
книги / Машины и оборудование нефтяных и газовых промыслов. Силовые приводы машин и оборудования нефтяных и газовых промыслов
.pdfэксплуатации тиристорных станций в условиях работы в Заполярье показал их достаточную надежность и несложность обслуживания в промысловых условиях. Используя систему тиристорных выпрямителей, можно значительно проще решать задачу применения двигателей постоянного тока, которые обеспечивают более простую конструкцию трансмиссий, чем при электродвигателях переменного тока и ДВС, дают лучшие качества привода, причем отпадает необходимость подвоза топлива.
В настоящее время выпускаются электродвигатели постоянного тока номинальной мощностью 500, 750 и 1000 кВт и тиристорные станции управления к ним.
Улучшение рабочих и пусковых характеристик, т.е. увеличение диапазона регулирования частоты вращения асинхронных электродвигателей переменного тока с фазным ротором представляет собой сложную техническую задачу и требует включения в цепь ротора сложной регулирующей аппаратуры, удорожающей привод и снижающей его надежность. Отечественная и зарубежная практика эксплуатации электродвигателей постоянного тока в буровых установках показала высокую надежность и безотказность их работы [6].
1.5. Конструкции приводов буровых установок
Групповые силовые приводы с ДВС
Буровые установки снабжаются групповыми приводами, состоящими из двух–пяти агрегатов, сблокированных между собой цепной или клиноременной передачей. В основном приняты две схемы расположения агрегатов в приводе; двух–четырёх агрегата установлены вместе на общей раме и предназначены для привода лебедки, ротора, двух насосов и вспомогательной лебедки; по такой схеме выполнены установки для бурения скважин глубиной 1600–5000 м; три агрегата соединены вместе, установлены на общей раме и предназначены для привода лебедки, ротора и одного бурового насоса; один-два других агрегата установлены на другой раме и кинематически не связаны с первыми тремя, они предназначены для привода второго бурового насоса; по такой схеме выполнены приводы буровых установок БУ3200БД и БУ650ДГ-1V.
Вбуровых установках ВЗБТ в групповых силовых приводах применяются агрегаты САТ-4М.
Групповой силовой дизельный привод буровой установки БУ250ОДГУ (см. рис. 1.6) состоит из трех силовых агрегатов САТ-4М 4, соединяемых с цепным суммирующим редуктором 9, а через карданные валы 5, 6 и МШ500 – с насосной трансмиссией 7 и коробкой перемены передач (КПП) 3. Цепная суммирующая трансмиссия при помощи муфты МШ700 соединяется с КПП, которая передает мощность одного или двух агрегатов САТ-4М на буровую лебедку 2, а также ротору 1.
Мощность насосам передается от суммирующего редуктора 9 при помощи муфт МШ500 и клиноременных передач со шкивом диаметром 500 мм. Компрессор 8 и регулятор подачи РПД соединены трансмиссиями с суммирующим редуктором 9.
Коробка перемены передач является самостоятельным агрегатом, соединенным с лебедкой 2 и силовым приводом цепной передачей 10 с помощью цепного колеса, установленного на консольной части ее ведомого вала.
Вбуровой установке БУ5000ДГУ-1 применен привод с четырьмя силовыми агрегатами СА-10, сблокированными в суммирующем редукторе трехрядными цепными передачами. Для удобства монтажа валы двигателей соединены с валами суммирующего редуктора карданными валами. На обоих концах суммирующего редуктора размещены валы привода насосов, а на первом валу – и цепная передача привода лебедки через трехступенчатую цепную КПП. Привод ротора осуществляется карданным валом от КПП.
21
Дизель-электрический привод на постоянном токе
Дизель-электрический автономный привод состоит из дизель-генераторов переменного или постоянного тока, выполненных в виде отдельной станции, и электродвигателей постоянного тока, приводящих основные исполнительные механизмы буровой установки.
Переменный трехфазный ток генераторов преобразуется в выпрямленный ток тиристорными станциями управления, аналогичными по устройству станциям, применяемым при питании электродвигателей постоянного тока от сетей трехфазного переменного тока. Этот вид привода обеспечивает широкий диапазон регулирования характеристики исполнительных механизмов и улучшает их монтажеспособность. При наличии дизель-электрического привода упрощаются основания и привышечные сооружения. Дизель-генераторы перемещаются в собранном виде на основании с укрытием.
При дизель-электрическом приводе нагрузку между дизелями можно автоматически перераспределить, направляя мощность любому потребителю: лебедке, ротору или насосам, что дает значительную экономию топлива. Повышается моторесурс вследствие более равномерной загрузки за счет защиты дизелей от резких изменений нагрузок. Кроме того, упрощается управление приводом и установкой и обеспечивается более безопасное ведение работ при газопроявлениях и фонтанировании скважин. Дизель-электрический привод имеет более высокий общий коэффициент полезного действия установки по сравнению с приводом от ДВС.
В состав оборудования буровой установки с дизель-электрическим приводом входят дизель-генераторные установки переменного тока; тиристорные станции переменного-постоянного тока; два электродвигателя насосов; электродвигатели лебедки и ротора, регулятора подачи двух компрессорных станций КСЭ-ЗМ; распределительный щит и рамы установок.
Преимущества этого привода заключаются в том, что он не имеет громоздкого цепного суммирующего редуктора, упрощена КПП и другие цепные трансмиссии привода, а также нет надобности в дополнительном дизель-генераторе переменного тока для подачи энергии двигателям вспомогательных механизмов и для освещения буровой. В связи с этим привод широко распространен в морских буровых установках, а в ряде случаев и в установках для бурения скважин средних глубин.
Все агрегаты дизель-электрического привода устанавливают в помещении, каждый на отдельной фундаментной раме. В этом же помещении находятся компрессорные станции, вентиляторы для охлаждения, распределительный щит и контрольноизмерительные приборы [6].
2.ТРАНСМИССИИ БУРОВЫХ УСТАНОВОК
Вбуровом оборудовании для осуществления кинематической связи между валами
вмеханизмах, изменения скорости и направления вращения, преобразования крутящих моментов используют цепные, клиноременные и зубчатые передачи. В установках малой мощности для геологоразведочного бурения при небольших межосевых расстояниях между валами (до 0,5 м) используют почти всегда зубчатые передачи, а при межосевых расстояниях более 0,5 м – клиноременные.
Вустановках для эксплуатационного бурения с целью передачи больших мощностей (500–2000 кВт и более) при межосевых расстояниях более 1 м применяют многорядные цепные и клиноременные передачи. Зубчатые передачи используют при межосевых расстояниях менее 1 м – в редукторах насосов, реверсивных устройствах КПП, приводах роторов и др. [6].
Вмеханических трансмиссиях для преобразования частоты вращения в крутящие моменты применяют коробки передач. В установках геологоразведочного бурения такие трансмиссии используют наиболее часто. Они позволяют получить широкий
22
диапазон изменения частоты вращения, просты в эксплуатации, имеют достаточно высокий КПД. Недостатками механических трансмиссий являются ступенчатое изменение передаточных отношений и ограниченное число скоростей, что исключает возможность полного использования мощности двигателя при спуско-подъемных операциях и затрудняет выбор рациональной частоты вращения породоразрушающего инструмента. Трансмиссия не предохраняет двигатель от перегрузки и вибраций, возникающих при бурении, недостаточно надежна при низких значениях температуры.
Кинематическая связь в механических трансмиссиях осуществляется с помощью различных передач и муфт.
Зубчатые цилиндрические и конические передачи используют в редукторах, коробках передач и других элементах трансмиссии при межцентровых расстояниях между валами до 1 м. В тихоходных передачах обычно применяют прямозубые, а при окружных скоростях более 4–6 м/с и значительной передаваемой мощности – косозубые и шевронные колеса, позволяющие уменьшить динамические нагрузки и снизить шум при работе. Для повышения работоспособности зубчатые передачи, имеющие окружную скорость более 1–2 м/с, размещают в масляных ваннах.
Цепные передачи применяют при расстоянии между осями валов до 4–5 м и окружных скоростях до 20 м/с. В установках геологоразведочного бурения цепные передачи используются редко. Они широко распространены в установках для бурения скважин на нефть и газ в коробках передач, при блокировании ДВС, в передачах от двигателей к лебедкам и роторам.
Применение цепных передач позволяет упростить кинематическую цепь благодаря большим расстояниям между валами и сохранению направления их вращения. Цепные передачи имеют высокий КПД, создают небольшие нагрузки на валы и опоры от предварительного натяжения. Важными преимуществами цепных передач перед зубчатыми являются меньшая масса, а также возможность оперативного устранения дефектного звена или замены всей изношенной цепи без съема валов.
Недостатками цепных передач являются необходимость точного монтажа, некоторая неравномерность скорости цепи и звездочек, шум при работе.
Клиноременные передачи используют при межцентровых расстояниях до 3 м и окружных скоростях до 25–30 м/с. Основное распространение они получили в приводах буровых насосов, компрессоров, глиномешалок, а также в передачах, блокирующих двигатели внутреннего сгорания тяжелых буровых установок.
Преимуществами клиноременных передач являются возможность передачи вращения при больших межцентровых расстояниях между валами, смягчение колебаний нагрузки за счет эластичности и частичного проскальзывания ремней, меньшая чувствительность к перекосам соединяемых валов, бесшумность работы и простота ухода. Наряду с этим, клиноременные передачи создают значительные нагрузки на опоры вследствие большого предварительного натяжения ремней, требуют применения устройств для периодического их подтягивания, чувствительных к попаданию смазки [8].
2.1. Клиноременные трансмиссии
Клиноременные трансмиссии применяют в приводах буровых насосов, компрессоров и в приводах вспомогательных механизмов установок. Благодаря своей упругости клиновые ремни обладают способностью несколько амортизировать резкие перегрузки и сглаживать неравномерность вращения, вызываемую кривошипношатунными механизмами этих машин.
Клиновые ремни применяют также в передачах силовых приводов, блокирующих двигатель мощностью до 300 кВт. Одна передача может передавать довольно большие мощности (до 600 кВт) с одного параллельного вала на другой при межосевых расстояниях до 4 м и частотах вращения до 1200 об/мин. Для передач больших
23
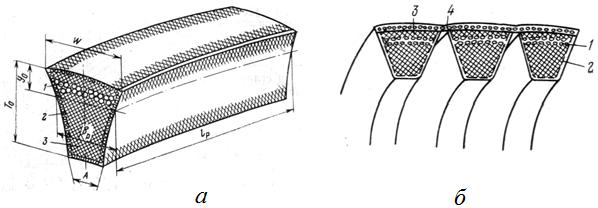
мощностей приходится применять трансмиссии с большим числом клиновых ремней (до 22), что обычно не делается в трансмиссиях общего назначения. В этих случаях необходимо точно подбирать длину ремней в комплекте, однако вследствие неоднородности ремни вытягиваются в комплекте неодинаково.
К недостаткам этих передач относятся: необходимость предварительного натяжения ремней, что увеличивает нагрузку на валы и подшипники; смена изношенных клиновых ремней, требующая демонтажа валов или сближения их консольных шкивов, что довольно сложно выполнять в полевых условиях; меньший КПД, чем у цепных передач; колебания ветвей и всей системы вследствие непостоянства размеров сечений по длине ремня и мгновенного изменения передаточного отношения. Эти обстоятельства и необходимость периодической подтяжки ремней ограничивают область их применения в передачах буровых установок.
Клиновые ремни (рис. 2.1, а) состоят из нейтрального слоя 1 – шнура, изготовленного из синтетического волокна большой прочности и навитого по спирали; обертки – наружного слоя 2 из хлоропрена, стойкого к действию масла, нефти, нагреву; слоев 3 (сжатия и растяжения) из резины. В буровых установках применяют многорядные клиноременные передачи, скомплектованные из одиночных клиновых ремней или нескольких (до шести) свулканизированных одной общей покрышкой 4
(рис. 2.1, б).
Угол клина прямолинейного участка ремня, находящегося под натяжением,
А = 40°+0,5° (см. рис. 2.1, а).
Используются клиновые ремни нормального сечения Г, Д, Е по ГОСТ 1284.1–80 и узкие ремни профиля УБ и УВ по РТМ 38-40545–79 (табл. 2.1). Клиновые ремни нормального типа имеют отношение lp/T0 = 1,4, а узкие lp/Т0 = 1,05…1,1.
При работе в канавке шкива клиновый ремень прогибается и из-за эксцентричного приложения сил трения нагрузка по ширине несущего слоя (корда) распределяется неравномерно. В узких ремнях вследствие меньшей ширины прогиб ремня незначителен и нагрузка распределяется более равномерно. Вогнутые боковые поверхности узкого ремня при огибании шкива становятся плоскими, и контактная нагрузка между ремнем и канавкой распределяется более равномерно, при этом уменьшается износ и увеличивается ресурс ремня.
Рис. 2.1. Клиновые ремни типа УВ:
а – сечение ремня; б – многорядный ремень с покрытием; W – ширина по нейтральному слою; Т0 – высота; y0 – расстояние между наружными и нейтральным слоями; А – угол клина ремня; lр – длина по нейтральному слою под нагрузкой
24
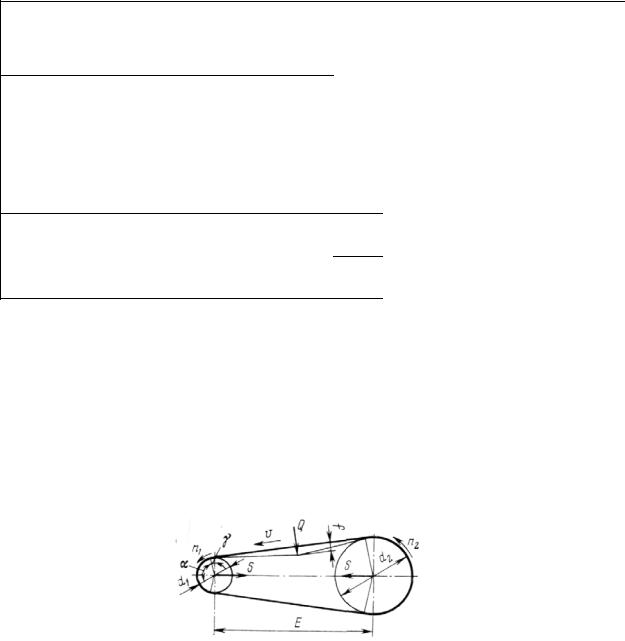
Клиновые ремни нормального сечения допускают скорости до 30 м/с, а узкие – до 50 м/с. Узкие ремни допускают большие натяжения и передают при той же площади сечения почти в 2 раза большие мощности.
Клиновые ремни чувствительны к попаданию на них масла, нефти и солнечных лучей. По этим причинам, а также из соображения безопасности их закрывают кожухами, имеющими вентиляцию для охлаждения.
Расчет мощности, передаваемой клиновыми ремнями нормальных сечений, регламентирован ГОСТ 1284.1–80, а узкими ремнями – РТМ 38-40545–79.
Таблица 2.1
Размеры приводных клиновых ремней (см. рис. 2.1, а)
Тип
ремней
Узкие Нормальные РТМ 38ГОСТ 1284.1–80 4054–79
Обозна- |
|
|
Размеры сечения, мм |
|
Площадь |
|
Масса |
||
|
|
|
Предельная |
1 м |
|||||
|
|
|
|
|
|
||||
чение |
|
|
|
|
|
|
сечения |
длина l, мм |
длины |
ремней |
|
lp |
W |
T0 |
y0 |
П, мм2 |
|||
|
|
|
+0,9 |
|
|
|
|
|
m, кг |
Г |
27 |
|
32 |
19±0,6 |
6,9 |
476 |
3150–15 000 |
0,60 |
|
|
–0,6 |
||||||||
|
|
|
|
|
|
|
|
|
|
Д |
32 |
|
+10 |
38 |
23,5±0,7 |
8,3 |
692 |
4500–18 000 |
0,90 |
|
–0,8 |
||||||||
|
|
|
|
|
|
|
|
|
|
|
|
|
+10 |
|
|
|
|
|
|
Е |
42 |
|
–0,8 |
50 |
30±0,8 |
11,0 |
1172 |
6300–18 000 |
1,52 |
|
|
|
|
|
|
|
|
|
|
|
|
|
+0,7 |
|
|
|
|
|
|
УБ |
14 |
|
17 |
13±0,5 |
3,5 |
159 |
1250–8000 |
0,20 |
|
|
–0,5 |
||||||||
|
|
|
|
|
|
|
|
|
|
|
|
|
|
|
|
|
|
|
|
УВ |
19 |
|
+0,8 |
22 |
18±0,5 |
4,8 |
278 |
2000–8000 |
0,37 |
|
|
–0,5 |
|
||||||
|
|
|
|
|
|
|
|
|
Расчетная схема клиноременной передачи приведена на рис. 2.2. |
|
Окружная скорость ремня (в м/с) |
|
πd1n1 / 60 . |
(2.1) |
Угол охвата малого шкива (в градусах) |
|
α 180 2γ 180 57 d2 d1 . |
(2.2) |
E |
|
Для передачи мощностей менее 200 кВт применяют ремни нормального сечения Б, В и Г или узкие УБ, а для передачи больших мощностей – нормального сечения Д и Е или узкие УВ. Зоны работы ремней показаны на рис. 2.3.
Рис. 2.2. Расчетная схема клиноременной передачи:
Е– межосевое расстояние, м; d1 и d2 – расчетные диаметры меньшего и большего шкивов, м; n1 и n2 – частоты вращения меньшего и большего шкивов, об/мин; Q – усилия контроля прогиба ремня, Н; f – стрела прогиба, мм;
S – натяжение струн передачи, Н
25
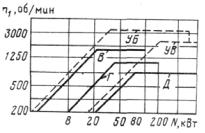
Рис. 2.3. График выбора сечения клинового ремня в зависимости от передаваемой мощности N и частоты вращения
После того как выбрано сечение ремня, определяют мощность, передаваемую одним ремнем:
Np = N0CaCL/Cp, |
(2.3) |
где N0 – номинальная мощность, передаваемая одним ремнем; Са – коэффициент угла охвата; CL – коэффициент длины ремня (1,0–1,08 при L = 6…8 м); Ср – коэффициент динамичности нагрузки и режима работы оборудования буровых установок, при работе не более 16 ч/сут Ср = 1,3…1,6.
Значения коэффициента Са |
160 |
140 |
120 |
110 |
100 |
80 |
80 |
70 |
|
Угол охвата α, градус |
180 |
||||||||
Са |
1,0 |
0,95 |
0,89 |
0,82 |
0,78 |
0,73 |
0,68 |
0,62 |
0,56 |
Промежуточные значения номинальной мощности и коэффициентов определяются линейной интерполяцией.
Машины и агрегаты установки работают в процессе бурения скважины при различных мощностях и нагрузках, поэтому число ремней в передаче определяют по эквивалентной мощности Nэ на ведущем валу:
z = Nэ / NpCz, |
(2.4) |
где Сz – коэффициент, учитывающий число ремней в комплекте (при z = 4…6 Сz = 0,9,
при z > 6 Сz = 0,85).
Наиболее рациональное число клиновых ремней в одной передаче до 12, но в ряде случаев применяют и 18–20, однако при этом требуется весьма точная комплектация ремней по длине.
На долговечность ремней значительно влияет их скорость. Скорости для длительно действующих передач – 15–20 м/с, для кратковременной работы – 20–25 м/с, но не более 30 м/с. Для узких ремней скорости можно выбирать на 30–40 % больше. Выбирая скорость ремня и зная частоту вращения двигателя, можно определить расчетный диаметр меньшего шкива d1.
В заданных габаритах рекомендуется применять d1 возможно большим, так как при этом снижаются напряжения изгиба в ремне, повышаются КПД и ресурс работы ремней, уменьшается окружное напряжение.
Минимальные расчетные диаметры шкивов |
|
|
|
||
Сечение ремня |
Г |
Д |
Е |
УБ |
УВ |
d1min, мм |
355 |
500 |
800 |
160 |
224 |
26
Диаметр большого шкива |
|
d2 = d1u12, |
(2.5) |
где u12 – передаточное отношение трансмиссии, u12 = n1 / n2β; β |
– коэффициент |
скольжения ремней (скольжение 1–2 %), зависящий от их натяжения, β = 0,98…0,99.
Предварительное межосевое расстояние |
|
|
|
|
|
|
|
|
||
|
|
E0 = (d2 + 3d1)/2. |
|
|
|
|
|
(2.6) |
||
Межосевое расстояние Е0 можно выбирать по величине отношения Е0 к диаметру |
||||||||||
большого шкива d2 в зависимости от передаточного отношения: |
|
|
|
|
||||||
u12 |
1 |
2 |
|
3 |
|
4 |
|
|
|
|
E0/d2 |
1,5 |
1,2 |
|
1,0 |
|
0,95 |
|
|
||
Предварительная эффективная расчетная длина ремня |
|
)2 |
|
|
||||||
|
|
Lp 2E0 |
π |
(d1 d2 ) |
(d d |
2 |
. |
(2.7) |
||
|
|
|
1 |
|
||||||
|
|
2 |
4E0 |
|
|
|||||
|
|
|
|
|
|
|
|
|
||
Расчетную |
длину |
ремня округляют |
до |
ближайшей |
|
стандартной |
длины |
по ГОСТ 1284.1–80 или РТМ 38-40545–79.
В передачах буровых установок натяжные ролики не применяют. Для натяжения ремней и их смены предусматривают натяжные устройства, обеспечивающие увеличение межосевого расстояния до 6 %. Силу натяжения клиноременной передачи (в Н) рассчитывают по формуле
где |
|
|
S zS0 , |
|
|
|
(2.8) |
|
|
|
850NэCpCL |
|
|
|
|
||
S |
0 |
|
|
m |
. |
(2.9) |
||
z Ca |
2 |
|||||||
|
|
|
|
|
Здесь m – масса 1 м длины ремня, кг (см. табл. 2.1).
Натяжение ремня контролируется по прогибу f ветви под действием силы Q (см. рис. 2.3). Прогиб ветви (в мм)
|
|
f 1,55 |
E0 |
. |
|
(2.10) |
|
|
100 |
|
|||
|
|
|
|
|
|
|
Усилия для контроля натяжения (в Н) определяют по следующим формулам: |
||||||
– для одного нового ремня |
Q = (l,4 + Cc)/16; |
|
(2.11) |
|||
– для приработанного ремня |
|
|||||
Q0 = (S0 + Cc)/16, |
|
(2.12) |
||||
|
|
|
||||
где Cс – коэффициент (в Н), зависящий от жесткости ремня. Зависимость коэффициента |
||||||
Сс от сечения ремня. |
|
|
|
|
|
|
Зависимость коэффициента Сс от сечения ремня |
УБ |
УВ |
||||
Сечение ремня |
Г |
Д |
|
Е |
||
Сс, Н |
320 |
470 |
780 |
60 |
150 |
При выходе одного из ремней из строя в многорядной передаче следует заменить весь комплект. Ремни, бывшие в употреблении, должны подбираться отдельным комплектом. При хорошем монтаже и предварительном натяжении ремней КПД передачи η = 0,92…0,97. КПД клиноременной передачи зависит от отношения диаметра малого шкива d1 к высоте ремня Т0 (рис. 2.4).
27
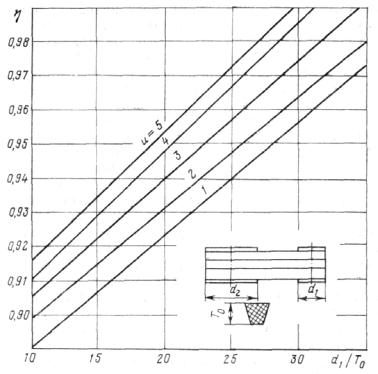
Критерии работоспособности клиновых ремней – наработка и удлинение. Наработка ремня (в ч)
Tср.с Nоц |
lp |
|
, |
(2.13) |
60πd n |
||||
1 |
1 |
|
|
где Nоц – наработка ремня, цикл (один цикл соответствует одному пробегу ремня). Удлинение ремней не должно превышать 2,5 %.
Рис. 2.4. Зависимость КПД клиноременной передачи от отношения d1/T0
Средний ресурс ремней в эксплуатации для среднего режима работы (Тср) принимается 2000 ч, при других режимах работы средний ресурс определяется по формуле
Тcр. р = Тсрk1k2, |
(2.14) |
где k1 – коэффициент режима работы (для тяжелого режима k1 = 0,5, для очень тяжелого k1 = 0,25); k2 – коэффициент, учитывающий климатические условия эксплуатации (для районов с холодным и очень холодным климатом k2 = 0,75, для центральных и других зон k2 = l) [6].
2.2. Цепные передачи буровых установок
В буровых установках преимущественно используются цепные передачи. В однорядном исчислении общая длина цепей, используемых в современных буровых установках, достигает 6000–7000 звеньев. Цепная передача состоит из ведущей и ведомой звездочек и огибающей их цепи. В зависимости от направления вращения звездочки ведущей ветвью цепи может быть как верхняя, так и нижняя. Предпочтительны передачи с верхней ведущей ветвью.
По конструктивному исполнению различают открытые и закрытые передачи с горизонтальным и наклонным расположением оси, соединяющей центры звездочек. Передачи с углом наклона к горизонту до 30° относятся к горизонтальным, с 30° до 60°
– к наклонным. Вертикальные передачи имеют угол наклона оси к горизонту 60°–90° и требуют установки дополнительных устройств для предварительного натяжения цепи.
28
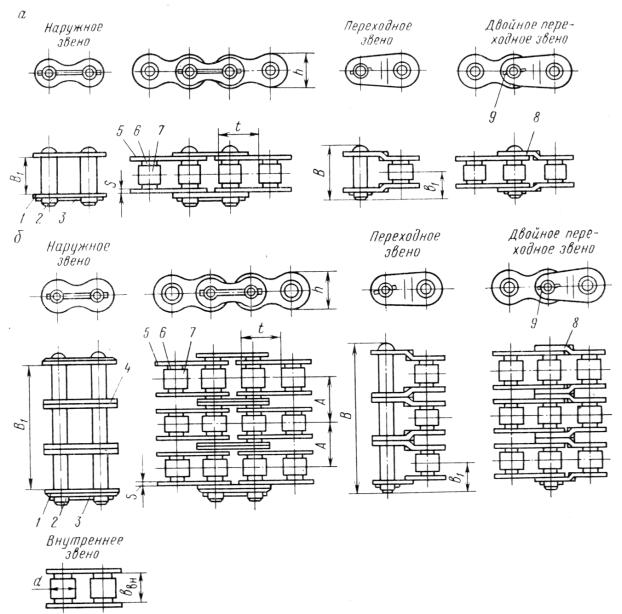
Различают одноконтурные и многоконтурные цепные передачи. В многоконтурных между соединяемыми валами установлено несколько параллельно расположенных цепных передач с одинаковыми и разными передаточными числами [1].
2.2.1. Типы, основные параметры и размеры цепей
Цепь представляет собой гибкую конструкцию, собранную из последовательно соединенных жестких звеньев. Цепи, используемые для передачи механической энергии от одного вала другому, называются приводными. По конструктивным признакам приводные цепи (рис. 2.5) относятся к роликовым и состоят из чередующихся наружных и внутренних звеньев, каждое из которых собирается из двух пластин, напрессованных на валики 2 со шплинтом 3 или на втулки 6. Втулки снабжены роликами 7, которые при входе в зацепление со звездочкой проворачиваются
относительно |
втулок. Благодаря |
этому уменьшается трение и снижается |
износ |
поверхностей |
контакта зубьев звездочки и роликов. Наружные 1 и внутренние 5 |
||
пластины по контуру напоминают |
восьмерку. |
|
Рис. 2.5. Приводная роликовая цепь: а – однорядная; б – трехрядная
29
Площадь поперечного сечения по проушинам примерно равна площади сечения пластины в средней ее части (шейке). Однако вследствие больших местных напряжений в зоне отверстий, являющихся концентратором напряжений, усталостная прочность в поперечном сечении отверстий меньше, чем в шейке пластины. Отверстия внутренних пластин растачивают по диаметру сопрягаемых с ними втулок и больше диаметра отверстий наружных пластин, растачиваемых по диаметру валиков. Равнопрочность наружных и внутренних пластин обеспечивается за счет соответствующего увеличения ширины внутренних пластин.
Валики цепи раскатывают либо развальцовывают с одного конца, и они имеют отверстия для шплинта на другом конце. Соединительное звено является составной частью цепи и состоит из наружной пластины с неподвижно закрепленными валиками (вилки), соединительной пластины и шплинтов. При нечетном числе звеньев цепь соединяется переходным звеном, состоящим из переходных пластин 8, валика, втулки, ролика 9.
В буровых установках вследствие больших нагрузок и скоростей преимущественно используется многорядная цепь (см. рис. 2.5, б), которая отличается от однорядной длиной В валиков и наличием промежуточных пластин 4, отличающихся от наружных диаметром отверстий. Наружные пластины соединяются с валиком с натягом, а промежуточные – с зазором 0,02 мм, облегчающим сборку многорядной цепи.
Следует отметить, что номинальный шаг внутренних пластин равен шагу цепи. У наружных пластин номинальный шаг меньше шага цепи на величину зазора между втулкой и валиком, а у промежуточных пластин – на величину зазора между отверстием пластины и валиком. При натяжении цепи зазоры выбирают, а шаги внутренних и внешних звеньев выравнивают. В результате этого обеспечивается равномерное нагружение наружных и промежуточных пластин. В отличие от наружных и внутренних пластин промежуточные изготавливают без фаски на внешнем контуре. Ниже приведены основные размеры пластин (в мм) для цепи с шагом t = 50,8 мм.
Тип пластины |
Внутренняя |
Наружная |
Промежуточная |
Ширина пластины |
46 |
40 |
40 |
Ширина шейки пластины |
32 |
27 |
27 |
Диаметр отверстия под валики |
– |
14,1+0,035 |
14,31+0,035 |
Диаметр отверстия под втулку |
20,57+0,045 |
– |
– |
Шаг пластины |
50,8+0,11 |
50,72 0,0550,055 |
50,65 0,0550,055 |
Длина пластины |
96,8 |
92,7 |
92,7 |
Фаска |
1,5 |
1,5 |
– |
Толщина пластины s |
6,4 |
6,4 |
6,4 |
Масса, кг |
0,146 |
0,128 |
0,128 |
Пластины цепи изготовляют из холоднокатаного проката повышенной точности, получаемого из стали марки 30ХН3А. После термообработки пластины имеют твердость 38–45 HRC. При вырубке продольная ось пластин должна быть расположена вдоль волокон металла. Как показали сравнительные испытания, принятая марка стали обладает достаточным сопротивлением усталости, хорошей обрабатываемостью и стабильными механическими свойствами после термообработки. Толщина пластины – расчетный параметр цепи, определяющей ее прочность.
Валик, неподвижно закрепляемый в отверстиях пластин наружного звена, представляет собой цилиндрический стержень с коническими торцами, облегчающими сборку цепи. В собранной цепи конические торцы валиков раскатывают либо развальцовывают. Валики должны обладать достаточной прочностью,
30