
книги / Машины и оборудование нефтяных и газовых промыслов. Силовые приводы машин и оборудования нефтяных и газовых промыслов
.pdf–соответствие требованиям технической эстетики, эргономики и техники безопасности;
–использование минимальной номенклатуры материалов, подшипников, модулей зацеплений и шлицев в целях облегчения освоения серийного производства;
–наличие резервов дальнейшего совершенствования параметров и конструктивного устройства по мере появления новых комплектующих изделий (элементов привода, приборов, средств механизации и т.д.).
При разработке буровых станков необходимо, кроме того, учитывать требования к их основным рабочим органам, изложенные в соответствующих подразделах.
Производительность бурения определяется техническими, геологическими, технологическими и организационными факторами. К техническим относятся конструкция и параметры, а также прочностные характеристики и надежность оборудования и инструмента, способ осуществления спуско-подъемных операций и применяемые для этого механизмы и приспособления. Геологические факторы представляют собой сочетания свойств пород, их чередование и характер залегания в разрезе, что обусловливает их буримость, устойчивость стенок ствола, изменение направления скважины, возможность реализации рациональных режимов бурения, поведение керна.
Технологические факторы включают способ бурения, тип породоразрушающего инструмента, параметры режима бурения, направление скважины, способ промывки и свойства промывочной жидкости. Организационные факторы объединяют такие особенности работ, как сменность и сезонность, расстояние между скважинами, способ
исредства транспортировки и монтажно-демонтажных операций, энергоснабжение, снабжение материалами, водоснабжение, расположение партии, перевозка бригад, оснащенность мастерских, организация профилактического обслуживания и ремонтов оборудования.
На стоимость бурения влияют все указанные выше факторы, что выражается в ее зависимости от производительности и стоимости станко-смены. Кроме того, на стоимость существенно влияет правильность выбора оборудования для конкретных условий и полнота использования его возможностей. Так, применение дорогостоящего оборудования приводит к удорожанию станко-смены и, как следствие, к повышению стоимости бурения, если не может быть реализована его мощность или отсутствует необходимый фронт работ и объемы бурения не соответствуют возможной производительности.
Важную роль в реализации возможностей бурового станка играет его коэффициент
полезного действия η. Он может быть выражен через потери мощности в станке ∆Nст и мощность привода N:
η |
N Nст |
1 |
|
Nст . |
(9.5) |
|
|||||
|
N |
|
N |
|
Потери мощности в станке зависят от типа трансмиссии, массы ее элементов и частоты вращения вращателя. Для шпиндельных станков с механическими передачами
∆Nст = kпN(A + Bn) = 1,1N(6·10–2+1,2·10–4n), |
(9.6) |
где kп – коэффициент, учитывающий увеличение потерь энергии в станке под нагрузкой; А – коэффициент, характеризующий потери мощности в элементах трансмиссии, вращающихся с постоянной частотой; В – коэффициент, характеризующий потери в элементах, частота вращения которых зависит от n.
Тогда
η = (0,93…1,32)·10–4n. |
(9.7) |
Для станков с подвижным вращателем и механической трансмиссией
171
η = (0,85…l,0) ·10–4n, |
(9.8) |
с гидроприводом |
|
η = (0,87…1,6) ·10–4n. |
(9.9) |
Приведенные формулы характеризуют средние значения КПД. Однако в зависимости от состояния станка, степени износа и правильности смазки и регулировки потери мощности в нем могут изменяться в широких пределах, увеличиваясь в 2–3 раза по отношению к средним значениям, что приводит к снижению КПД до 60–70 %.
В значительной мере производительность зависит от удобства управления оборудованием и его обслуживания. Удобство управления характеризуется соответствием оборудования психофизическим особенностям человека, числом элементов управления, с которыми одновременно приходится иметь дело оператору, степенью совмещения управляющих воздействий во времени, размещением и формой рукояток управления, группировкой рукояток управления, участвующих в выполнении отдельных операций, необходимыми усилиями на рукоятках, длиной их перемещений или числом оборотов и т.д. Удобство обслуживания определяется доступностью и простотой регулировки и смазки, необходимой частотой выполнения этих операций, унификаций приемов и приспособлений. Удобство управления и обслуживания в определенной степени зависит от освещенности соответствующих зон буровой.
Степень механизации определяется отношением числа механизированных операций к их общему числу. Среди операций, подлежащих механизации: свинчивание и развинчивание труб при спуске и подъеме, перемещение свечи с устья скважины на подсвечник при подъеме и с подсвечника на устье при спуске, извлечение керна из колонковой трубы, замена породоразрушающего инструмента, сборка и разборка бурового снаряда на рабочей площадке, наращивание инструмента и перекрепление патронов.
Значительным резервом сокращения затрат времени на спуско-подъемные операции, который может быть реализован при комплексной механизации, является совмещение их отдельных элементов, например свинчивания или развинчивания, с подъемом или спуском элеватора. При обсадке скважины необходимо механизировать сборку свечей обсадных труб на рабочей площадке, свинчивание их на устье, расхаживание и проворачивание при возникновении сопротивлений в стволе во время спуска. Трудоемкие операции при монтаже и демонтаже оборудования, его установке на рабочей площадке, подготовке к транспортировке, подъеме и опускании мачты подлежат механизации.
Важнейшим комплексным показателем, определяющим качество оборудования и инструмента, является надежность, т.е. свойство изделия выполнять заданные функции, сохраняя эксплуатационные показатели в определенных пределах в течение требуемого времени или объема работы. По надежности изделия подразделяются на ремонтируемые и неремонтируемые. К первой группе относятся станки, насосы, труборазвороты, элеваторы и другие механизмы. Неремонтируемые – это породоразрушающий инструмент, резьбовые соединения.
Основными величинами, участвующими в расчетах надежности, являются число отказов и величина наработки на отказ. Для ремонтируемых изделий одним из основных показателей является наработка на отказ, т.е. среднее значение времени его наработки между отказами. Оценивается вероятность безотказной работы за определенный период времени. Показателем надежности является также среднее время восстановления, т.е. среднее время, затрачиваемое на обнаружение и устранение одного отказа. Отношение времени наработки на отказ к суммарному времени наработки и восстановления представляет собой коэффициент готовности, характеризующий вероятность того, что ремонтируемое изделие будет работоспособным в любой момент
172
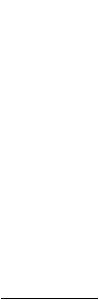
времени. Наконец, календарная продолжительность эксплуатации изделия определяет срок его службы.
Для неремонтируемых изделий по аналогии рассматривают наработку до отказа и интенсивность отказов в единицу времени. Различают постепенные и внезапные отказы. Первые являются функцией времени и вызываются постепенным изменением параметров изделия в результате износов или усталости. Внезапные отказы происходят в результате неожиданных поломок деталей, приводящих к потере работоспособности.
Влияние показателей надежности на время, затрачиваемое при ремонтах в процессе бурения скважины, Тр видно из следующей формулы:
Тр = Ltв / υтехtотк, |
(9.10) |
где L – глубина скважины, м; tв – среднее время восстановления, ч; υтех – техническая скорость, м/ч; tотк – средняя наработка на отказ, ч.
Систематическое изучение показателей надежности и установление характера распределения отказов позволяют выявить слабые, недоработанные места оборудования, устранить причины отказов и повысить качество изделий [8].
9.4. Принципиальные схемы буровых станков
Принципиальные схемы буровых станков определяются типом и сочетанием основных рабочих органов и их приводом, как видно из классификации (табл. 9.1).
|
|
|
|
|
Таблица 9.1 |
|
|
Типы основных рабочих органов и приводов буровых станков |
|||||
|
|
|
|
|
|
|
Вращатель |
Подача |
Средства спуско-подъемных |
Привод рабочих органов |
|||
|
|
операций |
|
|
|
|
|
|
Лебедочный |
Безлебедочный |
От единого |
|
|
Шпиндель- |
Поршневая |
Элеваторы |
Механизм |
Индиви- |
|
|
ный |
гидравличес- |
кольцевые, |
подачи; |
двигателя |
дуальными |
|
|
кая, винтовая |
полуавтома- |
экстракторы с |
посредством |
гидро-, |
|
|
|
тические, |
захватами |
трансмиссии |
пневмоили |
|
Ротор |
Канатная, |
вертлюжные |
Механизм |
|
электро- |
|
|
цепная, |
пробки |
подачи; |
|
двигателями |
|
|
поршневая |
|
элеватор, |
|
|
|
|
гидравличес- |
|
фартшуль |
|
|
|
|
кая |
|
|
|
|
|
Подвиж- |
Поршневая |
|
Механизм |
|
|
|
ный: |
гидравличес- |
|
подачи; |
|
|
|
проходной, |
кая, цепная, |
|
резьбовой |
|
|
|
непроход- |
канатная |
|
переходник, |
|
|
|
ной |
|
|
элеватор, |
|
|
|
|
|
|
гидропатрон, |
|
|
|
|
|
|
захваты |
|
|
|
Наибольшее влияние |
на принципиальную схему |
оказывает тип вращателя. |
В сочетании со шпиндельным вращателем чаще всего используется поршневой гидравлический и реже винтовой механизм подачи с ходом 0,5–0,6 м (как исключение до 1,5 м) и подъем бурового инструмента с помощью лебедки. Привод узлов обычно осуществляется от общей механической трансмиссии. С роторным вращателем сочетается свободная канатная либо принудительная канатная и цепная подача с приводом от индивидуальных двигателей или через общую трансмиссию. Ход подачи
173
находится в пределах 3–9, реже 18 м. Спуско-подъемные операции осуществляются одной или двумя лебедками. Привод, как правило, механический, хотя применяется и гидравлический привод рабочих органов от индивидуальных гидродвигателей.
С подвижным вращателем используется поршневой гидравлический механизм подачи (при ходе до 3 м) либо канатный и цепной механизмы (при ходе до 9 м) с приводом от гидроцилиндров или гидродвигателей. Для станков с подвижным вращателем характерно использование основных рабочих органов и для выполнения вспомогательных операций. Так, при спуско-подъемных операциях с помощью лебедки проходной подвижный вращатель может служить для свинчивания и развинчивания бурильных труб.
Для укладки и подъема со стеллажа бурильных труб предусматривается возможность поворота вращателя в вертикальной плоскости в цапфах каретки, на которой он перемещается по направляющим. Вращатели выполняются непроходными и проходными. Отличие схем с непроходным и проходным вращателями заключается в том, что в первом случае перекрепление отсутствует и независимо от хода подачи осуществляется только наращивание инструмента, который соединяется со шпинделем вращателя посредством резьбы.
При углублении скважины на интервал, равный длине наращиваемой трубы, вращатель, занявший крайнее нижнее положение, освобождается от колонны и соединяется с новой трубой, которая во время его подъема выводится на ось скважины. Свинчивание трубы с колонной производится вращателем. Таким образом, выполняется минимум операций, большинство из которых механизировано.
При проходном вращателе необходимо отвинтить от верхней трубы промывочный сальник и установить новую трубу с помощью лебедки или вручную, предварительно соединив ее с сальником, после чего поднять вращатель и произвести свинчивание. Очевидно, что в этом случае число операций больше, а степень их механизации меньше.
Наращивание бурового снаряда на установке с проходным подвижным вращателем можно производить двумя способами:
–с установкой наращиваемой бурильной трубы под вращатель;
–с опусканием бурильной трубы через вращатель.
Проходной вращатель позволяет наращивать бурильные трубы, длина которых превышает ход подачи установки, что особенно важно при бурении съемными керноприемниками на канате, с выносом керна обратным потоком промывочной жидкости, а также при бескерновом бурении, когда длина рейса может составлять несколько десятков метров.
Упрощение в станках с подвижным вращателем ряда вспомогательных операций и их механизация с помощью вращателя позволяют улучшить использование рабочего времени и повысить производительность труда. Эффективность подвижного вращателя возрастает по мере повышения производительности бурения. Это подтверждается данными, характеризующими относительное изменение затрат времени на вспомогательные операции по отношению к общему времени бурения.
Опыт эксплуатации буровых станков свидетельствует о несомненной целесообразности использования подвижного вращателя, особенно в оборудовании, предназначенном для высокопроизводительных методов бурения, таких как высокооборотное алмазное, со съемными керноприемниками, с выносом керна потоком промывочной жидкости, ударно-вращательное и бескерновое.
Влияние типа вращателя на затраты времени, связанные с выполнением вспомогательных операций, изменяется с глубиной. В интервале значений глубины 100–1500 м удельные затраты времени на вспомогательные операции в расчете на 1 м скважины составляют: при обычном колонковом бурении 0,25–0,64 ч для шпиндельного станка; 0,1–0,54 ч – для станка с подвижным вращателем; при бурении со съемным керноприемником 0,25–0,44 и 0,1–0,3 ч соответственно.
174
Рост производительности в результате использования оборудования с подвижным вращателем может достигать 15–35 % в зависимости от величины механической скорости бурения.
Принципиальная схема бурового станка влияет не только на эффективность процесса бурения и скорость вспомогательных операций, но и на массу оборудования. Статистический анализ характеристик значительного числа современных буровых станков позволил выявить, что эта зависимость является линейной, а ее характер различен для шпиндельных станков и станков с подвижным вращателем.
Масса шпиндельных станков Мшп зависит от расчетного крутящего момента, грузоподъемности лебедки и механизма подачи и с учетом массы мачты выражается уравнением
|
Рл, |
|
Мшп = 90 + 0,13 Рл +1,05 Мкр + 0,054 Рм + 56Нм+ 0,084Qм, |
(9.11) |
|
где |
Рм |
и Qм – грузоподъемность |
соответственно лебедки, механизма |
подачи |
|
и мачты, Н; Мкр – крутящий момент, Нм; Нм – высота мачты, м. |
|
||||
|
Масса станков с подвижным вращателем и гидроприводом наиболее существенно |
||||
зависит от мощности привода, грузоподъемности механизма подачи и его хода: |
|
||||
|
|
|
Мп = 160 +12N + 0,11 lпРм, |
(9.12) |
|
где N – мощность, кВт; lп – ход подачи, м; Рм – усилие подачи, Н. |
|
||||
|
Если станок имеет мачту, то в последнем уравнении добавляются члены, |
||||
характеризующие ее массу. |
|
|
|||
|
Масса насоса Мн, входящего в состав установки, ориентировочно может быть |
||||
найдена из выражения |
|
|
|||
|
|
|
Мн = 70Nг, |
(9.13) |
|
где |
Nг |
– |
гидравлическая мощность |
насоса, кВт, Nг = qp/1,02·107; q – |
расход |
жидкости, л/с; р – давление, соответствующее максимальному расходу, Па [8]. |
|
9.5. Компоновка буровых станков и установок
Взаимное расположение основных рабочих и вспомогательных механизмов, их кинематическая и конструктивная связь определяют компоновку буровых станков и установок. От компоновки зависят работоспособность узлов и механизмов, доступность их для ремонта и обслуживания, удобство сборки и разборки, а также габариты и масса оборудования. Компоновка существенно влияет и на эксплуатационные возможности буровой техники, поскольку от нее зависит, в какой мере оборудование отвечает технологическим требованиям бурения в различных условиях, в частности бурения наклонных, горизонтальных и востающих скважин, их обсадки. Компоновка имеет большое значение для удобства проведения спуско-подъемных операций и обеспечения нормальных условий навивки каната на барабан лебедки.
Известны две принципиально различные компоновочные схемы: моноблочная и разобщенная. Моноблочную компоновку применяют чаще всего в стационарных шпиндельных станках и в отдельных случаях в станках с подвижным вращателем, когда последний имеет небольшой ход. При моноблочной схеме основные узлы станка или агрегата расположены рядом и непосредственно связаны не только кинематически, но и конструктивно, причем кинематическая цепь располагается преимущественно в вертикальной плоскости и реже в горизонтальной.
Конструктивная связь выражается в том, что некоторые узлы являются несущими элементами и связующими звеньями. Кроме того, каждый из них связан с общей несущей конструкцией. Небольшие межцентровые расстояния в моноблочной схеме позволяют применять зубчатые передачи.
175
По мере увеличения мощности и массы оборудования компактность станков становится их недостатком, так как ухудшает доступ к отдельным узлам для осмотра и ремонта, а также усложняет транспортировку в связи с трудностью разборки и сборки при ремонтных работах. Для устранения этого недостатка используют схему, в которой лебедка и вращатель смонтированы на общей станине, а коробка передач вынесена изпод лебедки и расположена на нижней раме, где может быть легко вскрыта или демонтирована. В таких станках ремонт и обслуживание любого узла не вызывают трудностей, упрощаются также монтаж и демонтаж при перевозках. Разобщенную компоновку применяют в большинстве буровых установок с роторными и подвижными вращателями.
Разобщенная схема характеризуется тем, что основные узлы в большинстве случаев имеют только кинематическую связь и каждый из них независимо от другого связан с несущей конструкцией, которая может быть общей для всего станка или установки либо индивидуальной для отдельных рабочих механизмов и агрегатов.
Вшпиндельных станках с моноблочной компоновкой практически все узлы выполняют функции несущих элементов конструкции и непосредственно связаны друг
сдругом. Некоторые узлы конструктивно связаны с четырьмя-пятью другими узлами. Степень взаимной связи узлов характеризуется отношением числа таких связей к числу узлов. Для моноблочной компоновки это отношение равно четырем, для разобщенной, характерной для подвижного и роторного вращателей, – вдвое меньше, так как функции несущих элементов выполняют только специально предназначенные для этого узлы – рама, станина или основание.
Моноблочные буровые станки и агрегаты отличаются расположением лебедки, двигателя, взаимным расположением и кинематической связью узлов, типом несущей конструкции, конструктивной связью вращателя и мачты и др. Положение лебедки определяет принципиальную схему станка. Существуют две такие схемы: лебедка обращена к вращателю торцом или боковой поверхностью. В первом случае ось лебедки перпендикулярна, а во втором – параллельна оси кронблока.
Первая схема является преобладающей. В настоящее время 90 % оборудования имеет такую схему. Вторая схема применяется в станках, предназначенных в основном для бурения вертикальных скважин. Преимущества станков с лебедками, обращенными торцом к вращателю, заключаются прежде всего в сравнительной простоте кинематической схемы, так как их кинематические цепи располагаются преимущественно в одной вертикальной плоскости. Кинематика станков второго типа значительно сложнее, поэтому при аналогичных параметрах эти станки на 20–25 % тяжелее первых.
Лебедка, обращенная торцом к вращателю, позволяет устанавливать вращатель для бурения скважин под углом от 0° до 360°, в то время как при лебедке, обращенной к вращателю боковой поверхностью, этот угол ограничен 45°–90°. Усложняется и система управления тормозами лебедки, которая выводится к пульту бурильщика посредством тяг.
Встанках с лебедкой, обращенной торцом к вращателю, ухудшаются условия навивки каната на барабан лебедки при отодвигании станка для освобождения устья скважины, а также в связи с тем, что канат изгибается в двух взаимно перпендикулярных плоскостях – на барабане лебедки и шкиве кронблока. Исходя из этого применяется ряд конструктивных решений, позволяющих обеспечить нормальные условия навивки каната. Одним из наиболее распространенных решений является смещение тормозных шкивов лебедки в сторону, противоположную вращателю, что способствует приближению барабана к оси скважины. Для сохранения нормального угла девиации (отклонения) каната при любом положении станка и лебедки применяют на кронблоке шкивы увеличенного диаметра, а также дополнительные оттяжные ролики на мачте. Кроме того, увеличивают диаметр барабана лебедки и уменьшают его длину.
176
Вбуровых агрегатах с лебедкой, обращенной торцом к вращателю, преобладает компоновка, при которой основные узлы станка и двигатель размещены на общем основании. Оборудование, предназначенное для бурения на глубину до 100 и иногда до 200 м, имеет в большинстве случаев легкое сварное или собранное на болтах основание.
Впередней, более высокой части основания располагают вращатель и лебедку, а на задней, низкой – двигатель. Привод осуществляется обычно посредством гибких передач – клиноременной или цепной. Такая конструкция сводит до минимума число связующих элементов, обеспечивает легкий доступ к узлам и механизмам станка для осмотра, ремонта, сборки и разборки.
Воборудовании для бурения на глубину свыше 200 м в большинстве случаев преобладает компоновка, при которой агрегат включает основание с двигателем на нем
истанину, связывающую с основанием вращатель и лебедку. Основание обычно представляет собой сварную конструкцию и реже собирается на болтах из труб, уголков, литых или штампованных деталей.
Станина представляет собой независимый замкнутый каркас или коробчатую конструкцию либо состоит из нескольких элементов. В последнем случае роль несущей конструкции выполняют частично корпус коробки передач, корпус раздаточной коробки и опорные кронштейны вала лебедки. Такие станины обычно применяют в оборудовании для бурения до 500–800 м, так как по мере увеличения приводной мощности и нагрузок частичное использование основных узлов станка в качестве несущих конструкций требует значительного утяжеления их корпусных деталей и становится нецелесообразным. Ввиду этого в наиболее мощном оборудовании используется преимущественно первый вариант конструкции станины.
Важными особенностями компоновки буровых агрегатов являются расположение маслонасоса и место его привода в общей кинематической цепи. Возможны два принципиально различных варианта привода маслонасоса, отличающихся тем, что отбор мощности осуществляется до или после главного фрикциона агрегата. Преимуществом первого, наиболее распространенного варианта является более оперативное и независимое управление вращателем и механизмом подачи. Если мощность для привода насоса отбирается после фрикциона, то отключение его приводит к прекращению работы механизма подачи, что обусловливает дополнительные операции по переводу коробки передач в нейтральное положение при необходимости остановки вращения, например при перекреплении патрона. Такая взаимосвязь управления механизма подачи и вращателя крайне затрудняет, а иногда делает вообще невозможным проведение некоторых технологических операций, требующих эпизодического включения вращения при натяжении или осевом перемещении снаряда. Это относится прежде всего к срыву керна, а также к операциям с колоколом или метчиком, установке отклоняющих клиньев и другим специальным работам в скважине.
Для освобождения устья скважины некоторые буровые агрегаты независимо от их компоновки имеют дополнительную нижнюю раму, по которой и перемещаются посредством одного или двух гидроцилиндров.
Вбольшинстве случаев моноблочные буровые агрегаты используются в сочетании
с вышками или стационарными мачтами, имеющими независимое основание. Однако такая конструкция установки затрудняет нормальную навивку каната на барабан лебедки при наклонном бурении. В связи с этим в некоторых агрегатах мачта конструктивно увязывается с вращателем. В станках с лебедкой, обращенной боковой поверхностью барабана к вращателю, мачта шарнирно прикреплена к кронштейнам, размещенным на боковинах станины. Поворот мачты осуществляется независимо от вращателя посредством специального гидроцилиндра, а фиксируется она телескопической шарнирной стойкой.
177
Влегких агрегатах с лебедками, обращенными торцом к оси скважины, применяют мачты, основная ферма которых опирается на поворотную плиту, расположенную между вращателем и станиной. При таком конструктивном решении поворот мачты на заданный угол для наклонного бурения осуществляется одновременно с поворотом вращателя. Устье скважины в этом случае освобождается откидыванием вращателя и расстояние лебедки от оси скважины остается постоянным.
При конструктивной увязке бурового агрегата с мачтой можно создать компактную установку. Такая установка занимает минимально возможную площадь, легко монтируется на любую транспортную базу – автомашину, трактор, прицеп и при необходимости может быть быстро демонтирована. В более тяжелых установках мачта располагается рядом со станком на отдельном постаменте и устанавливается с необходимым углом наклона с помощью гидроцилиндра и винтовой стойки.
Оборудование с разобщенной компоновкой имеет ряд общих принципиальных особенностей. Основные узлы такого оборудования размещены на общей раме и обычно имеют только кинематическую связь. В самоходном исполнении мощность для привода таких установок отбирается от транспортного двигателя через коробку отбора мощности или непосредственно от специального двигателя, расположенного на раме. Далее напрямую или через карданный вал мощность передается на цепную или зубчатую раздаточную коробку, от которой приводятся ротор, лебедки и механизм подачи. Привод ротора во всех установках осуществляется через коробку передач, связанную с раздаточной коробкой упруго-демпфирующими или цепными муфтами. Ротор обычно связан с коробкой передач телескопическим карданным валом, позволяющим отодвигать его для освобождения устья скважины. Для привода лебедок служит обычно конический угловой редуктор, который приводится карданным валом или цепной передачей от коробки передач или непосредственно от раздаточной коробки. Карданный вал привода ротора расположен несколько ниже вала лебедок.
Вприводе механизма подачи применяют в основном объемные гидропередачи. Для привода промывочного насоса и компрессора мощность отбирается от той же
раздаточной коробки цепными или карданными передачами либо клиноременными и цепными передачами до раздаточной коробки.
Для ударных и комбинированных установок характерна своеобразная компоновка, отличающаяся тем, что от коробки скоростей или непосредственно от двигателя с помощью клиноременной или цепной передачи осуществляется привод трансмиссионного вала, а от него — лебедок, ударного механизма и ротора.
В стационарных и самоходных установках с подвижным вращателем на раме монтируются двигатель, маслонасосы и маслобак, гидросистема, лебедка, система управления и постамент, с которым шарнирно связана мачта, устанавливаемая в рабочее положение посредством гидроцилиндра. При этом мачта опирается на раму или непосредственно на грунт. В последнем случае она снабжена домкратами.
Механизм подачи связан с мачтой конструктивно и перемещает по имеющимся на ней направляющим подвижный вращатель. У основания мачты обычно предусматривают площадку с центратором для работы с подкладной вилкой или спайдером [8].
9.6. Оценка эксплуатационных возможностей буровых станков
Под эксплуатационными возможностями буровых станков следует понимать возможность бурения скважин в различных геологотехнических условиях на заданную глубину с обеспечением необходимых технико-экономических показателей. Ввиду этого, оценивая эксплуатационные возможности оборудования, надо определить значения глубины и диаметра скважин, которые могут быть пробурены с его применением в заданных условиях и с параметрами режима бурения, которые могут быть обеспечены. Для этого необходимо использовать закономерности,
178
характеризующие затраты мощности на работу породоразрушающего инструмента, вращение бурильных труб и промывку скважины.
Наиболее общими критериями эксплуатационных возможностей являются значения скорости бурения и стоимость 1 м скважины, которые могут быть получены в конкретных геологотехнических условиях. При этом следует рассматривать средние значения механической, рейсовой и цикловой скорости.
Средняя механическая скорость представляет собой частное от деления длины пробуренного интервала li на чистое время бурения ti, т.е. υм = li / ti. Механическая скорость функционально связана с частотой вращения, поэтому одним из параметров оценки буровых станков является средневзвешенная частота вращения на всей глубине скважины.
При оценке возможных значений глубины бурения с использованием различных значений частоты вращения необходимо учитывать геологотехнические условия. Нормальными условиями являются такие, когда бурят в устойчивых породах с минимальными зазорами между стенками скважин и бурильными трубами, отсутствуют резкие перегибы ствола и каверны, бурильные трубы соответствуют требованиям стандарта, а потери мощности в станках не превышают расчетных. Отклонение от таких условий вызывает уменьшение предельных значений глубины бурения с использованием тех же значений частоты вращения. Установлено, что низкое качество изготовления или неудовлетворительное регулирование станка могут уменьшить эту глубину на 20–30 %, применение бурильных труб, не отвечающих требованиям высокооборотного бурения, – на 30–40 %, а разбуривание скважин с увеличением диаметра и образование каверн – до 50 %. Одновременное действие перечисленных факторов до 2,5–3 раза сокращает предельную глубину бурения, а иногда вообще исключает возможность использования рациональных режимов бурения вследствие недостатка мощности.
Рейсовая скорость
υр = li / (tчб + tсп + tвсп), |
(9.14) |
где tчб – время чистого бурения; tсп и tвсп – соответственно время спуско-подъемных и вспомогательных операций.
Поскольку на рейсовую скорость влияет быстрота выполнения спуско-подъемных и вспомогательных операций, она зависит прежде всего от параметров и конструкции буровой установки. Быстрота спуско-подъемных операций зависит от мощности приводного двигателя, скоростей подъема, предусмотренных в станке, длины свечи и, следовательно, высоты мачты, затрат времени на свинчивание и развинчивание резьбовых соединений, типа элеватора.
На спуско-подъемные операции существенно влияет и состояние скважины, которое сказывается на величине коэффициента сопротивления подъема бурового инструмента. Вследствие нарушения устойчивости стенок ствола могут быть ограничены скорости спуска и подъема труб.
К вспомогательным операциям, влияющим на рейсовую скорость, относятся перекрепление патронов, наращивание инструмента, освобождение устья скважины, работа с колонковой трубой. Скорость выполнения этих операций зависит от конструктивных особенностей оборудования: типа вращателя и патрона, конструкции и хода механизма подачи, способа освобождения устья и т.д.
Структура затрат времени, влияющих на рейсовую скорость, изменяется в зависимости от способов извлечения керна: обычным способом с подъемом бурильной колонны или без ее подъема – съемным керноприемником на канате или восходящим потоком промывочной жидкости (гидротранспорт керна). В последнем случае возрастает влияние на рейсовую скорость вспомогательных операций и соответствующих конструктивных особенностей оборудования.
Цикловая скорость может быть найдена из выражения
179
ц |
L |
, |
(9.15) |
|
tчб tсп tвсп tтр tмд tр |
||||
|
|
|
где L – глубина скважины, м; tмд, tтр, tр – затраты времени на монтаж-демонтаж, транспортировку и ремонтные работы.
Цикловая скорость учитывает влияние способа транспортировки, типа транспортной базы установки, ее удобства при монтажно-демонтажных операциях, в том числе способ подъема и опускания мачты, наличие домкратов для выравнивания установки и прочее, а также надежности оборудования: наработки на отказ, среднего времени восстановления, ремонтопригодности.
Стоимость 1 м скважины (в руб/м)
∆s = S/П, |
(9.16) |
где S – стоимость станко-смены, руб.; П – производительность бурения, м/смену. Стоимость станко-смены зависит от типа бурового оборудования, его приводной
мощности, расхода бурового инструмента, расхода истирающих и горюче-смазочных материалов. В целом характерно увеличение стоимости станко-смены по мере повышения мощности приводного двигателя установки. Для конкретных случаев стоимость станко-смены должна определяться расчетами по известным методикам [8].
9.7. Перспективы совершенствования геологоразведочной буровой техники
В последние годы достигнут значительный рост скоростей геологоразведочного бурения. Дальнейшее их увеличение может быть получено на основе внедрения разработанных и создания новых технических средств, позволяющих повышать механические скорости бурения при одновременном улучшении использования рабочего времени.
К мероприятиям, направленным на увеличение механической скорости, относится прежде всего применение более рациональных технологических режимов и, в частности, увеличение окружной скорости вращения алмазных коронок до 5–8 м/с, что соответствует значениям частоты вращения до 3000 об/мин. Это мероприятие требует применения комплекса специальных технических средств. Необходимы алмазные коронки с меньшей шириной торца (4–5 мм), что позволит уменьшить осевые нагрузки, снизить затраты мощности на забое и повысить механическую скорость.
Для снижения затрат мощности на вращение бурильной колонны необходимы бурильные трубы, обладающие высокой точностью изготовления, прямолинейностью (кривизна до 0,3 мм/м), соосностью резьбовых соединений. Перспективны легкосплавные бурильные трубы, мощность на вращение которых сокращается в 1,5–1,8 раза по сравнению со стальными. Важной задачей является увеличение их прочности и износостойкости. Для ее решения следует применять методы механической и термической обработки поверхности таких труб и новые легкие и прочные сплавы, например магниево-циркониевые, титановые и др.
Рост механической скорости может быть достигнут путем наложения на вращающийся породоразрушающий инструмент высокочастотных ударных импульсов посредством гидроударных машин или других возбудителей ударов. Расчеты показывают, что рост механической скорости лишь до определенных пределов приводит к существенному увеличению производительности, так как при этом одновременно возрастает удельный вес спуско-подъемных и вспомогательных операций. Это наглядно иллюстрируется коэффициентом времени чистого бурения Kчб, представляющим собой отношение времени собственно бурения к общим затратам времени на бурение 1 м скважины:
Kчб = 1 / (1 + tвсп.уд υм), |
(9.17) |
где tвсп.уд – время на выполнение вспомогательных операций в расчете на 1 |
м, ч; |
υм – механическая скорость бурения, м/ч. |
|
180 |
|