
книги / Ремонт подъемных кранов
..pdf2.Шихту сталинита наплавляют стальным электродом. На плавленный слой получается более вязким, но менее износостойким.
3.Сталинит вводят в состав обмазки стальных электродов.
4.Сталинит вводят в состав шихты специальных пустоте лых электродов (трубчатых, ленточных и др.).
Устранение дефектов в деталях из чугуна. При ремонте чугунных деталей применяют дуговую и газовую сварку и наплавку, газопорошковую наплавку и пайку. Выбор спосо ба восстановления зависит от конфигурации детали, распо ложения в детали дефекта, характера нагрузки, восприни маемой деталью, и требований к обрабатываемости восста новленного участка.
У деталей из чугуна сваркой заделывают трещины и от верстия, присоединяют отколотые части детали, наплавляют износостойкие покрытия.
Ремонт чугунных деталей представляет некоторые труд ности, так как чугун имеет значительное содержание углеро да, низкую вязкость и свободный углерод в структуре. При быстром охлаждении чугуна возможно образование в околошовной зоне твёрдых закалочных структур. При расплавле нии чугуна может произойти местный переход графита в цементит, в результате этого в данном месте металл получа ет структуру белого чугуна. В закалённых и отбеленных зо нах металл твёрд и хрупок. Разница в коэффициентах ли нейного расширения серого и белого чугуна приводит к обра зованию внутренних напряжений и появлению трещин. Кроме этого, вследствие выгорания углерода и кремния сварной шов получается пористым и загрязнённым шлаковыми включе ниями, так как быстрый переход чугуна из жидкого состоя ния в твёрдое не позволяет образовавшимся газам и шлакам полностью выделиться из металла. Следует также иметь в ВИДУ возможность плохого сплавления присадочного метал ла с основным металлом в связи с насыщенностью чугуна газами. Такой чугун может быть в деталях, работавших в машине длительное время при температуре 400 °С и выше.
Отмеченные трудности при ремонте деталей из чугуна потре бовали разработки специальных технологических приёмов сварки, которые можно разделить на две группы: горячая и
холодная сварка чугуна. |
|
|
Горячая |
сварка чугуна. |
|
Уменьшить |
отрицательное |
|
влияние внутренних напряже |
|
|
ний и предупредить закалку |
|
|
околошовной зоны можно пу |
|
|
тём предварительного подогре |
|
|
ва крупногабаритных деталей |
|
|
и медленного охлаждения их |
Рис. 3.9 Влияние температуры |
|
после сварки. На рисунке 3.9 |
||
показано влияние температу |
нагрева детали на уменьшение |
|
ры нагрева детали на умень |
внутренних напряжений |
|
|
шение внутренних напряжений (ось ординат — степень на пряжённости Н, ось абсцисс — температура нагрева).
При горячей сварке деталь предварительно медленно на гревают в печи до температуры 550-600 °С. Рекомендуется двухстадийный нагрев детали. Например, блоки и головки цилиндров двигателей нагревают до 400 °С в течение 1 ч и от 400 до 650 °С в течение 0,5 ч. Для того чтобы в процессе заварки деталь не охлаждалась ниже 500 °С, после нагрева её накрывают теплоизоляционным кожухом, а заварку де фектного места ведут через окно в кожухе. По окончании заварки деталь вновь помещают в печь, нагревают до темпе ратуры 600-650 °С для снятия внутренних напряжений, а затем медленно охлаждают вместе с печью.
При горячей сварке чаще используют ацетилено-кислород ное пламя и реже — дуговую сварку. Лучшее качество обес печивает газовая сварка вследствие меньшего выгорания уг лерода. При газовой сварке следует пользоваться нейтраль ным пламенем. Расплавление металла ведут восстановитель ной зоной пламени. В качестве присадочного материала при меняют чугунные прутки марок А и Б диаметром 6 -8 мм. Химический состав прутков представлен в таблице 3.2.
Таблица 3.2
Химический состав прутков
Марка |
|
|
Содержание элементов, % |
|
|
|||
прут |
|
|
|
S (не |
|
Сг (не |
Ni (не |
|
ка |
с |
Si |
Мп |
Р |
||||
более) |
более) |
более) |
||||||
А |
3-3,5 |
3-3,4 |
0,5-0,8 |
|
||||
0,08 |
0,2-0,4 |
0,05 |
0,03 |
|||||
Б |
3-3,5 |
3,5-4 |
0,5-6,8 |
0,08 |
0,3-0,5 |
0,05 |
0,04 |
Прутки марки А предназначены для горячей сварки чугу на, а марки Б — для сварки с местным подогревом тонко стенных деталей. Номер наконечника горелки принимают из расчёта расхода 100-120 л/ч ацетилена на 1 мм толщины свариваемого металла. Кроме прутков марок А и Б, для сварки применяют также выбракованные поршневые кольца из се рого чугуна. Эти кольца имеют повышенное содержание крем ния, который снижает отбеливание чугуна.
При газовой сварке чугуна обязательно применение флюса, так как температура плавления чугуна ниже температуры плавления его оксидов (соответственно 1200 и i400 °С). Наи более распространены следующие флюсы: 1) бура; 2) смесь из 50 % буры и 50 % двууглекислого натрия; 3) смесь из 56 % буры, 22 % углекислого натрия и 22 % углекислого калия.
Дуговую сварку чугуна применяют для ремонта неответ ственных деталей, имеющих сравнительно толстые стенки. При этом используют электроды ОМЧ-1, представляющие собой прутки марки Б со специальным покрытием (мел, по левой шпат, графит, ферромарганец, жидкое стекло).
Горячая сварка чугуна обеспечивает высокие качества свар ного соединения, однако по техническим и экономическим соображениям применяется сравнительно редко и в основном при сварке сложных корпусных деталей. Более распростране на в практике ремонтного производства холодная сварка.
Холодную сварку чугуна ведут без предварительного подо грева детали, поэтому сварной шов охлаждается быстро. Это приводит к отбелу чугуна в зоне шва и возникновению в зоне
сварки больших внутренних напряжений и даже трещин. Чтобы уменьшить влияние этих факторов, применяют ряд специальных способов сварки. К ним относятся способ нало жения так называемых отжигающих валиков обычными элек тродами из низкоуглеродистой стали и сварка с помощью специальных электродов.
Сварка способом отжигающих валиков заключается в сле дующем. Сначала накладывают сварной валик длиной 35-50 мм электродом Э-34, а затем на этот валик сразу на кладывают второй валик. При этом первый валик больше прогревается и затем остывает с меньшей скоростью, поэто му часть цементита распадается, выделяется графит, а зака ленная часть шва частично подвергается нормализации. Кро ме того, верхний валик менее подвержен закалке, в резуль тате чего снижается твёрдость всего шва и частично снима ются остаточные напряжения. В зависимости от толщины стенки детали возможно наложение различного числа вали ков (рис. ЗЛО): а — в два слоя; б — в три слоя. При толщине стенки свыше 15 мм применяют многослойную наплавку.
•ч |
: |
5 |
|
|
‘О |
J______ |
|
•) |
б) |
||
S |
Рис. 3.10 Наложение различного числа валиков
Рассмотрим заделку трещины способом отжигающих ва ликов в тонкостенной чугунной детали (толщина стенки 6-7 мм). При толщине стенки до 7 мм фасок вдоль трещины не снимают и заделку трещины выполняют в такой последо вательности:
1)отступая на 8-10 мм от концов трещины, наваривают поперечные валики 1 и 2 (рис. 3.11, сечение А -А );
2)вдоль трещины, отступая от неё примерно на 2 мм, на варивают с двух сторон подготовительные и отжигаю щие валики (сечение В-В) участками длиной не более
Рис. 3.11 Наварка трещины валиками
50 мм и в последовательности, показанной на рисунке; при наложении валиков каждый участок проковывают ударами молотка и дают возможность шву охладиться до 50-60 °С;
3) накладывают соединительный валик в последователь ности I-IV (сечение С-С).
Трещину в чугунной детали с толщиной стенки 8 мм и более заваривают в следующем порядке (рис. 3.12, а, б):
1)засверливают отверстия на концах трещины;
2)разделывают трещину путём снятия фасок так, что бы ширина канавки составляла 2-3 толщины стенки детали;
Рис. 3.12 Заварка трещин
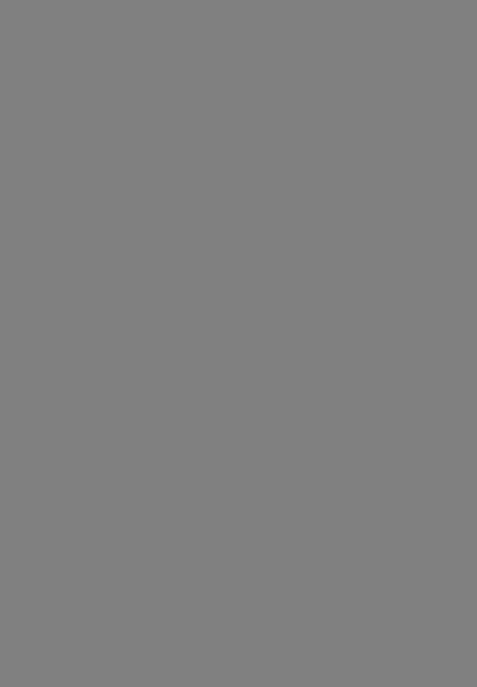
качестве материала стержня используют проволоку Св.-04Х19Н9 или Св.-04Х19Н9Т диаметром 3,5 мм с фтори сто-калиевым покрытием УОНИ-13/55. Металл шва — мед нохромоникелевый сплав, хорошо поддающийся механичес кой обработке. Трещин и пор при сварке не образуется. Сварку выполняют при силе тока 100-200 А.
Из группы специальных электродов на основе медных спла вов наиболее распространены электроды ОЗЧ-1 и МНЧ-1. Электроды ОЗЧ-1 изготовляют из медной проволоки с по крытием, содержащим железный порошок (50% ). Наплав ленный шов представляет собой железомедный сплав, обла дающий хорошей вязкостью. Однако в околошовной зоне образуются участки отбелённого чугуна, трудно поддающие ся механической обработке. Лучшие результаты даёт сварка электродами МНЧ-1, материал стержня которых — монельметалл (63 % Ni + 37 % Си). Электроды МНЧ-1 имеют по крытие УОНИ-13/55. Металл шва — железоникелевый сплав невысокой твёрдости (около 160 НВ). Шов пластичный, плот ный. Сварка чугунов электродами из цветных металлов ме нее экономична, но обеспечивает получение пластичного шва, достаточно прочного и хорошо поддающегося механической обработке.
Наплавку деталей специальными электродами ведут на постоянном токе обратной полярности.
Газопорошковая наплавка чугуна. Сущность этого спосо ба заключается в том, что на нагретую поверхность напыля ют тонкий слой порошкообразного сплава. В результате про текания диффузионных процессов между расплавленным порошком и поверхностью основного металла образуется на плавленный слой. Для наплавки чугунных деталей приме няют порошки марки НПЧ, имеющие следующий состав (в %): медь — 57; бор — 11,8; кремний — 0,7-0,95; никель — остальное. Наплавку осуществляют специальной ацетилено кислородной горелкой ГАЛ-2-68. Порошок поступает через воронку, закрепленную на стволе горелки. Слой можно на нести толщиной до 3 мм.
Сварка деталей из алюминия и его сплавов. Сварка и на плавка деталей из алюминия и его сплавов затруднена по следующим причинам:
1)при сварке образуются тугоплавкие плёнки оксидов А120 3 с температурой плавления 2050 °С, в то время как тем пература плавления алюминия 660 °С;
2)алюминий и его сплавы в расплаве весьма жидкотеку чи, а при остывании имеют большой коэффициент усад ки и высокий коэффициент линейного расширения;
3)при температуре 400-500 °С алюминиевые сплавы при обретают повышенную хрупкость, что способствует об разованию при сварке трещин;
4)алюминиевые сплавы обладают значительной раствори
мостью в расплавленном металле водорода, что способ ствует образованию пористого шва.
Детали из алюминиевых сплавов соединяют газовой или дуговой сваркой.
При газовой сварке в качестве горючего используют аце тилен. Сварку выполняют нейтральным пламенем. Приса дочный материал должен быть того же состава, что и ос новной металл. Для защиты металла от окисления приме няют флюс АФ-4А, способствующий удалению окислов. В состав флюса входят (в %): хлористый натрий — 28, хло ристый калий — 50, хлористый литий — 14 и фтористый натрий — 8.
При дуговой сварке чаще всего используют электроды ОЗА-2. Сварку ведут на постоянном токе при обратной полярности. Стержень электрода изготовляют из алюминиевой проволоки. Электрод имеет покрытие толщиной 0,6-0,8 мм следующего состава (в %): флюс АФ-4А65; криолит —25; хлористый ка лий — 9; губчатый титан — 1 и связующий раствор карбоксиметилцеллюлозы — 12-14 (к сумме компонентов). Режим свар ки: при толщине стенки детали 4-9 мм диаметр электрода берут 5 мм, длину дуги принимают 4-5 мм; при толщине стенки 4-6 мм сила тока 140-70 А; при толщине стенки 7-9 мм сила тока 160-210 А.
Другим способом дуговой сварки является сварка неплавящимся вольфрамовым электродом в среде защитного газа (аргона) на установках типа УДАР, УДГ. Присадочным ма териалом является проволока того же состава, что и основ ной металл. Сварку этим способом ведут на переменном токе без применения флюса, так как аргон хорошо защищает рас плав алюминия от окисления; шов получается прочным, без пор и оксидов. При всех способах соединения деталь перед сваркой необходимо подвергнуть местному или общему на греву до температуры 200-250 °С, что предотвратит коробле ние детали и образование трещин, а также улучшит крис таллизацию расплавленного металла. После сварки деталь подвергают термообработке при температуре 300-350 °С с последующим медленным охлаждением, что обеспечит сня тие внутренних напряжений в зоне сварки.
3.4.2 Присадочные материалы
Присадочные материалы служат для компенсации угара металла и заполнения зазора или канавки между сваривае мыми элементами. Они подбираются так, чтобы образующий ся при сварке сплав обеспечивал высокое качество шва. Для этого составы присадочной проволоки и свариваемого мате риала должны соответствовать друг другу. В состав приса дочной проволоки могут вводиться элементы имеющие мень шее сродство с кислородом, чем основа сплава, если они ока зывают благоприятные влияние на свариваемый материал.
Чтобы получить высококачественный шов, при выборе присадочной поволоки следует учитывать следующие реко мендации. В процессе сварки материал проволоки должен увеличивать количество элементов интенсивно выгорающих при сварке; вводить элементы, более активно соединяющие ся с кислородом по сравнению с основой и легирующими компонентами сплава; вводить элементы менее активные к кислороду, чем основа сплава и в тоже время благоприятно влияющие на свариваемый металл; уменьшать количество
элементов, оказывающих вредное воздействие на шов. При садочные проволоки, применяемые при сварке имеют 77 ма рок диаметром от 0,3 до 12 мм. Часть из них приведена в таблице 3.3. Марка проволоки содержит буквы Св (свароч ная) и далее через дефис — типовое обозначение использо ванный для её изготовление стали. Например: Св-08А, Св-08Г2С, Св-ЗОХГСА. В ГОСТ 10543—82 указанны 30 марок проволок диаметром от 0,3 до 8,0 мм, применяемых для на плавки, из которых 9 применяются для углеродистых ста лей, 11 — для легированных. Наплавочная проволока обо значается символом Нп (таблица 3.4).
Таблица 3.3
Присадочные проволоки для сварки сталей
Марка |
|
Содержание элементов, |
% (по массе) |
Р |
||||
|
|
|
|
|
S |
|||
проволоки |
с |
Мп |
Si |
Сг |
Ni |
|||
Не более |
||||||||
1 |
2 |
|
|
5 |
|
|||
3 |
4 |
6 |
7 |
8 |
||||
|
|
Углеродистые стали |
|
0,04 |
0,04 |
|||
Св-08 |
0,10 |
0,35... |
0,03 |
0,15 |
0,30 |
|||
Св-ОВА |
0,10 |
0,60 |
0,03 |
0,10 |
0,25 |
0,03 |
0,03 |
|
0,35... |
||||||||
|
|
0,60 |
|
|
|
|
|
|
СВ-08ГА |
0,10 |
0,80... |
0,03 |
0,10 |
0,25 |
0,03 |
0,03 |
|
Св-ЮГА |
0,12 |
1,10 |
|
0,20 |
|
0,03 |
|
|
1,10... |
0,03 |
0,30 |
0,03 |
|||||
|
|
1,40 |
|
|
|
|
|
|
Св-10Г2 |
0,12 |
1,50... |
0,03 |
0,20 |
0,30 |
0,04 |
0,03 |
|
|
|
1,90 |
|
|
|
|
|
|
|
|
Легированные стали |
|
|
|
|||
Св-08ГС |
0,10 |
1,40... |
0,60.:. |
0,20 |
0,25 |
0,03 |
0,03 |
|
|
|
1,70 |
0,85 |
|
(Al-0,05) |
|
|
|
Св-08Г2С |
0,11 |
1,80... |
0,70... |
0,20 |
0,25 |
0,03 |
0,03 |
|
|
0,14 |
2,10 |
0,95 |
0,20 |
(А 1-0,05) |
|
|
|
Св-12ГС |
0,80... |
0,60... |
0,30 |
0,03 |
0,03 |
|||
СВ-10ХГ2С 0,06... |
1,10 |
0,90 |
0,70... |
0,25 |
0,03 |
0,03 |
||
1,70... |
0,70... |
|||||||
|
0,12 |
2,10 |
0,95 |
1,10 |
|
|
|