
книги / Ремонт подъемных кранов
..pdf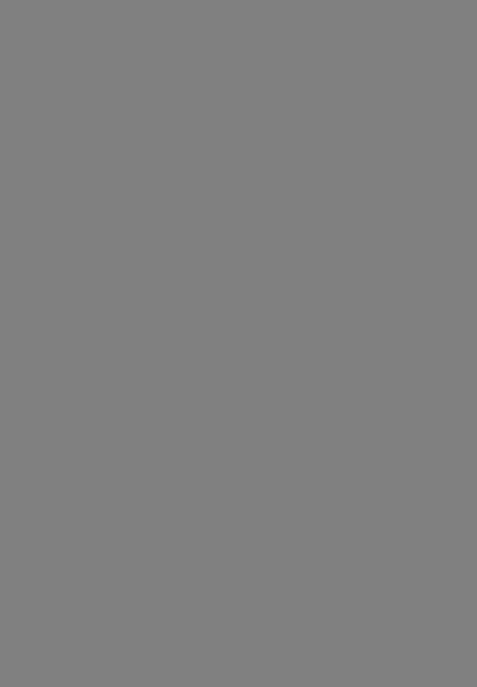
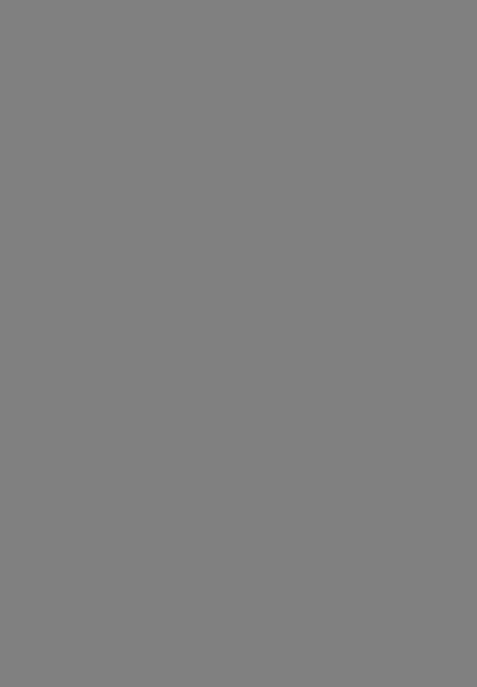
ляются электромагнит ным вибратором 7. Ос тальные элементы схемы следующие: 3 — канал для подачи охлаждающей жидкости; 9 — катушка самоиндукции; 1 0 — на сос. За один цикл вибра ции в 0,01 с электрод сна чала контактирует с по верхностью детали (ко роткое замыкание), а за тем, в момент отхода от неё, размыкает цепь.
В период отхода элект рода от поверхности воз никает дуговой разряд с выделением основного ко личества тепла(80-90 %) и материал электрода в
мелкокапельном состоянии попадает на наплавляемую по верхность. Вибрация электрода с амплитудой 1,5-2,5 мм со здаёт стабильность процесса наплавки и способствует равно мерному наложению наплавочного материала. Наплавку де талей лучше вести на постоянном токе обратной полярности. При работе на переменном токе возможны пропуски в на плавленном слое.
В ремонтной практике используют наплавочные головки с электромагнитным вибратором (УАНЖ-5, УАНЯС-6, ВДГ-5
идругие) и головки с магнитным вибратором (ОКС-1252А, КУМА-5М). Источником тока служат низковольтные генера торы. Применяют также выпрямители ВСА-600/300, ВСТ-ЗМ
идр. Диаметр электродной проволоки принимают от 1,2 до 2,5 мм в зависимости от требуемой толщины наплавленного слоя. Сила сварочного тока зависит от диаметра проволоки и скорости её подачи и составляет от 100 до 200 А. Напряже
ние на дуге колеблется в пределах 12-24 В. Скорость подачи электродной проволоки принимают в пределах 0,5-3,5 м/мин. С ростом скорости подачи проволоки сокращается время го рения дуги, что уменьшает выгорание углерода, но способ ствует образованию пор.
Вибродуговую наплавку выполняют с применением охлаж дающей жидкости, без охлаждения в среде защитных газов и под слоем флюса. Наплавка с применением охлаждающей жидкости (5% -ный раствор каустической соды) получила наи большее распространение. При подводе охлаждающей жидко сти непосредственно в зону наплавки значительно повышает ся твёрдость наплавленного слоя и его износостойкость, но снижается усталостная прочность детали на 30-40 % в связи с образованием микротрещин и пористости слоя. При подводе жидкости на некотором расстоянии от зоны наплавки устало стная прочность детали повышается, но снижается твёрдость и износостойкость наплавленного слоя.
При наплавке без охлаждения или в среде защитных га зов твёрдость наплавленного слоя в зависимости от марки электродной проволоки составляет 160-450 НВ, но наплав ленный слой имеет большую усталостную прочность.
При наплавке под слоем флюса получают покрытие наи лучшего качества.
Вибродуговая наплавка имеет следующие достоинства: не значительная зона термического воздействия, не оказываю щая влияния на деформацию детали и на её состояние, доста точно высокая производительность (8-10 см2 поверхности по крытия в 1 мин.). Недостатком способа является снижение усталостной прочности детали после наплавки на 30-40 % .
Вибродуговая наплавка получила распространение при вос становлении деталей из стали, серого и ковкого чугуна (шеек валов, шлицев, резьбовых поверхностей деталей), не испы тывающих значительную динамическую нагрузку.
Наплавка в среде защитных газов. Сущность способа зак лючается в том, что электрическая дуга горит между элект родом и наплавляемой деталью в струе газа, вытесняющего
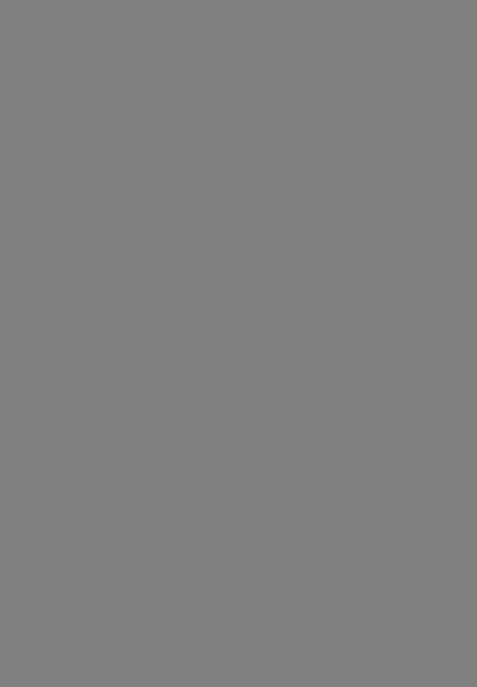
Оксиды Si02 и МпО образуют лекгоплавкие шлаки, всплы вающие на поверхность сварочной ванны.
Следует также иметь в виду роль кремния и марганца в предотвращении образования в металле пор. Будучи актив ными раскислителями, кремний и марганец предотвращают раскисление FeO углеродом, при котором бурно выделяется
окись углерода по реакции |
|
FeO + С -> Fe + СО. |
(3.20) |
Указанная реакция раскисления FeO подавляется крем нием и марганцем и процесс кристаллизации протекает спо койнее, без образовании пор.
Для автоматической наплавки используют обычно авто маты А-580М с установкой мундштука с горелкой для пода чи диоксида углерода, для полуавтоматической наплавки — полуавтоматы Л-547Р, ПДГ-301 и др. Источниками тока слу жат сварочные преобразователи ПСГ-500-1, ПСУ-500 и сва рочные выпрямители ВС-300, НДГ-301 и др.
Сварку и наплавку выполняют электродной проволо кой диаметром от 0,8 до 2,5 мм. Например, при наплавке цилиндрических деталей диаметром от 10 до 40 мм при меняют проволоку диаметром от 0,8 до 1 мм марки Нп-ЗОХГСА. Сила сварочного тока 75 А при диаметре де тали 10 мм и 130-160 А — при диаметре детали 40 мм. Напряжение на дуге 18-20 В. Толщина наплавленного слоя составляет 0,8 -1 мм, твердость 24-35 HRC#. После закал ки твёрдость повышается до 50 HRC9.
Наплавка деталей в среде углекислого газа по сравнению с наплавкой под слоем флюса имеет следующие преимуще ства: возможность наплавки шеек валов диаметром от 10 мм и выше; более высокая (на 20—30 % ) производительность процесса; меньший нагрев детали; отсутствие необходимости очистки наплавленного слоя от шлаковой корки. Недостат ком процесса является склонность наплавленного слоя к об разованию трещин и значительное разбрызгивание металла.
Наплавка порошковой проволокой. Порошковая проволо ка представляет собой свёрнутую из стальной ленты трубку
диаметром 2-3 мм, заполненную шихтой в виде механичес кой смеси легирующих (ферросплавы, углерод, различные металлы), защитных (мрамор, плавиковый шпат и др.) ком понентов, железного порошка, а также веществ, стабилизи рующих горение дуги.
Наплавка возможна открытой дугой, в среде углекислого газа, под слоем флюса, на установке для вибродуговой на плавки или вручную. При наплавке под слоем флюса или в среде углекислого газа шихта составляется в основном из легирующих элементов. Порошковые проволоки выпускают различных марок для автоматической и полуавтоматической наплавки и сварки низко- и среднеуглеродистых сталей (ПП-АН1, ПП-АНЗ и др.). При наплавке порошковой прово локой получают износостойкий наплавленный металл твёр достью 40-55 HRC. Наплавку обычно ведут на постоянном токе обратной полярности.
Преимущества процесса — простота его выполнения, так как не требуется наличие флюсов или защитных газов, возможность получения износостойкого наплавленного ме талла и относительно высокий коэффициент наплавки — 12-20 кг/(А-ч). Недостатки — значительная стоимость про волоки, получение наплавленного металла с неравномер ной структурой и с повышенной пористостью.
При наплавке поверхностей значительной ширины и ци линдрических поверхностей больших диаметров вместо по рошковой проволоки эффективнее применять порошковую ленту шириной от 20 до 100 мм.
Электроконтактная наплавка. Сущность способа заклю чается в навивке на поверхность восстанавливаемой детали проволоки, которая приваривается электроконтактным спо собом импульсами тока большой силы при одновременном деформировании проволоки до требуемой толщины слоя по крытия. На рисунке 3.20 показана схема электроконтактной наплавки. Деталь 2 устанавливают в центрах или в патроне токарного станка; контактный ролик 1 и наплавочный ро лик 4 смонтированы на суппорте токарного станка. В про-
Рис. 3.20 Схема электроконтактной наплавки
цессе наплавки ролик 4 с помощью прижимного механизма деформирует навиваемую проволоку 3 до слоя необходимой толщины. В качестве источника питания используют свароч ный трансформатор. Ток с ролика подаётся от вторичного контура 5 трансформатора. В первичный контур 6 вмонтиро ван прерыватель 7, обеспечивающий подачу тока импульса ми. Во вторичном контуре протекает ток силой до 20 000 А при напряжении до 7 В. Толщина наплавленного слоя может быть в пределах 0,2-1,5 мм при диаметре электродной про волоки соответственно 0,5-2 мм.
Электродную проволоку применяют марон Нп-40, Нп-50, Нп-ЗОХГСА и т.д. в зависимости от требуемого свойства на плавленного металла. Силу Р (в Н) прижатия наплавочного ролика определяют по формуле Р = 100d2, где d — диаметр проволоки, мм.
Электроконтактный способ наплавки является весьма пер спективным. Он обладает следующими достоинствами: высо кая производительность, достигающая 100 сМ2/мин. при тол щине покрытия 1 мм; незначительная зона термического влияния (до 0,3 мм); незначительные потери присадочного материала; благоприятные производственные условия для работы сварщиков.
Износостойкость покрытий, полученных наплавкой раз личными электродами. Износостойкость наплавленного слоя в значительной степени зависит от химического состава элек тродной проволоки. Для иллюстрации влияния химического состава электродной проволоки на рисунок 3.21 представле ны результаты исследования сравнительной износостойкос ти покрытий, полученных наплавкой в среде углекислого газа. Исследовалась степень износа по сравнению с эталоном (стать 45, закалённая) в условиях граничного трения сколь жения при удельном давлении 4 МПа и наплавке различной электродной проволокой: 1 — проволокой Св.-08Г2С; 2 — про волокой Нп-ЗОХГСА; 3 — проволокой Нп-ЗОХГСА с последу ющей закалкой токами высокой частоты; 4 — проволокой 2X13; 5 — сталью 45, закалённой токами высокой частоты до твёрдости 56-62 HRC.
Особенности механической обработки деталей после на плавки. Эти особенности заключаются в наличии неравно мерных припусков, включений шлака, неоднородности свойств наплавленного металла. В зависимости от твёрдости наплавленного слоя и требований к качеству поверхности применяют обработку на токарных и шлифовальных стан ках. При твёрдости наплавленного слоя не свыше 40 HRC возможна токарная обработка резцами с пластинками из спла ва ВК6. Еслй твёрдость наплавленного слоя превышает 40 HRC, то вместо токарной возможна анодно-механическая обработка.
3.4.4 Электроды для дуговой сварки
Электрод дДЯ дуговой сварки представляет собой металли ческий стержень, имеющий покрытие из специальной обмаз ки. Стержень электрода изготовляется из сварочной прово локи и служи? присадочным материалом. При сварке элект родом благодаря покрытию образуется шлак, оказывающий влияние на качество сварного соединения, технологические характеристики и химический состав металла шва. Шлак
2,2 |
6,6 |
11 |
IS |
19 |
24,2 |
Число оборотовролика, тыс.
Рис. 3.21 Износостойкость покрытий, полученных наплавок различными способами
должен полностью изолировать сварочную ванну, хорошо пропускать газы, выделяющиеся из сварочной ванны при кристаллизации металла. Важным требованием к покрытию является возможность выполнения сварки во всех простран ственных положениях, зависящая от вязкости жидкого шла ка. Шлаки с большим содержанием кремнезёма малоподвиж ны, и их вязкость заметно отличается от вязкости фтористо кальциевых шлаков, содержащих небольшое количество кремнезёма. Важное значение имеет также основность шла ка, мерой которой служит концентрация свободных ионов кислорода в шлаке и способность компонентов шлака увели чивать концентрацию ионов кислорода в шлаке путём разру шения кремнекислородных комплексных соединений. Металл шва, полученный сваркой электродом с основным покрыти ем, обладает большой пластичностью.
Покрытия электродов имеют обозначения: А — кислые, Б — основные, Р — рутиловые, Ц — целлулоидные, П — прочие. В кислых покрытиях преобладают окислы железа, марганца, кремнезем, в основных — мрамор, плавиковый шпат, ферросплавы. Тип электрода обозначается символом Э с указанием прочности металла стержня.