
книги / Машины и оборудование нефтяных и газовых промыслов. Силовые приводы машин и оборудования нефтяных и газовых промыслов
.pdfБуровые насосы должны обеспечивать достаточную равномерность подачи, быть безопасными в эксплуатации, удобными в обслуживании и ремонте в полевых условиях. Буровой насос — обычно самый тяжелый агрегат буровой установки. Масса современных наиболее мощных насосов достигает 50 т, поэтому его конструкция должна допускать транспортировку как при помощи транспортных средств, так и волоком в пределах промысла. Для этого насосы должны иметь жесткую раму-салазки.
Исходя из назначения и условий эксплуатации, к буровым насосам предъявляют следующие основные требования:
–подача насоса должна быть регулируемой в пределах, обеспечивающих эффективную промывку скважины;
–мощность насоса должна быть достаточной для промывки скважины и привода забойных гидравлических двигателей;
–скорость промывочной жидкости на выходе из насоса должна быть равномерной для устранения инерционных нагрузок и пульсаций давления, вызывающих осложнения
вбурении, дополнительные энергетические затраты и усталостные разрушения;
–насосы должны быть приспособлены для работы с абразиво- и маслосодержащими коррозионно-активными промывочными растворами различной плотности;
–узлы и детали, контактирующие с промывочным раствором, должны обладать достаточной долговечностью и быть приспособленными к удобной и быстрой замене при выходе из строя;
–крупногабаритные узлы и детали должны быть снабжены устройствами для надежного захвата и перемещения при ремонте и техническом обслуживании;
–узлы и детали приводной части должны быть защищены от промывочного раствора и доступны для осмотра и технического обслуживания;
–насосы должны быть приспособлены к транспортировке в собранном виде на далекие и близкие расстояния и перемещению волоком в пределах буровой;
–конструкция насосов должна допускать правое и левое расположение двигателей насосного агрегата;
–надежность и долговечность насосов должны сочетаться с их экономичностью и безопасностью эксплуатации.
Требованиям технологии промывки скважин удовлетворяют только поршневые (плунжерные) насосы. Попытки применять насосы других типов до сих пор успеха не имели. Рабочие органы буровых насосов преимущественно выполняются в виде поршней или в виде плунжеров. Наиболее распространены трехпоршневые насосы (триплексы) одностороннего действия, которые пришли на смену двухпоршневым насосам двустороннего действия. В насосах двустороннего действия жидкость перемещается в поршневой и штоковой полостях и за один двойной ход поршня совершаются два цикла всасывания и нагнетания. При одностороннем действии жидкость перемещается в поршневой полости рабочей камеры и за один двойной ход совершается один цикл всасывания и нагнетания.
Для снижения неравномерности подачи предпринимались попытки создания многоцилиндровых буровых насосов. Однако такие насосы не получили распространения из-за повышенных сложности изготовления и трудоемкости обслуживания при замене быстроизнашивающихся деталей. Тем не менее существуют четырехцилиндровые буровые насосы. Одновременно были созданы надежные и простые компенсаторы неравномерности подачи, которые позволяют успешно эксплуатировать двухцилиндровые и трехцилиндровые буровые насосы.
При конструировании буровых насосов важнейшее значение имеет показатель расхода металла на 1 кВт гидравлической (полезной) мощности. Этот показатель для двухцилиндровых насосов двойного действия составляет 35–55 кг/кВт. Обычно под буровые насосы не сооружают мощных фундаментов, поэтому для предупреждения
91
больших вибраций |
с увеличением мощности растет и общая |
масса насоса. |
|
У трехцилиндровых |
насосов одностороннего действия, наряду |
с другими |
их |
преимуществами, металлоемкость значительно ниже и составляет 22–35 кг на 1 |
кВт |
гидравлической мощности. Причем с ростом мощности насоса относительный расход металла снижается.
5.2. Основные параметры и общая характеристика насосов
Основные параметры насоса: мощность, напор и подача. Современные буровые насосы образуют группу гидравлических машин узкопрофильного назначения с параметрами, удовлетворяющими требованиям технологии бурения различных по глубине и конструкции нефтяных и газовых скважин. Обычно нефтегазовые скважины имеют ступенчатую конструкцию. С переходом к бурению другой ступени необходимо уменьшать подачу бурового раствора и увеличивать давление нагнетания для обеспечения интенсивной промывки забоя. Любой типоразмер поршневого насоса с изменяющимися подачей и напором удобно характеризовать величиной гидравлической мощности, которая определяется как произведение подачи и давления нагнетания. Величина необходимой подачи определяется требуемой скоростью восходящего потока бурового раствора в затрубном пространстве скважины. Необходимый напор должен несколько превышать суммарные гидравлические потери в напорных трубопроводах, бурильной колонне и в затрубном пространстве, т.е. гидравлической энергии должно быть достаточно для перекачки раствора через скважину и его перелива в желобную систему. Зная величину необходимой подачи, в каждом отдельном случае легко вычислить максимальный допустимый напор для данного насоса.
Мощность на трансмиссионном валу насоса, или приводная мощность – это согласно ГОСТ 6031–81 основной параметр насоса, который выражается в кВт и введен
вшифр насоса, например УНБ-1250. Гидравлическая (полезная) мощность насоса меньше па величину потерь энергии внутри его, которые характеризуются величиной КПД насоса.
Подача насоса – количество жидкости, перекачиваемой в единицу времени. Чаще всего подача буровых насосов выражается в л/с. Подача насосов может изменяться в широких пределах – от 7 до 60 л/с. Подача насоса регулируется изменением рабочего объема насоса путем замены цилиндровых втулок и поршней. Внешний диаметр втулок всегда одинаковый, а внутренний диаметр и, соответственно, диаметр поршня могут меняться, таких комплектов для одного насоса может быть от трех до семи. Также подача насоса может регулироваться изменением числа ходов поршня насоса в единицу времени, что реализуется изменением частоты вращения трансмиссионного вала.
Напор, или давление в нагнетательной линии насоса – потенциальная энергия, сообщаемая насосом перекачиваемой жидкости. Напор принято обозначать в м столба жидкости, давление в МПа. Важнейший параметр насоса – максимальное давление, которое в современных конструкциях буровых насосов уже достигло 53 МПа и, повидимому, будет возрастать в будущем. Чем больше давление бурового раствора, тем больше гидравлической энергии можно подвести к долоту и обеспечить его гидромониторный эффект. Рост глубин и протяженности бурящихся скважин также требует увеличения давления в нагнетательной линии насосов.
Кроме приведенных основных параметров, буровые насосы характеризуются другими, большей частью конструктивными, параметрами.
Горизонтальный приводной поршневой насос двойного действия (рис. 5.1) состоит из гидравлической и приводной частей. В гидравлическую часть входят цилиндр с поршнем 3, два всасывающих 2, 8 и два нагнетательных 4, 7 клапана. Клапаны устроены так, что пропускают жидкость только в одном направлении. При перемещении поршня
вобратном направлении соответствующие клапаны закрываются. К полости всасывающих клапанов подсоединен всасывающий трубопровод 1. Над
92
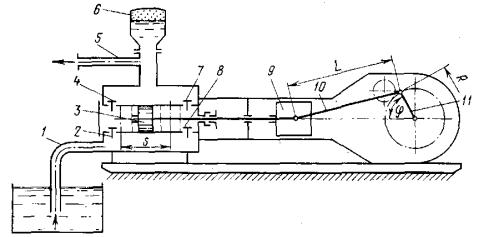
нагнетательными клапанами расположена напорная камера с компенсатором неравномерности подачи 6, откуда жидкость поступает в трубопровод 5.
При движении поршня от всасывающего клапана 2 в левой части цилиндра создается разрежение. Под действием разности значений давления в цилиндре и всасывающем трубопроводе 1 открывается клапан 2, и жидкость поступает в цилиндр. Нагнетательный клапан 4 в это время закрыт. Так происходит цикл всасывания насоса. Одновременно в правой части цилиндровой втулки движущийся поршень повышает давление жидкости, в результате чего закрывается всасывающий клапан 8 и открывается нагнетательный клапан 7. Жидкость выталкивается в нагнетательную полость насоса. Поршень перемещается в цилиндровой втулке на длину хода S . За один ход поршня происходит одновременно цикл всасывания и нагнетания. При обратном движении поршня камера всасывания и нагнетания меняются местами.
Приводная часть насоса представляет собой кривошипно-шатунный механизм, состоящий из кривошипа 11, шатуна 10 и ползуна 9. Поршень штоком соединен с ползуном. За один полный оборот кривошипа поршень совершает один двойной ход.
Рис. 5.1. Схема приводного поршневого насоса двойного действия
Поршни буровых насосов бывают в виде диска или плунжера. Дисковыми считаются поршни, длина которых меньше диаметра. Эти поршни имеют самоуплотняющиеся манжеты. Плунжерные поршни уплотняются внешними сальниковыми устройствами. По виду поршня насосы принято называть поршневыми или плунжерными. У поршневых насосов за один оборот кривошипа жидкость может всасываться и нагнетаться дважды. Эти насосы называют насосами двойного действия. Плунжерные насосы — насосы простого действия.
В буровых насосах используются самодействующие пружинные клапаны тарельчатой конструкции. Всасывающие и нагнетательные клапаны взаимозаменяемы. Оси поршней параллельны и располагаются в горизонтальной плоскости по одну сторону от привода насоса. Ведущее звено буровых насосов, сообщающее движение поршням, выполняется в виде вращающегося эксцентрикового, кривошипного, пальцевого либо коленчатого вала.
Коренной вал (ведущий) приводится от трансмиссионного вала насоса посредством цилиндрической зубчатой пары. В буровых насосных агрегатах используются преимущественно электродвигатели и дизели, вращение которых передается трансмиссионному валу насоса клиноременной передачей. В зависимости от частоты вращения коренного вала насосы подразделяют на тихоходные (n = 40…50 об/мин), средней быстроходности (n = 80…150 об/мин) и быстроходные (n > 50 об/мин). Трехпоршневые насосы одностороннего действия более быстроходные, чем двухцилиндровые двойного действия.
93
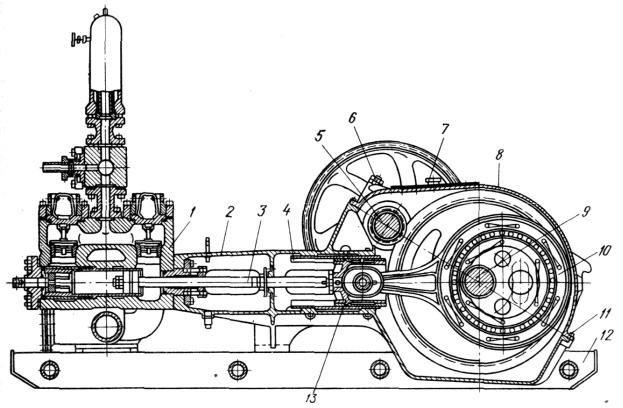
5.3.Конструкции буровых насосов
Внастоящее время буровые установки комплектуются насосами двух типов: двухцилиндровыми двойного действия или трехцилиндровыми простого (одностороннего) действия. Однотипные насосы не имеют различий в принципиальных схемах. Они отличаются параметрами технической характеристики и конструктивным исполнением отдельных узлов.
Все буровые насосы имеют гидравлическую и приводную части, смонтированные на общей раме-салазках. Гидравлическая часть поршневого насоса состоит из литой или
кованой гидрокоробки с двумя или тремя параллельно расположенными в горизонтальной плоскости цилиндрами, в которых установлены втулки с поршнями. Двухцилиндровые насосы двойного действия имеют четыре всасывающих и четыре нагнетательных клапанных узла. В трехцилиндровых насосах одностороннего действия установлены три всасывающих и три нагнетательных клапана. В каждом насосе имеется одна приемная (всасывающая) коробка и один нагнетательный тройник. Гидравлическая и приводная части обычно соединяются шпильками.
Различие насосов состоит в размерах и конфигурации клапанных коробок, способах их расположения, конструкции клапанных крышек, конструкции цилиндровых крышек, способах крепления цилиндровых втулок и т.д. Клапаны и гнезда различных насосов также имеют конструктивные отличия.
Буровой насос (рис. 5.2) состоит из приводного и гидравлического блоков, установленных на сварной раме 12.
Рис. 5.2. Буровой насос двустороннего действия
Приводная часть бурового насоса выполняет функции преобразования вращательного движения ведущего шкива в возвратно-поступательное крейцкопфов и передачи поршням энергии, получаемой от силового привода. Кроме того, трансмиссия насоса снижает частоту вращения коренного вала. Приводная часть насоса состоит из литой или сварной станины, в которой смонтированы трансмиссионный вал с одной или
94
двумя шестернями и приводным шкивом, коренной вал в сборе с одним или двумя зубчатыми колесами, шатуны и крейцкопфы с контрштоками.
Приводной блок состоит из трансмиссионного вала 5, коренного вала 9 и шатунного механизма 10, установленных на станине 2. Последняя представляет собой массивный металлический короб, в расточках которого монтируются подшипники трансмиссионного и коренного валов. Для удобства монтажа внутренних узлов и деталей станина имеет крышку 8. Стыкуемые поверхности станины и крышки подвергаются механической обработке и уплотняются при помощи резинового шнура либо прокладки, затягиваемой болтами 11 и ввернутыми в станину шпильками 6. Положение крышки относительно станины фиксируется коническими штифтами.
Отверстия под подшипники растачивают в сборе станины с крышкой. В горловине станины устанавливают направляющие 4 ползуна 13. Оси поверхностей расточек станины под направляющие ползуна должны совпадать с отклонением не более 0,15 мм. Внутренняя полость станины окрашивается маслостойкой краской и используется в качестве резервуара для масла, смазывающего зубчатую передачу, установленную между трансмиссионным и коренным валами. Горловина станины имеет боковые люки для монтажа и осмотра ползунов. Торец горловины снабжается отверстиями для штока 3 и крепления гидравлического блока 1.
Станины буровых насосов отливают из высокопрочных чугунов или сталей. Для насосов большой мощности изготовляют сварные или литосварные станины, имеющие меньшую массу по сравнению с литыми. Внутренняя полость станины используется как масляная ванна вместимостью 0,3 л на 1 кВт приводной мощности. Она плотно закрывается крышкой, в верхней части которой установлен сапун 7 для вытяжки масляных паров. Ванна имеет указатель уровня масла, заправочную горловину и сливное отверстие. Для изоляции приводной части от гидравлической в разделяющей стенке монтируется сальник контрштока.
Передачи предназначены для снижения частоты вращения коренного вала в 10– 20 раз. Первичные двигатели привода буровых насосов обычно имеют частоту вращения 700–1500 об/мин. Передача бывает двухступенчатой. Обычно между двигателем и трансмиссионным валом насоса имеется клиноременная передача с передаточным числом 2,0–3,5. Применяют от 9 до 20 клиновых ремней типа Д или Г. Шкивы для клиноременной передачи изготовляют из чугунного литья и сажают на консоли трансмиссионного вала по цилиндрической или конической поверхности на шпонке. Для снижения габаритов этой ступени передачи были попытки использования многорядных цепных передач, но они оказались безуспешными вследствие низкой долговечности цепей.
Вторая ступень – это зубчатая передача между трансмиссионным и коренным валами. Ее передаточное число 4–5, и она снижает частоту вращения коренного вала с
250–600 до 60–135 об/мин.
Трансмиссионный вал (рис. 5.3) служит для передачи крутящего момента коренному валу насоса и выполнен в виде выводного вала-шестерни 8, концы которого используются для установки клиноременного шкива или цепного колеса в зависимости от принятой в приводе насоса передачи. Шкив и цепное колесо крепятся на валу шпонкой 12. Для облегчения сборки и разборки шкивы имеют разрезную ступицу, затягиваемую болтами. Поскольку возможны перекосы в результате прогиба под действием нагрузки на консоли, а также вследствие технологических неточностей, трансмиссионный вал устанавливается на сферических двухрядных роликоподшипниках 6, воспринимающих радиальные и осевую нагрузки от косозубой передачи.
Для предупреждения смятия и разбивания опорных поверхностей станины, а также устранения брака дорогостоящей станины из-за расслабления отверстий при растачивании подшипники устанавливают на стальных гильзах 7, наружный диаметр которых больше диаметра шестерни. Благодаря этому при сборке насоса вал 8 свободно
95
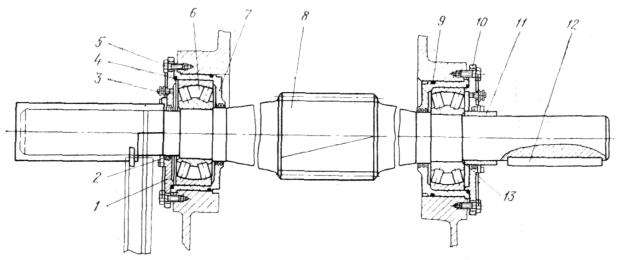
протаскивается через отверстия станины. Соосность наружной и внутренней поверхностей гильз обеспечивается жесткими допусками на их разностенность.
Гильзы имеют фланец небольшой высоты и притягиваются к станине сквозными крышками 1 и 10, закрепленными болтами 5. Благодаря затяжке болтами гильзы фиксируются в осевом направлении и предохраняются от проворачивания. Подшипники торцами внутренних колец упираются в буртики вала. Правый подшипник фиксируется в гильзе крышкой 10. Второй подшипник вала плавает в гильзе по наружной обойме.
Рис. 5.3. Трансмиссионный вал
Подшипники смазывают ручным насосом через пружинные тавотницы 3. Неподвижные стыки гильзы со станиной и крышкой уплотняются резиновыми кольцами 4, 9 и 13. Подвижный внутренний стык между гильзой и валом герметизируется бесконтактным щелевым уплотнением, выполненным в виде кольцевых канавок в гильзе. Между крышками и валом устанавливают контактные севанитовые уплотнения 2 и втулку 11.
Эксцентриковый коренной вал (рис. 5.4) имеет сборную конструкцию. Использование эксцентриков на коренном валу вместо кривошипов уменьшает ширину и массу насоса. При такой конструкции уменьшается длина трансмиссионного вала и даже трехцилиндровые насосы можно устанавливать на двух подшипниковых опорах. В результате усовершенствования конструкции приводной части масса и габариты двухцилиндровых насосов двойного действия мощностью 800–1200 кВт несколько меньше, чем насосов старых конструкций.
Прямой вал 15 с жестко закрепленными эксцентриками 9 опирается на коренные подшипники 6, расположенные в станине бурового насоса. Эксцентрики, выполняющие роль шатунных шеек, отливаются из углеродистой стали и соединяются сваркой. Число эксцентриков равно числу поршней бурового насоса. Угловое смещение шатунных шеек коренного вала определяется требованиями равномерной подачи. Согласно этому в двухпоршневых насосах двустороннего действия угловое смещение эксцентриков составляет 90°, а в трехпоршневых насосах одностороннего действия – 120°. Между эксцентриками располагается зубчатое колесо 8.
Составная конструкция коренного вала удобна в технологическом отношении, так как позволяет упростить форму заготовок и облегчить их механическую обработку. Окончательная обработка наружных поверхностей коренного вала и нарезка зубьев производятся после посадки эксцентриков на прямой вал и соединения венца зубчатого колеса с его ободом.
96
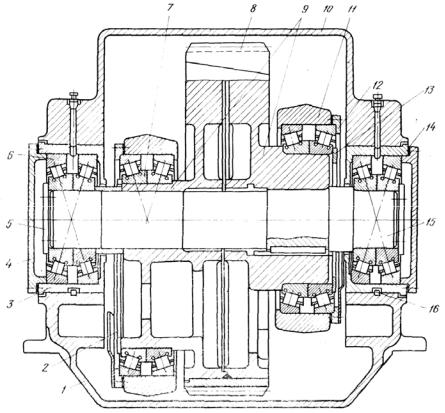
Рис. 5.4. Коренной вал
Для точной осевой фиксации зубчатого колеса коренной вал опирается на спаренные радиально-упорные конические подшипники 6, посаженные в переходные гильзы 3, установленные в расточки станины 1 и крышки 10 насоса. Наружные кольца подшипников удерживаются от продольного перемещения крышками 4, которые крепятся болтами к торцам гильз. Затяжка наружных колец подшипников регулируется мерными прокладками 14, установленными между крышкой 4 и торцом гильзы 3. Внутренние кольца подшипников затягиваются шайбами 5, крепящимися болтами к торцам вала. Осевое положение коренного вала фиксируется в нужном положении благодаря наружным кольцевым буртикам гильзы, упирающимся в торец расточек станины и крышки насоса.
Гильзы удерживаются от проворота с помощью дюбелей 16. Коренные подшипники смазывают ручным насосом через тавотницы, ввернутые в крышку станины. Эксцентриковые коренные валы преимущественно применяются в современных двух- и трехпоршневых буровых насосах. Коренные валы пальцевой конструкции используются реже, например в буровом насосе БрН-1. Буровые насосы У8-3 и У8-4 с кривошипным валом сняты с производства.
Кольца роликовых подшипников 7 удерживаются от осевого перемещения кольцевыми шайбами 12 и 13 и буртиками вала и шатуна. Кольцевые шайбы крепятся к торцам эксцентрика болтами. Натяг подшипников регулируется прокладками, установленными между торцом шейки шатуна и шайбой 12. Разбрызгиватели 2 отбрасывают масло на подшипники мотылевых шеек шатуна при их погружении в масляную ванну.
В современных конструкциях буровых насосов для передачи вращения от трансмиссионного вала коренному обычно применяется одна косозубая или шевронная передача. Это уменьшает ширину и массу насоса. Косозубые зубчатые передачи, по сравнению с прямозубой передачей, обладают большей нагрузочной способностью и плавностью зацепления, обусловливающей снижение уровня динамических нагрузок и
97
шума при работе. Направление зуба шестерни принимается левым, а для колеса – правым. Недостаток косозубых передач, по сравнению с прямозубыми, заключается в том, что в зацеплении возникает дополнительная осевая сила. Шевронные зубчатые колеса, представляющие разновидность косозубых колес, не создают осевых нагрузок, однако в буровых насосах применяются реже из-за сложности изготовления.
Шестерни изготовляют из сталей марок 34ХН1М, 35ХНВ и 38ХГН в паре с венцом зубчатых колес соответственно из сталей марок 38ХГН, 35Х и 35Л. Для увеличения долговечности и улучшения прирабатываемости зубьям шестерни придается большая твердость, чем зубьям колеса.
Зубчатое зацепление подвергается односторонней обкатке в направлении рабочего вращения, указанном стрелкой на станине насоса. Направление вращения можно изменить после предварительной обкатки зубчатых колес в обратную сторону.
Вбольшинстве конструкций буровых насосов угол наклона косозубых колес составляет 6°–9°. Зубчатую пару смазывают жидким маслом путем окунания ее в масляную ванну либо с помощью масляного насоса. Важно отметить, что косозубые колеса с твердыми поверхностями зубьев требуют повышенной защиты от загрязнения во избежание неравномерного износа по длине контактных линий и выкрашивания наружных слоев зубьев.
Шатун передает движение от коренного вала ползуну (крейцкопфу) и представляет собой кованый или литой стержень из углеродистой стали марки Сталь 35 с противоположно расположенными большой и малой шейками. Большая шейка 11 шатуна, называемая мотылёвой, охватывает коренной вал и имеет цельную либо разъемную конструкцию. Независимо от конструкций коренной вал соединяется с шатуном посредством конических роликовых подшипников. У эксцентриковых валов мотылевая шейка шатуна имеет значительно больший диаметр, чем у кривошипных и пальцевых валов. Благодаря этому в эксцентриковых валах мотылевые подшипники имеют больший диаметр и обладают более высокой долговечностью.
Наряду с износостойкостью сочленений шатуны буровых насосов должны обладать необходимой усталостной прочностью, так как при эксплуатации они подвергаются действию асимметричных циклических нагрузок. Стержень шатуна имеет двутавровое сечение, обеспечивающее достаточную жесткость при минимальной металлоемкости шатуна. Уменьшение массы способствует снижению инерционных нагрузок, поэтому простые в изготовлении, но более массивные шатуны с круглым сечением стержня в буровых насосах не используются.
Малая шейка (рис. 5.5), называемая ползунной, служит для шарнирного соединения шатуна 6 с ползуном 4, скользящим в прямолинейных направляющих. Центр шарнира движется аксиально, т.е. по прямой, проходящей через ось вращения коренного вала. Дезаксиальные кривошипно-шатунные механизмы в буровых насосах не применяются. Малая шейка шатуна соединяется с корпусом ползуна при помощи полого валика 9. При ремонтных работах через отверстие в валике пропускается ломик для выпрессовки валика соседнего ползуна 13. Кроме того, пустотелая конструкция способствует более интенсивному охлаждению валика и подшипника шатуна, нагреваемых в результате их взаимного трения.
Врасточку ползунной шейки запрессована втулка 8 из оловянной бронзы либо другого пластичного материала, которая является в данном случае подшипником скольжения. Запрессовка не гарантирует втулку от проворачивания и осевого смещения,
ипоэтому она стопорится дюбелем 7. Диаметральный зазор между валиком и втулкой шатуна определяется в зависимости от диаметра валика и выбранной посадки.
Валик 9 снабжен концевым центрирующим конусом, который входит в конусное отверстие ползуна. С помощью стопорной планки 11, входящей в поперечный паз торца валика, и болтов 10, ввинченных в ползун, валик запрессовывается в конусное отверстие и благодаря этому удерживается от продольного смещения и проворота
98
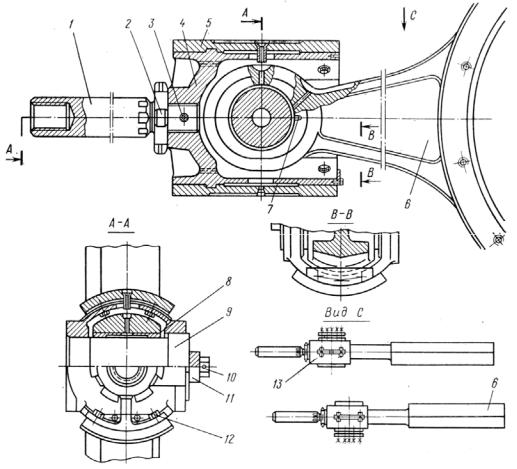
относительно ползуна. В мощных насосах шейка шатуна соединяется с валиком ползуна посредством двухрядных игольчатых подшипников.
Ползуны (крейцкопфы) необходимы для снятия радиальных усилий с резинометаллическпх поршней, которые возникали как бы при прямом соединении шатунов с поршнями. Ползун состоит из литого стального корпуса и сменных чугунных накладок 5. Аналогичные чугунные накладки крепятся к станине насоса для движения по ним ползуна. Накладки крепятся к цилиндрической поверхности корпуса болтами 12, застопоренными от самоотвинчивания упругими шайбами. В боковых стенках корпуса располагаются ступицы валика 9. В передней части крейцкопфа на резьбе ввинчивается контршток – ползунная часть штока 1, представляющего собой стальной цилиндрический стержень с наружной резьбой для крепления с корпусом ползуна и внутренней резьбой для соединения с поршневой частью штока. Стопорение штока в ползуне осуществляется шплинтом 3 и контргайкой 2.
Опорная поверхность днища под гайку 2 (упорный бурт штока) должна быть строго перпендикулярна к оси ползуна. Ползун перемещается по чугунным либо бронзовым направляющим, установленным в станине насоса. Для обеспечения нормальной эксплуатации зазор между направляющими накладками станины и накладками крейцкопфа должен быть 0,2–0,5 мм и должен регулироваться прокладками из белой жести либо латуни, установленными между корпусом ползуна и накладками. Поверхности трения накладок ползуна и станины имеют шероховатость Ra не более
2,5 мкм.
Рис. 5.5. Шатунный механизм
Станина насоса (см. рис. 5.2) снабжена маслоуловителем, в котором накапливается масло, забрасываемое вращающимися зубчатыми колесами из масляной ванны насоса.
99
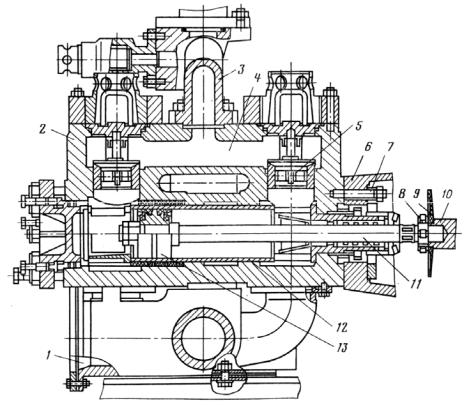
Из маслоуловителя масло по радиальным и продольным канавкам самотеком поступает на трущиеся поверхности накладок и валик ползуна.
Зубчатые передачи и подшипники приводной части насоса смазывают разбрызгиванием или в мощных буровых насосах специальным масляным насосом с цепным приводом от трансмиссионного вала. Шток смазывают и охлаждают другим насосом с приводом от отдельного электродвигателя.
Поршневая часть 11 (рис. 5.6) штока отличается от его ползунной части 10 меньшим диаметром и большей длиной, выбираемой в зависимости от хода поршня. На одном конце поршневого штока имеется наружная резьба для соединения со штоком 10 ползуна и закрепления контргайкой 8. Противоположный конец снабжен конусом с буртиком для посадки поршня 13 и резьбой для затяжки конусного соединения с целью предотвращения утечек между стыкуемыми поверхностями. Конусное соединение облегчает разборку поршней при их замене. Контактирующие поверхности штока и поршня целесообразно покрывать мягкими металлами гальваническими либо термодиффузионным способом. Такие покрытия предотвращают наклеп и сваривание посадочных поверхностей в соединениях, подвергающихся циклическим нагрузкам, и значительно повышают их несущую способность.
Для соединения поршневой и ползунной частей штока используется специальная цилиндроконическая либо метрическая резьба. Цилиндрический участок этой резьбы служит для стопорения соединяемых штоков контргайками. За присоединительной резьбой имеются шестилибо четырехгранники под гаечный ключ для завинчивания и отвинчивания соединений штоков. Поршневой шток контактирует с промывочной жидкостью и подвергается абразивному износу, в результате чего имеет ограниченный срок службы. Ползунная часть штока изолируется от промывочной жидкости дискомотражателем 9 из маслобензостойкой резины.
Рис. 5.6. Гидравлический блок бурового насоса двустороннего действия
Составная конструкция штока позволяет сохранить его ползунную часть при замене изношенного поршневого штока. Для удаления абразива и снижения износа
100