом или вибрационном способе.
Заделка трещин в корпусных деталях. Дефекты в корпус ных деталях в виде трещин устраняют путём применения клеевых композиций на основе эпоксидных смол. Клеевые композиции, используемые при заделке трещин, приведены в таблице 3.20.
Для ремонта чугунных деталей рекомендуются составы № 1
и4, для стальных деталей — N° 2, для алюминиевых — № 3
идля пластмассовых — № 5.
Заделка трещины в корпусной детали состоит из следую щих операций.
1.Подготовка детали: а) засверливание на концах трещи ны отверстий диаметром 2,5-3 мм; б) разделывание фас ки (при толщине стенки свыше 1,5 мм); в) зачистка покрываемых мест до металлического блеска на рассто янии 10-15 мм по обе стороны от трещины; г) обезжи ривание ацетоном, бензином или щелочным раствором.
2.Приготовление эпоксидного состава: нагрев эпоксидной смолы до 120-160 °С с выдержкой при этой температу ре в течение 12 ч с целью удаления влаги; введение дибутилфталата при тщательном перемешивании. В про-
Клеевые композиции
Состав композиции
Компоненты |
№ 1 |
(в массовых долях') |
|
||
Полимер — смола ЭД-16 |
№ 2 |
№ 3 |
№ 4 |
№ 5 |
|
100 |
100 |
100 |
100 |
100 |
|
Отвердитель — полиэтиленполиамин |
10 |
10 |
10 |
10 |
10 |
Пластификатор — дибутилфталат |
15 |
15 |
15 |
15 |
15 |
Наполнители: |
|
_ |
|
|
|
чугунный порошок |
150 |
|
|
|
|
оксид железа |
_ |
150 |
_ |
|
|
графит |
— |
— |
50 |
|
|
молотая слюда |
20 |
20 |
_ |
_ |
_ |
алюминиевая пудра |
— |
— |
20 |
_ |
_ |
(этрол |
- |
- |
- |
|
90 |
цессе перемешивания вводят наполнитель и массу про гревают при 80—100 °С в течение 10—15 мин. После это го массу охлаждают до комнатной температуры и затем вводят небольшими порциями отвердитель.
3.Нанесение шпателем эпоксидного состава путём втира ния его в трещину на ширину 10-15 мм с выдержкой в течение 3-6 мин.
4.Нанесение второго слоя и выдержка детали при ком натной температуре в течение 20-24 ч. При нагреве де тали до 60 °С продолжительность отверждения состав
ляет 4-5 ч.
5.Испытание на герметичность под давлением 0,3-0,4 МПа. Эпоксидными композициями заделывают трещины в во дяной рубашке блока цилиндров, в корпусах масляных
иводяных насосов, в картерах коробок передач и других корпусных деталях. Устранение пробоин производится наложением металлической накладки, которая фикси руется на стенке корпуса с помощью эпоксидного клея.
Втолстостенной детали возможно также заполнение про боины заподлицо поочерёдно — сначала эпоксидной смо лой, а затем стеклотканью в несколько слоёв.
3.7.2 Склеивание деталей
При ремонте машин для склеивания деталей применяют клеи типа БФ, ВС-ЮТ, ВС-350, ВК-200, эпоксидные смолы и др. Склеивание деталей состоит из операций подготовки поверхно стей к склеиванию, нанесения клеевого слоя, соединения дета лей и термообработки с целью отверждения клеевого шва.
Подготовка поверхностей к склеиванию необходима для хорошего сцепления (адгезии) клеевого состава с материа лом детали. Поверхности тщательно очищают от загрязне ний, масла и оксидов.
Металлические поверхности зачищают наждачными круга ми. Шероховатость поверхности должна соответствовать при мерно Rz = 20 мкм. После очистки поверхности соединяемых деталей обезжиривают ацетоном или авиационным бензином.
Клеи типа БФ (БФ-2, БФ-4, БФ-6) — спиртовые растворы термореактивных смол. Их теплостойкость не выше 80 °С, предел прочности при сдвиге 40-60 МПа. Клеи БФ-2 и БФ-4 применяют в основном для склеивания металлических дета лей между собой, а клей БФ-6, являющийся более эластич ным, — для приклеивания текстильных материалов к ме таллическим деталям.
На поверхность детали клеи БФ наносят в два или три слоя с помощью кисти или шпателя с промежуточным про сушиванием в течение 10-20 мин. Толщина клеевого слоя должна быть в пределах 0,1-0,2 мм. При большей толщине слоя силы сцепления (когезия) молекул клея уменьшаются в 1,5-2 раза. После нанесения клеевого слоя детали стягивают струбцинами или специальными приспособлениями до полу чения давления 0,5-1 МПа и в таком виде просушивают при температуре 140-150 °С в течение 30-60 мин.
Клей ВС-1ОТ — раствор синтетических смол в органичес ких растворителях. Этот клей отличается диапазоном рабо чих температур от — 60 до 100 °С. Его используют для при клеивания фрикционных накладок к дискам муфты сцепле ния и к колодкам.
Приклейка накладок к дискам состоит из следующих опе раций:
1)снятия изношенных накладок и зачистки дисков до ме таллического блеска;
2)зачистки поверхности накладок, прилегающих к дис кам, для придания им шероховатости;
3)промывки и обезжиривания ацетоном поверхностей дис ков и накладок и просушивания их в течение 10-15 мин.;
4)нанесения двух тонких слоёв клея с промежуточным просушиванием в течение 15 мин. при 20 °С и 5 мин при 60-65 °С;
5)сборки накладок с дисками в специальном приспособ лении, обеспечивающем давление 0,5-1 МПа;
6)сушки деталей вместе с приспособлением в сушильном шкафу при 180 °С в течение 40 мин.
Для сборки неподвижных соединений применяют клей БФ-2, если зазор в соединении невелик (0,1-0,15 мм). При больших зазорах пользуются клеевой композицией № 1 на основе эпоксидной смолы. Эпоксидный состав наносят в один слой.
3.7.3 Восстановление деталей опрессовкой
Опрессовкой восстанавливают изношенную или повреж дённую деталь с помощью расплавленной пластмассы в прессформе, рабочая полость которой имеет размеры новой детали. Раз личают компрессионное и литье вое прессование.
Компрессионное прессование
заключается в следующем. Де таль 7 (рис. 3.41) размещают с по мощью установочного элемента 6 в нижней части пресс-формы 5; за тем устанавливают верхнюю часть пресс-формы 3 и через загрузоч
ное окно 2 засыпают термореактивный порошок. Под воз действием электроподогрева 4 и давлении пуансона 1 рас плав порошка заполняет свободные полости, наращивая на детали определённый слой 10. Для удаления детали из прессформы предусмотрен выталкиватель 8. Позицией 9 обозна чена опорная плита.
Литьевое прессование произво |
|
|
дят с использованием термоплас |
|
|
тичных материалов. Полимерный |
|
|
материал предварительно расплав |
|
|
ляют и подают под давлением в |
|
|
пресс-форму, показанную на ри |
|
|
сунке 3.42: 1 — литник; 2 и 3 — |
|
|
верхняя и нижняя части пресс- |
|
|
формы; 4 — восстанавливаемая де |
Рис. 3.42 Пресс-форма |
|
таль; 5 — наращиваемый слой; |
||
|
6 — выпары для удаления воздуха. Пресс-форму предвари тельно подогревают до температуры 80-100 °С.
Опрессовкой можно восстанавливать или изготавливать малонагруженные шестерни, крыльчатки водяного класса, вкладыши подшипников.
3.7.4 Механическая обработка деталей с пластмассовыми покрытиями
Они имеют свои особенности. Поскольку они обладают низкой теплопроводностью, при механической обработке сле дует применять хорошо заточенный теплостойкий инстру мент и обильное охлаждение сжатым воздухом или кероси ном. Токарную обработку выполняют при скорости резания 200-300 м/мин. и подаче 0,15-0,2 мм/об.
При использовании полимерных материалов, особенно эпоксидных композиций и синтетических клеев, необходимо строго соблюдать меры техники безопасности, так как многие компоненты, входящие в их состав, токсичны и огне опасны.
3.8 Ремонт деталей методами пластического деформирования
Обработка пластическим деформированием (давлением) основана на способности металла изменять свою форму, раз меры и механические свойства без разрушения под действи ем внешних сил за счёт его пластических (остаточных) де формаций. При ремонте машин выполняют следующие ос новные операции: восстановление размеров изношенных уча стков путём перераспределения массы деталей (раздача, об жатие, осадка, вдавливание, вытяжка, растяжка, накатка); устранение дефектов формы деталей путем правки; повыше ние эксплуатационных свойств деталей в результате поверх ностного пластического деформирования металла.
Ремонтные операции проводят без дополнительного нагрева деталей и с предварительным их нагревом.
При обработке деталей в холодном состоянии пластичес кая деформация происходит вследствие сдвигов частиц, внут ри кристаллов металла (внутрикристаллическая деформация), что сопровождается изменением физико-механических свойств металла (увеличением предела текучести, снижени ем вязкости, повышением твёрдости). При обработке давле нием в горячем состоянии пластическая деформация проис ходит вследствие сдвигов целых зёрен металла (межкристал лическая деформация). Нагрев деталей приводит к измене нию физико-механических свойств и структуры металла, поэтому ответственные детали после обработки давлением под вергаются повторной термической обработке.
Рассмотрим основные операции при ремонте деталей дав лением.
Раздача. Эту операцию применяют для увеличения по на ружному диаметру изношенных полых деталей за счёт изме нения внутренних размеров деталей (поршневые пальцы, втулки, пустотелые валы, чашки дифференциала и др.). При раздаче направление давления р от внешних сил совпадает с направлением деформаций S(рис. 3.43, а).
149
Поршневые пальцы, на пример, раздают в приспо соблении, схема которого показана на рисунке 3.43, б. Палец 2 с зазором устанав ливают в матрицу 4, кото рая базируется в основа нии 1 штампа. Внутрь паль ца вводят пуансон 3 и, дей ствуя усилием Р от гидрав
лического пресса, увеличивают (раздают) наружный диаметр пальца до требуемого размера. Перед раздачей производят вы сокий отпуск пальцев при температуре 650-680 °С, что позво ляет повысить пластичность металла. После раздачи пальцы закаливают с поверхности токами высокой частоты, подверга ют предварительному и чистовому бесцентровому шлифова нию, суперфинишированию и полированию.
Давление р (в МПа) при раздаче рассчитывают по формуле
р = 1,15ат1п— |
(3.41) |
г |
|
где ат— предел текучести металла детали, МПа; Л и г — наружный и внутренний радиусы детали мм.
Обжатие применяют для уменьшения по внут реннему диаметру изно шенных полых деталей за счёт изменения наружно го диаметра (рис. 3.44, а). На рисунке 3.44, б пока зана схема обжатия брон зовой втулки по наружно му диаметру. Втулка про талкивается с помощью
пуансона 2 через матрицу 4, которая размещена в основа нии 1 штампа. Так как после обжатия наружный диаметр